汽车前后防撞梁设计地的要求的要求规范
后防撞梁设计总结

1规范性引用文件下列文件中的条款通过本标准的引用而成为本标准的条款。
凡是注日期的引用文件,其随后所有的修改单(不包括勘误的内容)或修订版均不适用于本标准,然而,鼓励根据本标准达成协议的各方研究是否可使用这些文件的最新版本。
凡是不注日期的引用文件,其最新版本适用于本标准。
GB 17354-1998汽车后、后端保护装置QC T 566-1999 轿车的外部防护GB 20072-2006乘用车后碰撞燃油系统安全要求2法规要求根据GB 17354-1998 之规定:装在车辆后后端的诸元件,其设计要求为在发生接触和轻度碰撞时,不会导致车辆的严重损伤根据GB 20072-2006乘用车后碰撞燃油系统安全要求之规定:1.在碰撞过程中,燃油装置不应发生液体泄漏;2.碰撞试验后,燃油装置若有液体连续泄漏,则在碰撞后前5min平均泄漏速率不应大于30g/min;如果从燃油装置中泄漏的液体与从其他系统泄漏的液体混淆且这几种液体不容易分开和辨认,则应根据收集到的所有液体评价连续泄漏量。
3后防撞梁总成功能描述后防撞梁总成要求能在车辆纵向及高度方向支撑汽车后端保护装置,保证汽车后端保护装置的安装牢靠。
能在车辆低速碰撞时连同汽车后端保护装置对车辆的照明和信号装置提供必要的保护;保证后备门(行李舱盖)、车辆的侧门正常的开闭;保证车辆燃料和冷却系统无泄漏、无堵塞,其密封装置与油、水箱口盖能正常开启;车辆的传动、悬架、转向和制动等系统能保持良好的调整状态并正常工作;车辆的排气系统不应该有妨碍其正常工作的损坏或错位。
后防撞梁总成要求在车辆发生中高速碰撞时能吸收部分撞击能量,并将能量平衡传递至车身左右纵梁,保障乘员安全和燃油箱的安全。
后防撞梁总成的最后表面应该能比后围板总成和后备门总成(后行李舱盖总成)更突出,保证车辆碰撞时能适当变形,减少车辆后围板总成(后行李舱盖总成)的维修成本。
4后防撞梁总成的设计4.1后防撞梁总成高度位置确定根据GB 17354-1998中4.3.5规定:碰撞发生时,碰撞器与车辆首先接触的应是撞击头与车辆的保护装置,当车辆分别在整车装备质量与加载试验车质量的状态是,位于车角间的保护装置均能被通过碰撞器基准线的水平面所截。
防撞柱标准规范要求

防撞柱标准规范要求
防撞柱是指用于防止车辆碰撞建筑物或其他设施的保护装置,其设计和安装应
符合一定的标准规范要求,以确保其有效性和安全性。
本文将就防撞柱的标准规范要求进行详细介绍,以便相关从业人员能够更好地理解和遵守相关规定。
首先,防撞柱的材料选择应符合相关标准,一般应选用钢材或混凝土等坚固耐
用的材料,并且应具有一定的抗冲击能力。
其尺寸和形状也需符合规范要求,一般应具有一定的高度和直径,以确保其在车辆碰撞时能够有效地起到保护作用。
其次,防撞柱的安装位置和间距也有一定的规范要求。
一般来说,防撞柱应该
设置在建筑物或设施周围需要保护的区域,如停车场出入口、建筑物立柱等位置。
同时,防撞柱之间的间距也需要根据具体情况进行合理设置,以确保车辆在碰撞时能够被有效地阻止。
此外,防撞柱的标识和警示也是非常重要的。
根据相关规范要求,防撞柱应该
进行明显的标识和警示,以提醒驾驶员注意避让,并避免发生碰撞事故。
标识和警示可以采用明亮的颜色和反光材料制作,以确保在不同光线条件下都能够清晰可见。
