第三章高炉内的还原过程
第三章 高炉炼铁工艺(工艺部分)-讲义

个放热反应一个吸热反应。
② b 、 d 、 c三条曲线交于570℃,在此
Fe 、 FeO 和Fe3O4三相平衡共存。
③ 曲线O4和 Fe2O3稳定存
在区域。 ④ T<570℃时还原顺序为:
Fe2O3→Fe3O4 →Fe
570℃ CO还原铁矿石气相平衡组成图
(1)提高鼓风温度; (2)提高鼓风中氧气含量; (3)降低鼓风湿度; (4)减少喷吹量; (5)减少炉缸煤气体积。
•回旋区和燃烧带
随着高炉冶炼强度的提高风速 增大(I00~200 m/s) 焦炭在风口 前随气流一起运动,形成一个非 静止的、疏散的、近似球形的自 由空间,即为风口回旋区。
影响燃烧带大小的因素主要有: ① 鼓风动能 表示鼓风的穿透能力。鼓风动能越大,燃烧带越大。 ② 燃烧反应速度 燃烧反应速度提高,燃烧带缩小。一般情况下,风温提高。燃烧反应 速度加快,燃烧反应时间减少,燃烧带长度减小;鼓风中氧增加,燃烧 反应速度加快,燃烧反应时间减少,燃烧带长度减小。 ③ 炉缸料柱压力 炉缸内料柱疏松,燃烧带延长;反之,燃烧带缩小。 ④ 焦炭性质焦炭粒度、气孔度、反应性等对燃烧带大小也有一定的影响。
洗涤器
coke sinter lumpore flux
配料间 主输送帶
鼓风嘴
热风
出铁口
高炉
废气 鼓风机
冷空气
鱼雷罐车
3.1.1 高炉冶炼过程及其特点
高炉炼铁的本质是铁的还原过程,即焦炭做燃料和还原剂,在 高温下将铁矿石或含铁原料的铁,从化合物状态(如Fe2O3、 Fe3O4等)还原为液态生铁。
在炉前用蒸汽吹成渣棉,作绝热材料。 冶炼多元素共生的复合矿时,炉渣中常富集有多种元素(如稀土、
钛等)。这类炉渣可进一步利用。
高炉内生成铁的原理是什么
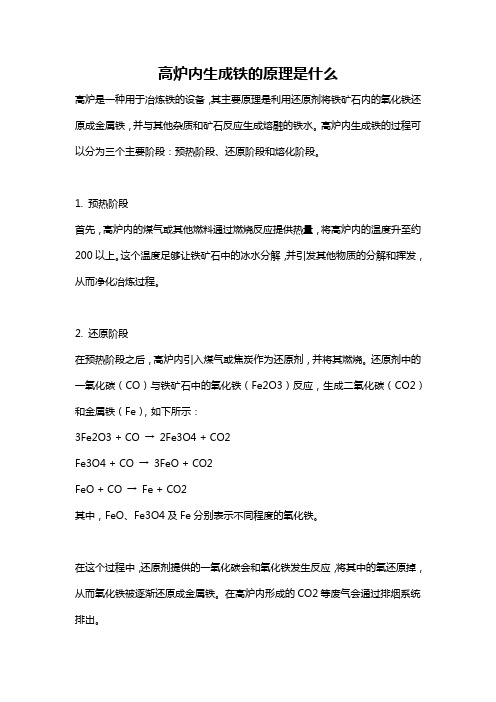
高炉内生成铁的原理是什么高炉是一种用于冶炼铁的设备,其主要原理是利用还原剂将铁矿石内的氧化铁还原成金属铁,并与其他杂质和矿石反应生成熔融的铁水。
高炉内生成铁的过程可以分为三个主要阶段:预热阶段、还原阶段和熔化阶段。
1. 预热阶段首先,高炉内的煤气或其他燃料通过燃烧反应提供热量,将高炉内的温度升至约200以上。
这个温度足够让铁矿石中的冰水分解,并引发其他物质的分解和挥发,从而净化冶炼过程。
2. 还原阶段在预热阶段之后,高炉内引入煤气或焦炭作为还原剂,并将其燃烧。
还原剂中的一氧化碳(CO)与铁矿石中的氧化铁(Fe2O3)反应,生成二氧化碳(CO2)和金属铁(Fe),如下所示:3Fe2O3 + CO →2Fe3O4 + CO2Fe3O4 + CO →3FeO + CO2FeO + CO →Fe + CO2其中,FeO、Fe3O4及Fe分别表示不同程度的氧化铁。
在这个过程中,还原剂提供的一氧化碳会和氧化铁发生反应,将其中的氧还原掉,从而氧化铁被逐渐还原成金属铁。
在高炉内形成的CO2等废气会通过排烟系统排出。
3. 熔化阶段在还原过程中,金属铁会逐渐与其他杂质、矿石和渣球反应,形成熔融的铁水。
铁水会下沉并从高炉底部的出铁口流出,而留下的渣球则会从高炉顶部排出。
高炉内生成铁的原理涉及到多种物理和化学过程,其中还包括矿石的分解、还原反应、熔化和脱渣等。
为了保持高炉的有效工作,还需注意控制气氛、燃料的使用和废气处理等方面。
