挤出成型常见故障的排除
挤塑常见问题及处理

2.填充料分散性差未塑化,杂质
1. 原料预热干燥
2. 换料,调节温度,清洁原料
管内壁有焦粒
1. 挤出机机头与口模内壁不干净
2. 局部温度过高
3.口模积料严重
1.清模
2. 检查热电偶是否正常。
3. 清模,适当降低口模温度
外径或壁厚随时变化
1. 挤出速度变化
2.牵引速度发生变化或打滑
3.下料不稳(回料粒径不均)
管壁黑点杂质
(1)原料中混入杂质
(2)过滤网破裂
(3)机头升温时间过长,物料分解
(1)更换原料
(2)更换过滤网
(3)清理机头
(4)降低机头温度
(5)速度放慢
管壁有气泡
(1)原料受潮
(2)黑母料中含低挥发物
(1)烘干原料
(2)更换色母料
壁划伤及烂洞
(1)绕带时被地角螺栓划伤
(2)冷却板或水箱内有杂物
将地角螺栓盖住
1.料温低
2.温度过高,原料分解
1.提高料温
2.清理模具,降低温度
管材开裂
1.机头温度低,挤出速度快Βιβλιοθήκη 2.冷却水太大1.升温,降速
2.减小冷却水流量
管材圆度不好,弯曲
1. 口模,芯模中心位置不正
2. 机头温度四周不均
3. 冷却水离口模太近
4. 冷却水喷淋力度过大
5.冷却水喷淋太小
6.水位过高
7.牵引机压力过大
1. 干燥原料
2.消除气泡。调整工艺温度。
外表面呈现光亮透明的块状(俗称眼晴)
1.机头温度过高
2.冷却水太小或不足,或不均匀
1. 降低机头温度
2.冷却水开大或清理定径套
聚丙烯管材挤出成型故障的排查

聚丙烯管材挤出成型故障的排查(3)螺杆温度太高.应适当降低.?内壁I凸不故障分析及排除方法:(1)螺杆转速太快.应适当减慢.(2)螺杆温度太高.应向螺杆内通人冷水或冷风,适当降低螺杆温度.l故障排查I?表面划痕故障分析及排除方法:(1)口模内壁有残存余料.廊清理机头,去除存料.(2)模15碰毛.应去除毛刺,研磨修光.聚丙烯管材挤出成型故障的排查?外壁毛糙故障分析及排除方法:(1)机头温度太低.应适当提高.(2)冷却定型环供水量太多.应适当减少.(3)原料内混入杂质.应清洁原料或换用新料.(4)定径套上粘附杂质.应清除杂质或调换定径套.?局部托薄透明故障分析及排除方法:(1)机头温度太高.应适当降低.(2)冷却定型环供水量太小.应适当加大.●?管壁太厚或太薄故障分析及排除方法:(1)牵引速度太快或太慢.应适当控制牵引速度.(2)挤出量太大或太小.应适当调整挤出量.?内壁不光滑故障分析及排除方法:(1)芯模上粘附了杂质或光洁度太差.应清除杂质或提高芯模的表面光洁度.(2)气塞橡皮不圆,带有尖角.应换用新的气塞.?内壁凹坑(见图)故障分析及排除方法:(1)原料潮湿.应进行预干燥处理.(2)压缩空气中带有冷凝水.应设法减少气体中的水分含量,如降低环境湿度等.?内壁有螺纹或竹节故障分析及排除方法:(1)机头温度不均匀或局部温度太高.应调整均匀.(2)压缩空气压力太低.应适当提高.?拉断或拉不出故障分析及排除方法:(1)机头设计不合理.应进行修整.(2)冷却定型环供水量太大或太小.应适当控制.(3)压缩空气供给量太大.应适当减小.(4)气塞橡皮太硬.应换用新的气塞.(5)牵引速度太快.应适当减慢.?椭圆及弯曲故障分析及排除方法:(1)芯模和口模不同心.