最后,防撞柱的设计和制造应符合相关的标准和规范,以确保其质量和安全性。
在制造过程中,需要严格控制材料和加工工艺,确保防撞柱能够承受一定的冲击力而不变形或损坏。
同时,还需要对防撞柱进行定期的检查和维护,以确保其在使用过程中能够始终保持良好的状态。
总之,防撞柱的标准规范要求涉及到材料、尺寸、安装位置、标识警示以及设
计制造等多个方面,相关从业人员应该严格遵守相关规定,确保防撞柱的有效性和安全性。
只有这样,才能更好地保护建筑物和设施,避免因车辆碰撞而造成的损失和伤害。
汽车车门防撞防撞梁设计规范
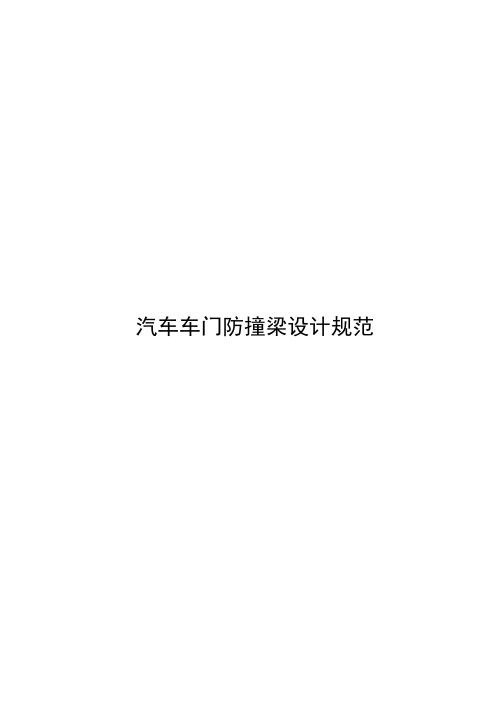
汽车车门防撞梁设计规范汽车车门防撞梁设计规范1 范围本标准规定了汽车车门防撞杆相关设计标准本标准适用于本公司汽车车门防撞杆产品2 规范性引用文件下列文件对于本文件的应用是必不可少的。
凡是注日期的引用文件,仅注日期的版本适用于本文件。
凡是不注日期的引用文件,其最新版本(包括所有的修改单)适用于本文件。
GB/T 10125-1997 人造气氛腐蚀试验盐雾试验GB 20071-2006 汽车侧面碰撞的乘员保护Q/B 05 021-2010 汽车门防撞杆技术规范3 术语和定义3.1防撞梁总成防撞梁总成位于侧门内外板之间,在汽车发生碰撞的时候能够保证车内的生存空间,很好的保证乘员的身体及生命安全。
3.2 MBD可移动可变性障壁3.3 R点车辆制造商规定的基准点,一般式正常行驶时最低、最后位置时,躯干和大腿旋转点的理论位置,或由车辆制造商对于每个乘坐位置给定的位置4 技术要求4.1安全性能要求碰撞过程中起到力的传递及抗冲击作用,减小碰撞过程中变形量,保护乘员生命安全,安全性能方面的要求符合《GB 20071-2006 汽车侧面碰撞的乘员保护》规定的相关要求;4.3 适应于外部环境要求标准数值/ 参考资料耐水性能车辆经过淋雨和涉水行驶后,产品仍然应该保持符合技术任务书要求。
耐腐蚀性能车门侧面防撞加强板应该经受以下试验:程序:按照GB/T 10125-1997的盐雾试验方法进行测试要求的结果:在试验之后, 在公差范围限度内,所有侧面防撞板的安全性功能应该得到保证。
为了确保在6年内外观无"红色锈迹", 在经过480h盐雾试验后,车的可见部分不允许出现红色锈迹和严重的白色锈迹,不管锈迹是来自那里(例如: 从不可见部分流下来的) 。
与加强板相关的螺纹连接在经过240h循环后不应该出现红色锈迹。
防腐涂镀层前车门侧防撞加强杆被固定在对角位置。
位于一个极易腐蚀的区域。
根据防腐标准,如果有水流过钢材的内部,为了保证没有锈液滴出,应该在钢材的每个表面涂镀10 µm的锌(不妨害外观6年的保质期).根据关于带镀层钢板车门侧防撞加强杆的防腐推荐措施,在进行电泳处理时,应该允许在加强杆的每一个表面去除掉8µm的电泳镀层。
汽车前后防撞梁设计要求规范
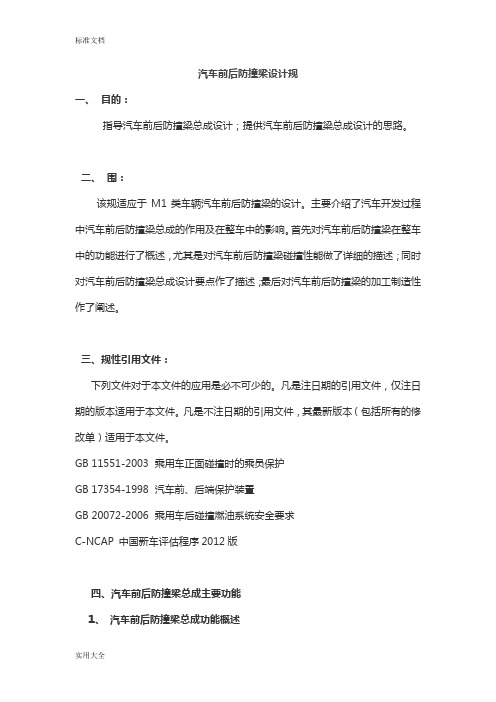
汽车前后防撞梁设计规一、目的:指导汽车前后防撞梁总成设计;提供汽车前后防撞梁总成设计的思路。
二、围:该规适应于M1类车辆汽车前后防撞梁的设计。
主要介绍了汽车开发过程中汽车前后防撞梁总成的作用及在整车中的影响。
首先对汽车前后防撞梁在整车中的功能进行了概述,尤其是对汽车前后防撞梁碰撞性能做了详细的描述;同时对汽车前后防撞梁总成设计要点作了描述;最后对汽车前后防撞梁的加工制造性作了阐述。
