最新汽车行业审核资料-福特Q1条款要求
标准条款
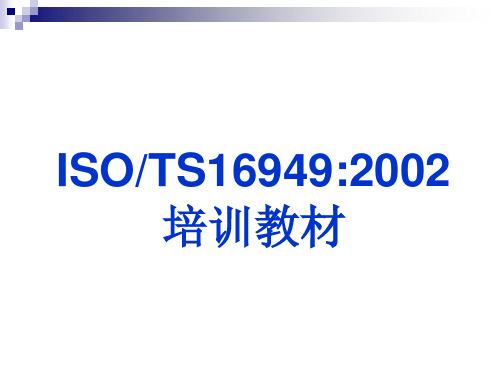
性的联合会。制定国际标准的工作通常由ISO的技术委员会完成。各成
员团体若对某技术委员会确定的项目感兴趣,均有权参加该委员会的工
作。与ISO保持联系的各国际组织(官方的或非官方的)参加有关工作。
ISO与国际电工委员会(IEC)在电工技术标准化方面保持紧密的合作关
系。
技术委员会的主要任务是制定国际标准。由技术委员会通过的国际
P — 策划:根据顾客的要求和组织的方针,为提供结果建立必要的 目标和过程;
D — 实施:实施过程;
C — 检查:根据方针、目标和产品要求,对过程和产品进行监视和测量, 并报告结果;
A — 处置:采取措施,以持续改进过程业绩。
引言
0.3 与ISO 9004的关系 ISO9001与ISO9004已制定为一对协调一致的质量管理体系标准,他们
引言
0.3.1 IATF关于ISO/TS16949:2002的指南 《IATF关于ISO/TS16949:2002的指南》是一份包含了推荐性的汽车行业
实践、范例、图解和解释的文件,并对符合本标准要求的应用提供帮助。 此IATF指南文件不拟用于认证或合同的目的。
0.4 与其他管理体系的相容性 为了使用者的利益,本标准与ISO14001:1996相互趋近,以增强两类标
1 范围
1.2 应用 本标准规定的所有要求是通用的,旨在适用于各种类型、不同规模和
提供不同产品的组织。 当本标准的任何要求因组织及其产品的特别而不适用时,可以考虑对
其进行删减。 除非删减仅限于本标准第7章中那些不影响组织提供满足顾客和适用
法律法规要求的产品的能力或责任的要求,否则不能声称符合本标准。 本标准仅允许在组织没有产品设计和开发责任的情况下删减与7.3有
APQP 第三版 中文
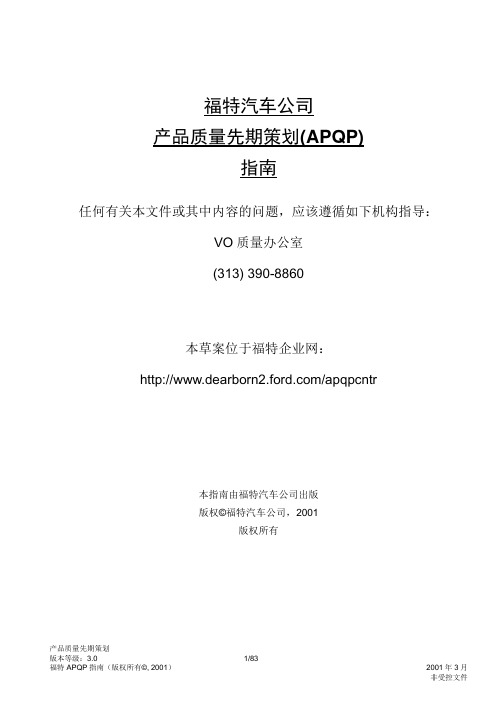
APQP 报告程序……………………………………………………………………………………10
APQP 状态报告流程图…………………………………………………………………………………11 APQP 状态报告…………………………………………………………………………………………12 APQP 状态报告表格……………………………………………………………………………………13 填写状态报告表格………………………………………………………………………………………14 质量事件检查表…………………………………………………………………………………………15 风险评估…………………………………………………………………………………………………15
产品质量先期策划
版本等级:3.0
8/83
福特 APQP 指南(版权所有©, 2001)
2001 年 3 月 非受控文件
要素(续)
最后级别的一个附加更改是两个要素的结合,“生产件批准(PSW)”和“MRD 的 PSW 零 件交付”合并为一个要素:
生产件批准程序(PPAP)/零件提交保证书(PSW)
产品质量先期策划
版本等级:3.0
3/83
福特 APQP 指南(版权所有©, 2001)
