聚合物挤出常见问题
聚合物口模挤出计算机模拟中的高We数问题研究

(2)流体力学控制方程和本构方程组成的代数方程组中既包括椭圆型偏微分方程,又包括双曲线型偏微分方程,数值算法的不精确可能导致应力张量正定性的改变,这种类型的变化对椭圆型偏微分方程的解影响不大,但对双曲线型偏微分方程的解会造成非常大的误差。
(3)局部高应力梯度的存在,首先,由于局部流场法向应力的升高,导致应力边界层的存在,其中高应力梯度对计算精度有非常大的影响,特别是在耦合算法中。其次,流场中几何奇异点造成其附近非常高的应力,在某些情况下这些应力是不可积的。因此,应力分量所受HWNP的影响比速度分量严重得多。
算的We数推进到5左右。1989年Crmela[7]提出了一系列高分子流体流变学模型,这些模型都以与大分子取向有关的构造张量作为内部变量为基础,它们对聚合物熔体的描述比分子理论方法更宏观。1992年Guénette[8]用其中一个模型,采用Fortin和Zine[9]发展的一种基于Krylov-Newton方法的GMRES(Generalized Minimal RESidual Method)去耦算法,对4∶1平面收敛流动问题进行了计算机模拟,求解过程中对We数没有限制,这个构造张量模型如下:
图4应力沿“流线”积分示意
2.2.4拉格朗日—欧拉动态模拟
结合数值分析研究中心常用的拉格朗日方法和欧拉方法的优点,袁学锋等[21,22]发展起来一种拉格朗日—欧拉动态模拟方法。其独特之处是利用随时间移动的多边形网格来
跟踪流体单元在流场中的运动轨迹和变形状况,在拉格朗日步骤中根据流动单元的应变情况求解非线性应力项,而在任意时刻下,定义在网格上的流场物理量如速度、压力等可以在欧拉步骤中通过迭代控制方程得到。然后,再以时间步长移动网格到下一时刻,同时计算这一时刻的粘弹应力,如此循环。在应力的求解方面,该数值技术与流线方法非常相似。在他们
挤出机挤出不稳定原因
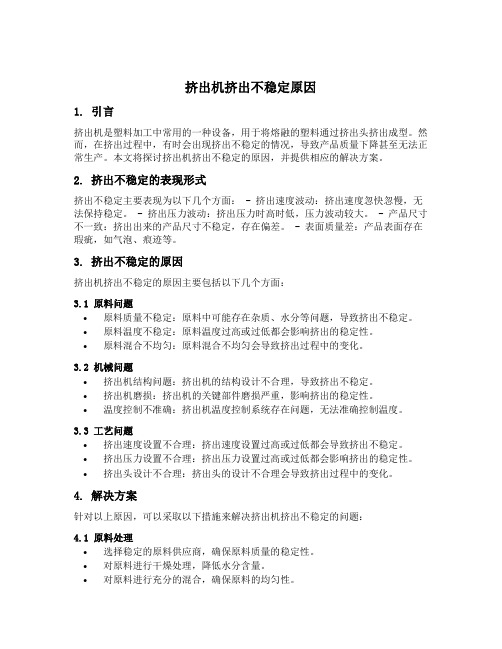
挤出机挤出不稳定原因1. 引言挤出机是塑料加工中常用的一种设备,用于将熔融的塑料通过挤出头挤出成型。
然而,在挤出过程中,有时会出现挤出不稳定的情况,导致产品质量下降甚至无法正常生产。
本文将探讨挤出机挤出不稳定的原因,并提供相应的解决方案。
2. 挤出不稳定的表现形式挤出不稳定主要表现为以下几个方面: - 挤出速度波动:挤出速度忽快忽慢,无法保持稳定。
- 挤出压力波动:挤出压力时高时低,压力波动较大。
- 产品尺寸不一致:挤出出来的产品尺寸不稳定,存在偏差。
- 表面质量差:产品表面存在瑕疵,如气泡、痕迹等。
3. 挤出不稳定的原因挤出机挤出不稳定的原因主要包括以下几个方面:3.1 原料问题•原料质量不稳定:原料中可能存在杂质、水分等问题,导致挤出不稳定。
•原料温度不稳定:原料温度过高或过低都会影响挤出的稳定性。
•原料混合不均匀:原料混合不均匀会导致挤出过程中的变化。
3.2 机械问题•挤出机结构问题:挤出机的结构设计不合理,导致挤出不稳定。
•挤出机磨损:挤出机的关键部件磨损严重,影响挤出的稳定性。
•温度控制不准确:挤出机温度控制系统存在问题,无法准确控制温度。
3.3 工艺问题•挤出速度设置不合理:挤出速度设置过高或过低都会导致挤出不稳定。
