钻孔动力头的PLC控制
基于PLC控制的数控钻孔机的设计与实现

基于PLC控制的数控钻孔机的设计与实现随着科技的进步和工业自动化水平的提高,数控(Numerical Control)钻孔机在工业生产中得到了广泛的应用。
数控钻孔机的设计与实现基于PLC(Programmable Logic Controller)控制,PLC控制具有可靠性高、灵活性强等优点。
本文将介绍基于PLC控制的数控钻孔机的设计与实现。
首先,在数控钻孔机的设计中,我们需要考虑到几个方面。
首先是机械部分的设计,包括钻头的选择、主轴的设计、夹持装置的设计等。
其次是电气部分的设计,主要包括电机的选择、传感器的选择、电气线路的设计等。
最后是PLC控制程序的编写,需要根据实际需求设计钻孔程序。
在机械部分的设计中,我们需要选择适合的钻头来满足不同的钻孔需求。
常见的钻头有立铣钻头、圆滚钻头等。
主轴的设计需要考虑到主轴的转速和稳定性,可以选择带有变频器的电机来调整主轴的转速。
夹持装置的设计需要满足钻孔材料的夹持需求,可以选择气动夹紧装置或电动夹紧装置。
在电气部分的设计中,我们需要选择适合的电机来驱动主轴。
根据钻孔材料的不同,可以选择不同功率的电机。
传感器的选择需要满足对材料位置和尺寸的检测需求,可以选择接近开关、压力传感器等传感器。
电气线路的设计需要根据实际需求进行布线,保证线路的安全稳定。
在PLC控制程序的编写中,我们需要根据实际需求设计钻孔程序。
首先,我们需要编写一个启动程序,通过点击按钮或接近开关来启动钻孔机的工作。
然后,我们需要编写一个控制程序,通过设定参数来控制钻孔机的运行。
控制程序可以设置钻孔深度、钻孔速度等参数。
最后,我们还需要编写一个停止程序,当钻孔完成或发生异常情况时,通过点击按钮或接近开关来停止钻孔机的工作。
总结起来,基于PLC控制的数控钻孔机的设计与实现需要考虑到机械部分的设计、电气部分的设计以及PLC控制程序的编写。
通过合理的设计和实施,可以实现数控钻孔机的自动化控制,提高生产效率,降低人工成本,提高产品质量。
PLC编程实例之钻孔动力头控制

PLC编程实例之钻孔动⼒头控制某⼀钻床如图35-1 (a)所⽰,⽤于在⼯作台上钻孔,钻床的⼯作过程如下:钻头在原位时,限位开关SQ1受压。
按下启动按钮SB1,动⼒电动机Ml得电,带动钻头转动。
同时⼯进电动机M2得电,钻头快进。
当碰到限位开关SQ2时,⼯进电磁阀YV得电,转为⼯作进给。
当碰到限位开关SQ3时,YV2失电,停⽌⼯进。
5s后,钻头快退,碰到SQ1时,动⼒电动机和电磁阀均失电,停⽌⼯作。
按下停⽌按钮,动机电动机和电磁阀均失电。
控制⽅案设计1.输⼊/输出元件及控制功能如表35-1所⽰,介绍了实例35中⽤到的输⼊/输出元件及控制功能。
2.电路设计钻孔动⼒头控制梯形图如图35-2所⽰。
3.控制原理⽅法1:图35-2 (a)中,钻头在原位时限位开关X1受压,接点闭合。
按下启动按钮XO, MC 主控指令的线圈Y0得电并⾃锁,主轴电动机启动。
此处⽤MC、MCR指令的⽬的是保证只有在主轴电动机Y0得电时钻头才能⼯作,另⼀个⽬的是简化电路(如果⽤OUT Y0指令梯形图较复杂)。
同时Y1得电⾃锁,进给电动机得电快进。
当快进碰到限位开关X2时,Y3 得电⾃锁,⼯进电磁阀得电钻头⼯进。
当⼯进碰到限位开关X3时,M0得电⾃锁,Y1、Y3 失电,钻头停⽌;TO得电延时5s, Y2得电。
进给电动机得电快退。