2001 年 3 月 非受控文件
目录(续)
附录部分…………………………………………………………………………………………52
福特APQP和Q1质量管理(PPT 111页)
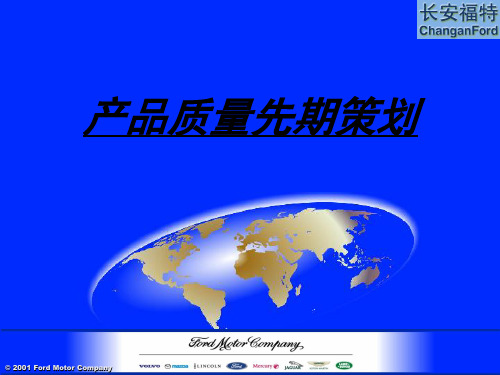
自动执行小组 (AIG) – 总监包括 VLD 和执行质量总监 质量总监 运营管理
项目
里程碑评审和/或设计评审 定期的 PST/PMT
小组现场供方评审
按新车制造进度而订
10
© 2001 Ford Motor Company
外部供方 和 APQP
APQP 适用于高影响度和非高影响度内部和外部供 方。
Q/R 小组 PTO Visteon
与 Q/R DAM 评 审里程碑
里程碑评审
VO STA – 外部
应用APQP为样件制造、试生产和 生产开发控制计划。
8
© 2001 Ford Motor Company
APQP的实施
VO
员工的全面支持 小组参与 网页上的状态报告
CC LR LS
J1
FS
CFMEA
50 41
36 33.5
25.5
14.5
8
4.5 3.5
0
26-6
© 2001 Ford Motor Company
4 – 设计评审
定义:
定期安排会议验证设计,并与管理层监控 计划进度
SI
SC PH
PA
ST
PR
CP
CC LR LS
J1
FS
50 41
36 33.5 30 25.5
24
© 2001 Ford Motor Company
3 – 设计FMEA
定义:
系统的方法,用以确定潜在设计失效模式 和相关的原因被考虑和指出
SI
SC PH
PA
ST
PR
CP
CC LR LS
福特Q1培训教材(1)
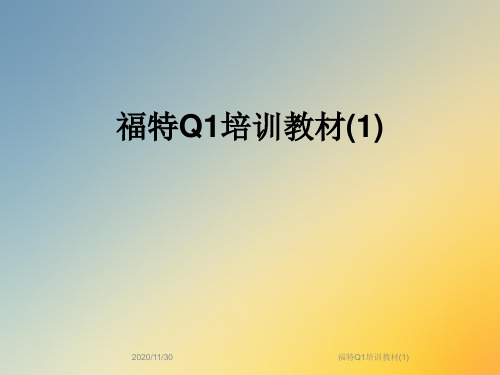
II. Significant
• Low Impact on Customer Satisfaction / Safety
• Poor Performance
IV. Autonomous
• Low Impact on Customer Satisfaction / Safety
• Good Performance
• Q1是福特执行的标准。主要作用为区分 制造现场的等级,并通过运用持续的、 可理解的矩阵工具来保证高质量。Q1已 经变成全球认可的质量品牌。
福特Q1培训教材(1)
Q1是什么? What is Q1?
❖Ford Motor Company exclusive designation ❖它是福特汽车公司所特有的 ❖Set of fundamental quality and manufacturing disciplines ❖基本的质量和制造规则 ❖Drives supplier's continual improvement ❖帮助供应商不断持续改进 ❖Put tools in place to maintain excellence ❖用一些工具维持最佳 ❖Improve each passing year ❖每年都得到提升
福特Q1培训教材(1)
How to archive Q1? 如何获得Q1?
