浇注系统的计算
浇注系统的设计与计算
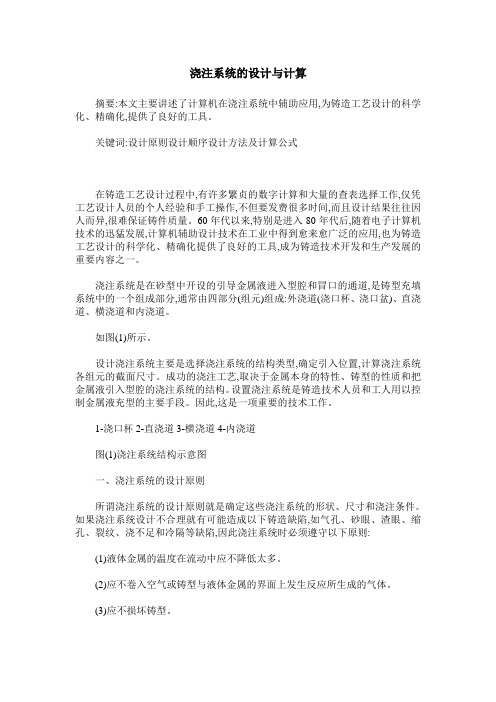
浇注系统的设计与计算摘要:本文主要讲述了计算机在浇注系统中辅助应用,为铸造工艺设计的科学化、精确化,提供了良好的工具。
关键词:设计原则设计顺序设计方法及计算公式在铸造工艺设计过程中,有许多繁贞的数字计算和大量的查表选择工作,仅凭工艺设计人员的个人经验和手工操作,不但要发费很多时间,而且设计结果往往因人而异,很难保证铸件质量。
60年代以来,特别是进入80年代后,随着电子计算机技术的迅猛发展,计算机辅助设计技术在工业中得到愈来愈广泛的应用,也为铸造工艺设计的科学化、精确化提供了良好的工具,成为铸造技术开发和生产发展的重要内容之一。
浇注系统是在砂型中开设的引导金属液进入型腔和冒口的通道,是铸型充填系统中的一个组成部分,通常由四部分(组元)组成:外浇道(浇口杯、浇口盆)、直浇道、横浇道和内浇道。
如图(1)所示。
设计浇注系统主要是选择浇注系统的结构类型,确定引入位置,计算浇注系统各组元的截面尺寸。
成功的浇注工艺,取决于金属本身的特性、铸型的性质和把金属液引入型腔的浇注系统的结构。
设置浇注系统是铸造技术人员和工人用以控制金属液充型的主要手段。
因此,这是一项重要的技术工作。
1-浇口杯2-直浇道3-横浇道4-内浇道图(1)浇注系统结构示意图一、浇注系统的设计原则所谓浇注系统的设计原则就是确定这些浇注系统的形状、尺寸和浇注条件。
如果浇注系统设计不合理就有可能造成以下铸造缺陷,如气孔、砂眼、渣眼、缩孔、裂纹、浇不足和冷隔等缺陷,因此浇注系统时必须遵守以下原则:(1)液体金属的温度在流动中应不降低太多。
(2)应不卷入空气或铸型与液体金属的界面上发生反应所生成的气体。
(3)应不损坏铸型。
(4)应防止掉砂和熔渣流入型腔。
(5)应防止液体金属过度加热铸型。
(6)应有助于方向性凝固。
(7)应不降低工艺出口率(型腔体积对包括浇注系统在内的整铸型型腔体积之比)。
(8)凝固以后应该容易去除。
二、浇注系统设计顺序不同的铸造方法、工厂、技术人员可能采用不同的浇注系统设计方法。
浇注系统的计算
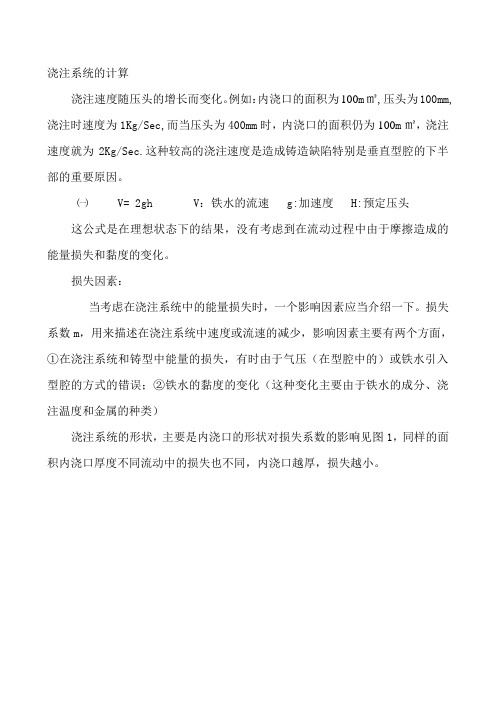
浇注系统的计算浇注速度随压头的增长而变化。
例如:内浇口的面积为100m㎡,压头为100mm,浇注时速度为1Kg/Sec,而当压头为400mm时,内浇口的面积仍为100m㎡,浇注速度就为2Kg/Sec.这种较高的浇注速度是造成铸造缺陷特别是垂直型腔的下半部的重要原因。
㈠ V= 2gh V:铁水的流速 g:加速度 H:预定压头这公式是在理想状态下的结果,没有考虑到在流动过程中由于摩擦造成的能量损失和黏度的变化。
