如何确定无溶剂复合的工艺参数
无溶剂复合工艺控制小窍门
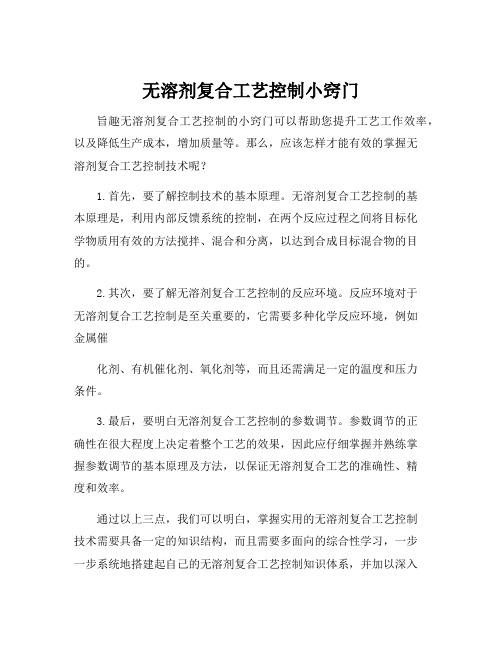
无溶剂复合工艺控制小窍门
旨趣无溶剂复合工艺控制的小窍门可以帮助您提升工艺工作效率,以及降低生产成本,增加质量等。
那么,应该怎样才能有效的掌握无
溶剂复合工艺控制技术呢?
1.首先,要了解控制技术的基本原理。
无溶剂复合工艺控制的基
本原理是,利用内部反馈系统的控制,在两个反应过程之间将目标化
学物质用有效的方法搅拌、混合和分离,以达到合成目标混合物的目的。
2.其次,要了解无溶剂复合工艺控制的反应环境。
反应环境对于
无溶剂复合工艺控制是至关重要的,它需要多种化学反应环境,例如
金属催
化剂、有机催化剂、氧化剂等,而且还需满足一定的温度和压力
条件。
3.最后,要明白无溶剂复合工艺控制的参数调节。
参数调节的正
确性在很大程度上决定着整个工艺的效果,因此应仔细掌握并熟练掌
握参数调节的基本原理及方法,以保证无溶剂复合工艺的准确性、精
度和效率。
通过以上三点,我们可以明白,掌握实用的无溶剂复合工艺控制
技术需要具备一定的知识结构,而且需要多面向的综合性学习,一步
一步系统地搭建起自己的无溶剂复合工艺控制知识体系,并加以深入
的研究,才能有效的掌握无溶剂复合工艺控制技术的相关知识,进而提升工作效率和生产质量,充分发挥无溶剂复合工艺控制的作用。
无溶剂复合推广的几个重要问题

无溶剂复合推广的几个重要问题一、如何正确认识无溶剂复合技术(一) 无溶剂复合的特点无溶剂复合是一项真正环保、可广泛应用于软包装印刷行业的工艺技术,代表了包装的复合技术的方向之一。
1.它是一项典型的“三无”工艺。
这是无溶剂复合最突出的特点。
①全过程无污染;②产品无溶剂残留;③生产过程无安全隐患。
2.其应用与人们日常生活密切有关。
表1 国外常见双层复合实例(二) 与其它复合方式相比较的优势与溶剂型、水性胶的干式复合相比,无溶剂复合在涂胶成本、节能、减排方面都有明显的优势。
1.涂胶成本分析国内外资料显示,无溶剂复合通常涂胶量在1.5~2.0 g/m2;而胶粘剂价格通常国产供应商为35~38元/公斤,国际供应商大约高15~20%;无溶剂涂布总成本为0.054~0.072元/m2。
溶剂型胶干式复合涂布总成本(含干燥成本)为0.132~0.157元/m2;而水性胶干式复合的涂布总成本(含干燥成本)为0.101~0.124元/m2。
通过改进工艺,现在有少量企业的干式复合成本已经能够操纵0.10元/m2以内。
有两点值得注意:①根据我们的实际测试与国内用户的调查,绝大部分印刷膜的无溶剂复合的涂胶量为1.2~1.5 g/m2,非印刷膜(白膜)的涂胶量在0.8~1.2 g/m2,因此实际成本比上述数据更低。
②水性胶的复合牢度与适用范围与无溶剂复合、溶剂型干式复合有一定差距,因此它们之间不具有完全的可比性。
2.干燥能耗分析无溶剂复合通常工作速度为250~300米/分,完全不需要机上干燥系统,而复合后的固化通常在40℃,相关于干式复合耗能很低。
干式复合机通常工作速度120~150米/分,干燥系统是一个必不可少的装置。
以150米/分速度、机器宽度1000毫米为例,假设平均电价0.8元/度、年工作时间3000小时(=250天/年×12小时/天),溶剂型干式复合机年电费约20万,水性胶干式复合年电费则近30万。
由分析计算还能够看出:- 无溶剂复合比溶剂型干式复合节约电费0.7分/平方米左右,比水性胶复合节约1.1分/平方米左右。
