飞机制造工艺导论-第四章讲解
飞机制造工艺导论-第四章

(1)、保证定位符合图纸和技术条件所规定的准确度要求; (2)、定位和固定要操作简单、可靠; (3)、定位用的工装简单,制造费用低。
定位方法种类
1、按工件(基准件)定位 2、用划线定位 3、接触照相法定位 4、用装配孔定位 5、用装配夹具(型架)定位
1、按工件(基准件)定位
按基准工件或先装工件的某些点、线、面来定位后装工件。 按工件定位
部件结构通过纵向或横向可分成几个大段—段件。如机翼 可沿翼弦方向分为机翼前缘段、后段;机身可沿机身纵向 分成前、后机身。 部件或段件可分为板件。板件是由部件或段件的一部分 蒙皮以及内部纵向、横向骨架元件(如长桁、翼肋或隔框的 一部分)所组成,有时还包括安装在其上的导管、电缆及设 备。如机翼中段的上下板件(壁板),机身的上下左右板件。 段件或板件进一步分为组合件。如翼肋、梁、框等。 零件为不需要做装配的基本单位。
设计人员
(1)、综合考虑构造、使用、生产工艺(装配); (2)、从成批生产的需求划分; (3)、应充分考虑工厂的加工能力。 (1)、工艺性审查;
工艺人员
(2)、取决于综合的技术经济分析结果。即工艺分离面划分的原则 (装配原则)
3、工艺分离面划分的原则(装配原则)
分散装配原则:
一个部件的装配工作在较多的工作地点和工艺装备 上进行。 (1)、增加平行工作地、装配分散进行、扩大工作面、 (2)、结构开敞可达性好,改善劳动条件 (3)、有利于机械化和自动化,提高劳动生产率,缩短 部件装配周期,提高装配质量。 成批生产阶段
装配钳工少 量夹具
机床设备
毛坯
零件
产品
按图纸保证尺寸和公差,产品的准确度主要取决于零件的制造准确度。
飞机制造中
零件特点
(完整版)飞机制造工艺基础3
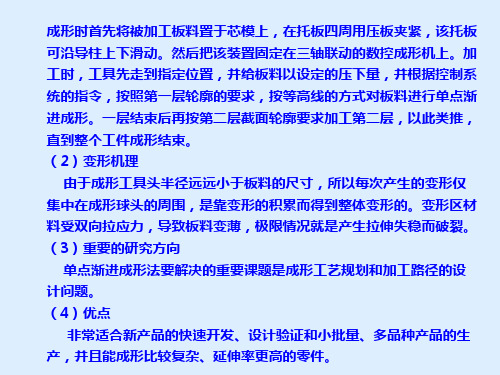
一.整体壁板毛坯 主要为铝合金,另有钛合金、镁合金。整体壁板毛坯的主要制造方法: 热摸锻、挤压、自由锻板坯、热轧平板毛坯和特种铸造。
1.大吨位液压机和锻模生产壁板毛坯 优点:生产率高、锻件纤维组织连续,晶粒致密,强度高,可制造复杂 形状筋肋和对接接头。
热模锻毛坯接近于成品尺寸,厚度和桁 条间距误差小于0.6mm,锻造斜度小锻需要吨位极大的机床,铝合金壁 板每平方米投影面积约需3万吨压力, 精锻时要5~6万吨。且锻模制造困难、 周期长、劳动量大。如某飞机整体壁板 的锻模重量达50~60吨。 这些问题限制了热模锻方法的广泛应用。
Most authors used in their experimental study on incremental forming regular 3 axis milling machine. Figure 7 presents the incremental forming process.
characteristics of the incremental forming process are pointed out:
- the sheet is formed according to a given locus - the deformation of the sheet is point-by-point - the deformation of every step is small.
Figure 8 The control system of Dieless NC Forming machine.
Figure 9 Equipment for Dieless NC Forming process
The blank sheet is attached to a blank holder. The blank holder moves in vertical direction according to descending of Ztool and along X- and Y-planes.
