浇注系统的计算和设计
第七章浇注系统设计

3.3 浇注系统最小断面尺寸的计算
①Osann(奥赞)公式
• 设单位时间内流经内浇道 金属液的体积为Qm3/s, 则
Q=F内v内 F内-内浇道断面积 m2; v内-内浇道口的平均流速 m/s,可由伯努里方程得 到;
•由伯努里方程可得
2 P外-p内 v外 v内 2 g H 0 h 2g
直浇道的结构设计
• 直浇道与横浇道的连接 要 增设直浇道窝的结构防止 冲砂和卷气,使金属液的 紊乱程度降低。窝座的直 径一般为横浇道宽的2倍左 右面,最好接近横浇道的 高度,直浇道与横浇道的 连接也应做成圆角。
直浇道窝
• 直浇道窝的作用:减小金属液的紊流和对 铸型的冲蚀作用,减小局部阻力和压头损 失,有利于渣、气与金属液分离并上浮。 • 湿型砂强度低,必要时可在直浇道底放一 干芯片(或耐火砖片)以承受金属液的冲 击。
•封闭-开放式浇注系统
• 控制流量的阻流断面位于直浇道下端,或在 横浇道中,或者在集渣包出口处等。 • 这类浇注系统在阻流之前是封闭的,可起挡 渣作用;其后开放,可使充型平稳。兼有开 放式和封闭式浇注系统的优点,一般用于小 型铸铁件和铝合金浇注,特别是在一箱多铸 小件时应用,这种浇注系统结构复杂,浇道 模样制造以及造型费事,多用于手工造型。
第七章
浇注系统设计
7.1 概述
浇注系统的功能
• 使液态合金平稳充满砂型; • 阻挡夹杂物进入型腔,以免形成渣孔; • 调节铸型与铸件各部分的温度分布以控制铸件的凝固 顺序; • 起一定的补缩作用,在内浇道凝固前补给部分液态收 缩; • 让液态合金以最短的距离,最合适的时间充满型腔, 有足够的压力头,并保证金属液面在型腔内有必要的 上升速度等,以确保铸件的质量; • 充型流股不要正对冷铁和芯撑; • 合理的浇注系统应能节约金属,有利于减少冒口的体 积。 • 结构简单紧凑,利于提高铸型面积的利用率,便于造 型和从铸件上清除。
浇注系统的设计与计算
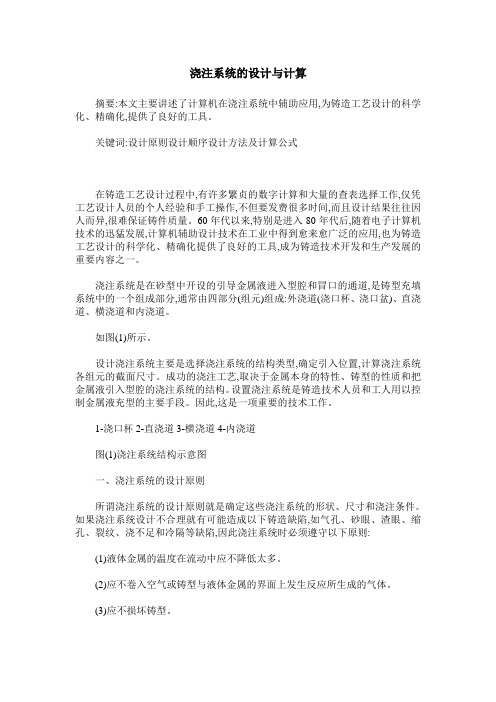
浇注系统的设计与计算摘要:本文主要讲述了计算机在浇注系统中辅助应用,为铸造工艺设计的科学化、精确化,提供了良好的工具。
关键词:设计原则设计顺序设计方法及计算公式在铸造工艺设计过程中,有许多繁贞的数字计算和大量的查表选择工作,仅凭工艺设计人员的个人经验和手工操作,不但要发费很多时间,而且设计结果往往因人而异,很难保证铸件质量。
60年代以来,特别是进入80年代后,随着电子计算机技术的迅猛发展,计算机辅助设计技术在工业中得到愈来愈广泛的应用,也为铸造工艺设计的科学化、精确化提供了良好的工具,成为铸造技术开发和生产发展的重要内容之一。
浇注系统是在砂型中开设的引导金属液进入型腔和冒口的通道,是铸型充填系统中的一个组成部分,通常由四部分(组元)组成:外浇道(浇口杯、浇口盆)、直浇道、横浇道和内浇道。
如图(1)所示。
设计浇注系统主要是选择浇注系统的结构类型,确定引入位置,计算浇注系统各组元的截面尺寸。
成功的浇注工艺,取决于金属本身的特性、铸型的性质和把金属液引入型腔的浇注系统的结构。
设置浇注系统是铸造技术人员和工人用以控制金属液充型的主要手段。
因此,这是一项重要的技术工作。
1-浇口杯2-直浇道3-横浇道4-内浇道图(1)浇注系统结构示意图一、浇注系统的设计原则所谓浇注系统的设计原则就是确定这些浇注系统的形状、尺寸和浇注条件。
如果浇注系统设计不合理就有可能造成以下铸造缺陷,如气孔、砂眼、渣眼、缩孔、裂纹、浇不足和冷隔等缺陷,因此浇注系统时必须遵守以下原则:(1)液体金属的温度在流动中应不降低太多。