应调节相互间隙,使之同心.(2)机头加热不均匀.应调整加热温度,使之均匀.(3)管材周围冷却水的供水量不均匀.应适当调整冷却水流向和流量.(4)管材浮力太大.应改变冷却方法,减少浮力,如采用风冷或风,水结合的冷却方法.(5)牵引机橡皮输送带问隙太小,夹得过紧.应调整输送带间隙.(6)机头,冷却水槽和牵引机不在一条直线上.应适当调整三者的相对位置,使之排列在一条直线上. 睡望!!墅堕2(3(36/'67:3。
挤出机常见故障及问题处理
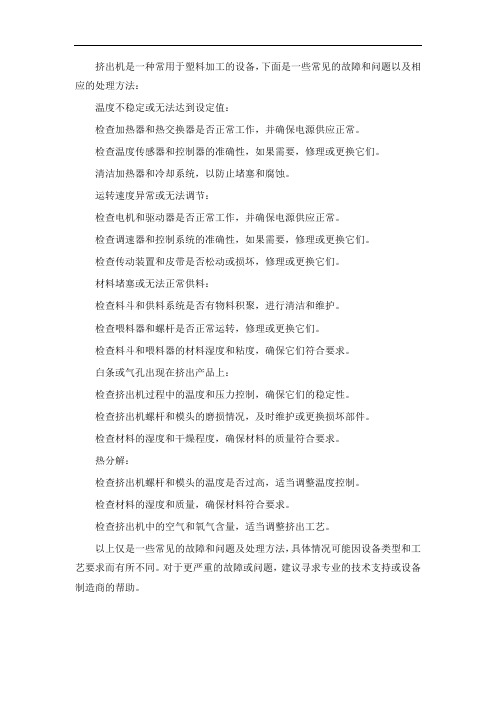
挤出机是一种常用于塑料加工的设备,下面是一些常见的故障和问题以及相应的处理方法:
温度不稳定或无法达到设定值:
检查加热器和热交换器是否正常工作,并确保电源供应正常。
检查温度传感器和控制器的准确性,如果需要,修理或更换它们。
清洁加热器和冷却系统,以防止堵塞和腐蚀。
运转速度异常或无法调节:
检查电机和驱动器是否正常工作,并确保电源供应正常。
检查调速器和控制系统的准确性,如果需要,修理或更换它们。
检查传动装置和皮带是否松动或损坏,修理或更换它们。
材料堵塞或无法正常供料:
检查料斗和供料系统是否有物料积聚,进行清洁和维护。
检查喂料器和螺杆是否正常运转,修理或更换它们。
检查料斗和喂料器的材料湿度和粘度,确保它们符合要求。
白条或气孔出现在挤出产品上:
检查挤出机过程中的温度和压力控制,确保它们的稳定性。
检查挤出机螺杆和模头的磨损情况,及时维护或更换损坏部件。
检查材料的湿度和干燥程度,确保材料的质量符合要求。
热分解:
检查挤出机螺杆和模头的温度是否过高,适当调整温度控制。
检查材料的湿度和质量,确保材料符合要求。
检查挤出机中的空气和氧气含量,适当调整挤出工艺。
以上仅是一些常见的故障和问题及处理方法,具体情况可能因设备类型和工艺要求而有所不同。
对于更严重的故障或问题,建议寻求专业的技术支持或设备制造商的帮助。
管材挤出成型常见故障及排除方法
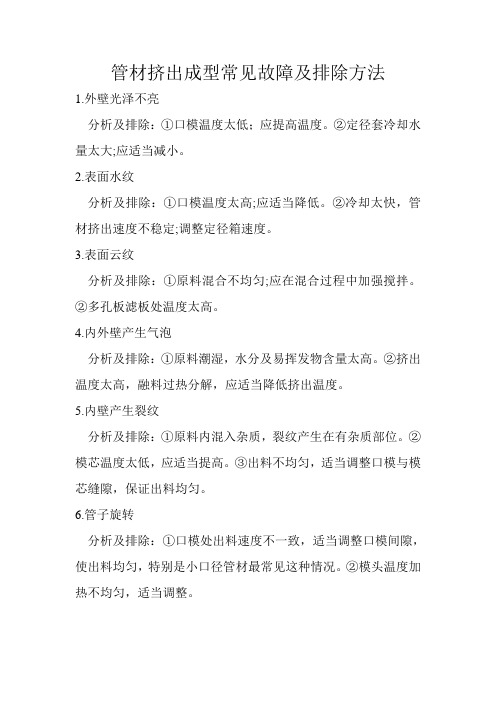
管材挤出成型常见故障及排除方法
1.外壁光泽不亮
分析及排除:①口模温度太低;应提高温度。
②定径套冷却水量太大;应适当减小。
2.表面水纹
分析及排除:①口模温度太高;应适当降低。
②冷却太快,管材挤出速度不稳定;调整定径箱速度。
3.表面云纹
分析及排除:①原料混合不均匀;应在混合过程中加强搅拌。
②多孔板滤板处温度太高。
4.内外壁产生气泡
分析及排除:①原料潮湿,水分及易挥发物含量太高。
②挤出温度太高,融料过热分解,应适当降低挤出温度。
5.内壁产生裂纹
分析及排除:①原料内混入杂质,裂纹产生在有杂质部位。
②模芯温度太低,应适当提高。
③出料不均匀,适当调整口模与模芯缝隙,保证出料均匀。
6.管子旋转
分析及排除:①口模处出料速度不一致,适当调整口模间隙,使出料均匀,特别是小口径管材最常见这种情况。
②模头温度加热不均匀,适当调整。
7.管子弯曲
分析及排除:①管壁厚薄不均匀,调整口模间隙。
②冷却太慢,加大冷却水量,提高冷却速率。
③冷却水槽安放不正。
8.外径不稳定
分析及排除:①压缩空气控制不正常,气压不稳定,应检查供气系统。
