不锈钢丝毛刺处理办法
金属小零件去毛刺抛光方法有哪些

金属小零件去毛刺抛光方法有哪些
加工行业普遍存在一个棘手的问题,金属怎样有效去毛刺?特别是请求比拟高的内孔去毛刺、穿插孔去毛刺更是让人头痛。
采用普通机械去毛刺容易对硬度较低的产品产生次生毛刺以致刮伤,那么,金属小零件去毛刺抛光办法有哪些?
一、假如是比较规整的,平面的,估量你也不会问这个问题了,由于太简单太多方法了;
二、假如是异形件,或者需求去除内孔穿插孔毛刺,或者齿轮状、凹凸面、曲面球面的,有以下几种方法:
1、目前比较通用的是磨粒流抛光,抛光介质是半流体或液体,所以十分合适复杂外形的工件;
2、假如毛刺比拟脆,能够用超声波或者振动研磨抛光,只是可能会遇到毛刺去除不彻底的问题;
3、假如你的产品比较耐腐蚀,能够思索用化学抛光或电解抛光,但有可能会形成毛刺四周的腐蚀;
4、电解去毛刺,所谓电解去毛刺就是一种化学去毛刺的办法,它可去除机械加工,磨削加工及冲压加工后的毛刺,并使金属零件尖边倒圆或倒棱。
5、化学去毛刺,用电化学反响原理,对金属资料制成的零件自动地、有选择地完成去毛刺作业。
它可普遍用于气动、液压、工程机械、油嘴油泵、汽车、发起机等行业不同金属材质的泵体、阀体、连杆、柱塞针阀偶件等零件的去毛刺加工。
适用于难于去除的内部毛刺、热处置后和精加工的零件。
6、磁力研磨机去毛刺:用于五金首饰工艺品、电子仪器仪表等精细零件成电子仪器仪表等精细零件废品,去除毛边、倒角、抛光品,去除毛边、倒角、抛光、洗净等精细研磨工作一次性完成。
只需5—
15分钟就能够完成!不损坏工件精细度!不规则状零件、孔内、管内、死角、夹缝等皆可研磨加工。
孔内毛刺怎么处理【图解】
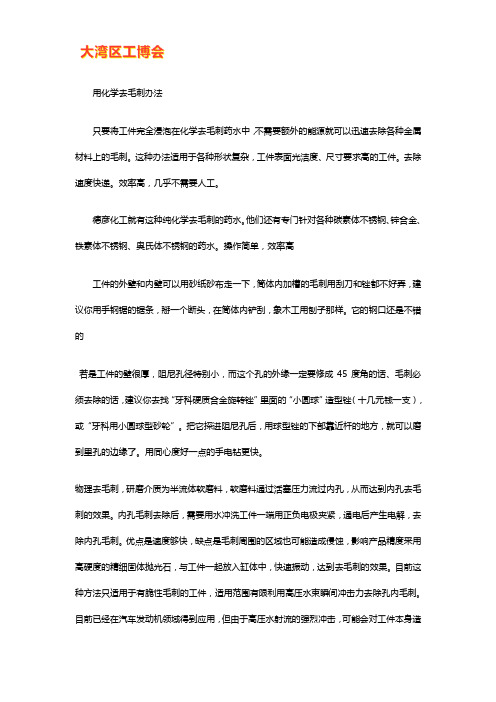
用化学去毛刺办法只要将工件完全浸泡在化学去毛刺药水中,不需要额外的能源就可以迅速去除各种金属材料上的毛刺。
这种办法适用于各种形状复杂,工件表面光洁度、尺寸要求高的工件。
去除速度快递。
效率高,几乎不需要人工。
德彦化工就有这种纯化学去毛刺的药水。
他们还有专门针对各种碳素体不锈钢、锌合金、铁素体不锈钢、奥氏体不锈钢的药水。
操作简单,效率高工件的外壁和内壁可以用砂纸砂布走一下,筒体内加槽的毛刺用刮刀和锉都不好弄,建议你用手钢锯的锯条,掰一个断头,在筒体内铲刮,象木工用刨子那样。
它的钢口还是不错的若是工件的壁很厚,阻尼孔径特别小,而这个孔的外缘一定要修成45度角的话、毛刺必须去除的话,建议你去找“牙科硬质合金旋转锉”里面的“小圆球”造型锉(十几元钱一支),或“牙科用小圆球型砂轮”。
把它探进阻尼孔后,用球型锉的下部靠近杆的地方,就可以磨到里孔的边缘了。
用同心度好一点的手电钻更快。
物理去毛刺,研磨介质为半流体软磨料,软磨料通过活塞压力流过内孔,从而达到内孔去毛刺的效果。
内孔毛刺去除后,需要用水冲洗工件一端用正负电极夹紧,通电后产生电解,去除内孔毛刺。
