冲压模具设计与制造(5-4、5、6)
《冲压模具设计与制造》课程教学大纲DOC

《冲压模具基础》课程教学大纲课程编号:课程英文译名:课内总学时:72学时学分:4。
5学分课程类别:必修课开课对象:汽车制造与装配技术专业执笔人:编写日期:一、课程性质、目的和任务《冲压模具设计与制造》是汽车制造及汽车整形专业的一门主干专业技术课,它是一门将冲压成形加工原理、冲压设备、冲压工艺、冲模设计与冲模制造有机融合,综合性和实践性较强的课程。
其目的是使学生了解冲压变形规律,认识冲压成形工艺方法,冲压模具结构,冲压模具制造方法与手段,掌握冲压模具设计与计算方法,掌握冲压工艺与模具设计方法,冲压模具制造工艺方法,能进行中等冲压零件的冲压工艺编制,冲模设计与冲模制造工艺编制,并培养学生发现问题、分析问题和解决问题的能力,培养学生逻辑思维能力,为毕业设计及毕业以后从事专业工作打下必要的基础。
二、教学基本要求本课程是冲压模具设计与计算,冲压模具结构,模具制造工艺方法为重点。
学外本课程应达到以下基本要求:1、能应用冲压变形理论,分析中等复杂冲压件变形特点,制定合理冲压工艺规程的能力。
2、协调冲压设备与模具的关系,选择冲压设备的能力。
3、熟悉掌握冲模设计计算方法,具备中等复杂冲模结构选择和设计的能力,所设计的冲模应工作可行、操作方便、便于加工和装配,技术经济性好。
4、具备正确选择冲压模具加工方法,制定中等复杂冲模制造工艺和装配工艺的能力.5、初步具备进行多工位级进模设计和制造的能力。
6、初步具备进行分析和处理试模过程中产生的有关技术问题的能力。
三、教学内容及要求:第1章冲压模具设计与制造基础1.1 冲压成形与模具技术概述掌握冲压与冲模概念;冲压工序的分类;冲模的分类;冲模设计与制造的要求;了解冲压现状与发展方向。
1.2 冲压设备及选用了解常见冲压设备;掌握冲压设备的选用;模具的安装。
1.3 冲压变形理论基础掌握塑性变形的概念;理解塑性力学基础;掌握金属塑性变形的一些基本规律;冲压材料及其冲压成形性能.1.4 模具材料选用掌握冲压对模具材料的要求;冲模材料的选用原则;冲模常见材料及热处理要求。
冲压模具的设计与制造

冲压模具的设计与制造冲压模具是机械工程领域中的重要组成部分,广泛应用于各个行业的生产制造中。
它是一种用于将金属板材加工成所需形状的工具,具有高效、精确和经济的特点。
在现代制造业中,冲压模具的设计与制造技术已经成为一个独立的学科,并且对于提高生产效率和产品质量起着重要的作用。
冲压模具的设计是一个复杂的过程,需要综合考虑材料力学、热力学、流体力学等多个学科的知识。
首先,设计师需要根据产品的要求和工艺流程确定模具的结构形式和工作原理。
然后,通过计算和仿真分析,确定模具的尺寸、形状和加工精度。
最后,根据设计结果制作模具,并进行试模和调试,确保其能够满足生产要求。
在冲压模具的制造过程中,材料的选择和加工工艺是关键。
模具材料需要具有高强度、高硬度和良好的耐磨性,以保证模具的使用寿命和加工精度。
常用的模具材料包括工具钢、硬质合金和陶瓷等。
而制造工艺则包括模具的加工、热处理和表面处理等环节,以提高模具的硬度、耐磨性和精度。