当快退(中途碰到限位开关X2吋,由于Y2常闭接点断开,不会误使Y3得电)到原位碰到限位开关X1时,X1上升沿接点取反,使主控线圈Y0失电,完成⼀次钻孔过程。
⽅法2:图35-2 (b)中,初始状态,钻头在原位时限位开关X1受压。
按下启动按钮X0,状态器SO置位,由于限位开关X1受压接点闭合,状态器SO⼜复位,S500置位,Y0置位,主轴电动机启动。
Y1线圈得电,进给电动机得电快进。
当快进时碰到限位开关X2时,Y0仍置位,Y1失电,Y3得电,⼯进电磁阀得电钻头前进。
当⼯进碰到限位开关X3时,Y3失电钻头停⽌,TO得电延时5s,Y2得电。
深孔钻机床PLC控制电路的设计

深孔钻机床PLC控制电路的设计深孔钻机床是一种专门用于加工深孔的机床,其加工深孔的工艺复杂,对控制系统的可靠性和精度要求较高。
PLC(Programmable Logic Controller,可编程逻辑控制器)被广泛应用于深孔钻机床的控制系统中,具有可编程性强、可靠性高等特点。
首先,深孔钻机床的PLC控制电路应包括输入模块、输出模块、中央处理器以及电源等组成部分。
输入模块主要负责检测各种传感器的输出信号,例如钻头的位置、进给速度等。
输出模块则负责控制机床的各种执行器,例如钻孔进给和回退等。
中央处理器是PLC的核心部分,负责处理输入信号,并输出相应的控制信号。
其次,深孔钻机床的PLC控制电路的设计要考虑以下几个方面:1.高精度控制:深孔钻机床的加工要求高精度,因此PLC控制电路应具有高精度的脉冲输出端口,以控制机床的进给速度和位置。
可以采用高速计数器模块,实现对脉冲信号的精确计数和控制。
2.多轴控制:深孔钻机床通常包括多个工作轴,如X、Y、Z轴等。
PLC控制电路应支持多轴控制,需要具备多个高速计数器和输出模块,实现对多个轴的独立控制。
3.安全保护:深孔钻机床的加工过程中存在一定的危险,PLC控制电路应包含相应的安全保护措施,如急停开关、过载保护等,确保操作人员和设备的安全。
4.自动化控制:PLC控制电路可以实现深孔钻机床的自动化控制,例如根据加工要求自动调整进给速度和切削参数等。
此外,还可以通过与上位机通信和数据交互,实现远程监控和故障诊断。
在深孔钻机床的PLC控制电路具体设计中,需要根据具体的机床加工要求和实际控制需求进行功能划分和模块选择。
同时,还需要考虑电源和接口电路的设计,确保PLC控制电路的稳定性和可靠性。
总结起来,深孔钻机床的PLC控制电路的设计应当考虑高精度控制、多轴控制、安全保护和自动化控制等方面。
在具体的设计中,需要根据实际需求进行功能划分和模块选择,并确保电路的稳定性和可靠性。
基于PLC控制的数控钻孔机的设计与实现

基于PLC控制的数控钻孔机的设计与实现数控钻孔机是一种通过计算机数控系统实现自动钻孔的设备,可以实现高精度、高效率的钻孔作业。
本文将基于PLC控制的数控钻孔机的设计与实现进行详细介绍。
1.设计概述数控钻孔机主要由机械部分和控制系统两部分组成。
机械部分主要包括电动机、传动装置和钻头等,控制系统则由PLC控制器和人机界面组成。
2.机械部分设计为了实现高精度的钻孔作业,机械部分需要具备较高的稳定性和刚度。
首先,选择质量较好的电动机,通过减速装置将电动机的转速转为稳定的钻头转速。
其次,使用高硬度的刀具材料,以保证钻头在高速转动时不会变形。
最后,选择高精度的导轨和滑块,确保钻孔机在运动过程中无偏差。
3.PLC控制系统设计PLC控制系统是数控钻孔机的核心部分,它通过计算机数控系统来实现自动化的钻孔操作。