•挤出压力设置不合理:挤出压力设置过高或过低都会影响挤出的稳定性。
•挤出头设计不合理:挤出头的设计不合理会导致挤出过程中的变化。
4. 解决方案针对以上原因,可以采取以下措施来解决挤出机挤出不稳定的问题:4.1 原料处理•选择稳定的原料供应商,确保原料质量的稳定性。
•对原料进行干燥处理,降低水分含量。
•对原料进行充分的混合,确保原料的均匀性。
4.2 机械维护•定期检查挤出机的结构,确保其正常运行。
•及时更换关键部件,避免磨损对挤出的影响。
•对温度控制系统进行维护,确保温度的准确控制。
4.3 工艺优化•合理设置挤出速度,根据产品要求进行调整。
•合理设置挤出压力,根据产品要求进行调整。
PVC塑料异型材挤出异常现象的原因及解决思路
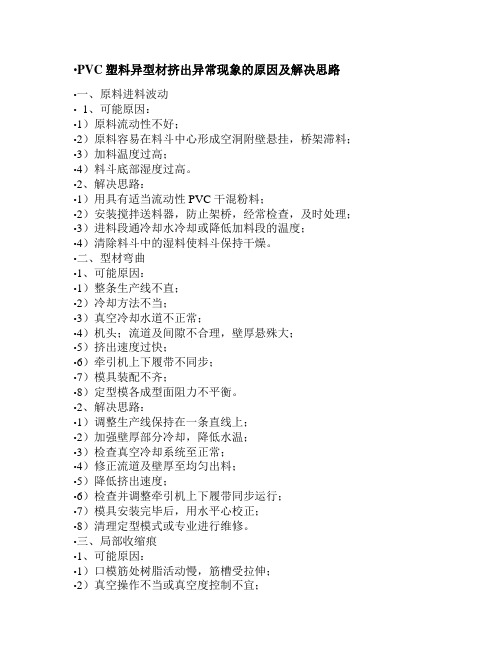
•PVC塑料异型材挤出异常现象的原因及解决思路•一、原料进料波动•1、可能原因:•1)原料流动性不好;•2)原料容易在料斗中心形成空洞附壁悬挂,桥架滞料;•3)加料温度过高;•4)料斗底部湿度过高。
•2、解决思路:•1)用具有适当流动性PVC干混粉料;•2)安装搅拌送料器,防止架桥,经常检查,及时处理;•3)进料段通冷却水冷却或降低加料段的温度;•4)清除料斗中的湿料使料斗保持干燥。
•二、型材弯曲•1、可能原因:•1)整条生产线不直;•2)冷却方法不当;•3)真空冷却水道不正常;•4)机头;流道及间隙不合理,壁厚悬殊大;•5)挤出速度过快;•6)牵引机上下履带不同步;•7)模具装配不齐;•8)定型模各成型面阻力不平衡。
•2、解决思路:•1)调整生产线保持在一条直线上;•2)加强壁厚部分冷却,降低水温;•3)检查真空冷却系统至正常;•4)修正流道及壁厚至均匀出料;•5)降低挤出速度;•6)检查并调整牵引机上下履带同步运行;•7)模具安装完毕后,用水平心校正;•8)清理定型模式或专业进行维修。
•三、局部收缩痕•1、可能原因:•1)口模筋处树脂活动慢,筋槽受拉伸;•2)真空操作不当或真空度控制不宜;•3)冷却水温过高;•4)局部冷却过快。
•2、解决思路:•1)清理口模修正模使口模内筋处流速加快或降低牵引速度;•2)调节真空度,或用夹头工具在灾坯进入定型模前在材料上戳小孔,使型材呈放开式,加强真空吸附;•3)降低水温,提高冷却效率;•4)关小局部冷却水。
•四、型材后收缩率大•1、可能原因:•1)牵引速度偏高;•2)定型模冷却不够;•3)机头温度过高;•2、解决思路:•1)调节牵引速度;•2)提高冷却效率;•3)降低机头温度;•五、制品尺寸、厚度时大时小•1、可能原因:•1)进料波动;•2)电热圈加热不正常;•3)牵引面不稳定,牵引电机打滑或速度波动;•4)混料不均匀;•5)模具间隙发生变化;•6)模头内有物料停滞。
聚合物成型工艺学复习重点及习题分析
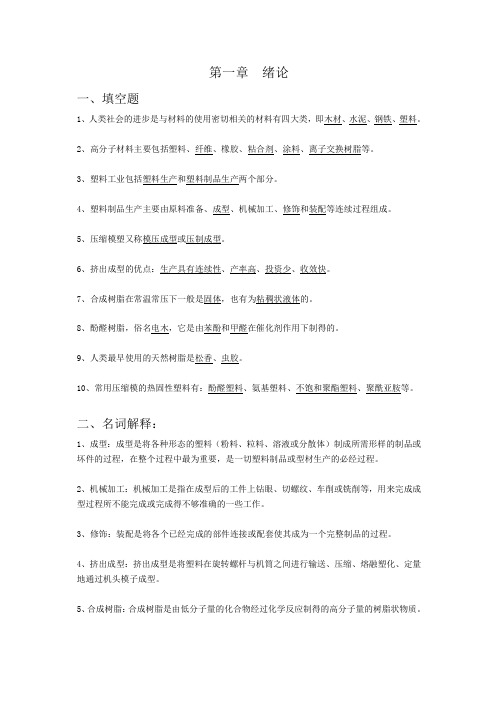
第一章绪论一、填空题1、人类社会的进步是与材料的使用密切相关的材料有四大类,即木材、水泥、钢铁、塑料。
2、高分子材料主要包括塑料、纤维、橡胶、粘合剂、涂料、离子交换树脂等。
3、塑料工业包括塑料生产和塑料制品生产两个部分。
