生产过程和产品风险评估
生产过程中的风险评估与管理

生产过程中的风险评估与管理在现代企业中,生产过程是实现产品交付的核心环节。
然而,生产过程中存在着各种潜在的风险,可能会对企业的生产效率、质量和安全造成严重影响。
因此,对生产过程中的风险进行评估与管理是一个至关重要的工作。
本文将探讨生产过程中的风险评估与管理的重要性,并提供一些有效的管理措施。
1. 风险评估的重要性生产过程中的风险评估是指对可能发生的风险进行全面的、系统的分析和评估。
它有助于企业了解潜在的风险来源,预测可能产生的影响,并制定相应的风险管理策略。
风险评估的重要性体现在以下几个方面:1.1 预防事故发生:通过对生产过程中的风险进行评估,企业可以提前识别潜在的事故隐患,并采取相应的预防措施,从而减少事故的发生概率。
1.2 保障生产质量:生产过程中的风险可能会导致产品质量下降或变得不可接受。
通过评估风险,企业可以及时发现并解决可能影响产品质量的问题,确保产品符合客户要求。
1.3 降低生产成本:风险评估有助于发现生产过程中的低效环节,帮助企业优化生产流程,提高生产效率,从而降低生产成本。
2. 生产过程中的常见风险生产过程中存在着多种潜在的风险,以下是一些常见的风险类型:2.1 设备故障:设备故障可能导致生产中断、生产效率下降或产品质量问题。
因此,对设备进行定期检修和维护是降低设备故障风险的重要措施。
2.2 人为失误:人为失误是生产过程中常见的风险源。
企业应加强员工培训,提高员工的操作技能和安全意识,减少人为失误对生产过程的影响。
2.3 原材料供应问题:原材料供应的延迟、不合格或断供可能会导致生产计划延误或产品质量问题。
企业应与供应商建立良好的合作关系,并制定备用供应计划,以应对潜在的供应问题。
3. 生产过程中的风险管理措施为了降低生产过程中的风险,企业可以采取以下管理措施:3.1 建立风险管理体系:企业应建立完善的风险管理体系,包括明确的责任分工、流程和制度,确保风险管理工作的有效开展。
3.2 定期进行风险评估:企业应定期对生产过程中的风险进行评估,及时发现和解决潜在的问题,并根据评估结果进行相应的调整和改进。
生产安全风险如何评估

生产安全风险如何评估
生产安全风险评估是通过对生产环境、操作过程、设备设施和人员行为等因素进行综合分析和评估,以确定潜在的风险和可能导致事故的因素。
常见的生产安全风险评估方法包括以下几个步骤:
1. 确定评估目标:明确评估的范围和目标,例如评估某一特定作业的安全风险,或者评估整个生产过程的安全风险。
2. 收集必要信息:收集与生产过程相关的信息,包括设备设施情况、操作流程、材料使用、工作人员资质等。
3. 识别潜在风险因素:通过观察和检查,识别潜在的安全风险因素,例如设备故障、操作疏忽、材料泄漏等,还可以借鉴类似的案例和经验。
4. 评估风险的可能性:根据实际情况和经验判断,评估各个风险因素发生事故的可能性,可以采用风险矩阵或者专业软件进行定量评估。
5. 评估风险的严重程度:评估风险事件发生时可能导致的后果和损失,包括人员伤亡、财产损失、环境影响等。
6. 确定风险等级和优先级:将风险按照可能性和严重程度进行综合评估,确定风险的等级和优先级。
7. 制定风险控制措施:根据评估结果,针对高等级和优先级的
风险,制定相应的风险控制措施,包括技术措施、管理措施和人员培训等。