冲压模具的设计与制造不仅仅是一个技术问题,也是一个经济问题。
在设计过程中,需要综合考虑成本、生产效率和质量等因素,以实现最佳的经济效益。
同时,制造过程中需要合理安排生产计划和资源配置,以提高生产效率和降低成本。
因此,冲压模具的设计与制造需要设计师、工程师和生产经理等多个角色的紧密合作。
近年来,随着科技的不断进步,冲压模具的设计与制造技术也在不断创新和发展。
例如,计算机辅助设计(CAD)、计算机辅助制造(CAM)和数控机床等先进技术的应用,使得模具的设计和制造更加精确和高效。
同时,新材料和新工艺的引入,也为模具的性能和寿命提供了更多的可能性。
总之,冲压模具的设计与制造是机械工程领域中的重要研究方向,对于提高生产效率和产品质量具有重要意义。
通过综合运用材料力学、热力学、流体力学等多个学科的知识,合理选择材料和加工工艺,以及利用先进技术和创新思维,可以不断提高冲压模具的设计与制造水平,推动制造业的发展。
冲压模具设计与制造(5-5)汇总

第五章 拉深
第五节 其它形状零件的拉深
一、有凸缘圆筒形件的拉深(续)
1.有凸缘圆筒形件的拉深变形程度 及拉深次数
有凸缘圆筒形件的拉深系数取决于 有关尺寸的三个相对比值:dt/d (凸缘的相对直径)、h/d(零件 的相对高度)、R/d(相对圆角半 径)。
根据拉深系数或零件相对高度,判 断拉深次数。
第五章 拉深
2.阶梯形件多次拉深的方法 (1)当任意两相邻阶梯直径之比(dn/dn-1)都不小于相应的圆 筒形件的极限拉深系数 。
拉深方法如图a) (2)若相邻两阶梯 直径之比(dn/dn-1) 小于相应圆筒形件的 极限拉深系数 。 拉深方法如图b)
第五章 拉深
第五节 其它形状零件的拉深
三、曲面形状零件的拉深
1.拉深变形特点 复合类冲压成形工序
球面、锥面、抛物面形状冲件拉深成形共同特点是由拉深 和胀形两种变形方式的复合。
起皱成为此类零件拉深要解决的主要问题。 做到既不起皱又不破裂。
第五章 拉深
第五节 其它形状零件的拉深
三、曲面形状零件的拉深(续)
2.球面冲件的拉深 拉深系数为常数,不能作为工艺设计的根据。
第五章 拉深
复习上次课的内容
1.拉深系数、极限拉深系数及其影响因素 ? 2.拉深次数、各次拉深工序件尺寸的确定?
第五章 拉深
第五节 其它形状零件的拉深
本节在掌握圆筒形件拉深成形的基础之上,分析其它形状 零件的拉深,从中掌握方法。
一、有凸缘圆筒形件的拉深 变形特点:
该类零件的拉深过程,其变形区的应力状态和变形特点与无 凸缘圆筒形件是相同的。但坯料凸缘部分不是全部拉入凹模。
沿周边应力应变分布不均匀。 工艺计算复杂,准确性不高,必要时需要工艺试验。 模具间隙、圆角半径沿周边分布不均匀。
冲压模具设计与制造

•第二章 冲裁工艺与冲裁模设计
PPT文档演模板
•侧刃结 构
冲压模具设计与制造
•第二章 冲裁工艺与冲裁模设计
PPT文档演模板
•侧刃定位误差比较
•1-导料板 2-侧刃挡块 3-侧刃 4-条料
冲压模具设计与制造
•第二章 冲裁工艺与冲裁模设计
PPT文档演模板
•尖 角 形 侧 刃
冲压模具设计与制造
•第二章 冲裁工艺与冲裁模设计