(2)应不卷入空气或铸型与液体金属的界面上发生反应所生成的气体。
(3)应不损坏铸型。
(4)应防止掉砂和熔渣流入型腔。
(5)应防止液体金属过度加热铸型。
(6)应有助于方向性凝固。
(7)应不降低工艺出口率(型腔体积对包括浇注系统在内的整铸型型腔体积之比)。
(8)凝固以后应该容易去除。
二、浇注系统设计顺序不同的铸造方法、工厂、技术人员可能采用不同的浇注系统设计方法。
第八章 浇注系统设计

Fmin
G 0.0443 H P
用上式计算浇注系统最小截面积时需仔细确定式中各因素的数值。
在计算的铸件确定以后,即已确定。铸件图上一般已标出了铸 件的重量(未标时根据铸件图可估算出铸件重量),再加上浇注系 统和冒口的重量即为G值。
影响µ值的因素很多,难于用数学计算方法确定,一般都按生产 经验和参考实验结果选定。对于航空铝、镁合金铸件所用的扩张式浇 注系统,其µ值可在0.3~0.7之间选取。实际铸造时可根据铸件合金种 类、浇注温度和铸件结构选择。
(1) 应在一定的浇注时间内,保证充满铸型 (2) 应能控制液体金属流入型腔的速度和方向 (3) 应能把混入金属液中的熔渣和气体挡在浇注系统里 (4) 应能控制铸件凝固时的温度分布
(5) 浇注系统结构应力求简单,简化造型,减少清理工作量和 液体金属的消耗。
(1)承接来自浇包的金属液,防止金属液飞溅和溢出,便于浇注;
H
p
P2 H 2C
用上式计算平均静压头有下列三种情况 (1) 采用底注式浇注系统时,因为P=C(图中(a)),所以有: HP=H-C/2 (2) 采用顶注式浇注系统时(图中(b)),因为P=0,所以有: HP=H (3) 采用中注式浇注系统时(图中(c)),HP可用上面的HM的计 算公式来计算。 HP=H-C/8
内浇道流量不均匀现象对铸件质量有显著影响: ① 对大型复杂铸件和薄壁铸件易出现浇不足和冷隔缺陷
② 在流量大的内浇道附近会引起局部过热、破坏原来所 预计的铸件凝固次序,使铸件产生氧化、缩松、缩孔
和裂纹等缺陷。பைடு நூலகம்
为了克服内浇道流量不均匀带来的弊病,通常采用如下方法
(1)尽可能将内浇道设置在横浇道的对称位置; (2)将横浇道断面设计成顺着液流方向逐渐缩小形式; (3)采用不同断面内浇道,缩小远离直浇道的内浇道断两积; (4)设置浇口窝等。
第三章 浇注系统的设计与计算(2)

2、冒口种类
冒口种类
普通冒口
顶冒口、暗冒口 侧冒口
特种冒口
大气压力冒口 发热冒口 保温冒口
铸铁件的 实用冒口
浇注系统当冒口 控制压力冒口
3、冒口形状
球形 圆柱形(带斜度) 球顶圆柱形 腰圆柱形 暗腰圆柱形
4、冒口形式 a)铸钢件 明边冒口 b)铸铁件 暗边冒口
5、冒口位置
1、铸件热节上方或侧旁; 2、铸件最高最厚部位; 3、一个冒口同时补缩几
Hp = Ho - C/ 2
间的确定
浇注快慢对铸件质量有重大影响。 浇注时间主要根据合金性质靠生产 经验选择。 球墨铸铁件的浇注时间参照图示曲线查 询。 一般采用快浇。 对于收缩大的合金件,采用慢浇有 利于补缩。
3)流量系数μ的确定
铸铁件流量系数
铸钢件流量系数
球墨铸铁件流量系数
计算步骤:
以内浇道为阻流(最小)截面,用奥赞(Osann)公式
S内
m
2gHp
计算每个内浇道截面积。
式中Hp可用浇口杯中液面到内浇道中心的距离Ho计算。
配套措施: 1)浇口杯应足够大; 2)严格控制浇注时间。
复习题
1.浇注系统由哪些部分组成?分别说明各个组元的 作用?
