无溶剂复合工艺
无溶剂聚氨酯复合的工艺控制
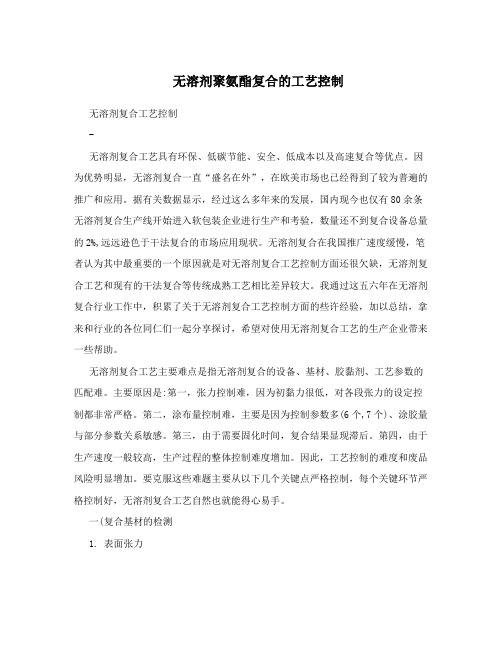
无溶剂聚氨酯复合的工艺控制无溶剂复合工艺控制-无溶剂复合工艺具有环保、低碳节能、安全、低成本以及高速复合等优点。
因为优势明显,无溶剂复合一直“盛名在外”,在欧美市场也已经得到了较为普遍的推广和应用。
据有关数据显示,经过这么多年来的发展,国内现今也仅有80余条无溶剂复合生产线开始进入软包装企业进行生产和考验,数量还不到复合设备总量的2%,远远逊色于干法复合的市场应用现状。
无溶剂复合在我国推广速度缓慢,笔者认为其中最重要的一个原因就是对无溶剂复合工艺控制方面还很欠缺,无溶剂复合工艺和现有的干法复合等传统成熟工艺相比差异较大。
我通过这五六年在无溶剂复合行业工作中,积累了关于无溶剂复合工艺控制方面的些许经验,加以总结,拿来和行业的各位同仁们一起分享探讨,希望对使用无溶剂复合工艺的生产企业带来一些帮助。
无溶剂复合工艺主要难点是指无溶剂复合的设备、基材、胶黏剂、工艺参数的匹配难。
主要原因是:第一,张力控制难,因为初黏力很低,对各段张力的设定控制都非常严格。
第二,涂布量控制难,主要是因为控制参数多(6个,7个)、涂胶量与部分参数关系敏感。
第三,由于需要固化时间,复合结果显现滞后。
第四,由于生产速度一般较高,生产过程的整体控制难度增加。
因此,工艺控制的难度和废品风险明显增加。
要克服这些难题主要从以下几个关键点严格控制,每个关键环节严格控制好,无溶剂复合工艺自然也就能得心易手。
一(复合基材的检测1. 表面张力对于复合基材的检测主要性能指标就是表面张力,对于通常使用的薄膜材料都须经过电晕处理(PE、BOPP膜的表面张力大于40达因,最差须大于38达因;VMPET 薄膜的表面张力大于42达因;PA薄膜的表面张力不得小于50 mN/m;PET薄膜的表面张力不得小于45 mN/m)。
其主要目的是提高胶粘剂的流平,涂布及复合牢度。
相反基材表面张力低于要求值时,会影响其复合牢度,严重的话会产生分层现象。
2. 厚度所用基材必须厚度均匀,厚度均匀性偏差要求控制在10%以内,质量符合国家或行业的相关标准。
挤出复合 干式复合 无溶剂复合

挤出复合、干式复合和无溶剂复合是当今复合材料领域的三种主要生产工艺方法。
它们各自具有独特的特点和应用范围,可以满足不同领域对复合材料的需求。
本文将就这三种复合工艺方法进行详细介绍,并分析它们的优势和不足之处。
一、挤出复合挤出复合是将连续纤维与热塑性基体材料结合的一种工艺方法。
其主要流程包括原料预处理、预成型、挤出成型、冷却固化等环节。
挤出复合具有以下优势:1.1 成型效率高挤出复合可实现高速连续生产,而且一次性成型多根复材,生产效率高。
1.2 产品性能优异挤出复合制品表面光滑、尺寸精度高,具有较好的力学性能和耐腐蚀性能。
1.3 应用广泛挤出复合制品广泛应用于汽车、建筑、航空航天等领域,适用性强。
但挤出复合也存在以下缺点:1.4 设备成本高挤出复合生产线设备投资大,一般中小型企业难以承担。
1.5 能耗较高挤出过程需要大量的能源投入,成本较高。
二、干式复合干式复合是指在无溶剂条件下,通过物理或化学方法将各种原材料进行混合,再进行热压成型而得到的复合材料。
它的优势主要体现在以下几个方面:2.1 无溶剂环保干式复合不需要使用有机溶剂,对环境友好。
2.2 成本低廉干式复合工艺简单、原材料成本低,适合中小企业生产。
