无溶剂复合工艺常见问题集锦
无溶剂复合应用技术的几个重点问题提示

无溶剂复合应用技术的几个重点问题提示首先做两点说明:1、作为一项新的工艺技术,对无溶剂复合我们保持一个开放的、学习的、共同进步的心态。
总体来说,国内对无溶剂复合的认识和经验都还很初浅,各种不同看法实属正常,有些观点不全面、不准确甚至错误都不奇怪!下面的观点也只是我们一家之言,欢迎批评指正!2、对于无溶剂复合,我们不仅要学习、更要创新!中国的情况(复合结构、最终用户、材质差异、印刷质量、技术管理基础、作业习惯等)比任何一个国家都复杂,国外的经验我们要充分地学习和借鉴,同时也必须看到:完全照搬是不能解决问题的的,最主体的、最复杂的应用技术最终要我们在创新的基础上立足于在国内解决。
特别强调:这是一项系统工程,需要我们一起努力!1、无溶剂复合工艺要素(1)料带张力。
料带张力的精确控制是料带正常运行和高速复合正常进行的基本条件。
(2)涂胶量。
涂胶量不仅直接决定了复合质量,而且还在很大程度上影响到复合成本。
(3)混配比。
混配比是双组份胶完成正常反应固化的关键因素,也是影响复合牢度的重要因素。
(4)工作环境,包括机外大环境和机上小环境。
机外大环境最重要的是指环境相对湿度。
机上小环境主要是指辊筒温度、气压等因素。
工作环境是工艺正常稳定的必要条件。
(5)固化条件,主要包括固化温度和固化时间。
固化条件是无溶剂复合最主要的机外工序条件,是实现预期复合质量的另一关键因素。
当然熟化空间的湿度也是一个重要因素。
上述5个方面我们称之为无溶剂复合的五大工艺要素。
2、关于张力的几点说明(1)在无溶剂复合中,对张力控制的要求比普通复合要高。
主要原因有二:1)无溶剂复合初粘力较低,2)无溶剂复合机通常速度比干式复合机要高很多(常见速度为250~600m/min),因此对张力的要求原则上比干式复合更为严格。
(2)我们强调的是两层复合料带之间张力的匹配性,而不仅仅是张力系统本身的精度。
在当前技术条件下,许多复合机张力系统的性能精度都是良好的,可以满足无溶剂复合的需要。
无溶剂复合工艺常见问题集锦

无溶剂复合工艺常见问题集锦近年来,无溶剂复合工艺因具有突出的节能、高效、低成本等优势而备受软包装企业的青睐,越来越多的软包装企业开始尝试采用无溶剂复合工艺。
但是,软包装企业在应用无溶剂复合工艺过程中,难免会遇到这样或那样的问题,甚至影响企业的正常生产。
在此,笔者结合自己的实践经验,总结了无溶剂复合工艺中的一些常见问题,在此与大家分享。
胶黏剂涂布后出现收缩现象如图1所示,在用VMPET阴阳膜复合第三层材料时,涂胶后在VMPET薄膜边缘出现胶液收缩现象,检查后发现系VMPET薄膜局部表面能不合格所致。
无溶剂胶液的表面张力远高于干法复合用的溶剂型胶液(稀释用溶剂乙酸乙酯的表面张力仅为26.29mN/ m),如果薄膜整体的表面能低于涂布胶液的表面张力,胶液在薄膜表面就会出现收缩现象;如果薄膜表面局部受一些低表面张力助剂的污染,则在该点就会出现胶液不润湿(收缩)现象,在最终的复合制品上形成气泡缺陷,甚至造成剥离不良的质量问题。
类似的涂胶后胶液收缩现象,在使用水性胶黏剂时也可能出现。