2.比较顶注式和底注式浇注系统的优缺点。
3.比较封闭式和开放式浇注系统的优缺点。
4 . 如何提高横浇道的撇渣效果?
铸钢冒口的理论依据及工作内容。 4. 何谓铸铁件的均衡凝固技术?有何重要意义? 5. 说明铸铁件实用冒口设计理念和设计计算内容。 6. 说明冷铁和铸肋的作用及应用。
u 防止旋涡,避免吸气或金属过度氧化; u 内浇道的位置和数量符合铸件所需凝固或补
缩原则; u 结构合理,造型简单; u 浇注系统本身消耗金属少。
[精彩]第三章 浇注系统的设计与计算
![[精彩]第三章 浇注系统的设计与计算](https://img.taocdn.com/s3/m/2c43a13b10a6f524ccbf85c8.png)
Department of Materials Engineering
计算
1、 奥赞(Osann)公式 —阻流(最小)截面积的计算 。 阻流(最小)组元指浇注系统中最小截 面积的浇道,一般为内浇道,即
m A阻= 2 gHp
H P H0 P
2
2C
湖北汽车工业学院材料工程系 Department of Materials Engineering
轻合金浇注系统中安装过滤网
湖北汽车工业学院材料工程系 Department of Materials Engineering
4、内浇道的设计
1) 内浇道的作用: 控制液态金属充型速度和流动方向、温度分布和凝固顺序。 2) 形状:扁平梯形、月牙形和三角形。 3) 位置的选择: 依据铸件所需凝固方式和流动特性考虑。 同时凝固: 对于壁厚均匀的铸件,拟采用多个内浇道分散引入; 对于不均匀的铸件,则从薄壁处引入。 顺序凝固: 从厚壁处引入金属液。
湖北汽车工业学院材料工程系 Department of Materials Engineering
5、确定内浇道位置的几个具体问题
结构复杂的铸件,壁厚差别大的补缩区域则按顺 序凝固从厚处引入;整个铸件按同时凝固方式采 用多个内浇道充型。 要求各内浇道的流量分布合理。 液流顺壁流入,不冲刷 型壁、型芯和铸型凸出部分。 避开铸件重要部位, 防止晶粒粗大。 造型、清理操作方便, 不阻碍铸件收缩。 湖北汽车工业学院材料工程系
(二)按浇注系统各组元截面积的比例关系分
1、封闭式浇注系统
∑A内< ∑A横<A直
一般为 ∑A内:∑A横:A直=1:1.1:1.15
特点:
挡渣力强,金属消耗少,易清理;
浇注系统浇口尺寸计算

浇注系统相关尺寸计算
浇口的平衡例题
解:由排列位置知2A2B4A4B相同,3A3B5A5B相同,1A1B相同, 因此只需求1A2A3A尺寸即可。先求2A尺寸,并以此为基准求2A3A 的尺寸。 2 2
d 5.08 1)分流道圆形截面积 AR :AR R mm 2 20.27 mm 2 2 2
2)基准浇口2A的截面尺寸: 由:AG 2 0.07 AR 1.42 mm2 得:t2 0.69mm, b2 3t2 2.07mm 3)求其他两组浇口的截面尺寸,由BGV相等得:
AG1 AG3 1.42 BGV 0.08 102 102 102 1.27 2 143 1.27 143 1.27 2 2 2
浇注系统相关尺寸计算
④点浇口 又称针点浇口或橄榄形浇口,是一种在塑件中央开设浇口时使 用的圆形限制性浇口,用于成型壳类、盒类的热塑性塑件。
优点: 浇口残留痕迹小,易取 得浇注系统的平衡,也利于 自动化操作。 缺点: 在模具结构上需增加一个 分型面,即双分型面,以便 浇口凝料取出。
