挤压造粒机常见故障及处理
大型双螺杆挤压造粒机生产过程中的常见问题
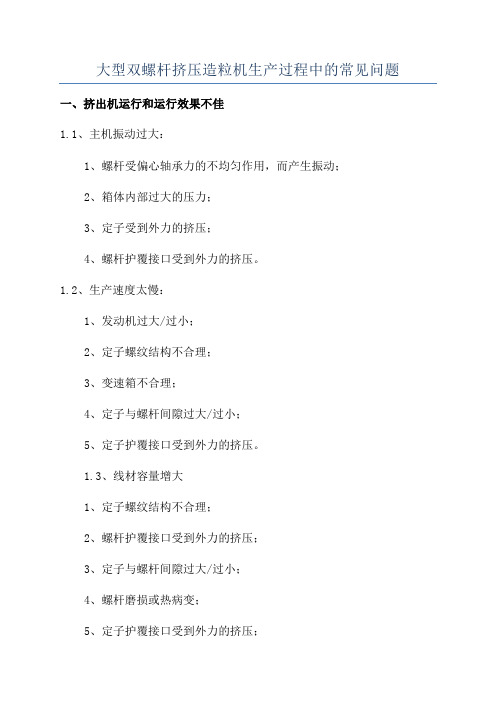
大型双螺杆挤压造粒机生产过程中的常见问题
一、挤出机运行和运行效果不佳
1.1、主机振动过大:
1、螺杆受偏心轴承力的不均匀作用,而产生振动;
2、箱体内部过大的压力;
3、定子受到外力的挤压;
4、螺杆护覆接口受到外力的挤压。
1.2、生产速度太慢:
1、发动机过大/过小;
2、定子螺纹结构不合理;
3、变速箱不合理;
4、定子与螺杆间隙过大/过小;
5、定子护覆接口受到外力的挤压。
1.3、线材容量增大
1、定子螺纹结构不合理;
2、螺杆护覆接口受到外力的挤压;
3、定子与螺杆间隙过大/过小;
4、螺杆磨损或热病变;
5、定子护覆接口受到外力的挤压;
6、定子表面磨损;
7、定子护覆接口受到酸碱腐蚀。
二、维修保养难题
2.1、螺杆磨损严重:
1、螺杆几何尺寸不符合要求;
2、螺杆表面热处理不合理;
3、螺杆与定子间隙过大/过小;
4、主机运行过程中的压力变化过大;
5、螺杆护覆接口受到外力的挤压;
6、定子护覆接口受到酸碱腐蚀。
2.2、螺杆耗损快:
1、螺杆几何尺寸不符合要求;
2、螺杆表面过度热处理;
3、螺杆与定子间隙过大/过小;
4、定子受到外力的挤压;
5、螺杆护覆接口受到外力的挤压;
6、定子受到外力的挤压;
7、定子护覆接口受到酸碱腐蚀。
煤化工聚烯烃挤压造粒机组故障分析董海燕

煤化工聚烯烃挤压造粒机组故障分析董海燕发布时间:2021-08-11T01:45:55.319Z 来源:《防护工程》2021年12期作者:董海燕[导读] 挤压造粒机组是聚丙烯产品造粒生产阶段主要的设备,自动化控制程度非常高。
在日常运行过程中会存在许多难以诊断的故障,需要逐步排除,其分析处理过程漫长,很多时间浪费在排查故障原因上,严重影响了挤压造粒机组的正常运行,很大程度上降低了经济效益。
大唐内蒙古多伦煤化工有限责任公司内蒙古锡林郭勒盟 027300摘要:随着煤化工的快速发展,中国的煤制烯烃项目方兴未艾。
聚烯烃(聚乙烯和聚丙烯)是煤制烯烃项目的最终产品。
挤出造粒机组是生产该产品的关键设备。
该机组集机械、电气、仪表于一体,自动化控制水平高。
它是聚烯烃装置中整体尺寸最大、结构最复杂、投资最大、制造周期最长的大型动力设备。
它通过混合、挤出和造粒过程将聚烯烃粉末制成颗粒状产品。
其运行的可靠性和稳定性直接影响聚烯烃产品的质量和装置的长期生产。
因此,分析挤出造粒机组的故障原因,总结解决方法具有重要意义。
聚烯烃的粉末造粒也是一个产品改性的过程。
在造粒过程中,各种添加剂,如稳定剂、润滑剂、增塑剂、阻燃剂、抗静电剂、防老剂、抗紫外线剂等。
是为了提高产品性能,满足预期要求,方便运输和后续加工。
