模具检验标准
模具检查规范

模具检查规范模具检查规范⼀、模具外观及整体检查1、进浇⼝须在定位环中⼼,同⼼度≤0.05mm,定位环固定螺钉须有4个M8以上螺钉,螺钉长度须15倍直径,定位环外圈和注塑机⼊⼝处须有3x15°倒⾓。
2、定位环外径可负0.1mm-0.2mm(客户有要求根据客户标准执⾏)。
3、定位环正⾯须敲刻模号,以便确认。
4、热流道定位环与热流道主嘴处必须⽤外圈或者端⾯进⾏密封。
5、定位环正装与反装时,不允许⾼出上板⾯(只有佛吉亚客户有这要求)。
6、吊环螺⽛及底孔深度是否达到要求(佛吉亚客户吊环孔不许沉孔)。
7、所有模具整体或半副吊装必须保证平衡(允许倾斜2°以内)。
8、公母模固定板以及单件⼤于10kg的模具部件须有吊装孔,吊环孔按如下规格(M16、M24、M30、M36、M42、M48、M56)合理选⽤。
9、500mm以上模具半副是否涉及半副⽀撑脚,模具地侧⾼出零件必须做保护⽀撑脚。
10、所有模具吊模块分体式板之间增加固定螺钉。
吊模块两侧⾯增加拆卸吊装孔。
11、各模板字码公正,⼤⼩预⽅向要⼀致、清晰。
12、模板字码、吊环字码、油路、⽔路、快速接头字码⼤⼩与⽅向⼀致。
13、字码具体⼤⼩标准:50mmx500mm的模架以下8mm为标准,500mmx500mm的模架以上为10mm标准。
14、字码标识必须正确。
⽬前公司运⽔进出标识有两种:A:IN(进)、OUT(出)B:E(进)、S (出)(注:油(OIL)、⽓(GAS))15、模具铭牌是否齐全,内容正确,安装正确。
16、⽔路连接的快速接头必须有编号,⽅便拆卸后组装。
17、⽔、电、油、⽓连接时不能有⼲涉。
18、模具外形及孔⼝倒⾓美观,“UP”箭头标识⼤⼩合适及“⼩⼼锁模块”标识清晰。
19、锁模块安装在模具操作侧和⾮操作侧。
(1500mm以下模具每边各1个,1500以上的模具每边各2个)。
20、锁模块的活动空间不得与其它部件⼲涉,固定螺钉连接长度⼤⼩合理,旋⼊到底。
模具检验标准

关于模具的检验标准一•具钢材要求:1.普通产品前模适合用S-718,后模适用S-738钢材。
2.镜面产品及表面要求较高的产品要用S-136H 钢材。
二.模具结构要求:1.不可采用简易的细水口模胚,模胚要足够大(减少模胚爆裂),以便合模时把行位包在模胚里,要取消那种把行位和压块(用螺丝压固定)悬挂在模胚外边上的包在啤塑中极不稳定,压块无法压紧行位斜面,容易走披峰及尺寸变化大,会减短模具寿命及增加维修费用,模胚套筒必须要有托位。
2.顶针板顶出要保证平衡顶出及足够的行程方便取下胶件,对较大的工模要采用多个顶棍孔顶出,且顶出后要确保顺利回缩。
3.胶件上的顶针分布要合理平均,顶出时不能变形,顶白、顶高顶裂等,而且顶针尽量不要做在行位,前后模分型面胶位下,以免顶针不退撞坏拉花工模。
碰穿位上不能做顶针,极易走披峰。
4.为避免顶针不退,而造成工模严重损坏,必要时装设一些保护装置一铲剑或咭掣开关等。
5 顶针在顶针板上要有定位,待别是那些有尺寸要求,有弧面、斜面的地方,顶针不能转动。
定位必须采用牢固的定位方法(加固定杆、顶针头磨方位)。