福特Q1培训教材(1)
Q1基本要求 Q1 Basically requirement
• Any external suppliers manufacturing facility that currently supplies parts to Ford is eligible for consideration
+国际汽车生产线安装标准
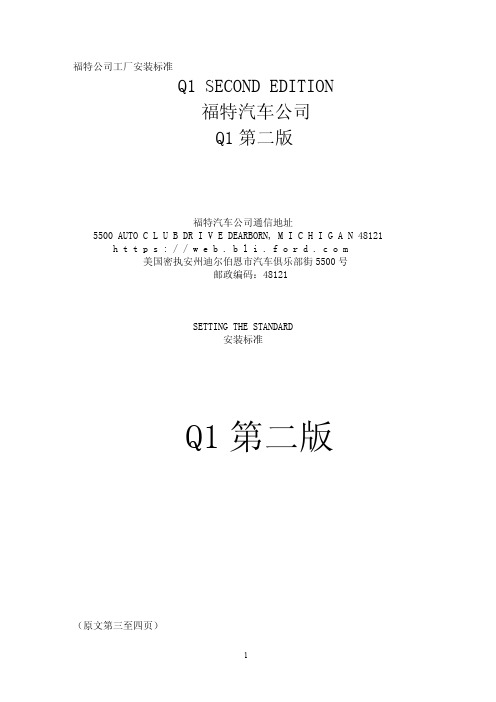
基本原则:工厂遭遇停产。由于关系到福特工厂,要提前通知福特工厂和供 应商技术服务部(STA),认可其存在的潜在的现场隐患。 4.现场评审(生产和服务)
部分现场评审选址中的关注因素已为供应商删去。现场自我评审的次数应基 于质量分段要求。现场整体评审遵循下列要求: •每 6 个月现场分割为 1-2 段 •每 12 个月现场分割为 3-4 段 对 Q1 的影响的现场评审得分也已修改,其两步骤由福特公司现场工程师修改。 5. 现场评审(生产和服务) 其步骤在下列情况下会触发问题: •现场评审频率迟于要求的 6-12 个月 •纠正行动计划未能按福特公司现场工程师的指示,在 30 天内提交。 •现场行动计划在执行中无效,首次 STA 行动结果为 150 分,第二次 STA 行动结果 为 250 分且丧失 Q1 资格。
Q1 是什么? 它是一套基本的质量与制造规则体系。随着时间的推进,它能持续确保供应 商并促使供应商不断改进服务质量。 我们期望供应商达到一定的分数值,让制度体系到位并保持优质服务和随年 改进。 但是,我们并不期望供应商自主达到 Q1 要求,这是一种关联体系。 福特公司在整个 Q1 质量发展历程中,坚持向供应商提供专家和协助。 Q1 将原则放在恰当的位置,协调福特和供应商之间的关系,从而获取优越性 与合作导向。 方法:Q1 应用了几个重要的方法,以确定供应商是否符合 Q1 的质量要求: 同样的测量也将用于确定哪一家供应商能保持 Q1 原则。第二版 Q1 把不断提高制 造现场的评审水平作为驱使他们持续改善的重要工具。经修改的现场评审依据《服 务质量体系》(QOS)做出了更高的要求,包括履行担保、投放市场、质量变动和 加工的可变性,提供持续获得改进的构架。 更新概要:Q1 第二版中的要求已于 2003 年 6 月 1 日实施生效,更新内容的 简介详见下一章节。
02 顾客特定要求评审表-ford
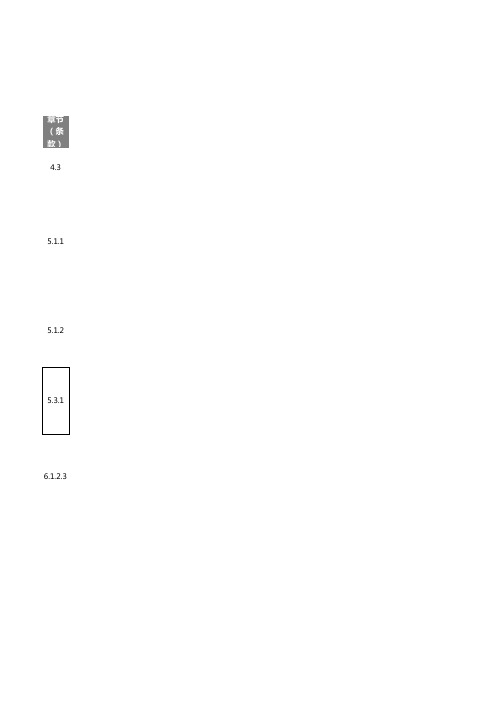
章节(条款)4.35.1.1 5.1.26.1.2.37.1.3.17.1.5.3 .2 7.2.17.5.3.2 .18.18.2.1 8.2.3.1 .18.2.3.1 .28.2.3.1 .3 8.3.1.18.3.2.18.3.48.3.4.48.4.1.3 8.4.2.18.4.2.2 8.4.2.38.4.2.4 8.5.1.2 8.5.2 8.6.18.6.2 8.6.3 8.6.6 8.7.1.19.1 9.1.1.19.1.2 9.1.2.19.2.2.39.3.1.1 9.3.210.2.1 10.2.2 10.2.5更多免费质量管理相关资料,请微信搜索公众号“体系君”,或扫码关注。
要求(具体描述)Determining the scope of the quality management systemCorporate Responsibility:The organization shall comply with Basic Working Conditions in the Global Terms and Conditions and the related Supplier Social Responsibility and Anti-CorruptionRequirements Web-Guide .组织应遵守基本的全球条款和工作条件条件,相关供应商的社会责任和反腐败要求。