高炉内的反应过程是与温度、压力、矿石和还原剂的性质以及高炉结构等多个因素相关的复杂过程。
为了提高冶炼效率、降低成本和减少对环境的影响,工程师和研究人员一直在致力于优化高炉的设计和操作。
炼铁原理深入解读高炉内铁矿石直接还原的热力学基础

炼铁原理深入解读高炉内铁矿石直接还原的热力学基础炼铁是将铁矿石中的铁元素还原为金属铁的过程,而高炉是最常见的炼铁设备之一。
在高炉内,铁矿石通过高温条件下的还原反应,被还原为金属铁,并与炉渣分离。
本文将深入解读高炉内铁矿石直接还原的热力学基础。
1. 高炉的工作原理高炉是一种巨大的筒形炉子,通常由钢铁砌成。
在高炉内,通过矿石投料口将铁矿石、焦炭和炉渣按一定比例投入。
在高炉内部,有燃烧室、还原室和熔化室三个区域,每个区域都具有特定的功能。
2. 铁矿石的还原反应铁矿石的主要成分是氧化铁,例如赤铁矿(Fe2O3)和磁铁矿(Fe3O4)。
在高炉内,还原室是铁矿石还原的主要区域。
3. 热力学基础直接还原是指在高炉内,铁矿石直接与还原剂(焦炭或其他还原剂)发生反应,而不经过中间产物。
在铁矿石直接还原反应中,热力学是非常重要的基础。
4. 铁矿石的直接还原反应铁矿石的直接还原反应包括两个主要过程:氧化还原反应和还原-熔化反应。
4.1 氧化还原反应氧化还原反应是指铁矿石中的氧化铁被还原成金属铁的反应。
例如,赤铁矿的氧化还原反应可以表示为:3Fe2O3 + CO → 2Fe3O4 + CO2Fe3O4 + CO → 3FeO + CO2FeO + CO → Fe + CO24.2 还原-熔化反应在氧化还原反应之后,还原得到的含碳铁矿石(通常含有一定质量分数的碳)将开始熔化,并与炉渣分离。
在这个阶段,很多复杂的化学反应发生。
其中一个重要的反应是碳与铁氧化物的反应:FeO + C → Fe + CO5. 温度对直接还原反应的影响在高炉内部,温度是影响直接还原反应的重要因素之一。
较高的温度有助于促进还原反应的进行,提高铁矿石的还原率。
6. 炉渣的作用炉渣在高炉内具有重要的作用。
它不仅能够吸收和稀释产生的有害杂质,还能够提供适宜的炉内温度和熔融性环境。
7. 其他关键因素除了温度和炉渣的作用,还有其他因素会对高炉内直接还原反应产生影响,例如矿石的粒度、还原剂的选择和投放位置等。
炼铁原理解析高炉冶炼过程中的矿石还原与炉渣形成机制
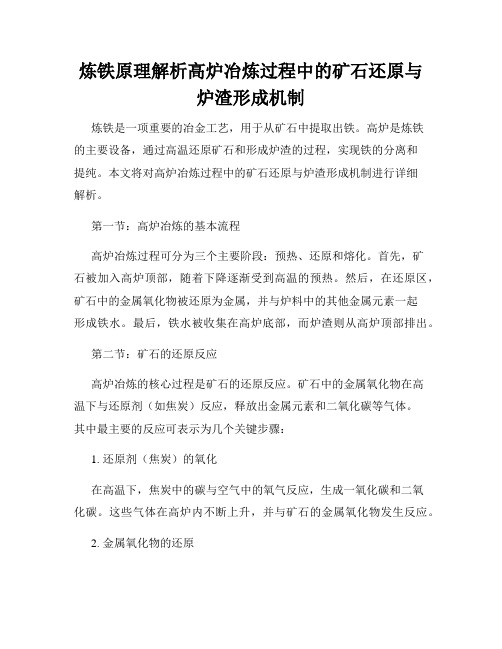
炼铁原理解析高炉冶炼过程中的矿石还原与炉渣形成机制炼铁是一项重要的冶金工艺,用于从矿石中提取出铁。
高炉是炼铁的主要设备,通过高温还原矿石和形成炉渣的过程,实现铁的分离和提纯。
本文将对高炉冶炼过程中的矿石还原与炉渣形成机制进行详细解析。
第一节:高炉冶炼的基本流程高炉冶炼过程可分为三个主要阶段:预热、还原和熔化。
首先,矿石被加入高炉顶部,随着下降逐渐受到高温的预热。
然后,在还原区,矿石中的金属氧化物被还原为金属,并与炉料中的其他金属元素一起形成铁水。
最后,铁水被收集在高炉底部,而炉渣则从高炉顶部排出。
第二节:矿石的还原反应高炉冶炼的核心过程是矿石的还原反应。
矿石中的金属氧化物在高温下与还原剂(如焦炭)反应,释放出金属元素和二氧化碳等气体。
其中最主要的反应可表示为几个关键步骤:1. 还原剂(焦炭)的氧化在高温下,焦炭中的碳与空气中的氧气反应,生成一氧化碳和二氧化碳。
