晶粒度评级图
第3章 奥氏体相变

G均匀
r*
*
2 GV GS
G均匀
16 3 3(GV GS ) 2
物理意义:新相核胚的原子团半径(r)必须大于临界半径(r*),系统才 )的阻碍,新相的核胚才能继续长大,完成形核过 能克服势垒( G均匀 程。否则核胚的原子团将重新散开,形核失败。
非均匀形核
3)残留渗碳体的溶解
1.实验现象: 1) F消失时,组织中的Fe3C还未完全转变 2) 测定后发现A中含碳量低于共析成分0.77% 2.原因: Fe-Fe3C相图上ES线斜度大于GS线,S点不在 CA-F与CA-C中点,而稍偏右。所以A中平均碳浓 度,即(CA-F + CA-C)/2低于S点成分。当F全部转 变为A后,多余的碳即以Fe3C形式存在。
σs=σi+Kyd-1/2 σs -屈服强度,σi-抵抗位错在晶粒中运动的 摩擦阻力,Ky-常数, d-晶粒直径
晶粒度 级别图 1-8级
3.4.1 晶粒度概念及晶粒长大现象
一)晶粒度
设N为放大100倍时每平方英寸in2面积内 的晶粒数,则下式中G即为晶粒度。
N=2
G-1
晶粒越细,G越大。 起始晶粒:加热转变终了时所得的A晶粒 实际晶粒:长大到冷却开始时的A晶粒 本质晶粒:930º C保温3~8小时所得的晶粒 1-4级:本质粗晶粒钢,5-8本质细晶粒钢
3.影响P转变为A的因素
温度 形核率与线长大速度随温度升高 而增加 碳含量:A形成速度随C%增加而增加 原始组织 P中Fe3C片厚度和颗粒大小影 响A形成过程及形成速度. 片状大于颗粒状;片层越小,速度越大 合金元素:改变临界点位置、影响C扩散 速度;形成各种碳化物(K)
如何进行晶粒度分析

教你如何进行晶粒度分析金属晶粒的尺寸(或晶粒度)对其在室温及高温下的机械性质有决定性的影响,晶粒尺寸的细化也被作为钢的热处理中最重要的强化途径之一。
因此,在金属性能分析中,晶粒尺寸的估算显得十分重要。
那么根据一张金相照片我们能从中得到哪些信息呢?首先来看看这一段小视频视频:晶粒度分析一、晶粒度概述晶粒度表示晶粒大小的尺度。
金属的晶粒大小对金属的许多性能有很大影响。
晶粒度的影响,实质是晶界面积大小的影响。
晶粒越细小则晶界面积越大,对性能的影响也越大。
对于金属的常温力学性能来说,一般是晶粒越细小,则强度和硬度越高,同时塑性和韧性也越好。
二、测定平均晶粒度的基本方法一般情况下测定平均晶粒度有三种基本方法:比较法、面积法、截点法。
具体如下1、比较法:比较法不需计算晶粒、截矩。
与标准系列评级图进行比较,用比较法评估晶粒度时一般存在一定的偏差(±0.5级)。
评估值的重现性与再现性通常为±1级。
2、面积法:面积法是计算已知面积内晶粒个数,利用单位面积晶粒数来确定晶粒度级别数。
该方法的精确度中所计算晶粒度的函数,通过合理计数可实现±0.25级的精确度。
面积法的测定结果是无偏差的,重现性小于±0. 5级。
面积法的晶粒度关键在于晶粒界面明显划分晶粒的计数图:面积法3、截点法:截点数是计算已知长度的试验线段(或网格)与晶粒界面相交截部分的截点数,利用单位长度截点数来确定晶粒度级别数。
截点法的精确度是计算的截点数或截距的函数,通过有效的统计结果可达到±0.25级的精确度。
截点法的测量结果是无偏差的,重现性和再现性小于±0.5级。
对同一精度水平,截点法由于不需要精确标计截点或截距数,因而较面积法测量快。
同心圆测量线(截点法)三、金相图具体案例分析以上只是大致的测定方法太过笼统,如果真的拿到一个具体的微观照片,我们该怎么做呢?下面我们来看一下具体操作与计算方法。
