转炉炼钢物料平衡和热平衡计算 模板-
转炉炼钢物料平衡和热平衡计算模板-

转炉炼钢物料平衡和热平衡计算模板- 第二章、转炉物料平衡和热平衡计算1、低磷生铁吹炼(单渣法)一、原始数据(一)铁水成分及温度表2-1-1成分 C Si Mn P S 温度 ?% 4.36 o.57 0. 62 0.07 0.05 1300 (二)原材料成分表2-1-2烧合计成分% CaO SiO MgO AlO S P CaF FeO FeO HO C 2232232减 % 种类100 91(08 1(66 1(54 1(22 0(06 4(44 石灰100 1(00 5(61 0(52 1(10 0(07 29(4 61(8 0(50 矿石100 6(00 0(58 1(78 0(09 0(55 89(00 2(00 萤石10 8 53(04 0(48 34(94 0(74 白云石100 1(40 2(60 85(00 11(00 炉衬(三)冶炼钢种及成分表2-1-3成分 C Si Mn P S % 0.12—0.20 0.20—0.55 1.20—1.60 ?0.045 ?0.045 (四)平均比热表2-1-4项目固态平均比热kcal/kg.? 熔化潜热kcal/kg 液态或气态平均比热kcal/kg.?生铁 0.178 52 0.20 钢 0.167 65 0.20 炉渣 50 0.298 烟尘 0.238 50 矿石炉气:CO 0.349 CO 0.558 2SO 0.555 2O 0.356 2N 0.346 2HO 0.439 2(五)冷却剂用废钢做冷却剂,其成分与冶炼钢种中限相同。
(六)反应热效应1反应热效应通常采用25?为参考温度,比较常用的反应数据见表2-1-5 (七)根据国内转炉实测数据选取1、渣中铁珠量为渣量的2.5%;2、金属中[C]假定85%氧化成CO,15%氧化成CO; 23、喷溅铁损为铁水量的0.3%;4、取炉气平均温度1450?,自由氧含量0.5%,烟尘量为铁水量的1.8%,其中FeO=75%,Fe0=22%; 235、炉衬侵蚀量为铁水量的0.15%;6、氧气成分为98.9% O,1.5% N。
转炉车间炼钢物料平衡热平衡计算
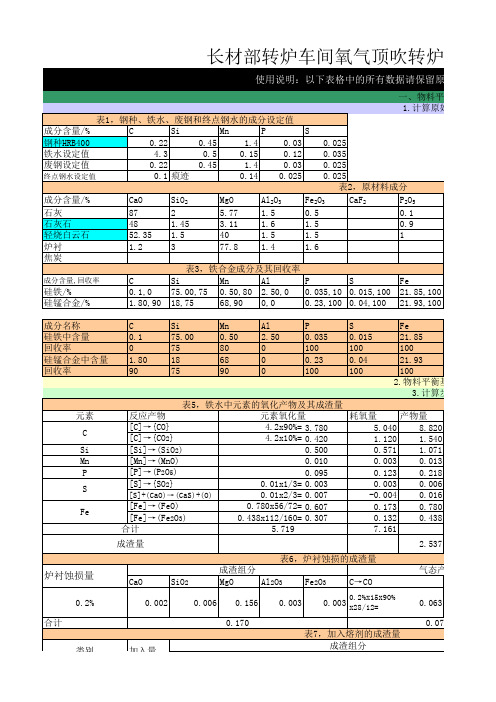
表13,加入废钢的物料平衡表(以100kg铁水为基础) 收入 支出 质量 质量 项目 % 项目 91.63+16.816= 铁水 100.00 76.51 钢水 7.10+0.446= 废钢 17.13 13.11 炉渣 11.19+0.051= 石灰 2.07 1.58 炉气 石灰石 1.40 1.07 喷溅 轻烧白云石 2.00 1.53 烟尘 炉衬 0.20 0.15 渣中铁珠 7.720+0.18= 7.902 氧气 6.05 130.70 130.29 合计 100 合计 表14,加入废钢的物料平衡表(以100kg(铁水+废钢)为基础) 收入 支出 项目 质量 % 项目 质量 % 铁水 85.37 76.51 钢水 92.58 83.23 废钢 14.63 13.11 炉渣 6.44 5.79 