这些气体在高炉内不断上升,并与矿石的金属氧化物发生反应。
2. 金属氧化物的还原金属氧化物与一氧化碳发生反应,还原成金属元素和二氧化碳。
这个还原反应是炉内主要的化学反应之一。
不同金属氧化物的还原程度和速率有所不同,这取决于各自的化学性质及温度条件。
3. 金属元素的迁移还原后的金属元素在高温下与其他金属元素结合,形成熔化的铁水。
这些金属元素在高炉内上升,直至达到悬浮于铁水上方的炉渣层。
第三节:炉渣的形成机制炉渣是高炉冶炼过程中的重要产物,它具有多种功能,如吸附杂质、稀释硫和磷等。
在高炉冶炼过程中,炉渣的形成主要经历以下几个步骤:1. 矿石中杂质的熔化矿石中的杂质(如硅、铝、钙等)在高温下被熔化,并分散于铁水和炉渣中。
这种熔化是高炉冶炼过程中的一个重要步骤,它有助于将杂质从铁水中分离出来。
2. 杂质的反应和吸附杂质在铁水和炉渣中发生各种化学反应,如与炉渣中的主要成分形成化合物或吸附于炉渣颗粒表面。
通过这些反应和吸附作用,炉渣能够有效地吸附和脱除铁水中的杂质。
第三章 高炉炼铁

的碳化硅砖或高导热的炭砖为主,高
炉下部以高导热的石墨质炭砖为主,
图 5.7 炉缸、炉底砌筑结构
6
图 3.7 为炉缸、炉底砌筑结构示意图。 3)冷却设备
冷却设备的作用是降低炉衬温度,提高炉衬材料抗机械、化学和热产生的侵蚀能力, 使炉衬材料处于良好的服役状态。高炉使用的冷却设备主要有冷却壁、冷却板和风口。冷却 壁紧贴着炉衬布置,冷却面积大;而冷却板水平插入炉衬中,对炉衬的冷却深度大,并对炉 衬有一定的支托作用。
(3)鼓风:空气通过高炉鼓风机加压后成为高压空气(鼓风),经过热风炉换热,将温 度提高到 1100~1300℃,再从高炉风口进入炉缸,与焦炭和煤粉燃烧产生热量和煤气。鼓风 带入高炉的物理热占高炉热量总收入的 20%左右。在鼓风中加入氧气可提高鼓风中的氧含 量(称为富氧鼓风)。采用富氧鼓风可提高风口燃烧温度,有利于高炉提高喷煤量和高炉利
4000m3 级高炉日产生铁量达到 10000 t 以
上。
hf
d1
β D
α
风口 中心线
d
铁口 中心线
h1
h2
h3
h4
h5
h6
炉 喉
炉 身
炉 腰 炉 腹 炉 缸 死铁层
Hu H
h0
3.2.3 高炉生产主要技术经济指标
图 5.3 高炉内型
(1)有效容积利用系数(ηu ):每 m3 高炉有效容积每天生产的铁水量( t / m3 ⋅ d ),
KΣ
=
每天装入高炉的焦炭量+ 每天喷入高炉的煤粉量×置换比 高炉每天出铁量
(3.4)
煤粉置换比通常小于 1.0,一般在 0.75~0.90 之间。
(6)冶炼强度( I ):每 m3 高炉有效容积每天消耗的(干)焦炭量( t / m3 ⋅ d )。
第三章 高炉炼铁

回旋区和中间层组成焦炭 在炉缸内进行燃烧反应的 区域称为燃烧带。 实践中常以CO2降至1~ 2%的位置定为燃烧带界 限。大型高炉的燃烧带长 度在1000~1500mm 左右。
3.3 还原反应
3.3.1 基本概念 3.3.2 高炉内铁氧化物的还原 3.3.3 高炉内非铁元素的还原
3.3.1基本概念
渣铁液滴在焦炭空隙间滴落的同时,继续进行还 原、渗碳等高温物理化学反应,特别是非铁元素的
还原反应。
4、风口燃烧带