转移胶辊表面温度过高涂布系统的实际温度往往与设定温度有一定偏差,在机速300m/min、上胶量1.45g/m2的条件下,胶桶温度设定为35℃(实测38℃),计量辊温度设定为32℃,涂布辊温度设定为35℃,涂布系统的实测温度分布如图2。
由图2可见,转移胶辊表面温度高达44℃,已严重偏离设定值。
这是由于转移胶辊摩擦生热造成的,其影响因素主要有辊面光洁度、胶水黏度、压力大小等,其中辊面光洁度的影响最大,须严加控制。
胶辊表面胶液分布不均涂胶量太小时,胶辊表面的胶液分布不均匀,局部发涩(不反光),这在某种程度上也反映出涂布系统(转移胶辊)的精度高低。
理论上讲,对于某些复合结构(如BOPP/珠光膜),涂胶量在1.0g/m2就能满足复合强度要求,但如果设备涂布系统的精度不高,则需要适当增加涂胶量,以保证涂胶均匀。
材料起皱引起的复合气泡现象原材料皱褶将直接导致下机的复合产品出现气泡现象,原因是皱褶处复合时压不实,夹入空气。
无溶剂复合的外观问题汇总99%的都解决了
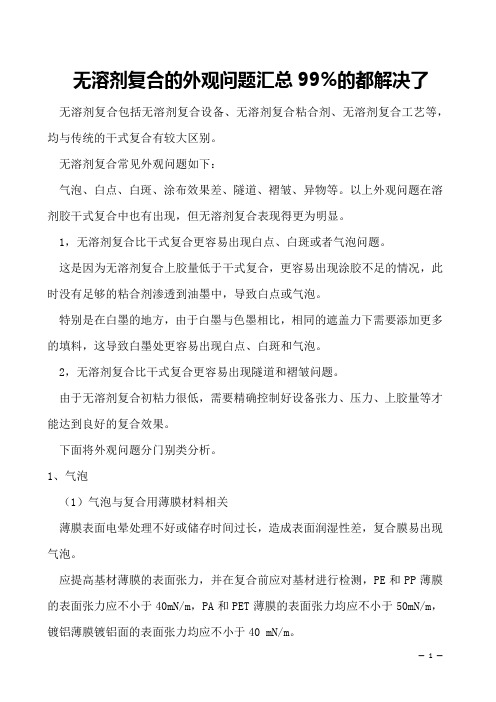
无溶剂复合的外观问题汇总99%的都解决了无溶剂复合包括无溶剂复合设备、无溶剂复合粘合剂、无溶剂复合工艺等,均与传统的干式复合有较大区别。
无溶剂复合常见外观问题如下:气泡、白点、白斑、涂布效果差、隧道、褶皱、异物等。
以上外观问题在溶剂胶干式复合中也有出现,但无溶剂复合表现得更为明显。
1,无溶剂复合比干式复合更容易出现白点、白斑或者气泡问题。
这是因为无溶剂复合上胶量低于干式复合,更容易出现涂胶不足的情况,此时没有足够的粘合剂渗透到油墨中,导致白点或气泡。
特别是在白墨的地方,由于白墨与色墨相比,相同的遮盖力下需要添加更多的填料,这导致白墨处更容易出现白点、白斑和气泡。
2,无溶剂复合比干式复合更容易出现隧道和褶皱问题。
由于无溶剂复合初粘力很低,需要精确控制好设备张力、压力、上胶量等才能达到良好的复合效果。
下面将外观问题分门别类分析。
1、气泡(1)气泡与复合用薄膜材料相关薄膜表面电晕处理不好或储存时间过长,造成表面润湿性差,复合膜易出现气泡。
应提高基材薄膜的表面张力,并在复合前应对基材进行检测,PE和PP薄膜的表面张力应不小于40mN/m,PA和PET薄膜的表面张力均应不小于50mN/m,镀铝薄膜镀铝面的表面张力均应不小于40 mN/m。
薄膜中的添加剂析出,也会造成表面润湿性差,复合膜易出现气泡。
薄膜不平滑,使粘合剂涂布不均匀或不足。
对此应选用优质薄膜或适当增加涂布量。
薄膜本身温度低,粘合剂涂布后流动不良造成阻塞而润湿性差。
粘合剂在熟化过程中与油墨或基材薄膜中的水分发生反应产生气泡。
在夏季,加工尼龙复合膜时易出现该问题;大面积白墨以及专色墨印刷时易出现该问题。
(2)气泡与印刷油墨相关油墨颗粒粗,使粘合剂涂布不均匀或不足。
对此应选用优质油墨或适当增加涂布量。
(3)气泡与粘合剂相关粘合剂涂布量不足,易造成气泡。
粘合剂流动性差、粘度大导致涂布效果不佳。
可适当提高固定辊和上胶辊温度以增加粘合剂的流动性。
粘合剂表面张力大,对基材薄膜润湿性不佳。
盘点无溶剂复合九大常见不良现象,够详细!