8. 实施和监控措施:将制定的风险控制措施落实到实际生产中,并进行监控和检查,确保措施的有效性和持续改进。
需要注意的是,生产安全风险评估是一个持续的过程,随着生产环境和操作过程的变化,评估和控制措施也需要进行相应的调整和优化。
GMP 产品生产过程潜在风险评估及控制记录表

1
1 按作业指导书 员工参照首板及从操作
7.车缝污迹 8.产品有虫子或血迹
、中衣、外衣、帽子、床上用品)甲醛含量不得超过20mg/kg。
b.接触皮肤的服装(文胸、腹带、针织内衣、衬衫、裤子、裙子、
睡衣、袜子、床单、被罩)甲醛含量不得超过75mg/kg。
IQC
3
1
3 按作业指导书
c.不接触皮肤的服装(毛衫、外衣、裙子、裤子)和室内装饰类(桌 布、窗帘、沙发罩、床罩、墙布)甲醛含量不得超过300mg/kg。
1
5 按作业指导书 培训员工
1.利器专人专管,做好每天收发做好收发记录。
1
5 按作业指导书 2.使用者每天将利器绑于工作台上。
3.针专人专管,严格做到一换一的政策,做好利器记录
1.定期对机台进行清洁
1
5 按作业指导书 2.专人负责检查机台、中转筐清洁程度
3.加强员工培训
1
1 按作业指导书 首件OK方可生产
影响产品品质 后序生产困难
1.储存不当 2.卫生不良
5
员工操作错误
1
6.套位不准
不符合标准客户拒收
员工操作错误
1
1
5 按作业指导书 加强员工培训
1
5 按作业指导书 加强员工培训
1
3 按作业指导书 加强员工培训
1
4 按作业指导书
1.加强员工培训 2.仓库加强检查力度
1
4 按作业指导书
1.加强员工培训 2.仓库加强检查力度
使用玻璃或易脆塑料易碎或破裂
பைடு நூலகம்造成人身安全,破碎物混入成衣
员工操作问题
5
品质部门意识不足,跟进不到位 5
意识不足
共线生产风险评估报告
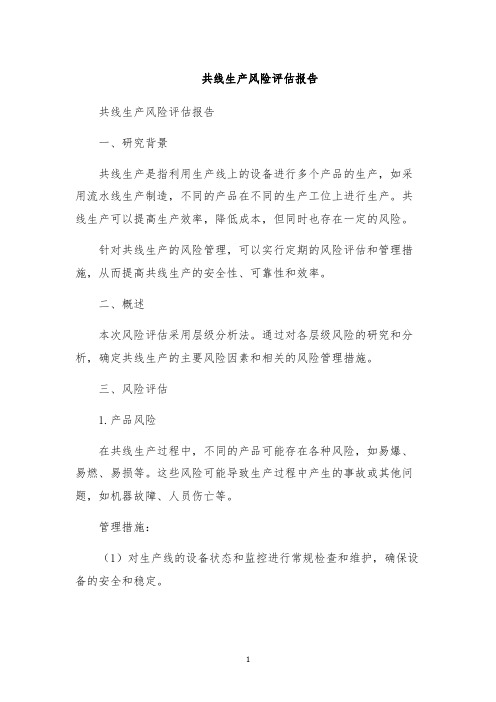
共线生产风险评估报告共线生产风险评估报告一、研究背景共线生产是指利用生产线上的设备进行多个产品的生产,如采用流水线生产制造,不同的产品在不同的生产工位上进行生产。
共线生产可以提高生产效率,降低成本,但同时也存在一定的风险。
针对共线生产的风险管理,可以实行定期的风险评估和管理措施,从而提高共线生产的安全性、可靠性和效率。
二、概述本次风险评估采用层级分析法。
通过对各层级风险的研究和分析,确定共线生产的主要风险因素和相关的风险管理措施。
三、风险评估1.产品风险在共线生产过程中,不同的产品可能存在各种风险,如易爆、易燃、易损等。
这些风险可能导致生产过程中产生的事故或其他问题,如机器故障、人员伤亡等。
管理措施:(1)对生产线的设备状态和监控进行常规检查和维护,确保设备的安全和稳定。
(2)对生产过程中的每个工位进行合理的规划和安排,避免不同产品之间的混淆和误用。
(3)对易燃易爆的物质,应严格遵守防火防爆的规定和操作流程,如禁止吸烟、明火等。
2.技术风险共线生产的生产线上通常会有不同类型的设备和工具,这些设备和工具可能存在使用问题或技术问题,如故障、损坏等。
管理措施:(1)确保设备和工具的正常、安全使用,如及时更换工具配件、检查设备磨损情况等。
(2)加强员工培训和技术培训,提高员工对设备和工具的操作技能和安全意识。
(3)定期进行设备和工具的维护和检查,发现和解决潜在的问题。
3.人员风险共线生产需要多个工人共同协作完成,不同的工人可能存在人员风险,如技能水平不足、误操作等。