损失因素:当考虑在浇注系统中的能量损失时,一个影响因素应当介绍一下。
损失系数m,用来描述在浇注系统中速度或流速的减少,影响因素主要有两个方面,①在浇注系统和铸型中能量的损失,有时由于气压(在型腔中的)或铁水引入型腔的方式的错误;②铁水的黏度的变化(这种变化主要由于铁水的成分、浇注温度和金属的种类)浇注系统的形状,主要是内浇口的形状对损失系数的影响见图1,同样的面积内浇口厚度不同流动中的损失也不同,内浇口越厚,损失越小。
损失系数m是一个典型的经验数据,可以预定一用于浇注系统的计算,预定的m在以后的流动实验中将被修正。
当考虑到m时公式㈠将被修正为:V=m 2gH ㈡流速 W 的概念是指在一段时间内经过浇道的铁水的公斤重量。
ω= G/T ㈢ω也可以表达为 W= ρ * F * V V 流过浇道的速度F 浇道的截面积G/T= ρ * F* VF=------------------------ 对于铁水:ρ=6.89*10 Kg/mm g =9810 mm/SecF= 1036*G/T*m* H ㈣只有对于理想运动状态才没有损失,在任何真实运动中都存在损失系数是0---1之间的分数,损失系数越大损失越小。
在水力系统中,如浇注系统中存在损失,由损失系数来表示,表 1 给出了不同损失系数的流动损失(在浇注系统中):m 0.9 0.8 0.7 0.6 0.5 0.4 0.3 0.2% 11 25 43 67 100 150 233 400 占无摩擦流动的百分比1/9 2/8 3/7 4/6 5/5 6/4 7/3 8/22.金属液在浇注系统中的流动:静态的流层、平稳的流动只能在以下条件下实现。
第三章 浇注系统的设计与计算(2)

2、冒口种类
冒口种类
普通冒口
顶冒口、暗冒口 侧冒口
特种冒口
大气压力冒口 发热冒口 保温冒口
铸铁件的 实用冒口
浇注系统当冒口 控制压力冒口
3、冒口形状
球形 圆柱形(带斜度) 球顶圆柱形 腰圆柱形 暗腰圆柱形
4、冒口形式 a)铸钢件 明边冒口 b)铸铁件 暗边冒口
5、冒口位置
1、铸件热节上方或侧旁; 2、铸件最高最厚部位; 3、一个冒口同时补缩几
Hp = Ho - C/ 2
间的确定
浇注快慢对铸件质量有重大影响。 浇注时间主要根据合金性质靠生产 经验选择。 球墨铸铁件的浇注时间参照图示曲线查 询。 一般采用快浇。 对于收缩大的合金件,采用慢浇有 利于补缩。
3)流量系数μ的确定
铸铁件流量系数
铸钢件流量系数
球墨铸铁件流量系数
计算步骤:
以内浇道为阻流(最小)截面,用奥赞(Osann)公式
S内
m
2gHp
计算每个内浇道截面积。
式中Hp可用浇口杯中液面到内浇道中心的距离Ho计算。
配套措施: 1)浇口杯应足够大; 2)严格控制浇注时间。
复习题
1.浇注系统由哪些部分组成?分别说明各个组元的 作用?