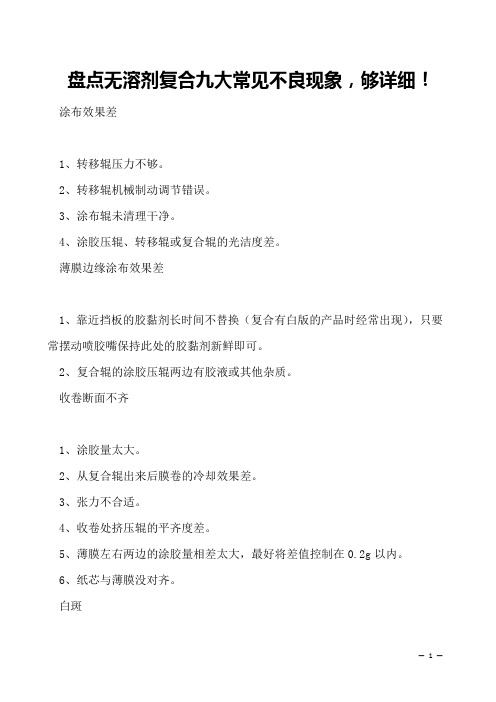
盘点无溶剂复合九大常见不良现象,够详细!涂布效果差1、转移辊压力不够。
2、转移辊机械制动调节错误。
3、涂布辊未清理干净。
4、涂胶压辊、转移辊或复合辊的光洁度差。
薄膜边缘涂布效果差1、靠近挡板的胶黏剂长时间不替换(复合有白版的产品时经常出现),只要常摆动喷胶嘴保持此处的胶黏剂新鲜即可。
2、复合辊的涂胶压辊两边有胶液或其他杂质。
收卷断面不齐1、涂胶量太大。
2、从复合辊出来后膜卷的冷却效果差。
3、张力不合适。
4、收卷处挤压辊的平齐度差。
5、薄膜左右两边的涂胶量相差太大,最好将差值控制在0.2g以内。
6、纸芯与薄膜没对齐。
白斑1、涂胶量低,没有足够的胶黏剂渗透到油墨中。
此时表现为复合膜整体出现细小、均匀的斑点。
解决办法是适当增加涂胶量,调整复合温度和复合压力。
2、涂胶部、复合部各辊的表现光洁度太差或粘有胶黏剂等异物。
此时表现为局部间断重复出现斑点。
可以通过测量重复出现的两斑点的间距来判断是哪根辊上有异物,清理干净即可。
3、基材膜张力不均,进入复合辊前打褶,造成局部复合效果较差,并会出现气泡,宏观表现为白斑。
解决办法是调整复合前的挠度辊,使薄膜进入复合之前保持平整,可适当调整张力或更换膜卷。
4、复合部分或涂胶部分的压力设置不当。
5、油墨与胶粘剂的的相溶性不好,在没有胶黏剂渗透的油墨处会出现白斑,应更换合适的胶黏剂或油墨。
刀线主要原因是涂布单元各辊没有清理干净或转移辊的光滑性太差。
此时应停机清理涂布单元,或更换转移辊,有时晃动计量辊也能消除刀线故障。
胶黏剂干燥不良1、胶黏剂没有按照正确配比要求配置。
2、胶黏剂失效。
3、混合后的胶液中混入水分或大量乙酸乙酯。
复合膜气泡1、由于材料不平滑、油墨颗粒粗,使胶液涂布不足。
对此应选用优质材料或适当增加涂布量。
2、固化中产生的CO2在阻隔性较好的薄膜中无法逸出而形成,主要在使用单组份无溶剂的场合出现,应改用双组份粘合剂。
3、表面润湿性差,应提高材料的表面润湿张力,提高粘合剂的润湿性。
无溶剂复合常见问题以及应对方法

无溶剂复合常见问题以及应对方法一、在生产操作层面应关注的几个环节与溶剂型干式复合相比,无溶剂复合具有"初粘力低、涂布量较小、固化时间较长"等特点,因此,在实际生产操作时,应真正了解和掌握无溶剂复合工艺、设备特点,关注几个关键环节,以减少或消除质量事故。
一是针对无溶剂复合"初粘力低"的特点,生产操作中应特别注意对料带张力匹配性、收卷张力和压力的调控。
二是针对无溶剂复合"涂布量较小"的特点,应特别注意对涂布均匀性、复合均匀性、收卷的松紧度控制。
三是针对无溶剂复合"固化时间较长"的特点,应敏感地认识到固化过程其实是双组份胶水的反应过程,该进程对复合质量有较大的影响,因此,应特别注意固化条件(如温度、湿度、环境)的设定,并对固化过程进行监控。
四是在使用双组分无溶剂胶黏剂时,应特别关注胶水混配比的设定和监控,对双组分自动混胶机的正确使用、维护保养,确保其始终处于良好状态尤为重要。
此外,对新的复合结构坚持进行涵盖"参数确定、剥离强度、胶水/油墨/材料的相容性、热封制袋、摩擦系数变化"等内容的工艺试验,"工艺试验--小批量试生产--批量生产"的流程应成为一种工作制度。
二、若干工艺异常现象的原因剖析和解决方法一)关于复合产品中出现"点"的现象与干法复合工艺一样,无溶剂复合工艺实施中,复合膜出现"点"是比较常见的异常现象。
产生"点"其成因不外有物理原因和化学原因。
但物理原因造成的"点"和化学原因造成的"点"无论从外在表象、形成机理和解决办法都不同。
因此,此"点"非彼"点",应该认真甄别,分别对待,千万不能"一视同仁"。
1、物理原因产生的"点"。
常见无溶剂复合机问题及解决方法

常见无溶剂复合机问题及解决方法复合机在运行过程中常会出现传动部位磨损的问题,如涂布机烘缸轴头磨损、卷纸辊轴承室磨损等。