②牵引速度不均匀,检查牵引设备使之平稳不打滑。
聚氯乙烯管材挤出成型故障的排除

(4)螺杆转速太快。应适当减慢。
(5)螺杆温度太高。应在螺杆内部打孑L后向螺杆内通人冷水或冷风,降低螺杆温度
内壁凹凸不平
(1)螺杆温度太高。应适当降低。
(2)螺杆转速太快。应适当减慢
内壁有规则螺杆印迹
(1)螺杆温度太高。应向螺杆内通人冷水或冷风,进行降温处理。
2.软管挤出故障的排除
故障名称
成 因 及 对 策
表面皱纹
(1)流料产生脉冲状流动。应适当调整挤出速度。
(2)冷却水温度太高。应开大冷却水阀门,增加供水量。
(3)口模周边温度不均匀。应检查口模加热器是否损坏,将温度调整均匀。
(4)牵引速度太慢。应适当加快
表面黑纹
(1)机头或料筒温度太高。应适当降低。
(2)过滤板未清理干净。应重新清理
(1)螺杆转速太快。应适当减慢。
(2)螺杆温度太高。应向螺杆内通人冷水或冷风,适当降低螺杆温度
内壁粗糙
(1)芯模温度偏低。应适当提高。
(2)料筒温度太低。应适当提高。
(3)螺杆温度太高。应适当降低
管径不均(失圆)
(1)定型套内径不均。应更换或校正定型套。
(2)冷却不充分。应提高冷却系统的冷却效率及适当降低成型温度。
(2)冷却定型环供水不足,水温较高。应适当增加供水量。
(3)牵引速度太慢。应适当加快。
(4)口模周边出料不均匀。应适当调整口模料缝隙
表面黑纹
(1)原料内的炭黑及稳定剂分散不匀。应改进混和,加强搅拌,提高分散性能。
(2)原料流动性能太差。应改进原料配方。
(3)料筒靠近机头部位及过滤板处的温度太高。应适当降低。
塑料挤出机常见故障排查方法

塑料挤出机常见故障排查方法塑料挤出机是一种常用的塑料加工设备,用于将塑料颗粒通过加热和挤压形成所需的塑料制品。
然而,由于长期使用或操作不当,挤出机可能会出现各种故障。
本文将详细介绍塑料挤出机常见故障的排查方法,并给出相应的解决方案。
一、料筒温度过高或过低1. 问题描述:塑料挤出机的料筒温度异常,可能过高或过低。
2. 解决方法:首先,确保温控仪表准确,校正温度显示。
然后检查加热器是否正常工作,如若发现异常应及时更换或修理。
对于温度过高的情况,可以适当减少电热圈加热功率或降低进料量;对于温度过低的情况,可以增加电热圈加热功率或增大进料量。
二、螺杆堵塞1. 问题描述:螺杆可能会因塑料熔体冷却或混料不均匀而堵塞。
2. 解决方法:首先,检查挤出机出口处是否有异常,如有异常,应检查切刀、冷却器和水温控制系统是否正常。
其次,排空螺杆中塑料残留物,清理挤出机内部,并确保塑料熔体的温度和湿度适中,避免堵塞现象的发生。
三、过度磨损1. 问题描述:长时间使用后,螺杆和机筒可能会出现过度磨损。
2. 解决方法:定期检查螺杆和机筒的磨损情况,如有需要及时更换。
在正常操作过程中,保持合适的塑料颗粒大小和质量,避免对螺杆和机筒造成过度磨损。
四、挤出机异常噪音1. 问题描述:挤出机工作时会产生噪音,若噪音过大可能存在异常。
2. 解决方法:检查挤出机螺杆、传动系统、润滑系统以及附件是否正常。
对于松动的零部件,应及时拧紧;对于磨损的零部件,应及时更换。
合理选择润滑油,并定期对润滑系统进行维护保养。