石灰 1.76 1.58 炉气 9.59 8.62 硅锰加入量 WMn= 石灰石 1.20 1.07 喷溅 0.85 0.77 轻烧白云石 1.71 1.53 烟尘 1.28 1.15 硅铁加入量 Wsi= 炉衬 0.17 0.15 渣中铁珠 0.48 0.44 氧气 6.75 6.05 合计 111.58 100 合计 111.24 100 表15,铁合金中元素烧损量及产物量 烧损量 类别 元素 脱氧量 成渣量 炉气量 1.91x1.80%x10%= 0.003 C 0.009 0.013 1.91x68.00%x10%= 0.130 Mn 0.038 0.167 1.91x18.00%x25%= 0.086 Si 0.098 0.184 硅锰合金 P S Fe 0.219 合计 0.145 0.351 0.013 0.30x2.50%x100%= 0.007 Al 0.007 0.014 0.30x0.50%x20%= 0.0003 Mn 0.0001 0.0004 0.30x75.00%x25%= 0.0559 Si 0.064 0.120 硅铁 P S Fe 0.064 合计 0.071 0.134 总计 0.282 0.216 0.485 0.013 附表,脱氧合金化后的钢水成分 0.031 (0.10%+ x100%)= 0.133% 94.70 0.257+0.168 x100%= 0.449% 94.70 1.167+0.001 (0.140%+ x100%)= 1.373% 94.70 0.004 (0.025%+ x100%)= 0.030% 94.70 0.001 (0.025%+ x100%)= 0.026% 94.70 表16,总物料平衡表 收入 质量 % 项目
转炉热平衡和物料平衡的计算
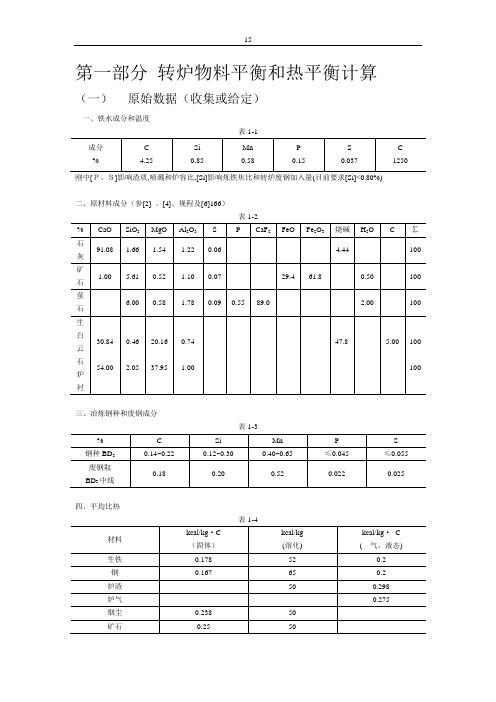
第一部分转炉物料平衡和热平衡计算(一)原始数据(收集或给定)一、铁水成分和温度表1-1刚中[P、S]影响渣质,喷溅和炉容比,[Si]影响炼铁焦比和转炉废钢加入量(目前要求[Si]<0.80%)二、原材料成分(参[2] 、[4]、规程及[6]166)表1-2三、冶炼钢种和废钢成分表1-3四、平均比热表1-4五、反应热效率(认为25℃与炼铁温度下两者数值近似)表1-5*参氧气转换炉炼钢原理(美),冶金工业出版社74年版75页六、有关参数的选用1、渣中铁珠占渣重的8%;2、金属中90%[C] →CO 10%[C]→CO2;3、喷溅铁损占铁水量的1%;4、炉气平均温度1450℃;含自愿氧0.5%;烟尘量占铁水量的1.6% 其中有77%FeO和20%Fe2O3;(作课程设计时刻改为;烟尘量占铁水量的1.16%。
参[4]31)5、炉衬侵蚀占铁水量的0.5%;6、氧气成分为98.5%O2和1.5%N;(作课程设计时可改为:99.5%O2和0.5%N2,参[4]31)。
(二)物料平衡计算由铁水成分冶炼钢种可选用单渣发不留渣的操作。
为简化计算,物料平衡以100kg铁水为计算基础。
一、炉渣量及炉渣成分的计算炉渣来自元素的氧化,造渣材料和炉衬侵蚀等。