2.3 产品性能优异干式复合制品性能稳定、尺寸精度高,适用广泛。
然而,干式复合也存在以下缺点:2.4 工艺复杂干式复合过程中需要严格控制温度、压力等工艺参数,工艺控制难度大。
2.5 质量稳定性差对原材料的要求较高,不同原材料之间容易出现不同的温度、热胀冷缩等性能差异。
三、无溶剂复合无溶剂复合是指复合材料的生产过程中不使用任何有机溶剂。
其主要优势包括:3.1 环保优势无溶剂复合不会对环境造成污染,能够符合现代环保要求。
3.2 节能降耗无溶剂复合生产过程中不需要消耗大量能源,成本较低。
3.3 产品质量高无溶剂复合产品表面光滑、尺寸精度高,性能稳定。
然而,无溶剂复合也存在以下不足之处:3.4 技术含量高无溶剂复合所需技术要求较高,对生产工艺和设备都有一定要求。
无溶剂复合工艺常见问题集锦

无溶剂复合工艺常见问题集锦近年来,无溶剂复合工艺因具有突出的节能、高效、低成本等优势而备受软包装企业的青睐,越来越多的软包装企业开始尝试采用无溶剂复合工艺。
但是,软包装企业在应用无溶剂复合工艺过程中,难免会遇到这样或那样的问题,甚至影响企业的正常生产。
在此,笔者结合自己的实践经验,总结了无溶剂复合工艺中的一些常见问题,在此与大家分享。
胶黏剂涂布后出现收缩现象如图1所示,在用VMPET阴阳膜复合第三层材料时,涂胶后在VMPET薄膜边缘出现胶液收缩现象,检查后发现系VMPET薄膜局部表面能不合格所致。
无溶剂胶液的表面张力远高于干法复合用的溶剂型胶液(稀释用溶剂乙酸乙酯的表面张力仅为26.29mN/ m),如果薄膜整体的表面能低于涂布胶液的表面张力,胶液在薄膜表面就会出现收缩现象;如果薄膜表面局部受一些低表面张力助剂的污染,则在该点就会出现胶液不润湿(收缩)现象,在最终的复合制品上形成气泡缺陷,甚至造成剥离不良的质量问题。
类似的涂胶后胶液收缩现象,在使用水性胶黏剂时也可能出现。
转移胶辊表面温度过高涂布系统的实际温度往往与设定温度有一定偏差,在机速300m/min、上胶量1.45g/m2的条件下,胶桶温度设定为35℃(实测38℃),计量辊温度设定为32℃,涂布辊温度设定为35℃,涂布系统的实测温度分布如图2。
由图2可见,转移胶辊表面温度高达44℃,已严重偏离设定值。
这是由于转移胶辊摩擦生热造成的,其影响因素主要有辊面光洁度、胶水黏度、压力大小等,其中辊面光洁度的影响最大,须严加控制。
胶辊表面胶液分布不均涂胶量太小时,胶辊表面的胶液分布不均匀,局部发涩(不反光),这在某种程度上也反映出涂布系统(转移胶辊)的精度高低。
理论上讲,对于某些复合结构(如BOPP/珠光膜),涂胶量在1.0g/m2就能满足复合强度要求,但如果设备涂布系统的精度不高,则需要适当增加涂胶量,以保证涂胶均匀。
材料起皱引起的复合气泡现象原材料皱褶将直接导致下机的复合产品出现气泡现象,原因是皱褶处复合时压不实,夹入空气。
如何确定无溶剂复合制品的工艺参数

如何确定无溶剂复合制品的工艺参数引言无溶剂复合制品是一种绿色环保的新型材料,其制备工艺参数的确定对于产品的质量和性能具有重要影响。
本文将介绍如何确定无溶剂复合制品的工艺参数,以保证产品的质量稳定性和性能优良性。
步骤一:材料选择在确定无溶剂复合制品的工艺参数之前,首先需要根据产品的要求选择合适的材料。
考虑到无溶剂复合制品的绿色环保特性,选择可再生或可回收利用的材料是一个明智的选择。
同时,还需要考虑材料的物理性质和化学性质,以确保其与其他材料的相容性和复合工艺的可行性。