传统的修复方法有堆焊、热喷涂、电刷镀等,但都存在一定的弊端:堆焊会使零件表面达到很高温度,造成变形或裂纹,严重时还会导致轴的断裂;电镀镀层不能太厚,且污染严重,应用也受到了限制。
近年来,无溶剂复合机因具有突出的节能、低本钱等劣势而备受软包装企业的喜爱,越来越多的软包装企业开端尝试采用无溶剂复合。
但是,软包装企业在使用无溶剂复合进程中,难免会遇到一些成绩。
在此,笔者结合本身经历,总结了无溶剂复合的罕见成绩。
胶黏剂涂布后呈现膨胀景象在用VMPET阴阳膜复合第三层资料时,涂胶后在VMPET薄膜边缘呈现胶液膨胀景象,反省后发现系VMPET薄膜部分外表能不合格所致。
无溶剂胶液的外表张力远高于干法复合用的溶剂型胶液(浓缩用溶剂乙酸乙酯的外表张力仅爲26.29mN/m),假如薄膜全体的外表能低于涂布胶液的外表张力,胶液在薄膜外表就会呈现膨胀景象;假如薄膜外表部分受一些低外表张力助剂的净化,则在该点就会呈现胶液不润湿(膨胀)景象,在最终的复合制品上构成气泡缺陷,甚至形成剥离不良的质量成绩。
相似的涂胶后胶液膨胀景象,在运用水性胶黏剂时也能够呈现。
转移胶辊外表温渡过高涂布零碎的实践温度往往与设定温度有一定偏向,在机速300m/min、上胶量1.45g/m2的条件下,胶桶温度设定爲35℃(实测38℃),计量辊温度设定爲32℃,涂布辊温度设定爲35℃,涂布零碎的实测温度散布如图1所示。
这是由于转移胶辊摩擦生热形成的,其影响要素次要有辊面光亮度、胶水黏度、压力大小等,其中辊面光亮度的影响较大,须严加控制。
胶辊外表胶液散布不均涂胶量太小时,胶辊外表的胶液散布不平均,部分发涩(不反光),这在某种水平上也反映出涂布零碎(转移胶辊)的精度上下。
实际上讲,关于某些复合构造(如BOPP/珠光膜),涂胶量在1.0g/m2就能满足复合强度要求,但假如设备涂布零碎的精度不高,则需求适当添加涂胶量,以保证涂胶平均。
十大无溶剂复合故障处理方法,让人茅塞顿开!
十大无溶剂复合故障处理方法,让人茅塞顿开!如今,无溶剂复合是软包装生产的一大趋势,无溶剂复合的故障怎么处理也就成了大家十分关心的问题,华印我特别整理出十大无溶剂复合故障的处理方法,以供参考。
1、塑料复合考虑内容物颜色对外观的影响包装深色类的贴体内容物,这些外观缺陷就会衬托表面为白点现象。
相同的印刷油墨,受墨层集中度的影响,最后在收卷紧的部位外观良好,而在收卷松的部分表现为胶斑,如果是不规则的胶斑则需要适当提高涂胶量。
2、收卷张力变化与收卷整齐度的关系收卷张力锥度设定过小时,外圈对内圈会产生较大的挤压力,如果薄膜收卷后内外层间的摩擦力又较小(薄膜过于爽滑则摩擦力小),则会出现如图右侧图所示的收卷挤出现象。
而当设定较大的收卷张力锥度时,就又能收卷整齐了。
上述例说明,无剂复合膜的收卷整齐度与张力参数设定有关,与薄膜间的爽滑剂也有关系。
3、水煮掉铝现象测试过三个厂家的无溶剂复合胶水样品,结果有两家胶水在水煮后的掉铝现象严重,另一家在多批次测试表现也不稳定。
解决方法:需要经过多次验证,才能投入批量生产。
4、材料起皱会导致复合膜白点气泡现象原材料皱折,直接导致复合下机产品出现气泡现象,原因是复合部位压不实,夹入了空气,严重时熟化不掉。
解决方法:不要盲目生产,至少要控制一下复合机速,确定好复合质量后才能生产。
荡边的薄膜,两侧的张力很难兼顾!5、收卷压皱现象可以确定,如果收卷时,压辊有跳动现象,二层PE复合膜面较软,则很容易将膜卷压皱。
引起膜卷跳动的因素较多,如纸芯变形(变成椭圆状)、纸芯端面切口不平产生装配误差、膜卷突然增厚明显等因素。
自然地,收卷张力大一些也会缓减这种现象。
6、橡胶边边缘溢胶易出现粘连边缘溢胶(,该现象与上胶量过大有关。
另外,如果生产过程中胶辊两端有堆积余胶现象则极易出现收卷后边缘溢胶现象,无溶剂复合在低速运行时胶辊边缘通常有积胶现象,说明低速运行时上胶量较大,在中途停机及重新开机时机速较低,此时容易出现粘边现象,转移胶辊宽度偏宽及材料不整齐纠偏跟不上都会产生粘边现象。
无溶剂复合常见问题解答