1.铁水中各元素的氧化量%表1-6说明:[Si]——碱性渣操作时终点[Si]量为痕迹;[P]——单渣发去磷约90%(±5%);[Mn]——终点余锰量约30~40%,这里实测为30%;[S]——转炉去硫约30~50%,这里取40%;[C]——终点碳与钢种及磷量有关,要求出钢后加铁合金增碳的量能满足钢的规格中限,即:[C]终点=[C]中限—[C]增碳这里取[C]终=0.15%,可满足去磷保碳与增碳两个条件。
2、铁水中各元素的氧化量,耗氧量和氧化产物量的计算。
表1-73.造渣剂成分及数量:(选自国内有关生产炉)1)矿石成分及重量的计算(1.0kg矿石/100kg铁水)表1-8S*:反应式为[S]+( CaO)= (CaS)+[O]其中:(CaS)重为0.001×7232=0.002[㎏][S]消耗(CaO) 重为0.001×5632=0.002[㎏][O]微量,可不计。
物料平衡与热平衡计算
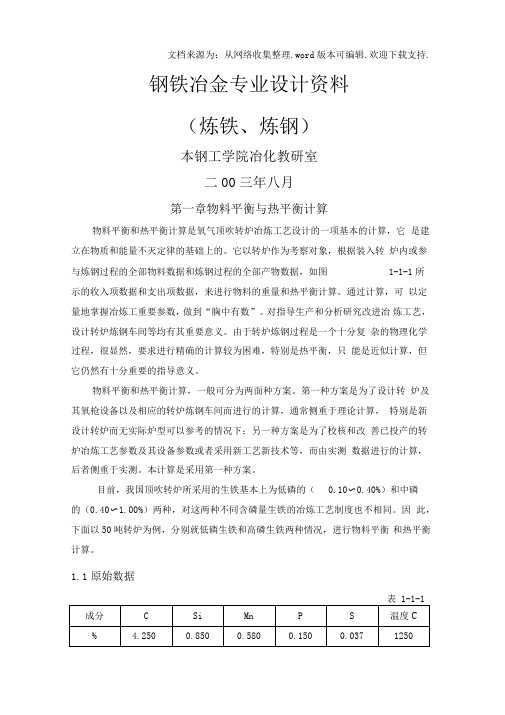
文档来源为:从网络收集整理.word版本可编辑.欢迎下载支持.钢铁冶金专业设计资料(炼铁、炼钢)本钢工学院冶化教研室二00三年八月第一章物料平衡与热平衡计算物料平衡和热平衡计算是氧气顶吹转炉冶炼工艺设计的一项基本的计算,它是建立在物质和能量不灭定律的基础上的。
它以转炉作为考察对象,根据装入转炉内或参与炼钢过程的全部物料数据和炼钢过程的全部产物数据,如图1-1-1所示的收入项数据和支出项数据,来进行物料的重量和热平衡计算。
通过计算,可以定量地掌握冶炼工重要参数,做到“胸中有数”。
对指导生产和分析研究改进冶炼工艺,设计转炉炼钢车间等均有其重要意义。
由于转炉炼钢过程是一个十分复杂的物理化学过程,很显然,要求进行精确的计算较为困难,特别是热平衡,只能是近似计算,但它仍然有十分重要的指导意义。
物料平衡和热平衡计算,一般可分为两面种方案。
第一种方案是为了设计转炉及其氧枪设备以及相应的转炉炼钢车间而进行的计算,通常侧重于理论计算,特别是新设计转炉而无实际炉型可以参考的情况下;另一种方案是为了校核和改善已投产的转炉冶炼工艺参数及其设备参数或者采用新工艺新技术等,而由实测数据进行的计算,后者侧重于实测。
本计算是采用第一种方案。
目前,我国顶吹转炉所采用的生铁基本上为低磷的(0.10〜0.40%)和中磷的(0.40〜1.00%)两种,对这两种不同含磷量生铁的冶炼工艺制度也不相同。
因此,下面以50吨转炉为例,分别就低磷生铁和高磷生铁两种情况,进行物料平衡和热平衡计算。
1.1原始数据表 1-1-1表1-1-2原材料成分表2-1-1铁水成分与温度转炉冶炼钢种常为普通碳素钢和低合金钢,在此以要求冶炼BD3钢考虑,其成分见表2-1-31-1-4用废钢作冷却剂,其成份与冶炼钢种成份的中限相同。
(见表1-1-3)虽然炉内化学反应,实际上是在炉料温度和炉内上部气相温度之间的任一温度发生的,但反应热效应通常仍采用25 C作为参考温度,值得指出的是,反应热还与组分在铁水中存在形态有关,至今对参与化学反应有关的实际组成物还有不同的看法。
转炉物料平衡与热平衡计算.