The organization is also encouraged to adopt and enforce a similar code with Ford’s Policy组织还应鼓励采取和实施类似ford的代码与政策.Customer focus:The organization shall demonstrate enhanced customer satisfaction by meeting the continuous improvement requirements of Q1, as demonstrated in the organization’s QOS (Quality Operating System).组织必须通过满足Q1持续改善的要求来证实顾客满意的提高,并在组织的QOS(质量运行系统)中被证实。
汽车行业审核 福特Q 条款要求
条款要求 量具标准可追溯至符合国家标准或同等的国际标准。量具校准和维护按相应的日程安排表和规范实施。日程安排 表和規範實施。 供应商对防错装置进行了定期评估(建议条款,非强制) 供应商有书面程序指导如何在生产、测试、实验,储存、办公等区域的各个阶段,辨识合格零件。 针对发运到福特后的产品(包括返工产品),供应商能进行批次追蹤。 供应商采取措施确保生产过程控制搬运、储存和包装,以防止产品损坏或腐蚀,并保持产品质量。 供应商遵守福特包装要求(表格150-北美;表格EU1121-欧洲),在拆包时,可使用并按要求遵守福特包装说明。 所有的检验、测量、和测试,包括工程规范(ES)和材料规格(MS), 都根据控制计划、指导书、和/或执行程序以确 保满足产品要求。 有适当的应対计划指示在测试或检查不通过时,将采取何种行动。这包括了在各种状况下的产品补救措施和通知 顾客政策。 提供热处理零件的供应商和分供方,需要满足福特的制造标准W-HTX并满足CQI-9特殊流程:热处理系统评审相关 要求。为了减少脆化的风险,热处理的钢零件需要满足福特材料规格WSS-M99A3-A。 T1供应商负责确保所有供应商根据CQI-9进行年度评审。 供应商有一套维护体系包括应対、预防和预见性的维护。该维护体系支持过程能力的改善 PM按计划实施情况需进行定期(至少每季度一次)管理评审。管理人员审查轿正措施计划,以确保积压未完(逾 期)的维护事项列入目前PM进度。管理阶层进行评估,以决定是否有减少机器/过程停止时间。 供应商针対工厂的清洁、整理、人体工学、和工作条件有持续不断的改进计划,并至少每月一次稽查他们的设备 。供应商能证明其管理团队正追踪持续不断的改进计划。 供应商采取措施减少无关的材料、碎屑、残材、污染物、过度的油污等。这些都会对零件的质量造成负面影响。 针対现有的零件及新车型零件,供应商将精益生产、6sigma原则融入到即时生产,消除浪费,并以团队导向的问 题解决手法来推动质量、过程能力及制造效率的持续改进。 供应商的QOS系统包括有关键的生产和6sigma衡量指标。至少要有两个精益生产衡量指标和一个6sigma衡量指 标来显示过去六个月内过程改进的趋势或历史。精益生产和6sigma衡量指标包括了:进货至出货(DTD)、首次通 过率(FTT)、设备总效率(OEE)、增值百分比(PVA)和Cpk。 供应商运用有组织的问题解决方法(例如,Global 8D)来处理顾客关注和客户抱怨。 建立供应商生产人员和协助人员能沟通质量问题的手法。矫正措施报告须提供至供应商的管理团队审查。矫正措 施影印传达到供应商各相关的部门。 供应商须有一套程序能及时的対应顾客厂方关心的问题。 供应商需审查过去所开发的产品、总结教训,并将相关经验运用到未来新产品的开发。
Q1介绍
Q1不是什么?