2.比较顶注式和底注式浇注系统的优缺点。
3.比较封闭式和开放式浇注系统的优缺点。
4 . 如何提高横浇道的撇渣效果?
铸钢冒口的理论依据及工作内容。 4. 何谓铸铁件的均衡凝固技术?有何重要意义? 5. 说明铸铁件实用冒口设计理念和设计计算内容。 6. 说明冷铁和铸肋的作用及应用。
u 防止旋涡,避免吸气或金属过度氧化; u 内浇道的位置和数量符合铸件所需凝固或补
缩原则; u 结构合理,造型简单; u 浇注系统本身消耗金属少。
[精彩]第三章 浇注系统的设计与计算
![[精彩]第三章 浇注系统的设计与计算](https://img.taocdn.com/s3/m/2c43a13b10a6f524ccbf85c8.png)
Department of Materials Engineering
计算
1、 奥赞(Osann)公式 —阻流(最小)截面积的计算 。 阻流(最小)组元指浇注系统中最小截 面积的浇道,一般为内浇道,即
m A阻= 2 gHp
H P H0 P
2
2C
湖北汽车工业学院材料工程系 Department of Materials Engineering
轻合金浇注系统中安装过滤网
湖北汽车工业学院材料工程系 Department of Materials Engineering
4、内浇道的设计
1) 内浇道的作用: 控制液态金属充型速度和流动方向、温度分布和凝固顺序。 2) 形状:扁平梯形、月牙形和三角形。 3) 位置的选择: 依据铸件所需凝固方式和流动特性考虑。 同时凝固: 对于壁厚均匀的铸件,拟采用多个内浇道分散引入; 对于不均匀的铸件,则从薄壁处引入。 顺序凝固: 从厚壁处引入金属液。
湖北汽车工业学院材料工程系 Department of Materials Engineering
5、确定内浇道位置的几个具体问题
结构复杂的铸件,壁厚差别大的补缩区域则按顺 序凝固从厚处引入;整个铸件按同时凝固方式采 用多个内浇道充型。 要求各内浇道的流量分布合理。 液流顺壁流入,不冲刷 型壁、型芯和铸型凸出部分。 避开铸件重要部位, 防止晶粒粗大。 造型、清理操作方便, 不阻碍铸件收缩。 湖北汽车工业学院材料工程系
(二)按浇注系统各组元截面积的比例关系分
1、封闭式浇注系统
∑A内< ∑A横<A直
一般为 ∑A内:∑A横:A直=1:1.1:1.15
特点:
挡渣力强,金属消耗少,易清理;
浇注系统浇口尺寸计算

浇注系统相关尺寸计算
浇口的平衡例题
解:由排列位置知2A2B4A4B相同,3A3B5A5B相同,1A1B相同, 因此只需求1A2A3A尺寸即可。先求2A尺寸,并以此为基准求2A3A 的尺寸。 2 2
d 5.08 1)分流道圆形截面积 AR :AR R mm 2 20.27 mm 2 2 2
2)基准浇口2A的截面尺寸: 由:AG 2 0.07 AR 1.42 mm2 得:t2 0.69mm, b2 3t2 2.07mm 3)求其他两组浇口的截面尺寸,由BGV相等得:
AG1 AG3 1.42 BGV 0.08 102 102 102 1.27 2 143 1.27 143 1.27 2 2 2
浇注系统相关尺寸计算
④点浇口 又称针点浇口或橄榄形浇口,是一种在塑件中央开设浇口时使 用的圆形限制性浇口,用于成型壳类、盒类的热塑性塑件。
优点: 浇口残留痕迹小,易取 得浇注系统的平衡,也利于 自动化操作。 缺点: 在模具结构上需增加一个 分型面,即双分型面,以便 浇口凝料取出。
浇注系统相关尺寸计算
浇注系统相关尺寸计算
浇口的平衡例题
由上式可得:
