提高感应电炉炉龄实用的技术
提高中频感应电炉炉衬寿命的解决方案

( 5 )无需补炉 ,维护简单 ( 仅以塑性料 勾抹 涂缝 ,即抹即熔无需等候 )。 ( 6 )炉龄更长 ,出液量 大 ( 炼钢 1 0 0 炉次 以
上 ,炼 铜2 0 0 炉次以上)。
( 7 )安全性高 ,避免 穿炉 ( 采用双 层炉衬复
合 结构
3 0 V 2 0
’
w w ̄ . r ne t o l w o r k l n ll g S O . c om
箩 期 热 孕簧 压 铸 造 ’ 参 霭 工 热 … 加 … 工 一
I l c !
若按平均送 电6 0 k W烘炉 l O h 计算可省电6 0 0 k W・ h , 以0 . 8 / k W・ h 元计算 ,合人民币4 8 0 元。 ( 3 )熔钢 量大 手工 捣制的炉衬熔钢 一般在 2 3 0 k g 左右 ( 使用后期 ,容量 稍大 )。而采用成型 炉 衬后第 一炉熔 钢就在 2 8 0 k g 以 上 ,每 炉多化 钢 5 0 k g 。一般熔炼 l t 钢需耗电8 0 0 k W・ h 。若 1 0 0 炉 多 熔炼5 t 钢 ,折算节省的 电为4 0 0 0 k W・ h ,节省人 民
几种典型的成型炉衬及相应 的中频 电炉感应线 圈尺寸情况见表 1 。
表1 成型炉衬型号及对应的感应线圈尺寸
型号/ k g 1 0 0 1 5 0 2 5 0 5 0 0 7 5 0 l O 0 0 1 5 0 0 2 O 0 0 3 0 o 0 5 o o 0
币3 2 0 0 元。
炼钢量和降低用电功率三项就节省电费1 8 0 0 0 元。 综上所述 ,使用成型炉衬仅节省的 电费就大于 购买成 型炉衬 的费用 。减 少 了筑 炉次数也 就减少 了原料 、人工 的投入 。使用次数越 多 ,效 果越 明 显。因此 ,成型炉衬是一种高效节电产 品。
提高工频有芯感应熔铜炉使用寿命的方法与措施

提高工频有芯感应熔铜炉使用寿命的方法与措施摘要:工频有心感应电炉,具有投资少,上马快,经济效果显著等优点。
目前在国内享有一定声誉,普遍用于有色金属加工行业。
本文通过论述炉体主要金属构件等对炉子使用寿命的影响,提出了提高炉子使用寿命的具体方法和措施。
关键词:工频有芯感应熔铜炉;使用寿命;方法前言工频有芯感应电炉具有加热速度快、热效率高、金属烧损少、熔化质量容易控制、操作方便、劳动条件好等优点,广泛用于熔化铜及铜合金。
但这种电炉在生产中是长期连续作业,每次筑炉使用材料较多,费用大,技术要求高,烘炉周期长,因此提高炉子的使用寿命一直是生产企业追求的目标。
1.炉体主要金属构件的质量1.紫铜熔沟紫铜熔沟的质量影响着工频有芯感应电炉的使用寿命,当紫铜熔沟发生断裂时,感应器的二次线圈便会短路,电流变为零,炉子便会失去熔化功能。
紫铜熔沟可以在高温或复杂多轴交变应力下等环境进行工作,如果熔沟出现如气孔、夹渣、夹杂、疏松、裂纹等冶金缺陷时,在高温环境条件下,会使得这些缺陷相互扩散串通,并使得晶粒边界的移动速度变快,导致边界与过渡区的强度快速下降,当紫铜熔沟烤炉到达末期高温烧结阶段时,紫铜溶沟在拉应力的条件作用下,最容易发生热断裂现象出现。
制作紫铜溶沟时最好选取T2纯铜,能够在保证材料的同时,并起到减少杂质的作用。