关键词:聚丙烯;造粒机组;故障分析挤压造粒机组是聚丙烯产品造粒生产阶段主要的设备,自动化控制程度非常高。
在日常运行过程中会存在许多难以诊断的故障,需要逐步排除,其分析处理过程漫长,很多时间浪费在排查故障原因上,严重影响了挤压造粒机组的正常运行,很大程度上降低了经济效益。
一、挤压造粒机组的工艺流程聚乙烯装置的树脂粉料脱气后与多种助剂按一定比例混合,经挤压机的喂料器送至混炼机中,在200℃高温下,聚乙烯粉末变为熔融树脂并通过进料调节阀调节树脂的混炼程度;熔融树脂通过熔融泵增压,经过自动换网器的滤网去除杂质,再经出料模板的模孔挤压;挤出后的熔融树脂进入切粒水箱,由水箱中的旋转切刀在颗粒冷却水中切割造粒;切割出的树脂颗粒被颗粒水带入除块器,在除块器中大块树脂被去除后送至离心干燥机进行脱水干燥;干燥后的颗粒送至颗粒振动筛,振动筛筛出的合格粒料经风送系统送至产品料仓掺混存放。
挤压造粒机常见故障分析及处理

挤压造粒机常见故障分析及处理挤压造粒机组集机、电、仪高度一体化,自动化控制水平高。
因此,在实际运行中将出现较多难以诊断的故障,导致处理时间过长,从而影响整套聚丙烯装置的正常运行,大大地降低了生产经济效益。
笔者结合挤压造粒生产过程的理论知识以及十余年实际生产运行的管理经验,对该机组在运行中出现故障的常见原因进行分析判断,制定了相应的解决措施及处理方法,从而确保其长周期的稳定运行。
故障原因在挤压造粒机组中,导致挤压造粒机组在运行中出现摩擦离合器脱开,机组联锁停车的原因可分为四大类:主电机系统故障1、主电机扭矩过高或过低;2、主电机转速过低;3、主电机轴承温度过高;4、主电机绕组温度过高;5、主电机水冷的冷却器出入口温度过高;6、主电机轴承润滑油泵出口流量过低;7、主电机轴承润滑油泵出口压力过低;8、主电机水冷的冷却器水泄漏量过高等。
传动系统故障1、齿轮箱变速杆位置偏离;2、摩擦离合器的仪表风压力过高;3、摩擦离合器速度差过大;4、齿轮箱润滑油泵出口压力过低;5、齿轮箱润滑油泵出口油温过高;6、摩擦离合器内部故障等。
挤压造粒机螺杆工艺段故障1、节流阀前后熔体压力过高;2、机头熔体压力过高;3、换网器前后熔体压差过大;4、开车阀转动故障等。
水下切粒系统故障1、切粒电机绕组温度过高;2、切粒机转速过低;3、切粒机扭矩过高;4、颗粒水旁通自动切换故障;5、颗粒水压力过高或过低;6、颗粒水流量过低;7、切粒机夹紧螺栓未把紧;8、切粒室旁路水阀未关;9、切粒机液压夹紧压力过低;10、切粒电机故障;11、液压切刀轴向进给压力过低等。
在上述故障原因中,出现频次较多的有:主电机系统的主电机扭矩过高或过低;传动系统的摩擦离合器故障;挤压造粒机螺杆工艺段系统的熔体压力高;水下切粒机系统故障等。
下文将对这些常见的故障原因进行详细的分析,给出相应的解决方法。