飞机制造技术基础

传统飞机结构研制过程(模拟量传递):样件,模具 数字量传递飞机结构研制过程:三维数模 钣金件数字化制造过程:以橡皮囊液压成形为例 弯边角度线定义方法:弯边角度线 工艺耳片:1、钣金件在成形过程中定位;
2、钣金件在切边过程中定位; 3、钣金件在装配过程中定位 工艺耳片的表示方法:1、用点和轴线(法矢)表示;
2,用点、轴线(法矢) 、孔轮廓和耳片轮廓表示; 3、用实体和轴线表示
航空产品数控加工的特点:(1)产品类型复杂,具有小批量、多样化特点 (2)结构趋于复杂化和整体化,工艺难度大,过程复杂; (3)薄壁化、大型化特点突出,变形控制极为关键; (4)材料去除量大,切削加工效率问题突出 (5)质量控制要求高 (6)产品材料多样 (7)大型结构件毛料价值高,质量风险大
2、降低造型材料的发气量;严格控制铸型中的水分,清除冷铁、型芯撑表面的锈蚀、油污, 并保持干燥等。
3、增加铸型的排气能力;控制型砂的干湿程度和紧实度,降低浇注速度等。
第二节 铸造的类型和概念 离心铸造,陶瓷模铸造,压铸,熔模铸造: 熔模铸造的特性:
尺寸精度高;表面粗糙度小;可浇 注形状复杂的薄壁铸件,铸型预热后浇注冷却速度 慢 ,铸件的力学性能较低。最适于铸造几克到十几千克;型壳用耐高温材料制成,故能适用于 各种铸造合金,特别是形状复杂的高熔点合金和难机械加工合金。熔模铸造的铸型属一次性铸 型。 失模铸造 近净成型铸造是指把金属铸造成非常接近最终成形件的形状,铸造出的工件只需少量的机加工, 由此它被称作近净成型 硬模铸造,石膏模铸造,壳型铸造,砂模铸造
第五节 铸造在航空航天中的应用
铸造在航空航天工业中的应用特点 1、铸造材料以轻质铝合金、高温钛合金等为主。钛合金精密铸造方向上,以熔模精密铸造和石 墨型铸造为主。 2、铸造成形采用当前最先进的技术完成精密铸造 3、铸造基本属于近净成型铸造
《飞机装配工艺学》课件
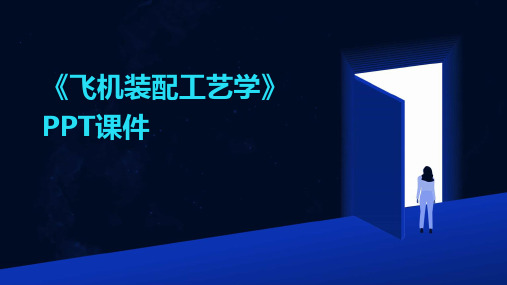
符合设计要求
保证互换性和通用性
飞机装配应保证各部件之间的互换性 和通用性,提高飞机的维护性和修理 性。
飞机装配应严格遵循设计图纸和技术 要求,确保各部件的安装位置、角度 、间隙等参数符合设计标准。
飞机装配的质量检测
01
02
03
外观检测
对飞机各部件的外观进行 检查,确保无损伤、无裂 纹、无锈蚀等缺陷。
加强培训
对飞机装配人员进行定期培训和考 核,提高其技能水平和质量意识。
05
飞机装配的未来发展
智能装配技术
自动化装配
Hale Waihona Puke 01利用机器人和自动化设备进行飞机零部件的精确装配,提高生
产效率。
智能化检测
02
通过传感器和数据分析技术,实时监测装配过程中的各项参数
,确保装配质量。
集成化管理
03
实现装配过程的信息化和数字化管理,优化资源配置,降低生
产成本。
绿色装配技术
环保材料
采用可再生、可降解的环保材料,降低飞机制 造过程中的环境污染。
节能减排
优化装配工艺,降低能耗和排放,实现绿色生 产。
循环利用
对飞机零部件进行回收和再利用,延长飞机使用寿命,减少资源浪费。
虚拟装配技术
模拟装配
通过计算机仿真技术,模拟飞机装配过程,提前发现 和解决潜在问题。
通过柔性装配技术,可以适应不同型号、不同批次 飞机的装配需求,提高生产效率和灵活性。
03
柔性装配技术包括柔性工装、柔性夹具和柔性检测 等。
04
飞机装配的质量控制
飞机装配的质量标准
符合国际和国内航空标准
飞机装配应遵循国际民用航空组织( ICAO)、国际标准化组织(ISO)以 及中国民航局的相关标准,确保飞机 的安全性能和可靠性。
91075-飞机制造工艺-第四章3(网)
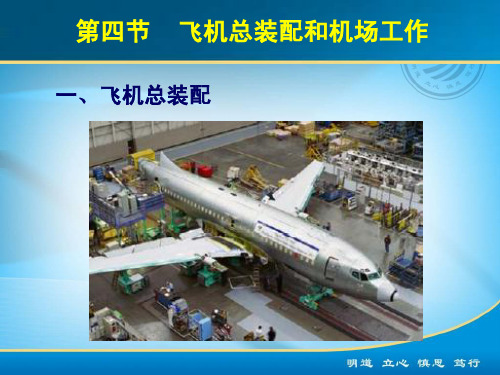
国产新型涡轮风扇发动机地面试车
三、飞机试飞
移交试飞和成批试飞
在真实飞行条件下,针对机体、发动机和机载设备 等进行飞行试验,暴露设计和制造缺陷、排出故障,并 获取性能数据(包括由研制单位负责的调整试飞、国家 鉴定试飞和提交鉴定报告)。