三、规性引用文件:下列文件对于本文件的应用是必不可少的。
凡是注日期的引用文件,仅注日期的版本适用于本文件。
凡是不注日期的引用文件,其最新版本(包括所有的修改单)适用于本文件。
GB 11551-2003 乘用车正面碰撞时的乘员保护GB 17354-1998 汽车前、后端保护装置GB 20072-2006 乘用车后碰撞燃油系统安全要求C-NCAP 中国新车评估程序2012版四、汽车前后防撞梁总成主要功能1、汽车前后防撞梁总成功能概述汽车前后防撞梁总成,是车身第一次承受撞击力的装置,也是车身中的一个重要构件,其功能主要有:a. 保护保险杠在低速碰撞过程中尽量不要破裂或者发生永久变形。
b. 保护车身骨架前后端纵梁在行人保护或者可维修性碰撞时不发生永久变形或者破裂。
c. 在100%正面高速碰撞、后面高速碰撞时起到第一次的吸能作用,在偏置碰撞中不仅起到第一次吸能作用,还能起到碰撞过程中均衡传递受力的作用,防止车身左右两侧受力不均。
2、汽车前后防撞梁总成碰撞性能概述前防撞梁总成碰撞性能前防撞梁总成的碰撞性能主要需满足低速碰撞和高速碰撞两个部分的法规要求。
其中,低速碰撞需满足的法规要求为: GB17354-1998 汽车前、后端保护装置。
高速碰撞需满足的法规要求为:GB11551-2003 乘用车正面碰撞时的乘员保护;C-NCAP标准,需满足其100%正面碰撞和40%偏置碰撞要求。
3、低速碰撞对前防撞梁设计的性能要求低速碰撞的国家标准GB l7354—1998规定的正撞速度为4km/h,车角碰撞速度为2.5 km/h,对车身的要求就是车身本体、前防撞梁和吸能盒等不能有任何损坏,最好前保险杠也不能破裂或者发生永久变形。
整车碰撞安全设计建议
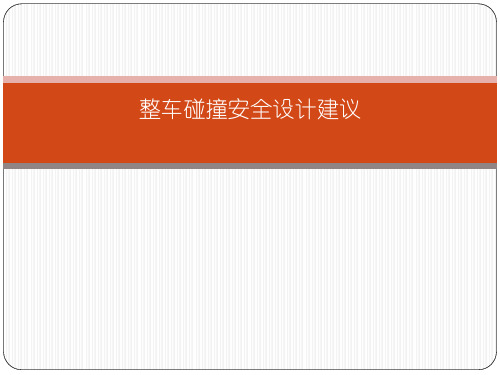
330mm 200mm
空载地面线
L
建议: 前纵梁上端到空载地面线 的高度小于570mm。
后端腔体 较前端相 比太粗壮。
2)前纵梁截面及形状要求
Z方向凸起太高 ,腔体截面相对 前后急剧变小
期望的纵梁结构形式 红线围城的区域
腔体截面大小保持一致
前防撞横梁
1、断面问题: 参考车防撞横梁抗弯能力弱,建议换成辊压 结构。 2、防撞横梁长度不够,前碰撞纵梁易弯。
整车碰撞安全设计建议
说明: 如下要求主要针对在分析计算遇到的问题以及结合自身经验所 提出的建议,希望在前期设计阶段能够规避掉,其中达到碰撞安全 要求的一些技术参数不再体现(例如前碰空间等等)。
目录 一、前碰撞 二、侧面碰撞 三、行人保护-小腿撞击区域空间要求 四、总布置要求及其他设计要求
一、前碰撞 1)前纵梁离地高度
三、行人保护-小腿撞击区域空间要求
小腿撞击区域
小腿碰撞区域最小距离L=24.8mm,小于理论计算的37.0mm,更达不到工程 经验要求的60mm。
1、调整总布置、使得小腿碰撞区域空间达到60mm以上; 2、细化造型、缩小小腿碰撞区域,从而规避小腿碰撞未达到60mm的区域。
3)总布置要求及其他设计要求
发动机托架
存在问题:前碰撞中,发动机挤压发动机托板,造成加速度偏大。 建议:局部优化发动机托板结构。
二、侧面碰撞
后座椅前横梁
存在问题:侧碰时该区域薄弱,易变形。 建议:按虚线趋势优化横梁结构。
B柱结构