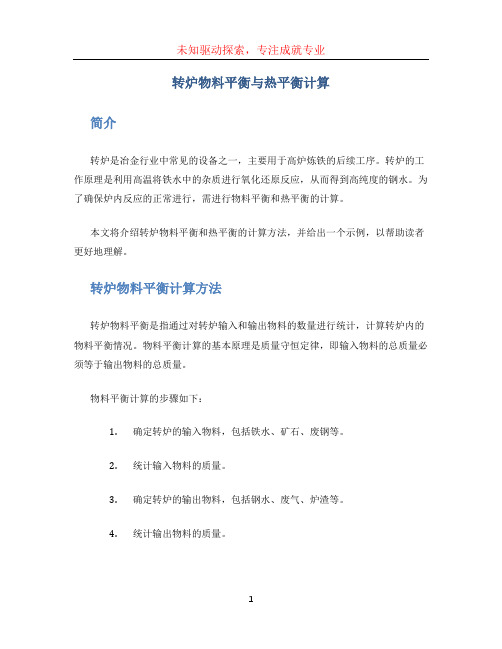
转炉物料平衡与热平衡计算简介转炉是冶金行业中常见的设备之一,主要用于高炉炼铁的后续工序。
转炉的工作原理是利用高温将铁水中的杂质进行氧化还原反应,从而得到高纯度的钢水。
为了确保炉内反应的正常进行,需进行物料平衡和热平衡的计算。
本文将介绍转炉物料平衡和热平衡的计算方法,并给出一个示例,以帮助读者更好地理解。
转炉物料平衡计算方法转炉物料平衡是指通过对转炉输入和输出物料的数量进行统计,计算转炉内的物料平衡情况。
物料平衡计算的基本原理是质量守恒定律,即输入物料的总质量必须等于输出物料的总质量。
物料平衡计算的步骤如下:1.确定转炉的输入物料,包括铁水、矿石、废钢等。
2.统计输入物料的质量。
3.确定转炉的输出物料,包括钢水、废气、炉渣等。
4.统计输出物料的质量。
5.比较输入物料的总质量和输出物料的总质量,若两者相等,则物料平衡成立;若不相等,则存在物料的损失或增加。
下面以一个具体的例子来说明转炉物料平衡的计算过程。
假设一个转炉的输入物料包括1000kg的铁水、200kg的矿石和100kg的废钢。
经过转炉反应后,得到800kg的钢水、400kg的废气和100kg的炉渣。
通过统计计算,我们可以得到输入物料的总质量为1000kg + 200kg + 100kg = 1300kg,输出物料的总质量为800kg + 400kg + 100kg = 1300kg。
两者相等,说明物料平衡成立。
转炉热平衡计算方法转炉热平衡是指通过对转炉内的能量输入和输出进行统计,计算转炉的热平衡情况。
热平衡计算的基本原理是能量守恒定律,即输入能量的总量必须等于输出能量的总量。
热平衡计算的步骤如下:1.确定转炉的输入能量,包括燃料的热值、还原剂的热值等。
2.统计输入能量的总量。
3.确定转炉的输出能量,包括钢水的热值、废气的热值等。
4.统计输出能量的总量。
5.比较输入能量的总量和输出能量的总量,若两者相等,则热平衡成立;若不相等,则存在能量的损失或增加。
转炉炼钢物料及热平衡
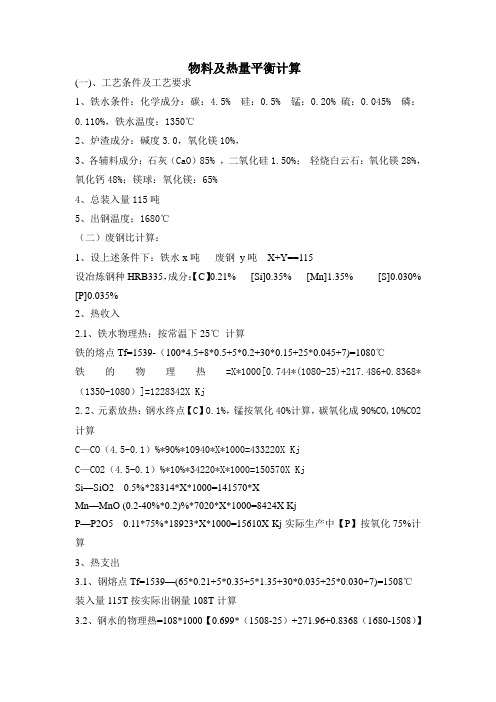
物料及热量平衡计算(一)、工艺条件及工艺要求1、铁水条件:化学成分:碳:4.5% 硅:0.5% 锰:0.20% 硫:0.045% 磷:0.110%,铁水温度:1350℃2、炉渣成分:碱度3.0,氧化镁10%,3、各辅料成分:石灰(CaO)85% ,二氧化硅1.50%;轻烧白云石:氧化镁28%,氧化钙48%;镁球:氧化镁:65%4、总装入量115吨5、出钢温度:1680℃(二)废钢比计算:1、设上述条件下:铁水x吨废钢y吨X+Y==115设冶炼钢种HRB335,成分:【C】0.21% [Si]0.35% [Mn]1.35% [S]0.030% [P]0.035%2、热收入2.1、铁水物理热:按常温下25℃计算铁的熔点Tf=1539-(100*4.5+8*0.5+5*0.2+30*0.15+25*0.045+7)=1080℃铁的物理热=X*1000[0.744*(1080-25)+217.486+0.8368*(1350-1080)]=1228342X Kj2.2、元素放热:钢水终点【C】0.1%,锰按氧化40%计算,碳氧化成90%CO,10%CO2计算C—CO(4.5-0.1)%*90%*10940*X*1000=433220X