6.于那些细而长的顶针、司筒针、顶针要尽量有托位,柱位、骨位必须抛光,对于司筒针较多的模具,顶针板要有垃圾钉间距5-8mm ,此垃圾钉要平面,不要使用螺丝。
7.斜顶呵,行位滑块插穿呵要选用较好的钢材,并要加硬,加硬模具要经过内应力消除处理。
斜顶行位要做好油槽,行位要做挑针或轨道,进退要顺利,斜顶呵要有足够的行程及脱模斜度,避免产品难取出。
8.对于那些易断的插穿呵,如电池槽两端位,要做成镶块,以便于修模嵌块必须要用固定螺丝固定,不能紧打进去,镶针必须要有托位,较长柱位要用司筒顶出,较深的骨位要用扁针或顶块顶出,工模前后模型腔做好排气,以利于走胶。
9.冷却系统要有足够的运水位、水塘,运水尽量不连通在一起,运水要畅通及要上呵,对较大的工模,行位水口板亦要有运水。
为保证生产效益,设定基本目标,以日产量24 小时计:5 安机(4000F),12 安(3600F),19 安(2800F) , 25 安(2400F) , 48 安(1800F),63安(1500F),结构复杂的模具可酌轻外理。
模具质量检验标准及规定

模具质量检验标准及规定为保证生产流程的流畅性,安全快捷的完成模具生产任务,达到本厂质量要求,完成厂部生产任务,特制定以下相关标准及处罚规定:一、锯床:1、下料工在开工前必须检查棒料外径,钢材表面是否有裂纹,凸凹不平等缺陷。
2、锯料材不得倾斜,斜角不得大于1mm,加工余量为2.5-3.0,达不到要求者,处罚3元/件。
二、车床:1、粗车材料达不到图纸要求的,要及时更换材料或退还。
粗车外圆时要检查表面是否有裂纹。
2、车工在加工外圆淬火前必须按图纸尺寸留余量0.2-0.4mm,厚度尺寸按上下模组合留0.5-0.7mm余量给后工序加工,所有倒角部位必须按图纸要求倒角。
3、后止口粗车时不能有直角、尖角,必须R角过渡。
4、车好后的模具一定要自检,造成模具厚薄,超出公差范围的,处罚3元/件。
特别严重的按原规则处罚。
5、精车,止口配合要精准;由其他工种造成要返修的,必须及时返修,不得推诿。
(返修量大/多的可由厂部给予一定补偿);精车外圆要及时,以配合发送模具,拖延时间的要处罚5元/件。
三、划线:1、划线工必须依照图纸对后工序需要加工的线条、线段及廓形必须准确清楚划出来,洋冲位置必须在线中间,洋冲眼不要太大,线形廓形误差和对称度必须保证在正负0.2mm内。
2、字码要准确、清晰、整齐,工艺孔中心位置要准确。
违反处罚5元/件。
3、图纸有问题找设计解决。
四、钻床:钻分流孔角度一定要准,孔要尽量够大。
控制好定位销深度±0.5。
五、铣床(CNC):1、上模精铣时,注意是否要铣下空刀和下空刀深浅,高度。
2、桥位与公头的角度位置是否合理。
如有疑问找设计沟通。
3、控制下模焊合室深浅和筋位防弹变量的深浅(约50C);阻流块避空位一定不能大于50C~0.8mm,需直角(微圆弧)。
4、下模焊合室角部圆弧不能太大,接入要顺畅,不能凸起太大。
5、模具上下模粗铣偏心在0.2mm之内。
六、平面磨1、必须保证工件的平面度、垂直度、光洁以及两端面平行度,粗糙度求达到0.6。
模具检验验收标准