4、塑料制品生产主要由原料准备、成型、机械加工、修饰和装配等连续过程组成。
5、压缩模塑又称模压成型或压制成型。
6、挤出成型的优点:生产具有连续性、产率高、投资少、收效快。
7、合成树脂在常温常压下一般是固体,也有为粘稠状液体的。
8、酚醛树脂,俗名电木,它是由苯酚和甲醛在催化剂作用下制得的。
9、人类最早使用的天然树脂是松香、虫胶。
10、常用压缩模的热固性塑料有:酚醛塑料、氨基塑料、不饱和聚酯塑料、聚酰亚胺等。
二、名词解释:1、成型:成型是将各种形态的塑料(粉料、粒料、溶液或分散体)制成所需形样的制品或坏件的过程,在整个过程中最为重要,是一切塑料制品或型材生产的必经过程。
2、机械加工:机械加工是指在成型后的工件上钻眼、切螺纹、车削或铣削等,用来完成成型过程所不能完成或完成得不够准确的一些工作。
3、修饰:装配是将各个已经完成的部件连接或配套使其成为一个完整制品的过程。
4、挤出成型:挤出成型是将塑料在旋转螺杆与机筒之间进行输送、压缩、熔融塑化、定量地通过机头模子成型。
5、合成树脂:合成树脂是由低分子量的化合物经过化学反应制得的高分子量的树脂状物质。
6、过程集中制:过程集中制是将塑料制品的加工工序所需要的各种设备分别集中起来进行生产的机制。
7、过程集中制:按照一种产品所需要的生产过程实行配套成龙的生产。
三、问答题1、塑料主要应用于哪些方面?答:塑料主要应用于农牧渔业、包装、交通运输、电气工业、化学工业、仪表工业、建筑工业、航空工业、国防工业、家具、日用品、玩具、医用等方面。
2、塑料制品生产目的是什么?答:塑料制品生产是一种复杂而又繁重的过程,其目的在根据各种塑料的固有性能,利用一切可以实施的方法,使其成为具有一定形状有价值的塑料制件和型材。
聚合物挤出中的流变学

聚合物挤出中的流变学——PPXCL 刘晓君1.0流变学流变学是研究材料变形和流动的科学。
希腊语中流变学被表示为"Panta Rei ",意思是:“所有物体的流动”。
事实上只要给予足够的时间,所有材料都能够流动。
有趣的是,挤出、注射成型和吹塑成型等过程中的聚合物材料的流动时间都在一个相同的数量级上。
在一个非常短的加工时间里,聚合物的表现象是固体,而从较长的加工过程来看,聚合物的行为则像是液体。
这种双重特性(液态-固态)称为粘弹性。
1.1粘度和融体流动指数粘度是最重要的流动特性,它表示流动的阻力,严格的说,是剪切的阻力。
假如将流体设想为一些运动的薄片,如图1.1,我们可以定义粘度为剪切应力和剪切速率的比值。
图1.1 简单的剪切流体γτνη===h A F //剪切速率剪切应力 (1.1) η : Pa *SF: 压力A: 面积ν: 速度h: 距离τ: Pa=(N/㎡)γ: S -1希腊字母τ (tau) 和 γ(gamma dot) 按惯例分别表示剪切压力和剪切速率, 流体在圆形管道或者两个金属平面间流动,剪切应力从中心轴的零到管壁最大值之间呈线性的改变;而剪切速率则呈非线性改变。
对两个金属平面之间的流体,速率剖面最大值在堆成平面,管壁处为零,如图1.2。
在SI 中,粘度的单位是Pa*S 。