wodeai常见故障原因分析及解决措施主电机扭矩过高原因分析:油润滑系统故障,主电机输出轴与齿轮箱出入轴对中不良,电机及离合器振动等原因都将损坏主电机轴承,导致扭矩过高。
挤压造粒机异常振动分析、解决

挤压造粒机异常振动分析、解决挤压造粒机是一种常用的颗粒制造设备。
如项目出现了挤压造粒机异常振动,可能会严重影响生产效率和产品质量,甚至会导致设备的损坏。
因此,深入分析挤压造粒机异常振动的原因,找到解决办法是非常关键的。
一、异常振动的原因(一)构造问题挤压造粒机结构简单,由进料机构、挤压部分、取料机构、电控部分组成。
如果其中任何一个部件出现问题,都可能会导致振动异常。
有些厂商为了追求低成本,使用了低质量材料生产造粒机,导致机器寿命短,使用寿命结束后容易出现问题。
(二)设计问题挤压造粒机的设计和选择也是导致异常振动的主要原因之一。
挤压造粒机的设计应尽可能地精细化,且必须考虑工作原理和流程,满足实际生产需求。
如果设计不合理,机器各部件间间隙过大或过小,都有可能导致振动过大。
(三)零部件松动挤压造粒机在使用的过程中,由于长时间的振动,零部件之间可能会松动,导致异常振动。
例如,螺旋轴连通轴套筒松动,螺旋轴和壁板之间的间隙变大等。
这也是造成挤压造粒机异常振动的常见原因之一。
二、解决办法(一)加强检查定期检查各部分的零部件,确保它们没有松动。
因为挤压造粒机使用的时间长,因此有时出现零部件松动的情况也是很正常的。
只有经常进行检查,将有问题的部分及时处理或更换,让机器处于良好状态,才能保证设备的正常运行。
(二)优化结构挤压造粒机的结构设计应充分考虑到使用的环境和待处理物料的特点,使结构设备充分利用材料的特性,保证设备在高效率和低噪音的基础上实现优化比例。
此外,在振动的设计处理上,需要通过减震、减振等措施,降低振动水平,进一步缩小振动范围。
(三)改善配件针对经常出现故障的零部件,应该适时对其进行更换或者改善,以便提高零部件的耐用性,减小故障发生的频度。
(四)维修意识挤压造粒机在工作之前需要经过维修检查,这样才能保证设备在使用中更加安全。
因此,管理人员需要加强对工人的培训,提高维修检查的意识,定期对挤压造粒机进行维修保养,减共振损伤,提高生产效率。
挤压造粒机组常见故障分析及处理

推动 切刀刀轴 活动 的是 1 个 由气压 转换至 液 压的控制单元 。正常运行时 ,模板前物料压力为 4 . 6 MP a , 当液 压 缸漏 油 时 ,刀轴 向前 的推 力 会 下 降 , 导 致 推 力不 足 。 当模 板 后 树 脂 压 力 大 于进 刀 压力 后 ,就 会 发生退 刀现 象 。
( 2 ) 油 路带 气
液 压 油 在 工 作 时 必 须 保 证 无 气 体 。若液 压 油
铝进 入树脂 中造成色粒 ;④树脂下料 系统氧含量 高,导致物料在高温和氧的作 用下发生 了分解 ;
第9 期
张鑫 挤压造粒机组 常见故 障分析 及处理
一 5 5.