风口前的焦炭在燃 烧时能被高速鼓风气 流 ( 1100~1300℃ ) 所 带动,形成一个“鸟 窝”状的回旋区,焦 炭在回旋运动的气流 中悬浮并燃烧。
回旋区的径向深度达不到高炉中心,因而炉子中心 仍燃堆积着一个圆丘状的焦炭死料柱,构成了滴落带
煤比 风温 渣铁比 入炉品 位% kg/t kg/t ℃ 200 1274 258 60.09 138 1104 268 60.00
160 125 1113 1099 294 325 59.73 59.98
太钢 莱钢 鄂钢 杭钢 三明
3 4 8 4 3
1200 750 620 450 380
2.159 3.030 2.640 3.970 3.98
3.4 高炉炉渣与脱硫
高炉炉渣是铁矿石中的脉石和焦炭(燃料)中 的灰分等与熔剂相互作用生成低熔点的化合 物,形成非金属的液相。
高炉炉渣的成分 高炉炉渣作用 成渣过程 生铁去硫
3.4.1 高炉炉渣的成分
高炉炉渣的来源:矿石中的脉石、焦炭(燃料)中的灰 分、熔剂中的氧化物、被侵蚀的炉衬等。 高炉炉渣的成分:氧化物为主,且含量最多的是SiO2、 CaO、Al2O3、MgO。 炉渣中氧化物的种类:碱性氧化物、酸性氧化物和中 性氧化物。以碱性氧化物为主的炉渣称碱性炉渣;以 酸性氧化物为主的炉渣称酸性炉渣。 炉渣的碱度(R):炉渣中碱性氧化物和酸性氧化物的质 量百分数之比表示炉渣碱度: 高炉炉渣碱度一般表示式:R=m(CaO)/m (SiO2) 炉渣的碱度根据高炉原料和冶炼产品的不同,一般在 1.0~1.3之间。
第三章高炉炼铁工艺[1]
![第三章高炉炼铁工艺[1]](https://img.taocdn.com/s3/m/ae50eca68bd63186bcebbcfc.png)
第三章高炉炼铁工艺[1]
炼 铁 高 炉 的 结 构
第三章高炉炼铁工艺[1]
1一炉底耐火材料: 2一炉壳; 3一炉内砖衬生产后的侵 蚀线; 4一炉喉钢砖, 5一炉顶封盖; 6一炉体砖衬; 7一带凸台镶砖冷却壁; 8一镶砖冷却壁; 9一炉底碳砖; 10一炉底水冷管;炉底砌筑结构示意图
对高炉炉衬的基本要求如下: ① 各部位内衬与热流强度相适应,以保持在强热流冲击 下内衬的稳定性。 ② 炉衬的侵蚀和破坏与冶炼条件密切相关,不同位置的 耐火材料受侵蚀破坏机理不同,因此要求各部位内衬与侵 蚀破损机理相适应,以延缓内衬破损速度。
第三章高炉炼铁工艺[1]
第三章高炉炼铁工艺[1]
3.4.1 开炉
开炉是高炉一代炉龄的开始。 (1) 开炉前的准备检查:开炉前必须对高炉全部设备进行仔细 检查和试运转。 (2) 烘炉必须根据一定的烘炉制度对高炉和热风炉逐渐加热, 彻底烘干炉衬以免影响一代寿命。 (3) 装料应选用最好的炉料作为开炉引料,按照计算的配料表 进行合理的开炉装料。
第三章高炉炼铁工艺[1]
湿法除尘系统
重力除尘器 1—煤气下降管;2—塔前管;
3—中心导入管;4—清灰口
第三章高炉炼铁工艺[1]
高炉煤气干法除尘系统 1—重力除尘器;2—脏煤气管;3 —一次布袋除尘器;4— 二次布袋除尘器;5—蝶阀;6—闸阀;7—净热煤气管道
第三章高炉炼铁工艺[1]
⑸ 渣铁处理系统 高炉渣铁处理系统主要包括:炉前工作平台、出铁场、渣及 铁沟、开口机、泥炮、堵渣机、铸铁机、炉渣处理设备、铁 水罐等。出铁场一般比风口平台低约1.5m。由铁口到砂口 (撇渣器或渣铁分离器)的一段为主沟。