优点是速度够快,缺点是毛刺周围的区域也可能造成侵蚀,影响产品精度采用高硬度的精细固体抛光石,与工件一起放入缸体中,快速振动,达到去毛刺的效果。
目前这种方法只适用于有脆性毛刺的工件,适用范围有限利用高压水束瞬间冲击力去除孔内毛刺。
目前已经在汽车发动机领域得到应用,但由于高压水射流的强烈冲击,可能会对工件本身造成损伤,因此在应用前需要对工件进行评估。
一种环保的内孔去毛刺方案,利用氢气和氧气燃烧产生高热,瞬间氧化内孔毛刺,同时氧化后的毛刺也会附着在工件上,需要二次加工去除附着物。
在使用这种方法之前,需要知道工件是否能承受高温这种工艺叫斯曼克磨粒流去毛刺工艺,适用于各类内孔、交叉孔、微细孔以及齿面去毛刺,利用挤压研磨的原理,将半流体或液体磨料,挤压研磨工件内孔或端面,进行物理式研磨抛光,快速去除加工面毛刺。
不锈钢毛刺怎么处理【干货技巧】

不锈钢毛刺怎么处理内容来源网络,由“深圳机械展(11万㎡,1100多家展商,超10万观众)”收集整理!更多cnc加工中心、车铣磨钻床、线切割、数控刀具工具、工业机器人、非标自动化、数字化无人工厂、精密测量、3D打印、激光切割、钣金冲压折弯、精密零件加工等展示,就在深圳机械展.关于不锈钢去毛刺的简单的方法,主要针对小件产品工具/原料•不锈钢产品•磁力抛光机方法/步骤1. 根据不锈钢产品的大小,选择使用的机器型号,在工作槽内放入适合的钢针跟适量的水。
2. 根据产品的要求抛光亮度,放入适合的研磨液。
3. 启动机器,根据毛刺的大小,设置时间5到10分钟。
4. 时间到了,把产品拿出来,用清水清洗,把钢针拾起保存好一:有工具去除五金冲压件的毛刺1.孔:使用倒角刀或直径较大的钻头前端,2.边:使用锉刀,油石,砂纸,磨刀石,3.焊渣:有震动除焊渣工具也可去除较脆的毛刺,4.外径:加工过程时就以车床进行导角,5.还有抛光,研磨,喷砂,要看什么工件和产品要求,二:要根据产品来决定去不锈钢冲压件毛刺工艺的:1.用电化学去毛刺。
若自制设备,费用不高,经济、高效、使用。
2.震动磨去毛刺(齿轮毛刺),效率挺高,质量也可以。
3.热处理零件还可以通过喷丸去毛刺,还可以消除表面应力,4.用风枪配上各种形状的枪头去毛刺效果比较好,效率也高,5.齿轮去毛刺可以用以下几种方法:(1)电解去毛刺,效率最高,质量最好,但设备造价太高,一般的小企业用不起;(2)震动去毛刺,质量一般,不过成本较低,(3)手工去毛刺,质量比较好,只是效率可能低一些;4可采用滚压。
不锈钢焊条6.气动去毛刺.END注意事项•不要在研磨槽放入太多的水•不锈钢针要保存好,不要轻易丢失内容来源网络,由“深圳机械展(11万㎡,1100多家展商,超10万观众)”收集整理!更多cnc加工中心、车铣磨钻床、线切割、数控刀具工具、工业机器人、非标自动化、数字化无人工厂、精密测量、3D打印、激光切割、钣金冲压折弯、精密零件加工等展示,就在深圳机械展.。
解决不锈钢的须状毛刺所导致加工缺陷的方法.