管理措施:(1)确保员工的技能和操作水平符合要求,如定期进行培训和考核。
(2)加强员工的安全教育和培养责任心,提高员工的安全意识和责任感。
(3)对安全生产责任人进行培训,必要时可以配置安全保障人员。
4.质量风险共线生产过程中可能出现质量问题,如缺陷产品、次品等。
管理措施:(1)确保生产过程的质量控制和管理,如定期检查和测试产品质量等。
(2)对生产过程和工艺进行优化升级,提高产品质量和生产效率。
生产过程和产品风险评估

生产过程和产品风险评估导言:在现代工业社会中,生产过程和产品的安全性是一项至关重要的工作。
一个安全的生产过程和产品不仅能够保障工人和消费者的生命财产安全,也能够提高企业的竞争力和声誉。
因此,对生产过程和产品进行风险评估,是企业必不可少的工作之一一、生产过程风险评估生产过程中,存在着各种各样的潜在风险,如火灾、爆炸、电击、机械伤害等。
为了减少这些风险,企业需要进行生产过程的风险评估,并采取相应的措施进行防范。
首先,企业需要对生产过程进行全面的排查,发现潜在风险点。
这可以通过工作人员的实地观察、安全监测设备的使用等方式进行。
通过这种方法,企业可以发现诸如高温、高压、易燃、易爆等风险点,以及可能引发事故的设备故障等。
其次,企业需要对发现的潜在风险进行具体的评估和分析。
这可以通过专业的技术手段和方法进行,如风险矩阵评估法、风险树分析法等。
通过这种方法,企业可以确定潜在风险的严重程度、可能性和影响范围,为后续的风险应对提供依据。
最后,企业需要采取相应的措施进行风险防范。
这可以包括安装安全设备、进行工艺改进、完善作业指导书等。
通过这些措施,企业可以减少潜在风险的发生概率,并降低其对生产过程的影响程度。
产品的安全性对消费者来说至关重要。
为了保障产品的安全性,企业需要对产品进行风险评估,并采取相应的措施进行防范。
首先,企业需要对产品进行全面的检测和测试。
这可以包括原材料的检验、零部件的质量检查,以及最终产品的性能测试等。
通过这些检测和测试,企业可以发现产品中的潜在安全问题,并进行相应的改进。
其次,企业需要对产品进行使用场景和风险分析。
这可以通过用户反馈、历史事故案例和市场调研等方式进行。
通过这种分析,企业可以确定产品的使用场景和潜在风险,为产品安全设计和警示标识提供依据。
最后,企业需要采取相应的措施进行风险防范。
这可以包括改进产品设计、加强产品制造过程的质量控制,以及提供详细的产品使用说明和警示标识等。
通过这些措施,企业可以减少产品安全事故的发生,并提高产品的安全性。
食品安全食品生产过程风险评估
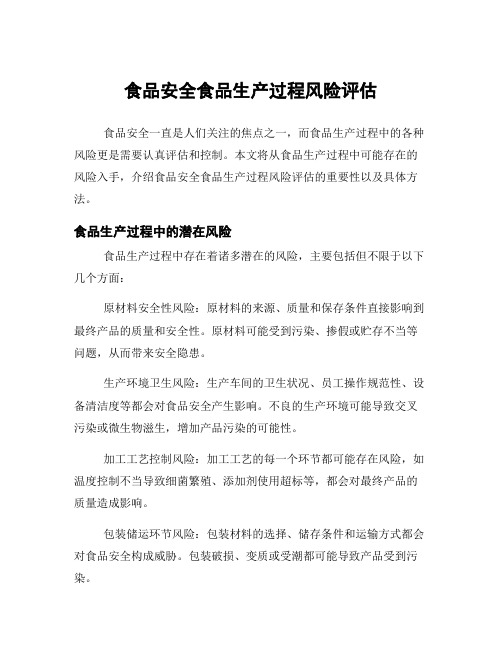
食品安全食品生产过程风险评估食品安全一直是人们关注的焦点之一,而食品生产过程中的各种风险更是需要认真评估和控制。
本文将从食品生产过程中可能存在的风险入手,介绍食品安全食品生产过程风险评估的重要性以及具体方法。
食品生产过程中的潜在风险食品生产过程中存在着诸多潜在的风险,主要包括但不限于以下几个方面:原材料安全性风险:原材料的来源、质量和保存条件直接影响到最终产品的质量和安全性。
原材料可能受到污染、掺假或贮存不当等问题,从而带来安全隐患。
生产环境卫生风险:生产车间的卫生状况、员工操作规范性、设备清洁度等都会对食品安全产生影响。