为了让紫铜熔沟晶粒更细、组织致密度更高、强度更高,可以选用铸铁模铸造紫铜熔沟。
在铸造紫铜熔沟时可以加入小计量的铜与磷中间合金,以达到脱氧除气的目的,并起到减少紫铜熔沟气体含量的作用。
在实际对紫铜熔沟质量进行判断时,可以根据紫铜熔沟的尺寸,计算紫铜溶沟的理论重量,通过称重的方法进行判断。
1.水冷套水冷套可以处在冷热恶劣条线环境下工作,水冷套安装前要进行水压试验,确认无漏水现象后才可以安装使用。
水冷套最好选用大企业生产的1Crl8Ni9Ti厚约4毫米的不锈钢板制作水冷套,以保证长期使用水冷套时能保持性能的稳定,预防因水冷套产生裂纹而导致炉子报废的情况发生。
提高转炉炉龄的措施
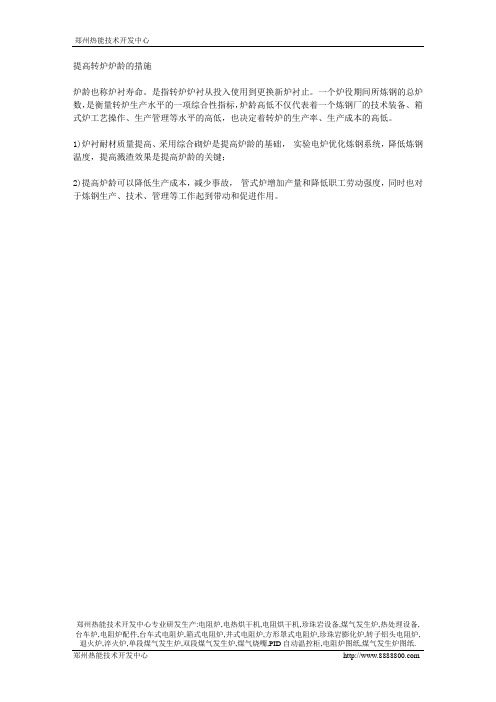
郑州热能技术开发中心
提高转炉炉龄的措施
炉龄也称炉衬寿命。
是指转炉炉衬从投入使用到更换新炉衬止。
一个炉役期间所炼钢的总炉数,是衡量转炉生产水平的一项综合性指标,炉龄高低不仅代表着一个炼钢厂的技术装备、箱式炉工艺操作、生产管理等水平的高低,也决定着转炉的生产率、生产成本的高低。
1)炉衬耐材质量提高、采用综合砌炉是提高炉龄的基础,实验电炉优化炼钢系统,降低炼钢温度,提高溅渣效果是提高炉龄的关键;
2)提高炉龄可以降低生产成本,减少事故,管式炉增加产量和降低职工劳动强度,同时也对于炼钢生产、技术、管理等工作起到带动和促进作用。
郑州热能技术开发中心专业研发生产:电阻炉,电热烘干机,电阻烘干机,珍珠岩设备,煤气发生炉,热处理设备,台车炉,电阻炉配件,台车式电阻炉,箱式电阻炉,井式电阻炉,方形罩式电阻炉,珍珠岩膨化炉,转子铝头电阻炉,退火炉,淬火炉,单段煤气发生炉,双段煤气发生炉,煤气烧嘴,PID自动温控柜,电阻炉图纸,煤气发生炉图纸. 郑州热能技术开发中心。
浅谈如何提升中频炉炉龄
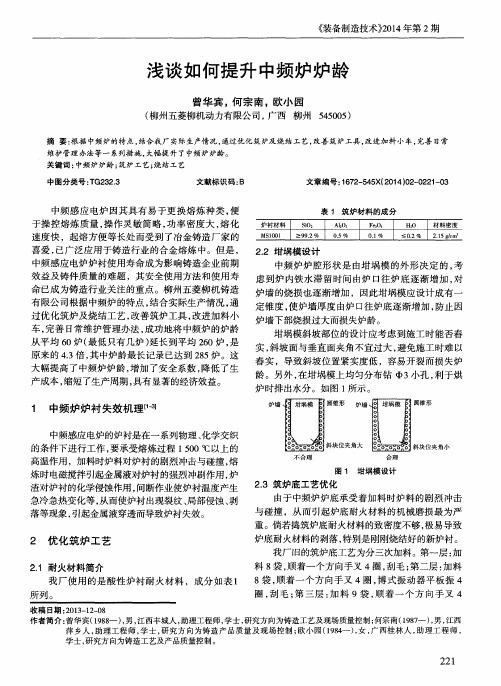
纹 的倾 向, 同时也提高工段 : 使用 0 . 2 M P a 压缩空气 , 振动 5 分钟 ; 第二阶段 , 使用 0 . 4 M P a 压缩空气振动 2 0 分钟 ; 第三阶段 , 使用 0 . 6 M P a 压缩空气振动 5 分钟。
维护管理 办法等一 系列措施 , 大幅提升 了中频炉 炉龄 。
关键词 : 中频 炉 炉 龄 ; 筑炉工艺; 烧结工 艺
中图分类号: T G2 3 2 . 3
文献标识码 : B
文章编号 : 1 6 7 2 — 5 4 5 X( 2 0 1 4) 0 2 — 0 2 2 1 — 0 3
表 1 筑 炉 材 料 的成 分
炉衬材料 l S i O 2 l A 1 2 0 , l F e 2 0 l H 2 0 I材料密度
MS 1 0 0 1 l 9 9 . 2 % l 0 . 5 % l 0 . 1 % l 0 . 2% 2 l . 1 5 加m 3