步骤二:复合工艺设计在进行无溶剂复合制品的工艺参数确定之前,需要进行复合工艺的设计。
复合工艺的设计包括以下几个方面:温度控制确定适宜的复合温度是保证产品质量的重要因素之一。
可以通过调整温度来控制复合材料的粘度和流动性,从而影响材料的分布均匀性和成型性能。
压力控制在无溶剂复合制品的制备过程中,合适的压力能够保证材料的充填性能和密实度,影响产品的强度和稳定性。
通过对压力的控制,可以调节复合制品的力学性能和物理性能。
时间控制复合工艺中的时间控制是影响产品成型和固化的重要因素。
合适的时间控制可以确保复合材料的反应充分,从而影响产品的硬度、耐久性和稳定性。
步骤三:实验验证确定无溶剂复合制品的工艺参数后,需要进行实验验证。
通过不同工艺参数的调整,制备一系列样品,并进行性能测试和分析。
根据实验结果,可以评估和优化工艺参数,以获得最佳的产品性能。
结论通过以上步骤,可以确定无溶剂复合制品的工艺参数,从而保证产品的质量稳定性和性能优良性。
在实际应用中,还可以根据不同的产品要求和工艺条件进行适当的调整和优化,以满足特定的需求和要求。
参考文献:- 张三, 李四. 无溶剂复合材料的制备工艺与性能研究. 材料科学与工程学报, 2018, 36(4): 123-135.- 王五, 赵六. 无溶剂复合制品的制备及其应用. 化学工业, 2019, 45(2): 67-76.。
无溶剂复合_上胶原理_概述及解释说明

无溶剂复合上胶原理概述及解释说明1. 引言1.1 概述本文旨在对无溶剂复合的胶原理进行概述及解释说明。
无溶剂复合技术是一种特殊的复合方法,通过在无需溶剂介质的情况下将不同材料进行结合,以实现特定功能或性能的提升。
1.2 文章结构文章首先介绍了本文的大纲和目录,随后详细阐述了无溶剂复合的胶原理、其优势和挑战、关键步骤和操作方法,并举例分析了实际应用案例。
最后,总结研究内容和发现结果,并展望无溶剂复合技术的未来发展方向。
1.3 目的我们撰写这篇长文的目的是为了深入探讨无溶剂复合技术,揭示其工作原理、优势和挑战,以及关键步骤和操作方法。
通过对该技术的系统介绍和分析,我们希望能够提供给读者一个全面而清晰的理解,同时为相关领域中研究人员提供参考和启示。
此外,文章还致力于展望无溶剂复合技术未来可能取得的突破和应用领域,以期激发更多创新和研究的热情。
2. 无溶剂复合的胶原理:2.1 胶原理概述:无溶剂复合是一种制备复合材料的技术方法,其原理是通过将两种或更多不同类型的材料混合在一起,形成具有新的性能和特性的复合材料。
在无溶剂复合过程中,没有使用溶剂来促使材料之间的粘结,并且通常需要一定的压力或温度条件来实现有效地结合。
2.2 无溶剂复合技术介绍:无溶剂复合技术是采用物理、化学或机械方法将材料混合在一起,形成均匀分散并结实粘附的复合材料。
这通常涉及将两个或多个组分(如固体颗粒、纤维、填充物等)以适当比例混合,并通过加热、压缩、挤出等工艺步骤施加特定条件来完成粘结和固化过程。
无溶剂复合技术可以应用于不同领域,例如塑料制品、纤维增强复合材料、金属-陶瓷复合材料等。
2.3 无溶剂复合应用领域:无溶剂复合技术在各个领域都有广泛的应用。
在塑料制品方面,无溶剂复合可用于制造高性能工程塑料和塑料复合材料,提供优异的力学性能和特殊功能。
在纤维增强复合材料中,无溶剂复合可用于制备轻质、高强度和刚度的纤维增强复合材料,如碳纤维复合材料、玻璃纤维复合材料等。
知识点21 软包装无溶剂复合工艺.