解决不锈钢的须状毛刺所导致加工缺陷的方法1、现象在不锈钢的穿孔加工中,激光束一照射到金属上,金属就开始熔融。
如图如1所示,熔融物将被喷出到材料表面,飞溅到小孔的周围,并形成须状毛刺。
这些须状毛刺会使切割面出现划痕,还会影响到静电容量传感器的仿形动作。
图1 不锈钢穿孔的毛刺2、原因辅助气体使用氧气时,熔融金属会在穿孔过程中氧化,不会形成须状物,且与不锈钢材料表面间的紧贴性也不强。
而辅助气体使用氮气时,熔融金属不会被氧化,此时熔融金属的黏度较低,会伸展成为须状物,且由于该熔融金属与材料表面间的紧贴性较强,将在小孔的四周堆积。
3、解决方法防止熔融金属的飞溅、黏着的方法有:(a)减少产生的量;(b)防止黏着;(c)黏着之后去除(如图2所示)。
图2 解决不锈钢须状毛刺问题的方法(2)减少产生的量①调整穿孔条件,提高频率降低单一脉冲的输出功率将可有效减少熔融的量。
图3是分别以200Hz和1500Hz频率进行加工的结果。
需要注意的是,使用此加工条件时,热量输入也会同时增加,是不能用于厚版切割的。
图3 不锈钢1mm的加工②利用辅助气体或侧吹气体将从穿孔洞中喷出的熔融金属吹散。
图4所示为分别以0.05MPa和0.7MPa压力的辅助气体进行加工的结果。
可以看出,使用高压气体时,黏着在表面的熔渣量较少。
图4 不锈钢6mm的加工(2)防止黏着在材料表面涂抹隔离膜也可起到防止熔融金属黏着的作用。
材料表面上涂有隔离膜时,穿孔中所产生的熔融金属将会堆积在隔离膜上,而不会直接黏着在材料表面。
隔离膜可以使用熔避防止剂或易于后序处理的界面活性剂(图5)。
图5 防止黏着在材料表面(3)去除有两种去除须状毛刺的方法:一种是在穿孔洞的附近切割很小的圆孔,切割圆孔时将熔融金属一起切除;另—种是在穿孔后把焦点位置向上方移动,将堆积物进行再熔化,并用气体将之吹散(图2(C))。
修边,去毛刺的常用方法
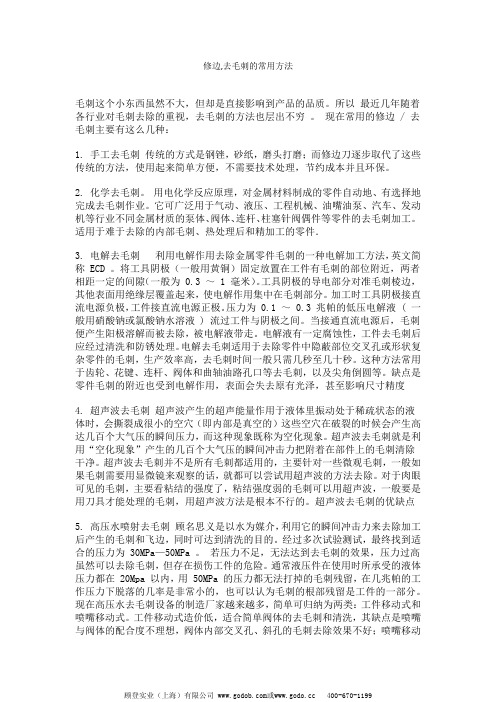
修边,去毛刺的常用方法毛刺这个小东西虽然不大,但却是直接影响到产品的品质。
所以最近几年随着各行业对毛刺去除的重视,去毛刺的方法也层出不穷。
现在常用的修边 / 去毛刺主要有这么几种:1. 手工去毛刺传统的方式是钢锉,砂纸,磨头打磨;而修边刀逐步取代了这些传统的方法,使用起来简单方便,不需要技术处理,节约成本并且环保。
2. 化学去毛刺。
用电化学反应原理,对金属材料制成的零件自动地、有选择地完成去毛刺作业。
它可广泛用于气动、液压、工程机械、油嘴油泵、汽车、发动机等行业不同金属材质的泵体、阀体、连杆、柱塞针阀偶件等零件的去毛刺加工。
适用于难于去除的内部毛刺、热处理后和精加工的零件.3. 电解去毛刺利用电解作用去除金属零件毛刺的一种电解加工方法,英文简称 ECD 。
将工具阴极(一般用黄铜)固定放置在工件有毛刺的部位附近,两者相距一定的间隙(一般为 0.3 ~ 1 毫米)。
工具阴极的导电部分对准毛刺棱边,其他表面用绝缘层覆盖起来,使电解作用集中在毛刺部分。
加工时工具阴极接直流电源负极,工件接直流电源正极。