存在问题:B柱加强件结构零散,材料牌号低,碰撞易变 形。 建议:完整设计铰链加强件,强化B柱结构。
B柱内饰缺口未 能覆盖假人肋骨
B柱内饰要求: B柱的缺口要覆盖整个假人肋骨,并且上下Z 方向的距离大于40mm,缺口的宽度(X方向)大于 80mm。
顶盖前横梁布置规范及技术标准

2
加磷强化钢
B170P1、B210P1、B250P1
加磷强化钢主要应用于顶盖横梁,A、B、C柱内板、加强板、保险杠本体、纵梁本体,水箱横梁本体等部件
3
烘烤硬化钢
B140H1、B180H1
烘烤硬化钢主要应用于顶盖、发动机盖外板、车门外板
4
低合金高强钢
图1
图 2
5
5
前横梁的布置和形状要考虑顶盖和前挡风玻璃,能与顶盖形成一个封闭的腔体,起到加强的作用。初步分析开口结构前横梁布置断面图(如下图)。
5.2
5.2.1材料的选取
汽车常用板材及用途
序号
名称
牌号
用于车身部位
1
普通冷轧板(低碳)
DC01(ST12)、DC03(ST13)、DC04(St14、St15)、DC06(St16)
所以该类钢具有良好的冲压性能和高的强度以及具有烘烤硬化性能。
5.2.2料厚的选取
根据项目定义,参考车等成熟结构材料和料厚进行初步确定,后期再根据CAE反馈和供应商渠道配合确定最终材料和料厚。以下是一些车型的料厚:
车型
G20
C20
H50
维特拉
料厚
0.8
0.8
0.8
0.7
顶盖前横梁的料厚一般选取0.8mm。
5.5.3与前顶灯的配接设计
前顶灯的位置和安装点是由总布置和厂家提供,安装在顶棚和顶盖前横梁上,所以在前横梁上也会布置前顶灯的安装点。
在顶盖前横梁上的安装方式会根据前顶灯的位置来定,所以各款车型的前顶灯的安装方式也各有不同。有的会在前横梁上安装支架,有的是直接安装在前横梁上,用螺栓连接。
汽车前机舱纵梁设计规范

汽车前机舱纵梁设计规范前机舱纵梁设计规范前机舱纵梁设计规范1范围本标准包含机舱前纵梁总成设计要点及其判定标准等。
本标准适⽤于轿车、SUV等新车型前机舱纵梁设计。
2 规范性引⽤⽂件ECE R33 关于正⾯碰撞车辆结构特性认证的统⼀规定3 术语和定义3.1 前纵梁前纵梁作为碰撞中的主要吸能部件,是汽车发动机舱框架的重要组成部分,它与前保险杠、A柱及前挡板相联接,焊接在车⾝下部,其上再焊接轮罩等构件。
3.2 断⾯断⾯是反映整车性能、结构、配合、法规等⽅⾯要求的截⾯。
主要规定了车⾝主要部位的结构形式、搭接关系、间隙设定、主要控制尺⼨及公差、装配、⼈机⼯程、法规等各⽅⾯信息,是车⾝设计⼯程可⾏性分析的重要⼿段和车⾝结构设计的重要依据。
3.3 NVH NVH是指车辆⼯作条件下乘客感受到的噪声(noise)、振动(vibration)以及声振粗糙度(harshness),是衡量车⾝质量的⼀个综合性指标。
4 功能介绍4.1⼀般功能该系统提供发动机变速箱悬置、前副车架、前防撞梁、蓄电池⽀架、保险丝盒、底盘及空调的管路,线束等总成的安装结构。
4.1.1整车中相关区域固定点前纵梁⼦系统提供整车各个功能块的安装结构。
下图1表达了前纵梁⼦系统在整车中的相关区域。
底盘电器前防撞梁轮胎前悬架线束副车架内外饰空调系统前轮罩挡泥⽪空调管路动⼒总成发动机和变速箱悬置图1 整车中相关区域4.1.2车⾝中相关区域固定点前纵梁⼦系统需要满⾜结构和安全等要求。
下图2表达了前纵梁⼦系统在车⾝中的前端区域。