⑤ 因异常 而进 入系 统 的其他 物 质造 成 色粒 。
相 对 较 大 的液 压 缸 时 ,会 发 生 体 积变 化 ,造 成 进 刀压 力不 稳 ,从而 引起 刀轴跳 动 。
( 3 1 进 刀不及 时
切 粒 机 开 车 过 程 中 , 需 要 手 动 进 行 切 粒 室
锁 紧 。锁 紧切 粒 室 与 切 粒机 启 动之 间有 一 个 短 暂 的 时 间 间 隙 ,在 此 期 间 ,模 板 依 然 会 流 出部 分 树 脂 , 待通 水 进 刀 后 ,树 脂 冷 却粘 在 切 刀 盘 上 ,形 成 垫 刀 。 因此 在 进 行 合模 操 作 时 ,应 尽 可 能 将模
产 生蛇 皮 粒 的主 要 原 因 是 切 刀 刀 刃 不 锋 利 或 刀 刃 背 面 不 光 滑 。切 下 的物 料 不 能 及 时 与 切 刀脱 离 , 随着 切 刀 不 断 切 下物 料 ,最 终 形 成蛇 皮状 物
Hale Waihona Puke 出 ,进 而 导 致 整 个 切 粒 室和 后 系 统 管 线 被 物 料 堵 满 ,发生 “ 灌 肠 ”事故 。
挤压机运行故障原因分析及解决方案

挤压机运行故障原因分析及解决方案设计能力 60 t/h 的造粒机组是国内引进大型挤压造粒机组之一,该机组是某大型煤炭深加工项目 35 万 t/a聚丙烯装置的配套设备。
在运行过程中,其自动控制系统存在一些需要改进和调整的地方,特别是造粒机组运行过程中经常联锁停车,经过反复分析研究,最终找到问题所在,并制定出相应的解决方案。
该机组主要由主电动机、减速箱、筒体、熔融泵、换网器、水下切粒机、干燥器、块料分离器以及颗粒振动筛等主要设备组成。
项目基本情况工艺流程简介造粒机组示意如图 1 所示,聚合单元生产的聚丙烯粉料由脱气仓进行脱活、干燥后,经粉料输送鼓风机送至造粒单元进料仓,粉料与助剂经过配置并在规定时间内充分混合,通过助剂计量称进入筒体。
聚丙烯粉料和助剂在筒体中充分混炼、熔融和均化,熔融聚丙烯经熔融泵增压,通过换网器过滤,由水下切粒机切粒。
切粒前产品的熔融指数用 MFR 在线测定仪测定。
熔融聚丙烯经过切粒机模板束状挤压后进入切粒室,旋转的切刀将聚丙烯切成小颗粒。
由于与颗粒冷却水接触,颗粒立即固化,同时由颗粒水送出切粒室。
颗粒经块料分离器把大的或不均匀的块料分离出来,其余送入颗粒干燥器中离心干燥,将颗粒与水完全分离。
另外,颗粒干燥器排风扇将空气吹入,加快带走颗粒表面的水分。
干燥的颗粒送到振动筛进行筛分,大颗粒和小颗粒均被筛掉,合格的颗粒送到颗粒料斗中。
最后由风送系统输送到料仓进行掺和包装。
机组 PLC 控制系统设计造粒机组的控制系统采用西门子公司的 PCS7 系统来实现。
整个造粒系统的电源模块、中央处理器、通信均采用冗余结构,分布式 IO 模块。
32 路数字输入模块12 块,32 路数字输出模块 10 块,8 路模拟输入模块 10 块,8 路模拟输出模块 10 块,24 路 F-DI4 安全模块,6 路 F-AI 安全模块 3 块,10 路F-DO 安全模块 4 块。
共有数字量输入点 372 个,数字量输出点 253 个,模拟量输入点 192 个,模拟量输出点 34 个,同时设计了与 PC 上位机通信的接口。
挤出造粒四大常见问题及解决对策

挤出造粒四大常见问题及解决对策一、断条1.原料有杂料,检查下料口的物料中是否含有杂料。