压力为 0.1 ~ 0.3 兆帕的低压电解液 ( 一般用硝酸钠或氯酸钠水溶液 ) 流过工件与阴极之间。
当接通直流电源后,毛刺便产生阳极溶解而被去除,被电解液带走。
电解液有一定腐蚀性,工件去毛刺后应经过清洗和防锈处理。
电解去毛刺适用于去除零件中隐蔽部位交叉孔或形状复杂零件的毛刺,生产效率高,去毛刺时间一般只需几秒至几十秒。
这种方法常用于齿轮、花键、连杆、阀体和曲轴油路孔口等去毛刺,以及尖角倒圆等。
缺点是零件毛刺的附近也受到电解作用,表面会失去原有光泽,甚至影响尺寸精度4. 超声波去毛刺超声波产生的超声能量作用于液体里振动处于稀疏状态的液体时,会撕裂成很小的空穴(即内部是真空的)这些空穴在破裂的时候会产生高达几百个大气压的瞬间压力,而这种现象既称为空化现象。
超声波去毛刺就是利用“空化现象”产生的几百个大气压的瞬间冲击力把附着在部件上的毛刺清除干净。
如何消除不锈钢熔模铸件的毛刺缺陷

如何消除不锈钢熔模铸件的毛刺缺陷【摘要】对因硅溶胶型壳裂纹而引起的铸件毛刺缺陷进行了分析,找出了影响此类缺陷的主要原因,制定了防范措施,并在实际生产中取得一定效果。
【关键词】硅溶胶型壳;不锈钢精密铸造;毛刺;型壳裂纹我公司主要生产硅溶胶型壳的不锈钢精密铸件,有阀门管件和机械零件等。
铸件的毛刺是生产中时常批量产生的缺陷,必须在后处理工序经过打磨和抛丸等工序才能消除,即造成人物力的浪费,又影响了铸件表面的质量及尺寸精度,给生产和经营带来不利影响。
1.原因分析毛刺缺陷一般发生在铸件的外表面或较大平面上,连续或断续不规则凸起,形成毛刺飞边。
大件比小件发生几率要高。
形成毛刺的原因是由于型壳在浇注前就产生了裂纹,钢水注入后,渗入型壳的裂纹之中,凝固后就形成了毛刺缺陷。
而型壳的裂纹形成的原因有以下三点:1.1在型壳干燥时产生的,由于面层干燥过快,或涂料干燥收缩过大引起的。
1.2脱蜡时蜡模膨胀大于型壳膨胀,而型壳湿强度又较差使型壳开裂。
1.3型壳焙烧工艺不当,产生型壳裂纹。
2.改进措施2.1型壳的干燥2.1.1型壳干燥车间温度、湿度对型壳裂纹的影响制壳工况三要素有温度、湿度和风速。
我公司以3″球阀阀体为例作实验,产品材质为0Cr18Ni9,在风速一定的情况下,对型壳干燥车间的温度和湿度每隔4小时测量一次。
当温度变化超过5℃或湿度变化超过10%时,生产铸件较大部分出现表面毛刺缺陷。
在相同温度和湿度条件下,调整风速。
在对被层调整风速时,铸件表面毛刺影响极小;在对面层调整风速时,吹中强风干燥的型壳,浇注后铸件表面有严重毛刺缺陷,吹微风干燥或无风干燥时,铸件表面无毛刺缺陷。
经过以上统计分析,确定型壳干燥工艺为:(1)面层干燥间温度控制在20-24℃范围内,湿度在60%-70%范围内,无风或微风干燥。
(2)过渡层和背层干燥间温度在22-26℃范围内,湿度在50%-55%。
干燥时要求吹中强风,但不要正对模壳,要尽量使干燥间空气流动。
工厂去毛刺打磨方案
柳赖去毛刺打磨工具方案一、内孔去毛刺刷1尼龙纤维镀颗粒磨料内孔去毛刺刷 适用于非铁金属零件的内孔去毛刺。