在进入SI 之前,经常用Poise 作为粘度的单位(1 Pa ⋅s = 10 poise). 这里有一些其它有用的转换:1 Pa ⋅s = 1.45*10-4lb f s/in2 = 0.67197 lb m /s ft = 2.0886*10-2lb f s/ft 2水的粘度是10-3 Pa ⋅s 当最多的聚合体在挤出状态下融化可能会从102Pa ⋅s 到105Pa ⋅s 之间改变。
剪切应力的标准单位用Pa = (N/m 2) 或者 psi (英镑 (lb f ) /平方英寸) 表示,剪切速率单位为:s –1聚合物流体一个值得注意的特性就是他们的剪切变稀特性(也就是大家知道的假塑性)。
单螺杆挤出机的常见故障

单螺杆挤出机的常见故障
单螺杆挤出机是塑料加工中常用的设备,常见的故障包括但不限于以下几种:
1. 温度控制问题,挤出机需要在一定的温度范围内工作,如果温度控制系统出现故障,可能导致塑料材料无法达到理想的熔融状态,甚至造成塑料烧焦或结块。
2. 压力控制问题,挤出机在工作过程中需要保持一定的压力,如果压力控制系统出现问题,可能导致挤出的塑料产品外观质量不佳或者产量下降。
3. 螺杆磨损,长时间使用会导致螺杆磨损,造成挤出机的工作效率下降,甚至无法正常工作。
4. 挤出机结构问题,挤出机的结构件如螺杆、机筒等零部件出现损坏或磨损也会导致挤出机的故障。
5. 清洁问题,挤出机需要定期清洁和维护,如果清洁不到位或者维护不当,可能导致挤出机堵塞或者其他故障。
针对这些常见故障,我们可以采取一些预防和维护措施,比如定期对挤出机进行维护保养,注意温度和压力的稳定控制,及时更换磨损的零部件等。
另外,操作人员的培训和技术水平也是影响挤出机故障的重要因素,加强操作人员的技能培训和安全意识教育也是预防故障的重要手段。
希望以上内容能够帮助你全面了解单螺杆挤出机的常见故障及预防措施。
挤出机常见故障的原因及方法
挤出机出现问题大概有几种情况,本文主要阐述焦烧与塑化不良两种现象。
1、焦烧的现象(1)温度反映超高,或者是控制温度的仪表失灵,造成塑料超高温而焦烧。
(2)机头的出胶口烟雾大,有强烈的刺激气味,另外还有噼啪声。
(3)塑料表面出现颗粒状焦烧物。
(4)合胶缝处有连续气孔。
2、产生焦烧的原因(1)温度控制超高造成塑料焦烧。
(2)螺杆长期使用而没有清洗,焦烧物积存,随塑料挤出。
(3)加温时间太长,塑料积存物长期加温,使塑料老化变质而焦烧。
(4)停车时间过长,没有清洗机头和螺杆,造成塑料分解焦烧。
(5)多次换模或换色,造成塑料分解焦烧。
(6)机头压盖没有压紧,塑料在里面老化分解。
(7)控制温度的仪表失灵,造成超高温后焦烧。
3、排除焦烧的方法(1)经常的检查加温系统是否正常。
(2)定期地清洗螺杆或机头,要彻底清洗干净。
(3)按工艺规定要求加温,加温时间不宜过长,如果加温系统有问题要及时找有关人员解决。
(4)换模或换色要及时、干净,防止杂色或存胶焦烧。
(5)调整好模具后要把模套压盖压紧,防止进胶。
1、塑化不良地现象(1)塑料层表面有蛤蟆皮式地现象。
(2)温度控制较低,仪表指针反映温度低,实际测量温度也低。
(3)塑料表面发乌,并有微小裂纹或没有塑化好地小颗粒。
(4)塑料的合胶缝合的不好,有一条明显的痕迹。
2、塑化不良产生的原因(1)温度控制过低或控制的不合适。
(2)塑料中有难塑化的树脂颗粒。
(3)操作方法不当,螺杆和牵引速度太快,塑料没有完全达到塑化。
(4)造粒时塑料混合不均匀或塑料本身存在质量问题。