1、确定照片的放大率先测量微观照片的尺寸,长度或宽度选择其一,然后测量出试样的实际长度或者宽度放大率=图片距离/实际距离2、找出晶粒度级别数计算出放大率之后就可以确定晶粒度级别数。
奥氏体晶粒长大及其控制

*
起始晶粒度:珠光体刚刚转变成奥氏体 的晶粒大小。 实际晶粒度:热处理后所获得的奥氏体 晶粒的大小。 本质晶粒度:度量钢本身晶粒在930℃ 以下,随温度升高,晶粒长 大的程度。
加热速度愈大,过热度就愈大,即奥氏体实际形成温度就愈高,奥氏体的形核率与长大速度之比值I/G增大(表9.1),所以快速加热时可以获得细小的奥氏体起始晶粒。而且,加热速度愈快,奥氏体起始晶粒就愈细小。
*
表9.1 奥氏体的形核率I、长大速度G 与温度的关系
转变温度 (℃)
形核率I (1/mm3·s)
*
(2)晶界推移阻力
图9.12 晶界移动时与第二相粒子的交互作用示意图
1
2
*
在第二相粒子附近的晶界发生弯曲,导致晶界面积增大,界面能升高。弥散析出的第二相粒子愈细小,粒子附近晶界的弯曲曲率就愈大,晶界面积的增大就愈多,因此界面能的增大也就愈多。这个使系统自由能增加的过程是不可能自发进行的。所以,沉淀析出的第二相粒子的存在是晶界推移的阻力。
9.1.4 奥氏体晶粒长大 及其控制
1.奥氏体晶粒度 2.奥氏体晶粒长大原理 3.影响奥氏体晶粒长大的因素
奥氏体化的目的是获得成分均匀和一定晶粒大小的奥氏体组织。多数情况下希望获得细小的奥氏体晶粒,有时也需要得到较大的奥氏体晶粒。因此,为获得所期望的奥氏体晶粒尺度,必须了解奥氏体晶粒的长大规律,掌握控制奥氏体晶粒度的方法。
*
(4)合金元素的影响
钢中加入适量形成难溶化合物的合金元素如Nb、Ti、Zr、V、Al、Ta等,将强烈地阻碍奥氏体晶粒长大,使奥氏体晶粒粗化温度显著升高。上述合金元素在钢中形成熔点高、稳定性强、不易聚集长大的NbC、NbN、Nb(C,N)、TiC等化合物,它们弥散分布于奥氏体基体中,阻碍晶粒长大,从而保持细小的奥氏体晶粒。
常用齿轮钢的晶粒度显示方法
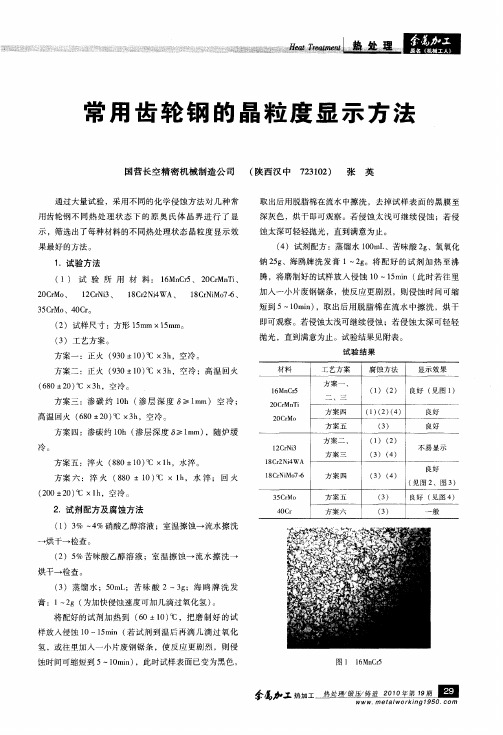
方案 六 :淬 火 ( 8 80±1 o X1 ,水 淬 ;回 火 0) h c
( 0 2 )c×1 ,空冷 。 2 0± 06 3 CMO 5r 4 C 0r
方 案 四 方 案 五 方 案六
( )( ) 3 4 () 3 () 3
抛光 ,直到满意为止。试验结 果见 附表。
试 验 结 果
材 料 1 Mn r 6 C5
2 r n i 0C M T
( )试样尺寸 :方形 1 mlX1 r 2 5 i 5 m。 l a ( )工艺方案 。 3 方案一 :正火 (3 9 0±1 )c× h 0 o 3 ,空冷 。 方 案二 :正火 (3 90±1 ) X3 ,空冷 ;高温 回火 0 ℃ h
常 用 齿 轮 钢 的 晶 粒 度 显 示 方 法
国营长空精密机械制造公 司 ( 陕西汉 中 7 3 0 ) 张 2 12 英
通过大量试验 ,采用不 同的化 学侵蚀方 法对几种 常
取 出后用脱脂棉在流水 中擦洗 ,去掉试样表 面 的黑膜 至
用齿轮钢不 同热 处理 状 态下 的原 奥 氏体 晶界进 行 了显 示 ,筛选出 了每种材料的不同热处 理状态 晶粒度显示 效
用前必须先进行 自身渗碳 ,即使正常生产情 况下 ,停炉 再升温时 ,也应进行炉膛 预渗。这一点至关重要 ,否则
