Moldflow设计指南 浇口及浇注系统
moldflow6.1中文教程第8 章 最佳浇口位置和流道平衡分析实例
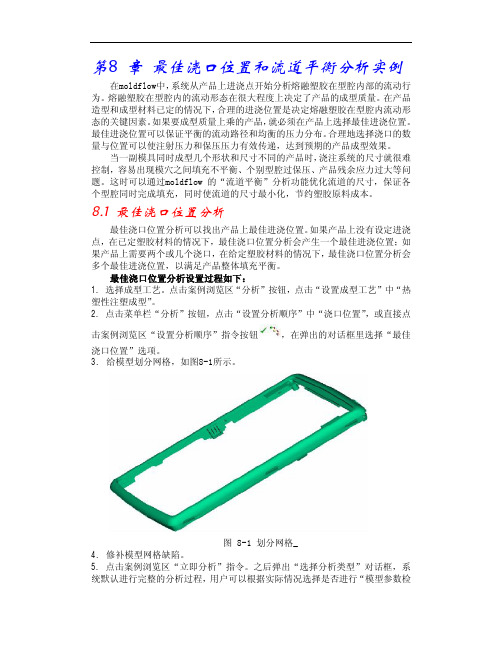
第8 章最佳浇口位置和流道平衡分析实例在moldflow中,系统从产品上进浇点开始分析熔融塑胶在型腔内部的流动行为。
熔融塑胶在型腔内的流动形态在很大程度上决定了产品的成型质量。
在产品造型和成型材料已定的情况下,合理的进浇位置是决定熔融塑胶在型腔内流动形态的关键因素。
如果要成型质量上乘的产品,就必须在产品上选择最佳进浇位置。
最佳进浇位置可以保证平衡的流动路径和均衡的压力分布。
合理地选择浇口的数量与位置可以使注射压力和保压压力有效传递,达到预期的产品成型效果。
当一副模具同时成型几个形状和尺寸不同的产品时,浇注系统的尺寸就很难控制,容易出现模穴之间填充不平衡、个别型腔过保压、产品残余应力过大等问题。
这时可以通过moldflow 的“流道平衡”分析功能优化流道的尺寸,保证各个型腔同时完成填充,同时使流道的尺寸最小化,节约塑胶原料成本。
8.1 最佳浇口位置分析最佳浇口位置分析可以找出产品上最佳进浇位置。
如果产品上没有设定进浇点,在已定塑胶材料的情况下,最佳浇口位置分析会产生一个最佳进浇位置;如果产品上需要两个或几个浇口,在给定塑胶材料的情况下,最佳浇口位置分析会多个最佳进浇位置,以满足产品整体填充平衡。
最佳浇口位置分析设置过程如下:1. 选择成型工艺。
点击案例浏览区“分析”按钮,点击“设置成型工艺”中“热塑性注塑成型”。
2. 点击菜单栏“分析”按钮,点击“设置分析顺序”中“浇口位置”,或直接点击案例浏览区“设置分析顺序”指令按钮验”的分析。
点击“确定”,分析正式开始。
勾选案例浏览区中“日志”,用鼠标将主窗口下边缘向上拖动直到顶部,查看屏幕输出结果。
8.2 最佳浇口位置分析结果解析图 8-2 最佳进浇位置显示勾选,在主窗口显示产品模型。
红色区域为最佳进浇位置,相比之下,其它颜色区域进浇合理性均低于红色区域,其中蓝色区域进浇合理性最差,如图8-2 所示。
在案例浏览区点击“工艺”,将主窗口下边缘向上拖动,在屏幕结果输出中查看经系统得出的最佳进浇点,如8-3所示,显示本产品的最佳进浇点在节点N9560附近。
基于MoldFlow的注塑模具浇口优化设计

图3 划分网格后的模型
3.2 材料及工艺参数的确定
本文设计的手机上盖属于中小塑件。此制 品将直接与用户手部接触并需承受频繁的按 动。因此,要求很高的表观质量和手感,并具 有一定的强度。这里选用ABS塑料,工艺条件 如下:
()模温:60.0 ℃ (2)熔体温度:240 ℃ (3)注塑时间:.2 s (4)注塑机的压力控制模块的最大注塑压
4
力:80 MPa (5)模块中的最大锁模力:702.2 kN,其
余均采用默认值。
3.3 浇口位置优化的预分析
浇口设计应保证提供一个快速、均匀、平 衡、单一方向流动的充填模式,避免喷射、滞 流、凹陷等现象的发生,所以要在选定浇口方 案之前,对制品进行最佳浇口位置的预分析。 利用MPI软件中的Gate Location分析模块,在 前处理中将分析类型设为Gate Location,并设 置好工艺过程参数。运行Gate Location分析 后,得到一个最佳的浇口位置(图4中圆圈所 示)。Gate Location分析模块只是为设计分析 初步找到一个最佳的浇口位置区域,该浇口位 置只是一个参考位置,对将来的设计有很好的 参考价值。下一步需要根据现有的分析结果对 手机上盖进行注塑、保压及相应的翘曲计算, 再根据得到的结果进一步分析产品的质量及模 具设计的合理性,从而向最佳方案逼近。
