粘胶纱线产生细节的原因分析与控制
纺纱过程中出现的问题及解决措施

纺纱过程中出现的问题及解决措施纺纱疵点及解决措施1. 纱线不匀原因:原料品质不佳、梳理不充分、牵伸不均匀、锭子质量差解决措施:采用优质原料、加强梳理、优化牵伸工艺、更换或维修锭子2. 毛羽原因:原料纤维过短、梳理不足、牵伸过度、加捻不当解决措施:选用较长纤维原料、加强梳理、调整牵伸工艺、优化加捻参数3. 太紧原因:牵伸过大、加捻过多、锭子调整不当解决措施:减少牵伸倍数、降低加捻强度、调整锭子4. 太松原因:牵伸不足、加捻过少、锭子调整不当解决措施:增加牵伸倍数、提高加捻强度、调整锭子5. 粗细不均原因:原料纤维粗细不均、牵伸不均匀、加捻不均匀解决措施:选用均匀原料、优化牵伸工艺、调整加捻参数6. 结头原因:原料中有杂质、梳理不充分、牵伸不均匀、加捻过大解决措施:去除原料中的杂质、加强梳理、优化牵伸工艺、降低加捻强度7. 条痕原因:原料染色不均匀、混纺原料不匹配、牵伸不均匀、加捻不均匀解决措施:均匀染色原料、选择匹配的混纺原料、优化牵伸工艺、调整加捻参数8. 花疵原因:原料中有杂色纤维、梳理不充分、牵伸不均匀、加捻不均匀解决措施:去除原料中的杂色纤维、加强梳理、优化牵伸工艺、调整加捻参数9. 脆硬原因:原料纤维成熟度差、梳理不足、加捻过度解决措施:选用成熟度高的原料纤维、加强梳理、降低加捻强度10. 棉结原因:原料中有棉结、梳理不充分、牵伸不均匀、加捻过大解决措施:去除原料中的棉结、加强梳理、优化牵伸工艺、降低加捻强度11. 裂口原因:原料纤维强度低、梳理过度、牵伸过大、加捻过大解决措施:选用强度高的原料纤维、加强梳理、优化牵伸工艺、降低加捻强度12. 僵硬原因:原料纤维弹性差、梳理不足、牵伸过大、加捻过度解决措施:选用弹性好的原料纤维、加强梳理、优化牵伸工艺、降低加捻强度13. 刺毛原因:原料纤维中含有短纤维、梳理不足、牵伸不均匀、加捻过度解决措施:去除原料中的短纤维、加强梳理、优化牵伸工艺、降低加捻强度14. 络筒时断头原因:原料强度低、梳理不足、牵伸不均匀、加捻不足、络筒张力过大解决措施:选用强度高的原料纤维、加强梳理、优化牵伸工艺、调整加捻参数、降低络筒张力。
成纱8cm、9cm、10cm连续机械波的成因与控制措施探讨

成纱8cm、9cm、10cm连续机械波的成因与控制措施探讨
成纱8cm、9cm、10cm连续机械波的成因与控制措施探讨
成纱8cm、9cm、10cm连续机械波是众多纱线产品中常见的一种产品,
这种产品的出现会带来一定的困扰,主要是因为它们的波动较大,有
时会影响产品的质量。
那么,成纱8cm、9cm、10cm连续机械波的成因
与控制措施是什么呢?
首先,成纱8cm、9cm、10cm连续机械波的成因主要是由于纱线材料本
身的质量问题,尤其是纱线的纤维强度差异。
纱线纤维强度差异会使
得纱线材料在成纱过程中出现变形,从而产生不同的机械波。
其次,成纱机的把纱控制不当也是成纱8cm、9cm、10cm连续机械波的
一个重要原因。
如果成纱机的把纱控制不当,会导致经纱不均匀,产
生变形,从而产生机械波。
最后,还有一些成纱8cm、9cm、10cm连续机械波的控制措施可以采用。
首先,要提高纱线材料的质量,尤其是纱线的纤维强度,以维持纱线
材料的一致性。
其次,在成纱过程中,要对把纱进行有效的控制,确
保经纱均匀,避免出现变形。
通过上述讨论,我们可以看出,成纱8cm、9cm、10cm连续机械波的成
因主要是由于纱线材料本身的质量问题,以及成纱机的把纱控制不当,而控制措施主要是提高纱线材料的质量,以及对把纱进行有效的控制。
只有通过这些措施,我们才能有效的控制成纱8cm、9cm、10cm连续机
械波,从而提高产品的质量。
技术涤粘混纺色纺纱质量控制措施