中频感应 电炉因其 具有易于更换熔炼种类 , 便 于操控熔炼质量 , 操作灵敏简略 , 功率密度大 , 熔化 速度快 ,起熔方便等长处而受到了冶金铸造 厂家 的 喜爱 , 已广泛应用于铸造行业 的合金熔炼 中。但 是 , 中频感应 电炉炉衬使用寿命成为影响铸造企业前期 效益及铸件质量 的难题 ,其安全使用方法和使用寿 命 已成 为铸造行业关 注的重点。柳州五菱柳机铸造 有限公 司根据 中频炉的特点 , 结合实际生产情况 , 通 过优化筑炉及烧结工艺 , 改善筑炉工具 , 改进加料小 车, 完 善 日常 维护 管 理 办法 , 成功 地 将 中频 炉 的炉 龄 从平均 6 0 炉( 最低 只有几炉 ) 延长到平均 2 6 0 炉, 是 原来 的 4 . 3 倍, 其 中炉 龄最 长 记 录 已达 到 2 8 5炉 。这 大幅提高 了中频炉炉龄 , 增加了安全系数 , 降低了生 产成本 , 缩短了生产周期 , 具有显著的经济效益。
提高中频感应电炉炉衬寿命的解决方案

提高中频感应电炉炉衬寿命的解决方案..............................................................................................................时间:2011-5-7 13:29:20提高中频感应电炉炉衬寿命的解决方案孟昌辉,李建国摘要:本文介绍了中频电磁感应熔炼电炉炉衬的予制成型产品—成型炉衬(坩埚)在熔炼生产中的应用技术。
成型炉衬以高纯刚玉Al2O3和电熔镁MgO为基材制成,具有一系列的优点,广泛地适用于熔炼黑色、有色金属及其各类合金。
文章推荐以电动筑炉机采用干法施工安装实现了成型炉衬的快速、可靠安装,并大幅度提高了炉衬的使用寿命,具有广泛的应用前景。
前言中频电磁感应炉具有熔炼速度快、效率高、温度易于控制、环保等突出优点,成为铸造企业生产铸件的主要熔炼设备,但是,中频熔炼电炉炉衬的使用寿命成为影响铸件早期质量及企业效益的难题。
经过多年的生产实践,本公司推出“成型炉衬+电动筑炉机施工”的解决方案,彻底的摈弃了手工捣制炉衬的落后工艺,避免了人为因素的影响。
目前从25KG到5000KG成型炉衬已在国内外数千个铸造企业生产中应用,广泛地适应于熔炼黑色及有色金属及其各类合金,取得了很好的经济效益。
1成型炉衬成型炉衬是指以机械方法制作并实现工业化批量生产的固定尺寸耐火材料的衬体。
它具有体积密度大、强度高、材质好、粒度均匀、成品一致性好等一系列在炉体内捣制炉衬所无法比拟的优势。
成型炉衬采用高纯刚玉Al2O3和电熔镁MgO为主要基材制成。
由于在熔炼过程中形成了镁铝尖晶石或铝镁尖晶石烧结层所以成型炉衬既有优良的热稳定性能、不易受热震开裂又具有优良的耐高温性能、不易受渣化侵蚀的特点。
表1是几种典型的成型炉衬及相应的中频电炉感应线圈尺寸情况。
表1 企鹅牌成型炉衬型号及对应的感应线圈尺寸型号(kg)100 150 250 500 750 1 000 1 500 2 000 3 000 5 000 感应圈尺寸(mm) 320 360 450 560 620 720 770 810 870 1 100 (来源:沈阳恒丰实业有限公司产品目录)成型炉衬的优点如下:(1)安装简便,省时省力。
提高中频感应电炉炉衬寿命的解决方案

提高中频感应电炉炉衬寿命的解决方案一、背景介绍中频感应电炉是一种广泛应用于金属加工和热处理的设备,其炉衬是承受高温和腐蚀的关键部件之一。
然而,由于工作环境的恶劣和长时间的使用,炉衬的寿命往往较短,需要频繁更换,给生产造成了很大的损失。
因此,提高中频感应电炉炉衬寿命成为一个重要的问题。