⽔箱横梁前轮罩总成前挡板总成图2 车⾝中相关区域4.2特殊功能该系统的特殊功能是保证汽车的安全性要求,⾸先是发⽣正⾯碰撞或偏置碰撞时,能够按⼀定规律变形,有效吸收并分散碰撞能量,从⽽最⼤程度地保证车辆和乘员的安全。
其次是通过对车⾝的NVH(即噪⾳(Noise)、震荡(Vibration)、平稳(Harshness)三项标准)的有效控制,使乘员感到可靠和舒适。
汽车碰撞安全要求指南

汽车碰撞安全要求指南随着汽车的广泛应用,汽车碰撞安全成为了人们关注的重要问题。
针对汽车碰撞安全,制定并遵守相应的规范和标准是确保车辆和乘员安全的基础。
本文将从车身结构、安全气囊、制动系统等方面,论述汽车碰撞安全的要求和指南。
一、车身结构车身结构是汽车碰撞安全的基础。
制定规范的车身结构要求可以提升汽车碰撞时的承载能力和吸能能力,保护乘员免受伤害。
具体要求如下:1. 钢材质量要求:车身结构主要由钢材构成,要求选用高强度钢材,以提供更好的抗碰撞能力。
2. 结构稳固性:车身要具备较高的整体稳固性,以确保在碰撞时不会发生严重变形或崩溃,减少乘员受伤的可能性。
3. 碰撞缓冲区域设计:车身前部和后部应设计为缓冲区域,以吸收和分散碰撞能量,并减小乘员所受冲击。
4. 防撞柱设计:车身结构中应设置防撞柱,以增强车身的抗碰撞性能,并能吸收和分散碰撞能量。
二、安全气囊安全气囊是汽车碰撞安全的重要装置,可在碰撞发生时为乘员提供额外的保护。
安全气囊的要求和指南如下:1. 安全气囊布局:汽车内部应设置多个安全气囊,包括驾驶员气囊和乘客气囊。
安全气囊布局应覆盖乘员的头部和胸部,以最大程度地减小碰撞时头部和胸部的受伤风险。
2. 气囊充气速度和压力:安全气囊的充气速度和压力应适中,既能迅速为乘员提供保护,又不会对乘员造成二次伤害。
3. 气囊感应器:安全气囊应配备感应器,能够精准地识别碰撞发生时的意外情况,并迅速触发气囊充气。
三、制动系统制动系统是汽车碰撞安全中的关键环节,主要影响着汽车在碰撞中的减速和停止能力。
以下是对制动系统的安全要求和指南:1. 刹车距离:制动系统应设计合理,确保在紧急情况下,能够在较短的距离内迅速减速并停止车辆。
2. 刹车响应时间:制动系统的响应速度应快,确保在驾驶员踩刹车时,系统能立即响应以减少碰撞风险。
3. 刹车防抱死系统(ABS):汽车制动系统应配置防抱死系统,能够提供最佳的制动力,并防止轮胎在制动时出现抱死现象,保持车辆的稳定性。
- 1、下载文档前请自行甄别文档内容的完整性,平台不提供额外的编辑、内容补充、找答案等附加服务。
- 2、"仅部分预览"的文档,不可在线预览部分如存在完整性等问题,可反馈申请退款(可完整预览的文档不适用该条件!)。
- 3、如文档侵犯您的权益,请联系客服反馈,我们会尽快为您处理(人工客服工作时间:9:00-18:30)。
汽车前后防撞梁设计规范一、目的:指导汽车前后防撞梁总成设计;提供汽车前后防撞梁总成设计的思路。
二、范围:该规范适应于M1类车辆汽车前后防撞梁的设计。
主要介绍了汽车开发过程中汽车前后防撞梁总成的作用及在整车中的影响。
首先对汽车前后防撞梁在整车中的功能进行了概述,尤其是对汽车前后防撞梁碰撞性能做了详细的描述;同时对汽车前后防撞梁总成设计要点作了描述;最后对汽车前后防撞梁的加工制造性作了阐述。