浇注系统相关尺寸计算
浇注系统相关尺寸计算
浇口的平衡例题
由上式可得:
AG1 3t1 0.73mm2 , t1 0.49mm, b1 3t1 1.47 mm
2
AG3 3t3 1.87 mm2 , t 3 0.79mm, b3 3t3 2.37mm
2
计算结果:
1A/1B 型腔号、 尺寸
浇注系统相关尺寸计算
浇口的尺寸一般根据经验确定,截面积为分流道断面积的 3%~9%,截面形状常为矩形或圆形,浇口的长度为1~1.5mm。
注意: 在设计浇口时,往往先取较小的尺寸值,以便在试模时 逐步加以修正。
熔模铸造浇注系统计算
熔模铸造浇注系统计算熔模铸造是一种常用的制造复杂和精密铸件的工艺,其浇注系统的设计和计算对于确保铸件质量和生产效率具有重要意义。
本文将介绍熔模铸造浇注系统的计算方法和步骤,并详细阐述其中的关键要点。
1.浇注系统的设计原则1.1浇注系统应保证熔融金属顺利流入模腔,并避免气体和杂质的混入。
1.2浇注系统应能够提供足够的金属流量和压力,以填充模腔和充实铸件。
1.3浇注系统应使金属液的速度和压力逐渐减小,以避免金属的喷溅和侵蚀模具。
1.4浇注系统设计应考虑模具的结构特点和铸件形状,以获得良好的浇注效果。
2.浇注系统的主要计算参数在进行浇注系统的计算前,需要收集和确定以下参数:2.1铸件的形状和尺寸:包括铸件的几何形状、尺寸、壁厚等。
2.2材料的液态性能:包括铸造合金的熔点、密度、表面张力等。
2.3系统的性能:包括浇注管道和浇注头的直径、长度和形状等。
2.4浇注过程的条件:包括金属液的温度、浇注速度和压力等。
3.浇注系统的计算步骤根据以上参数和原则,进行浇注系统的计算,一般可分为以下几个步骤:3.1确定浇注管道和浇注头的几何参数:根据铸件的形状和尺寸,确定浇注管道和浇注头的直径、长度和形状。
通常,浇注管道和浇注头的直径会逐渐减小,以保证金属液的速度和压力逐渐降低。
3.2计算浇注头的流速和压力:根据材料的液态性能和浇注过程的条件,计算金属液在浇注头中的流速和压力。
这一步需要考虑金属液的粘度、密度以及浇注头的形状、长度等参数。
3.3计算浇注管道和浇注头的阻力:根据浇注管道和浇注头的形状和尺寸,计算流动的阻力。
这一步需要考虑流动的雷诺数、曼宁系数和摩擦因数等参数。
3.4确定浇注时间和浇注压力:根据铸件的尺寸和形状,计算金属液的流速和浇注时间,进而确定浇注压力。
通常,浇注时间应保证金属液充分填充模腔,并保持一定的冲刷效果。
4.浇注系统的优化完成上述计算后,可以进行浇注系统的优化,包括以下几个方面:4.1浇注管道的优化:可以通过改变浇注管道的形状和尺寸,减小阻力和压力损失,提高浇注效率。
浇注系统设计
23:29
38
• C)根据标准冒口形状,从圆柱形冒口中 选择与计算值最接近且大于计算值的冒 口。MR=0.84(6#)符合条件:
MR ≥0.79cm
23:29
39
• d) 冒口直径为:DR=45mm • e)冒口径的横截面积计算如下:
冒口径直径: DN>1/3DR=45/3=15mm 冒口径的面积(为圆形)
34
冒口计算范例
• 为更好的说明冒口计算,此处以球铁的 万向节冒口设计为例。很显然圆柱支柱 是铸件最紧实部分,这部分冷却最慢, 凝固最晚,因此在金属收缩时需要金属 补缩。模板的布置图如下:冒口放置在
圆柱的顶部,以便(1)获得顺序凝固