Q1不是独立获得的——是引导福特和供
应商之间的关系
获得Q1的好处
得到福特的认可(Q1旗帜和标志) 用于宣传和广告 得到世界优秀供应商的奖励 成为福特首选的供应商(只有Q1工厂才
会在选点中被考虑)
如何获得Q1
Q1基本要求
★适用于所有为福特工厂供货的外部供 应商的制造现场 现场表现 供应商制造现场在以下五个重要方面必 须做到最好 ★合格的体系 ★持续的实际业绩 ★现场的行动计划 ★满意的顾客 ★持续改进
Q1分数
召回(-250分)
六个月内由于供应商(1级、2级、3级…) 的责任造成召回 供应商工厂减去250分 Q1状态立即取消 停止发车(0-250分) 六个月内有2个或更多的停止发车 供应商工厂减去250分 Q1状态立即取消
Q1分数
PPM(+100到-250分)
6个月的PPM(生产件和售后件)超过同 类商品的100%或更多,同时PPM值大于 110 供应商减去250分 Q1状态撤消 如果比同类商品平均值低一倍加 100分 PPM值为60或更少加100分
行动计划
二、证明制造过程能力
1、分供方质量体系管理 2、进料质量控制 3、控制计划/作业指导书 4、过程变异监控(CC,SC,HIC的SPC控制) 5、量具的 校准和使用 6、零件标识、不合格零件、包装和发货的管理 7、测试、工程规范 8、预防性维护(PM)/仓储管理 9、制造过程流程、精益生产 10、问题解决,纠正措施
现场行动计划
完整的现场评审要求:
一、二类供应商每六个月进行一次; 三、四类供应商每十二个月进行一次 现场评审频率比要求的6个月/12个月高 纠正计划在现场评审后30天内必须提交 给STA 纠正计划能有效执行
各大主机厂供应商审核要求一览行业必备宝典
在汽车行业的朋友,相信你一定听说过“审核”,今天莱茵公司刚审核好,明天大众的审核员又要过来了,福特的Q1审核近期又要开始准备了!这些“审核”搞晕你了吗?汽车上的零部件太多了,一辆汽车上有上万个零件,除了动力总成和少部分零件外,绝大部分的零件都是由供应商来制造甚至是设计的。
要知道,除了极少数的零件,主机厂是没有入库检验的,想想如果这么多零件都要检验的话,这会是一个多么壮观的场景。
很多人可能在想,那主机厂是如何保证这么多零件的质量的呢?主机厂的思路不再局限在零件质量上了,过程和体系质量也成为其关注的一部分。
如何去理解零件、过程和体系的关系?我们以快餐品牌KFC(肯德基)举个例子。
KFC这么多家门店,我们去吃的时候,味道、感受是一样的,因为:他们的人员接受的培训是一样的;所使用的设备(锅)品牌型号是一致的;原材料(鸡、土豆)是统一配送的;奶油挤多少,油几度,炸几分钟这些方法都是标准化的;整个店面、厨房环境也是统一装潢的;如果说味道、感受是零件(产品)质量。
上面提到的人、机、料、法、环就是过程质量。
过程质量是如何保证的呢?靠体系质量,经常我们会调换个顺序,就是质量体系。
质量体系有这么牛?竟然保证了过程,而过程又保证了产品。
作为爷爷辈的它到底有哪些呢?早期的时候比较混乱,美国有QS 9000、意大利有AVSQ、法国有EAQF、德国有VDA6.1。
后来将要求统一了,形成ISO/TS 16949(现为IATF 16949),当然,之前的认证大多都还保留着。
比如VDA6.1,现在的大众公司需要过ISO/TS 16949和VDA6.1两个体系的认证。
这些体系的认证多为第三方进行。
什么叫第三方?指两个相互联系的主体之外的某个客体,叫作第三方,比如你给大众供货,你自己叫自己第一方,你叫大众第二方,没有直接供货的机构(比如莱茵认证机构)叫第三方。
第三方的(体系)审核讲完了,下面我们就来看看第二方(各大主机厂)在审核方面的要求。
Q1介绍
Done on Time
CAP Acceptable
✔ ✘ ✔
CAP Late
+ ✔ + ? + ✘
CAP unacceptable
= = =
0 -50,-150,-250 -50,-150,-250
超 期 , 系 统 自 动 扣 除 超 期 , 第 一 次 提 醒 超 期 , 第 二 次 提 醒
Page 23
Ⅲ. Q1流程
Q1 Attainment
供应商满足 Q1要求 ↓
Q1简报
1.Site STA ↓ 2.Site STA Sup./Mgr. 3.高级经理 Q1 MSA终审
↓ STA背书 制造背书 物流背书
背书有效期6个月
CAF Quality Mgr. Purchase Mgr.