AG1 3t1 0.73mm2 , t1 0.49mm, b1 3t1 1.47 mm
2
AG3 3t3 1.87 mm2 , t 3 0.79mm, b3 3t3 2.37mm
2
计算结果:
1A/1B 型腔号、 尺寸
浇注系统相关尺寸计算
浇口的尺寸一般根据经验确定,截面积为分流道断面积的 3%~9%,截面形状常为矩形或圆形,浇口的长度为1~1.5mm。
注意: 在设计浇口时,往往先取较小的尺寸值,以便在试模时 逐步加以修正。
浇注系统的计算

铸造业常用的浇注系统的计算方法:根据流体力学的百努利方程式可以导出如下的浇注系统的液流式子:v= G/(γ*F*t)= μ*√(2*g*H) ------------------------------------(1)其中:v 流速单位cm/s (计算时可以按最小截面积的流速)G 铸件质量(重量)单位kgF 截面积单位cm2 (计算时可以按最小截面积)t 浇注时间单位sg 重力加速度981cm/s2H 平均压力头单位cm (取值计算见后)γ金属液体的密度单位kg/cm3μ由铸件壁厚和结构以及浇道等因素引起的金属液体流速损耗系数,复杂铸件可取为0.34由(1)式,得F=G/(γ*t*μ*√(2*g*H)) -----------------------------------------(2)设y=γ*μ*√(2*g)则F=G/(y *t*√H) ---------------------------------------------------(3)此公式的各种变形铸造书中常称作迪台尔公式。
系数y,对特定的金属液和特定类型的铸件(如壁厚等)和特定的生产工艺,可视为常数,具体数值可从试验中,通过记录浇注时间反求y的平均值作为今后计算的常数。
如,一拖一铁厂的原二线为0.18—0.22 原三四线为0.13 原一线为0.15—0.16现在的KW线,由于砂型的紧实度特高,y=0.04左右平均压头H的取值:顶注为H=h底注为H=h-c/2从铸件中间浇注为H=h-c/4其中h为浇口杯平面到内浇口的高度,c为铸件的高度。
公式推导从略,见有关的书籍。
以上计算出的是浇注系统的最小截面积。
在不同类型的浇注系统中,最小截面积的位置是不同的。
封闭式浇注系统的最小截面积是内浇口,开放式浇注系统的最小截面积是直浇口,最常用的半封闭式浇注系统的最小截面积是阻流段。
现将半封闭式浇注系统的各段截面积之比推荐如下:F直:F阻;F横:F内=1.3:1:2:1.5 根据不同情况,比例有较大的取值范围,原则不变的前提下可以灵活运用。
熔模铸造浇注系统计算
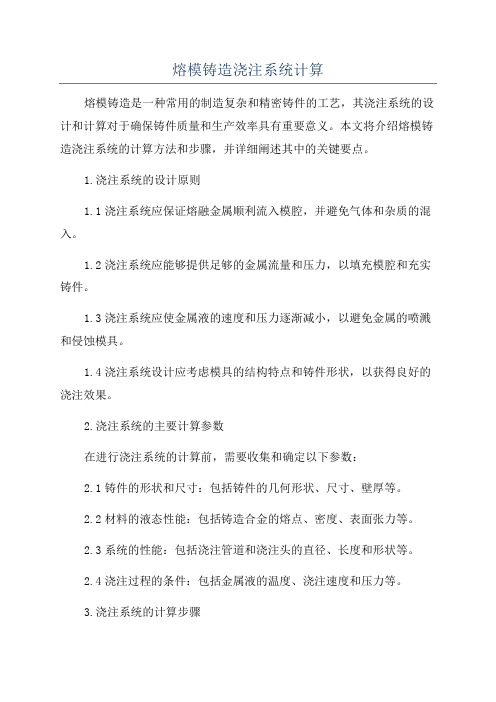
熔模铸造浇注系统计算熔模铸造是一种常用的制造复杂和精密铸件的工艺,其浇注系统的设计和计算对于确保铸件质量和生产效率具有重要意义。
本文将介绍熔模铸造浇注系统的计算方法和步骤,并详细阐述其中的关键要点。
1.浇注系统的设计原则1.1浇注系统应保证熔融金属顺利流入模腔,并避免气体和杂质的混入。
1.2浇注系统应能够提供足够的金属流量和压力,以填充模腔和充实铸件。
1.3浇注系统应使金属液的速度和压力逐渐减小,以避免金属的喷溅和侵蚀模具。
1.4浇注系统设计应考虑模具的结构特点和铸件形状,以获得良好的浇注效果。
2.浇注系统的主要计算参数在进行浇注系统的计算前,需要收集和确定以下参数:2.1铸件的形状和尺寸:包括铸件的几何形状、尺寸、壁厚等。
2.2材料的液态性能:包括铸造合金的熔点、密度、表面张力等。
2.3系统的性能:包括浇注管道和浇注头的直径、长度和形状等。