无溶剂聚氨酯复合的工艺控制
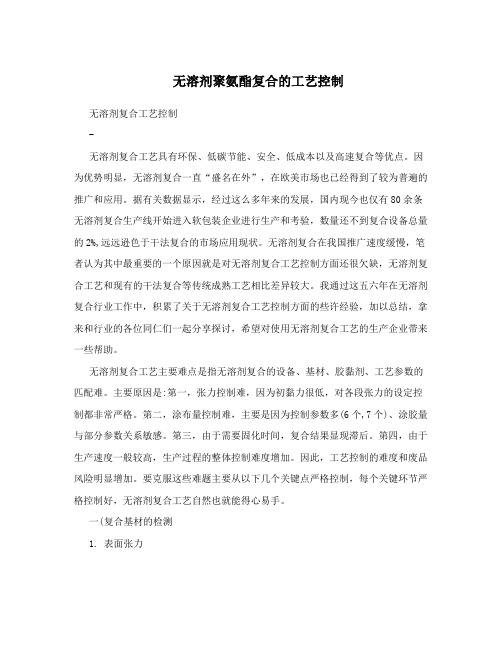
无溶剂聚氨酯复合的工艺控制无溶剂复合工艺控制-无溶剂复合工艺具有环保、低碳节能、安全、低成本以及高速复合等优点。
因为优势明显,无溶剂复合一直“盛名在外”,在欧美市场也已经得到了较为普遍的推广和应用。
据有关数据显示,经过这么多年来的发展,国内现今也仅有80余条无溶剂复合生产线开始进入软包装企业进行生产和考验,数量还不到复合设备总量的2%,远远逊色于干法复合的市场应用现状。
无溶剂复合在我国推广速度缓慢,笔者认为其中最重要的一个原因就是对无溶剂复合工艺控制方面还很欠缺,无溶剂复合工艺和现有的干法复合等传统成熟工艺相比差异较大。
我通过这五六年在无溶剂复合行业工作中,积累了关于无溶剂复合工艺控制方面的些许经验,加以总结,拿来和行业的各位同仁们一起分享探讨,希望对使用无溶剂复合工艺的生产企业带来一些帮助。
无溶剂复合工艺主要难点是指无溶剂复合的设备、基材、胶黏剂、工艺参数的匹配难。
主要原因是:第一,张力控制难,因为初黏力很低,对各段张力的设定控制都非常严格。
第二,涂布量控制难,主要是因为控制参数多(6个,7个)、涂胶量与部分参数关系敏感。
第三,由于需要固化时间,复合结果显现滞后。
第四,由于生产速度一般较高,生产过程的整体控制难度增加。
因此,工艺控制的难度和废品风险明显增加。
要克服这些难题主要从以下几个关键点严格控制,每个关键环节严格控制好,无溶剂复合工艺自然也就能得心易手。
一(复合基材的检测1. 表面张力对于复合基材的检测主要性能指标就是表面张力,对于通常使用的薄膜材料都须经过电晕处理(PE、BOPP膜的表面张力大于40达因,最差须大于38达因;VMPET 薄膜的表面张力大于42达因;PA薄膜的表面张力不得小于50 mN/m;PET薄膜的表面张力不得小于45 mN/m)。
其主要目的是提高胶粘剂的流平,涂布及复合牢度。
相反基材表面张力低于要求值时,会影响其复合牢度,严重的话会产生分层现象。
2. 厚度所用基材必须厚度均匀,厚度均匀性偏差要求控制在10%以内,质量符合国家或行业的相关标准。
一种四合一无溶剂复合机及复合工艺控制方法与流程

一种四合一无溶剂复合机及复合工艺控制方法与流程一、引言复合技术是指将两种或以上不同材料通过某种方法结合成一种材料的技术。
该技术主要应用于塑料、合成革、医用材料、保温材料、建筑防水材料等领域。
目前,复合设备主要采用溶剂法和无溶剂法两种方式进行。
为了避免溶剂对环境造成的危害,无溶剂复合技术逐渐成为行业的热点。
二、四合一无溶剂复合机的组成4合1无溶剂复合机由辊式平移复合机、膜式压力复合机、热合复合机和超声波复合机4个部分组成。
1.辊式平移复合机该部分主要由平移机台、辊式压制机、剪切装置和送材装置等组成。
在送材装置中采用磨粒式主动送材系统,材料经由左侧进料杆自动上料,材料以恒定速率进入压力机,通过对辊轴直径、辊表面、压力、转速的合理配合,将原辅材料进行压制固化,以增强复合基体的抗拉力和撕裂强度。
2.膜式压力复合机膜式压力复合机主要由人机界面、电磁阀控制系统、加热板、冷却系统、吸附式膜夹层和卷取装置等部分组成。
人机界面主要由PLC控制系统和触摸屏组成,通过操作触摸屏调整加热、加压、温度等参数,确保复合过程中的稳定性。
3.热合复合机热合复合机主要由加热板、压力机构、切割系统、自动送料机和控制系统等部分组成。
加热板采用热油循环系统,加热快速、均匀,可调节温控,确保复合品质。