技术涤粘混纺色纺纱质量控制措施涤粘混纺色纺纱面料是“百万米无色差”的环保面料,受到设计师及广大消费者的青睐。
由于色纺纱是通过多道工序生产而成,即不可避免的会产生这样或那样的质量问题,通过多年的色纺纱生产,结合下游客户的主要投诉作一点探索:一、颜色控制1.1配色与调色配色和调色是色纺纱生产的核心技术。
配色:通常是指选取一些有色纤维,初定一定比例,做成小样,达到与目标标样基本相似的过程。
调色:通常是指根据做出来的样品与标样之间的颜色差距,进行调整各色纤维之间的比例再进行试样,使之进一步接近标样颜色的过程。
配色一般很难一次成功,需要多次反复试验才能达到与用户提供的标准色样颜色一致。
配色完成后对色打样,待用户确认后投产。
批量上机后第一时间应再次取样对色,以防止批量与小样颜色差异,便于及时采取补救措施。
对色需要在合适的光源下进行,一般采用自然北光或标准灯箱内的 D65 光源。
由于光线对颜色的影响较大,应提前与用户约定统一光源,便于准确对色。
1.2色偏色偏是指大货成品布颜色与客户确认LAB-DIP或客户原始标样之间的差异,俗称级差,一般以灰卡4级为合格作为评判标准。
涤粘混纺色纺纱采取高温190°三分钟,模拟后道整理温度和时间,整理后进行对色调色,达到与标样无限近似。
颜色作为色纺纱的关键指标,是客户最易提出异议反馈项,结合工作实际,我们要做到以下几点预控措施:1.2.1 确定对色标准1.2.1.1无对色要求说明或要求对色卡(需反馈确定色卡版本号):⑴针织用纱对色在原坯色卡与水洗色卡之间,接近原坯色卡;⑵毛织用纱对色在原坯色卡与水洗色卡中间,并制毛片水洗后参考;⑶若最新版色卡没有该色号,则要求相关部门提供客户要对的色卡版号。
1.2.1.2 要求对客批样(即客人所确认的A板或B板):⑴第一批,对色在客批样与客户来样之间,接近客批样;⑵第一批以后,对色在客批样与第一批之间,接近客批样。
1.2.1.2 要求跟X批:⑴对色在X批与原坯色卡或客批样之间,接近X 批;⑵若难做到X批与原坯色卡之间,可对色在X批与水洗色卡之间,接近X批。
《细纱工序产生细节的因素分析和改进措施》

《细纱工序产生细节的因素分析和改进措施》细纱工序产生的中短片段细节对后道工序的生产会造成不利的影响,使织造工序断头增加,给生产效率的提高带来困难,同时使布面质量和风格受到影响。
所以最大程度地减少细节就尤为重要。
1细节的产生机理1.1纤维在牵伸过程中,由于受到各因素的影响,纤维不在同一界面上变速而产生移距偏差。
如在牵伸区内,须条的某一截面上有较多的纤维提前变速,便会产生粗节,在粗节的后面就是细节;反之,若有较多的纤维变速较晚,便会产生细节,在细节的后面就是粗节。
当纤维的变速位置越分散,则移距偏差值越大,粗细节越多。
1.2在粗纱进入牵伸区后,纤维所受到的力是多方面的,理想的状态是这些作用力始终不发生变化,设备状态保持如一,使每根纤维的变速点趋于一致,而实际情况是或多或少都存在差异,控制和减少这种差异就是我们要努力的目标和方向。
2产生细节的因素2.1前牵伸区,纤维在此区域运动最为激烈,罗拉和胶辊的状态直接影响纤维的运动。
罗拉弯曲、晃动、齿型不良以及前胶辊铁壳游隙过大、胶辊表面有凹槽、不光滑,摇架压力或大或小等因素都会造成对纤维的控制力不断的发生变化,易产生8cm机械波;胶辊表面粗糙,纤维易粘附在胶辊表面,造成纤维散失,产生细节。
2.2中区牵伸,如该部位对纤维控制不当,使纤维在上下皮圈间的运动不规则,发生位移。
如浮游区过大、上下皮圈龟裂、上下肖变形、表面不光滑、中铁壳表面生锈、皮圈内积花、皮圈跑偏、下皮圈张力架弹簧失效等,这些会造成皮圈的回转速度不匀,产生皮圈顿挫,使从后罗拉钳口输送过来的纱条不能被有效拉伸,而发生扭曲;上肖变形极易造成上皮圈起拱,使纤维在上下皮圈之间失去控制而产生30-40cm机械波;浮游区过大会增加浮游纤维的数量,使纤维的变速位置紊乱而产生细节。