3、排除塑化不良的方法(1)按工艺规定控制好温度,发现温度低要适当的把温度调高。
(2)要适当地降低螺杆和牵引的速度,使塑料加温和塑化的时间增长,以提高塑料塑化的效果。
(3)利用螺杆冷却水,加强塑料的塑化和至密性。
(4)选配模具时,模套适当小些,加强出胶口的压力。
挤出机常见故障及对策
夺检查电动机轴承,加润滑油或更 换轴承。
6:挤出物料不稳
1)原料加料口“架桥”
^清除料斗下料口的架桥。
2)主电动机转速不均匀,有波动
^检查主电动机及控制系统。
3)加热冷却系统匹配不好或热电偶误 差太大
夺对加热功率进行调整,检查热电 偶的接触及安装情况,热电偶是 否损坏,必要时更换热电偶。
1)主电动机电源没有接通。
^检查主电动机电源接线。
2)加热升温时间不足或某加热器不工 作,造成扭矩过大,使电动机过 载。
^检查各段温度显示,确认预热升 温时间;或提高温度。
动机转动, 但螺杆不转动。
1)传动带松,打滑。
^调整两带轮中心距,张紧皮带。
2)齿轮箱故障
WI Number指导号:WI-009
Effective Date生效日期:Jun15, 2016
故障现象
产生原因
处理方法
3:螺杆有转速显示 但挤不出物料
9)电压不稳,变频器不稳有波动。
夺立即停机。
10)螺杆磨损了。
夺拆卸螺杆进行检查。
11)螺杆打滑
夺检查物料及性能(有的料容易打 滑,比如PP料)。
挤出机常见故障及对策
TROUBLE SHOOTING
WI Number指导号:WI-009
Effective Date生效日期:Jun15, 2016
目的:
明确告知作业员,当问题出现时应当采取的对策。
适用范围:
本指导针对任何操作挤出机的操作人员。
常见故障及对策:
故障现象
产生原因
处理方法
1:启动主电动机, 主电动机不动或瞬间 停机。
Signature签名:Signature签名:
浅谈聚乙烯装置挤压造粒机常见问题及解决方法
浅谈聚乙烯装置挤压造粒机常见问题及解决方法摘要:挤压造粒机是将粉料树脂经过加温熔融、挤压切割成颗粒状的重要设备,在聚乙烯生产中有着至关重要的作用。
因此,对于造粒机的常见故障我们要有一定的分析和处理能力。
本文列举了聚乙烯造粒机组近几年发生的故障和处理方法,也总结出操作经验以保证装置长满优运行。
关键词:色粒;拖尾粒;切刀磨损;转速差报警1、聚乙烯挤压造粒机简介聚乙烯挤压造粒机是将上游生产的线性低密度聚乙烯(LLDPE)挤压熔融造粒,整套设备包括混炼机,熔融泵,换网器,水下切粒单元。
2、常见故障分析与处理2.1粘结粒子和拖尾粒子①切刀盘找正不准;在开车前,应该确认切刀上没有上次停车粘有的粒料和碎屑,并且水室干净没有块料。
尤其是刀背看不到的地方,用手触摸检查。
在清理模板、水室小块料和切刀缠刀料时会造成刀盘和切刀轴变形或者切刀卷刃,导致切粒时与模板贴合不好,影响产品质量,严重时会造成切刀后退、缠刀、灌肠的后果。
造粒机在正常停车后一般不对刀盘找正,但出现上述问题引起的停车,建议对切刀重新多次找正;②操作人员操作不到位;这一点主要体现在开车过程中:在开车前操作人员应该对小车轨道检查,确认轨道没有颗粒,使小车在前进中能够畅通无阻。