2.4浇注过程的条件:包括金属液的温度、浇注速度和压力等。
3.浇注系统的计算步骤根据以上参数和原则,进行浇注系统的计算,一般可分为以下几个步骤:3.1确定浇注管道和浇注头的几何参数:根据铸件的形状和尺寸,确定浇注管道和浇注头的直径、长度和形状。
通常,浇注管道和浇注头的直径会逐渐减小,以保证金属液的速度和压力逐渐降低。
3.2计算浇注头的流速和压力:根据材料的液态性能和浇注过程的条件,计算金属液在浇注头中的流速和压力。
这一步需要考虑金属液的粘度、密度以及浇注头的形状、长度等参数。
3.3计算浇注管道和浇注头的阻力:根据浇注管道和浇注头的形状和尺寸,计算流动的阻力。
这一步需要考虑流动的雷诺数、曼宁系数和摩擦因数等参数。
3.4确定浇注时间和浇注压力:根据铸件的尺寸和形状,计算金属液的流速和浇注时间,进而确定浇注压力。
通常,浇注时间应保证金属液充分填充模腔,并保持一定的冲刷效果。
4.浇注系统的优化完成上述计算后,可以进行浇注系统的优化,包括以下几个方面:4.1浇注管道的优化:可以通过改变浇注管道的形状和尺寸,减小阻力和压力损失,提高浇注效率。
浇注系统设计
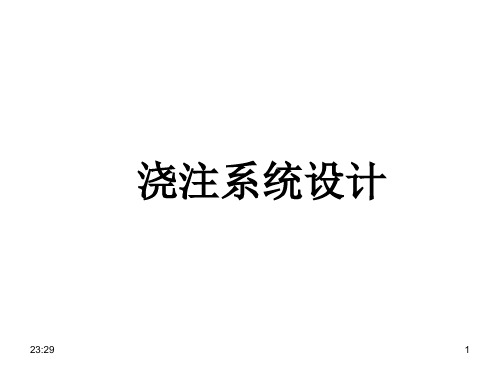
23:29
38
• C)根据标准冒口形状,从圆柱形冒口中 选择与计算值最接近且大于计算值的冒 口。MR=0.84(6#)符合条件:
MR ≥0.79cm
23:29
39
• d) 冒口直径为:DR=45mm • e)冒口径的横截面积计算如下:
冒口径直径: DN>1/3DR=45/3=15mm 冒口径的面积(为圆形)
34
冒口计算范例
• 为更好的说明冒口计算,此处以球铁的 万向节冒口设计为例。很显然圆柱支柱 是铸件最紧实部分,这部分冷却最慢, 凝固最晚,因此在金属收缩时需要金属 补缩。模板的布置图如下:冒口放置在
圆柱的顶部,以便(1)获得顺序凝固
(2)补缩时借助重 力
23:29
35
如图:
冒口计算范例
35mm
80mm
45
铸造常见的几种缺陷
23:29
1.冷隔 2.砂渣眼 3.掉砂 4.粘板 5.押入
6.错模 7.粘砂 8.气孔 9.缩孔 10.打联
46
分析对铸件缺陷产生原因
1.浇注系统
a)因浇道位置引起的铸件缺陷。 b)因浇道形状引起的铸件缺陷。 c)因浇道面积引起的铸件缺陷。
2.因机器参数设置引起的缺陷
23:29
4. 冒口与铸件如何连接(冒口径) 冒口径的形状设计必须能保证冒口与铸
件间通道始终畅通,金属液以最佳的方式 对铸件进行补缩。
23:29
26
冒口有两种类型的收缩
1.表面缩孔。 2.内部缩松。 改善内部的缩松对策:
a.提高CE值 b.增加砂型强度 c.使用冷铁 d.顺序凝固 e.减少孕育用量 f.铁液净化 g.镁残留量趋进0.035
23:29
- 1、下载文档前请自行甄别文档内容的完整性,平台不提供额外的编辑、内容补充、找答案等附加服务。
- 2、"仅部分预览"的文档,不可在线预览部分如存在完整性等问题,可反馈申请退款(可完整预览的文档不适用该条件!)。
- 3、如文档侵犯您的权益,请联系客服反馈,我们会尽快为您处理(人工客服工作时间:9:00-18:30)。
浇注系统的计算
浇注速度随压头的增长而变化。
例如:内浇口的面积为100m㎡,压头为100mm,浇注时速度为1Kg/Sec,而当压头为400mm时,内浇口的面积仍为100m㎡,浇注速度就为2Kg/Sec.这种较高的浇注速度是造成铸造缺陷特别是垂直型腔的下半部的重要原因。
㈠ V= 2gh V:铁水的流速 g:加速度 H:预定压头