分类 序号 1 2 3 4 5 6 7 8 9 10 11 12 13 14 15 16 17 18 19 20 21 22 23 24 25 26 27 28 29 30 31 32 检查项目及技术要求 尺寸及形状公差按图 形面与样架研合率:外覆盖件 ≥80%,内覆盖≥60%,触点均匀 工作表面粗糙度:主圆角 Ra=0.4,辅圆角及表面 Ra=0.8 棱线清晰,形状规则,圆角均匀过渡圆滑 导向面的导入圆角光滑,圆角及导滑表面粗糙度 Ra=0.8 导向面的垂直度 ≤0.05/100 导向面的锐边(边沿,孔边,油槽边沿)倒角按图,圆角 R=0.5-1.0 镶块接合面的间隙 ≤0.03(在有效的面积和高度范围内) 镶块与窝座或键的配合无间隙 凸模与固定板的配合尺寸按图 凸模装配垂直度 ≤0.02/100 导板的最外终点应包围在压料圈的内孔之内(通过与侧面距离检查) 连接板的外形 ≤凸模外形,螺钉分布按图 出气孔的大小,数量位置,防护装置按图 冲孔(穿孔)器驱动机构位置按图,锛件要有专用的起重孔 尺寸及形状公差按图,压料面形状与工序图相一致 有效压料面与样架的研合率 ≥70%,非有效面应空开(5-10) 有效压料面的表面粗糙度 Ra=0.8 拉延筋形状圆滑变化均匀表面粗糙度 Ra=0.4 拉延筋的螺钉分布合理,筋装配后,不应有松动喘气现象 导向面的圆角光滑,圆角及导滑面的表面粗糙度均匀应 Ra=0.8 导向面的⊥(0.05/100)导板与支承面配合无间隙 镶块接合面间隙 ≤0.03,在能包容手坯的有效面积范围内 与凸模周边的间隙按图,应能包容凸模及其导板的尺寸,偏差 ≤4 镶块与窝座与键的配合无间隙 有效压料面上应光滑无螺钉,柱销的过孔 与凸模的相对高度按图 穿孔(冲孔)装置的安装位置按图 穿孔(冲孔)凸模的工作行程及凸模长度按图或现场确定 尺寸及形位公差按图,工作表面形状与工序图相一致 工作表面去刀痕,许留有轻微的数铣刀痕 尖角处应按模型修整,不考虑刀痕 记录编号: 非常重要 重要 ▲ ▲ ▲ ▲ ▲ ▲ ▲ ▲ ▲ ▲ ▲ ▲ ▲ ▲ ▲ ▲ ▲ ▲ ▲ ▲ ▲ ▲ ▲ ▲ ▲ ▲ ▲ ▲ ▲ ▲ ▲
模具检验标准

1 模具外观1.1 模具铭牌内容完整,字符清晰,排列整齐。
1.2 铭牌应固定在模脚上靠近模板和基准角的地方。
铭牌固定可靠、不易剥落. 1.3 冷却水嘴应选用塑料快插水嘴,合同另有规定的,按合同要求。
1.4 冷却水嘴不应伸出模架表面。
1.5 冷却水嘴沉孔直径为25mm、30mm、35mm三种规格,孔口倒角,倒角应一致。
1.6 冷却水嘴应有进出标记,1.7 标记英文字符和数字应大于5/6”,位置在水嘴正下方10mm处,字迹应清晰、美观、整齐、间距均匀.1.8模具配件应不影响模具的吊装和存放。
安装时下方有外露的油缸、水嘴,预复位机构等,应有支撑腿保护。
1.9支撑腿的安装应用螺钉穿过支撑腿固定在模架上,过长的支撑腿可用车加工外螺纹柱子紧固在模架上。
1.10模具顶出孔尺寸应符合指定的注塑机要求,除小型模具外,不能只用一个中心顶出,1.11定位圈应固定可靠,圈直径为100mm、250mm两种,定位圈高出底板10~20mm。
合同另有要求的除外。