基于Moldflow软件的多腔注塑模浇注系统设计
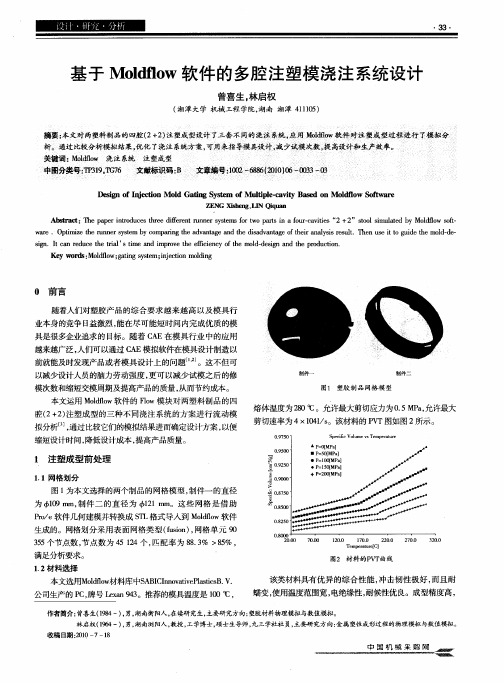
本文运用 Mo fw软件 的 Fo ll do l w模块 对两塑料制 品的 四
35 5 个节点数 , 点数为 4 2 , 节 51 4个 匹配率 为 8.% > 5 , 83 8%
满足分析要求 。
12材料选择 .
图2 材 料 的P T 线 V 曲
本文选用Mo f w l t 材料库 中S BC noa vPat s . do A I Invt e l i B V. i sc
收稿 日期 : 1 7— 8 2 0— 1 0
q 国十傅 墨婴 一 ] 几 一
・
3 பைடு நூலகம் 4・
尺寸稳定性好。但其缺点是 自身流动性差 , 且疲劳性 , 耐磨性 较差 , 口效应敏感 。 缺
13浇注 系统的建立 . 为了探讨浇注系统对注塑成型 的影 响, 文设计 了三种 本 不 同的浇注系统。如图 3所示 , 流道分为热流道部分 , 冷流道
析。通过比较分析模拟结果, 优化 了浇注系统方案 , 可用来指导模具设计, 减少试模次数, 提高设计和生产效率。 关键词: odo 浇注系统 M llw i 注塑成型
中圈分类号: 9 7 如 1. 6 文献标识码 : 文章编号: 0 。 86删 O0 g 03 o B l 2 68( ) 03 一 3 O 6
制件一
图1 塑胶 制 品 网格 模 型
腔( + ) 2 2 注塑成型 的三种 不同浇 注系统 的方案进 行流 动模 拟分析 , 比较它们的模拟结果进 而确定设计方案 , 通过 以便 缩短设计时间 , 降低设计成本 , 提高产品质量。
moldflow 2010培训之《浇口与流道系统设计》
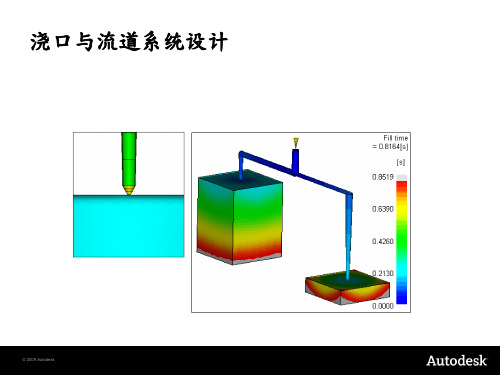
塑料件注塑模具的浇口及流道设计
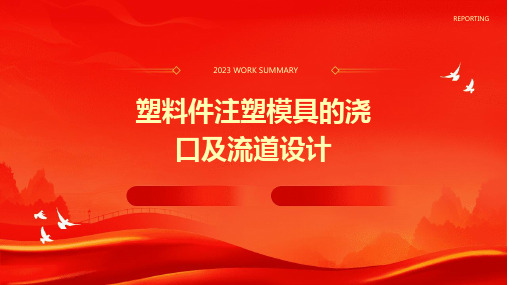
间接配合
浇口和流道通过其他结构进行间接连 接,这种配合方式可以更好地适应复 杂模具结构的要求。
配合实例
侧浇口与直通式流道的配合
侧浇口与直通式流道配合使用,可以保证塑料熔体的流动顺畅,适用于生产小 型塑料件。
扇形浇口与分流道的配合
扇形浇口与分流道配合使用,可以满足大型塑料件的充填要求,并减少溢料现 象的发生。
根据塑料件的精度要求选择浇口类型,高精度要求的塑料件应选择潜伏式浇口或直 接浇口。
根据塑料件的成型周期和生产效率要求选择浇口类型,生产效率要求高的应选择侧 浇口或扇形浇口。
浇口的尺寸
浇口的尺寸应根据塑料件的尺 寸、形状、精度要求以及塑料 熔体的流动特性来确定。
浇口的尺寸过大会导致塑料件 产生过大的收缩率,尺寸过小 会导致塑料件充填不足或产生 喷射痕。
SolidWorks
一款广泛使用的CAD软件,也适用于注塑模具设 计,提供了丰富的流道设计和分析工具。
3
Moldflow
专业的注塑模具设计软件,提供了流道设计和分 析功能,可以模拟塑料熔体的流动和冷却过程。
PART 05