易形成黑 色组织及表面腐 蚀,导致整炉工 件报废 。 另外 ,因乙醇尿素饱 和 溶液 的滴入 经 常堵 塞滴 孔 ,
图3 1C NM 7 8 r i o- 6
管道要经常用铁棍导通 。
用 ,同时减少 [ 、 [ c] N]原子复 合 ,维持较多 的活性
碳原子数 ,且保持 炉 内碳势 和氮 势 , 充 当活性 [ ] 并 C、
ASTME112中文修订版

金属平均晶粒度测定方法引言本标准规定了金属材料平均晶粒度的基本方法。
由于纯粹以晶粒几何图形为基础,与金属和合金本身无关。
因此,这些基本方法也可以用来测量非金属材料中晶粒、晶体和晶胞的平均尺寸。
如果材料的组织形貌非常接近某一个标准系列评级图,可以使用比较法。
测定平均晶粒度常用比较法,也可以用截点法和面积法。
但是,比较法不能用来测量单个晶粒。
1范围1.1 本标准规定了金属组织的平均晶粒度表示及评定的三种方法——比较法、面积法和截点法。
这些方法也适用于晶粒组织形貌与标准系列评级图相似的非金属材料。
这些方法主要适用于单相晶粒组织,但也适用于多相或多组元试样中特定类型组织的晶粒平均尺寸的测量。
1.2 本标准使用晶粒面积、晶粒直径、截线长度的单峰分布来测定式样的平均晶粒度。
这些分布近似正态分布。
本标准的测定方法不适用于双峰分布的晶粒度。
双峰分布的晶粒度参见标准E1181。
测定分布在细小晶粒基体上个别非常粗大的晶粒的方法参见E 930。
1.3本标准的测量方法仅适用平面晶粒度的测量,也就是试样截面显示出的二维晶度;不适用于试样三维晶粒,即立体晶粒尺寸的测量。
1.4 试验可采用与一系列标准晶粒度图谱进行对比的方法或者在简单模板上进行计数的方法。
利用半自动计数仪或自动图象分析仪测定晶粒尺寸的方法参见E 1382。
1.5本标准仅作为推荐性试验方法,它不能确定受检材料是否接收或适合使用的范围。
1.6 测量数值应用SI单位表示。
等同的英寸-英镑数值,如需标出,应在括号中列出近似值.1.7 本标准没有列出所有的安全事项,只是一些使用的注意事项。
本标准的使用者在使用前应掌握较合适的安全健康的操作规范和使用时限制的规章制度。
1.8 章节的顺序如下:2、参考文献2.1ASTM标准E3 金相试样的制备E7 金相学相关术语E407 金属和合金浅腐蚀的操作E562计数法计算体积分数的方法E691 通过多个实验室比较决定测试方法的精确度的方法E883 反射光显微照相指南E930 截面上最大晶粒的评估方法(ALA晶粒尺寸)E1181双峰分布的晶粒度测试方法E1382 半自动或全自动图像分析平均晶粒度方法2.2 ASTM附件2.2.1 参见附录X23术语3.1 定义-本标准采用的专业术语定义参照E73.2 本标准中特定术语的定义:3.2.1 ASTM晶粒度——G,通常定义如公式(1)N AE=2G-1 (1)N AE为100倍下每平方英寸(645.16mm2)面积内包含的晶粒个数,相当于1倍下每平方毫米面积内包含的晶粒个数乘以15.5倍。
实验一 钢的奥氏体晶粒度的测定及评级方法

实验一钢的奥氏体晶粒度的显示与测定一.实验目的1.熟悉钢的奥氏体晶粒度的显示与测定的基本方法。
学习利用物镜测微尺标定目镜测微尺和毛玻璃投影屏刻度格值。
通过它们间的关系到确定显微镜物镜和显微镜的线放大倍数。
2.熟悉钢在加热时,加热温度和保温时间对奥氏体晶粒大小的影响。
3.测定钢的实际晶粒度。
用直接计算法和弦计算法测量晶粒大小。
用比较法评定晶粒度级别。
二.实验原理金属及合金的晶粒大小与金属材料的机械性能、工艺性能及物理性能有密切的关系。