2.3横动装置不良(小于5mm)或者整个装置失灵、无左右移动,使纤维在同一点上连续牵伸、摩擦,没有恢复弹性的时间,均会造成胶辊、胶圈出现凹槽,影响纤维在牵伸过程中的运动。
第七章 粘胶纤维的质量控制
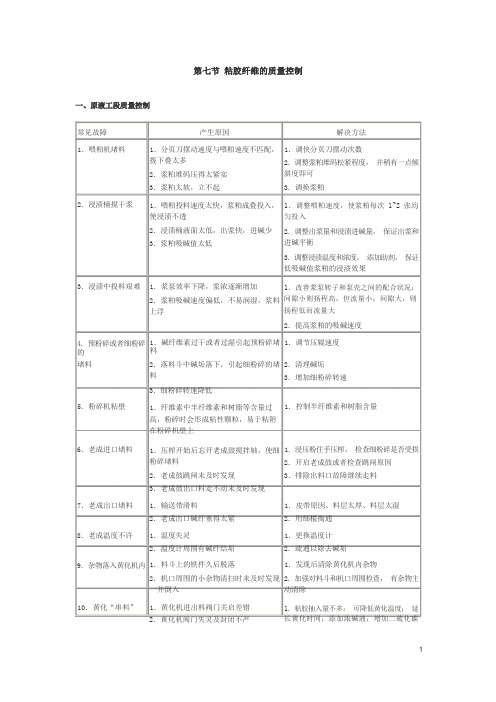
常见故障产生原因解决方法1.喂粕机堵料1.分页刀摆动速度与喂粕速度不匹配,拨下叠太多2.浆粕堆码压得太紧实3.浆粕太软,立不起1.调快分页刀摆动次数2.调整浆粕堆码松紧程度,并稍有一点倾斜度即可3.调换浆粕2.浸渍桶搅干浆1.喂粕投料速度太快,浆粕成叠投入,使浸渍不透2.浸渍桶液面太低,出浆快,进碱少3.浆粕吸碱值太低1.调整喂粕速度,使浆粕每次 1~2 张均匀投入2.调整出浆量和浸渍进碱量,保证出浆和进碱平衡3.调整浸渍温度和浓度,添加助剂,保证低吸碱值浆粕的浸渍效果3.浸渍中投料艰难1.浆泵效率下降,浆浓逐渐增加2.浆粕吸碱速度偏低,不易润湿,浆料上浮1.改善浆泵转子和泵壳之间的配合状况:间隙小则扬程高,但流量小;间隙大,则扬程低而流量大2.提高浆粕的吸碱速度4.预粉碎或者细粉碎的1.碱纤维素过干或者过湿引起预粉碎堵料1.调节压辊速度堵料2.落料斗中碱垢落下,引起细粉碎的堵料3.细粉碎转速降低2.清理碱垢3.增加细粉碎转速5.粉碎机粘壁1.纤维素中半纤维素和树脂等含量过高,粉碎时会形成粘性颗粒,易于粘附在粉碎机壁上1.控制半纤维素和树脂含量6.老成进口堵料1.压榨开始后忘开老成鼓搅拌轴,使细粉碎堵料2.老成鼓跳闸未及时发现3.老成鼓出口料走不动未及时发现1.浸压粉住手压榨,检查细粉碎是否受损2.开启老成鼓或者检查跳闸原因3.排除出料口故障继续走料7.老成出口堵料1.输送带滑料2.老成出口碱纤塞得太紧1.皮带原因、料层太厚、料层太湿2.用细棍掏通8.老成温度不许1.温度失灵2.温度计周围有碱纤结垢1.更换温度计2.疏通以除去碱垢9.杂物落入黄化机内1.料斗上的铁件久后脱落2.机口周围的小杂物清扫时未及时发现一并倒入1.发现后清除黄化机内杂物2.加强对料斗和机口周围检查,有杂物主动清除10.黄化“串料”1.黄化机进出料阀门关启差错2.黄化机阀门失灵及封闭不严1.粘胶抽入量不多:可降低黄化温度;延长黄化时间;添加浓碱液;增加二硫化碳用量2.粘胶抽入量较多: 则不宜补救, 应报废1.关闭有关阀门 2.检修机台密封系统 3.增加真空泵中的水1.住手进料2.纠正操作错误 3.纠正操作错误3.前面一批料未走完就进下一批料常见故障 产生原因 1.成品中有粗纤维或者 1.个别纺丝部位烛形滤芯由于包扎不良 并丝 而使粘胶短路 2.个别喷丝孔被杂质阻塞2.丝束上有粒状细微 1.脱泡不良 胶块3.丝束上有大胶块 1 .凝固浴硫酸浓度过低造成成形差2.喷丝头组件泄露,粘胶连续被丝条带 出 3.喷丝头损伤4.纺前进口压力大,出口压力过低,形 成压力降过大4.断头(闷头) 1.纺前不能连续供胶(换滤布后没有充 胶而存在气泡) 2.喷丝头组件破裂3.计量泵齿轮啮合不良,发生间歇式转 动或者不转动5.异状纤维 1.脱泡不良2.黄化时 CS2 量过多3.更换喷丝头及滤器时未排尽气泡6.出塑化浴的丝束出 1.凝固浴酸度过高导致反应剧烈而浮现 现毛丝 脆丝,经不起拉伸 2.粘胶熟成度过大导致流动差,份子运 动被束缚,不易拉伸 3.塑化浴内拉伸倍数过高 4.丝束在塑化机内机械磨损7.复丝中单丝根数不 1.喷丝孔阻塞2.部份断头缠牵伸盘11.黄化时抽不起真 1.机台有阀门未关到位 空 2.机台密封系统漏气3.真空泵无水或者水太少12.后溶解溢胶 1.进料机台搞错,使后溶解机内粘胶满 料2.阀门开错或者该关的未关到位 1.酸站补加硫酸2.更换喷丝头组件 3.更换喷丝头4.