压力机构采用气动控制,保证压力均匀,使复合品质更加完美。
4.超声波复合机超声波复合机由超声波振荡器和机械臂组成,其中超声波振荡器通过传递高频声波使两个材料发生摩擦热,产生熔融状态并形成复合。
机械臂用于操纵工件进行复合,使其不会受复合过程中的拉伸或切割等影响。
三、四合一无溶剂复合机的工艺控制方法及流程1.材料准备准备好需要复合的材料,进行定量分装。
要求材料宜在干燥条件下保管,并要求原厂提供质保书和生产合格证等相关资料。
2.预处理准备好的材料进入预处理室,经过去污、去油、去水等多道工序,然后放置在烘箱中进行烘干处理。
待材料完全干燥后,依次送入辊式平移复合机。
无溶剂复合应用技术的几个重点问题提示

无溶剂复合应用技术的几个重点问题提示首先做两点说明:1、作为一项新的工艺技术,对无溶剂复合我们保持一个开放的、学习的、共同进步的心态。
总体来说,国内对无溶剂复合的认识和经验都还很初浅,各种不同看法实属正常,有些观点不全面、不准确甚至错误都不奇怪!下面的观点也只是我们一家之言,欢迎批评指正!2、对于无溶剂复合,我们不仅要学习、更要创新!中国的情况(复合结构、最终用户、材质差异、印刷质量、技术管理基础、作业习惯等)比任何一个国家都复杂,国外的经验我们要充分地学习和借鉴,同时也必须看到:完全照搬是不能解决问题的的,最主体的、最复杂的应用技术最终要我们在创新的基础上立足于在国内解决。
特别强调:这是一项系统工程,需要我们一起努力!1、无溶剂复合工艺要素(1)料带张力。
料带张力的精确控制是料带正常运行和高速复合正常进行的基本条件。
(2)涂胶量。
涂胶量不仅直接决定了复合质量,而且还在很大程度上影响到复合成本。
(3)混配比。
混配比是双组份胶完成正常反应固化的关键因素,也是影响复合牢度的重要因素。
(4)工作环境,包括机外大环境和机上小环境。
机外大环境最重要的是指环境相对湿度。
机上小环境主要是指辊筒温度、气压等因素。
工作环境是工艺正常稳定的必要条件。
(5)固化条件,主要包括固化温度和固化时间。
固化条件是无溶剂复合最主要的机外工序条件,是实现预期复合质量的另一关键因素。
当然熟化空间的湿度也是一个重要因素。
上述5个方面我们称之为无溶剂复合的五大工艺要素。
2、关于张力的几点说明(1)在无溶剂复合中,对张力控制的要求比普通复合要高。
主要原因有二:1)无溶剂复合初粘力较低,2)无溶剂复合机通常速度比干式复合机要高很多(常见速度为250~600m/min),因此对张力的要求原则上比干式复合更为严格。
(2)我们强调的是两层复合料带之间张力的匹配性,而不仅仅是张力系统本身的精度。
在当前技术条件下,许多复合机张力系统的性能精度都是良好的,可以满足无溶剂复合的需要。
无溶剂复合涂布均匀性

涂布均匀性也称涂胶均匀性、上胶均匀性,是复合工艺最基本的要求之一。
1、涂布均匀性的含义所谓涂布均匀性是指在涂布区域内涂层厚度或涂胶量分布的一致性。
涂层厚度或涂胶量的一致性越好,涂布均匀性越好,反之越差。
涂布均匀性并没有统一的度量指标,可以用一定区域内各点的涂层厚度或涂胶量相对于该区域的平均涂层厚度或涂胶量之偏差或偏差百分比来衡量,也可以用一定区域内最大和最小涂层厚度或涂胶量之差来衡量。
涂层厚度通常用µm表示,而涂胶量用g/㎡表示。
在软包装无溶剂复合中,涂胶量一般为1.0~2.0 g/㎡。
如果涂胶量误差控制在±0.1 g/㎡之内的属于均匀性好;涂胶量误差在±0.2 g/㎡之内的属于均匀性良好;涂胶量误差在±0.3 g/㎡或更大的则属于均匀性一般或较差。