细晶粒金属的材料的机械性能、工艺性能均比较好,它的冲击韧性和强度都较高,在热处理和淬火时不易变形和开裂。
粒晶粒金属材料的机械性能和工艺性能都比较差,然而粗晶粒金属材料在某些特殊需要的情况下也被加以使用,如永磁合金铸件和燃汽轮机叶片希望得到按一定方向生长的粗大柱状晶,以改善其磁性能和耐热性能。
硅钢片也希望具有一定位向的粗晶,以便在某一方向获得高导磁率。
金属材料的晶粒大小与浇铸工艺、冷热加工变形程度和退火温度等有关。
晶粒尺寸的测定可用直测计算法。
掌握了这种方法也可对其它组织单元长度进行测定,如铸铁中石墨颗粒的直径;脱碳层深度的测定等。
某些具有晶粒度评定标准的材料,可通过与标准图片对比进行评定。
这种方法称为比较法。
1.奥氏体晶粒度的显示钢在临界温度以上直接测量奥氏体晶粒大小比较困难的,而奥氏体在冷却过程中将发生相变。
一般采用间接的方法显示其原奥氏体晶界,以测定奥氏体晶粒大小。
根据GB6394-86规(4)网状渗碳体法适用于含碳量大于1.0%的过共析钢的奥氏体晶粒度。
方法是:将试样在930±10℃(或特定的温度)下加热保温40min以上(或特定的时间)后以缓慢的速度冷却冷却到600℃,在过共析钢的奥氏体晶界上析出网状渗碳体,以此来显示奥氏体晶粒形貌与大小。
经上述热处理的试样抛光后,应使用硝酸或苦味酸酒精溶液腐蚀。
图1 过共析钢的状渗碳体(×100)在经上述方法之一制备的金相试样上,即可进行奥氏体晶粒度的测定。
晶粒度评级

表1 常用材料使用的标准系列图片
系列图片号
Ⅰ
适
用
范
围
1)铁素体钢的A晶粒(用氧化法、直接淬硬法、F网法、 铁素体钢的A晶粒(用氧化法、直接淬硬法、 网法、 Fe3C网法及其他方法显示 晶粒) 网法及其他方法显示A Fe3C网法及其他方法显示A晶粒) 2)铁素体钢的铁素体晶粒 镁和镁合金、锌和锌合金、 3)铝、镁和镁合金、锌和锌合金、超强合金 1)奥氏体钢的A晶粒(有孪晶的) 奥氏体钢的A晶粒(有孪晶的) 铁素体钢的铁素体晶粒有孪晶的) 2)铁素体钢的铁素体晶粒有孪晶的) 镁和镁合金、镍和镍合金、锌和锌合金、 3)镁和镁合金、镍和镍合金、锌和锌合金、超强合金 铜和铜合金 1)渗碳钢的A晶粒 渗碳钢的A 奥氏体钢的A晶粒(无孪晶的) 2)奥氏体钢的A晶粒(无孪晶的)
F钢与A钢的奥氏体晶粒度 钢与A 形成及显示
对于铁素体钢
奥氏体晶粒的显示方法: 奥氏体晶粒的显示方法:
国家标准GB/T6394-2002《 国家标准GB/T6394-2002《金属平均晶粒 GB/T6394 度测定法》规定可使用渗碳法、氧化法、 度测定法》规定可使用渗碳法、氧化法、 铁素体网法、渗碳体网法、直接淬硬法、 铁素体网法、渗碳体网法、直接淬硬法、 网状珠光体法、相关法、模拟渗碳法等。 网状珠光体法、相关法、模拟渗碳法等。
晶粒数N的计算: 晶粒数N的计算: • 用5000mm2的圆形网置于晶粒图形上; 的圆形网置于晶粒图形上; • 选放大倍数M使网内晶粒数为50个; 选放大倍数M使网内晶粒数为50 50个 • 计算落入数N内和切割数N交,该面积内的晶粒数N 计算落入数N 和切割数N 该面积内的晶粒数N /2) 为: N= N内+( N交/2)-1 计算试样检测面上每mm 内晶粒数n 计算试样检测面上每mm2内晶粒数n: n = M2×N/A 式中: 式中:M—所用的放大倍数 所用的放大倍数 放大M 面积为A N—放大M时,面积为A的网格内晶粒计数 放大 晶粒度级别数: 928lgn晶粒度级别数:G=3.321 928lgn-2.954