浇口与流道设计案例分析
案例一:手机壳浇口设计
总结词
手机壳浇口设计需考虑浇口位置、尺寸和数量,以确保塑料能够顺利填充模具并 减少缺陷。
详细描述
根据餐具的形状和尺寸,选择合适的浇口位置和尺寸,以实现均匀填充。同时,流道的走向应与餐具的形状相匹 配,以减少流动阻力。在设计过程中,还需考虑餐具的功能需求,如刀叉的锐利度、碗盘的承重能力等,以确保 设计的实用性和可靠性。
PART 04
设计优化与改进
优化原则
减小浇口截面积
避免死角和滞留
浇口截面积的大小直接影响塑料熔体的流 动速度。减小浇口的截面积可以使熔体的 流动速度增加,从而提高生产效率。
MOLDFLOW详细操作手册
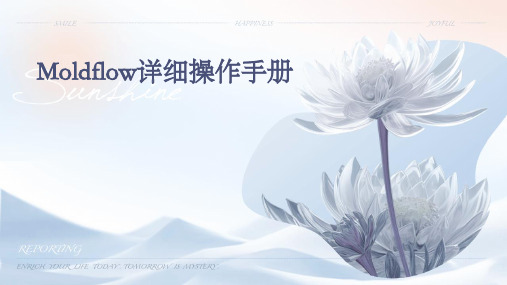
VS
4. 在必要情况下,采用多级注射工艺 来改善填充效果。
05
Moldflow案例分析
案例一:手机壳模具设计优化
总结词
通过Moldflow对手机壳模具进行模拟分析, 优化模具设计,提高生产效率和产品质量。
1. 导入3D模型
将手机壳的3D模型导入Moldflow软件中,并 进行适当的单位和网格划分设置。
冷却介质
根据模具结构和生产条件,选择合适的冷却介质,如水、油等, 以提高冷却效果和减小冷却时间。
模具热平衡分析
温度场分布
通过热平衡分析,了解模具温度场分布情况,为优化模具设计和减 小热误差提供依据。
热传导与对流
分析模具材料、冷却介质和塑料之间的热传导与对流情况,以提高 冷却效果和减小成型周期。
热膨胀与收缩
多模腔模拟
模腔耦合分析
通过多模腔模拟,分析各模腔之间的耦合效应, 以优化模具设计和减小成型误差。
充型平衡
通过多模腔模拟,分析各模腔的充型情况,以实 现各模腔的充型平衡和减小缺陷。
冷却平衡
通过多模腔模拟,分析各模腔的冷却情况,以实 现各模腔的冷却平衡和减小成型周期。
04
Moldflow常见问题与解决 方案
浇注材料等。
03
4. 设计调整
根据模拟分析结果,对模具设计方案进行调 整,如优化浇注系统、改进模具结构等。
05
04
3. 模拟分析
对模具进行充填、流动、保压和冷却 等模拟分析,观察分析结果,评估模 具设计方案的有效性和可行性。
06
5. 验证调整效果
通过再次模拟分析验证调整后的模具设计方案 效果,确保方案的有效性和可行性得到提高。
4. 尝试增加模拟迭代次数或采用更高级的求解算法以提高模 拟精度。
Moldflow设计指南——流动行为及注射压力
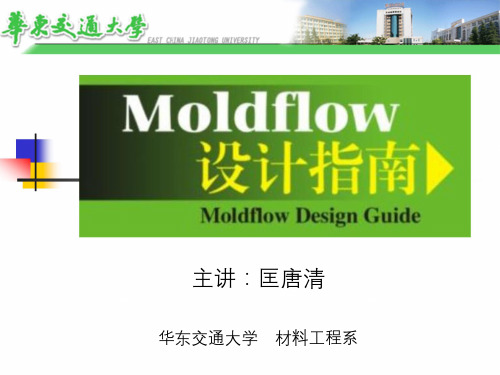
主讲:匡唐清华东交通大学材料工程系Moldflow简介⏹MoldFlow软件是澳大利亚MOLDFLOW公司的产品,该公司自1976年发行了世界上第一套塑料注塑成型流动分析软件以来,一直主导塑料成型CAE软件市场。
2000年4月,收购了美国AC-Tech公司开发的世界著名的塑料成型分析软件C-Mold,推出了MPI3.0,该软件综合了Moldflow 和C-Mold的功能。
2008年5月1日,Moldflow被Autodesk收购。
⏹经过30多年的持续努力和发展,Moldflow已成为全球塑料行业公认的分析标准。
企业通过Moldflow这一有效的优化设计制造的工具,可将优化设计贯穿于设计制造的全过程,彻底改变传统的依靠经验的“试错”的设计模式,使产品的设计和制造尽在掌握之中。