尺寸 A*B*C*D 粒度 型号最小包装数最大转数 10*50*6*60#320BGCD-12110个2120 13*50*6*60 BGCD-122 16*50*6*60 BGCD-123 19*50*6*60 BGCD-124 25*50*6*60 BGCD-125 2190 32*50*6*60 BGCD-126 2320 38*50*6*60 BGCD-127 2470 50*50*6*60BGCD-12826202.不锈钢内孔去毛刺刷刷毛为高强度不锈钢丝,主要用于钢件的内孔去毛刺。
尺寸 A*B*C*D 刷毛直径 型号 最小包装数最大转数 10*50*6*60 Φ0.15 BGCD-10110个200013*50*6*60 BGCD-10216*50*6*60 BGCD-10319*50*6*60 BGCD-10425*50*6*60 BGCD-105 32*50*6*60 BGCD-106 38*50*6*60 BGCD-107 50*50*6*60 BGCD-1083黄铜内孔去毛刺刷刷毛为高强度黄铜,主要用于非铁金属的内孔去毛刺尺寸 A*B*C*D 刷毛直径 型号最小包装数 最大转数 10*50*6*60Φ0.15BGCD-11110个200013*50*6*60 BGCD-112 16*50*6*60 BGCD-113 19*50*6*60 BGCD-114 25*50*6*60 BGCD-115 32*50*6*60 BGCD-116 38*50*6*60 BGCD-117 50*50*6*60 BGCD-118二、带式打磨机1打磨机小巧的体积,全长仅275mm,手柄90度自由可弯设计,让抛光变得更加简单! 标准附属品:AZ60打磨带一条,Rc1/4接口一个型号 最大转速 线速度 全长 打磨带尺寸 重量 使用压力 气体消耗量 AGBS-10 17000 1100M/min275 12/10*330mm840g 0.588MPa 0.9m³/min AGBS-20 17000 2580M/min245 20*520mm 1.4kg 0.588MPa 1.2m³/min 打磨带从左至右依次为 树脂粘合AZ,树脂粘合A,尼龙,棉,电镀粘合尺寸 材质/粒度 最小包装数 最大线速度M/minAZ A#120 #24010*330 BY10-120 BY10-240 50条 250020*520 BY20-120 BY20-240 20条气锉适用范围超越普通锉刀,大大减轻操作者劳动量,大幅提高打磨效率。
介绍几种去除不锈钢冲压件毛刺的工艺
介绍几种去除不锈钢冲压件毛刺的工艺
在不锈钢冲压件行业的同仁们一定都知道,无论使用多么高级的冲压设备,毛刺都会随着不锈钢冲压件一同产生。
那么何为毛刺?小编告诉你主要是不锈钢材料经过变形加工后边缘产生的多余铁屑。
那我们可以通过什么工艺来减少或者克服它?一般情况下,不锈钢冲压件去除毛刺的工艺可以分为4大类:
粗级:不锈钢冲压件有毛刺时,可以采用切削,磨削,锉刀,刮刀等常见工艺除去,这些工艺只适用于精度要求不高的不锈钢冲压件;