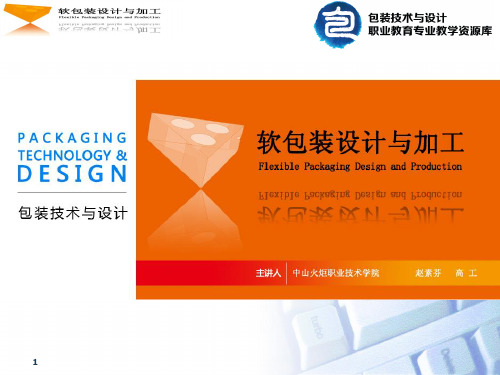
第一放卷:刚性较大、形变较小、涂布性能好。
第二放卷:易拉伸、形变大。
BOPP 和 CPP分别是哪个放卷装置?
涂布单元:是无溶剂复合机的中心部分,胶黏剂在此混合 、加热、计量和涂布。
涂布由计量辊、转移钢辊、转 移胶胶辊、涂布钢辊和涂布压 辊组成。
• 1辊固定不动,它起到刮胶作用;
• 1和2辊两辊的间槽起储胶作用,两者的间隙决定了上胶
收卷装置:因无溶剂复合初粘力低,要求收卷时尽量收紧。
pressure
无溶剂复合
优点: 1.环保适性好
2. 安全性好
3. 产品质量得到保证 4.可明显降低成本
无溶剂复合
缺点:
实际生产中,由于无溶剂胶黏剂的初始黏度很低,操作
控制难度加大,容易出现各种质量问题。
软包装设计与加工
主讲人:赵素芬
1
软包装无溶剂复合工艺
无溶剂复合是采用无溶剂类胶粘剂,使膜状基材(塑
料薄膜或其它膜状材料)相互帖合,然后经熟化(胶粘剂的 化学反应)使各层基材牢固地结合在一起,从而取得多层复 合薄膜的一种加工方法。
无溶剂复合由第一放卷、涂布单元、复合单元、第二
放卷和收卷单元组成。
量的量,1辊也称之为计量辊;
• 涂布量的大小的调节是根据辊2转移钢辊、辊3转移胶
辊和辊4涂布钢辊之间速比变化和温度的稳定性来调节 的,它们分别使用单个直流电机控制;
复合单元:把第一基材和第二基材复合在一起。
复合辊
复合膜
白点/气泡
复合强度高 外观优
复合强度低 外观差
检验方法:放复写纸在2张打印纸中间/压合在左、中、右/ 测量复写纸在打印纸上的压痕宽度/进行比较
无溶剂复合机工艺流程
无溶剂复合机工艺流程
1、准备工作。
检查无溶剂复合机的电源、机械传动和液压系统是否正常工作;准备复合膜和基材,并确保其质量符合标准;对基材表面进行清洗处理,以提高复合效果;确定复合机的工作参数,如复合温度、压力和速度。
2、操作步骤。
开启无溶剂复合机,等待设备升温至设定温度;将基材放入放卷装置中,并拉出一定长度的基材,同时将复合膜放入复合装置中;通过操作控制台调整复合参数,使设备达到最佳操作状态;开始复合操作,将基材和复合膜送入复合装置,设备自动完成复合过程;复合完成后关闭设备开关,并使用切断机将复合膜和基材分开。
无溶剂复合工艺试验及质量控制
无溶剂复合工艺试验及质量控制无溶剂复合主要工艺流程(1)放卷:在一定张力控制下,将待复合基材(料卷)平稳地展开,以便进行涂胶和复合等操作。
两层复合基材中,被涂胶的基材称为主基材,另一基材则称为副基材,相应的放卷操作分别称为主放卷和副放卷。
(2)上胶:一定温度下,将双组分胶黏剂按照一定比例(通常为重量比)进行均匀混合,再输送到无溶剂复合机的储胶部位,或将单组分胶黏剂直接输送到无溶剂复合机的储胶部位。
(3)涂布:按照复合结构和具体使用要求,将混合好的无溶剂胶黏剂适量地涂覆在基材上。
(4)复合:在适当均匀的压力下,将已涂胶的基材与另一基材进行黏合。
(5)收卷:将黏合的复合膜在适当的张力和收卷压力下进行卷取。
(6)固化:将复合卷材放置在一定温度的环境中,使无溶剂胶黏剂充分反应,从而得到期望的复合强度。