•1.导料销、导料板 •导料销:•两个,位于条料的同侧, •从右向左送料时,导料销装在后侧; •从前向后送料时,导料销装在左侧。 •结构形式:•固定式、活动式
PPT文档演模板
冲压模具设计与制造
•第二章 冲裁工艺与冲裁模设 计•第九节 冲裁模零部件设计
•二、定位零件(续)
•1.导料销、导料板(续)
•导料板:•设在条料两侧
最小搭边得到保证。 •结构形式:•①弹簧式侧压装置(图2.9.15a)
•②簧片式侧压装置 •③簧片压块式侧压装置 •④板式侧压装置
•不宜设置侧压装置的场合:•①板料厚度在0.3mm以下的薄板;
•②辊轴自动送料装置的模具。
PPT文档演模板
冲压模具设计与制造
•第二章 冲裁工艺与冲裁模设 计•第九节 冲裁模零部件设计
•第二章 冲裁工艺与冲裁模设计
PPT文档演模板
•1-内六角螺钉 2-销钉 3-模柄 4-卸料螺钉 5-垫板 6-上模座 7-凸模固定板 8、9、10-凸模 11-导料板 12-承料板 13-卸料板 14-凹模 15-下模座 16-侧刃 17-侧刃挡块
•双侧刃定距的冲孔落料级进 模
冲压模具设计与制造
冲压模具设计与制造
•第二章 冲裁工艺与冲裁模设计
《冲压模具设计与制造》知识点汇总
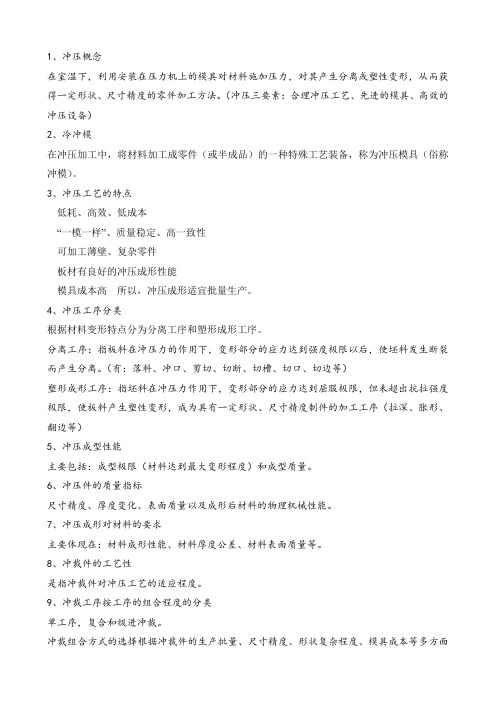
1、冲压概念在室温下,利用安装在压力机上的模具对材料施加压力,对其产生分离或塑性变形,从而获得一定形状、尺寸精度的零件加工方法。
(冲压三要素:合理冲压工艺、先进的模具、高效的冲压设备)2、冷冲模在冲压加工中,将材料加工成零件(或半成品)的一种特殊工艺装备,称为冲压模具(俗称冲模)。
3、冲压工艺的特点低耗、高效、低成本“一模一样”、质量稳定、高一致性可加工薄壁、复杂零件板材有良好的冲压成形性能模具成本高所以,冲压成形适宜批量生产。
4、冲压工序分类根据材料变形特点分为分离工序和塑形成形工序。
分离工序:指板料在冲压力的作用下,变形部分的应力达到强度极限以后,使坯料发生断裂而产生分离。
(有:落料、冲口、剪切、切断、切槽、切口、切边等)塑形成形工序:指坯料在冲压力作用下,变形部分的应力达到屈服极限,但未超出抗拉强度极限,使板料产生塑性变形,成为具有一定形状、尺寸精度制件的加工工序(拉深、胀形、翻边等)5、冲压成型性能主要包括:成型极限(材料达到最大变形程度)和成型质量。
6、冲压件的质量指标尺寸精度、厚度变化、表面质量以及成形后材料的物理机械性能。
7、冲压成形对材料的要求主要体现在:材料成形性能、材料厚度公差、材料表面质量等。
8、冲裁件的工艺性是指冲裁件对冲压工艺的适应程度。
9、冲裁工序按工序的组合程度的分类单工序,复合和级进冲裁。
冲裁组合方式的选择根据冲裁件的生产批量、尺寸精度、形状复杂程度、模具成本等多方面考虑(1)生产批量(2)冲裁件的尺寸精度(3)对工件尺寸、形状的适应性(4)模具制造、安装调整和成本(5)操作方便与安全10、冲模的分类(1)按工序性质分:落料模、冲口模、切断模、整修模、弯曲模、拉深模,成形模等。
(2)按工序组合程度分为:单工序模、级进模、复合模。
级进模:一次行程中,在一副模具的不同位置上完成不同的工序。
因此对工件来说,要经过几个工位也即几个行程才能完成。