这公式是在理想状态下的结果,没有考虑到在流动过程中由于摩擦造成的能量损失和黏度的变化。
损失因素:
当考虑在浇注系统中的能量损失时,一个影响因素应当介绍一下。
损失系数m,用来描述在浇注系统中速度或流速的减少,影响因素主要有两个方面,①在浇注系统和铸型中能量的损失,有时由于气压(在型腔中的)或铁水引入型腔的方式的错误;②铁水的黏度的变化(这种变化主要由于铁水的成分、浇注温度和金属的种类)
浇注系统的形状,主要是内浇口的形状对损失系数的影响见图1,同样的面积内浇口厚度不同流动中的损失也不同,内浇口越厚,损失越小。
损失系数m是一个典型的经验数据,可以预定一用于浇注系统的计算,预
定的m在以后的流动实验中将被修正。
当考虑到m时公式㈠将被修正为:V=m 2gH ㈡
流速 W 的概念是指在一段时间内经过浇道的铁水的公斤重量。
ω= G/T ㈢
ω也可以表达为 W= ρ * F * V V 流过浇道的速度
F 浇道的截面积
G/T= ρ * F* V
F=------------------------ 对于铁水:ρ=6.89*10 Kg/mm g =9810 mm/Sec
F= 1036*G/T*m* H ㈣
只有对于理想运动状态才没有损失,在任何真实运动中都存在损失系数是
0---1之间的分数,损失系数越大损失越小。
在水力系统中,如浇注系统中存在
损失,由损失系数来表示,表 1 给出了不同损失系数的流动损失(在浇注
系统中):
m 0.9 0.8 0.7 0.6 0.5 0.4 0.3 0.2
% 11 25 43 67 100 150 233 400 占无摩擦流动的百分比
1/9 2/8 3/7 4/6 5/5 6/4 7/3 8/2
2.金属液在浇注系统中的流动:
静态的流层、平稳的流动只能在以下条件下实现。
ⅰ、系统被液态所填满,没有气体的充填。
静压头高度是固定的(铁水高
度在浇口杯中不变):
为得到连续的铁水的流动,浇道和内浇口面积的相关计算必须以保证浇道迅速被充满,铁水能够同时进入各型腔。
浇道过大造成下部型腔先进铁水,可造成的缺陷有:
a.气孔缺陷:在型腔中产生的气体被紊流带进浇注系统流入型腔。
b.夹砂缺陷:紊流的铁水可以冲掉砂粒并把他们带入型腔。
c.夹渣缺陷:在铁水中产生的渣滓不能上升到铁水的表面(升到浇口
杯中),由于铁水的流管是不连续的。
d.模型的全部浇注时间将会比同时进入型腔的时间长,这将会引起由
于热作用于模型时间过长而造成的铸造缺陷;由于过长的浇注时间
超过了造型的周期时间,生产率将会降低。
ⅱ.当浇道和内浇口面积减小后,浇注系统可以迅速的被充满,从而形成了这些情况:
a.迅速形成预设的静压头 H1、H2、H3,从而使铁液连续的、迅速的、
无阻碍的流动。
b.几乎同时充满型腔,从而是最短的浇注时间。
ⅲ. 由于内浇口过小,虽然可以同时充填型腔,但也会造成浇不足现象而引起铸造缺陷。
造成这种现象的原因是通过内浇口的流速太小,换句话说内浇口与浇道截面积和型腔体积的不协调。
这种情况可以造成以下缺陷:
a.浇不足。
b.铸件冷隔(浇注工通常使铁水面保持在较低的水平,然后充满浇
口杯。
c.铸件的夹渣、夹砂缺陷(杂质如砂、渣,当连续浇注时上升到上
部,如果突然断流或液面下降,杂质将被压在铸型中)。
3. 充填型腔的次序:
不正确的充型顺序是大多数情况下造成铸造缺陷的原因。
不合理的浇冒口设计会造成不同时的充填各个型腔,这样不但会造成浇注时间过长和生产率下降,也会造成废品率的大幅上升。
从而可以得出这样的结论,不只是内浇口的截面积对合适的充填系统是重要的,内浇口与浇道面积的合理比例也是一项具有重大意义的因素。