固化是无溶剂复合的一个重要工序,该过程通常需要在特定的温度和持续较长时间的条件下才能基本完成。
通常情况下,双组分胶黏剂常见的固化温度为35〜45C,常见的固化时间为24〜48小时,视胶黏剂类型、复合结构和使用场合不同而异,通常后加工工序为分切或再次复合时,固化时间可以较短,而后加工工序为制袋时则固化时间较长。
无溶剂复合工艺试验当初次使用无溶剂复合工艺时,或无溶剂复合生产过程中所使用的复合基材、油墨、胶黏剂及包装成品使用条件等任一因素发生变更时,都应进行无溶剂复合工艺试验。
1.目的和内容无溶剂复合工艺试验的目的是检验无溶剂复合工艺的适用性,确认复合基材、油墨和胶黏剂等因素的符合性,确定复合产品的外观质量和使用性能,并探讨最佳的无溶剂复合工艺方案或标准。
简单地说,无溶剂复合工艺试验要解决3 个问题,即能否复合?复合后产品能否合格?如何确定批量生产的工艺条件?无溶剂复合工艺试验通常包含以下几方面内容:印刷油墨与无溶剂胶黏剂的相容性检测;复合产品外观质量检测;复合产品表面摩擦系数检测;镀铝转移检测;其他使用性能检测;涂胶量、混配比、设备参数、固化温度、固化时间等生产工艺参数的确定。
无溶剂复合工艺
上海康达公司WD8118A/B,WD8158A/B, WD8168A/B双组分胶性能指标
性能 WD/B A 固体含量 配比(重 量比) 100 100 B 100 75 WD/B A 100 100 B 100 80 WD/B A 100 100 B 100 80
密度 1.12± ( g/cm3 ) 0.01 粘度/ mPa· s 用途 1000~ 1200 水煮
3、贴合型复合工艺 贴合型复合工艺,指应用粘合的方法,将两基材贴(粘)合而 生产复合薄膜的方法,包括挤出复合、热熔胶复合、干法复合、湿 法复合、无溶剂复合等等 挤出复合:使用挤出机将热塑性塑料熔融,然后经过T型模头, 流淌涂覆在一基材薄膜的表面上,趁热将另一基膜压贴在它的上面 而生产复合薄膜的工艺。 热熔胶复合:采用熔胶池(或者挤出机)使热熔胶熔融,再通 过辊涂(或T模头)涂布到一基膜表面上,趁热将另一基材贴合到 其上面而生产复合薄膜的工艺。 干法复合:将溶剂型化学反应性胶粘剂涂布在一基材薄膜的表 面,然后干燥挥发胶中的溶剂,再与另一基材薄膜ห้องสมุดไป่ตู้合,经化学反 应(熟化)而生产复合薄膜的工艺; 湿式复合:将溶剂型化学反应性胶粘剂涂布一基材薄膜的表面,随 即使其上贴合另一基膜,然后使胶粘剂干燥、固化而生产复合薄膜 的工艺。 无溶剂复合:将无溶剂型化学反应性胶粘剂涂布一基材薄膜的 表面,随即使其上贴合另一基膜,然后使胶粘剂熟化而生产复合薄 膜的工艺。
无溶剂复合与干法复合两种工艺的工艺过程的比较: 无溶剂复合: 基材1→放卷→涂胶(涂无溶剂型胶粘剂)→贴合→收卷→ ↑ 放卷 ↑ 基材2 熟化→成品 干法复合 : 基材1→放卷→涂胶(涂溶剂型胶粘剂)→烘道干燥→贴合→ ↑ 放卷 ↑ 基材2 收卷→熟化→成品