三、规范性引用文件:下列文件对于本文件的应用是必不可少的。
凡是注日期的引用文件,仅注日期的版本适用于本文件。
凡是不注日期的引用文件,其最新版本(包括所有的修改单)适用于本文件。
GB 11551-2003 乘用车正面碰撞时的乘员保护GB 17354-1998 汽车前、后端保护装置GB 20072-2006 乘用车后碰撞燃油系统安全要求C-NCAP 中国新车评估程序2012版四、汽车前后防撞梁总成主要功能1、汽车前后防撞梁总成功能概述汽车前后防撞梁总成,是车身第一次承受撞击力的装置,也是车身中的一个重要构件,其功能主要有:a. 保护保险杠在低速碰撞过程中尽量不要破裂或者发生永久变形。
b. 保护车身骨架前后端纵梁在行人保护或者可维修性碰撞时不发生永久变形或者破裂。
c. 在100%正面高速碰撞、后面高速碰撞时起到第一次的吸能作用,在偏置碰撞中不仅起到第一次吸能作用,还能起到碰撞过程中均衡传递受力的作用,防止车身左右两侧受力不均。
2、汽车前后防撞梁总成碰撞性能概述前防撞梁总成碰撞性能前防撞梁总成的碰撞性能主要需满足低速碰撞和高速碰撞两个部分的法规要求。
其中,低速碰撞需满足的法规要求为:GB17354-1998 汽车前、后端保护装置。
高速碰撞需满足的法规要求为:GB11551-2003 乘用车正面碰撞时的乘员保护;C-NCAP标准,需满足其100%正面碰撞和40%偏置碰撞要求。
3、低速碰撞对前防撞梁设计的性能要求低速碰撞的国家标准GB l7354—1998规定的正撞速度为4km/h,车角碰撞速度为2.5 km/h,对车身的要求就是车身本体、前防撞梁和吸能盒等不能有任何损坏,最好前保险杠也不能破裂或者发生永久变形。
在国外,从事汽车保险业务的保险机构,一般采用15km/h的碰撞试验来模拟最常见的可维修碰撞,试验的目的是要求尽量减少零部件的损坏以减少维修和保险费用。
具体来说,一般要通过合理设计将损坏零件控制在翼子板、发动机罩盖、前保险杠系统、前格栅、前大灯等外表面零件和部分骨架件,比如前防撞梁以及吸能盒等零件范围内。
车身零体,特别是纵梁不能产生任何变形。
当然最好大灯支架、水箱上横梁等零件不要损坏,即使损坏,也要便于修复。
在可维修碰撞中,合理设计传力路径是非常重要的,重点来说说汽车防撞梁吸能盒的设计a、将吸能盒设计成和纵梁在同一轴线上,避免产生弯曲变形。
b、在吸能盒上预设一些压溃筋,以便让吸能盒在轴向上发生压溃进而吸收所有能量,从而不对包括前纵梁在内的车身本体产生损害。
c、将这些容易损坏的部分骨架件,如前防撞梁和吸能盒设计成用螺栓和车身本体联结的可拆卸结构,为减少维修和保险成本。
4、高速碰撞对前防撞梁设计的性能要求目前设计上普遍接受和采用的是将车身分为前中后3个吸能区,其中前吸能区主要由前防撞梁和吸能盒组成,利用强韧的吸能材料尽可能多地通过变形吸收因撞击产生的巨大能量,同时利用结构上的受力连续进行左右分流并将能量向后面传递。
中吸能区主要由前纵梁和副车架组成,通过合理变形来吸收大部分能量。
后吸能区主要为高强度和刚度的驾驶舱,设计上通过避开可能发生对乘员不利的危险变形,减少正面碰撞导致的对驾驶舱的侵入和保持相对较低的碰撞减速度,以此保证乘员的安全。
前中后3个吸能区是设置正面碰撞多层传力路径的基础,设置正面碰撞多层传力路径的目的也就是为体现3个吸能区的优势,使能量能合理有效地吸收和传递。
正面碰撞多层传力路径一般是3层。