合模时应将小车前进至模板0.5米的位置,快速清理模板,在颗粒水到达前,模孔尽量减少流出树脂,保证启动切粒机电机、进刀、PCW水打直通(进水)这三者操作紧密连接,一气呵成;③保证充模质量;为了保证填充模板的有效性,将之前的开车负荷4t/h改为6t/h,让树脂充分填充模板;④调整切粒水温和模板温度;在开车前将颗粒水箱加热蒸汽打开对颗粒水加热至53度左右,不要过高也不要过低,保证合适的水温有利于树脂的成型和冷却。
过高的水温颗粒将来不及冷却造成粘结粒子,过低的水温容易产生碎屑粒子;⑤调整进刀压力和平衡压力;进刀压力太低,切刀和模板离得太远,颗粒不能被及时切断,导致拖尾。
切刀和模板离得太近,切刀磨损太快,减少了切刀和模板的使用寿命;⑥有垫刀料导致切刀后退;这类事故初期可降低造粒负荷,反复进刀两次处理,处理后通过视镜查看水室切刀、颗粒外观,判断是否有好转。
挤出问题解决方法
板材向先冷却的部分弯曲,产生内应力。为了减少成型内应力,应尽可能均匀冷却,不加牵
伸,这就要求冷却输送部分必须具有足够的长度
2.肖顺仁
3.余建兴
4.彭方武
5.林毅
6.谢禄清
7.张小平
8.潘新斌
9.王振虎
10.曾素华
11.曹
板边不齐(荷叶边)
(1)机头分料不均匀。应调整阻力块或调节分配螺杆的转速。
(2)供料不稳,料片脉动。应适当调整机身温度,温度变化不能太大。同时,应适当调节主
机螺杆转速,并保证电压稳定
板材断裂
(1)挤出温度偏低,熔料塑化不良。应适当提高机身及机头温度。通常,挤出机机身温度
应根据成型原料的种类而定,机头温度一般比机身温度高5—10℃左右,机头温度的分布按中
(4)模唇表面光洁度太差。应重新研磨模唇,提高表面光洁度。
(5)模唇平直部分太短。应增加平直部分长度。
(6)原料未充分干燥,水分含量偏高。应进行预干燥处理。
(7)压缩空气压力不足,压光辊筒压不紧。应适当提高压缩空气压力,增加辊筒压力。
(8)辊筒温度偏低。应适当提高
板厚不均匀
<1)机头温度分布不均匀。应适当调整。
(2)压光机辊筒表面有析出物粘附。应清洗辊面
表面光斑
(1)压光机下辊温度偏高,板材与辊筒表面粘着。应适当降低下辊温度。
(2)原料配方中的液体助剂在机头和辊筒间析出,使料片粘着在辊面上。应清洗辊面
表面凹凸不平及光
泽不良
(1)机头温度偏低。应适当提高。
(2)压光辊表面不光洁。应调换辊筒或重新抛光辊面。
(3)压光辊温度偏低。应适当提高辊筒温度。
- 1、下载文档前请自行甄别文档内容的完整性,平台不提供额外的编辑、内容补充、找答案等附加服务。
- 2、"仅部分预览"的文档,不可在线预览部分如存在完整性等问题,可反馈申请退款(可完整预览的文档不适用该条件!)。
- 3、如文档侵犯您的权益,请联系客服反馈,我们会尽快为您处理(人工客服工作时间:9:00-18:30)。
气泡 与工艺及设备相关的可能原因
1.料筒温度过高 2.注射压力、背压过低。 3.保压压力(时间)不足 4.射速太高 5.充模料量不足 6.料管各区温度设定不良 ◆ 与模具相关的可能原因
1.壁厚处(加强筋)模温太高 2.浇口或流道不良 3.浇口类型或位置选择不良 4.浇口凝固太早 5.筋太厚 6.模温太低 7.排气不良 ◆ 与材料相关的可能原因
1.材料流动性、收缩性不合要求 2.回料用量过多 3.原料未充分干燥 熔接缝 与工艺及设备相关的可能原因