两种工艺的相同之处在于:它们都是利用粘 合剂,将两种膜状基材粘合而制取复合薄膜,由于 在复合过程中有粘合剂的熟化过程(化学反应), 粘合效果较好、层间复合牢度较高,对基材的适应 好、应用面广。 两种工艺之间,也有一个“细微的”差别, 即干法复合工艺使用的是溶剂型(或水分散型)黏 合剂,在生产复合软包装材料的过程中,涂胶以后 两基材贴合(复合)之前 ,需要把粘合剂中的溶 剂(或分散剂水)烘干;而无溶剂复合工艺使用的 是无溶剂粘合剂,涂胶以后两基材不经过烘干处理, 即将两基材贴合(复合),也正因为这一“微小的 差异”,无溶剂复合较之干法复合,呈现出一系列 突出的优点。
无溶剂复合工艺三大技术风险,有什么控制要点
无溶剂复合工艺三大技术风险,有什么控制要点无溶剂复合工艺显著的优势有降低成本、高效节能、生产安全稳定、提升产品质量等,是一种值得大力倡导、极具实用价值的生产工艺。
然而,当前无溶剂复合工艺还没有达到成熟阶段,软包装企业在应用过程中仍然存在一些容易被忽视的技术风险,从而导致质量问题的出现。
为此,我总结了3个较为常见的无溶剂复合技术风险控制要点,并对其原因进行了分析,与行业人士分享。
要点一,无溶剂复合中增加A胶量的技术风险无溶剂复合双组分(A胶和B胶)胶黏剂混配比例一般是指A胶和B胶的重量比,而不是二者的体积比。
双组分胶黏剂的混配比例一般由胶黏剂生产厂家来确定,因为不同品牌、不同用途胶黏剂的配比一般也不同。
虽然目前国内无溶剂胶黏剂生产厂家有很多,但A胶和B胶重量比的选项并不多,比较常见的A∶B有100∶80、100∶75、100∶50、100∶45等。
但在软包装企业实际的无溶剂复合生产中,双组分胶黏剂的配比会出现失调的情况,这就会对软包装产品无溶剂复合质量产生影响。
案例:复合结构为OPP/VMPET/PE的软包装袋,经过印刷、无溶剂复合工序后都没有出现质量问题,但在分切制袋后,其封边却出现了卷边现象。
该结构复合软包装袋采用的是某品牌低黏度无溶剂胶黏剂,实际复合生产中A、B胶的配比为100∶67(注意:根据上文所述,与之比较接近的正常配比为100∶75)。
在分析故障原因时,发现袋子卷边的同时还伴随内层胶黏剂不干的现象。
原本以为是复合膜熟化程度不完全所致,后延长熟化时间再进行分切制袋,袋子卷边问题依然存在,且开口性也严重变差。
在干式复合工艺中存在“提高固化剂(-NCO组分)可以提高复合强度”的说法,行业人士很容易将这种思路也“复制”到无溶剂复合工艺中,从而导致了较严重的质量事故。
事实上,在无溶剂复合工艺中,无论是-OH过量还是-NCO过量,都可能导致无溶剂胶黏剂不干的现象,只是-OH过量造成的是永久性不干,而-NCO过量造成的是短暂性不干,其还可以与空气中的水分子发生反应而继续固化。
- 1、下载文档前请自行甄别文档内容的完整性,平台不提供额外的编辑、内容补充、找答案等附加服务。
- 2、"仅部分预览"的文档,不可在线预览部分如存在完整性等问题,可反馈申请退款(可完整预览的文档不适用该条件!)。
- 3、如文档侵犯您的权益,请联系客服反馈,我们会尽快为您处理(人工客服工作时间:9:00-18:30)。