正面碰撞3层传力路径一般分为上中下3层,正面碰撞传力路径上层是由发动机舱上纵梁和前悬塔状形罩板等零件组成,吸收了部分从前部传来的碰撞能量并把其余能量向A柱和前围及其加强梁进行分散传递。
中层主要是由前纵梁组成,也包括了前防撞梁和吸能盒等,是主要的传力路径。
前防撞梁和吸能盒将接受到的碰撞能量进行左右分流和初步吸收,并通过它们将能量往前纵梁延伸板、门槛、中央通道等分散传递。
下层主要是由前副车架组成,吸收了部分从前部传来的碰撞能量并把其余能量向前纵梁延伸板和门槛等分散传递。
五、汽车后防撞梁总成碰撞性能后防撞梁总成的碰撞性能主要需满足低速碰撞和高速碰撞两个部分的法规要求。
其中,低速碰撞需满足的法规要求为:GB 17354-1998 汽车前、后端保护装置。
高速碰撞需满足的法规要求为:GB 20072-2006 乘用车后碰撞燃油系统安全要求。
低速碰撞对后防撞梁设计的性能要求:后防撞梁总成需满足的低速碰撞性能要求同前防撞梁总成。
高速碰撞对后防撞梁设计的性能要求:国标GB 20072-2006规定:碰撞器撞击表面应平坦,高度不小于800mm,撞击器表面下边缘至地面的间隙应为175±25mm,后防撞梁对后碰的主要贡献为利用吸能盒的压溃变形吸收能量,缓解碰撞刚性变形,保证燃油箱周围安全的变形空间。
因此在设计后防撞梁及吸能盒时,需综合考虑下面三方面:a、保证基本的许可变形量。
许可变形量,决定了碰撞过程中的平均减速度。
汽车的纵向变形量与平均减速度是成反比的。
平均减速度作为汽车结构耐碰撞性的主要设计指标,在设计开始阶段就必须综合考虑确定。
b、保证基本的许可变形空间。
保证许可变形空间是指汽车在发生碰撞后,变形区域不会对乘员和危险部件(如油箱、燃汽罐)形成威胁和伤害,而且包括后部许可变形区域内的塑性变形不会导致在碰撞过程中车门打开、碰撞后车门锁死等状况发生。
c、调整截面形状(通过吸能筋与加强筋的布置)、厚度、尺寸和结构形式等使结构的变形阻力保持在适当水平,并重视局部弱化使整车刚度分配符合设计原则及能量吸收曲线图,增大撞击吸收能量的腔型结构。
六、汽车前后防撞梁总成设计要点概述1.汽车前后防撞梁总成设计,主要是根据市场法规和标准来定义前防撞梁总成的性能。
如:法规前碰ODB的定义、汽车前后防撞梁低速碰撞吸能、压溃空间、C NCAP 试验ODB碰撞标准、整车性能等。
为满足这些要求,我们需要对汽车前后防撞梁的碰撞性能的敏感性,如:汽车前后防撞梁的布置高度、结构、压溃空间、截面面积、材料等进行研究。
2、整车碰撞对汽车前后防撞梁的布置要求汽车前后防撞梁的布置高度由前纵梁的高度来决定,如果此高度匹配不合理会导致前纵梁在碰撞过程中压溃失稳,导致前纵梁后端大弯曲变形很可能对乘员舱侵入量过大。
汽车前后防撞梁的安装位置,除需满足上述碰撞要求的相容性原理,即两车发生正面相撞时,不合适的防撞梁高度既保护不到自身,还会对对方车辆造成巨大伤害;还需要根据车身高度,轮毂直径的大小来综合评定,并没有一个明确的标准。
一般车型的安装高度在400-500mm左右,但如果超过520mm,则会对C NCAP等相关碰撞试验的成绩造成影响。
保证与周边件间隙≧10mm。
前防撞梁总成一般是螺接到机舱纵梁上,误差积累大,同时车身前端安装有很多子件,故要求前防撞梁总成与周边件的间隙在10mm 以上。