尾旋
经纬仪 水平仪
总装配过程示意图
A320天津总装线
飞机各部件的对接和水平测量
部件对接后的技术要求 图4-100 飞机水平测量图 图4-101 水平测量原理 图4-102 翼面、飞机对称性及测量点分布
各系统设备的安装、调整和检验 安装依据 安装工作的划分 液压系统、冷气系统的安装
பைடு நூலகம்、机场车间工作
验收飞机 地面试验
第四节 飞机总装配和机场工作
一、飞机总装配
飞机总装配包括
飞机机体各部件的对接、水平测量 安装调整发动机、燃油和滑油系统、安装调整
发动机操纵系统 液压和冷气系统的附件和导管的安装和试验 起落架及其收放机构、信号系统的安装、调整
和试验 飞机操纵系统的安装和调整 电器、无线电、仪表设备与电缆的安装、试验 高空救生设备的安装和试验 特种设备的安装和试验
液压系统
冷气系统
强度试验 强度试验
疲劳试验 环境试验
飞机装配工艺学

第三节 装配定位
六、用装配型架定 位
2021/7/21
翼肋装配夹具
第三节 装配定位
2021/7/21
接头定位器
第三节 装配定位
• 二次定位:指装配过程中某些外形和接头已经装配完毕, 而下一个装配阶段又需在另一个型架上再次定位。
• 飞机装配中,大力推广安装定位孔的定位方法,可大大 简化装配型架,且改善型架内的工作通路。
• 飞机设计时,应考虑工艺分离面的部位、形式和数量, 必须从成批生产的要求出发。
• 对于飞机结构上已具备的工艺分离面,在生产中是否 加以利用,这取决于综合的技术经济分析结果。
2021/7/21
第二节 装配基准
• 在装配过程中,使用两种装配基准:以骨架外形为基 准和以蒙皮外形为基准的装配。
2021/7/21
第一节 普通铆接
2021/7/21
图3-9 正铆和反铆 1-铆枪; 2-顶铁
第一节 普通铆接
• 正铆的优点:铆接埋头铆钉时表面质量好,蒙皮不受锤击; • 正铆的缺点:顶铁较重,劳动强度大,铆枪必须置于工件 • 反内铆。的优点:顶铁较轻,劳动强度小; • 反铆的缺点:部分锤击力直接打在钉头周围的零件表面。
2021/7/21
第一节 普通铆接
确定铆钉孔的位置
铆钉孔的位置,一般是指边距、排距(行距)、孔距 确定钉孔位置的方法有: (1) 按画线钻孔; (2) 按导孔钻孔; (3) 按钻模钻孔。
2021/7/21
锪窝 埋头窝过深,蒙皮受力后,会使铆钉松动,降低连接强度。
2021/7/21
2021/7/21
第一节 基本概念
• 在一般的机械制造中,各个零件和组合件都是独立地根 据图纸尺寸制造的。配合尺寸之间的协调准确度是通过 独立地控制各零件和组合件的制造准确达到的。
飞机设计导论(第四章)PPT课件
27.09.2020
隐身技术
第3页
4.1.1 Fighters
Fig. 4.1 shows a plot of combat wing loading against thrust/weight ratio, which is a good indication of the maneuverability of combat a/c.
27.09.2020
隐身技术
第4页
4.1.1 Fighters
Short range, high performance interceptor carries the minimum of equipment and maximum speed is always important. However, the rate of climb and maneuverability may be even more important. Due to the fighter’s short range it cannot take off until a target is definitely located, then rapidly climb to interception.