无溶剂复合常见问题解答(2010-11-18 16:33:34)1. 无溶剂复合机为什么多采用单工位放卷和收卷?国内外无溶剂复合机大多数都采用单工位放、收卷,主要原因有如下三点:1) 由于无溶剂复合初粘力很低,采用双工位放、收卷很可能在接料过程中因裁切导致张力波动而产生较多的废品,而单工位则可以明显减少接料废品。
2) 单工位比双工位机上料带的长度明显缩短,因此可相应地减少发生废品的可能性。
3) 一般单工位更换料卷可在很短时间内(一般3分钟左右)完成,而在此时间内已涂布在基材上的双组份胶不会固化,因此不会出现因停机造成的复合废品。
2. 一台无溶剂复合机比干式复合机1年节能多少?从计算可以看出:– 1台无溶剂复合机比溶剂型干式复合机1年干燥节能近20万元,比水性胶干式复合机节能近30万元。
–无溶剂复合比溶剂型干式复合节省电费0.7分/平方米左右,比水性胶复合节省1.1分/平方米左右。
–如果按产能计算,上述数据则加倍。
注:表无溶剂复合与干式复合干燥成本的比较假设:1)机器宽度为1000毫米;2)年工作时间3000小时(=250天/年X12小时/天)3. 无溶剂复合涂胶量是多少?无溶剂复合涂胶量与复合基材、印刷图案、使用场合等不同因素有关,一般情况下,涂胶量在1.2~2.0 g/m2之间。
- 非印刷膜复合,1.0~1.2 g/m2- 普通印刷膜,1.3~1.6 g/m2- 铝箔复合、蒸煮袋复合等,1.8~2.0 g/m2另外,由于不同厂家产品使用条件不同(比如温度),涂胶量也会有一定差别。
4. 无溶剂复合与干式复合涂胶成本的比较在当前经济形势下,无溶剂复合的涂胶量和涂布成本分别为:- 涂胶量为: 1.5~2.0 g/m2;- 胶粘剂价格为:国产胶,30~33元/Kg(特殊用途胶除外)进口产品,价格约高15%- 涂胶成本为: 4.5~6.6分/m2。
注:表无溶剂复合与干式复合涂胶成本的比较注:上述胶粘剂价格为2009年2-3月的市场中间价格。
无溶剂复合常见故障分析与解决
无溶剂复合常见故障分析与解决(总5页)--本页仅作为文档封面,使用时请直接删除即可----内页可以根据需求调整合适字体及大小--无溶剂复合常见故障分析与解决近年来,无溶剂复合工艺在软包装生产过程中逐步得到推广,尽管该工艺较为简单和稳定,但在应用过程中还是凸显出了一些共性问题。
本文中,笔者总结了几类无溶剂复合常见故障,并给出了原因及解决方案,供业内人士参考。
固化不充分原因分析:双组分胶黏剂混合不均匀;双组分胶黏剂混配比有误,如-OH组分偏少;固化时间不够或固化温度偏低;胶黏剂已变质。
解决方案:提高双组分胶黏剂混合均匀性,检查相关混配设置是否正常工作,如检查静态混合管,一旦发现问题,应立即对其进行更换;检查双组分胶黏剂混配比,并按照说明书要求调整至正确的混配比;适当延长固化时间,提高固化温度;如果胶黏剂已变质,应立即更换。
复合膜上产生纵向或横向皱纹原因分析:横向皱纹产生的主要原因是两种复合基材张力不匹配;收卷压力不稳定,复合基材两侧收卷压力不平衡、自身横向松紧度严重不一致、接头不平整。
纵向皱纹产生的主要原因是收卷张力过大;复合基材两侧收卷压力不平衡、接头不平整。
解决方案:调节通道、第二放卷单元的收卷张力;更换质量更好的复合基材;仔细黏结新旧料带;调节收卷张力大小及两侧收卷压力的平衡。
芯皱(里皱)芯皱(里皱)是指复合料卷内部靠近芯管的区域出现皱褶。
在无溶剂复合生产中,芯皱发生的概率和造成的影响都要比干式复合生产大一些。
芯皱产生的主要原因是胶黏剂初黏力较低,其他影响因素如下。
(1)芯管的直径和质量。
通常我们使用的芯管直径为3英寸和6英寸,一般情况下,芯管直径越大,产生芯皱的概率就越少。
此外,芯管不圆、表面不平整或存在其他质量缺陷也都会直接影响芯皱数量。
(2)料头和胶带状况。
在单工位无溶剂复合设备中,我们经常采用手工操作方式黏结新旧料带,而接头和胶带粘贴是否平整会直接影响芯皱问题的发生。
(3)两种复合基材的张力匹配状况。
无溶剂复合中常见的问题有哪些?