(2)补缩时借助重 力
23:29
35
如图:
冒口计算范例
35mm
80mm
45
铸造常见的几种缺陷
23:29
1.冷隔 2.砂渣眼 3.掉砂 4.粘板 5.押入
6.错模 7.粘砂 8.气孔 9.缩孔 10.打联
46
分析对铸件缺陷产生原因
1.浇注系统
a)因浇道位置引起的铸件缺陷。 b)因浇道形状引起的铸件缺陷。 c)因浇道面积引起的铸件缺陷。
2.因机器参数设置引起的缺陷
23:29
4. 冒口与铸件如何连接(冒口径) 冒口径的形状设计必须能保证冒口与铸
件间通道始终畅通,金属液以最佳的方式 对铸件进行补缩。
23:29
26
冒口有两种类型的收缩
1.表面缩孔。 2.内部缩松。 改善内部的缩松对策:
a.提高CE值 b.增加砂型强度 c.使用冷铁 d.顺序凝固 e.减少孕育用量 f.铁液净化 g.镁残留量趋进0.035
23:29
浇注系统
第2章浇注系统§2-1 概述§2-2 液态金属在浇注系统中的流动§2-3 浇注系统类型及其应用范围§2-4 铸铁件浇注系统计算方法§2-5 其它合金铸件浇注系统特点§2-1 概述1.浇注系统浇注系统是铸型中使液态金属充填型腔的通道。
浇注系统设置不当,常使铸件产生冲砂、夹砂、缩孔、缩松、裂纹、冷隔,以及气孔等多种缺陷,甚至会使铸件报废。
因此,正确的设计浇注系统,对提高铸件质量及降低生产成本具有重要意义。
2.浇注系统的结构一般情况下,浇注系统的结构由:浇口杯、直浇道、横浇道和内浇道组成。
对于某些复杂铸件的浇注系统,除上述四个组元外,尚可增加其他组元;而对于某些简单铸的浇注系统可以少于四个组元。
图2-1 浇注系统的基本组元3.浇注系统的设计内容包括浇注系统的结构、开设位置及各组元尺寸等。
4.浇注系统要求良好的浇注系统通常满足以下几点要求:1) 控制金属液流动的速度和方向,并保证充满型腔,保证适当的浇注时间。
2) 金属注入方式及内浇口方向应不致使金属冲毁铸型或砂型,并有利于杂质上浮和型中气体排出。
金属液在型腔中的流动应平稳、均匀以免夹带空气、产生金属氧化物。
3)有利于铸件温度的合理分布。
(铸型充满后,型内金属的温度分布状态尽可能有利于铸件预期的凝固方式。
希望同时凝固的铸件,温度应分布均匀;希望顺序凝固的铸件,温度应朝向冒口递增。
)4)浇注系统应具有除渣功能。
生产无锡青铜、球墨铸铁等铸铁件,要求浇注系统具有较强的挡渣能力,以防止溶渣进入铸型。
5)浇注系统不应阻碍铸件收缩,在生产裂纹敏感性强的大型铸件时,这点尤为重要。
6)在保证铸件质量的前提下,浇注系统力求简单,便于造型,金属消耗量最少,以及有利于铸件清理。
附加:对浇注系统的基本要求由以上的叙述大致上可以看出,浇注系统对铸件质量的影响是多方面的,其作用显然是重要的。
对浇注系统的基本要求如下:(1)根据铸件结构和合金凝固特点考虑浇注系统的结构,使金属液能以合理的充填速度或上升速度、尽可能平稳地(紊流程度低)、无喷射、飞溅地充填型腔;金属流股不冲蚀砂型或砂芯,也不在型内相互冲击,防止卷入气体和吸收气体,防止金属氧化。
材料成型浇注系统
浇注系统是为填充型腔和冒口而开设于铸型中的一系列通道。
常用的浇注系统大多由浇口杯、直浇道、横浇道、内浇道等部分组成。
除导入液态合金这一基本作用外,浇注系统还能实现其它的一些作用,其作用如下:(1)使液态合金平稳充满砂型,不冲击型壁和砂芯,不产生激溅和涡流,不卷入气体,并顺利地让型腔内的空气和其它气体排出型外,以防止金属过渡氧化及生产砂眼、铁豆、气孔等缺陷。