涂布均匀性的要求并不是一成不变的,与复合产品的用途和复合基材类型等都有密切关系。
比如,在纸塑复合、网布复合、皮革复合中,涂胶量误差控制在±(0.3~0.5)g/㎡都属于涂布均匀性良好的情况,因为在这些场合中涂胶量一般都比较大,比如纸塑复合常见的涂胶量为2.0~3.5 g/㎡,多数网布复合的涂胶量为5.0~10.0 g/㎡。
因此,用涂胶量偏差的百分比来衡量涂布均匀性是一个更合理的方法。
我们认为:涂胶量误差在±10%以内的是均匀性好的涂布,在±20%以内的是均匀性较好的涂布,±20%以上的是均匀性较差的涂布。
如前所述,软包装无溶剂涂胶量一般为1.0~2.0 g/㎡,如果涂胶量误差为±0.1 g/㎡,其误差百分比即为±(5%~10%)。
2、涂布的横向均匀性和纵向均匀性涂布均匀性都是用来评价一个区域的整体涂胶状况的。
但在实际生产中,我们通常更关心在基材横向和纵向两个方向上的均匀性。
所谓横向均匀性在涂布宽度方向(或机器横向)上的均匀性。
所谓纵向均匀性是在涂布长度方向(或基材行进方向)上的均匀性。
无溶剂复合工艺关键控制点
无溶剂复合工艺关键控制点作者:於亚丰来源:《印刷技术·包装装潢》2014年第03期无溶剂复合工艺凭借环保、节能、安全、低成本、高速等优点,目前在欧美地区软包装市场已得到较为普遍的推广和应用。
相比之下,国内目前仅有百余条无溶剂复合生产线在软包装企业安装使用,市场应用规模远不及干式复合工艺。
无溶剂复合工艺之所以在我国软包装市场推广缓慢,笔者认为其中一个重要原因就是,无溶剂复合与干式复合在工艺控制上存在很大差异,操作人员对无溶剂复合工艺缺乏实际操作经验和系统认识。
无溶剂复合工艺控制的难点主要在于无溶剂复合设备、复合基材、胶黏剂、工艺参数之间的合理匹配。
其一,张力控制难,这是因为无溶剂胶黏剂的初黏力很低,对复合基材各段张力的设定和控制要求都非常严格;其二,涂布量控制难,这是因为涂布量控制参数较多(6~7个),且涂胶量受部分参数的影响较大;其三,无溶剂复合需要较长的固化时间,复合结果显现滞后;其四,生产速度较高,使得生产过程的整体控制难度较大。
以上这些难点如果控制不好,就会严重影响软包装产品复合质量,从而无法满足客户需求。
因此,笔者认为,要想攻克这些难点,操作人员需要把握好无溶剂复合过程中的几个关键点。
复合基材的检测与要求1.表面张力表面张力是复合基材检测的主要性能指标,常用的薄膜材料都须经过电晕处理,以使其具有合适的表面张力。
一般要求PE、BOPP薄膜的表面张力>40mN/m,VMPET薄膜的表面张力>42mN/m,PA薄膜的表面张力≥50mN/m,PET薄膜的表面张力≥45mN/m。
这样做的主要目的是为了提高胶黏剂的流平性和复合牢度。
如果复合基材的表面张力低于要求值,就会影响复合膜的复合牢度,严重时还会导致分层现象。
2.厚度复合基材厚度必须均匀,且厚度均匀性偏差要求控制在10%以内,产品质量符合国家或行业相关标准。
3.宽度复合基材宽度不应超过无溶剂复合设备允许的最大幅宽,同时也不应小于无溶剂复合设备允许最大幅宽的60%;复合基材宽度应大出涂布基材宽度0~5mm;各试验基材最小幅宽至少大出试验用转移胶辊宽度10mm,但最多不大出20mm。
如何确定无溶剂复合的工艺参数
如何确定⽆溶剂复合的⼯艺参数
如何确定⽆溶剂复合的⼯艺参数
1、涂胶量
即通过⼯艺试验来确定最佳涂胶量范围,为批量⽣产提供依据。
这⼀点只要⽐较不同涂布量的样品质量就能判断。
2、混配⽐