加强头、 二道过滤, 改善粘胶质量或者增 加纺前滤机换布次数 1.有效脱泡 2.减少 CS2 用量 3.更换组件前用 N2 排空 1.降低硫酸浓度 2.减少熟成度3.降低塑化拉伸倍数4.检修塑化槽内部 1.严格纺前滤机开新车操作2.更换喷丝头组件 3.修理计量泵传动部位1.减少粘胶中树脂、蜡质等杂质 2.在粘胶中加助剂,防止结垢1.重新包扎烛形滤芯 2.清洗喷丝头组件1.提高真空度,保证脱泡时间解决方法足3.部份单丝合并到邻丝的丝条上3.提高酸浴清洁度,防止硫及硫化锌沉淀到喷丝头表面4.在酸浴中加助剂,防止结垢8.纺丝机件漏胶1.机件质量差,互换性不好2.垫圈裂边,缺口和带胶皮3.曲管(鹅颈管)边缘破损4.摇摆杆罗纹或者滤套罗纹磨损5.纺丝泵装配不良或者平整度差1.纺丝机件在进厂时应检查质量,保证机件的互换性2.选用弹性和抗疲劳性好的密封圈或者平整的纸垫3.使用中对不合格的机件要剔除,如罗纹磨损的摆杆、滤套、边缘破损的曲管和垫圈等不得使用4.正确装配纺丝泵9.卷曲丝饼1.漏斗偏离离心罐中心2.漏斗本身偏斜3.漏斗或者离心罐振动1.纠正漏头位置2.纠正漏头位置3.制止漏斗或者离心罐振动10.大小头丝饼1.漏斗口距离心罐底部过高或者过低1.调节漏斗口距离心罐底部应为 5mm 摆布11.条纹丝饼1.整台纺丝机浮现条纹丝饼,是漏斗升降次数和离心罐转速配合不良造成的2.个别锭子产生条纹丝饼,是升降架跳动或者个别离心罐转速下降造成1.调节漏斗升降次数和离心罐转速使配合良好2.防止升降架跳动,提高离心罐转速12.羽毛丝饼1.离心罐或者内套中有废丝1.清除离心罐或者内套中废丝13.小丝饼1.纺丝时间不足2.断头时间过长3.漏胶1.增加纺丝时间2.检修设备14.大丝饼1.超时落丝1.缩短落丝时间15.乳白丝1.CS2 超过黄化用量的 20%2.酸浴中硫酸和硫酸钠含量偏高,浴温也过高3.纺丝胶熟成度过低(过嫩胶),氯化铵值>12mL4.浆粕中树脂含量太低5.纤维烘干过于迅速1.保证二硫化碳加入量的准确性2.严格控制酸浴组成和温度。
粘胶纤维粘连丝成因及控制措施

3 1 粘胶质量 工艺优化前、后粘胶原液中的大粒子数
量,如表2 所示。
【 6 】
第 卷第期 人造纤维 年 月版 49
6 2019 12
Hale Waihona Puke , , Vol 49 № 6
Artificial Fibre
第 卷第期 人造纤维 年 月版 49
6 2019 12
, , Vol 49 № 6
Artificial Fibre
December 2019
粘胶纤维粘连丝成因及控制措施
刘长军 贾守江 时志宏
潍坊欣龙生物材料有限公司 山东潍坊261100
6
274
, 2019 № 6
Artificial Fibre
Sum274
图2 喷丝头内聚物的红外谱图
红外谱图及喷丝头内聚物分析可以确定, 成喷的丝纤头维内素聚磺物酸为酯半易纤溶,解由、于析半出纤,与在CS纺2 反丝应再生生 成形反应中提前析出,造成喷丝头内部堵塞, 形成堵孔或半堵孔。 1 3 纺丝成形
1 粘连丝产生原因分析
粘连丝与并丝不同,并丝是几十甚至上百 根单丝粘在一起,呈线粘连,并且是深层粘 连,比较粗,原棉分析机很容易析出,通过疵 点指标能表征其多少;而粘连丝一般是少数几 根单丝粘在一起,且粘连多数为点粘连,表层 粘连,较轻,原棉分析机无法将其析出,无法 单用疵点指标,衡量产品内在质量。 1 1 截面形状
由图1 中可以看出:A、B、C 三处相邻 丝条之间表层粘在一起,形成粘结,截面严重 不规则。 1 2 红外光谱分析
对换下的喷丝头进行观察,发现其堵孔多, 喷丝头内的白色聚集物大面积覆盖喷孔,使得
图1 粘连丝截面形态图