奥氏体晶粒度测定

实验 钢的奥氏体晶粒度的测定在钢铁等多晶体金属中,晶粒的大小用晶粒度来衡量,其数值可由下式求出:12-=N n式中:n —显微镜放大100倍时,6.45cm 2 (1in 2) 面积内晶粒的个数。
N —晶粒度奥氏体晶粒的大小称奥氏体晶粒度。
钢中奥氏体晶粒度,一般分为1~8等8个等级。
其中1级晶粒度晶粒最粗大,8级最细小(参看YB27—64)。
奥氏体晶粒的大小对以后冷却过程中所发生的转变以及转变所得的组织与性能都有极大的影响。
因此,研究奥氏体晶粒度的测定及其变化规律在科学研究及工业生产中都有着重要的意义。
一、奥氏体晶粒度的一般概念奥氏体晶粒按其形成条件不同,通常可分为起始晶粒、实际晶粒与本质晶粒三种,它们的大小分别以起始晶粒度,实际晶粒度与本质晶粒度等表示。
1、起始晶粒度在临界温度以上,奥氏体形成刚刚结束时的晶粒尺寸,称起始晶粒度。
起始晶粒度决定于奥氏体转变的形核率(n )及线生长速度(c )。
每一平方毫米面积内奥氏体晶粒的数目N 与n 及c 的关系为2101.1⎪⎭⎫⎝⎛=c n N由上式可知,若n 大而c 小,则起始晶粒就细小。
若n 小而c 大则起始晶粒就粗大。
在一般情况下n 及c 的数值决定于原始组织的形态和弥散程度以及加热时的加热速度等因素。
由于在珠光体中存在着大量奥氏体形核部位,n 极大。
故奥氏体的起始晶粒总是比较细小的。
如果加热速度快,则转变被推向高温,奥氏体起始晶粒将更加细化。
这是因为,随着加热速度的增大和转变温度的升高,虽然形核n 和c 都增大,但n 比c 增加的幅度更大。
表1—6示出钢在加热时,奥氏体的n 与c 数值与加热温度的关系,由表1—6中的数据可知。
相变温度从740℃提高到800℃时n 增大280倍而c 仅增加40倍。
表1—6 奥氏体形核(n )和线生长速度(c )与温度的关系应当指出,奥氏体起始晶粒随加热速度的增大而细化的现象,只是在加热速度不太大时比较明显。
当加热速度很大时起始晶粒不再随之细化(见表1—7)表1—7 加热速度对起始奥氏体晶粒大小的影响这可能是由于在快速加热时,转变被推向高温(大于800℃),奥氏体的核不仅可以在铁素体与渗碳体的交界面上形成,而且可以在铁素体晶粒内嵌镶块的边界上形成。
- 1、下载文档前请自行甄别文档内容的完整性,平台不提供额外的编辑、内容补充、找答案等附加服务。
- 2、"仅部分预览"的文档,不可在线预览部分如存在完整性等问题,可反馈申请退款(可完整预览的文档不适用该条件!)。
- 3、如文档侵犯您的权益,请联系客服反馈,我们会尽快为您处理(人工客服工作时间:9:00-18:30)。
金属平均晶粒度评级图—系列图片I无孪晶晶粒100×00级0级
金属平均晶粒度评级图—系列图片I无孪晶晶粒100×0.5级 1.0级
金属平均晶粒度评级图—系列图片I无孪晶晶粒100×1.5级 2.0级
金属平均晶粒度评级图—系列图片I无孪晶晶粒100×2.5级 3.0级
金属平均晶粒度评级图—系列图片I无孪晶晶粒100×3.5级 4.0级
金属平均晶粒度评级图—系列图片I无孪晶晶粒100×
4.5级
5.0级
金属平均晶粒度评级图—系列图片I无孪晶晶粒100×5.5级 6.0级
金属平均晶粒度评级图—系列图片I无孪晶晶粒100×
6.5级
7.0级
金属平均晶粒度评级图—系列图片I无孪晶晶粒100×7.5级8.0级
金属平均晶粒度评级图—系列图片I无孪晶晶粒100×
8.5级9.0级
金属平均晶粒度评级图—系列图片I无孪晶晶粒100×9.5级10.0级。