2.塑化不良,需提高加工温度。
(对于玻纤增强复合材料而言,往往是由于温度过高引起的。
)3.抽真空的力度不够,检查真空的运转是否良好,密封是否达到要求;密封是否达到要求4.过滤网堵塞,换过滤网。
5.口模孔数不对,料流失衡。
6.未加多孔板(玻纤类产品除外),熔体扰动而造成断条,断条主要集中在左侧。
7.挤出压力太低,螺杆内的物料不充实,需提高喂料频率、加大过滤网目数。
二、冒料没有塑化的物料1.适当降低喂料量或者降低螺杆转速。
2.升高前面段的温度,加快物料在机筒中的塑化;如增强料玻纤口前后的常规调节:输送及其熔化区温度适当提升5-10℃,将玱纤口后殌加热区温度适当调低10-20℃。
3.调整前面的螺杆组合,使前后输送平衡幵加快物料在机筒中的塑化。
塑化好的物料1.喂料太大;降低喂料频率。
2.真空盖开口。
3.机头网板出现炭化、填充等堵塞现象;清理机头。
4.螺杆排列错误(比如反向螺纹块的位置不排气口的位置过于接近,一般需要间隔一个螺纹的距离)。
三、粒子外观1.粒子两端的有孔问题。
两端都有孔:说明料里含的低分子物质戒水份较多,真空排气没抽干净戒原料含的低分子戒水成分较多。
只有一端有孔:说明料里含的低分子物质戒水份较少,没有严格要求时可以接受。
解决:前处理(干燥、密封等);加强真空排气(同时要考虑到螺杆设计);提高水槽温度。
2.粒子发泡。
出过高,原料成分的分解等。
原料含水分过高;原料(较差的副牌料)不耐温或成分使用不当,相互间化学反应而发;现多个孔,或者表面粗糙真空度不够;温度3.颗粒表面光滑平整问题。
颗粒表面光滑平整,要看所用的原材料的成分——玻纤、无机矿物、表面较粗燥的阻燃剂等物质。
但相比对下,同个料批次有差异,原因有:1)不均匀——数量多?时间短?机器?加工温度不够,塑化不好;螺杆组合不合理戒转速低,剪切不够,物料熔化不好;润滑剂过多戒加工特征特殊(如滑、低熔点),物料表面打滑剪切无效;2)机器问题,如模孔不平整、不够光滑等;3)原料成分间相容性不好(也包括色粉色母在内),出现分层、析出等。
挤出造粒现场常见异常及处理
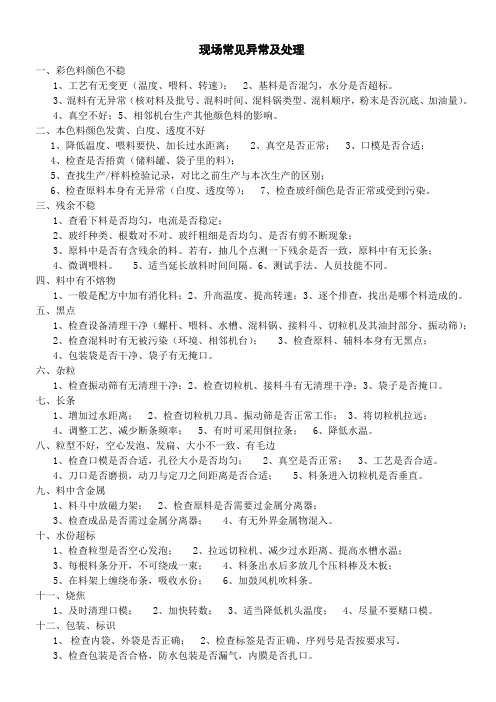
现场常见异常及处理一、彩色料颜色不稳1、工艺有无变更(温度、喂料、转速);2、基料是否混匀,水分是否超标。
3、混料有无异常(核对料及批号、混料时间、混料锅类型、混料顺序,粉末是否沉底、加油量)。
4、真空不好;5、相邻机台生产其他颜色料的影响。
二、本色料颜色发黄、白度、透度不好1、降低温度、喂料要快、加长过水距离;2、真空是否正常;3、口模是否合适;4、检查是否捂黄(储料罐、袋子里的料);5、查找生产/样料检验记录,对比之前生产与本次生产的区别;6、检查原料本身有无异常(白度、透度等);7、检查玻纤颜色是否正常或受到污染。
三、残余不稳1、查看下料是否均匀,电流是否稳定;2、玻纤种类、根数对不对、玻纤粗细是否均匀、是否有剪不断现象;3、原料中是否有含残余的料。
若有,抽几个点测一下残余是否一致,原料中有无长条;4、微调喂料。
5、适当延长放料时间间隔。
6、测试手法、人员技能不同。
四、料中有不熔物1、一般是配方中加有消化料;2、升高温度、提高转速;3、逐个排查,找出是哪个料造成的。
五、黑点1、检查设备清理干净(螺杆、喂料、水槽、混料锅、接料斗、切粒机及其油封部分、振动筛);2、检查混料时有无被污染(环境、相邻机台);3、检查原料、辅料本身有无黑点;4、包装袋是否干净、袋子有无掩口。