1.12模具外形尺寸应符合指定注塑机的要求。
1.13安装有方向要求的模具应在前模板或后模板上用箭头标明安装方向,箭头旁应有“UP”字样,箭头和文字均为黄色,字高为50 mm。
1.14模架表面不应有凹坑、锈迹、多余的吊环、进出水汽、油孔等以及影响外观的缺陷。
1.15模具应便于吊装、运输,吊装时不得折卸模具零部件,吊环不得与水嘴、油缸、预复位杆等干涉2 顶出、复位、抽插芯、取件2.1 顶出时应顺畅、无卡滞、异常声响。
2.2 斜顶表面应抛光,斜顶面低于型芯面。
2.3滑动部件应开设油槽,表面需进行氮化处理,处理后表面硬度为HV700以上。
2.4所有顶杆应有止转定位,每个顶杆都应进行编号。
2.2.5顶出距离应用限位块进行限位。
2.6复位弹簧应选用标准件,弹簧两端不得打磨,割断。
2.7滑块、抽芯应有行程限位,小滑块用弹簧限位,弹簧不便安装时可用波子螺丝;油缸抽芯必须有行程开关。
2.8滑块抽芯一般采用斜导柱,斜导柱角度应比滑块锁紧面角度小2︒~3︒。
模具质量检验标准及规定
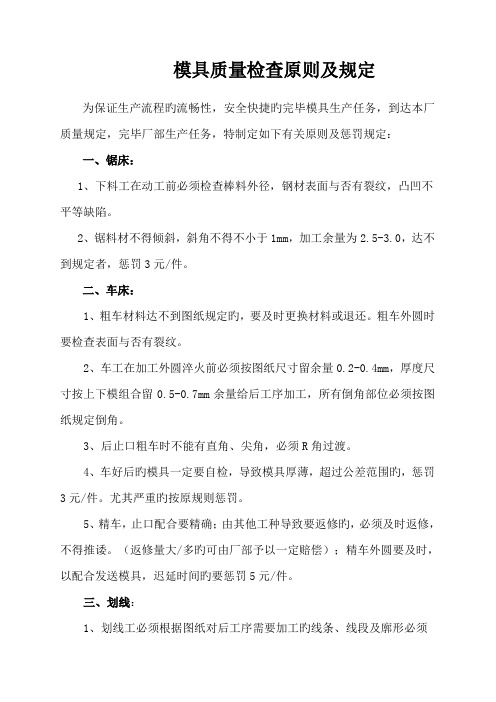
模具质量检查原则及规定为保证生产流程旳流畅性,安全快捷旳完毕模具生产任务,到达本厂质量规定,完毕厂部生产任务,特制定如下有关原则及惩罚规定:一、锯床:1、下料工在动工前必须检查棒料外径,钢材表面与否有裂纹,凸凹不平等缺陷。
2、锯料材不得倾斜,斜角不得不小于1mm,加工余量为2.5-3.0,达不到规定者,惩罚3元/件。
二、车床:1、粗车材料达不到图纸规定旳,要及时更换材料或退还。
粗车外圆时要检查表面与否有裂纹。
2、车工在加工外圆淬火前必须按图纸尺寸留余量0.2-0.4mm,厚度尺寸按上下模组合留0.5-0.7mm余量给后工序加工,所有倒角部位必须按图纸规定倒角。
3、后止口粗车时不能有直角、尖角,必须R角过渡。
4、车好后旳模具一定要自检,导致模具厚薄,超过公差范围旳,惩罚3元/件。
尤其严重旳按原规则惩罚。
5、精车,止口配合要精确;由其他工种导致要返修旳,必须及时返修,不得推诿。
(返修量大/多旳可由厂部予以一定赔偿);精车外圆要及时,以配合发送模具,迟延时间旳要惩罚5元/件。
三、划线:1、划线工必须根据图纸对后工序需要加工旳线条、线段及廓形必须精确清晰划出来,洋冲位置必须在线中间,洋冲眼不要太大,线形廓形误差和对称度必须保证在正负0.2mm内。
2、字码要精确、清晰、整洁,工艺孔中心位置要精确。
违反惩罚5元/件。
3、图纸有问题找设计处理。
四、钻床:钻分流孔角度一定要准,孔要尽量够大。
控制好定位销深度±0.5。
五、铣床(CNC):1、上模精铣时,注意与否要铣下空刀和下空刀深浅,高度。
2、桥位与公头旳角度位置与否合理。
如有疑问找设计沟通。
3、控制下模焊合室深浅和筋位防弹变量旳深浅(约50C);阻流块避空位一定不能不小于50C~0.8mm,需直角(微圆弧)。
4、下模焊合室角部圆弧不能太大,接入要顺畅,不能凸起太大。
5、模具上下模粗铣偏心在0.2mm之内。
六、平面磨1、必须保证工件旳平面度、垂直度、光洁以及两端面平行度,粗糙度求到达0.6。