Moldflow为企业产品的设计及制造的优化提供了整体的解决方案,帮助工程人员轻松的完成整个流程中各个关键点的优化工作。
Moldflow简介⏹2011年5月,欧特克公司宣布推出Autodesk Moldflow 2012版,该软件包括:⏹Autodesk MoldFlow Insight(Moldflow高级成型分析专家,简称AMI)⏹Autodesk MoldFlow Advisers(Moldflow塑件顾问,简称AMA)⏹Autodesk MoldFlow Design Link(设计链接,简称MDL)⏹Autodesk MoldFlow CAD Doctor⏹Autodesk MoldFlow Structural Alliance(结构关联,简称MSA)⏹Autodesk MoldFlow Communicator(Moldflow浏览器,简称AMC),翻译人员主要内容☐聚合物在注射模塑中的流动行为☐成型条件与注射压力☐熔体充模图☐Moldflow设计原则☐Moldflow网格技术☐产品设计☐浇口设计☐浇注系统设计☐冷却系统设计☐收缩与翘曲☐Moldflow设计流程☐制件缺陷聚合物在注射模塑中的流动行为 注射过程⏹注射过程➢充填阶段:➢压实阶段:熔体具有可压缩性(约15%)➢补缩阶段:熔-固转变有体积收缩(约25%)⏹注射过程➢充填阶段⏹流动形态●喷泉流动:通道内为向前流动,流动前沿为向外流动●表层分子取向程度低⏹注射过程➢充填阶段⏹热平衡●冻结层厚度一定时,由熔体流动带来的热输入及剪切热与由热传导进入模具的热损失之间会达到平衡●注射速率、料温、模温对冻结层厚度的影响⏹注射过程➢充填阶段⏹分子取向●剪切速率分布⏹注射过程➢充填阶段⏹分子取向●分子取向分布→●残余应力分布(超过屈服强度则引起翘曲变形)表层熔体(来自喷泉流中心)快速冻结,取向程度低次表层熔体剪切应力大,停止流动时即冻结,取向程度高中心熔体剪切应力小,熔体冷却慢,取向程度低取向程度高,收缩大;取向程度低,收缩小外部受拉应力,内部受压应力⏹注射过程➢压实阶段⏹压力控制,建立起模腔压力,熔体流速降低,冻结层厚度增加⏹模腔静水压增大(静水压本身不在制件内留下任何残余应力)⏹注射过程➢补缩阶段⏹不稳定流动●温度不稳定→●流动不稳定→●河流状的补料流→●取向收缩→●翘曲变形⏹注塑件内大部分应力产生于补缩阶段,通过控制熔体流动状态,将流动应力降至最低,从而优化产品质量☐流变行为➢黏弹属性☐流变行为➢变形⏹剪切、拉伸☐流变行为➢剪切粘度⏹聚合物熔体一般2k-3k Pa.s☐流变行为➢剪切变稀⏹解缠、重排,减少流动抗力⏹水:P增大一倍,v增大一倍;聚合物熔体:P增大一倍,v增大2-15倍☐流变行为➢速率分布及剪切速率分布⏹模腔内剪切速率100/s-1000/s⏹喷嘴出来剪切速率应大于10 000/s☐流变行为➢温度、压力、剪切对粘度的影响☐流变行为➢充模时压力分布与变化☐流变行为➢压力梯度和注射时间充模时间越短,所需压力梯度越大充模时,速率控制,压力梯度应保持恒定☐流变行为➢熔体流长⏹与制件壁厚、工艺条件、材料自身热性能及剪切性能有关☐流变行为➢注射压力与充填时间快速充填要求高慢速充填,剪切热少,的注射压力来克熔体温度下降快,黏度服流动阻力增加,流动阻力增大优化的充模时间取决于注射压力、熔体温度变化及切应力变化聚合物在注射模塑中的流动行为☐流变行为➢流动的不稳