六、杂粒1、检查振动筛有无清理干净;2、检查切粒机、接料斗有无清理干净;3、袋子是否掩口。
七、长条1、增加过水距离;2、检查切粒机刀具、振动筛是否正常工作;3、将切粒机拉远;4、调整工艺、减少断条频率;5、有时可采用倒拉条;6、降低水温。
八、粒型不好,空心发泡、发扁、大小不一致、有毛边1、检查口模是否合适,孔径大小是否均匀;2、真空是否正常;3、工艺是否合适。
4、刀口是否磨损,动刀与定刀之间距离是否合适;5、料条进入切粒机是否垂直。
九、料中含金属1、料斗中放磁力架;2、检查原料是否需要过金属分离器;3、检查成品是否需过金属分离器;4、有无外界金属物混入。
- 1、下载文档前请自行甄别文档内容的完整性,平台不提供额外的编辑、内容补充、找答案等附加服务。
- 2、"仅部分预览"的文档,不可在线预览部分如存在完整性等问题,可反馈申请退款(可完整预览的文档不适用该条件!)。
- 3、如文档侵犯您的权益,请联系客服反馈,我们会尽快为您处理(人工客服工作时间:9:00-18:30)。
挤压造粒机常见故障及处理' ?) Q! D3 v' z! J2 v2 ]0 S 挤压造粒机组集机、电、仪高度一体化,自动化控制水平高。
因此,在实际运行中将出现较多难以诊断的故障,导致处理时间过长,从而影响整套聚丙烯装置的正常运行,大大地降低了生产经济效益。
* @; w! ]1 O6 { 在挤压造粒机组中,导致挤压造粒机组在运行中出现摩擦离合器脱开,机组联锁停车的原因可分为四大类:& l9 O" |: P; i" x1 e& p \' k主电机系统故障5 _) v) \) z7 Y7 S2 x1、主电机扭矩过高或过低;2、主电机转速过低;3、主电机轴承温度过高;4、主电机绕组温度过高;5、主电机水冷的冷却器出入口温度过高;6、主电机轴承润滑油泵出口流量过低;7、主电机轴承润滑油泵出口压力过低;8、主电机水冷的冷却器水泄漏量过高等。
3 `& L$ ?, }1 k/ c9 y+ @$ J9 z- v: W2 _- B' r g传动系统故障; S6 U) s# u7 n) C- A+ r% g/ }9 w/ p( F0 z, X% f1、齿轮箱变速杆位置偏离;2、摩擦离合器的仪表风压力过高;3、摩擦离合器速度差过大;4、齿轮箱润滑油泵出口压力过低;5、齿轮箱润滑油泵出口油温过高;6、摩擦离合器内部故障等。
! ~0 g( e# s! ^ b; A* O1 b/ Q/ b t2 a7 q; _9 x挤压造粒机螺杆工艺段故障& z% k; e* S( z% X5 ?( n' G! `/ h9 `# q" P! ]2 H5 p* ~( o1、节流阀前后熔体压力过高;2、机头熔体压力过高;3、换网器前后熔体压差过大;4、开车阀转动故障等。
2 `* C. B9 |8 q# X A. |) g4 D* w! w2 i% }. f水下切粒系统故障; N. h6 l9 Z: C% j9 Z- K/ r: z* k. b: O* G4 G1、切粒电机绕组温度过高;2、切粒机转速过低;3、切粒机扭矩过高;4、颗粒水旁通自动切换故障;5、颗粒水压力过高或过低;6、颗粒水流量过低;7、切粒机夹紧螺栓未把紧;8、切粒室旁路水阀未关;9、切粒机液压夹紧压力过低;10、切粒电机故障;11、液压切刀轴向进给压力过低等。