无溶剂复合中常见的问题有哪些?⑴熟化后胶水发黏:无溶剂胶黏剂熟化后不干、发黏从化学的角度来说是因为两组分没有完全反应,没有形成大分子结构所引起的。
导致这种现象的原因及解决方案主要有下面几个。
①胶黏剂两组分分配比错误:两组分比例失调,特别是羟基组分过多会引起胶黏剂熟化后长期发黏,使用混胶机时应该首先检查混胶机是否有堵塞,出胶比例是否正确;手工混胶时检查配胶比例是否有误。
②胶黏剂搅拌不均匀:特别是手工配胶、胶黏剂黏度较大时,容易产生混胶不均匀引起胶水不干、发黏的现象。
混胶不均匀从本质上来讲也是局部的配比错误。
③胶黏剂失效:确认胶黏剂在保持期内,并且无结皮、结块、浑浊、絮状等现象;必要时按比例少量配胶放置进行试验,观察固化情况,如果确实是胶黏剂本身质量引起,则更换质量稳定、可靠的胶黏剂。
④胶黏剂内混入水分或大量溶剂:胶黏剂内混入水分或大量溶剂从本质上来说也是有黏剂失效,分析使用过程中有无混入水分或溶剂的可能,如发现有这种潜在的可能,则排除这些可能因素后再进行复合。
⑵剥离强度低:复合薄膜出现剥离强度低的现象,引起的因素较多,主要与胶黏剂的种类、胶黏剂的配胶比例及混合均匀度、涂布均匀度、上胶量、复合基材的表面张力、基材的添加剂以及熟化程度等几个方面因素有关。
①胶黏剂的种类选择:应该根据复合材料的用途不同选择合适的胶黏剂种类。
如复合袋需要经过高温蒸煮杀菌的,就应该选择耐高温蒸煮的胶黏剂;需要装一些辛辣食品或者农药包装的,就需要选择专门的耐介质胶黏剂或者农药专用胶黏剂。
另外,由于市场上胶黏剂的生产厂家技术力量参差不剂,产品的质量、稳定性也是千差万别,故在选择胶黏剂的型号时,首先要选择具有一定技术力量的生产厂家的产品。
目前应用较好的国外进口的无溶剂胶黏剂生产厂家有德国汉高、美国陶氏、法国波士、西班牙Cromogenia-units,S.A.等,国内上海康达化工新材料股份有限公司等单位的无溶剂复膜胶产品,在适应性、剥离强度、操作性等性能方面也基本达到了国外产品的性能。
- 1、下载文档前请自行甄别文档内容的完整性,平台不提供额外的编辑、内容补充、找答案等附加服务。
- 2、"仅部分预览"的文档,不可在线预览部分如存在完整性等问题,可反馈申请退款(可完整预览的文档不适用该条件!)。
- 3、如文档侵犯您的权益,请联系客服反馈,我们会尽快为您处理(人工客服工作时间:9:00-18:30)。
无溶剂复合工艺常见问题集锦
近年来,无溶剂复合工艺因具有突出的节能、高效、低成本等优势而备受软包装企业的青睐,越来越多的软包装企业开始尝试采用无溶剂复合工艺。
但是,软包装企业在应用无溶剂复合工艺过程中,难免会遇到这样或那样的问题,甚至影响企业的正常生产。
在此,笔者结合自己的实践经验,总结了无溶剂复合工艺中的一些常见问题,在此与大家分享。
胶黏剂涂布后出现收缩现象
如图1所示,在用VMPET阴阳膜复合第三层材料时,涂胶后在VMPET薄膜边缘出现胶液收缩现象,检查后发现系VMPET薄膜局部表面能不合格所致。
无溶剂胶液的表面张力远高于干法复合用的溶剂型胶
液(稀释用溶剂乙酸乙酯的表面张力仅为 m),如果薄膜整体的表面能低于涂布胶液的表面张力,胶液在薄膜表面就会出现收缩现象;如果薄膜表面局部受一些低表面张力助剂的污染,则在该点就会出现胶液不润湿(收缩)现象,在最终的复合制品上形成气泡缺陷,甚至造成剥离不良的质量问题。
类似的涂胶后胶液收缩现象,在使用水性胶黏剂时也可能出现。
转移胶辊表面温度过高
涂布系统的实际温度往往与设定温度有一定偏差,在机速300m/min、上胶量m2的条件下,胶桶温度设定为35℃(实测38℃),计量辊温度设定为32℃,涂布辊温度设定为35℃,涂布系统的实测温度分布如图2。
由图2可见,转移胶辊表面温度高达44℃,已严重偏离设定值。