无溶剂复合较之干法复合的的主要优点 1、安全、卫生性好 无溶剂复合生产中不使用可燃、易爆性有机溶剂,故安全性 好;复合薄膜中不会因残余溶剂的存在导致卫生性能下降, 产品卫生性能可靠性佳。 2、环保适应性好 无溶剂复合使用的胶粘剂是百分之百的胶,不含任何溶剂, 因而在生产过程中,除停机时需要用少量溶剂对涂胶部分进 行清洗之外,没有溶剂排放,生产中没有三废物质产生,不 会由于大量溶剂的排放影响生产工人的身体健康,也不会对 周边环境产生污染,有利于清洁化生产。 3、节约资源显著: 不使用溶剂; 没有烘道干燥过程,可节约大量能源; 上胶料少:无溶剂复合单位面积胶粘剂涂布量约为干法复合 单位面积胶粘剂干基涂布量的五分之二;
无溶剂复合与干法复合两种工艺的工艺过程的比较: 无溶剂复合: 基材1→放卷→涂胶(涂无溶剂型胶粘剂)→贴合→收卷→ ↑ 放卷 ↑ 基材2 熟化→成品 干法复合 : 基材1→放卷→涂胶(涂溶剂型胶粘剂)→烘道干燥→贴合→ ↑ 放卷 ↑ 基材2 收卷→熟化→成品
ห้องสมุดไป่ตู้
两种工艺的相同之处在于:它们都是利用粘 合剂,将两种膜状基材粘合而制取复合薄膜,由于 在复合过程中有粘合剂的熟化过程(化学反应), 粘合效果较好、层间复合牢度较高,对基材的适应 好、应用面广。 两种工艺之间,也有一个“细微的”差别, 即干法复合工艺使用的是溶剂型(或水分散型)黏 合剂,在生产复合软包装材料的过程中,涂胶以后 两基材贴合(复合)之前 ,需要把粘合剂中的溶 剂(或分散剂水)烘干;而无溶剂复合工艺使用的 是无溶剂粘合剂,涂胶以后两基材不经过烘干处理, 即将两基材贴合(复合),也正因为这一“微小的 差异”,无溶剂复合较之干法复合,呈现出一系列 突出的优点。
无溶剂复合工艺
中包联塑料委专家委员会副主任兼秘书长 上海市包协会绿色包装委员会秘书长 陈昌杰
无溶剂复合是经典的、成熟的、常 用的一种生产复合薄膜的工艺;
• 西德Herbert公司继上世纪六十年初期干法复合工 艺产业化之后,即开始了无溶剂复合的研究,并 于1974年推出了无溶复合工艺,自二十世纪八十 年代以后,逐渐成为欧洲工业发达国家的塑料复 合薄膜的主导生产工艺。 • 我国从上世纪八十年代初开始引进无溶剂复合生 产线,经历了漫长的孕育期,至2008年全国仅30 来条生产线,2008年以后,有了飞速的发展,目 前无溶剂复合生产线已发展到100条左右。
3、贴合型复合工艺 贴合型复合工艺,指应用粘合的方法,将两基材贴(粘)合而 生产复合薄膜的方法,包括挤出复合、热熔胶复合、干法复合、湿 法复合、无溶剂复合等等 挤出复合:使用挤出机将热塑性塑料熔融,然后经过T型模头, 流淌涂覆在一基材薄膜的表面上,趁热将另一基膜压贴在它的上面 而生产复合薄膜的工艺。 热熔胶复合:采用熔胶池(或者挤出机)使热熔胶熔融,再通 过辊涂(或T模头)涂布到一基膜表面上,趁热将另一基材贴合到 其上面而生产复合薄膜的工艺。 干法复合:将溶剂型化学反应性胶粘剂涂布在一基材薄膜的表 面,然后干燥挥发胶中的溶剂,再与另一基材薄膜贴合,经化学反 应(熟化)而生产复合薄膜的工艺; 湿式复合:将溶剂型化学反应性胶粘剂涂布一基材薄膜的表面,随 即使其上贴合另一基膜,然后使胶粘剂干燥、固化而生产复合薄膜 的工艺。 无溶剂复合:将无溶剂型化学反应性胶粘剂涂布一基材薄膜的 表面,随即使其上贴合另一基膜,然后使胶粘剂熟化而生产复合薄 膜的工艺。