首先,选择适合的PLC控制器,通常选择具有高速计算和多IO口的控制器。
其次,编写PLC程序,根据用户输入的坐标参数和钻头尺寸,计算出钻孔的位置和深度。
然后,通过控制器的输出口,控制电动机的转速和钻头的升降运动,实现自动化的钻孔操作。
最后,在控制界面上添加合适的控制按钮和显示界面,方便用户操作和监测钻孔过程。
4.人机界面设计为了方便操作和监测钻孔过程,需要设计一个直观清晰的人机界面。
在界面上添加坐标输入框和尺寸调节按钮,方便用户输入钻孔的坐标和尺寸参数。
同时,添加控制按钮和监测指示灯,方便用户启动和停止钻孔过程,并实时监测钻孔状态。
另外,在界面上添加错误提示功能,当出现异常情况时能及时提示用户,并采取相应的应对措施。
5.钻孔机的实现在完成设计后,将机械部分和控制系统进行组装和调试。
首先,根据设计要求,选择适合的材料和加工工艺,制作机械部分的各个零件。
然后,组装机械部分,确保各个部件的协调配合。
接下来,将PLC控制器和人机界面与机械部分进行连接,并进行电气布线和信号调试。
最后,进行整机调试和测试,检查钻孔机的各项指标是否符合设计要求。
基于PLC的钻孔加工过程自动化控制系统的设计
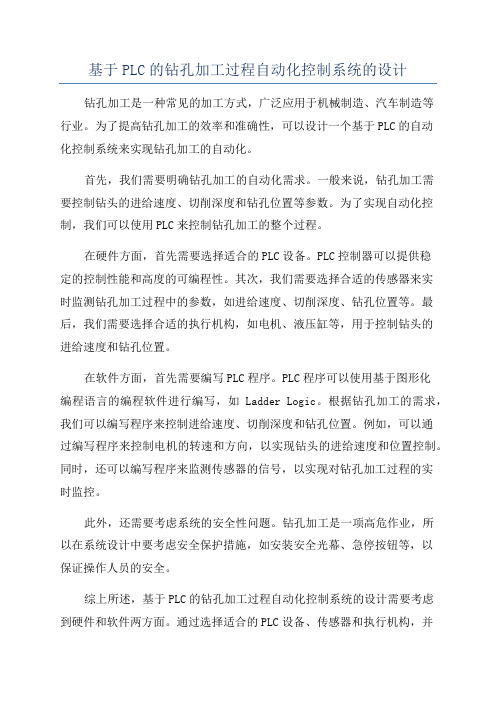
基于PLC的钻孔加工过程自动化控制系统的设计钻孔加工是一种常见的加工方式,广泛应用于机械制造、汽车制造等行业。
为了提高钻孔加工的效率和准确性,可以设计一个基于PLC的自动化控制系统来实现钻孔加工的自动化。
首先,我们需要明确钻孔加工的自动化需求。
一般来说,钻孔加工需要控制钻头的进给速度、切削深度和钻孔位置等参数。
为了实现自动化控制,我们可以使用PLC来控制钻孔加工的整个过程。
在硬件方面,首先需要选择适合的PLC设备。
PLC控制器可以提供稳定的控制性能和高度的可编程性。
其次,我们需要选择合适的传感器来实时监测钻孔加工过程中的参数,如进给速度、切削深度、钻孔位置等。
最后,我们需要选择合适的执行机构,如电机、液压缸等,用于控制钻头的进给速度和钻孔位置。
在软件方面,首先需要编写PLC程序。
PLC程序可以使用基于图形化编程语言的编程软件进行编写,如Ladder Logic。
根据钻孔加工的需求,我们可以编写程序来控制进给速度、切削深度和钻孔位置。
例如,可以通过编写程序来控制电机的转速和方向,以实现钻头的进给速度和位置控制。
同时,还可以编写程序来监测传感器的信号,以实现对钻孔加工过程的实时监控。
此外,还需要考虑系统的安全性问题。
钻孔加工是一项高危作业,所以在系统设计中要考虑安全保护措施,如安装安全光幕、急停按钮等,以保证操作人员的安全。
综上所述,基于PLC的钻孔加工过程自动化控制系统的设计需要考虑到硬件和软件两方面。
通过选择适合的PLC设备、传感器和执行机构,并编写合适的PLC程序,可以实现对钻孔加工过程的自动化控制。
这样可以提高钻孔加工的效率和准确性,降低人工操作的工作强度,提高生产效益。
同时,还需要考虑系统的安全性问题,采取相应的安全保护措施,确保操作人员的安全。
基于PLC控制的数控钻孔机的设计与实现
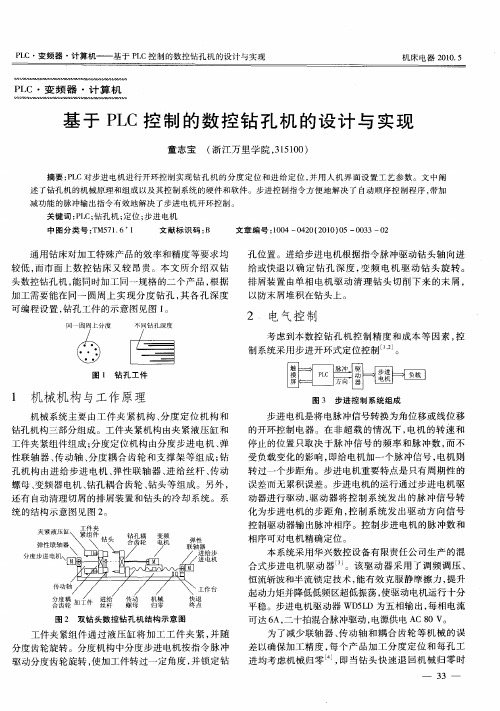
中 图分 类 号 : M 7 . 1 T 516 文献 标 识 码 : B 文章 编 号 : 0 0 2 ( 00 0 03 0 1 4— 40 2 1 )5— 0 3— 2 0