不良的生产环境可能导致交叉污染或微生物滋生,增加产品污染的可能性。
加工工艺控制风险:加工工艺的每一个环节都可能存在风险,如温度控制不当导致细菌繁殖、添加剂使用超标等,都会对最终产品的质量造成影响。
包装储运环节风险:包装材料的选择、储存条件和运输方式都会对食品安全构成威胁。
包装破损、变质或受潮都可能导致产品受到污染。
食品安全食品生产过程风险评估的重要性针对上述潜在风险,进行科学合理的食品安全食品生产过程风险评估显得尤为重要。
其重要性主要体现在以下几个方面:保障消费者健康:通过对食品生产过程中各环节的风险进行评估,可以有效地避免因为原材料、加工工艺等环节问题导致的产品质量下降或安全隐患,从而保障消费者的健康。
提升企业竞争力:建立科学完善的食品安全管理体系,对生产过程中的各种潜在风险进行评估和控制,有助于提升企业产品质量和信誉,增强市场竞争力。
符合法律法规:各国家和地区都有相关的法律法规对食品安全进行规范,进行食品安全食品生产过程风险评估可以帮助企业更好地遵守相关法规,避免因违规操作而受到处罚。
食品安全食品生产过程风险评估方法进行食品安全食品生产过程风险评估需要综合考虑原材料、加工工艺、人员操作、设备清洁等多个方面因素。
常用的方法包括但不限于以下几种:危害分析关键控制点(HACCP):HACCP是一种系统性的预防性方法,通过识别可能存在于食品生产过程中的危害,并确定关键控制点来预防、消除或减少这些危害。
生产过程中的风险评估与管理

生产过程中的风险评估与管理在当下追求高效、高质量生产的时代背景下,企业面临越来越多的风险与挑战。
为了保障生产过程顺利进行,降低风险造成的不利影响,风险评估与管理变得尤为重要。
本文将探讨生产过程中的风险评估与管理,并提出一些有效的方法和措施。
一、风险评估的重要性在生产过程中,风险是无法避免的。
无论是内部的人员操作失误,还是外部的自然灾害等不可预见因素,都可能对生产造成影响。
因此,风险评估变得至关重要。
通过风险评估,企业可以在生产过程中及时识别潜在的风险因素,以便采取相应的管理措施。
此外,风险评估还可以帮助企业制定合理的预算和资源分配,确保生产效率的提高。
二、风险评估与管理的方法1. 采用专业的风险评估工具为了提高风险评估的准确性和全面性,企业可以借助专业的风险评估工具。
这些工具可以帮助企业对各种风险因素进行分类和评估,包括生产设备故障、工艺不稳定性、人员行为等。
通过定量和定性的评估,企业能够更好地了解风险的程度和来源,从而采取相应的管理措施。
2. 引入风险管理团队为了更好地管理风险,企业可以成立专门的风险管理团队。
这个团队由不同部门的专业人员组成,他们可以共同研究和评估不同风险因素,并提出有效的控制措施。
通过团队的合作,企业能够更好地协调各个环节之间的工作,做到风险防范和及时应对。
3. 有效监控和信息共享及时监控和信息共享是风险评估与管理的重要环节。
企业可以借助先进的监控设备和系统,对生产过程进行实时监测和数据采集。
这些数据可以帮助企业快速发现潜在的风险,并采取相应的预防措施。
此外,企业还可以与供应商、客户等业务伙伴共享信息,共同防范风险。
三、风险管理的关键措施1. 建立风险清单企业可以建立一份详细的风险清单,列出各个环节可能存在的风险因素和可能造成的影响。
通过对风险的梳理和分析,企业能够更好地了解风险的来源和特点,从而有针对性地制定管理计划。
2. 制定应急预案在生产过程中,意外情况时有发生。