定性⏹熔体流速高→⏹剪切速率和剪切热高→⏹熔体黏度低→⏹熔体流动加速→⏹剪切速率和剪切热更高→⏹……⏹切敏性材料与生俱来的流动不稳定性☐注射压力➢注射压力用于克服流动阻力,流动阻力与浇注系统结构、模腔结构及熔体黏度有关⏹影响注射压力的因素➢制件设计⏹影响注射压力的因素➢浇注系统设计⏹影响注射压力的因素➢工艺条件⏹影响注射压力的因素➢材料性质⏹数学关系➢圆截面流道➢矩形截面流道P为压力,n为材料常数(0.15-0.36,一般取0.3做近似)数学关系⏹成型条件对制件质量的影响➢制件质量⏹残余应力越小越好,尽量避免产生翘曲和表面缩痕⏹残余应力的测定●透明件——偏振光实验●非透明件——网目实验(退火去应力)测量椭圆长短轴了解残余应力的类型、大小和分子取向程度⏹成型条件对制件质量的影响➢熔体温度料温高,密度小,制件重量小;冷却收缩大,易产生表面缩痕料温高(低于降解温度),剪切应力小⏹成型条件对制件质量的影响➢模具温度⏹对制件质量的影响类似于熔体温度⏹在制件发生熔-固转变前,模温对压力和应力的影响不太明显⏹对制件冷却时间的影响比熔体温度大⏹提高模温,可适当降低充模注射速率⏹成型条件对制件质量的影响➢充模时间充模时间越长,流前温度下降越大充模时间短,要求注射速率快,所需的注射压力也高充模时间长,料流前沿温度下降大,熔体粘度增加,流动阻力增大⏹成型条件对制件质量的影响➢剪应力变化料流末端充模时间短,注射速度就快;充模时间长,料流温度越低;多数情况剪应力与注射时间呈U型曲线关系有些情况剪应力随注射时间增加而持续增加料流始端热量损失很小,剪应力主要由剪切速率决定,充模时间越长,注射速度越慢,剪应力就越小⏹成型条件对制件质量的影响⏹保压压力和保压时间⏹短时高保压的制件应力通常比长时低保压的制件的应力小在材料、结构和工艺条件不变的前提下,保压力越高,为获得相同重量制件所需的保压时间越短⏹成型条件对制件质量的影响➢静水压⏹制件内不产生残余应力⏹残余应力主要产生在保压补缩时(流动与冻结同时进行)⏹成型条件对制件质量的影响➢回流⏹发生在浇口尚未凝固,保压力又低于模腔压力时⏹易导致较大的缩痕➢理想模塑方案⏹熔体充模-保压切换后,短时保压,直到制件表面缩痕达到可接受的程度,同时让浇口充分冻结,确保无熔体流进/出模腔⏹应用MF优化成型工艺——成型窗口分析➢成型窗口分析可快速评价多个影响制件质量的因素⏹优化工艺条件⏹确定成型参数取值范围(成型窗口区域)⏹优选材料⏹预测熔体充模所需压力⏹设置浇口⏹给出制件壁厚参考⏹应用MF优化成型工艺——成型窗口分析➢优选材料示例⏹制件5浇口单侧进胶——保证单向、平衡的熔体充填。
Moldflow设计指南——浇口及浇注系统

流长缩短至900 mm, 所需充模压力降低
熔体大部分单向流动, 初期辐射状流动区较大
流长缩短至800mm 熔体单向流动较好
产生了较多的熔接线
浇口设计
Moldflow在浇口设计中的应用示例
成型窗口
不可行区:充模压力 高于额定注射压力的 80%(流长过长导致)
厚度h约为0.8mm~4.8mm 宽度为1.6mm~6.4mm
浇口设计
浇口类型
手工去浇类浇口
薄膜浇口
相当于扇形浇口的简化 版,不能获得平坦的熔 体流动前沿
薄膜浇口:由直流道、 熔体分配流道和浇口面 组成;熔体分配流道长 与制件进胶尺寸相当
常用于注射丙烯酸制品 和翘曲度要求很高的平 板制品
厚度h约为0.25mm~0.63mm 长L为0.63mm