通用 钻床对加工特殊 产品 的效率 和精度等要 求均 较低 , 而市面上数 控 钻床 又较 昂贵。本文 所介 绍 双钻 头数控钻 孑 机 , 同时加 工同一规格 的二个产 品 , L 能 根据
图 2 双钻 头数 控 钻 孔机 结构 示 意 图
工件 夹紧组 件通 过液 压 缸将 加工 工件 夹 紧 , 随 并 分度齿轮旋转 。分度机构 中分度 步进 电机按 指令脉 冲 驱动分度齿 轮旋 转 , 使加工件转 过一定角度 , 并锁定 钻
可达 6 二十拍混合脉冲驱动 , A, 电源供 电 A 0V。 C8 为 了减少联轴 器 、 动轴 和耦 合齿 轮 等机 械 的误 传 差 以确保 加工精度 , 个产 品加 工分 度定 位和 每孔 工 每 进均 考虑机械归 零M , ] 即当钻头 快速 退 回机械 归零 时
应 考虑如下关系。
控制信号和电机脱 机控制信 号 、 变频器正 向启 动信号 、 工件夹紧电磁 阀控制信 号等 。变频器调节频率 以控制 钻头的转速 。触摸屏人机界面设置或修改工件加工技 术参数 , 并显示工作状况 。系统控制 电路见 图 4 。
凶
O Y 2
。ቤተ መጻሕፍቲ ባይዱ
奎
—
:
一
—
以防 末 屑 堆 积 在 钻 头 上 。
2 电气 控 制
考虑到本 数控钻 孔机 控制 精度 和成 本等 因素 , 控 制系统采用 步进开环式定位控 制 。
钻孔动力头的plc控制分析

钻孔动力头的PLC控制分析钻孔动力头在各种钻探和钻孔工作中起着关键的作用,其性能直接影响到工作效率和质量。
随着现代工业的快速发展,自动化程度越来越高,PLC控制系统作为一种重要的控制方式得到了广泛应用。
本文将针对钻孔动力头的PLC控制系统进行分析,介绍其控制原理和实现方法。
钻孔动力头的工作原理首先,了解钻孔动力头的工作原理对于我们理解PLC控制系统非常重要。
在石油、水利、地质等领域,钻孔动力头的主要作用是将钻具传递给井下的钻头,同时驱动钻头进行钻孔作业。
具体来说,钻孔动力头主要由钻杆、传动机构、动力机构等部分组成,其工作原理如下:1.钻杆通过传动机构连接到动力机构;2.动力机构通过电机、液压或气动系统提供动力;3.传动机构将动力传递到钻头,驱动钻头旋转钻孔或钻取地质样品。
PLC控制系统的特点PLC即Programmable Logic Controller,可编程逻辑控制器,也是一种数字控制器,广泛应用于各种现代工业控制系统中。
它拥有以下几个特点:1.开放性:PLC控制系统采用国际标准编程语言,具有开放性,易于维护;2.稳定性:PLC控制系统的硬件和软件都比较稳定,能够长时间运行;3.可编程性:PLC控制系统可以方便地进行编程,可根据需要随时修改程序;4.灵活性:PLC控制系统可根据控制参数的变化自动调整输出信号,实现自动化控制。
钻孔动力头的PLC控制系统钻孔动力头的PLC控制系统可分为三个主要部分:硬件平台、软件平台和外部设备。
其中:1.硬件平台:PLC控制系统的硬件平台主要包括PLC主控板、输入输出模块、通信模块、LCD显示屏等,其中,输入输出模块负责收集钻孔动力头的运行数据和操作命令,通信模块负责与上位机进行通讯,LCD显示屏用于显示工作状态和参数。
2.软件平台:PLC控制系统的软件平台主要由控制程序和监控程序组成。
控制程序主要负责控制钻孔动力头的运行,实现自动化控制;监控程序主要负责对钻孔动力头的状态进行监测和报警。
钻孔动力头PLC控制课程设计说明书