1.射出压力(速度)太低或太高 2.背压设定不合适 3.料管温度太低 ◆ 与模具相关的可能原因
1.模温太低 2.浇口或流道太小 3.排气不良 4.浇道太长 ◆ 与材料相关的可能原因
1.流动性不好 2.润滑剂太多 3.材料存在异物质 喷射痕 与工艺及设备相关的可能原因
1.射速太快 2.熔胶温度太高或太低 3.射嘴直径太小 .料管温度太高或太低 ◆ 与模具相关的可能原因
1.浇口类型或位置不当 2.浇口形状不当 3.模温太低 4.浇口凝固太早 ◆ 与材料相关的可能原因
1.材料流动性不当 尺寸差异 与工艺及设备相关的可能原因
1.供料不稳定。 2.螺杆转速不稳定。 3.温度失控,背压不稳定。 4.螺杆复位不稳定,有多于0.4mm的变化. 5.成型周期不稳定。 ◆ 与模具相关的可能原因
1.模具强度和刚性不足。 2.使用了不良的一模多腔形式。 3.顶出系统、浇注系统、冷却系统的设置不合理。 ◆ 与材料相关的可能原因 1. 材料干燥不良,颗粒不均匀。 2.原料收缩率有太大。 3.材料粘度存在批次差异 白化 与工艺及设备相关的可能原因
1.充填太急 2.熔胶温度不当 3.射压太高 4.射嘴直径太小 5.射嘴温度太低 ◆ 与模具相关的可能原因
1.浇口类型或位置不当 2.浇口直径太小 3.模温太低 4.冷料井不足 5.剧弯处厚度不均 6.顶出受力不均或太大 ◆ 与材料相关的可能原因
1.材料应力松弛性差 2.材料屈服强度低 银纹 与工艺及设备相关的可能原因
1.料筒温度过高 2.螺杆转速太快 3.喷嘴太小、太热或阻塞 4.射胶量超过机器容量的80% 5.有气体或水汽在熔胶内 6.清料不彻底 ◆ 与模具相关的可能原因
1.浇口太小 2.浇口或流道阻塞 3.模具表面有微裂缝
与材料相关的可能原因 1.材料没充分干燥 2.材料含异物 3.材料高温分解 表面剥离 与工艺及设备相关的可能原因
1.料筒温度过低 2.注射速度太慢。 3.保压压力(时间)不足 ◆ 与模具相关的可能原因
1.模温太低 2.浇口或流道剧弯 3.浇口类型选择不当 4.脱模剂太多 ◆ 与材料相关的可能原因
1.材料干燥不良 2.回料太多 3.有不相容添加物 黑条 与工艺及设备相关的可能原因
1.射速太快 2.熔胶温度太高 3.射压太高 4.射嘴直径太小 5.射嘴温度太高 6.料管温度高 7.成型周期太长 8.料管中有碳化物 ◆ 与模具相关的可能原因 1.浇口类型或位置不当 2.浇口直径太小 ◆ 与材料相关的可能原因
1.材料高温稳定性不够 2.材料含异物 色差 原料问题
1. 选用的着色剂或其它助剂的热稳定性差 2. 选用的着色剂与树脂或添加的助剂起反应分解 3. 原料的流变性能过低 ◆ 加工工艺问题
1. 烘料时间过长或烘料温度过高 2. 注塑温度或压力过高 3. 滞留时间过长,导致变色 4. 注塑机清洗不干净,受污染 ◆ 周围环境及其它影响因素
1. 原料或制品不宜存放在阳光直射的场所 2. 色差仪类型的差异或其测色精度不够所造成 3. 测色差时制品温度的影响 充填不足 与工艺及设备相关的可能原因
1.熔胶量不足 2.料筒温度太低 3.背压设定不良 4.注塑压力(速度)不足 5.注塑时间太短 6.止回阀间隙大 7.射嘴阻塞 ◆ 与模具相关的可能原因