这是由于转移胶辊摩擦生热造成的,其影响因素主要有辊面光洁度、胶水黏度、压力大小等,其中辊面光洁度的影响最大,须严加控制。
胶辊表面胶液分布不均
涂胶量太小时,胶辊表面的胶液分布不均匀,局部发涩(不反光),这在某种程度上也反映出涂布系统(转移胶辊)的精度高低。
理论上讲,对于某些复合结构(如BOPP/珠光膜),涂胶量在m2就能满足复合强度要求,但如果设备涂布系统的精度不高,则需要适当增加涂胶量,以保证涂胶均匀。
材料起皱引起的复合气泡现象
原材料皱褶将直接导致下机的复合产品出现气泡现象,原因是皱褶处复合时压不实,夹入空气。
如图3所示是CPP 材料表面的软皱褶,在无溶剂复合时,我们用频闪仪在线观察时,会发现复合膜有明显的气泡现象。
当然,过大的气泡点,熟化后也不能完全消除。
所以,
遇到这种不合格的材料时,不要盲目地进行生产,要控制一下复合机速,在确认复合质量合格后才能进行批量生产。
复合膜收卷压皱现象
如果收卷时压辊出现跳动现象,由于两层PE复合膜面较软,很容易将膜卷压皱,如图4所示。
引起膜卷跳动的因素较多,如纸芯变形、纸芯端面切口不平、膜卷突然明显增厚等。
当然,收卷张力大一些会缓解这种现象。
复合膜边缘溢胶
复合膜边缘溢胶与涂胶量过大有关。
如果生产过程中转移胶辊两端有堆积余胶现象,则极易出现收卷后边缘溢胶现象。
无溶剂复合机在低速运行时转移胶辊两端通常会有积胶现象,说明低速运行时涂胶量较大,在中途停机及重新开机时机速较慢,容易出现因溢胶造成的粘边现象。
需要说明的是,如果转移胶辊边缘的积胶现象很明显,则是胶辊边缘有磨损所致,需要对转移胶辊重新研磨(新辊在使用时边缘溢胶现象往往都较轻)。
复合膜透明处出现气泡
从传统干复合工艺转换为无溶剂复合工艺时,最大的难题是,墨层厚度未变,而涂胶量却大幅减少了,特别是针对透明窗设计的图案,油墨处需要较高的涂胶量才能保证外观质量,而涂胶量较大时透明处则易出现严重的胶水纹现象,造成油墨处和透明处的上胶量不能同时兼顾。
无溶剂复合时透明设计处由于涂胶量大易出现胶水纹
现象,熟化后复合膜透明处则会出现气泡现象(约几十米),如图5所示。
另外,收卷后透明部位的张力通常较墨层厚实处小,更容易出现气泡现象。
解决方法:①改变墨层厚度,以减少整体涂胶量,避免透明处出现明显的胶水纹;②选用高黏度的无溶剂胶黏剂,相同的涂胶量时,胶水纹现象会明显减轻。
转移胶辊表面起泡、起皮
转移胶辊在使用中会出现起泡、起皮现象,这属于胶辊本身的质量问题,最直接的影响就是引起涂胶不均匀。
需要说明的是,新制的转移胶辊只有在使用一段时间后,该质量问题才能表现出来,即使将胶辊重新研磨后再使用,也很快又会出现起泡、起皮现象。
因此,在选购转移胶辊时,一定要选择有经验的生产厂家,不能只考虑价格因素。
膜卷表面固定位置的气泡
如果气泡出现在膜卷表面的同一位置,是膜卷收卷较松,卸料及称重时表面受挤压引起的,经放大后观察气泡形状很不规则。
解决方法:①卸料用的叉车表面用毛毯包裹好,减少膜卷表面局部受压力;②表面收卷要紧一些。
镀铝复合膜表面出现小黑点
对于相同的复合工艺参数,不同的胶黏剂型号,小黑点
表现出来的严重程度有所不同。
笔者曾试过两个厂家的胶水样品,最终制得的镀铝复合膜表面的小黑点程度是有所差异的,如图6所示,左侧样品的小黑点要明显一些。
改善方法:①胶水与油墨的匹配性;②减少涂胶量;③低温熟化。
镀铝复合膜表面划墨现象
这种现象多出现在镀铝复合膜收卷接近纸芯部位或接头部位。
要划墨部位的背面可以看到明显的褶皱,说明该处所受收卷压力较大。
放大观察,还发现墨痕处存在小黑点现象。
解决方法:①保证收卷平整,不起皱;②降低涂胶量;③复合后可先在室温条件下放置2~3小时,然后再放入熟化室进行熟化。
内容物颜色对复合膜外观的影响