二、问题分析当前中频感应电炉炉衬的主要问题包括: 1. 高温腐蚀:高温下的化学反应会导致炉衬表面的腐蚀,从而损害其使用寿命; 2. 热疲劳:炉衬在加热和冷却过程中会经历很大的温度变化,容易出现热疲劳裂纹; 3. 磨损:金属材料在高温下的相互摩擦会导致炉衬表面的磨损,加速其老化; 4. 氧化:炉衬表面长期暴露在空气中,容易与氧发生反应,形成氧化层,进一步损害其性能。
三、解决方案为了提高中频感应电炉炉衬的寿命,可以采取以下措施:1. 材料的选择选择高温腐蚀性能较好的材料作为炉衬,例如耐火材料、高温合金等。
这些材料具有良好的耐高温、耐腐蚀和耐磨损性能,能够有效延长炉衬的使用寿命。
2. 耐火涂层的应用在炉衬表面涂覆耐火涂层,可以增加炉衬的抗高温腐蚀和抗热疲劳能力。
耐火涂层能够形成致密的氧化层,阻止金属与氧发生反应,同时能够承受更高的温度变化,减少热疲劳裂纹的产生。
3. 温度控制的优化合理控制中频感应电炉的工作温度,避免温度过高或过低对炉衬造成的损伤。
可以通过改变工作参数、优化电磁场分布等手段,减少炉衬的热应力和热疲劳。
4. 炉衬的定期维护和保养定期对中频感应电炉的炉衬进行维护和保养,包括清理表面积聚的杂质、修补炉衬表面的裂纹、检查耐火涂层的状况等。
及时发现和修复炉衬的问题,能够延长其使用寿命。
四、实施效果与展望通过采取上述措施,可以显著提高中频感应电炉炉衬的寿命,降低更换频率和维护成本,提高生产效率和产品质量。
同时,还能减少废品产生,降低对环境的影响。
然而,目前的解决方案仍然存在一些问题,如耐火涂层的性能和稳定性有待改进,温度控制的精度有待提高等。
如何提高中频炉炉衬寿命的筑炉工艺技术
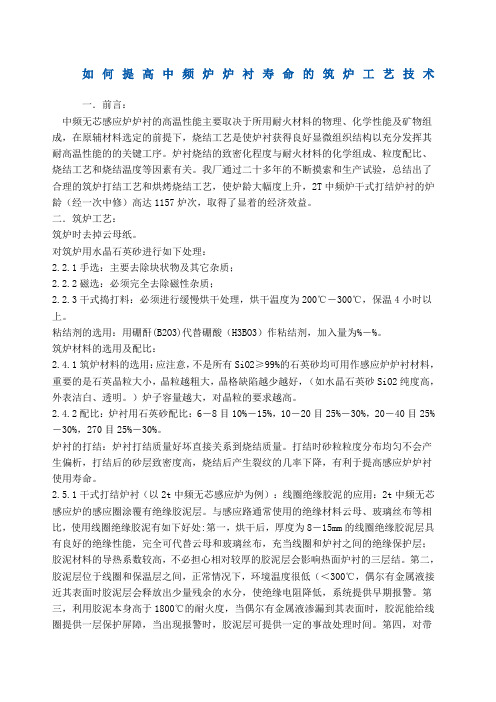
如何提高中频炉炉衬寿命的筑炉工艺技术一.前言:中频无芯感应炉炉衬的高温性能主要取决于所用耐火材料的物理、化学性能及矿物组成,在原辅材料选定的前提下,烧结工艺是使炉衬获得良好显微组织结构以充分发挥其耐高温性能的的关键工序。
炉衬烧结的致密化程度与耐火材料的化学组成、粒度配比、烧结工艺和烧结温度等因素有关。
我厂通过二十多年的不断摸索和生产试验,总结出了合理的筑炉打结工艺和烘烤烧结工艺,使炉龄大幅度上升,2T中频炉干式打结炉衬的炉龄(经一次中修)高达1157炉次,取得了显着的经济效益。
二.筑炉工艺:筑炉时去掉云母纸。
对筑炉用水晶石英砂进行如下处理:2.2.1手选:主要去除块状物及其它杂质;2.2.2磁选:必须完全去除磁性杂质;2.2.3干式捣打料:必须进行缓慢烘干处理,烘干温度为200℃-300℃,保温4小时以上。
粘结剂的选用:用硼酐(B2O3)代替硼酸(H3BO3)作粘结剂,加入量为%-%。
筑炉材料的选用及配比:2.4.1筑炉材料的选用:应注意,不是所有SiO2≥99%的石英砂均可用作感应炉炉衬材料,重要的是石英晶粒大小,晶粒越粗大,晶格缺陷越少越好,(如水晶石英砂SiO2纯度高,外表洁白、透明。
)炉子容量越大,对晶粒的要求越高。
2.4.2配比:炉衬用石英砂配比:6-8目10%-15%,10-20目25%-30%,20-40目25%-30%,270目25%-30%。
炉衬的打结:炉衬打结质量好坏直接关系到烧结质量。
打结时砂粒粒度分布均匀不会产生偏析,打结后的砂层致密度高,烧结后产生裂纹的几率下降,有利于提高感应炉炉衬使用寿命。