为了应对这些情况,企业应制定相应的应急预案。
产品及制程风险评估表

璃制品
1、玻璃及塑料 等工具器的
破损混入;
2、机器零部件 及设施配件 等的异物故 障破损混入
1、玻璃、塑料等制 品严格登记;
2、玻璃器具进行附
膜防护;
3、品管针对性检查
4、机修人员针对性 检查;
每日品管
班前检查
品管负责
人
低风险
潜在的污染区域:
1、车间有机树脂的门窗,辅料库的玻璃窗;
3、照明的玻璃灯具;
物
理
金属异物
一、原辅料料 初加工等带入
二、加工器具
及设备零部件
金属等损坏混 入;
1、对利器等每日专人检查发放,同
时保持记录;
2、加工场所有设备的易脱落零部件登记;
3、由专人对每日零部件按班前、班
后、生产中每两小时时行检测查Байду номын сангаас并记录;
4、负责人培训上岗;5.过程严控;
利器每日检查;
管理者
低风险
物
理
硬质塑
4、玻璃的温湿度计;
5、化工品的包装桶;
6、产品用塑料筐;
7、原料塑料叉板等
清洗与更换
1、严格按清洁计划进行工器具清洁;
2、玻璃器具的破损在品管监控下由机修人 员更换
怡富包装(深圳)有限公司产品风险评估分析表-加工过程的风险1
危害识别
危害描述
风险控制手段
控制频次/时间
责任者
风险的描述
备注
人为蓄意破坏
抱怨等对公司 心怀不满的员 工
员工教育
日常
生产部
低风险
入口门警监视
随时
门卫
关键区域的上锁
等的管理
随时
生产及品管
- 1、下载文档前请自行甄别文档内容的完整性,平台不提供额外的编辑、内容补充、找答案等附加服务。
- 2、"仅部分预览"的文档,不可在线预览部分如存在完整性等问题,可反馈申请退款(可完整预览的文档不适用该条件!)。
- 3、如文档侵犯您的权益,请联系客服反馈,我们会尽快为您处理(人工客服工作时间:9:00-18:30)。
1.0目的
为了发现和评估产品在开发过程中和产品生产过程中潜在的失效及其後果,找到能够避免或者减少这些潜在失效发生的措施。
2.0 范围
适用於本厂生产的各工序生产过程(包括工艺、设备、环境等) 和各类型产品的风险评估。
3.0 定义
3.1 DFMEA (Design Failure Mode and Effects Analysis,设计开发中失效模式与後果分析)。
设计FMEA 不是靠程式控制来克服设计中潜在的缺陷,即在体现设计意图的同时,还应保证制造或装配能够实现设计意图,即要考虑制造/装配过程中技术的/能力的限制。
3.2 PFMEA (Process Failure Mode and Effects Analysis,过程中失效模式与後果分析)。
3.2.1 在产品制造过程(包括工艺、设备、环境等),对构成产品的各子系统、零部件,
成品、过程、服务的各个工序逐一进行分析,找到潜在的失效模式,评估其可
能的後果、风险,找到能避免或减少这些潜在失效发生的措施,预先采取措施
防止发生。
3.2.2 失效分析在於找出零元件或系统的潜在失效极其後果,并为此而采取的可行之
对策。
3.3 潜在风险(Potential Hazard):按照法律法规要求,客人安全规格,在玩具设计里
固定含有的特徵或部件(如小物件,尖点,利边,小球,磁石,长绳,突出物、
等)必须要避免发生。
不能满足PRD (Product requirement document)所定义、客人
要求等的风险。