而对模具来说,则每个行程都能冲压出一个制件。
冲压模具设计与制造_冲压工艺过程设计的步骤与内容
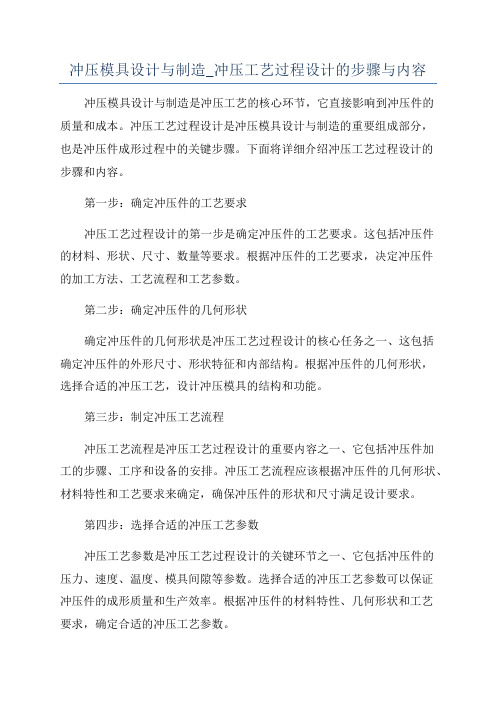
冲压模具设计与制造_冲压工艺过程设计的步骤与内容冲压模具设计与制造是冲压工艺的核心环节,它直接影响到冲压件的质量和成本。
冲压工艺过程设计是冲压模具设计与制造的重要组成部分,也是冲压件成形过程中的关键步骤。
下面将详细介绍冲压工艺过程设计的步骤和内容。
第一步:确定冲压件的工艺要求冲压工艺过程设计的第一步是确定冲压件的工艺要求。
这包括冲压件的材料、形状、尺寸、数量等要求。
根据冲压件的工艺要求,决定冲压件的加工方法、工艺流程和工艺参数。
第二步:确定冲压件的几何形状确定冲压件的几何形状是冲压工艺过程设计的核心任务之一、这包括确定冲压件的外形尺寸、形状特征和内部结构。
根据冲压件的几何形状,选择合适的冲压工艺,设计冲压模具的结构和功能。
第三步:制定冲压工艺流程冲压工艺流程是冲压工艺过程设计的重要内容之一、它包括冲压件加工的步骤、工序和设备的安排。
冲压工艺流程应该根据冲压件的几何形状、材料特性和工艺要求来确定,确保冲压件的形状和尺寸满足设计要求。
第四步:选择合适的冲压工艺参数冲压工艺参数是冲压工艺过程设计的关键环节之一、它包括冲压件的压力、速度、温度、模具间隙等参数。
选择合适的冲压工艺参数可以保证冲压件的成形质量和生产效率。
根据冲压件的材料特性、几何形状和工艺要求,确定合适的冲压工艺参数。
第五步:设计冲压模具设计冲压模具是冲压工艺过程设计的重要内容之一、它包括冲压模具的结构、尺寸、材料和加工工艺等方面。
根据冲压件的几何形状、工艺要求和生产效率要求,设计合理的冲压模具。
冲压模具应具备高精度、高强度和高耐磨性的特点,确保冲压件的成形质量和生产效率。
第六步:制造冲压模具制造冲压模具是冲压工艺过程设计的最后一步。
它包括冲压模具的加工工艺、装配和调试等环节。
冲压模具的制造应根据设计要求和工艺要求,选择合适的材料和加工工艺,确保冲压模具的质量和寿命。
制造冲压模具还需要进行装配和调试,确保冲压模具的合理性和可靠性。
总结:冲压工艺过程设计是冲压模具设计与制造的重要环节,它直接关系到冲压件的质量和生产效率。
冲压模具的设计与制造分析
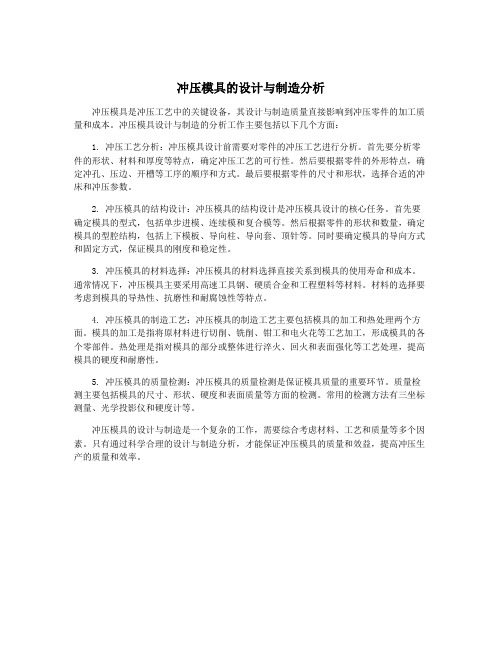
冲压模具的设计与制造分析冲压模具是冲压工艺中的关键设备,其设计与制造质量直接影响到冲压零件的加工质量和成本。
冲压模具设计与制造的分析工作主要包括以下几个方面:1. 冲压工艺分析:冲压模具设计前需要对零件的冲压工艺进行分析。
首先要分析零件的形状、材料和厚度等特点,确定冲压工艺的可行性。
然后要根据零件的外形特点,确定冲孔、压边、开槽等工序的顺序和方式。
最后要根据零件的尺寸和形状,选择合适的冲床和冲压参数。
2. 冲压模具的结构设计:冲压模具的结构设计是冲压模具设计的核心任务。
首先要确定模具的型式,包括单步进模、连续模和复合模等。
然后根据零件的形状和数量,确定模具的型腔结构,包括上下模板、导向柱、导向套、顶针等。
同时要确定模具的导向方式和固定方式,保证模具的刚度和稳定性。