普通级:对不锈钢冲压件有一定的精度要求的可以使用研磨、砂轮抛等工艺去除毛刺;
精密级:对于精密级的不锈钢冲压件,小编教你两种工艺除掉毛刺,那就是电化学加工、滚动加工;
超精密级:对于超精密级的不锈钢冲压件,要求非常非常的高,可以采用磁力研磨、超声波研磨等工艺去除毛刺,这类工艺可获得不锈钢冲压件非常高的精度。
如何清除不锈钢管生产中出现的毛刺
如何清除不锈钢管生产中出现的毛刺
很多人可能都对不锈钢管的生产过程中出现毛刺的现象感到头疼,那么为什么会出现这种情况呢,它是电流集中在焊缝处加热至熔融状态,经挤压辊侧向加压焊接时,受挤压力作用,多余的金属和氧化物堆积于焊缝上部形成外表面毛刺;受挤压力和重力的共同作用,另一些多余金属和氧化物沿钢管轴线方向在内侧下垂形成内毛刺。
那么有什么方法可以清除不锈钢管的毛刺,我们为您介绍以下几种方法:
1、切削法:该方法是利用伸进管内固定刀刃或旋转切削头,对毛刺进行切削。
2、辗压法:该方法是利用伸进管内的滚压装置,使内毛刺产生塑性变形,达到减薄内毛刺高度的效果。
3、氧化法:钢管焊接开始时,用通气喷嘴向内焊缝喷射氧气流,利用焊缝焊接余热,使内毛刺加速氧化,并在气流冲出下脱落。
4、拉拔法:钢管通过模具时,在浮动塞的环形刀刃作用下,清除钢管内毛刺。
以上我们为您讲解了不锈钢管出现的原因,从根本上了解出现问题的原因才能更好的解决问题。
另外,我们还为您介绍了几种小方法,可以使您有效的去除毛刺,您不妨试一试。
钢管切割后有毛刺如何解决【详解】
不锈钢管切割成了大家常常使用的加工方式,不锈钢管作为金属,切割时不会像切菜一样那么简单,在用普通切割机切割时一定会产生毛刺,这个毛刺一不小心就会割伤皮肤而且相当的难看。
而去除毛刺的方法大概可以分为以下几种:1、手工拔除法:就是肉眼能看到,比较容易除掉的毛刺,不利用其他工具,直接用手拔出。
当然这种方法比较原始,但是要注意安全。
2、摩擦去除法:用磨光机、锉刀等工具将毛刺去除,就是在砂轮机转动的时候,拿着不锈钢管的一头,轻轻靠近砂轮机的侧面,两物一摩擦,毛刺就不见了。
3、是用专业的切割设备来切不锈钢管,比如说线切割、水切割、圆锯机切割等,线切割和水切割的成本太高,一般都不会应用到普通的装饰用不锈钢管的切割上。
还有一种就是不锈钢用的圆锯机切割,圆锯机切割不锈钢管成本较低、效果却是相当的好。
这种专业的圆锯机配合上各种型号规格的不锈钢管模具和水,切割出来的不锈钢管切口非常的平整光滑,没有毛刺的产生,也不会变形。
一、端铣加工中毛刺的主要形式按照切削运动——刀具切削刃毛刺分类体系,端铣过程中产生的毛刺主要有主刃两侧方向毛刺、侧边切出切削方向毛刺、底边切出切削方向毛刺及切入和切出进给方向毛刺五种形式。
端铣加工形成的毛刺一般而言,底边切出切削方向毛刺与其它毛刺相比具有尺寸大、去除困难的特点。
为此,本文以底边切出切削方向毛刺作为主要研究对象开展研究。