浇口处熔体流动的压力降由传热控制,工艺条件的微小变 化会给熔体充模流动方式带来很大改变
浇口处易发生迟滞现象 浇口处熔体流动不稳定,会形成很大的压力降 浇口的加工误差和摩擦磨损对流经浇口的熔体压力降影响
极大 通过浇口调整来实现的流动平衡,成型窗口很小,其流动
平衡极易被工艺参数的微小波动破坏
浇注系统设计
牛角浇口/香蕉入水: 镶块加工
浇口设计
浇口类型
自动去浇类浇口
热流道浇口
无浇注系统凝料,热流道(浇 口)模具也称无流道模具
成型保压时间 由浇口附 近的制件冻结程度控制
浇口设计
浇口类型
自动去浇类浇口
阀浇口
增设阀针 可控制保压时间 浇口可更大,浇口痕更光滑 可生产出质量更加稳定的塑 料制品
主讲:匡唐清
华东交通大学 材料工程系
主要内容
- 1、下载文档前请自行甄别文档内容的完整性,平台不提供额外的编辑、内容补充、找答案等附加服务。
- 2、"仅部分预览"的文档,不可在线预览部分如存在完整性等问题,可反馈申请退款(可完整预览的文档不适用该条件!)。
- 3、如文档侵犯您的权益,请联系客服反馈,我们会尽快为您处理(人工客服工作时间:9:00-18:30)。
浇口设计
浇口设计准则
浇口布局
平衡浇口位置
等流长两浇口:多浇口等距 设置,不产生过保压,可降 低翘曲 多浇口,产生熔接线,熔接 质量取决于前沿温度和压力
两近中心浇口:浇口间过保 压,易引发翘曲
熔接线熔接质量略高
浇口设计
浇口设计准则
浇口布局
在厚壁区设置浇口
浇口设置在厚壁区,体积收 缩率较低且较均匀
牛角浇口/香蕉入水: 镶块加工
浇口设计
浇道(浇 口)模具也称无流道模具
成型保压时间 由浇口附 近的制件冻结程度控制
浇口设计
浇口类型
自动去浇类浇口
阀浇口
增设阀针 可控制保压时间 浇口可更大,浇口痕更光滑 可生产出质量更加稳定的塑 料制品
浇注系统设计
浇注系统定义
浇注系统(流道系统)
从模具入口到模腔间的熔体流动通道
冷流道系统
每个成型周期需取出流道系统冷凝料 包括有主流道、分流道、浇口
主流道必须有锥度, 小端与喷嘴相接
浇注系统设计
浇注系统定义
热流道系统
无流道系统冷凝料
包括有主流道、分流道(热支管)、浇 口(热滴管/热竖井) 热流道系统后可接冷流道
浇注系统设计原则
浇口尺寸相同时, 近主流道型腔迟滞
增大中间型腔浇口尺寸 后,最外侧腔迟滞明显
浇口类型
手工去浇类浇口
边缘浇口
边缘浇口:侧浇口,设 在模具分型面上
浇口厚度h为制件厚度t的 6%~75%(0.4mm~6.4mm) 宽度W为1.6mm~12.7mm 长度L不大于1mm(最好 0.5mm)
浇口设计
浇口类型
手工去浇类浇口
重叠式浇口
重叠式浇口:浇口与制 件壁或制件表面重叠
可消除充模喷射现象
浇口设计
浇口设计准则
控制单向流动 平衡熔体流动 合理处置熔接线和汇熔线 避免迟滞效应 避免潜流效应 采用导流器/节流器迫使熔体流动平衡 确定浇口数 控制熔体流动方式 浇口布局
浇口设计
浇口设计准则
确定浇口数
浇口数主要由熔体充模压 力决定,不考虑流道时充 模压力应低于设备额定压 力的一半
可行区:充模压力高 于额定注射压力的 50% (流长过长导 致) ,其他参数均 未超过设定范围
推荐区:充模压力低 于额定注射压力的 50%(70MPa),其 他参数包括剪切应力、 剪切速率、前沿温度 和锁模力都在规定范 围内
浇口设计