⑶ 高炉冷却设备
冷却设备的作用是降低炉衬温度;提高炉衬材料抗机械、 化学和热产生的侵蚀能力,使炉衬材料处于良好的服投状态。
炼铁学 高炉冶炼过程的物理化学

炼铁学——高炉冶炼过程的物理化学
炼铁学——高炉冶炼过程的物理化学
3.1.3 碳酸盐分解
当炉料中单独加入熔剂(石灰石或白云石) 当炉料中单独加入熔剂(石灰石或白云石)或炉料中尚有其他类型 的碳酸盐时,随着温度的升高,当其分压 超过炉内气氛的CO 的碳酸盐时,随着温度的升高,当其分压pCO2超过炉内气氛的 2分压 时,碳酸盐开始分解。 碳酸盐开始分解。 FeCO3、MnCO3、MgCO3分解较容易,在炉内较高的位置即可开始。 分解较容易,在炉内较高的位置即可开始。 以上三种碳酸盐的分解反应发生在低温区,对冶炼过程无大影响。 以上三种碳酸盐的分解反应发生在低温区,对冶炼过程无大影响。 但石灰石(CaCO3)开始分解的温度高达 开始分解的温度高达700℃,且其分解速度受熔剂 但石灰石 开始分解的温度高达 且其分解速度受熔剂 粒度的影响较大。目前石灰石粒度多为 粒度的影响较大。目前石灰石粒度多为25~40mm,有相当一部分 有相当一部分 CaCO3进入 进入900℃以上的高温区后才发生分解 此时反应产物 此时反应产物CO2会与 ℃以上的高温区后才发生分解。此时反应产物 会与 固体碳发生碳素溶解损失反应: 固体碳发生碳素溶解损失反应: CO2+C= 2CO
炼铁学——高炉冶炼过程的物理化学
该反应吸收大量热量,并消耗碳素,对高炉能量消耗不利。 该反应吸收大量热量,并消耗碳素,对高炉能量消耗不利。计算中一 般取石灰石在高温区分解的部分占50~70%。 般取石灰石在高温区分解的部分占 炉料中碳酸盐来源:生熔剂 石灰石 白云石)、 石灰石、 炉料中碳酸盐来源:生熔剂(石灰石、白云石 、天然块矿 碳酸盐分解反应: 碳酸盐分解反应: FeCO3= FeO+ CO2 MnCO3= MnO+ CO2 MgCO3= MgO+ CO2 CaCO3= CaO+ CO2 碳酸盐分解条件 开始分解: 分解压) 炉内CO 分压)⇐⇒T开 开始分解:Pco2(分解压 ≥Pco2(炉内 2分压 分解压 炉内 化学沸腾: 分解压) 总 炉内总压 炉内总压)⇐⇒T沸 化学沸腾:Pco2(分解压 ≥P总(炉内总压 分解压
- 1、下载文档前请自行甄别文档内容的完整性,平台不提供额外的编辑、内容补充、找答案等附加服务。
- 2、"仅部分预览"的文档,不可在线预览部分如存在完整性等问题,可反馈申请退款(可完整预览的文档不适用该条件!)。
- 3、如文档侵犯您的权益,请联系客服反馈,我们会尽快为您处理(人工客服工作时间:9:00-18:30)。
第三章高炉内的还原过程第一节炉料的蒸发、挥发和分解一、水分的蒸发炉料中的水以吸附水和化合水两种形式存在。
吸附水存在于热烧结矿以外的一切炉料中,吸附水一般在l05℃以下即蒸发。
吸附水蒸发对高炉冶炼并无坏处,因为炉喉煤气温度通常大于200℃,流速也很高,炉料中的吸附水在炉料入炉后,下降不大的距离就会蒸发完,水的蒸发仅仅利用了煤气的余热,不会增加焦炭的消耗;同时因水分的蒸发吸热,降低了煤气温度,对装料设备和炉顶金属结构的维护还带来好处。
此外,煤气温度降低,体积减小,流速也因之降低,炉尘吹出量随之减少。