五、过度震动1. 问题描述:挤出机在工作过程中过度震动,可能会导致设备损坏。
2. 解决方法:检查挤出机的基础支撑是否稳固,若不稳固应及时加固。
同时,检查螺杆传动部分和主机密封部分是否正常,如有异常应进行相应的维修操作。
六、塑料制品尺寸不准确1. 问题描述:制造出的塑料制品尺寸不符合要求。
2. 解决方法:首先,检查模具和挤出机的进料系统是否合理,确保塑料颗粒均匀进入挤出机。
棒材挤出成型故障的排除
段棒材芯部会出现无数小泡孔,产生“白芯”,造成报废
螺杆憋死(转不动)
(1)料筒温度太低。应适当提高。
(2)过滤板处及机头温度太低。应适当提高
棒材挤出成型故障的排除
故障名称
成因及对策
表面脱皮及黑点杂质
(1)原料内混有异物杂质。应彻底清除,净化原料。
(2)挤出温度太高,熔料过热分解产生碳化物。应降低料筒及机头温度,清洗料筒
表面斑痕及裂纹
(1)原料未充分干燥,水分含量偏高。应进行预干燥处理。
(2)料筒及机头温度太低。应适当提高挤出温度。
(3)冷却定型模温度偏低。应关小冷却水,适当提高冷却模温度。
(4)制动装置太松。应适当调紧
胀模及表面凹痕
(1)机头或冷却定型模温度偏高。应适当降低机头温度或增加冷却水的供给量。
(2)绝热隔板尺寸配合不当或变形损坏。应更换用于绝热和隔热的聚四氟乙烯垫圆。
(3)制动装置夹得太紧。应适当放松。
(4)螺杆转速偏快。应适当减慢
截面不圆
(1)冷却定型模或机头温度太低。应减少冷却水的供水量,提高冷却定型模温度,也可适
当提高机头温度。
(2)螺杆转速偏低。应适当提高。
(3)制动装置未夹紧。应适当调整
棒芯有泡孔
(1)挤出温度偏低或冷却定型模温度偏高。应适当提高料筒及机头温度或降低冷却定型
模温度。
(2)原料未充分干燥,水分含量太高。应进行预干燥处理。
(3)螺杆转速太高。应适当降低。
(4)制动装置未ห้องสมุดไป่ตู้紧。应将制动装置调得紧一些,增加阻力;同时,再将螺杆降至最低转
塑料管材挤出遇到的常见问题分析以及解决方式
塑料管材挤出遇到的常见问题分析以及解决方式一、壁厚不匀称1.口模板精准定位不准确因为模头内模板精准定位不准确,进而造成口模空隙不匀称,造成巴拉斯效应的水平不一样,制冷后造成管材的厚度不匀称。
防范措施:校准模板间定位销,调节口模空隙。
2.口模的成型长度短口模的成型长度的明确是挤出机头设计方案的重要。
针对不一样的管材,用成型长度来调节速度,使出入口料流匀称。
不然,管材可能出现薄厚不匀及皱褶。
防范措施:参照有关指南,适度延长口模成型长度。
3.模头加温不匀因为模头发热板或加热圈的加温温度不匀,促使模头内各部聚合物溶体黏度不一致,待制冷收拢后,便造成不匀称的厚度。
防范措施:调节发热板或加热圈的温度。
4.口模损坏不匀称口模是成型管材表层的零部件,与物料直接接触,会产生损坏和腐蚀状况。
口模往往产生不匀称的损坏是由口模内壁与分流锥不一样部位的物料流速、总流量、壁压、阻力不一样造成的。
塑料根据口模后能获得必须的样子和规格。
因此口模损坏将立即造成薄厚不匀。
防范措施:选用“节流与开源”的方式修复口模版空隙或分流锥角度。
5.物料带有残渣阻塞流道流道的阻塞促使口模出入口的流速不匀称,物料不稳定,进而造成管材壁厚不匀称。