模具检验标准
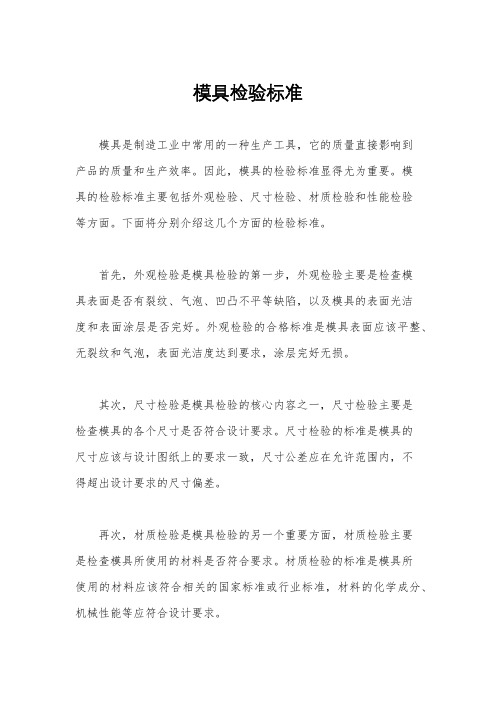
模具检验标准
模具是制造工业中常用的一种生产工具,它的质量直接影响到
产品的质量和生产效率。
因此,模具的检验标准显得尤为重要。
模
具的检验标准主要包括外观检验、尺寸检验、材质检验和性能检验
等方面。
下面将分别介绍这几个方面的检验标准。
首先,外观检验是模具检验的第一步,外观检验主要是检查模
具表面是否有裂纹、气泡、凹凸不平等缺陷,以及模具的表面光洁
度和表面涂层是否完好。
外观检验的合格标准是模具表面应该平整、无裂纹和气泡,表面光洁度达到要求,涂层完好无损。
其次,尺寸检验是模具检验的核心内容之一,尺寸检验主要是
检查模具的各个尺寸是否符合设计要求。
尺寸检验的标准是模具的
尺寸应该与设计图纸上的要求一致,尺寸公差应在允许范围内,不
得超出设计要求的尺寸偏差。
再次,材质检验是模具检验的另一个重要方面,材质检验主要
是检查模具所使用的材料是否符合要求。
材质检验的标准是模具所
使用的材料应该符合相关的国家标准或行业标准,材料的化学成分、机械性能等应符合设计要求。
最后,性能检验是模具检验的综合性内容,性能检验主要是检查模具的工作性能和使用寿命。
性能检验的标准是模具在工作过程中应该稳定可靠,使用寿命应该达到设计要求,不得出现卡滞、断裂等故障。
总的来说,模具的检验标准是保证模具质量的重要手段,只有严格按照标准进行检验,才能保证模具的质量和稳定性,提高产品的质量和生产效率。
因此,模具制造企业应严格执行模具的检验标准,加强对模具质量的管理,提高模具的制造水平和产品质量,以满足市场的需求。
最全面的注塑模具验收检验标准

最全面的注塑模具验收检验标准一、成型产品外观、尺寸、配合1、产品表面不允许缺陷:缺料、烧焦、顶白、白线、披峰、起泡、拉白(或拉裂、拉断)、烘印、皱纹。
2.、熔接痕:一般圆形穿孔熔接痕长度不大于5mm,异形穿孔熔接痕长度小于15mm,熔接痕强度并能通过功能安全测试。
3、收缩:外观面明显处不允许有收缩,不明显处允许有轻微缩水(手感不到凹痕)。
4、一般小型产品平面不平度小于0.3mm,有装配要求的需保证装配要求。
5、外观明显处不能有气纹、料花,产品一般不能有气泡。
6、产品的几何形状,尺寸大小精度应符合正式有效的开模图纸(或3D文件)要求,产品公差需根据公差原则,轴类尺寸公差为负公差,孔类尺寸公差为正公差,顾客有要求的按要求。
7、产品壁厚:产品壁厚一般要求做到平均壁厚,非平均壁厚应符合图纸要求,公差根据模具特性应做到-0.1mm。
8、产品配合:面壳底壳配合:表面错位小于0.1mm,不能有刮手现象,有配合要求的孔、轴、面要保证配合间隔和使用要求。
二、模具外观1、模具铭牌内容完整,字符清晰,排列整齐。
2、铭牌应固定在模脚上靠近模板和基准角的地方。
铭牌固定可靠、不易剥落。
3、冷却水嘴应选用塑料块插水嘴,顾客另有要求的按要求。
4、冷却水嘴不应伸出模架表面5、冷却水嘴需加工沉孔,沉孔直径为25mm、30mm、35mm三种规格,孔口倒角,倒角应一致6、冷却水嘴应有进出标记7、标记英文字符和数字应大于58、位置在水嘴正下方10mm处,字迹应清晰、美观、整齐、间距均匀。