其他未堵的喷孔粘胶流量相对增大,丝条喷出 后胀大,造成粘连,而堵孔的喷丝头孔目、孔 径变细,喷出的丝条在机械外力拉伸下易断 裂、粘连。采用红外光谱对喷丝头白色内聚物 进行了分析,见图2。
粘胶短纤维成品质量影响因素分析
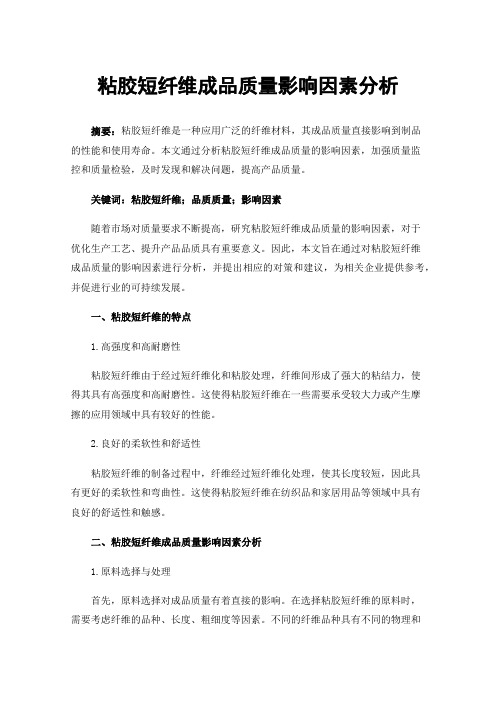
粘胶短纤维成品质量影响因素分析摘要:粘胶短纤维是一种应用广泛的纤维材料,其成品质量直接影响到制品的性能和使用寿命。
本文通过分析粘胶短纤维成品质量的影响因素,加强质量监控和质量检验,及时发现和解决问题,提高产品质量。
关键词:粘胶短纤维;品质质量;影响因素随着市场对质量要求不断提高,研究粘胶短纤维成品质量的影响因素,对于优化生产工艺、提升产品品质具有重要意义。
因此,本文旨在通过对粘胶短纤维成品质量的影响因素进行分析,并提出相应的对策和建议,为相关企业提供参考,并促进行业的可持续发展。
一、粘胶短纤维的特点1.高强度和高耐磨性粘胶短纤维由于经过短纤维化和粘胶处理,纤维间形成了强大的粘结力,使得其具有高强度和高耐磨性。
这使得粘胶短纤维在一些需要承受较大力或产生摩擦的应用领域中具有较好的性能。
2.良好的柔软性和舒适性粘胶短纤维的制备过程中,纤维经过短纤维化处理,使其长度较短,因此具有更好的柔软性和弯曲性。
这使得粘胶短纤维在纺织品和家居用品等领域中具有良好的舒适性和触感。
二、粘胶短纤维成品质量影响因素分析1.原料选择与处理首先,原料选择对成品质量有着直接的影响。
在选择粘胶短纤维的原料时,需要考虑纤维的品种、长度、粗细度等因素。
不同的纤维品种具有不同的物理和化学性质,在成品的性能和外观上会有所差异。
此外,纤维的长度和粗细度也会影响到成品的强度和手感等特性。
因此,在选择原料时,需要根据产品的要求进行合理的选择,以确保成品的质量达到预期。
其次,原料的处理过程也对成品质量产生重要影响。
处理过程包括原料的清洁、染色、漂白等环节。
首先,原料要经过充分的清洁处理,去除其中的杂质和污染物,以保证纤维本身的质量。
其次,在染色和漂白过程中,需要控制好温度、时间和药剂浓度等参数,以确保颜色的均匀度和纤维的亮度。
处理过程中的不当操作或者使用低质量的药剂可能会导致纤维受损或者出现色差等问题,进而影响到成品的质量[1]。
2.纺纱过程中的工艺参数控制首先是纺纱过程中的喷丝压力和喷丝速度。
技术 细纱质量问题的原因分析及措施
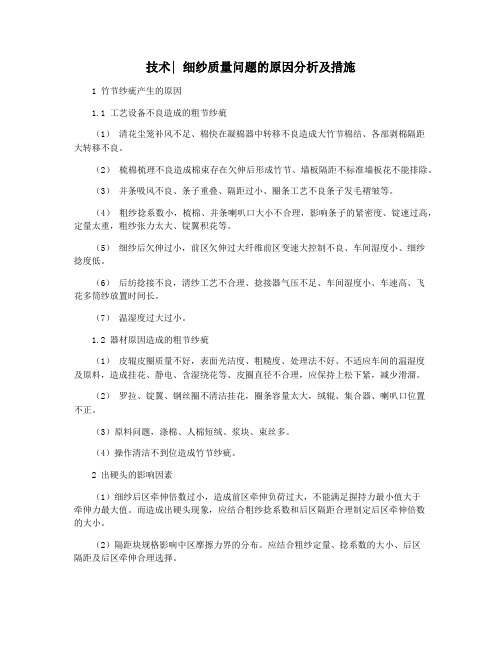
技术| 细纱质量问题的原因分析及措施1 竹节纱疵产生的原因1.1 工艺设备不良造成的粗节纱疵(1)清花尘笼补风不足、棉快在凝棉器中转移不良造成大竹节棉结、各部剥棉隔距大转移不良。
(2)梳棉梳理不良造成棉束存在欠伸后形成竹节、墙板隔距不标准墙板花不能排除。
(3)并条吸风不良、条子重叠、隔距过小、圈条工艺不良条子发毛褶皱等。
(4)粗纱捻系数小,梳棉、并条喇叭口大小不合理,影响条子的紧密度、锭速过高,定量太重,粗纱张力太大、锭翼积花等。
(5)细纱后欠伸过小,前区欠伸过大纤维前区变速大控制不良、车间湿度小、细纱捻度低。
(6)后纺捻接不良,清纱工艺不合理、捻接器气压不足、车间湿度小、车速高、飞花多筒纱放置时间长。
(7)温湿度过大过小。
1.2 器材原因造成的粗节纱疵(1)皮辊皮圈质量不好,表面光洁度、粗糙度、处理法不好、不适应车间的温湿度及原料,造成挂花、静电、含湿绕花等、皮圈直径不合理,应保持上松下紧,减少滑溜。
(2)罗拉、锭翼、钢丝圈不清洁挂花,圈条容量太大,绒辊、集合器、喇叭口位置不正。
(3)原料问题,涤棉、人棉短绒、浆块、束丝多。
(4)操作清洁不到位造成竹节纱疵。
2 出硬头的影响因素(1)细纱后区牵伸倍数过小,造成前区牵伸负荷过大,不能满足握持力最小值大于牵伸力最大值。
而造成出硬头现象,应结合粗纱捻系数和后区隔距合理制定后区牵伸倍数的大小。