! d& V8 [ @8 B- a& y. p, c: R- i& [3 h8 H- r! o在上述故障原因中,出现频次较多的有:主电机系统的主电机扭矩过高或过低;传动系统的摩擦离合器故障;挤压造粒机螺杆工艺段系统的熔体压力高;水下切粒机系统故障等。
下文将对这些常见的故障原因进行详细的分析,给出相应的解决方法。
( e# S9 G( Q3 f$ o$ P' y V; l. v! C% e常见故障原因分析及解决措施: Y1 ^' V" i0 L: m$ `& h# ~, m! f, x5 v主电机扭矩过高. a3 i7 [; b/ O* Y4 s) P% _6 |9 O; F$ H4 ]: v; b/ j原因分析:% J6 K) @' N! R' ~7 l' `% U5 ?1 e3 |$ U+ Y+ n9 S' p; L油润滑系统故障,主电机输出轴与齿轮箱出入轴对中不良,电机及离合器振动等原因都将损坏主电机轴承,导致扭矩过高。
此外,喂料负荷过大或物料熔融不良也都会导致主电机扭矩过高。
, R9 r1 K( ^) _3 A# e9 A O- c3 X) T6 Y1 \; [ I, a( y# P解决措施:6 x8 X. O3 I( Z" l) H0 E& r P) s2 m# l6 G7 X5 t! ?定期对润滑油系统进行检查、清洗,用振动测量仪和红外测温仪对主电机轴承进行测量并形成趋势图。
如果超趋势值,则测定主电机空转电流值或功率值是否超规定值,判断是否应更换轴承。
定期检查主电机输出轴与齿轮箱输入轴之间的对中状况,首次开车或更换轴承运行三个月后必须检查对中情况。
进行电气测试检查,确定转子不平衡的原因;对离合器进行振动速度测试,如果超出规定值则应重新调整动平衡。
定期对筒体加热、冷却系统进行检查,保证物料受热均匀熔融充分。
如果挤压机开车瞬间,主电机功率曲线和熔体压力曲线瞬间增大,则表明喂料系统的喂料量瞬间过大,应减小喂料量。
/ j9 F/ ~5 V! ]0 i" b0 p1 n- D" q% B+ J) W% s0 B$ G主电机扭矩过低8 f' U- y( M$ u" E- r/ _$ L$ A5 y* B Q2 A% {; R! j* h7 a原因分析:7 M2 R) \+ q' z' O% V$ R, b3 x1 L2 D/ H. Y: W% s喂料系统故障使双螺杆空转将导致主电机扭矩过低。
# |3 p0 \! K# u1 H) ?2 u7 Q" P& y: [" v7 s3 X, t$ N解决措施:* n2 J8 Z, c( t2 d3 y7 W. O& z* `' D$ h) }检查判断添加剂系统或主物料下料系统是否有故障,清理堵塞点。
5 Z1 S K6 n9 }0 c$ e, x% \% o+ ^2 V+ `: ?" _! ]* [8 E: q7 }/ s摩擦离合器故障4 I0 m- s0 W9 U" v8 D$ X$ b+ c& N& d9 M9 x4 f6 V原因分析:3 @0 n: y* T% K; `# D( {& R; [' s. s# d+ P$ n主电机瞬间启动电压过低,摩擦盘、摩擦片过热,摩擦盘与摩擦片老化,摩擦盘的空气压力过低等原因都能导致离合器脱开。