↓ 签署Q1 Letter ↓ 签署Q1 VR
Threshold to maintain Q1
No -250 score No -250 score With receipts within 13 months <200% of industry commodity PPM No -250 score No delivery score adjustment of 250
Page 19
Ⅱ. Q1评分
量产表现
F. 违背诚信 ( -250分)
SREA 未通知STA及通过SREA,擅自进行:制造或设备过程变更、成分
或材料的变更或替换、分供方或代理商变更等
PSW 投产 ……
自评的PSW不完整或不准确、PSW支持数据不真实 生产爬坡不能满足承诺的工厂装车计划
Page 20
Ⅱ. Q1评分
- 1、下载文档前请自行甄别文档内容的完整性,平台不提供额外的编辑、内容补充、找答案等附加服务。
- 2、"仅部分预览"的文档,不可在线预览部分如存在完整性等问题,可反馈申请退款(可完整预览的文档不适用该条件!)。
- 3、如文档侵犯您的权益,请联系客服反馈,我们会尽快为您处理(人工客服工作时间:9:00-18:30)。
第 3 页,共 6 页
Q1 条款要求
条款要求 供应商通过了由第三方执行的 ISO/TS 16949的体系认证 供应商的环境管理体系需通过ISO14001认证。 供应商的质量手册包括现场审核所有方面的流程。质量手册需不断更新升级以驱动供应商的质量体系能以统计数 据形式表现出持续改善。包括来自制造,质量,工程,和人力资源的代表组成的供应商的高级管理层,需对各方 面进行评估。 经由内审查出的不符合项不可重复发生。 供应商有文件程序来定期识别及更新顾客的期望、目标及要求。 供应商有文件程序来定期识别及更新公司内部期望、目标和要求。 供应商有文件程序将公司内外部期望、目标及要求转化为QOS衡量指标。 供应商有文件程序分解公司目标至每一个QOS衡量指标。 供应商有文件程序分配公司所选定的衡量指标至适当管理层,以便於审查、追蹤及改進。 驱动衡量指标持续改善的行动计划需在QOS会议上得到追踪。 供应商管理团队是否每月举行QOS绩效审查会议,参与会议的人员应包括来自制造、质量、工程和人力资源等部 门的代表。 改进行动须由包括了组织所有层级的跨功能小组来执行 QOS审核包括福特所有SIM衡量指标,关键流程衡量指标,和顾客满意度衡量指标的审核 了解和追踪与供应商生产有关联的顾客满意度指标。 所有福特的零件都具有文件化的设计和过程失效模式及影响分析(DFMEA, PFMEA)并制定相应的控制计划(或 DCPs)。具有一个稳健的过程来开发这些文件。 FMEAs需每年或在问题发生时进行评审。柏拉图被用来关注: 1) 严重度, 2) 产品的严重度和发生度,以及 3) 识别高的RPN以确定改进中优先采取的行动 如有可能,所有缺陷检测领域都需得到评审并有制定预防缺陷装置的计划。 供应商需和他的顾客协作,以便对每个福特部件在PFMEA和控制计划中定义SC和HIC。 供应商同福特车辆项目小组(PVT)、项目工程办公室(PEO)、CRT和STA一起就SCs与HICs的确定最终达成一致。 对于任何还没有SCs 或 HICs的零件,供应商从福特获得特定协议 供应商确保所有工程图纸上的尺寸和批注,与控制计划,作业指导书,作业准备指导书和来料检验一致。 供应商必须对部件的传递特性进行验证并确保部件在车辆运作状态(VO, Vehicle Operation)及最终顾客端为零缺 陷。 控制计划是适宜的质量策划的结果,并包括DFMEA和PFMEA之间的清晰联系。 