在实际生产中,往往因炉顶温度过高,而向炉料或炉喉内打水以降低煤气温度。
二、碳酸盐分解炉料中碳酸盐主要来自石灰石(CaC03)、白云石(MgC03),有时也来自碳酸铁(FeCO3)或碳酸锰(MnCO3)。
1.碳酸盐的分解当炉料加热时,碳酸盐按FeCO3、MnC03、MgCO3、CaCO3的顺序依次分解。
碳酸盐分解反应通式可写成:MeCO3 = MeO十CO2一Q反应式中Me代表Ca、Mg、Fe及Mn等元素。
碳酸盐的分解反应是可逆的,随温度升高,其分解压力升高,即有利于碳酸盐的分解。
高炉冶炼最常见的碳酸盐是作为熔剂用的石灰石。
石灰石的分解反应为:CaC03=CaO十CO2—42500×4.1868kJ反应发生的条件是:当碳酸钙的分解压力(C02分压)PCO2大于气氛中C02的分压PCO2时,该反应才进行。
CaCO3在高炉内的分解温度与炉内总压力和煤气中C02分压有关。
据测定表明,石灰石在高炉内加热到700~800℃开始分解,900~1000℃达到化学沸腾。
石灰石的分解速度和它的粒度有很大关系。
因为CaCO3的分解是由表及里,分解一定时间后,在表面形成一层石灰(CaO)层,妨害继续分解生成的C02穿过石灰层向外扩散,从而影响分解速度。
当大粒度分成若干小块时,比表面积增加,在相同条件下,分解生成的石灰量增多,未分解部分减少,粉状的石灰石在900℃左右即可分解完毕,而块状的要在更高的温度下才能完全分解。
粒度愈大,分解结束的温度愈高。
此外CaO层的导热性差,内部温度要比表面温度低;粒度愈大,温差愈大。
因此,石灰石因块度的影响,分解完成一直要到高温区域。
2.碳酸盐分解对高炉冶炼的影响及其对策碳酸盐在高炉内若能在较高部位分解,它仅仅消耗高炉上部多余的热量,但如前述CaCO3若在高温区分解,必然影响到燃料的过多消耗。
其影响可按以下分析进行估量:(1)CaCO3分解是吸热反应,1kg CaCO3分解吸热425×4.1868kJ,或者每分解出1kgC02吸热956×4.1868kJ。
(2) CaCO3在高温区分解出的C02,一般有50%以上与焦炭中的C发生气化(溶损)反应:C02十C=2CO一39600×4.1868kJ/kg分子反应既消耗C又消耗热量。
因耗C而减少了风口前燃烧的C量,(两者在数量上是相当的)即减少了C燃烧的热量:C十1/202=CO十29970x4.1868U/kg分子两项热量之和为69570×4.1868kJ/kg分子,(3)CaCO3分解出的CO2冲淡还原气氛,影响还原效果。
综上分析,CaCO3分解造成热能损失,又影响还原和焦炭强度。
据理论计算以及实践经验表明,每增加100KG石灰石,多消耗焦炭30KG左右。
为消除石灰石作熔剂的不良影响,可采取以下措施:a、生产自熔性(特别是熔剂性)烧结矿,使高炉少加或不加熔剂,实现熔剂搬家;b、缩小石灰石粒度,改善石灰石炉内分解条件,使入炉熔剂尽可能在高炉内较高部位完成分解;c、使用生石灰代替石灰石作熔剂.第二节铁氧化物还原的热力学分析高炉炼铁的主要目的,即是将铁矿石中铁和一些有用元素还原出来,所以还原过程是高炉冶炼最基本的物理化学反应。
一、铁氧化物还原条件在铁矿石中,主要是含铁氧化物,也有少量非铁氧化物——如硅、锰等氧化物。
在高炉冶炼中,铁几乎能全部被还原,而硅、锰只能部分被还原,这主要决定于还原反应的平衡状态,即热力学条件;也受达到平衡状态难易程度的影响,即动力学条件。