换句话说,内浇口的面积与各自的静压头是相匹配的,但充填的方式仍可不正确(当静压头还未形成时),如果浇道还未充满,在内浇口处的静压头与预设的完全不同了。
所以应必要的调整浇道的尺寸以尽快充满浇道。
调整浇注系统的结果将使实际的浇注顺序更接近于同时充型,浇注系统的充满时间和浇注时间尽可能的短。
4. 观察充型的顺序
5.标准浇注计算图表
迪砂介绍了计算浇注系统的标准图表给出结合公式㈣的相关因素,提供了相对容易的决定内浇口和浇道面积的方法。
为了使用图表需要知道的因素有:
a. 各铸件的重量 G (Kg)
b. 充满个别型腔需要的时间 T (Sec)
c. 损失系数 m
d. 铁水静压头 H (mm)
6. 铸件的重量
铸件的重量是一个典型因素在图表中,当要使用冒口时,冒口作为铸
件的一部分,冒口颈的截面积由别的原则决定。
有些时候两铸件公用一个冒口,在这种情况下,两铸件和冒口的总重量将用于确定相关铸件之上的截面积,最后对于整个分支的铁水提供的浇道的截面积用整个分支的总重量决定。
总而言知浇道的截面积是由浇注过程中流经这个截面的总的金属重量来决定的。
7. 浇注时间:当选择浇注时间时,下列因素应在考虑之中:
a. 整个浇注时间T2是流满各型腔的时间T和充满浇注系统所用的时间
T1的总和。
b. 最大的浇注时间必须小于造型周期(设备周期)t.
c. 设备的工作周期 t2 是造型周期 t 和模型传送带运输时间 t1
在浇注后运输一般为 2—3 Sec
d. T2一般来说越短越好,应比 t 短。
根据浇注系统设计和铸件类型,浇注系统的充满时间一般在1—3 Sec之间,充满型腔的最长时间由机器的类型和所需生产率决定。
以上主要表示如下:
T + T1 < 3600/P (Sec) T + T1 < t
8. 压力头
压力头由内浇口中心线到浇口杯中液面高度的距离决定。
冒口技术
一个合理的冒口工艺可提供以下好处:
更好的铸件质量
模型高的利用率
减少熔炼损失
更高的模板利用率
铸件的磨修减少
这是因为一套设计良好的冒口系统配合一套合理的浇注系统,在大多数情况下可明显减少必须的浇口数量和尺寸。
1.缩松的产生
液态金属由浇注时的温度冷却到室温,将会发生三个阶段的收缩过程
a.由浇注温度到早期凝固温度
b.由液态到固态区域
c.由凝固结束到室温
缩松的产生在图(32)中说明
当图(32)中的铸件在 T1的浇注温度下被浇注高度达到 A1时,液态金属开始收缩(液态收缩),当达到凝固温度 T2 时,铸件液面高度已降至 A L 。
下一步金属紧靠型腔收缩(因为热量大部分是在这里散发出的)和铸件向内的凝固,但是因为固态金属比液态金属重,在凝固过程中会有进一步的收缩,最后固态金属在冷却到室温的过程中发生收缩,铸件轻微离开型壁 A S的距离。
如果我们认为在整个凝固过程中没有复加的液体进入型腔,在凝固的早期铸件的表面层与型壁紧密结合,金属的收缩导致了没有足够的铁水去填充模型
空间,从而导致了缩松的产生。
这里有两种缩松的种类:
a.微观缩松:在凝固过程中发生在从熔体中沉淀下来的枝晶的间隙中。
在树枝晶包围下的熔体的不到其余熔体的补充,从而在收缩和凝固过
程中产生了微观缩松,缩松的形状与枝晶形状相对应,这种缩松常发
生在结晶区间大的合金中(T1—T2)。
微观缩松是不容易用冒口方式消
除的。
b.宏观缩松:指在铸件上大的孔洞(有时也表现为铸件表面的下陷),
一般发生在最后凝固和冷却最慢的部位,出现在热节部位,宏观缩松
通过铸件的凝固过程和冷却速度的控制来消除,使缩孔发生在铸件以
外的冒口部分。
基本原则。