(2)隔距块规格影响中区摩擦力界的分布。
应结合粗纱定量、捻系数的大小、后区隔距及后区牵伸合理选择。
(3)粗纱的定量大,在同样的胶辊状态和后区牵伸倍数及粗纱捻系数情况下,相应细纱牵伸时的胶圈钳口握持力增加,以满足牵伸力握持力的匹配。
(4)胶辊的表面处理方式和胶辊胶圈的表面摩擦系数影响握持力和牵伸力的大小匹配。
不粘缠的情况下尽量加大胶辊的表面摩擦系数,控制胶圈滑溜的情况下适当减小胶圈的表面摩擦系数,以稳定中区牵伸力。
(5)温湿度过大,使须条中纤维间的摩擦阻力相应增加,导致须条中纤维抱合力增加,造成牵伸力大小波动而造成牵伸不稳定的现象。
- 1、下载文档前请自行甄别文档内容的完整性,平台不提供额外的编辑、内容补充、找答案等附加服务。
- 2、"仅部分预览"的文档,不可在线预览部分如存在完整性等问题,可反馈申请退款(可完整预览的文档不适用该条件!)。
- 3、如文档侵犯您的权益,请联系客服反馈,我们会尽快为您处理(人工客服工作时间:9:00-18:30)。
粘胶纱线产生细节的原因分析与控制随着市场对纺织品质量要求的不断提高,纺织面料提升档次已成为我国纺织工业发展的新突破口,从而对纱线质量要求也更加严格,而成纱细节是纱线质量中的十分重要的因素。
生产实践证明,成纱细节对细纱断头,机织和针织生产时的断头有较大的影响。
尤其是一刀切细节,更是严重影响织物、尤其是针织物的强力。
从目前市场情况来看,粘胶纤维纱线主要用作针织纱来和长丝交织,其对成纱细节的要求更是越来越严格,更要加强对成纱细节的研究和控制。
1 细节产生的原因棉纱细节从广义上讲指比棉纱平均截面积细的部分都是细节,我们在实际生产中通常将细节分为短细节和长细节。
短细节一般为40cm以下的细节,对于短细节单纯从长度上来看显然是产生在粗纱之后,但追根究底,除了粗纱、细纱的意外牵伸之外,最根本的原因是短绒造成的。
这一点可以从同支精梳棉纱与普梳棉纱对比中得到有力的验证。
另外,半制品的纤维伸直状况也是一个不可忽略的因素。
40cm以上的细节称为长细节。
虽然长细节的数量远低于短细节,但其危害性远大于短细节。
一般来说,长细节主要是由于并粗意外牵伸、机械设备性能不良以及挡车工操作时不注意把清细条,接头质量不过关造成的。
因此,控制长细节的关键部位是在并条和粗纱工序。
2细节的控制措施2.1 合理选择工艺参数2.1.1 合理使用回花、再用棉,控制短绒含量原料中的短绒控制是减少成纱细节的第一道关口。
作为化学纤维的一类,粘胶纤维含杂情况与棉不同,一般只含少量的粗硬丝、并丝、胶块及超长纤维,长度整齐度较好,短绒含量极少,因此,选配时可不必考虑短绒含量的多少,只要做好可纺性能的选配就行了。
但是,为了兼顾生产成本,不可避免要使用回花、再用棉,而回花、再用棉的质量情况各不相同,必须根据不同再用棉的情况,选用适当的比例。
一般来说,回用棉的短绒较少,可适当本支回用,而吸风棉、斩刀花等不但结杂多,而且含有大量短绒,必须经过处理方可少量回用,比例一般不能超过2%。
2.1.2 合理配置清梳工艺,减少纤维损伤,加强短绒排除因粘胶纤维无杂质而又较蓬松,仅含少量疵点,强力又低,所以开清棉工序贯彻“以梳代打、梳打结合工艺,少用打击方式和改进打手形式,加强短绒排除”的原则,并合理选择打手速度和隔距等重点工艺参数,以减少纤维的损伤。
为了排除短绒,可适当增加尘笼吸风,一般增至1400r/min左右。
另外,必须加强对握持打击开清棉机械性能和短绒测试,在原料变化较大或机台保全保养后进行短绒的测定,并及时调整工艺参数,使短绒增长率控制在规定范围内。
梳棉工序减轻纤维损伤的关键部位在给棉和刺辊部位。
必须根据不同纤维长度选用不同长度给棉板工作面和后部工艺参数。
实践证明,粘胶纤维刺辊速度一般掌握在850r/min以下,否则纤维损伤加剧。