所谓还原反应,是指利用还原剂夺取金属氧化物中的氧,使之变为金属或该金属的低价氧化物的反应。
还原反应可表示为:MeO十B=Me十BO反应得以进行,必须是还原剂B和氧的化学亲和力,大于金属Me和氧的化学亲和力。
衡量金属或非金属与氧亲和力大小的尺度,可用元素与氧生成化合物时,系统中自由能△Z变化的大小来区别。
如△Z负的绝对值越大,即自由能减少越多,该化合物越稳定。
自由能随温度不同而变化,如图,可看出各种氧化物的生成自由能与温度的关系。
在一定温度下,各种氧化物都有一定的生成自由能,其值愈小(即负的绝对值愈大),该氧化物中的金属和氧的亲和力愈大.此金属愈难还原;相反,氧化物的生成自由能愈大,该氧化物中的金属和氧的亲和力愈小,此金属则易还原。
依此,Cu、Ni比 Fe容易还原,而Mn、Si比Fe则难还原。
同时,与氧亲和力大的金属,可以作为还原剂,还原与氧亲和力小的金属氧化物。
例如Al就可作为还原剂还原Ti;而且生成自由能越小的氧化物中的金属,作为还原剂时其还原能力越强。
随着温度的升高,各种氧化物的生成自由能变大,即各种元素与氧的亲和力变小,则有利于元素的还原。
高炉冶炼主要是以CO和C作为还原剂,还原区域的温度一般不大于1500℃,在此条件下,CaO、A1203和MgO在高炉冶炼过程中不可能被还原。
氧化物中的金属(或非金属)和氧亲和力的大小,也可用氧化物的分解压力大小来表示,即氧化物的分解压力越小,元素和氧的亲和力越大,该氧化物越稳定。
高炉内常见氧化物的分解压力如图所示。
由图可知,铁氧化物的分解压力比其它一些氧化物大,FeO 即比MnO 和Si02易于还原。
铁的高价氧化物分解压力更大,如Fe 203在1375℃时的分解压力为0.02lMPa ,在此温度下。
即使无还原剂,Fe203也能热分解,生成Fe 3O 4;而Fe 3O 4与FeO 的分解压力比Fe 203小得多,FeO 要达到 3487℃时才能分解,高炉内达不到这样高的温度,因此在高炉内不能靠加热分解以获得铁的低价氧化物直至金属铁,而需借助还原剂还原。
二、铁氧化物还原顺序铁的氧化物主要以三种形态存在:Fe 2O 3(赤铁矿)、Fe 3O 4(磁铁矿)、FeO (浮士体)。
还原顺序是从高价铁氧化物逐级还原成低价铁氧化物,最后获得金属铁。
其还原顺序为:Fe 2O 3——Fe 3O4——FeO ——Fe由于FeO 在低于570 ℃时是不稳定的,所以还原情况是: 当温度大于570 ℃时:Fe 2O 3——Fe 3O 4——FeO ——Fe 当温度低于570 ℃时:Fe 2O 3——Fe 3O 4——Fe三、铁氧化物的还原反应 1.用CO 还原铁氧化物(1)反应特点。
在实际生产中,CO 能还原铁的各级氧化物。
当温度大于570℃时,还原反应为:3Fe203十CO=2Fe3O4十CO2十8870×4.1868kJ (1)2Fe304十CO=3FeO十C02—4990×4.1868kJ (2)FeO十CO=Fe十CO2十3250×4.1868kJ (3)在温度小于570℃时,由于FeO不能稳定存在,Fe304将被CO还原成金属铁,故反应为:3Fe203十CO = 2Fe34十C02十8870×4.1868KJFe304十CO=3Fe十4C02十4100×4.1868kJ (4)上述诸反应的特点是:(1)从Fe2O3还原成Fe,除反应(2)为吸热反应外,其余反应均为放热反应;(2)Fe2O3分解压力较大,可以被CO全部还原成Fe3O4;(3)除从Fe2O3还原成Fe3O4的反应为不可逆外,其余反应都是可逆的,反应进行的方向取决于气相反应物和生成物的浓度。