防范措施:留意原料的清洁,清除模头流道内残渣。
二、弯折1.壁厚不匀称不匀称的厚度自然造成管材制冷后的弯折。
造成壁厚不匀称的缘故及防范措施参照所述1所示。
2.制冷不匀称或制冷不充足从口模挤压后的熔融料流在定型模中,根据制冷和真空吸附做好热交换和制冷定型,假如管材各部位制冷不一致,那么因为各部位制冷收拢快慢不一样会造成管材弯折;或是在管材出了定型模及定型水箱后,部位温度依然较高未彻底制冷,在再次制冷时,管材部位收拢仍会造成管材弯折。
防范措施:减少冷却水的温度,查验制冷水路是不是通畅,调节冷却水的总流量,提升或阻塞水孔。
3定型模阻力遍布不匀称熔融的物料在定型模中因为制冷收拢会造成必须的阻力,假如阻力遍布较差距,则会因部位阻力影响造成管材在定型模中情况不一致造成管材弯折。
挤出系统生产过程中常见故障及解决方法
1、加清机料停机
2、磨具温度过高
2、检查热电偶是否松动(接触是否正常工作)
2、查看热电偶(接触器)
13、管壁厚度不均匀
牵引速度不均、打滑,使得管径忽大忽小
检查橡胶块是否磨损
调整牵引机
14、成品发脆
螺杆转速太快
检查仪表是否失灵
降低转速,调节机头加热圈,提高温度
15、管子壁有分解黄线
6、加热圈不加热
不加热
加热圈是否损坏
断路器是否跳匣、检查接触器7Leabharlann 水泵压力小过滤器、水泵堵塞
查看过滤器、水泵是否堵塞
清洗过滤器、清理水泵
8、管子有裂口
锯齿坏、上刀太快
查看锯齿是否损坏、上刀是否太快
换锯片、调整上刀速度
9、管子有长短
1、行程开关(编码器)
1、检查计长行程开关(编码器)
换行程开关(编码器)
关闭总电源,打包机内是否有杂质
中顶刀经调整或拆装后应固定
19、主机直流电机出现火花
碳刷磨损
检查炭刷是否磨损
更换碳刷
20、加热温度偏芯
没有电压或加热圈坏
检查电压是否正常,加热圈是否损坏
电压正常更换加热圈
21、正常生产时管材内壁有气泡不光或毛糙
主机料筒没有真空或真空不足,原料温度偏高
检查真空泵是否损坏,排气孔是否有堵死,检测原料温度
2、低调整主机速度
3、螺杆间隙不佳
3、重新调整螺杆间隙
4原料不佳
4、更换原料
29、牵引机压不紧
塑料条磨损造成倾斜
更换塑料条
第2页
更换或修理真空泵,清理排气孔,降低原料温度
22、正常生产时外径偏小
挤出机常见故障的原因及方法
挤出机出现问题大概有几种情况,本文主要阐述焦烧与塑化不良两种现象。
1、焦烧的现象(1)温度反映超高,或者是控制温度的仪表失灵,造成塑料超高温而焦烧。
(2)机头的出胶口烟雾大,有强烈的刺激气味,另外还有噼啪声。
(3)塑料表面出现颗粒状焦烧物。
(4)合胶缝处有连续气孔。
2、产生焦烧的原因(1)温度控制超高造成塑料焦烧。
(2)螺杆长期使用而没有清洗,焦烧物积存,随塑料挤出。
(3)加温时间太长,塑料积存物长期加温,使塑料老化变质而焦烧。
(4)停车时间过长,没有清洗机头和螺杆,造成塑料分解焦烧。
(5)多次换模或换色,造成塑料分解焦烧。
(6)机头压盖没有压紧,塑料在里面老化分解。
(7)控制温度的仪表失灵,造成超高温后焦烧。
3、排除焦烧的方法(1)经常的检查加温系统是否正常。
(2)定期地清洗螺杆或机头,要彻底清洗干净。