给棉板工作长度一般选用32mm,有条件可采用菱形给棉罗拉。
盖板花和后车肚落棉是梳棉排除短绒的关键部位。
可适当增加前上罩板隔距,增加盖板速度,同时减小漏底入口隔距,除尘刀在高刀大角度前提下,尽量隔低,可有效降低生条短绒率,但由于粘胶纤维短绒含量低,为了节约原料,降低成本,此处工艺必须适当兼顾。
总之,粘胶纤维清梳工序短绒增长率应力争控制在1.5%以内。
2.1.3 并粗采用纤维伸直度工艺,改善半制品内在结构生产实践证明,粗纱内在质量,纤维伸直平行度、分离度和短绒率对成纱条干CV%,特别是成纱细节有较大影响。
一般来讲,纤维伸直度小,牵伸区中有效长度变短,从而使浮游动程增加,纤维易缠结,产生集束运动,破坏运动规律,产生粗细节。
纤维分离度小,纤维中小棉束、棉结增多,由于小棉束抱合力大,同样易成束运动,产生粗、细节,因此,并粗工艺必须采取伸直度工艺,改善半制品结构。
根据系统棉纺工艺学理论,1.5D×38mm粘胶纤维正确工艺为:头并总牵伸8倍,后区牵伸配置为1.7~1.8倍,罗拉隔距48mm,二并后牵伸1.10~1.30倍。
粗纱在不产生意外伸长的情况下,采用适当紧张力纺纱,保证纱条有一定紧密度。
后区牵伸一般为1.10~1.20左右。
生产实践证明,这种工艺配置对改善纤维伸直状态有很大的效果,能明显减少成纱细节。
2.1.4 合理选择牵伸工艺,加强短纤维控制由于清梳工序排除短绒的能力有限,因此,并条、粗纱、细纱三个牵伸工序必须合理配置牵伸区的摩擦力界,强化控制浮游纤维。
尤其是细纱工序,做好“强控制”是非常有利于提高成纱质量,减少成纱粗细节的。
但由于粘胶纤维长,摩擦抵抗力大,对“强控制”的工艺参数,放到什么水平,什么效果最好,还必须认真探索。
(1)适当增加粗纱捻系数。
经过细纱后区解捻牵伸后还保留有较多的捻度进入前区,加强了前区摩擦力界控制,从而加大了前区对浮游纤维的控制能力。
但粗纱捻系数不是越大越好,应综合考虑细纱牵伸装置尤其是老机的性能、半制品质量状况、细纱后区牵伸倍数以及后区罗拉中心距等因素,通过试验择优而定。
增大捻系数的上限以细纱不出硬头为标准。
粘胶纤维粗纱捻系数一般控制在65~78之间。
(2)选用较小细纱后区牵伸。
细纱后区的主要作用是为前区作准备,使喂入前区的纱条具有结构均匀和必要的紧密度,使之与前区摩擦力界相配合而形成稳定的前区摩擦力界分布,以充分发挥皮圈控制纤维运动的作用,从而减少成纱粗细节,改善纱布外观质量。
选用较小的后区牵伸,可减少牵伸不匀率,并适当利用粗纱捻度,增加后区与前区牵伸纱条的紧密度,既有利于后区控制纤维运动,又有利于发挥前区皮圈控制纤维运动的作用,集中前区牵伸,从而改善成纱细节和条干。
但后区牵伸也不宜过小,否则会出现涌条现象,反而恶化条干,增加粗细节。
值得注意的是,较小的后区牵伸必须和较大的后区隔距配合,以有利于满足牵伸力小于握持力的要求。
对粘胶纤维而言,后区牵伸一般不大于1.25。
(3)改善细纱前区工艺细纱前罗拉采用低硬高强胶辊。
低硬高强胶辊在受压状态下变形大,同下罗拉表面可以形成更大的圆弧接触面,即增大了对纤维的有效接触面积,实际上就是减小了中间浮游区,对纤维的控制更有力了,从而有利于提高条干水平和减少成纱细节。
生产实践证明,使用低硬高强胶辊可以改善条干0.5%左右,细节也明显减少。
但在粘胶品种上使用必须注意选择合适的硬度及准确掌握调换周期,否则会适得其反。
合理分布中部摩擦力界。
上下皮圈的配套选择是加强中部摩擦力界控制的先决条件,一般采用上松下紧和上薄下厚的皮圈配套原则,皮圈的弹性和柔软度都要良好,保证上下皮圈在回转中密和无隙。
在销子选择上,上销选择碳素上销,下销可选用新型T型下销。
新型T 型下销对胶圈下销的上表面形状做了改进,加强了上下胶圈对纤维的控制力,使摩擦力界的分布更为合理。