Moldflow在浇口设计中的应用示例
充模流动方式
平坦而单向推进的流动前沿
浇口
浇口设计对制件质量和批量生产具有极其重要的作 用,包括浇口类型、浇口尺寸及浇口位置
单点浇口和多点浇口
一般一个模腔最好一个浇口 多浇口可降低熔体充模压力或达到预期的充模方式
浇口设计
浇口设计概述
浇口尺寸 浇口位置
浇口截面小于制件/流 道截面,便于浇口去 除并减小断痕
浇口位置影响熔体流 动形态,借助MF可在 设计约束范围内确定 最佳浇口位置
是熔体流动充模的控制器 浇注系统设计非常关键
流动平衡
各模腔或模腔各末端的充填时间和压力相等 多模腔或多浇口模腔内的熔体流动越平衡,制件质
量越好,也越容易成型 必须同时考虑流道系统及模腔内的流动平衡 流道系统的流动平衡通过浇注系统设计来实现
浇注系统设计
浇注系统设计原则
流动控制
浇口——低劣的熔体流动控制器
厚h为0.4mm~6.4mm 宽度W为1.6mm~12.7mm
浇口设计
浇口类型
手工去浇类浇口
扇形浇口
扇形浇口:边缘宽大,厚度逐 渐变薄 允许熔体快速充模 可减缓熔体对易折、易弯型芯 的冲击 可获得均匀且单向推进的流动, 从而减少翘曲和提高尺寸稳定 性
浇口末端熔体流速恒定 熔体在浇口整个宽度上平衡流 动 浇口宽度方向上压力一致
厚度h约为0.8mm~4.8mm 宽度为1.6mm~6.4mm
浇口设计
浇口类型
手工去浇类浇口
薄膜浇口
相当于扇形浇口的简化 版,不能获得平坦的熔 体流动前沿
薄膜浇口:由直流道、 熔体分配流道和浇口面 组成;熔体分配流道长 与制件进胶尺寸相当
常用于注射丙烯酸制品 和翘曲度要求很高的平 板制品
厚度h约为0.25mm~0.63mm 长L为0.63mm
浇口冻结时间
浇口冻结时间对模腔保压的影响最大 浇口截面过大,浇口冻结时间大大长于制件冻结时
间,成型周期过长 若保压压力释放时浇口尚未冻结,则制件中未冻结
的熔体可能倒流回流道,近浇口缩痕明显 避免熔体倒流是设计浇口冻结时间的前提
浇口设计
Moldflow在浇口设计中的应用示例
浇口位置
熔体单向流动,减少 或缩短了熔接线
流长近1050mm,所 需充模压力过高
流长缩短至900 mm, 所需充模压力降低
熔体大部分单向流动, 初期辐射状流动区较大
流长缩短至800mm 熔体单向流动较好
产生了较多的熔接线
浇口设计
Moldflow在浇口设计中的应用示例
成型窗口
不可行区:充模压力 高于额定注射压力的 80%(流长过长导致)
边缘浇口/侧浇口长度越短越好,以降低过大的压降 典型长度为0.5mm-1.5mm
浇口厚度
一般浇口厚度为近浇口处制件壁厚的50%-80%,手动 去除的可达100%,自动去除的应小于80%
潜伏浇口直径一般为0.5mm-2.5mm 借助MF,可由材料的许可剪切速率来精确定义浇口
尺寸
浇口设计
浇口设计准则
浇口设计
浇口设计准则
浇口布局
在浇口数和控制流动方式不能兼顾时,哪方面对实 现充模平衡更重要
在厚壁区设置浇口,以利于保压 远离薄壁区,以免迟滞 正对模壁或型芯,以免喷射 调整多浇口位置,防止熔接痕出现在制件薄弱位置
或可见位置 增加浇口,以消除或降低过保压 模具是两板/三板 浇注系统是冷/热流道或二者的复合
浇口设计
Moldflow在浇口设计中的应用示例
根据剪切速率优化浇口尺寸
制件厚度3mm,浇口初始厚 2mm,宽4mm。 浇口内最大剪切速率60 000s1,超出材料允许极限值50