Only 1 crew can be carried and acquisition and life cycle costs are reasonably low. Relative simplicity of its equipment, reliability should be high. F-16 is in this category.
The innovation led to the powerful Sea harrier interceptor a/c flown from small aircraft carriers.
91073-飞机制造工艺-第四章1(网)
表示机翼尾翼与机身位置的参数 图3-8 机身各段之间位置的准确度:同轴度 操纵面相对于固定翼面位置的准确度 图3-9 部件之间对接接合准确度 图3-10
部件内部各零件和组合件的准确度
提高装配准确度的补偿方法
工艺补偿
装配时相互修配 图3-12 无互换性 装配后精加工 图3-13 图3-15 有互换性
第四章 飞机装配过程
第一节 飞机装配的基本问题
一、飞机结构的分解
飞机的基本组成
装配过程:零件
组合件、板件
段件、部件 飞机
设计分离面:结构和使用需要,可卸连接
工艺分离面
生产需要,不可卸连接
划分工艺分离面的作用
缩短装配周期 减少装配型架数量 改善装配工作的开敞性,提高装 配质量
进一步划分为板件的意义:
设计补偿
垫片补偿 连接补偿件 图33-17 在使用过程中可调
三、装配基准
以骨架外形为基准 图3-19 误差积累过程:由内向外
部件外形误差组成: 骨架零件制造的外形误差 骨架的装配误差 蒙皮的厚度误差 蒙皮和骨架由于贴合不紧而产生的误差 装配连接的变形误差
(1)提高装配的机械化和自动化程度 (2)有利于提高连接质量
二、装配准确度
飞机装配准确度对飞机性能的影响
飞机外形准确度影响飞机的空气动力性能 操纵系统的准确度影响飞机的各种操纵性能 装配变形影响飞机的结构强度和疲劳寿命 飞机的装配准确度直接影响产品的互换性
飞机装配准确度要求
飞机气动外形的准确度
外形准确度 图3-5 外形表面平滑度 图3-7
以蒙皮外形为基准
误差积累过程:由外向内 图3-20 部件外形误差的组成:
装配型架卡板的外形误差 蒙皮(壁板)和卡板外形之间由于贴合不
《智能制造导论》第四章智能制造核心技术
智能制造过程中涉及大量数据采集、传输和使用, 需要加强数据安全和隐私保护措施。
3
人才短缺
智能制造需要具备跨学科知识和技能的复合型人 才,企业需要加强人才培养和引进。
THANKS
感谢观看
总结词
智能制造技术为航空航天行业带来了更高的制造精度 和更短的研发周期,推动了行业的创新发展。
详细描述
航空航天行业对产品的质量和精度要求极高,智能制 造技术的应用使得这一要求得以更好地实现。通过引 入高精度的数控机床、激光切割和焊接设备等,航空 航天产品的制造精度得到了大幅提升。同时,智能化 的生产管理系统和仿真技术也使得产品的研发周期大 大缩短,加速了新产品的上市速度。此外,智能制造 技术还为航空航天行业提供了更高效的生产方式,降 低了生产成本。
详细描述
智能制造在汽车行业的应用主要体现在生产线的自动化和智能化方面。通过引入机器人、自动化设备和智能 化管理系统,汽车生产过程中的焊接、涂装、装配等环节实现了高效、精准的生产,大大提高了生产效率和 产品质量。此外,智能制造技术的应用还使得汽车行业能够更好地满足个性化定制的需求,快速响应市场变
化。
智能制造在航空航天行业的应用
01
02
03
数据采集与存储
利用传感器、RFID等技术 采集设备运行数据,通过 分布式存储等技术进行数 据存储。
数据处理与分析
利用数据挖掘、机器学习 等技术对海量数据进行处 理和分析,提取有价值的 信息。