4、可明显地降低生产成本 ⑴无溶剂复合单位面积上胶量少,上胶成本低,有 望节约粘合剂成本30 % ~50%(无溶剂复合单位 面积胶粘剂用量约为干法复合单位面积胶粘剂干基 涂布量2/5~1/2,且不耗用溶剂); ⑵无溶剂复合一次性投资少,设备回收折旧成本也 比较小(复合设备没有预干燥烘道,设备造价较低, 可降低30%或者更多;设备占地面积小,可明显降 低车间面积;无溶剂复合黏合剂的体积小且不用储 藏溶剂,可以减少仓储面积;); ⑶无溶剂复合,节能显著 ; ⑷无溶剂复合生产线速度明显提高,因而可以使生 产成本降低; ⑸无溶剂复合不需治理三废
小结:贴合型复合工艺将两种不同的基材贴合 而生产复合薄膜,适应面极广,理论上可用于任何 两种基材贴合而生产如何结构的复合薄膜,但实际 上由于挤出复合与热熔胶复合,依靠的是物理结合, 层间粘合力强度收到限制,因此一般只用于生产复 合强度要求较低的产品;湿法复合在贴合之后,需 要通过基材排除溶剂型粘合剂中的溶剂(或乳液型 粘合剂中的分散液),使粘合剂的干燥,才能得到 最终的复合制品,只适用于至少一个具有疏松结构 的基材(比如纸张)的复合,应用面受到极大的限 制,在贴合型复合工艺中惟有干法复合、无溶剂 复合是目前真正应用面广、应用量极大的两种复 合工艺。
2、表面涂覆型复合工艺 表面涂覆型复合工艺,包括挤出涂敷、溶液(或乳液)涂布、 热熔胶涂布与蒸镀等工艺。 挤出涂敷:使用挤出机将热塑性塑料熔融,然后经过T型模头, 流淌涂覆在一基材薄膜的表面上而生产复合薄膜的工艺。 溶液(或乳液)涂布:该法将所溶液(或乳液)涂布到基材的 表面,然后干燥而生产复合薄膜的工艺。 热熔胶涂布:采用熔胶池(或者挤出机)使热熔胶熔融,再通 过辊涂(或T模头)涂布到一基膜表面上而生产复合薄膜的工 艺。 蒸镀亦称喷涂:在高真空条件下使铝或低沸点的氧化物挥发 (或者通过化学反应形成等离子体)、再使之沉积于基材的表 面,形成致密的涂层而生产复合薄膜的工艺。 表面涂覆型复合工艺,可以通过在基材的表面,涂覆一层薄薄 的涂层,甚至于纳米级的涂层,达到复合改性的目的,但局限 性较大,除用于生产一些特定的复合薄膜(如表面保护膜)等 终端产品之外,大量用于生产复合薄膜的基材。
复合薄膜的常用工艺盘点
• 复合薄膜的常用工艺有三个大类,即共挤 出、表面涂覆和贴(粘)合型复合三个大 类。
1、共挤出复合:使用两台和两台以上的挤出机将 塑料熔融体,供入一个共挤出模头中,在共挤出模内 分层汇合后从模唇挤出,从而生产多层复合薄膜的方 法; 共挤出复合的突出优点是直接由塑料粒子生产复 合薄膜,工艺路线短、能耗小且可把价格昂贵的塑料 层做得很薄(比如2μ左右),降低生产成本; 它在生产过程中,不产生任何有毒有害物质,是 典型的清洁化生产工艺,是一种值得大力倡导的复合 工艺。 共挤出复合的两大局限: ⑴它只能生产全部由热塑性塑料生产的塑料复合 薄膜; ⑵它只能生产表面印刷的复合薄膜而不能生产里 印的复合薄膜;