(3)按工艺规定要求加温,加温时间不宜过长,如果加温系统有问题要及时找有关人员解决。
(4)换模或换色要及时、干净,防止杂色或存胶焦烧。
(5)调整好模具后要把模套压盖压紧,防止进胶。
1、塑化不良地现象(1)塑料层表面有蛤蟆皮式地现象。
(2)温度控制较低,仪表指针反映温度低,实际测量温度也低。
(3)塑料表面发乌,并有微小裂纹或没有塑化好地小颗粒。
(4)塑料的合胶缝合的不好,有一条明显的痕迹。
2、塑化不良产生的原因(1)温度控制过低或控制的不合适。
(2)塑料中有难塑化的树脂颗粒。
(3)操作方法不当,螺杆和牵引速度太快,塑料没有完全达到塑化。
(4)造粒时塑料混合不均匀或塑料本身存在质量问题。
3、排除塑化不良的方法(1)按工艺规定控制好温度,发现温度低要适当的把温度调高。
(2)要适当地降低螺杆和牵引的速度,使塑料加温和塑化的时间增长,以提高塑料塑化的效果。
(3)利用螺杆冷却水,加强塑料的塑化和至密性。
(4)选配模具时,模套适当小些,加强出胶口的压力。
- 1、下载文档前请自行甄别文档内容的完整性,平台不提供额外的编辑、内容补充、找答案等附加服务。
- 2、"仅部分预览"的文档,不可在线预览部分如存在完整性等问题,可反馈申请退款(可完整预览的文档不适用该条件!)。
- 3、如文档侵犯您的权益,请联系客服反馈,我们会尽快为您处理(人工客服工作时间:9:00-18:30)。
端部开裂或成锯齿状
1.口模端部熔料流动速度太慢
(1)应适当增大端部定型段的人口处。
(2)应减小端部定型段的长度。
2.模唇温度控制不当
(1)应适当提高模唇温度。
(2)应在口模喷嘴的端部附近分别插入筒形加热器。
(3)应适当降低料筒温度,提高熔料粘度
进料不稳定
1.树脂在挤出机进料段打滑
(3)应将配混料在40—45~C下放置约lOh,使聚氯乙烯很好地吸收增塑剂,进行熟化处理。
2.混炼及挤出条件控制不当
(1)应适当调整挤出机的成型条件,使排气完全,充分脱除熔料中的易挥发物。
(2)应选用适当的螺杆类型,进行充分混合及混炼
3.型材形体结构设计不良
(1)应尽量使型材周边的壁厚对称均匀。
(2)应在厚壁截面内设置小面积的中空。
(3)壁厚悬殊不能太大。
4.配方设计不合理
(1)树脂牌号选用不当,分子量较低。应换用新料。
(2)再生料用量不当。应适当减少再生料及填料的掺混量。
(3)增塑剂用量太多。应适当减少。
(4)改性剂用量太少。应适当增加
(4)料斗内应安装搅拌器,防止搭桥。
(5)再生料必须定量掺混
尺寸不稳定
1.进料不稳定
应适当调整挤出机进料段和料斗部位的工艺条件。
2.牵引装置产生机械故障
(1)牵引机的电机转速太低。应适当提高。
(2)皮带或变速器打滑。应进行检修。
(3)型材在牵引辊或牵引履带上打滑。应适当调整夹紧力。
3.口模结构及定型装置设计或调整不当
(5)应清除定型模滑移面的锈斑
表面斑点及鱼眼
1.原料不符合成型要求
(1)应防止混用聚合度不同的聚氯乙烯原料。
(2)应防止混用熔体粘度不同的树脂。
(3)应控制再生料的掺混比例及混合工艺。
2.成型条件控制不当
(1)应选用适当的螺杆类型,需防止螺杆过热。
(2)在挤出过程中,应严格控制混人异物杂质。
(3)应采用金属网过滤熔料,同时增大熔料压力