在X 向预留出70mm 的行人保护缓冲空间。
3 、汽车前后防撞梁总成结构形式标准的汽车前后防撞梁总成一般由防撞梁本体和吸能盒组成,部分车型还包含拖车钩螺纹管,为降低维修成本,防撞梁一般采用螺栓连接固定在车身上。
4、前后防撞横梁结构形式前防撞横梁的结构主要有四种方式:冷冲压不同技术对应的优化断面,有不同程度的差别。
冷冲压拼焊的前防撞横梁保持了与车身其它钣金相同的制造技术,不需要单独生产线,故制造成本低廉,不足在于重量大,不便于车身轻量化。
通常材料选用HC420/780DP或HC550/980DP,具体结构、材料根据车型差异及CAE分析相应选择。
辊压成形的前防撞横梁,需要一条专用辊压线,其断面为箱体结构,类似双层板,重量方面优势不大。
通常材料选用HC420/780DP或HC550/980DP,料厚1.8mm,具体根据车型差异及CAE分析相应选择。
根据目前供应商制造工艺限制,目前合理的防撞梁半径R≥2700mm。
热冲压的前防撞横梁,需要一条专用热成形加工线及专用模具,综合成本较高,优势在于重量轻。
铝制的前防撞横梁,需要专用设备及工装,综合成本较高,优势在于重量轻。
5、后防撞横梁结构形式后防撞横梁的制造主要为冷冲压和铝制,冷冲压横梁一般为U形截面结构,通常材料选用HC250/450DP、HC340/590DP,具体形状、材料根据车型差异及CAE分析相应选择。
6、吸能盒设计要求吸能盒上一般需布置2至3条吸能筋,主要目的是便于低速碰撞时吸收足够的能量,保证车身本体不被破坏。
同时设计吸能筋时需遵循以下4条原则:a. 加强筋的轴线必须垂直于受力方向,否则在振动时会引起扭转;b. 必须沿支撑之间最短距离布置;c. 采用交叉筋时,应考虑在交叉点容易产生应力集中,相对减小了交叉点的刚性,所以在交叉点要注意圆角过渡,圆角半径应大于筋的宽度的两倍;d. 加强筋的形状在平的或稍凸起的零件上,加强筋应沿零件对角线布置,在深弯曲的零件上应垂直于零件的弯曲轴线。
定义防撞梁本体和吸能盒截面尺寸:Z 向高度、Y 向宽度、X 向长度: A 级车型吸能盒在X 向长度一般在120mm 左右,A0 级车型长度约在100 mm。
横梁本体X 向截面尺寸受吸能盒和保险杠位置所限制,故不能取值太大,一般在55mm。
可以根据钣金材料级别、整车受力大小和整车安全星级等综合因素而调整。
吸能盒Z向高度、Y向宽度与纵梁截面基本一致,偏差不大于5mm。
吸能盒和纵梁中心轴线一致。
7、前拖车钩结构设计要求前拖车装置工作方式(如:螺接、挂钩)和布置位置;一般前拖车装置采用螺接方式。
布置位置,理论上希望拖车装置对称中心线与机舱纵梁中心重合,或偏离距离越小越好。
挂钩或螺母套主要配合尺寸;根据整车装备质量,确定拖车装置所需要承受载荷,选择合适的螺母套及拖钩,公司现有M20 螺纹规格,不同车型可以通用。
8、防撞梁和车身连接标准件采用8.8级M8螺栓。
七、防撞梁总成设计经验1、吸能盒螺栓固定点分布要求尽量靠近吸能盒,均匀分布。
四个螺栓连接点分布距吸能盒偏远,碰撞中受到扭转力或拉力作用导致前纵梁前安装板和前防撞梁安装板连接处开口。
优化方案:将螺栓安装点靠近吸能盒安装。
2、吸能盒与防撞梁及安装板连接必须可靠,保证连接强度。
中心柱碰撞及偏置碰撞时由于吸能盒与安装板点焊强度不足,导致吸能盒脱落,优化方案:加强连接强度,将点焊改为二保焊,并增加焊接点。