2.5.1干式打结炉衬(以2t中频无芯感应炉为例):线圈绝缘胶泥的应用:2t中频无芯感应炉的感应圈涂覆有绝缘胶泥层。
与感应路通常使用的绝缘材料云母、玻璃丝布等相比,使用线圈绝缘胶泥有如下好处:第一,烘干后,厚度为8-15mm的线圈绝缘胶泥层具有良好的绝缘性能,完全可代替云母和玻璃丝布,充当线圈和炉衬之间的绝缘保护层;胶泥材料的导热系数较高,不必担心相对较厚的胶泥层会影响热面炉衬的三层结。
提高电炉炉龄工艺实践

摘要:某炼钢分厂90 t UHP电弧炉自2009年电炉兑铁水以来,一次性炉龄一直徘徊在400 -500炉,使用周期20 -25天。经过对电
炉耐材
理的分析,结合冶炼工艺的 ,并 优化耐材材质、改炉 打方式、摸索炉耐材砌筑工艺、优化冶炼操作工
艺
,在不挖修、
打 炉底及少喷补的条件下,2018年的一次性炉
850炉,最 炉
亠录4誑
INDUSTRIAL HEATING
・15 -
上述反应使
成了 l~2mm厚的脱碳
层 损,
被化 成孔隙,熔渣从孔隙或裂
纹处 ,与 MgO 反 成 CMS( CaO • MgO • Si02)、
C3MS2(3Ca0 - Mg02Si02)
点固 ,加速了炉
的熔损。
,炉
FeO
线
的主
(
炉
几大
图1所示。
,在高 固溶反
,形成一些 点物相,这样 炉
成
层。
电间 ,温
,硬
厚,
层
定厚 炉底炉 能具有很高
的强度,较好的防 能力、
炼过程中,高温水与炉衬、炉直接接
, 炉的
件十分恶劣,炉 损
有:
炉渣、钢水、对炉衬的、电弧的热辐射、炉对
炉 的化学 、
和 水对炉 的
击、炉温 化引起的炉
W
1-2电炉炉底捣打料的物理侵蚀
目前电炉炉底耐材物理
、炉
位 水对炉底耐材造成较大的机械
刷,导 炉 打料脱层并在局 成
温
并 合理的温度范围*10-1+。
951炉,取 了
的经济 (
关键词:电弧炉'一次性炉龄;耐材;炉衬
中图分类号:TG232.3 文献标志码:A 文章编号:1002-1639(2020)01-0014-03
- 1、下载文档前请自行甄别文档内容的完整性,平台不提供额外的编辑、内容补充、找答案等附加服务。
- 2、"仅部分预览"的文档,不可在线预览部分如存在完整性等问题,可反馈申请退款(可完整预览的文档不适用该条件!)。
- 3、如文档侵犯您的权益,请联系客服反馈,我们会尽快为您处理(人工客服工作时间:9:00-18:30)。
提高感应电炉炉龄实用技术电炉炉衬的使用寿命对于需要连续大规模生产的冶金、铸造企业来说具有重大意义。
我公司使用无芯感应酸性炉衬电炉(先是1.5 t工频炉,后为2 t、3 t中频电炉)熔炼灰铁和球铁铁液,炉衬寿命平均达到400次以上,最高达到620炉(按总出铁量除以电炉额定铁液容量计算)。
达到电炉的高炉龄是一个系统工程,必须做好以下各方面的工作。
1 筑炉前期工作包括水冷、感应线圈、磁轭、支撑胶木、绝缘涂料、耐火胶泥的检查和处理。
1.1 要求各个部件之间必须连接稳固,通电元件之间必须部件本身无隐患、保持规定的距离,通水元件本身及连接无渗漏;通电线圈上必须无多余金属残留物且涂刷专用线圈涂抹料(绝缘材料);线圈内侧圆周之间必须要涂抹专用耐火胶泥,耐火胶泥在线圈内部形成的柱(锥)面必须光滑,不允许出现凸凹点、在线圈每匝之间形成良好的连续填充;凡涂抹料、耐火胶泥在筑炉前必须干燥,可以自然停留24—48h晾干,也可以晾干12h后置人坩埚模小功率10kW左右烘烤1~2h烘干。