(2)坯材应经鼓风机风冷后再进入定型模。
(3)在定型模内表面和型坯间不能留有间隙。
(4)应采用含氟材料处理定型模的滑移面。
2.定型模结构设计及操作不当
(1)在真定吸引孑L或缝隙的棱角部位应设置圆角。
(2)应改进定型模滑移面的冷却效果。
(3)应检查定型模是否长度太长,以及各定型模是否同心。
(4)应清理定型模的孔隙。
(1)应采用料斗于燥器将原料加热。
(2)应提高料斗底部及挤出机进料段的温度。
(3)应适当增加螺杆进料段长度,特别是在挤出聚酰胺及纤维素树脂时应考虑采取这一
措施。
(4)应在挤出机进料段的料筒上开槽。
2.树脂在料斗处供料不稳定
(])应选用粒径均一的树脂原料。
(2)原料温度应保持均一。
(3)送人料斗内的原料应保持较稳定的供给量。
1.金属的前处理不良
(1)应彻底清除金属表面的油渍。
(2)应在金属表面涂布粘合剂。
(3)应彻底清除金属表面的残留溶剂。
(4)应采用高频加热装置将金属升温到略高于熔料温度。
2.口模结构设计不合理
(1)在铁芯与熔料处应设置可以形成最大挤出压力的结构。
(2)应适当增加合流后共挤出段的距离。
(3)型坯山口模后应进行缓冷,不要急冷
2.定型模冷却不良
(1)应采用导热系数较大的黄铜制作定型模,改进其冷却效率。
(2)应降低冷却水的温度。
(3)应采用分离式定型模。
(4)在干法真空定型时,应在定型模人口处加少量水,改进滑移性能。
3.熔料温度太高
(1)应适当降低料筒温度。
(2)应向螺杆内通人冷却水或冷风,适当降低螺杆温度
与包覆金属粘接不良
熔料在口模内分解
1.熔料在料筒内过热
(1)应适当降低螺杆的压缩比。
(2)应使用渐变型螺杆,避免急剧压缩。
(3)应适当降低螺杆转速。
(4)应使用压缩空气冷却螺杆,适当降低螺杆温度。
2.口模结构设计不合理
(1)应适当增大口模流料导人部位,增大口模前端的压力。
(2)应尽量消除口模内的滞料死角。
(3)应尽量缩短口模长度,减少熔料在口模处的滞留时间
(1)应不增加筋部间隙,将熔料人口处扩大,提高熔料在筋槽中的流动速度。
(2)应尽量提高熔料在筋槽末端部分的流动速度。
2.筋槽内熔料大多
(1)应在口模筋槽内设置隔板使熔料分流。
(2)应加快牵引,并采用滑移定型模。
(3)应采用真空定型模,使筋部拉伸冷却。
3.成型速度太快
(1)应尽量减小口模的拉伸收缩率。
(4)应适当调整成型条件,使排气充分。
3.口模结构及定型装置设计不当
(1)应采用加有前端压力的口模。
(2)应适当减小牵引收缩率。
(3)定型装置应采用缓冷的方式,不要急冷。
(4)型坯与定型模不应有太大的摩擦
聚氯乙烯制品加热减量太大
1.原料处理不符合成型要求
(1)应采用加热减量小及分子量高的增塑剂。
(2)配混后应在45~C下熟化20h。
2.材料选择与成型条件不一致
(1)应选用熔体粘度较低、流动性能较差的原料。
(2)应适当提高料筒温度,降低口模温度。
(3)应适当降低挤出速度
表面条纹及云纹
1.原料不符合成型要求
(1)对于PVC原料,应适当降低熔料的流动性能。
(2)应避免混用不同颜色的树脂。
(3)应避免混用熔体流动速率或牌号不同的树脂。
(4)原料应进行预干燥处理。
(5)应适当提高熔料的流动性能。