数据可视化技术
将处理后的数据以图形、 图表等形式展示,便于理 解和决策。
工业人工智能技术
机器学习
智能制造导论-第四章 智能制 造核心技术
• 智能制造概述 • 智能制造核心技术 • 智能制造实践案例
南航 飞行器制造工艺 知识点
飞行器制造工艺完整知识点解析南京航空航天大学 011110301第一章1.飞机结构组成。
机体(包括机翼、机身、及尾翼等部件)、飞机操纵系统、飞机动力装置、机载设备等。
2.机翼的作用和组成;作用:机翼是产生升力和滚转操纵力矩的主要部件,也是现代飞机存储燃油的地方。
机翼作为飞机的主要气动面,是主要的承受气动载荷部件,其结构高度低,承载大。
通常在机翼上有用于横向操纵的副翼、扰流板,机翼的前缘和后缘还有各种形式的襟翼,用于增加升力或改变机翼的升力分布。
组成:由蒙皮和骨架组成。
机翼结构属薄壁型结构形式,构造上主要由蒙皮和骨架结构组成;蒙皮和骨架结构的功用;蒙皮功用:直接功用是保持机翼外形和承载。
气动载荷直接作用在蒙皮上,蒙皮将作用在上面的局部气动力传给结构骨架。
在总体承载时,蒙皮和翼梁或翼墙的服板组合在一起,形成封闭的盒式薄壁结构承受翼面扭矩,与长桁一起,形成壁板,承受翼面弯矩引起的轴力。
骨架功用:骨架的功用:是形成和保持翼面外形,承受和传递外载荷骨架结构有哪些构件。
骨架结构中,纵向构件有:翼梁、长桁和墙(腹板),横向构建有翼肋(普通肋、加强肋)3.机身的作用和组成,机身是指飞机机体结构中除各机翼结构之外的机体结构部分。
主要用于装载和传力,同时将机翼、尾翼、发动机和起落架等部件连接在一起,此外,可以安置空勤组人员和旅客、装载燃油、武器、各种仪器设备和货物等。
前机身主要是由雷达罩、设备舱、座舱、进气道、油箱、前起落架舱等组成。
中机身一般由进气道、油箱、部分发动机舱、设备舱和武器舱组成。
后机身主要是用于支持尾翼、装载发动机及部分设备。
机身结构构造上的组成:蒙皮、纵向骨架、横向骨架。
内部骨架的种类和作用。
骨架的结构:纵向构件有翼梁,长桁和墙;横向构件有普通肋和加强肋。
桁梁式结构:桁架只承受拉压力,蒙皮起维型作用,小轻型飞机采用;桁条式结构:长桁与蒙皮组成壁板承受弯曲轴力,蒙皮承受剪力和扭矩引起的剪流;桁梁式结构:桁梁承受弯曲轴向力,蒙皮长桁承受小部分轴力,蒙皮承受剪力;梁式结构:大梁承受主要载荷,蒙皮只承受剪力;硬壳式结构:蒙皮承受结构总体弯曲、剪切和扭转载荷。
- 1、下载文档前请自行甄别文档内容的完整性,平台不提供额外的编辑、内容补充、找答案等附加服务。
- 2、"仅部分预览"的文档,不可在线预览部分如存在完整性等问题,可反馈申请退款(可完整预览的文档不适用该条件!)。
- 3、如文档侵犯您的权益,请联系客服反馈,我们会尽快为您处理(人工客服工作时间:9:00-18:30)。
(1)、为提高装配工作的机械化和自动化程度创造了条件。 自动压铆机——钻孔、划窝、送铆钉、铆接、铣平铆钉头(埋头铆钉) (2)、有利于提高连接质量(开敞性、机械代替手工); (3)、改善劳动条件、缩短装配周期。
工艺分离面如何合理划分?
决定工艺分离面划分的因素——结构设计 (1)、飞机结构上是否存在相应的分离面; (2)、划分出的装配单元必须具有一定的强度、刚度、气 动方面的因素。
(1)、削弱了结构强度、增加了结构重量; 一般用于部件骨架与蒙皮之间,以保证部 求; 增加了装配工作量; (5)、具有互换性。
(3)、 件 气动力外形要 (4)、
4.1.4 装配基准
一、设计基准与工艺基准
常用的两种装配基准的装配:
二、以骨架为基准的装配 三、以蒙皮外形为基准的装配
一、设计基准与工艺基准
提高外形准确度的措施
1.加垫补偿; 2.精加工补偿(梁架精加工).
现代飞机:采用厚蒙皮或整体壁板结构,应提高结构件的加工准确度.