(2)阻挡夹杂物进入型腔,以免在铸件上形成渣孔。
(3)调节砂型及铸件上各部分温差,控制铸件的凝固顺序,不阻碍铸件的收缩,减少铸件变形和开裂等缺陷。
(4)起一定的补缩作用,一般是在内浇道凝固前补给部分液态收缩。
(5)让液态合金以最短的距离,最合宜的时间充满型腔,并有合适的型内液面上升速度,得到轮廓完整清晰的铸件。
(6)充型流股不要对正冷铁和芯撑,防止降低外冷铁的激冷效果及表面熔化,不使芯撑过早软化和熔化,而造成铸件壁厚变化。
(7)在保证铸件质量的前提下,浇注系统要有利于减小冒口体积,结构要简单,在砂型中占据的面积和体积要小,以方便工人操作、清除和浇注系统模样的制造,节约金属液和型砂的消耗量,提高砂型有效面积的利用。
一、浇注系统各组成部分与作用:(1)浇口杯:浇口杯又称外浇口,其作用是承接来自浇包的金属液,减轻金属液对铸型的冲击,阻止熔渣、杂物、气泡等进入直浇道,增加金属液的充型压力等。
常用浇口杯有呈漏斗形和池形(浇口盆),漏斗形浇口杯可单独制造或直接在铸型内形成,成为直浇道顶部的扩大部分;它结构简单,体积小,可节约金属,但阻渣能力较差,它常用于中、小型铸件,在机器造型中广泛采用。
对大、中型铸件,特别是铸铁件,常采用浇口盆,它具有较好的阻渣效果,浇口盆是与直浇道顶端连接,用以承接导入熔融金属的容器。
在浇口盆出口处常放置有浇口塞,当浇口盆充满金属后,塞子升起即开始浇注。
(2)直浇道:浇注系统中的垂直通道,它通常带有一定的锥度。
对黑色金属,直浇道应做成上大下小的锥体,锥度一般为1:20,其底部常比横浇道的底部稍低并呈(它可储存最初进入的金属液,球形。
- 1、下载文档前请自行甄别文档内容的完整性,平台不提供额外的编辑、内容补充、找答案等附加服务。
- 2、"仅部分预览"的文档,不可在线预览部分如存在完整性等问题,可反馈申请退款(可完整预览的文档不适用该条件!)。
- 3、如文档侵犯您的权益,请联系客服反馈,我们会尽快为您处理(人工客服工作时间:9:00-18:30)。
如果铸件质量很大,则计算铸件质量m时,应包括型 腔扩大量——由于各种原因引起的增重。增重原因有: 木模壁厚偏差 起模时扩砂量 铸型及砂芯干燥过程中的尺寸变化 合箱偏差及浇注时的涨砂等
6.确定浇口比并计算各组元截面积 7.绘出浇注系统图形
二、阶梯式浇注系统的计算
计算原理及步骤: 1、阻流面积S阻的计算
若铸件低于A-A水平面
若A-A水平面低于铸件最高点
2、分配直浇道截面积 依经验,分配直浇道截面积等于1~2倍阻流面积。
3、每层内浇道的总截面积
三、垂直分型浇注系统的计算
3、铸钢件浇注系统的特点
铸钢件浇注系统 特点: 铸钢的特点是熔点高,流动性差,收缩大,易氧化, 而且夹杂物对铸件力学性能影响严重,多使用底注 浇包(bottom pouring ladle, 俗称漏包、柱塞包), 要求浇注系统结构简单、截面积大,使充型快而平 稳,流股不宜分散,有利于铸件的顺序凝固和冒口 的补缩,不应阻碍铸件的收缩。
3、其他组元截面积
以包孔截面积为基准,参照下述浇口比确定浇注系统各组元截面积 S包孔:S 直:S横:S内 =1:(1.8~2.0): (1.8~2.0) :(2.0~2.5)
指出图51所示二种横浇道形式的优劣
析下图所示截面形状内浇道的应用。
一、平均静压头HP的计算