⼀般胶粘剂说明书中都指定了该胶粘剂的“标准混配⽐”,但在实际⽣产中,时常会有⽤户根据产品要求,⼩幅度调整混配⽐,以达到改变熟化速度和胶膜柔软性、或提⾼转移膜剥离效果等⽬的。
这⼀点在镀铝膜、转移膜复合中⽐较常见。
因此,通常需要通过⼯艺试验来确认“⽣产混配⽐”。
3、机器参数
包括各段张⼒、收卷张⼒锥度、涂布压⼒、复合压⼒、收卷压⼒、最⾼运⾏速度等。
4、固化温度
⼀般胶粘剂说明书中都指定了该胶粘剂的“参考熟化温度”,但在实际⽣产中,时常会有⽤户根据复合结构和使⽤要求,在指定范围内⼩幅度调整熟化温度。
因此,可通过⼯艺试验来确认最佳的“⽣产熟化温度”。
5、上胶基材
对于部分复合结构(⽐如纸塑复合、纸铝复合、铝塑复合等),改变涂布基材可以获得不同的复合质量和最佳涂胶量,因此,通过⼯艺试验确定上胶基材是⼀项⾮常必要的试验。
6、固化⽔分
主要是确认空⽓中的⽔分或湿度是否满⾜⽣产要求。
在使⽤单组分胶的复合中,⽔分是反应固化的⼀个必要条件。
但它是由基材(如纸张)中的含⽔量和空⽓湿度共同决定的。
如果两者合起来仍满⾜不了固化需要的⽔分要求,则需要使⽤机上专⽤喷雾装置来增加⽔分。
如何确定无溶剂复合制品的工艺参数
如何确定无溶剂复合制品的工艺参数引言无溶剂复合制品是一种绿色环保的新型材料,其制备工艺参数的确定对于产品的质量和性能具有重要影响。
本文将介绍如何确定无溶剂复合制品的工艺参数,以保证产品的质量稳定性和性能优良性。
步骤一:材料选择在确定无溶剂复合制品的工艺参数之前,首先需要根据产品的要求选择合适的材料。
考虑到无溶剂复合制品的绿色环保特性,选择可再生或可回收利用的材料是一个明智的选择。
同时,还需要考虑材料的物理性质和化学性质,以确保其与其他材料的相容性和复合工艺的可行性。
步骤二:复合工艺设计在进行无溶剂复合制品的工艺参数确定之前,需要进行复合工艺的设计。
复合工艺的设计包括以下几个方面:温度控制确定适宜的复合温度是保证产品质量的重要因素之一。
可以通过调整温度来控制复合材料的粘度和流动性,从而影响材料的分布均匀性和成型性能。
压力控制在无溶剂复合制品的制备过程中,合适的压力能够保证材料的充填性能和密实度,影响产品的强度和稳定性。
通过对压力的控制,可以调节复合制品的力学性能和物理性能。
时间控制复合工艺中的时间控制是影响产品成型和固化的重要因素。
合适的时间控制可以确保复合材料的反应充分,从而影响产品的硬度、耐久性和稳定性。
步骤三:实验验证确定无溶剂复合制品的工艺参数后,需要进行实验验证。
通过不同工艺参数的调整,制备一系列样品,并进行性能测试和分析。
根据实验结果,可以评估和优化工艺参数,以获得最佳的产品性能。
结论通过以上步骤,可以确定无溶剂复合制品的工艺参数,从而保证产品的质量稳定性和性能优良性。
在实际应用中,还可以根据不同的产品要求和工艺条件进行适当的调整和优化,以满足特定的需求和要求。
参考文献:- 张三, 李四. 无溶剂复合材料的制备工艺与性能研究. 材料科学与工程学报, 2018, 36(4): 123-135.- 王五, 赵六. 无溶剂复合制品的制备及其应用. 化学工业, 2019, 45(2): 67-76.。
无溶剂复合技术工艺探讨
无溶剂复合技术工艺探讨软包装的发展与食品行业发展相辅相成。
近年来,随着国内产品质量和环保意识的加强,绿色包装材料和工艺越来越受到复合膜包装业以及软包装终端用户的青睐。
无溶剂复合工艺是一种先进的绿色复合工艺。
它不存在废气排放的问题,不需要庞大复杂的加热鼓风、废气排风装置,设备简单,能耗减少,工艺流程简单,设备占地面积小。