3. 冲压模具的材料选择:冲压模具的材料选择直接关系到模具的使用寿命和成本。
通常情况下,冲压模具主要采用高速工具钢、硬质合金和工程塑料等材料。
材料的选择要考虑到模具的导热性、抗磨性和耐腐蚀性等特点。
4. 冲压模具的制造工艺:冲压模具的制造工艺主要包括模具的加工和热处理两个方面。
模具的加工是指将原材料进行切削、铣削、钳工和电火花等工艺加工,形成模具的各个零部件。
热处理是指对模具的部分或整体进行淬火、回火和表面强化等工艺处理,提高模具的硬度和耐磨性。
5. 冲压模具的质量检测:冲压模具的质量检测是保证模具质量的重要环节。
质量检测主要包括模具的尺寸、形状、硬度和表面质量等方面的检测。
常用的检测方法有三坐标测量、光学投影仪和硬度计等。
冲压模具的设计与制造是一个复杂的工作,需要综合考虑材料、工艺和质量等多个因素。
只有通过科学合理的设计与制造分析,才能保证冲压模具的质量和效益,提高冲压生产的质量和效率。
冲压模具设计与制造

冲压模具设计与制造冲压模具设计与制造是现代工业制造中常用的一种技术和方法。
冲压模具是用于模压薄板材料的一种工具,通过将板材材料放入模具中,然后用压力将其加工成所需形状或大小的零件。
冲压模具广泛应用于汽车制造、电子设备制造、家电制造等行业,对于提高生产效率和产品质量具有重要意义。
冲压模具设计与制造涉及多个方面的知识和技能,包括材料力学、机械设计、热处理工艺、加工工艺等。
在整个设计制造过程中,需要从产品设计、模具设计、模具加工、模具调试等多个环节中进行协调和配合,以确保最终产品的质量和成本要求。
冲压模具设计的第一步是根据产品的结构和要求进行模具设计。
设计过程中需要考虑到产品的尺寸、形状、材料等因素,并结合模具的特点和加工工艺的要求进行合理的设计。
模具设计包括三维绘图、结构设计、零件分解和装配等工作。
在模具制造过程中,材料的选择和工艺的控制对于模具的质量和耐用性有重要影响。
冲压模具常用的材料有高速钢、硬质合金等,这些材料具有高强度、良好的耐磨性和热稳定性。
在材料选择的基础上,还需要通过热处理等工艺对模具进行强化和改善材料的性能。
冲压模具的加工过程通常包括铣削、钳工、磨削和电火花等多种工艺。
这些工艺的选择和控制对于模具的精度和质量具有决定性的影响。
在加工过程中,需要根据模具的设计图纸,合理选择加工工艺和设备,保证加工过程的精度和质量。
模具制造完成后需要进行调试和试模工作。
调试过程中需要对模具进行调整和修正,以满足产品的要求。
如果出现问题,需要及时进行处理和修复,并通过试模检测对加工质量进行验证。
冲压模具设计与制造需要设计师和制造工程师的协作和配合,要求相关专业背景和经验。
设计师需要具备良好的创新能力和设计思维,能够将产品的要求转化为可行的模具设计方案。
制造工程师需要具备良好的工艺控制能力和技术经验,能够根据设计要求进行模具的加工和调试。
- 1、下载文档前请自行甄别文档内容的完整性,平台不提供额外的编辑、内容补充、找答案等附加服务。
- 2、"仅部分预览"的文档,不可在线预览部分如存在完整性等问题,可反馈申请退款(可完整预览的文档不适用该条件!)。