1.2 目的达到尽量减少因为炉体的绝缘(胶木发烟、匝间短路和感应线圈吸附铁豆)、漏电、炉体内圆柱(锥)面影响炉衬自然收缩产生裂纹等意外事故,而导致的必须或者难以判断的停炉、拆炉。
2 筑炉工序包括筑炉准备工作、筑炉操作两个步骤。
2.1 筑炉准备工作2.1.1 筑炉工具一般要用到以下三种工具:耘松叉、捣固叉、捣固锤和通用的连接棒、电振动器等。
(1)耘松叉:因为并排几个铁齿较短(一般常为40~50mm)、较细且端部较尖,主要用于把加入坩埚四周的炉衬材料耙匀并预叉实,在加入后一层炉衬材料之前把前一层筑好的炉衬上表面耘松约20mm。
(2)捣固叉:一是要求齿的分布形状与坩埚圆周仿形,便于叉到坩埚模的边沿部位;二是叉齿的长度应比较适中,达到电振动器传输冲量到前一层与本层的交接处又不至于影响效率,取100~120mm的齿长较合适。
(3)电振动器:拉法基乐法耐火材料(上海有限公司)和美国联矿生产的电振动器性能卓越,比一般的气动、手动筑炉振动效果好得多且效率高;另外,乐法提供的不用叉、锤,在坩埚壁上三个振动点的新式电振动器更具有效率极高、炉衬整体均匀优质的特点。
2.1.2 坩埚模额定3 t以内一般为5~6 mm的A3钢分段焊接而成。
1.5 t 以上的电炉坩埚模一般是在烧结阶段被熔化,因为这个规格以上的坩埚模即使加大斜度也难以拔出,即使拔出也很可能拉裂炉壁,烘烤烧结效果(特别是均匀性)比不上熔掉坩埚模,否则将得不偿失。
另外其结构特点将对炉衬寿命有直接影响。
(1)坩埚模主体圆周:这一段可以根据线圈处内面耐火胶泥层的形状(炉衬推出式一般从炉底至炉口有一定便于炉衬推出的斜度),保持一定炉衬厚度而让坩埚此段随形,也可以以保证最薄位置的安全厚度将此段做直。
根据使用中此段的侵蚀状况而将坩埚此段在电炉厂家规定的坩埚圆周尺寸上每边缩小10 mm~15mm。
(2)坩埚模高度的确定:一般认为,底部炉衬厚度以达到高过最下面一匝感应线圈为基准,但是在实际过程中应充分考虑以下因素:熔化效率、熔炼材料、中/工频炉的炉衬侵蚀部位。
一般情况下生产灰铁或者球铁的中频炉的炉底侵蚀不大(大约30~50 mm),可以按压着最下面一匝感应线圈上沿为准,而工频炉的炉底侵蚀比较严重(往往达到100 mm以上),这就要求将工频炉的炉底比同规格的中频炉炉底炉衬厚50~100 mm,整个坩埚模的高度应为炉底炉衬上平面至炉沿平面垂直高度距离加上高过炉沿平面约50 mm的高度,这个高度有利于后面的满炉铁液烧结炉衬,具体高度以不影响合上炉盖准。
(3)转角处的尺寸和形状:这是至关重要的。
因为灰铁、特别是球铁在高温(1 500~1 550℃)下此处易产生“大象脚”侵蚀,而且此处的耐火胶泥层直径也较小,所以此处是可能穿炉的“薄弱环节”。
这个地方的转角应该平缓,转角梯度由一次改为不低于二次,而整体炉衬应该加厚是一个基本方向。
(4)钻排气孔和底部形状:在坩埚模底及侧壁上应按200—300 mm的间距钻出呈菱形分布的小孔,这有利于烘烤阶段炉衬材料中水分的排出和增大电阻,提高发热烘烤效果。