三、以蒙皮外形为基准的装配
装配过程
装配成上下壁板骨架(含蒙皮)、施加外力、上下蒙皮紧贴卡板、上下壁板 骨架连接(通过设计补偿)、形成外形。
误差积累的特点
“由外向内”
外形误差包括
特点
1.适用刚性较好的工件; 2.定位准确度要求不高的工件; 3.辅助的定位方法. 如:以骨架为基准的装配
2、用划线定位
划线定位 根据飞机图纸用通用量具划线定位。
特点
1.适用刚性较好的工件; 2.定位准确度要求不高的工件; 3.通用性大,辅助的定位方法; 4.生产效率低,取决于操纵者技术水平.
特点
第四章 飞机装配工艺
4.1 飞机装配的基本问题 4.2 装配连接技术
4.3 保证互换与协调的方法
4.4 飞机总装及机场工作
4.1飞机装配的基本问题
4.1.1 4.1.2 4.1.3 4.1.4 4.1.5
飞机结构的分解 装配准确度 装配基准 装配定位 装配工艺过程设计
4.1 飞机结构的分解
装配定位的要求
(1)、保证定位符合图纸和技术条件所规定的准确度要求; (2)、定位和固定要操作简单、可靠; (3)、定位用的工装简单,制造费用低。
定位方法种类
1、按工件(基准件)定位 2、用划线定位 3、接触照相法定位 4、用装配孔定位 5、用装配夹具(型架)定位
1、按工件(基准件)定位
按基准工件或先装工件的某些点、线、面来定位后装工件。 按工件定位
主要特点
可拆卸的连接(螺栓、铰链接合等)
2、工艺分离面
工艺概念
为了生产(装配)的需要,满足工艺过程的要求将飞机 结构进一步划分所形成的分离面。 (1)、一般采用不可拆卸的连接(铆接、胶接、焊接等); (2)、装配成部件后,工艺分离面消失。
主要特点
工艺分离面合理划分的优点:
(1)、增加了平行装配工作面,可缩短装配周期; (2)、减少了复杂的部件或段件的装配型架数量; (3)、改善了开敞性,提高装配质量。
1、定位准确度较划线定位高; 2、省略了划线工序和工装定位; 需专用接触照相设备。
适用范围
低速飞机的肋、隔框等装配和与外形无关的零件定位 (主要为平板件)。
结构模线
角材样板
缘条样板
腹板样板
角材零件
缘条零件
腹板零件
协调
特点Leabharlann 1、定位准确度取决于装配孔的协调制造方 法,协调环节较多,误差积累较大; 2、不需专用夹具;
产品的装配,必须用体现产品尺寸和形状的专用工艺装备(装配型架、 夹具)进行装配,而且还需分解在不同工作场地、不同工艺装备上进行装 配,以保证其尺寸和形状的准确度。
专用工装 专用工装
毛坯
零件
产品
飞机结构的分解
板件 毛坯 零件 组合件 段件
部件
试飞
飞机
4.1.1 设计分离面和工艺分离面
1、设计分离面(使用分离面)
段件
板件
组件
零件
飞机装配:将大量的飞机零件,按一定的组合和顺序(按图纸、技术条件),逐步装 成组合件、板件、段件和部件,最后将各部件对接成整架飞机的机体。
板件 毛坯 零件 组合件 段件
部件
试飞
飞机
为什么飞机制造中有如此复杂的装配过程呢?
一般机械制造中
零件特点
形状比较规则、刚性比较大的机加件, 制造、装配中不易产生变形。
(1)、装配型架卡板的外形误差; (2)、蒙皮和卡板外形之间由于贴合不紧而产生的误差; (3)、装配后产生的变形。
4.1.5
装配定位
一、装配定位的要求和特点
二、装配定位的方法 1、按工件定位 2、用划线定位 3、接触照相法定位 4、用装配孔定位 5、用装配夹具(型架)定位
一、装配定位的要求和特点
设计人员
(1)、综合考虑构造、使用、生产工艺(装配); (2)、从成批生产的需求划分; (3)、应充分考虑工厂的加工能力。 (1)、工艺性审查; (2)、取决于综合的技术经济分析结果。即工艺分离面划分的原则 (装配原则)
工艺人员
3、工艺分离面划分的原则(装配原则)
分散装配原则:
一个部件的装配工作在较多的工作地点和工艺装备 上进行。 (1)、增加平行工作地、装配分散进行、扩大工作面、 (2)、结构开敞可达性好,改善劳动条件 (3)、有利于机械化和自动化,提高劳动生产率,缩短 部件装配周期,提高装配质量。 成批生产阶段