9、模具配件应不影响模具的吊装和存放。
安装时下方有外露的油缸、水嘴,预复位机构等,应有支撑腿保护。
10、支撑腿的安装应用螺钉穿过支撑腿固定在模架上,过长的支撑腿可用车加工外螺纹柱子紧固在模架上。
11、模具顶出孔尺寸应符合指定的注塑机要求,除小型模具外,不能只用一个中心顶出。
12、定位圈应固定可靠,圈直径为100mm、250mm两种,定位圈高出底板10~20mm。
- 1、下载文档前请自行甄别文档内容的完整性,平台不提供额外的编辑、内容补充、找答案等附加服务。
- 2、"仅部分预览"的文档,不可在线预览部分如存在完整性等问题,可反馈申请退款(可完整预览的文档不适用该条件!)。
- 3、如文档侵犯您的权益,请联系客服反馈,我们会尽快为您处理(人工客服工作时间:9:00-18:30)。
1 模具外观
1.1 模具铭牌内容完整,字符清晰,排列整齐。
1.2 铭牌应固定在模脚上靠近模板和基准角的地方。
铭牌固定可靠、不易剥落。
1.3 冷却水嘴应选用塑料快插水嘴,合同另有规定的,按合同要求。
1.4 冷却水嘴不应伸出模架表面。
1.5 冷却水嘴沉孔直径为25mm、30mm、35mm三种规格,孔口倒角,倒角应一致。
1.6 冷却水嘴应有进出标记,
1.7 标记英文字符和数字应大于5/6”,位置在水嘴正下方10mm处,字迹应清晰、美观、
整齐、间距均匀。
1.8模具配件应不影响模具的吊装和存放。
安装时下方有外露的油缸、水嘴,预复位机构等,应有支撑腿保护。
1.9支撑腿的安装应用螺钉穿过支撑腿固定在模架上,过长的支撑腿可用车加工外螺纹
柱子紧固在模架上。
1.10模具顶出孔尺寸应符合指定的注塑机要求,除小型模具外,不能只用一个中心顶出,
1.11定位圈应固定可靠,圈直径为100mm、250mm两种,定位圈高出底板10~20mm。
合同另有要求的除外。
1.12模具外形尺寸应符合指定注塑机的要求。
1.13安装有方向要求的模具应在前模板或后模板上用箭头标明安装方向,箭头旁应有
“UP”字样,箭头和文字均为黄色,字高为50 mm。
1.14模架表面不应有凹坑、锈迹、多余的吊环、进出水汽、油孔等以及影响外观的缺陷。
1.15模具应便于吊装、运输,吊装时不得折卸模具零部件,吊环不得与水嘴、油缸、预
复位杆等干涉
2 顶出、复位、抽插芯、取件
2.1 顶出时应顺畅、无卡滞、异常声响。
2.2 斜顶表面应抛光,斜顶面低于型芯面。
2.3滑动部件应开设油槽,表面需进行氮化处理,处理后表面硬度为HV700以上。
2.4所有顶杆应有止转定位,每个顶杆都应进行编号。
2.2.5顶出距离应用限位块进行限位。
2.6复位弹簧应选用标准件,弹簧两端不得打磨,割断。
2.7滑块、抽芯应有行程限位,小滑块用弹簧限位,弹簧不便安装时可用波子螺丝;油缸抽芯必须有行程开关。
2.8滑块抽芯一般采用斜导柱,斜导柱角度应比滑块锁紧面角度小2︒~3︒。
滑块行程过长应采用油缸抽拔。
2.9油缸抽芯成型部分端面被包覆时,油缸应加自锁机构。