- 3、如文档侵犯您的权益,请联系客服反馈,我们会尽快为您处理(人工客服工作时间:9:00-18:30)。
复习上次课的内容
1.其它冲压成形工序的共同特点是什么? 哪些属于伸长类成形?哪些属于压缩类成形?其成形极限各自主要受什么限制?
2.当工件的竖边高度较高时,有哪些方法可成形?
a
1
第五章 其它成形工艺与模具设计
第四节 缩口
缩口: 将管坯或预先拉深好的圆筒形件通过缩口
模将其口部直径缩小的一种成形方法。
旋压: 将平板或空心坯料固定在旋压机的模具上,在坯料随机床主轴转动的同时,
用旋轮或赶棒加压于坯料,使之产生局部的塑性变形。
优点: 设备和模具都较简单,除可成形各种曲线构成的旋转体外,还可加工相当复杂
形状的旋转体零件。 缺点:
生产率较低,劳动强度较大,比较适用于试制和小批量生产。
a
8
第五章 其它成形工艺与模具设计
径和间隙较小。
整形力F可按下式计算:
F Ap
a
16
第五章 其它成形工艺与模具设计
第六节 校形
三、空间形状零件的整形(续)
弯曲件的整形方法: 无凸缘拉深件的整形:
通常取整形模间隙等于(0.9~0.95)t,即采用变薄拉深 的方法进行整形。
带凸缘拉深件的整形部位常常有: 凸缘平面、侧壁、底平面和凸模、凹模圆角半径。
当 t1 t1min时, max min
所以极限变薄率
max 和极限半锥角 min 的关系为:
ma xttt1min1si nmin
a
13
第五章 其它成形工艺与模具设计
第六节 校形
一、校形的特点及应用
校形: 通常指平板工序件的校平和空间形状工序件的整形。
目的: 使冲压件获得高精度的平面度、圆角半径和形状尺寸。
(2)局部变形,因此变形力比冷挤压小得多。
(3)经强力旋压后,材料晶粒紧密细化,提高了强度,表面质量也比较好,表面粗糙 度Ra可达0.4μm。
a
12
第五章 其它成形工艺与模具设计
第五节 旋压
二、变薄旋压工艺(续)
2.变薄旋压成形极限
变形程度 tt11t11sin
t
t
用模具的半锥角
也可以表示变薄旋压的变形程度。
平板零件的校平模形式: 光面校平模、齿形校平模
加热校平法
校平力可按下式计算:
F Ap
a
15
第五章 其它成形工艺与模具设计
第六节 校形
三、空间形状零件的整形
空间形状零件的整形: 指在弯曲、拉深或其它成形工序之后对工序件的整形。
目的: 使工序件某些形状和尺寸达到产品的要求,提高精度。
整形模的特点: 与前工序的成形模相似,但对模具工作部分的精度、粗糙度要求更高,圆角半
一、缩口变形特点及变形程度
坯料变形区受两向压应力的作用 缩口的变形程度用缩口系数m表示
md/D
a
2
第五章 其它成形工艺与模具设计
第四节 缩口
二、缩口工艺计算
1.缩口次数
若工件的缩口系数m小于允许的缩口系数时,则需进行多次缩口,缩口次数n按 下式估算:
n lgmlgdlgD
lgm0
lgm0
a
3
第五章 其它成形工艺与模具设计
m mi n0.6~0.8
圆锥形件的极限旋压系数可取为:
m min 0.2~0.3
当工件需要的变形程度较大(即m较小)时,便需多次旋压。多次旋压时必须进行 中间退火。
a
11
第五章 其它成形工艺与模具设计
第五节 旋压