替换
同一种工件之间的一致性。安装时,需切削、钻孔、铰孔、加垫、敲 修等补充加工。
互换与协调的关系 互换——同一种工件之间的一致性,控制制造误差。 协调——相配合工件之间的一致性,相互修配或控制制造误差。 互换一定协调,协调并不一定互换。
4.1.3、提高装配准确度的补偿方法
补偿方法
零件、组合件或部件的某些尺寸在装配时可进行加工或调 整,可以部分抵消零件制造和装配的误差,最后能够达到 技术条件所规定的准确度要求。 (1)、飞机产品特点所决定的; (2)、有利于技术经济效果; (3)、消除制造、装配过程中的各种误差积累。 1、修配—工艺补偿 2、装配后精加工—工艺补偿 3、间隙补偿—设计补偿; 4、加垫补偿—设计补偿; 5、可调补偿件—设计补偿; 6、搭接补偿—设计补偿。
特点
集中装配原则:
少数工作地点、少量工艺装备。
特点
(1)、装配工艺装备较少,减少了工艺装备的制造费用 (2)、协调关系较简单, (3)、生产准备周期较短 研制、试制生产阶段
4.1.2
装配准确度
一、飞机装配准确度要求 二、制造准确度和协调准确度的基本概念 三、提高装配准确度的补偿方法
一、飞机装配准确度要求
1、设计基准
基准 确定结构之间相对位置的一些点、线、面。
设计基准
产品设计需要建立的基准。如:飞机水平基准线、对称轴线、翼 弦平面、弦线、梁轴线、长桁轴线、框轴线、肋轴线等。
设计基准的特点
一般都不存在于结构表面上的点、线、面,在生产上 往往无法直接利用。
2、工艺基准
工艺基准 装配过程中需要建立的工艺基准。
5、可调补偿件—设计补偿
可调补偿 在结构上使两零件或构件的相对位置可以调节,以补偿协 调误差。
特点
(1)、减少了装配工作量; (2)、工件 结构复杂,重量稍有增加;(3)、具有互换性。
6、搭接补偿—设计补偿
搭接补偿 利用补偿角片,通过搭接长度的变化改变装配件的有关尺 寸,从而保证准确度要求。
特点
适用范围
内部骨架的零、组件装配,平板件,单曲度以及双曲 度(曲度变化不大)外形板件。
部件结构通过纵向或横向可分成几个大段—段件。如机翼 可沿翼弦方向分为机翼前缘段、后段;机身可沿机身纵向 分成前、后机身。 部件或段件可分为板件。板件是由部件或段件的一部分 蒙皮以及内部纵向、横向骨架元件(如长桁、翼肋或隔框的 一部分)所组成,有时还包括安装在其上的导管、电缆及设 备。如机翼中段的上下板件(壁板),机身的上下左右板件。 段件或板件进一步分为组合件。如翼肋、梁、框等。 零件为不需要做装配的基本单位。
装配准确度
装配后飞机机体及部件的几何形状、尺寸等实际数 值与设计所规定的理论数值的误差。对于不同类型的飞 机和飞机上不同的部位,装配准确度的要求不同。
部件气动力外形准确度 飞机的空气动力性能
部件内部组合件和零件的位置准确度
飞机的操纵性能
部件间相对位置的准确度
1、部件气动力外形准确度
(1)、外形要求 (2)、外形波纹度 (3)、表面平滑度要求
飞机制造过程:毛坯制造、零件加工、装配安装、试验。
毛坯制造
零件加工
装配安装
试验
锻 压 车 间
铸 造 车 间
机 加 车 间
钣 金 车 间
部 装 车 间
总 装 车 间
试 飞 站
几个概念的区分
结构
能承受和传递载荷的系统——即受力构件,承受指定 的外载,满足一定的强度、刚度、寿命、可靠性等要求。
部件结构
结构上和工艺上完整的装配单元。如机翼、尾翼、 机身、发动机短舱、起落架、动力装置等大结构。
典型工艺过程
试装
定位
确定余量线
修剪
检验
防腐
试装
定位
确定余量
扩孔
铰孔
检验
2、装配后精加工—工艺补偿
特点
(1)、单个装配后的工件单独补偿加工; (2)、需专用设备,依据样板、钻模或靠模进一步加工; (3)、增加了制造成本和装配周期; (4)、具有互换性。
典型工艺过程
精加工对接孔: 定位 夹紧 检查加工余量 扩孔 铰孔 检验
装配钳工少 量夹具
机床设备
毛坯