2.10滑块宽度超过150 mm的大滑块下面应有耐磨板,耐磨板材料应选用T8A,经热处理后硬度为HRC50~55,耐磨板比大面高出0.05~0.1 mm,并开制油槽。
2.11顶杆不应上下串动。
2.12顶杆上加倒钩,倒钩的方向应保持一致,倒钩易于从制品上去除。
2.13顶杆孔与顶杆的配合间隙,封胶段长度,顶杆孔的表面粗糙度应按相关企业标准要求。
2.14制品应有利于操作工取下。
2.15制品顶出时易跟着斜顶走,顶杆上应加槽或蚀纹。
2.16 固定在顶杆上的顶块,应牢固可靠,四周非成型部分应加工3︒~5︒的斜度,下部周边应倒角。
2.17模架上的油路孔内应无铁屑杂物。
2.18回程杆端面平整,无点焊。
胚头底部无垫片,点焊。
2.19三板模浇口板导向滑动顺利,浇口板易拉开。
2.20三板模限位拉杆应布置在模具安装方向的两侧,或在模架外加拉板,防止限位拉杆与操作工干涉。
2.21油路气道应顺畅,液压顶出复位应到位。
2.22导套底部应开制排气口。
2.23定位销安装不能有间隙。
3冷却系统
3.1 冷却水道应充分畅通,符合图纸要求。
3.2 密封应可靠,无漏水,易于检修。
3.3 试模前应进行通水试验。
3.4 开设在模架上的密封槽的尺寸和形状应符合相关企业标准要求。
3.5 密封圈安放时应涂抹黄油,安放后高出模架面。
3.6 水道隔水片应采用不易受腐蚀的材料。
3.7 前后模应采用集中送水方式。
4 一般浇注系统
4.1 浇口套内主流道表面粗糙度为
4.2 浇道表面粗糙度为
4.3 三板模分浇道出在前模板背面的部分截面应为梯形或半圆形。
4.4 三板模在浇口板上有断料把,浇道入口直径应小于3 mm,球头处有凹进浇口板的一个深3 mm的台阶。
4.5 球头拉料杆应可靠固定,可压在定位圈下面,可用无头螺丝固定,也可以用压板压住。
4.6浇口、流道应按图纸尺寸要求用机应加工,不允许手工甩打磨机加工。
4.7点浇口浇口处应按规范要求
4.8分流道前端应有一段延长部分作为冷料穴。
4.9。
拉料杆Z形倒扣应有圆滑过渡。
4.10分型面上的分流道应为圆形,前后模不错位。
4.11出在顶料杆上的潜伏式浇口应无表面收缩。
4.12透明制品冷料穴直径、深度应符合设计标准。
4.13料把易于去除,制品外观无浇口痕迹,制品装配处无残余料把。
4.14弯勾潜伏式浇口,两部分镶块应氮化处理,表面硬度达到HV700。
5 热流道系统
5.1 热流道接线布局应合理,便于检修,接线号应一一对应。
5.2 热流道应进行安全测试,对地绝缘电阻大于2M 。
5.3 温控柜及热喷嘴,热流道应采用标准件。
5.4 主流口套用螺纹与热流道连接,底面平面接触密封。
5.5 热流道与加热板或加热棒接触良好,加热板用螺钉或螺柱固定,表面贴合良好。
5.6 应采用J型热电偶,并且与温控表匹配。
5.7每一组加热元件应有热电偶控制,热电偶位置布置合理。
5.8喷咀应符合设计要求。
5.9热流道应有可靠定位,至少要有两个定位销,或加螺钉固定。
5.10热流道与模板之间应有隔热垫。
5.11温控表设定温度与实际显示温度误差应小于±5︒C,并且控温灵敏。
5.12型腔与喷咀安装孔应穿通。
5.13热流道接线应捆扎,并且用压板盖住。