# ]( O. q4 t0 o5 g) v2 l3 w" A- q. R" a3 W$ C& l% U% Z解决措施:0 A6 u) L s$ a/ N& l4 n0 A! A$ [) l0 s5 c$ B! z 主电机启动时,应避开用电高峰,降低喂料负荷量,重新启动的间隔时间最短为30分钟;在夏季时,反覆两次以上启动主电机时,更应延长间隔时间或用风扇强制降温。
用仪表风吹扫并用抹布擦净摩擦片和摩擦盘表面灰迹,如果磨损较重或表面出现“玻璃化”现象时,应更换摩擦盘、摩擦片。
确认空气压力值是否能使摩擦盘与摩擦片相贴合。
# Z' G- @1 I$ \3 X# {5 |& a/ E, G8 \ b5 }* \& \. t" B2 n x熔体压力高# Y& [. @& L Y9 m. a! n d K0 b& e2 j原因分析:2 c5 r) r$ D+ L: Z$ c' J7 O& g: t* l5 w6 B2 ` w/ m( Z 过滤网目数高,聚丙烯粉熔融指数低且喂料量大,各段筒体温度低使物料熔融不彻底,模板开孔率低使机头物料挤出受阻等原因都能导致熔体压力过高。
8 t8 Q: I- C4 N. `$ O5 E$ q) b0 A# [0 a/ u( y解决措施:$ b. x; i* {; ^) t5 ^) l% k5 f& Z5 w- V! O: @. r1 k: Q2 c1 O$ ?. d% q 生产低熔融指数产品时,应使用低目数的过滤网,增加节流阀开度以减少背压;及时更换过滤网,监控各种添加剂的质量及聚丙烯粉料中灰份含量。
降低喂料负荷量。
在不影响挤压产品质量的条件下,提高各段筒体温度,使聚丙烯熔体温度提高,加大物料流动性。
挤压机停车之后,提高机头温度并恒温一段时间后,彻底冲洗清理模板。
2 m) d" @! h7 x8 w9 b& y0 a3 M6 \) g# N# Q3 X6 F; ?水下切粒系统故障- m% M- j8 W. D7 O" f- n2 Y R0 C [6 T9 b3 v+ b原因分析:9 \" m l7 F9 D- {" N& G* {: ^6 r" Q# _切刀磨损过量或切刀刃口损伤,颗粒水流量过低,切粒机振动过大,切刀与模板贴合不紧,物料熔融指数波动较大使出料流速不一致,颗粒水温度过高等原因都能导致水下切粒系统停车从而造成整个机组联锁停车。
# O. b7 o* h+ z+ x2 X- Z X) D* }# r7 i, h. X# l' w解决措施:- t$ O% z" D; c$ T/ L2 T' g- C' y0 V7 R/ I5 a$ G5 n停车后,目视检查切刀刃口是否磨损过量或有损伤,如果有则应全部更换切刀。
检查并确认颗粒水是否内漏,颗粒水罐过滤器及冷却器是否堵塞,如果堵塞应人工清理;检查颗粒水泵的出入口压力是否正常,如果不正常则应检修颗粒水泵及泵管线上的阀门。
检查刀轴与切粒电机之间的对中是否超差,刀轴的轴承组件是否有损坏,切刀转子动平衡是否失衡。
在运行中检查切粒小车四个移动轮与导轨之间的接触是否有间隙。
控制聚丙烯粉中的挥发份,消除流经模板孔时对切刀及切刀轴产生的振动。
降低模板处的热油温度,检查筒体及模板温度分布,筒体冷却水的流量、压力及温度是否正常;确认“水、刀、料”到达模板处的时间设定,防止颗粒水过早到达模板使模板孔冻堵。
切粒机合上机头后,应快速把喂料量提升到挤压机的设定负荷。
) i+ ^. {. F0 G- A) x若能将以上故障原因点与联锁的逻辑关系结合起来汇编成故障诊断软件,则能为该机组的操作、检修及管理提供快捷、直观的参考和帮助。