反应在一定温度下达到平衡,其平衡常数KP 为:Kp=PCO2/PCO= (%CO2)/(%CO)由于(%C02)十(%CO)=100%所以(%CO)=100/(1+Kp)=f(T)按Kp与温度关系,上述各还原反应的平衡常数为:反应(1):lgKp=2726/T十2.144 (5)反应(2):lgKp=1645/T十1.935 (6)反应(3):lgKp=429/T—1.140 (7)反应(4):lgKp=2462/T—0.997 (8)由(5)、(6)、(7)、(8)式,可计算出反应(1)至(4)的平衡常数。
据此便能算出各反应平衡气相中CO的浓度。
由于各反应的Kp不同,因而平衡气相中%CO也不相同。
(2)温度对反应的影响。
各级铁氧化物在不同温度下,其平衡气相成分是不相同的。
将各种温度下的平衡常数代入(%CO)=100/(1+Kp)=f(T) ,便可以计算出各个反应在不同温度下的CO%,则可作出CO%—t曲线图。
曲线1、2、3、4,分别为反应(1)、(2)、(3)和(4)的平衡气相成分曲线。
在570℃时,曲线2、3和4相交于一点。
曲线将平衡图分成四个区域,即Fe、FeO、Fe3O4和Fe2O3的稳定区。
在曲线1以下为Fe2O3稳定区;曲线1、2和4之间为Fe3O4稳定区;曲线2和3之间为FeO稳定区;曲线3和4之上为Fe的稳定区。
不在曲线上的点,表明体系处在非平衡状态,并且反应将向着该区域内稳定存在的物质方向转化。
例如,将Fe放在曲线2和3之间,在>570℃的任一温度下,气相组成中C02含量均大于曲线3上平衡气相中的C02含量,或者说气相组成CO含量均小于平衡曲线3上的CO含量,所以反应(3)将向左进行,最终Fe会被氧化成FeO。
从图也可看出,曲线1、3、4向右上方倾斜,曲线2向下斜,表明前者为放热反应,后者为吸热反应。
同时FeO十CO=Fe十C02反应的平衡曲线位置最高,说明它达到平衡需要的CO%量最大,所以FeO最难还原。
例如900℃时,用C060%,C0240%的煤气不可能将FeO还原成Fe,但这一组成的煤气完全可以将Fe304还原成FeO。
煤气上升过程中,CO将首先在高炉中下部把FeO还原成Fe,剩余的CO在继续上升时,再将Fe04还原成FeO,最后将Fe23还原成Fe3O4,煤气的化学能得到很好利用。
衡量高炉内CO利用程度的指标为CO利用率,即高炉内参加间接还原反应的CO与炉内CO总量之比值。
一般表示为:ηCO =CO2/(CO2+C)×100%式中C02、CO——分别为高炉炉顶煤气中CO2和CO的百分含量。
(3)碳的气化反应及其对还原的影响在高炉内进行上述各级铁氧化物的还原反应,是在有碳素存在的情况下进行的。
而碳素在较高温度下将发生气化反应(又称贝一波反应,溶损反应,C02的还原反应):C02十C=2CO—39500×4.1868kJ/kg分子将C的气化反应在不同温度下达到平衡时的气相组成,和CO%—t平衡图绘于同一图上,可得出铁氧化物、碳氧化物和碳的平衡与温度关系图。