1.模温太低 2.浇口类型或位置选择不当 3.模具排气不良 4.模具的流道(浇口)过小 5.模具型腔的分布不平衡 ◆ 与材料相关的可能原因
1.材料本身流动性不良 2.材料干燥不良 翘曲 与工艺及设备相关的可能原因
1.射出压力或时间不当 2.熔胶在料管时间太长 3.成型周期不当 4.料筒温度太低 5.射嘴温度低 6.保压压力及时间不当。 ◆ 与模具相关的可能原因
1.模温太高或太低 2.浇口或浇道太小 3.浇口类型或位置不当 4.模温不均 5.顶杆面积太小或分布不平衡 6.壁厚偏差太大 ◆ 与材料相关的可能原因
1.流动性不当 2.材料纵、横向收缩率偏差大 烧焦 与工艺及设备相关的可能原因
1.射速(射压)太高 2.熔胶温度太高 3.背压太高 4.射嘴直径太小 5.射嘴温度太高 6.料管温度高 7.螺杆转速太快 ◆ 与模具相关的可能原因
1.浇口类型或位置不当 2.浇口直径太小 3.模具排气不好 ◆ 与材料相关的可能原因
1.材料耐热不够 2.二次材料太多 3.材料高温稳定性不够 光泽不良 与工艺及设备相关的可能原因
1.料筒温度太低 2.射压不足 3.射嘴温度低 4.熔胶在料管时间太长 5.成型周期不当 ◆ 与模具相关的可能原因 1.模具光洁度差。 2.浇口或流道太小 3.浇口类型或位置不当 4.排气不良 5.模具表面有异物。 ◆ 与材料相关的可能原因
1.材料没充分干燥 2.流动性能不当 3材料本身光泽性差 飞边 与工艺及设备相关的可能原因
1.射出压力(速度)太高 2.熔胶停留料管时间太长 3.成型周期太长 4.锁模力不足 5.料温太高 ◆ 与模具相关的可能原因
1.合模面接触不良 2.模具强度不够 3.排气不良 4.浇道太长 5.模具配件尺寸不精密 ◆ 与材料相关的可能原因
1.流动性太好 2.润滑剂太多 凹陷 与工艺及设备相关的可能原因
1.料筒或模具温度过高 2.注射压力、速度、背压过低、注射时间过短 3.保压压力(时间)不足 4.冷却时间设定不良 5.止回阀不良 ◆ 与模具相关的可能原因
1.浇口或流道太小 2.浇口位置或类型选择不良 3.浇口凝固太早 4.筋太厚 5.流动不平衡 ◆ 与材料相关的可能原因
1.材料流动性、收缩性不合要求 2.回料用量过大 流痕 与工艺及设备相关的可能原因
1.料筒温度过低 2.注射压力过低 3.保压压力(时间)不足 4.周期时间不当 5.熔胶在料管停留时间太长 ◆ 与模具相关的可能原因
1.模温太低 2.浇口或流道太小 3.排气不良 ◆ 与材料相关的可能原因
1.材料流动性不合要求 2.润滑剂不当 3.易挥发物太多 裂纹 与工艺及设备相关的可能原因
1.过度充填、保压、使残留应力过大 2.保压时间太长 3.模温太低 ◆ 与模具相关的可能原因
1.脱模斜度不够 2.顶出不良 3.脱模剂过多 ◆ 与材料相关的可能原因
1.干燥不良 2.二次料太多 3.材料高温分解 黑点 产生黑点不良的原因
1. 注塑机清洗不干净 2. 注塑机温度设定过高 3. 注塑机射嘴结构不合理 4. 滞留时间过长,易烧焦,产生黑点 5. 烘料桶内清洗不干净 6. 烘料桶吹(吸)风装置,过滤网污染 7. 储料桶内清洗不干净 8. 搬运、拆包、投料过程管理不当,易带入周围环境中的灰尘等杂质 9. 产品本身的黑点不良,应及时反馈,便于进行调查