传统的解法中假定: 1) 金属液从浇口杯顶液面至流出阻流所作的功,可用 总质量m、 重力加速度g和平均计算压力头Hp的连乘积来表示,即等于mgHp
2) 假定铸件(型腔)的横截面积S沿高度方向不变
二、浇注时间
浇注时间对铸件质量有重要影响,应考虑铸件 结构、合金和铸型等方面的特点来选择快浇、 慢浇或正常浇注为好
快浇适用于:
薄壁的复杂铸件、铸型上半部分有薄 壁的铸件,具有大平面的铸件,铸件 表皮易生成氧化膜的合金铸件,采用 底注式浇注系统而铸件顶部又有冒口 的条件下和各种中大型灰铸铁件、球 墨铸铁件
慢浇的优点 金属对型壁的冲刷作用轻;可防止涨砂、抬箱、冲砂等缺陷。 有利型内、芯内气体的排除。对体收缩大的合金,当采用顶 注法或内浇道通过冒口时,慢浇可减小冒口。浇注系统消耗 金属少。
快浇的优点: 金属的温度和流动性降低幅度小,易充满型腔。 减小皮下气孔倾向。充型期间对砂型上表面的热作用时间短, 可减少夹砂结疤类缺陷。对灰铸铁、球墨铸铁件,快浇可以 充分利用共晶膨胀消除缩孔缩松缺陷。
快浇的缺点: 对型壁有较大的冲击作用,容易造成涨砂、冲 砂、抬箱等缺陷。浇注系统的重量稍大,工艺出品率略低
浇注系统的计算和设计
1、浇注系统计算的水力学公式
在浇注系统的类型和引入位置确定以后、 就可进一步确定浇注系统各基本单元的尺寸和 结构。
目前大都采用水力学近似公式或经验公式 计算出浇注系统的最小截面积,再根据铸件的 结构特点、几何形状等确定浇道比,确定各单 元的尺寸和结构。
计算阻流截面的水力学公式
合适的浇注时间与铸件结构、铸型工艺条件、合 金种类及选用的浇注系统类型等有关。每种铸件, 在已确定的铸造工艺条件下,都对应有适宜的浇 注时间范围。由于近年来普遍认识到快浇对铸件 的益处,因此浇注时间比过去普遍缩短,特别是
灰铸铁和球墨铸铁件更是如此。
浇注系统的流量系数通 常是指阻流截面的 流 量系数。
用底注浇包浇注时,浇注系统必须是开放式的,直 浇道不被充满,保证钢液不会溢出浇道以外。为快 速而平稳地充型,对一般中小铸件多用底注式,高 大铸件常采用阶梯式浇注系统。
(一)底注包浇注系统的经验计算法
铸钢车间的浇包容量和熔炉吨位一致,一般只有一种 或几种容量的浇包和数种直径的包孔。生产中先确定 浇包容量和包孔直径,依经验的浇口比确定浇注系统 各组元尺寸。 1、浇包容量及包孔选择 浇包总容量应大于铸型内金属需要量。小浇包只设一 个包孔,大于30t的浇包可设两个包孔。每个包孔的钢 液流量——浇注速度,不仅决定于包孔直径,还与包 内钢液深度有关。但实践中为方便起见,给出了包孔 直径和平均浇注速度的关系。 2、浇注时间和液面上升速度
2、铸铁件浇注系统设计与计算
一、设计步骤 通常在确定铸造方案的基础上设计浇注系统。大致步骤为
1、选择浇注系统类型 2、确定内浇道在铸件上的位置、数目和金属引入方向 3、决定直浇道的位置和高度
4.计算浇注时间并核算金属上升速度 应指出,重要的是核算铸件最大横截面处的型
内金属上升速度。当不满足要求时,应缩短浇注 时间或改变浇注位置。
慢浇的缺点 浇注期间金属对型腔上表面烘烤时间长,促成夹砂结疤和粘 砂类缺陷。金属液温度和流动性降低幅度大,易出现冷隔、 浇不到及铸件表皮皱纹。慢浇还常降低造型流水线的生产率。
慢浇法适用于 有高的砂胎或吊砂的湿型;型内砂芯多, 砂芯大而芯头小或砂芯排气条件差的情况 下;采用顶注法的体收缩大的合金铸件。