控制计划包括下列要素: -- 操作编号/名称 -- 零件名称/零件编号 --检查要求 -- 规范 -- 控制方法 --SC, CC, HIC(如果有的话), 和工程规范的要求已被恰当的识别 --适宜的SC, CC, HIC(如果有的话), 和 ES 控制方法(过程检查,过程计量,和零件测量) --防错的方法 --过程控制的方法 -- 样本大小和抽样频率 -- 所需的工具、量具和其它设备 --当过程失控或产品没有通过检测时,反应计划必须明确指导操作者如何反应。 供应商有责任评估那些影响产品质量的全部作业所需要的员工技能。 员工有技能评估、培训计划、和培训纪录。 供应商确保只有培训合格的人员,才可以参与福特零件的生产 供应商有APQP 追踪机制在运作。 供应商有一系统来管理新车型项目的上线。 供应商有一个流程可以确保准时的配合福特原型车及试产的开发时程点。 供应商有流程以持续监控并改进上线量产业绩。 所有的PPAP文件必须包括AIAG的PPAP手册的信息,这些信息必须在福特审查时可获得。北美的供应商需要有 一个程序以符合阶段性PPAP、initial run at rate、生产验证及产能验证
Q1 条款要求
条款编号 1.1.1 1.1.2 1.1.3 1.1.4 1.1.5 1.1.6 1.1.7 1.1.8 1.1.9 1.1.10 1.1.11 1.1.12 1.1.13 1.2.1 1.2.2 1.2.3 1.2.4 I.制造 过程 能力 的规 划 I.2.FMEAs/ 控制计划 1.2.5 1.2.6 1.2.7 1.2.8
I.1.质量程序 /QS9000/TS169 49/QOS
1.2.9
I.3. 员工准备 /培训评审 I.4.APQP/ 上 线/PPAP/ 与 Run-at-Rate 审核
1.3.1 1.3.2 1.3.3 1.4.1 1.4.2 1.4.3 1.4.4 1.4.5
第 1 页,共 线/PPAP/ 与 Run-at-Rate I.制造 审核 过程 能力 的规 划 I.5.变更管理 1.4.6 1.4.7 1.4.8 1.4.9 1.5.1 1.5.2 1.5.3 II.1.1 II.1.2 II.1.3 II.1.外包商的 质量管理 II.1.4 II.1.5 II.1.6 II.1.7 II.2. 1 II.2.进货质量 II.2. 2 的控制 II.2. 3 II.2. 4 II.3.1 II.制造 II.3.控制计划 过程 / 作业指导书 能力 的验 证 II.3.2 II.3.3 II.3.4 II.4.1 II.4.2 II.4过程变异 监控 II.4.3
第 4 页,共 6 页
条款要求 供应商要求其分供方需具备能满足所有的PPAP要求的作业流程,无论分供商与福特的业务关系如何 节拍生产必须完成,并支持项目中所有福特零件的产能要求。 产能验证必须包含以下元素并针对整个生产流程或最慢的操作(瓶颈流程)开展:机器可用小时数,工作班次, 工作天数,机器停机时间(计划内及计划外),机台切换时间,休息及质量报废。 供应商会监控产能状况并有程序来确保提供福特量产零件的充足产能 。 供应商具有文件程序以有效实施 post--Job# 1 设计变更、过程变更、或产量变更。 供应商对这些变更进行有效审查并更新其质量支持文件。可能需要变更的文件包括:制造流程图、FMEAs、控制 计划、作业指导书、目视化辅具(教具)、和PPAP文件。 供应商按照文件程序以确保采取变更之前先得到福特的批准。批准的过程包括使用供应商工程批准申请单 (SREAs)、全球工程发布系统(WERS)的变更请求单/问题报告(CR/CR)、管理警示,以及(如果需要的话)修改 的PPAP文件。 供应商有明确的程序管理其供应商阵容,包括那些对质量有较高影响度供应商的识别。 供应商要求外包商通过类似于ISO/TS16949或VDA的质量体系认证,并且每年通过对影响度大的外包商进行设施现 场评审来确认外包商的资格。 供应商需要从外包商那里获得所有零件的PPAP(不论外包商与福特的关系如何)。 