采用这样的配置后,皮圈牵伸能力大为提高,在牵伸过程中控制须条能力增加,浮游纤维的浮游情况得到改善,纤维变速点稳定,使纱条粗细均匀,粗节、细节明显减少,CV值降低。
但对粘胶纤维而言,由于纤维的特殊性能,新型下销最高点的位置前移多少最适合还需经反复试验择优而定,同时在安装平修上也必须高要求。
2.1.5 合理配置其它工艺参数,减少意外牵伸并粗意外牵伸是纱条产生长细节的主要原因。
在工艺配置上,主要涉及到张力参数的制订。
一般来说导条部分张力配置的原则是在不出现涌条情况下以小掌握为宜。
如张力配置过大,机台断头多,挡车工处理时搭头又不良,会产生很长的细节。
粗纱张力牙配置适当,以免经常收放张力牙,产生张力不匀。
另外,在不影响纱条条干的前提下,适当加大棉条定量,可以增加纤维抱合力。
如定量过轻,纤维抱合力不足,通过粗纱导条架时意外牵伸加剧。
另外并条压缩喇叭口口径偏小掌握,也可增加熟条抱合力,减少牵伸时的意外牵伸。
2.2 加强设备维护管理,保证设备状态设备维护质量的好坏直接影响到产品质量的稳定与提高,这是不容讳言的事实。
粘胶纤维纱线由于抱合力差,纤维与金属的摩擦系数大,成纱细节尤其是长细节与设备的关系相当密切,主要表现在以下几个方面。
2.2.1 开关车细节这是传统设备与生俱来的缺陷。
无论棉条还是粗纱均是如此。
老式并条机械由于是直齿传动,加之前后罗拉之间齿轮啮合点较多,较容易导致传动时啮合不良,开关车时出现“反啮合”现象,产生开关车细节。
要想减少此种现象,没有比较好的办法,只有将车速降低,或者更换目前性能较好的高速并条机,但是车速也不宜太高,在满足产量供应的情况下,宜偏低掌握。
粗纱机的关车细节只要铁炮存在就不可避免。
由粗纱机的传动系统知,由于卷绕部分的传动路线比牵伸部分的传动路线长,使得粗纱关车时筒管停转的时刻比前罗拉滞后,导致纺纱段一段纱条张力过大,意外伸长严重,形成细节。
解决这种问题的办法不多,有效的办法应是保持卷绕部分的传动状态良好,最好是改用变频传动,增强传动的稳定性,可有效减少开关车细节。
另外在粗纱锭翼顶端使用高效橡塑假捻器,加强纺纱段的强力,也可减少纱条意外牵伸,改善细节。
2.2.2 机械不良机械不良,尤其是熟条、粗纱的机械不良将会产生严重的长细节。
主要情况有:(1)并条导条架压辊转动不灵活或安装位置不正,引起导条部分棉条意外伸长。
(2)粗纱高架部分导条架运转不良,时转时停,使条子意外伸长。
(3)并条机后断条自停失灵,缺条时挡车工又未及时处理,从而形成很长很长得细节。
(4)牵伸罗拉有毛刺,喇叭口破损等产生绕、粘、带而产生长细节。
(5)细纱托锭、吊锭回转不灵活,产生打顿现象,使粗纱伸长。
2.3 加强操作管理,加强质量把关运转管理跟不上,操作不到位,产生细条是产生长细节的另一主要因素,因此必须加强运转操作管理。
(1)保证接头质量,防止包卷过松或搭头过短,经过牵伸后产生长细节。
(2)加强质量把关,及时抠清细条。
(3)加强清洁工作,保证通道清洁、光滑,防止须条在纺纱过程中被剥掉部分纤维,产生粘、缠、带现象,从而出现粗细节。
粘胶纤维由于纤维抱合力差,更易产生粘带现象,更要重点加强清洁工作。
3结语减少细节,是一项技术性很强的工作,涉及到很多方面,除了上述主要因素外,还涉及到温湿度、职工素质等诸多方面。
尤其是粘胶纤维的性能和棉有一定区别,因此,解决粘胶纤维纱线细节问题必须具体问题具体分析,根据纤维的特性,抓住主要矛盾,才能使成纱细节处于受控状态。
日常生产中,一般短细节的产生远高于长细节,因此,我们的工作重点应着重围绕减少短细节来进行。
它是一项技术极强的工作,主要是围绕减少短纤维的产生,有效排除短纤维,改善纤维伸直度以及有效控制短纤维运动等几个主要方面进行。
而长细节只要围绕如何减少意外伸长、加强设备维护、保证接头质量和防止并条缺条等方面开展工作即可。