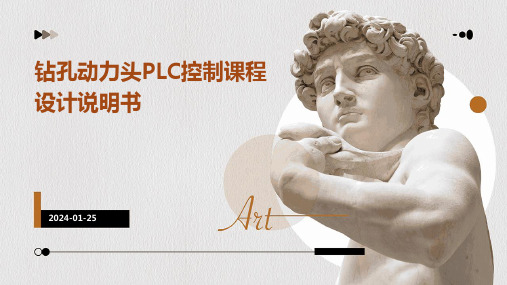
在未来的相关课程中,可以进一步加强对PLC控制理论的学习,包括PLC的工作原理、编程语言、通信协议等方面的知识。
加强PLC控制理论学习
通过增加实践环节,让学生有更多的机会亲自动手进行PLC编程和调试,提高学生的实践能力和动手能力。
增加实践环节
THANKS
感谢您的观看。
04
CHAPTER
软件编程与实现
编程语言选择
模块化
强大的数学运算能力
易于与硬件接口
结构化
特点分析
根据钻孔动力头控制需求,选用结构化文本(ST)作为编程语言。ST语言采用类似于高级编程语言的语法结构,易于理解和维护,同时支持复杂的算法和数学运算,适用于钻孔动力头的精确控制。
ST语言具有以下特点
采用类似于C/C等高级语言的语法结构,代码清晰易懂。
手动/自动模式选择模块
03
根据用户需求选择手动或自动模式,手动模式下用户可以通过操作面板直接控制钻孔动力头的动作,自动模式下则按照预设的程序进行自动控制。
允许用户设置钻孔动力头的运行参数,如转速、进给速度、钻孔深度等。
参数设置模块
当钻孔动力头出现故障时,及时停止设备运行并显示故障信息,方便用户进行维修和调试。
01
实现了钻孔动力头的PLC控制
通过编写PLC程序,成功实现了对钻孔动力头的精准控制,包括启动、停止、转速调节等功能。
02
完成了人机交互界面设计
设计了易于操作的人机交互界面,使得操作人员能够方便地对钻孔动力头进行控制和监控。
通过本次课程设计,我进一步熟悉了PLC编程语言和编程环境,提高了自己的编程能力。
03
在操作面板上显示当前转速、进给速度和位置;
VS
- 1、下载文档前请自行甄别文档内容的完整性,平台不提供额外的编辑、内容补充、找答案等附加服务。
- 2、"仅部分预览"的文档,不可在线预览部分如存在完整性等问题,可反馈申请退款(可完整预览的文档不适用该条件!)。
- 3、如文档侵犯您的权益,请联系客服反馈,我们会尽快为您处理(人工客服工作时间:9:00-18:30)。
• 设计人:田帅伟 谭凡强 • 指导教师:金梅
一、控制任务
1.动力头在原位时,加启动命令后接通电磁阀 F1,动力头快进。 2.动力头碰到限位开关K1后,接通电磁阀F1和 F2,动力头由快进转为工进
3.动力头碰到限位开关K2后,停止进给, 延时10S。 4.延时时间到,接通F3,动力头快速退 回。当原点限位开关K3接通时,动力头快 速退回结束。
*名称
代号
*启动按钮
启动
*快进限位开关 K1
*工进限位开关 K2Fra bibliotek*原点限位开关 K3
*停止按钮
停止
输入点编号 X001 X002 X003 X004 X005
*输出信号 *名称
*前进接触器
*转动接触器
*后退接触器
代号 KM1 KM2 KM3
输出编号 Y000 Y001 Y002
四、梯形图设计
启动后X001置1,F1接 限位开关K1接通
限位开关K2接通
延时10秒后后退 到达K3后停止
五、组态王设计
1.变量命名
2.组态王设计界面
3.运行界面
谢谢观赏
二、动力头的工作循环过程
• 动力头在原位时,加启动命令后接通电磁阀 F1,动力头快进,碰到限位开关K1时接通 电磁阀F1和F2转为工作进给,碰到限位开 关K2时,停止进给。延时10s后接通电磁阀 F3,动力头快速退回,当原点限位开关K3 接通时动力头快退结束。
三、 I/O地址的分配及接线图
*输入信号