二、变薄旋压工艺
1.变薄旋压变形特点
(1)无凸缘起皱,也不受坯料相对厚度的限制,可一次旋压出相对深度较大的零件。 一般要求使用功率大、刚度大并有精确靠模机构的专用强力旋压机。
图5.4.2c所示工件:
Hh11 41 D d D2d2
a
5
第五章 其它成形工艺与模具设计
第四节 缩口
二、缩口工艺计算
4.缩口力 将图5.4.2a所示锥形缩口件,在图5.4.3a所示无支承缩口模上进行缩口时,其
缩口力F可用下式计算:
FK 1.1 D bt 1D d (1c t)gc1 o s
a
17
第五章 其它成形工艺与模具设计
作业布置:
思考与练习题3、4、5、7。
a
18
第五章 其它成形工艺与模具设计
缩口工件
a
19
第五章 其它成形工艺与模具设计
校平和整形工序的共同特点: (1)只在工序件局部位置使其产生不大的塑性变形; (2)模具的精度比较高; (3)所用设备最好为精压机。若用机械压力机时,机床应有较好的刚度,并需要装 有过载保护装置。
a
14
第五章 其它成形工艺与模具设计
第六节 校形
二、平பைடு நூலகம்零件的校平
校平方式: 模具校平、手工校平、在专门校平设备上校平。
旋压的基本要点: (1)合理的转速 (2)合理的过渡形状 (3)合理加力
a
10
第五章 其它成形工艺与模具设计
第五节 旋压
一、普通旋压工艺(续)
2.旋压成形极限
变形程度以旋压系数m表示:
m d
D
坯料直径D可按等面积法求出,但旋压时材料的变薄较大些,因此应将理论计算值
减小5%~7%。
圆筒形件的极限旋压系数可取为:
第五节 旋压
一、普通旋压工艺
1.普通旋压变形特点
点接触 两种变形: ①赶棒直接接触的材料产生局部凹陷 的塑性变形; ②坯料沿着赶棒加压的方向大片倒伏。
1-顶块2-赶棒3-模具4-卡盘 1 ~(9 系坯料的连续位置)
a
9
第五章 其它成形工艺与模具设计
第五节 旋压
一、普通旋压工艺(续)
1.普通旋压变形特点(续)
第四节 缩口
二、缩口工艺计算
2.颈口直径
多次缩口时,最好每道缩口工序之后进行中间退火,各次缩口系数可参考下面公 式确定:
首次缩口系数
m1 0.9m0
后各次缩口系数
m n(1.0~ 51.1)0 m 0
各次缩口后的颈口直径则为:
d1 m1D
d 2 m nd1 m1m n D
d3
mnd2
m
1
m
2 n
式中
――冲件与凹模接触面摩擦系数;
K ――b ――材速料度抗系拉数强,在度曲;轴压力机上工作时K=1.15。
其余符号如图5.4.2a所示。
a
6
第五章 其它成形工艺与模具设计
第四节 缩口
三、缩口模结构
不同支承方法的缩口模 带有夹紧装置的缩口模 缩口与扩口复合模
a
7
第五章 其它成形工艺与模具设计
第五节 旋压
D
dn
m n d n1
m
1
m
n n
1
D
a
4
第五章 其它成形工艺与模具设计
第四节 缩口
二、缩口工艺计算
3.坯料高度 缩口前坯料高度H按下面公式计算:
图5.4.2a所示工件: 图5.4.2b所示工件:
H1.05 h18D D 2sid n21 D d
H1.05 h1h2
D d8 D D 2sd i 2n 1 D d