孔的直径在3 mm左右较好,太小则排气效果不好,太大则导致筑炉时炉衬材料从孔中大量喷人。
坩埚模底部平面不能向内凹进,最好水平,要么由中心向外凸出1 mm左右,以免筑炉后底部有气隙和结构性应力导致烘烤烧结时“底爆”。
(5)其余:焊缝必须打磨光滑不留锐角;坩埚的外圆尺寸公差及同心度严格限制在5 mm以内;备用坩埚模应在使用前除锈。
2.1.3 筑炉材料这里指的是炉衬材料,熔炼灰铁、球铁铁液一般选用二氧化硅为骨料配粘结剂硼酸等的酸性炉衬。
材料的好坏是决定炉衬寿命的第一要素,对此有以下要求。
(1)用量不大的可以自己配制①石英砂成分ω为:SiO2>99%,CaO<0.5%,MgO<0.5%,FeO<0.5%,Al2O3 <0.5%,H2O<0.5%。
②配方目数:6~8、10~20、40~70、200及以下;比例:分别为30%、20%、30%、20%。
另外加入2.0%~2.2%未潮解的过筛硼酸;对上部(感应线圈最上面一匝平面以上)“炉领”炉衬材料最好适量加入模数在2.2~2.8的水玻璃。
③混制:首先对石英砂进行磁选,再把各种目数的石英砂按以上配比加入,用铁铲翻转均匀;按以上配比加入硼酸,再翻转均匀,最后用手再次搓匀。
混制炉领炉衬材料时硼酸加入量取下限,与水玻璃同时加入并翻转均匀和用手搓揉,水玻璃的加入量以硅砂的粉尘全部变潮、手捏不成团为准。
否则,加入过多炉领处易开裂。
(2)用量较大且需要连续生产时最好选取专业炉衬材料厂配制好的“干打料”。
对此作以下说明。
①供应商和炉衬材料种类、牌号的选择:外国厂家有联矿(天津)、拉法基乐法(上海)等,国内厂家有沈阳力达等;需要什么种类和牌号的材料只需要提供给供应商所在单位熔炼合金种类、最高使用温度等参数即可。
②对供应炉衬材料的使用前检查:一般库存量够用即可,以防炉衬材料回潮;使用前必须检查是否回潮结块,否则要么停用,要么将潮湿料仅仅用于修筑炉嘴,否则容易导致炉衬局部裂纹、剥落。
拆开袋后的炉衬材料要求经过磁选,对非石英质的其它杂质也尽量选出;对材料的种类、牌号等应在使用中适时调整。
3 筑炉操作3.1 耐火、绝缘材料的铺设对内部涂有耐火胶泥的特别是拆炉衬为推出式的,建议先铺设一层云母板,再铺一层石棉板;对非以上情况的,铺设两层石棉板、一层云母板,其中云母板置于两层石棉板之间,要求云母板、石棉板的接头应在50~100 mm,且接头应相互错开;云母板、石棉板与线圈内侧(或者耐火胶泥层)之间必须伸展、紧贴;云母板、石棉板必须用张紧圈张紧,特别是在炉口部位必须箍紧,不得留下让异物(特别是铁屑)掉入的隐患。
3.2 倒砂、拨匀将经过磁选的炉衬材料用塑料或者木质瓢沿环状的炉衬区倒人,尽量均匀;再用耘松叉将炉衬材料沿环状的炉衬区拔平并预紧实,每次倒人的炉衬材料以拨平、预紧实后比前一层增高不超过120mm为准;耘松叉应在再次倒人炉衬材料前将上一批的已打结炉衬上面耘松20 mm深。
3.3 打结先用捣固叉,每次都应争取让捣固叉的叉齿扎到此层与上一层的交界处,捣固叉主要是通过向下传递冲量将炉衬材料中的空气排除,从而达到炉衬材料的紧实;当捣固叉难以下扎时就换用捣固锤,捣固锤的打击平面要求下一个要压着上一个的1/3~1/2,直到回弹有力打不动为止。
用叉和锤都应离开石棉板而贴近坩埚模并沿着环状炉衬区旋转打结;这样有利于避免将石棉板打破为碎屑造成穿炉隐患,又可让炉衬在径向方向形成从内到外逐步降低的紧实度梯度,并且在圆环每个同心圆的各点紧实程度均一。