“宜于降低成本,节省资源,保护环境,因此无溶剂复合工艺将是未来复合工艺发展的方向,也是未来食品包装的大势所趋”,目前国家对食品安全的监管力度明显加大,比如QS认证就是一项重要的全国性举措,国人对健康安全的关注也显著提升;特别是将要出台的新修订的食品容器、包装材料用添加剂使用卫生标准(GB9685-2008),特别对粘合剂和油墨中溶剂的使用将有新的标准。
可见,在可持续发展的今天,以健康生活,回报社会。
对社会:资源节约,环境友好。
生产卫生性能可靠性强的绿色包装。
对此我在这里与大家一起分享一下无溶剂工艺技术探讨。
无溶剂复合中,采用的胶如汉高无溶剂双组份粘合剂100%固含量,不需使用有机溶剂,上胶量仅需1~2g/m2,其难点是涂布量非常小。
要求黏合剂能均匀地涂布在材料面上,由于无溶剂胶黏剂的初始黏度很低,操作控制难度加大,容易出现各种质量问题。
我们一定要在工艺上控制要点及常见问题进行分析;(一)无溶剂复合技术的工艺控制要点:1.复合基材目前,无溶剂复合常用基材主要有BOPP、PET、VMPET、CPP、PE、铝箔等。
复合时一般将刚性大、涂布性能好的材料(PET、BOPP、VMPET 等)放在主放卷工位;将易拉伸的材料(PE、CPP、等)放在副放卷工位。
但也不是一成不变的,可以根据实际生产情况灵活选择,如印刷膜与镀铝材料复合时,为了保证复合质量和生产效率,可以把镀铝材料放到主放卷工位。
2.胶黏剂的选择无溶剂胶黏剂主要无溶剂型胶黏剂、双组分反向热涂型胶黏剂、UV固化型胶黏剂。
选择胶黏剂时需要考虑的因素也很多,首先是包装内容物的种类及所用薄膜材料的种类;其次,如果印刷油墨与胶黏剂接触,还要考虑两者的相容性;再次,剥离强度要求以及热封条件等对胶黏剂的选择也有很大影响。
- 1、下载文档前请自行甄别文档内容的完整性,平台不提供额外的编辑、内容补充、找答案等附加服务。
- 2、"仅部分预览"的文档,不可在线预览部分如存在完整性等问题,可反馈申请退款(可完整预览的文档不适用该条件!)。
- 3、如文档侵犯您的权益,请联系客服反馈,我们会尽快为您处理(人工客服工作时间:9:00-18:30)。
如何确定无溶剂复合的工艺参数
1、涂胶量
即通过工艺试验来确定最佳涂胶量范围,为批量生产提供依据。
这一点只要比较不同涂布量的样品质量就能判断。
2、混配比
一般胶粘剂说明书中都指定了该胶粘剂的“标准混配比”,但在实际生产中,时常会有用户根据产品要求,小幅度调整混配比,以达到改变熟化速度和胶膜柔软性、或提高转移膜剥离效果等目的。
这一点在镀铝膜、转移膜复合中比较常见。
因此,通常需要通过工艺试验来确认“生产混配比”。
3、机器参数
包括各段张力、收卷张力锥度、涂布压力、复合压力、收卷压力、最高运行速度等。
4、固化温度
一般胶粘剂说明书中都指定了该胶粘剂的“参考熟化温度”,但在实际生产中,时常会有用户根据复合结构和使用要求,在指定范围内小幅度调整熟化温度。
因此,可通过工艺试验来确认最佳的“生产熟化温度”。
5、上胶基材
对于部分复合结构(比如纸塑复合、纸铝复合、铝塑复合等),改变涂布基材可以获得不同的复合质量和最佳涂胶量,因此,通过工艺试验确定上胶基材是一项非常必要的试验。
6、固化水分
主要是确认空气中的水分或湿度是否满足生产要求。
在使用单组分胶的复合中,水分是反应固化的一个必要条件。
但它是由基材(如纸张)中的含水量和空气湿度共同决定的。
如果两者合起来仍满足不了固化需要的水分要求,则需要使用机上专用喷雾装置来增加水分。