3.4 RPN (Risk Priority Number,风险序数):测量失效模式的风险程度。
3.5 失效的类别
物理性失效——任何潜在损害产品机械物理性能的危害;
化学性失效——重金属,Phthalate对产生的危害;
生物性失效——能够产生致病菌且能够引发消费者发生疾病的微生物危害。
4.0 风险评估的流程
4.1 D FMEA流程图。
范围:
1.客人指定要做FMEA的产品。
2.三岁以下的玩具产品。
3.复杂的产品(由工程部及品质部共同决定)。
发中存在的潜在失效模式进行分析及改正。
4.2 PFMEA流程图。
应该有品管部,IE,工程师,生产参与,也可以包含采购,维修及供应商等相关人员参与。
4.4 列出各环节潜在的失效模式和潜在的失效後果。
4.4.1 确定潜在失效模式:是对具体环节不符合要求的具体描述。
它可能引起下一
环节的潜在失效模式,也可能是上一道环节的潜在失效的後果。
4.4.2 分析潜在的失效後果:对顾客(内部和外部) 的影响,用顾客的经历来描述失
效的後果,如噪声,外观不良,无法固定,配合不良反应等。
4.5 确定严重度,频度,探测度。
4.5.1 严重度和分级
严重度是潜在失效模式对顾客的影响後果的严重程度的评价指标。
严重度仅适用於失效的後果。
采用1~10分制来进行评估。
数字越大,代表後果的严重程度越高。
评估时,应只考虑其最坏的後果。
4.5.2 频度和分级。
频度是指具体的失效原因导致失效模式的频率。
频率的分级数着重在其含义而不是数值。
应该运用一致的频度分级规则,以保证连续性。
“可能的失效率”是根据过程实施中预计发生的失效来确定的。
当确定频度级别时,应该考虑多方面的资讯,包括拒收记录舆能力研究。
采用1~10分制来进行评估,10分代表发生该失效或者该失效的原因非常高,且不可避免,1分代表几乎不可能发生。
4.5.3 探测度和分级。
探测度是评估在目前的控制条件下,发现失效或者失效原因的能力,以避免次品流到客户手中。
通常采用1~10分制来进行评估。
数字越大,代表越难发现。
在确定探测度之前,应列出目前的预防措施和检测方法。
现行控制措施:防错夹具,SPC 统计工具,过程评价
A. 阻止失效起因/机理或失效模式/後果发生, 或减少其发生率
B. 查明起因/机理并找到纠正措施
C. 查明失效模式
4.6 风险序数(RPN)
4.6.1 风险序数=严重度X频度X探测度
4.6.2 风险序数越大,代表风险越高。
4.6.3当完成PFMEA时,必须确保所有项目的RPN序数小於或者等於100。
4.6.4如果风险序数RPN值超过100,工艺人员必须采取纠正措施,努力减少该RPN
值。
4.7 改善行动
4.7.1 对於不符合要求的项目必须作出改善行动,并且确定改善方案的负责人以及改善
的完成日期。
4.7.2 对於已经符合要求的项目,我们也应该尽量采取一些行动,以降低RPN值。
4.8 确认改善行动,并重新计算RPN值。
4.8.1 确认改善行动的可行性和有效性。
4.8.2 重新计算RPN值,确认是否达到要求。
4.9 发现下面情况时需更新DFMEA/PFMEA记录
4.9.1 工艺/工序被改善後。
4.9.2 新的失效模式被确认後。
4.9.3 某些失效後果取得新的数据。
4.9.4 根本原因被确定後。
5.0 记录表格
5.1 <<过程风险评估报告>>
5.2 <<产品风险评估报告>>。