根据端铣中底边切出切削方向毛刺尺寸和形态的不同,又可将其分为如下三种:I型毛刺(尺寸较大,去除困难,去除费用较高),II型毛刺(尺寸较小,可以不去除或去除容易)和III型毛刺即负毛刺影响端铣毛刺形成的主要因素毛刺的形成是一个非常复杂的材料变形过程。
工件材料特性、几何形状、表面处理、刀具几何形状、刀具切削轨迹、刀具磨损、切削参数及冷却液的使用等多种因素都直接影响毛刺的形成。
在具体的铣削条件下,端铣毛刺的形态和尺寸取决于各影响因素的综合作用,但不同的因素对毛刺的形成具有不同的影响。
- 1、下载文档前请自行甄别文档内容的完整性,平台不提供额外的编辑、内容补充、找答案等附加服务。
- 2、"仅部分预览"的文档,不可在线预览部分如存在完整性等问题,可反馈申请退款(可完整预览的文档不适用该条件!)。
- 3、如文档侵犯您的权益,请联系客服反馈,我们会尽快为您处理(人工客服工作时间:9:00-18:30)。
许多不锈钢丝产品在加工时,都会存在毛刺、飞边、锐边、表面粗糙、表面无光泽等问题。
如何正确高效率地处理这些问题呢?
电解去毛刺:
利用电解作用去除金属零件毛刺的一种电解加工方法,英文简称 ECD 。
将工具阴极(一般用黄铜)固定放置在工件有毛刺的部位附近,两者相距一定的间隙(一般为 0.3 ~ 1 毫米)。
工具阴极的导电部分对准毛刺棱边,其他表面用绝缘层覆盖起来,使电解作用集中在毛刺部分。
加工时工具阴极接直流电源负极,工件接直流电源正极。
压力为 0.1 ~ 0.3 兆帕的低压电解液 ( 一般用硝酸钠或氯酸钠水溶液 ) 流过工件与阴极之间。
当接通直流电源后,毛刺便产生阳极溶解而被去除,被电解液带走。
电解液有一定腐蚀性,工件去毛刺后应经过清洗和防锈处理。
电解去毛刺适用于去除零件中隐蔽部位交叉孔或形状复杂零件的毛刺,生产效率高,去毛刺时间一般只需几秒至几十秒。
这种方法常用于齿轮、花键、连杆、阀体和曲轴油路孔口等去毛刺,以及尖角倒圆等。
缺点是零件毛刺的附近也受到电解作用,表面会失去原有光泽,甚至影响不锈钢丝尺寸精度。
化学去毛刺:
用电化学反应原理,对金属材料制成的零件自动地、有选择地完成去毛刺作业。
它可广泛用于气动、液压、工程机械、油嘴油泵、汽车、发动机等行业不同金属材质的泵体、阀体、连杆、柱塞针阀偶件等零件的去毛刺加工。
适用于难于去除的内部毛刺、热处理后和精加工的零件。
手工去毛刺:
传统的方式是钢锉,砂纸,磨头打磨;而修边刀逐步取代了这些传统的方法,使用起来简单方便,不需要技术处理,节约成本并且环保。
超声波去毛刺:
超声波产生的超声能量作用于液体里振动处于稀疏状态的液体时,会撕裂成很小的空穴(即内部是真空的)这些空穴在破裂的时候会产生高达几百个大气压的瞬间压力,而这种现象既称为空化现象。
超声波去毛刺就是利用“空化现象”产生的几百个大气压的瞬间冲击力把附着在部件上的毛刺清除干净。
超声波去毛刺并不是所有毛刺都适用的,骏荣不锈钢认为此方法主要针对一些微观毛刺,一般如果毛刺需要用显微镜来观察的话,就都可以尝试用超声波的方法去除。
对于肉眼可见的毛刺,主要看粘结的强度了,粘结强度弱的毛刺可以用超声波,一般要是用刀具才能处理的毛刺,用超声波方法是根本不行的。