福特规定的由外包商负责的工程规范或特殊特性,外包商就必须在向上一阶供应商提交的PPAP中展现出符合工 程规范(ES)或特殊特性。 在有PTC传递特性相关要求时,供应商需要求下级供应商采取具体的行动以所有的PTC满足顾客的规范要求。 供应商在将产品融入到自己的制造过程之前,必须先通过审查并确认外包商提交的PPAP,以确保外包商符合要 求。 供应商对外包商实施体系审核,并在万一有停止发车或市场召回的情况时,确保能越过供应商设施,对其外包商 实施纠正措施。 供应商有进货质量检验的策略。 进料质量要求是控制计划的一部分。如果执行了进货质量检查,有证据表明规范符合要求。如果没有进行进货检 验,需有外包商认可的制度。 如果原材料或采购的零件被发现不符合质量规格,进料检验人员有反应计划可遵循实施。 供应商有适当的资源来管理外包商的质量,包括现场审核高影响外包商的能力。 建立标准化的作业指导书(包括控制计划、工作指导书、工作辅具、检查表、作业准备指导书和图示说明)并提 供给作业员。 标准化的作业指导书清晰、明确、且受控制。在工作地点存放作业指导书并保证得到操作者的遵守。 反应计划已有明确的规定,并保护福特不受到不合格原料的影响。 当产品或过程与目前的生产状态不相符时,控制计划得到了及时的修改或更新。 供应商运用合适的统计技术。防止缺陷的关键是减少过程变差并使用SPC(统计过程控制)方法来确定何时采取行 动(比如调整和改变工/模具),与此相反则应该避免扰乱过程 基于操作员的统计过程控制图表须依据其样本频率、样本大小和相应的图表类别而择优选取。SPC要定时执行检 测并在过程失控时制定相应的矫正措施。 由设备操作者维护、监控和应用SPC数据,并通过减少过程变差来驱动过程和产品的改善。过程改善的证据包 括:报废品减少、返工/修理和DPU的减少、首次通过率的增加、Rolled Throughput Yield的增加、cpk的改善、 过程标准差水平的提升、实施防错机制的记录、停机时间的减少。 (当适用时)所有的SCs, CCs, 和 HICs的Ppk和Cpk水平分别大于等于1.67和1.33。所有的SCs、 CCs 和Cpk趋势 都要全程追踪,而且须有各种能持续减少过程变异原因的行动计划,来提升Cpk值。这些Cpk趋势将会作为供应 商例行管理审核的内容。 必须论证所有新設备和工具/模具对SCs、CCs和HICs(如果有的话)所具有的机器能力。 供应商确保控制计划中规定的所有量具可有效使用。量具校准和量具维护计划需确保有备份量具或备份测量过程 以有效支持控制计划要求的检查。 対所有的SC和CCs尽可能运用计量型量具。HIC量具则按各控制计划所列使用。所有的量具(公司和员工个人 的)均按控制计划明确表列。 Gage R&R 與 AIAG 测量系統分析手冊的指导要求相符一致。 一旦GagR&R不符合這些指导要求,需有特定的 计划来保证會符合這些指导要求。此外,供应商需具备适当的测量能力以满足所有生产阶段的测量要求。 供应商有明文的「量具废弃/损坏」规定,且所有员工必须遵守。这确保了仅有功能具备又符合规范的量具才会被 使用。
II.4.4 II.4.5 II.5.1 II.5.量具校准 和使用 II.5.2 II.5.3 II.5.4
第 2 页,共 6 页
条款编号 II.5.量具校准 和使用 II.6.零件标识 /不合格零件/ 包装/装运 II.5.5 II.5.6 II.6.1 II.6.2 II.6.3 II.6.4 II.7.1 II.7.测试/工 程规范 II.制造 过程 能力 的验 II.8 .预防性 证 維護(PM) / 整理 II.7.2 II.7.3 II.8.1 II.8.2 II.8.3 II.8.4 II.9.制造流程 / 6个标准差 和精益生产 衡量指标 II.9.1 II.9.2 II.10.1 II.10.问题解 II.10.2 决/纠正措施 II.10.3 II.10.4