在打结转角处时应格外注意,一是炉衬材料最好按每层80~100mm加料,二是应该将捣固叉、锤适当偏斜,确保能打结该处坩埚模附近区域的炉衬材料。
3.4 筑炉其它注意事项确保整个筑炉过程中炉衬及耐热、绝缘材料中不掉入任何杂物(特别是铁质材料),否则应该予以清除;坩埚模水平放置在炉内正中的前提下,根据电炉的侵蚀、出铁时辐射烘烤主要在后面炉衬的情况,建议坩埚模向前面移动5 mm左右。
4 烘烤、烧结这是炉衬寿命的关键之一。
应制订《烘烤、烧结工艺》,并用热电偶、温度数字显示仪进行监控。
烘烤、烧结应注意以下控制要点。
4.1 烘烤和初期烧结阶段的加料特点通常工频炉需要加入起炉块,大约为电炉额定容量的20%~30%,起炉块的四周与坩埚模内壁留5~15 mm的间隙;而中频炉不必加入起炉块,只需要加入的炉料块小、密实、干燥无锈。
在底下金属没有熔化之前,一般可将炉内加满炉料,在金属开始熔化后小批量的每次加入50~200 kg炉料(视电炉规格定),直到最后金属液面离炉沿50~100 mm。
4.2 烘烤、烧结阶段的升温特点总的原则是“低温阶段慢升温,持续时间长”,烧结阶段温度要比平时最高出铁温度高50~80℃左右,烧结时间保温2~3h。
低温阶段900℃以前升温速度为1.2℃/min,这有利于炉衬材料中水和晶间水的逸出,在900℃左右保温2~3 h后石英稳定发生相变;否则,升温过快将导致石英急剧相变,内应力过大将导致以后炉衬开裂、剥落,急剧降低炉衬寿命及使用安全。
高温烧结做到位,有利于在炉衬的径向上从内到外形成各占1/3厚度的烧结层、过渡层、松散层,这样炉衬既有一定抗高温侵蚀性能,又有较好的强度和韧性。
4.3 其它烘烤、烧结使用炉料尽量少用,避免长时间用高碳质炉料在过高温度下熔炼,这将加大炉衬的侵蚀,因为将发生以下反应:C+SiO2=CO2+Si—Q,高温有利于吸热反应的进行。
为使坩埚表面形成一定厚度的耐侵蚀的烧结釉质层,应在烘烤前向炉内投入5~10 kg的石英玻璃碎屑;新炉开始使用的前7、8炉铁液建议每次出铁1/5~1/3左右,有利于对炉衬的保护和进一步完好烧结。
5 使用维护良好的使用方法对炉衬寿命也很重要。
以下要点应予以注意。
5.1 加料、出铁要求炉料的块度不得太大,炉料小批量多批加入,不能蓬料,减少炉料对炉壁、炉底的冲击。
炉内留的铁液在不影响交界材质和加料不飞溅的情况下应适当多些,避免铁料直接撞击炉底。
每次出铁后电炉应平放,减少炉内铁液对后壁的辐射烘烤和重力对整体炉壁的不均匀作用。
5.2 “冷凝金属起熔”为减少炉衬因为反复骤热骤冷的热疲劳导致开裂,往往连续开炉对炉衬寿命的延长是相当重要的,但是由于突发性事件导致电炉停电,炉内的铁液冷凝后重新启炉的情况难以避免。
对此,提出以下要求。
(1)在炉内金属顶部没熔穿之前必须将炉体合上炉盖并向前倾斜15°左右,以低于电炉的保温功率开始送电。
(2)在冷凝金属没有软化之前不得提高功率,因为此时升温太快将导致金属的膨胀严重超过炉衬的膨胀而导致金属凝块将炉衬拉裂,最终导致穿炉等严重事故;金属冷凝软化后可以将功率升到保温功率左右,直到冷凝金属上面的金属壳被下面的液体金属熔穿,此时可将炉体放平,以较高的功率升温熔化。