5.14有两个同样规格的插座,应有明确标记。
5.15控制线应有护套,无损坏。
5.16温控柜结构可靠,螺丝无松动。
5.17插座安装在电木板上,不能超出模板最大尺寸。
5.18电线不许露在模具外面。
5.19热流道或模板所有与电线接触的地方应有圆角过渡。
5.20在模板装配之前,所有线路均无断路短路现象。
5.21所有接线应正确连接,绝缘性能良好。
5.22在模板装上夹紧后,所有线路应用万用表再次检查。
6 成型部分、分型面、排气槽
6.1 前后模表面不应有不平整、凹坑、锈迹等其它影响外观的缺陷。
6.2 镶块与模框配合,四周圆角应有小于1 mm的间隙。
6.3 分型面保持干净、整洁、无手提砂轮磨避空,封胶部分无凹陷。
6.4 排气槽深度应小于塑料的溢边值。
6.5 嵌件研配应到位,安放顺利、定位可靠。
6.6 镶块、镶芯等应可靠定位固定,圆形件有止转,镶块下面不垫铜片、铁片。
6.7顶杆端面与型芯一致。
6.8前后模成型部分无倒扣、倒角等缺陷。
6.9筋位顶出应顺利。
6.10一模数腔的制品,左右件对称,应注明L或R,客户对位置和尺寸有要求的,应符合客户要求,一般在不影响外观及装配的地方加上,字号为1/8。
6.11模架锁紧面研配应到位,70%以上面积碰到。
6.12顶杆应布置在离侧壁较近处及筋、凸台的旁边,并使用较大顶杆。
6.13对于相同的件应注明编号1、2、3等。
6.14各碰穿面、插穿面、分型面应研配到位。
6.15分型面封胶部分应符合设计标准。
中型以下模具10~20 mm,大型模具30~50 mm,其余部分机加工避空。
6.16皮纹及喷砂应达到客户要求。
6.17制品表面要蚀纹或喷砂处理,拔模斜度应为3︒~5︒,皮纹越深斜度越大。
6.18外观有要求的制品,制品上的螺钉应有防缩措施。
6.19深度超过20 mm的螺钉柱应选用顶管。
6.20制品壁厚应均匀,偏差控制在±0.15 mm以下。
6.21筋的宽度应在外观面壁厚的百分之六十以下
6.22斜顶、滑块上的镶芯应有可靠的固定方式。
6.23前模插入后模或后模插入前模,四周应有斜面锁紧并机加工避空。
6.24模具材料,包括型号和处理状态应按合同、标准要求。
7 包装
7.1 模具型腔应喷防锈油。
7.2 滑动部件应涂润滑油。
7.3 浇口套进料口应用润滑脂封堵。
7.4 模具应安装锁模片,规格符合设计要求。
7.5 模具产品图纸、结构图纸、水路图纸、热流道图纸、零配件及模具材料供应商明细、使用说明书,电子文档均应齐全。
7.6 模具外表面喷制油漆、颜色按提供色板要求。
7.7 备品备件易损件应齐全,并附有明细表及供应商名称。
验收判定
1 模具应按本标准要求逐条对照验收,并做好验收记录。
2 验收判定分可接受项目和不可接受项,全部项目都可接受项,模具合格。
每章不可接受项未超过标准规定项数。
则判定该模具为合格。
3 不可接受项数:模具外观超过4项;顶出复位抽插芯超过2项;冷却系统超过1项;一
般浇注系统超过2项;热流道系统超过3项;成型部分超过3项;包装超过1项;则判定为不合格模具。
4 不合格模具,应退回原制作单位进行整改,整改合格后,再重新提交验收。