000s-1
浇口宽度调整到8mm,浇口 内的最大剪切速率降至约25 000s-1,低于材料允许极限值
50 000s-1
流经浇口的熔体剪切速率可能 比材料许用极限剪切速率还大
浇口直径为0.25mm~1.6mm
浇口设计
浇口类型
自动去浇类浇口
潜伏式浇口
潜伏式浇口:又称隧道式浇口 或剪切式浇口,用于两板模
可设在制件侧壁或较大顶杆侧, 顶出时自动切断 浇口直径为相连处产品厚度的 25%~74%(0.25mm~2mm)
厚度h约为1mm 宽度W一般大于25mm,甚至 可超过750mm,通常与制件进 胶部位尺寸一致
浇口设计
浇口类型
手工去浇类浇口
盘浇口
盘浇口:隔膜式浇 口,常用于圆筒状 或圆环状制件,能 均匀地将熔体前沿 分配给模腔
制件特点: 具有较大内径,对 内、外表面的同轴 度要求很严格,且 不允许出现熔接痕
有时需增加浇口以平衡熔 体充模
增加浇口后各浇口的子 模塑区的压力降应相等、 体积相近; 熔接线置于不敏感处; 避免迟滞、潜流现象
过保压引发 翘曲
浇口设计
浇口设计准则
控制熔体流动方式
熔体前沿推进越平稳越均匀越好,最 理想的是熔体前沿以单向流动方式充 满整个模腔
多浇口需要平衡的流道系统,在给定 压力下,使熔体以相同的体积通过每 个浇口进入模腔
浇口设计
浇口设计准则
浇口布局
增设浇口以降低充模压力
若充模压力过高(不考虑流 道,压力超过70MPa),则 需调整浇口位置或增设浇口 以缩短流长
多浇口布局应能让 所有浇口输送的熔 体体积相当、流长 相近、流动平衡, 以较好地降低充模 压力
浇口设计
浇口设计准则
浇口布局
增设浇口以避免过保压
浇口设计
浇口设计准则
浇口布局
平衡浇口位置
流动平衡: 熔体在同一压力、同一时间 到达模腔的各个末端
一端进胶:单向流动 分子或纤维沿制件轴向分布,可 减少翘曲 熔体流长长,所需充填压力高; 恒定保压力下,体积收缩变化大, 需优化保压曲线
中心进胶:适于圆形/方形制件
在宽度方向存在一定程度的潜流, 存在某种程度的翘曲
浇口处熔体流动的压力降由传热控制,工艺条件的微小变 化会给熔体充模流动方式带来很大改变
浇口处易发生迟滞现象 浇口处熔体流动不稳定,会形成很大的压力降 浇口的加工误差和摩擦磨损对流经浇口的熔体压力降影响
极大 通过浇口调整来实现的流动平衡,成型窗口很小,其流动
平衡极易被工艺参数的微小波动破坏
浇注系统设计
根据制件特点增设浇口来提 高熔体充模流动的均匀性, 从而改善制件的保压状况, 避免过保压
中间单浇口,充 填基本平衡,但 中间筋板过保压, 中部与两端体积 收缩相差过大, 导致制件翘曲
两侧两浇口,中 间筋板最后充填, 避免了过保压, 体积收缩分布均 匀多了
浇口设计
浇口设计准则
其他与浇口设置有关的问题
浇口厚度一般为制件 壁厚的2/3 浇口厚度可用来控制 保压时间
浇口截面较大,可降 低流速及剪切热,允 许更长时间保压,从 而获得更好外观、更 低内应力及更好的尺 寸稳定性。
浇口设计
浇口类型
手工去浇类浇口
浇口截面尺寸过大,开模动作无法剪断浇口 剪应力敏感的材料,不宜采用具有高剪切速率的自
动去浇口结构 获取自动去浇类浇口无法获得的纤维或分子取向 浇口形式有:直浇口、护耳浇口、边缘浇口、重叠
浇口设计
浇口类型
自动去浇类浇口
利用开模或顶出动作自动折断或剪断,避免人工去 除