(6)应适当降低挤出速度。
2.口模结构设计不合理
(1)应适当增大口模前端的压力。
(2)应适当增大口模定型段流料的导人部位。
(3)口模定型段应保持平滑。
(4)喷嘴出口处应设有0.2R的圆角
定型模出口处有纵向筋条
1.析出物粘附和堆积
(1)应适当降低熔料温度。
型材整体收缩太大
1.牵引收缩率太大
(1)应尽量减小口模的牵引收缩率。
(2)牵引收缩率太大时,应尽量提高熔料温度。
2.冷却不充分
(1)型材固化定型后,仍应充分冷却到室温以下。
(2)应适当降低冷却水的温度。
(3)对于中空型材和厚壁件,应适当增加冷却长度。
(4)应适当降低挤出及牵引速度
筋部收缩太大
1.口模筋槽内熔料流动太慢,筋槽受到拉伸Fra bibliotek聚氯乙烯制品的强
度及伸长率降低
1.原料处理不符合成型要求
(1)配混后应在40—45℃下熟化10—20h。
(2)应适当降低熔料的流动性能。
(3)应进行充分的混合及混炼。
(4)应在混合器内进行减压脱气。
2.成型设备及条件选定不当
(1)应选用混炼性能良好的螺杆类型。
(2)应使选用的挤出机混炼均匀。
(3)应尽量采用口模加有压力的大型挤出机。
(1)应适当降低口模的牵引收缩率。
(2)应在定型模人口前进行空气冷却。
(3)应在定型模不过热条件下充分冷却。
(4)应采用分离式定型模
型坯在定型模中滑 移不良
1.模唇处出料速度不稳定
(1)应修正口模定型段长度或定型段人口处,调节口模喷嘴处的出料速率。
(2)应在口模端部插入筒形加热器,局部调节熔料的流动。
异型及复合材挤出成型常见故障的排除
故障名称
成 因 及 对 策
表面熔接痕
1.口模结构设计不良
(1)在设置口模内的流道时应使熔料流量均匀。
(2)应适当增加口模前端的压力。
(3)应适当增加口模定型段长度。
(4)应在模芯支架后设置熔料池。
(5)应适当增大口模入口处的流道截面。
(6)应采用板式流道的突变型口模。
2.螺杆选型不正确及口模结构设计不当
(1)应选用混炼及混合性能良好的螺杆。
(2)口模内应设置熔料池或支管。
(3)应尽量采用板式流道的突变型口模。
(4)应适当增加过滤网的目数
表面光泽不良及纵向条纹
1.成型条件及原料处理不当
(1)应适当降低螺杆温度,防止其过热。
(2)应适当降低料筒温度,防止熔料过热。
(3)应适当减少正电性较强的钡(Ba)金属皂和钙(h)金属皂的用量。
型材弯曲变形
1.口模出料不均
(1)应修正口模,使口模出口处熔料的挤出速度均一,可增加口模定型段长度及增设阻流块。
(2)应减小拉伸收缩率。
2.冷却方法不当
(1)应提高厚壁处的冷却效率,加快固化速度。
(2)应减少薄壁处的冷却量或以热风加热,减慢固化速度。
(3)冷却水应保持一定的温度。
(4)定型模和牵引辊的中心位置应对正。
(3)应在混合器内于80~(2以上进行减压脱气。
(4)应进行充分混炼。
2.挤出条件控制不当
(1)应采用压缩比较高的螺杆。
(2)应合理控制成型条件,保证排气充分。
(3)应尽可能在高温、高压条件下挤出成型
聚氯乙烯残留单体
及苯二甲酸酯渗出过多
1.配合条件不当
(1)应采用干燥法去除部分残留单体。
(2)应在混合器内于80'E以上进行减压脱气,除去氯乙烯单体和游离苯二甲酸酯。