无溶剂复合加工的塑塑复合膜,表面多少都会有一些胶斑等外观缺陷,单个包装袋检测时都是合格产品,但在包装深色的贴体内容物后,这些外观缺陷就会呈现为白点现象,极可能引起客户的质量投诉,如图7所示。
而且,即使是相同的印刷油墨,受墨层集中度的影响,最后在收卷紧的部位外观良好,而在收卷松的部分则表现为胶斑,如果是不规则的胶斑,则需要适当提高涂胶量。
收卷不齐与隧道现象
无溶剂复合膜收卷一定要整齐,否则在收卷松的边缘极
易出现隧道现象。
例如,小纸芯收卷时设定收卷张力锥度为10%(150mm)/15%(300mm)/20%(450mm)时,复合面层时能收卷整齐,在复合内层时则出现收卷不齐现象;改用大纸芯收卷,设定收卷张力锥度为10%(200mm)/30%(350mm)/40%(550mm)时,基本收卷整齐。
收卷张力锥度设定过小时,外层对内层会产生较大的挤压力,如果复合膜收卷后内外层间的摩擦力又较小(薄膜过于爽滑则摩擦力小),则会出现收卷挤出现象。
当设定较大的收卷张力锥度时,就又能收卷整齐了。
这说明无溶剂复合膜的收卷整齐度与张力参数设定有关,与复合膜层间的摩擦力也有关系。
镀铝复合膜水煮后掉铝
无溶剂复合加工的BOPP/VMPET/ PE复合膜,在水煮之后出现掉铝现象,这也是常见问题之一。
笔者测试过三个厂家的无溶剂复合胶水样品,结果有两家的胶水在水煮后的掉铝现象严重,另一家的胶水在多批次测试中的表现也不稳定。
可见,无溶剂复合含镀铝结构的水煮产品时有一定的风险,需要经过多次验证,才能投入批量生产。
爽滑剂含量与摩擦系数
图8是薄膜中爽滑剂含量与薄膜摩擦系数的一般对应关系。
从图8中可见,当薄膜中的爽滑剂浓度高于1000PPM时,
薄膜的摩擦系数已趋于稳定。
可见,在来料检测时规定无溶剂复合膜用PE膜的摩擦系数要小于,以此来控制最终复合膜的摩擦系数,这种方法本身就不太准确可靠。
再比如,我们通过红外光谱法分析PE膜热封面的爽滑剂含量,可以得到如图9所示的红外光谱对照图。
图9中有四条红外光谱曲线,从上至下分别是:
1#曲线薄膜对应的摩擦系数us/ ud=;
2#曲线薄膜是1#薄膜表面用乙醇擦试过的表面(爽滑剂被擦试掉了,以找到爽滑剂的红外光谱峰);
3#曲线薄膜对应的摩擦系数us/ ud=;
4#曲线薄膜对应的摩擦系数us/ ud=。
从图9可见,1#和4#曲线薄膜的爽滑剂峰值最高,说明其表面的爽滑剂含量最多,基本上是3#曲线薄膜的2倍,但摩擦系数上却没有明显区别。
PE膜中爽滑剂量过多引起复合膜剥离强度下降
PE膜中的爽滑剂含量过多,将引起复合膜剥离强度下降,严重的在复合膜熟化完成时就能检测到,而轻微的则在复合膜放置过程中才会出现剥离强度的衰减。
下面两例实际检测情况,可以作为参考。
实例一
(1)结构:消光BOPP/PET12/抗静电PE70,无溶剂复合内层。
(2)主要参数:涂胶量m2,42℃下熟化24小时。
(3)纵向剥离强度检测数据:15mm、15mm(PET撕裂)、15mm、15mm 。
(4)横向剥离强度检测数据:
15mm、15mm、15mm。
(5)现象:如图10所示,PE膜上有一层用手即可擦去的白色物质,用溶剂擦试表明胶层在PE一侧。
实例二
(1)结构:BOPA15/PE133-137,光膜,10月12日生产。
(2)主要参数:涂胶量m2,熟化24小时。
(3)剥离强度检测数据
10月13日检测:横向剥离强度为15mm。
11月4日检测:横向剥离强度为15mm,剥开后PE面上有一层可擦去的雾状物质。
11月18日检测:横向剥离强度为15mm,与前次检测数据接近,说明剥离强度进入稳定状态。
需要说明的是,我们通常检测的都是复合膜熟化完成后不久的剥离强度,很少跟踪测试复合膜在放置过程中剥离强度是否会出现衰减。
采用在PE膜中过量添加爽滑剂的方法,虽然能在一定程度上解决无溶剂复合膜熟化后摩擦系数异
常增大的现象,但也往往会造成剥离强度在包装袋流通环节出现明显衰减。