KjC—CO2(4.5-0.1)%*10%*34220*X*1000=150570X KjSi—SiO2 0.5%*28314*X*1000=141570*XMn—MnO (0.2-40%*0.2)%*7020*X*1000=8424X KjP—P2O5 0.11*75%*18923*X*1000=15610X Kj实际生产中【P】按氧化75%计算3、热支出3.1、钢熔点Tf=1539—(65*0.21+5*0.35+5*1.35+30*0.035+25*0.030+7)=1508℃装入量115T按实际出钢量108T计算3.2、钢水的物理热=108*1000【0.699*(1508-25)+271.96+0.8368(1680-1508)】=156870756 Kj3.3、钢渣的物理热=115*1000*11%【1.247(1680-25)+209.2】=28753260Kj (渣量按装入量的11%计算)3.4、炉气的的物理热:主要按炉气生成CO和CO2计算,炉气温度1450℃【C】+1/2O2=CO (4.5-0.1)%*90%*28/12=0.0924Kg【C】+1/2O2=CO2 (4.5-0.1)%*90%*44/12=0.0161Kg 则炉气物理热=(0.0924+0.0161)*1.136*(1450-25)*X*1000=175639.8X Kj4、热收入=热支出则得出1977736X=156870756+287532260.25+175639.8X解得铁水=103废钢y==12t(二) (1)铁水【Si】波动0.1%,调整废钢量【Si】波动0.1%则放热波动如下:103*1000*0.1%*28314=2916342K j 根据资料这部分热量的70%用于熔池有效升温每公斤废钢的冷却效应(按出钢温度1680℃,废钢熔点1500℃)Q 废=1*【0.699(1500-25)+271.96+0.8368(1680-1500)】=1453.609Kj/Kg 则得出铁水【Si】波动0.1%,调整废钢量为:2916342*70%/1453.609=1400Kg=1.4t(2) 每吨废钢的降温值(出钢量108t)1453.609*1000=108*1000*0.8368*△t △t=16.1℃.根据经验与资料取△t=14.5℃(3)铁水温度波动10℃调整废钢量,铁水温度波动10℃,则带入的物理热波动为103*1000*0.8367*10=861801Kj 70%用于有效升温则调整废钢量为861801*70%/1453.609=415Kg(4)增加1t铁水,则带入的物理热为1000*【0.744(1080-25)+217.486+0.8368(1350-1080)】=1228342(Kj)元素放热增加如下:C—CO 433220Kj C—CO2 150570Kj Si—SiO2 141570Kj Mn—MnO 8424Kj P—P2O5 15610Kj 总计 621974Kj增加1t铁水总计增加的热量1228342+621974Kj=1850316Kj 70%用于有效升温,则能使钢水升温△t℃则得出:1228342*70%+621947*70=108*1000*0.8368*△t △t=20℃(三)(1)如果每炉烧结矿定为3吨,则需减废钢Xt,增加铁水y吨(103+y)+(12-x)=115,14.5x+20y=3*43 得出x=y=3.74吨即铁水调整为103+3.74=106.74t 废钢调整为12—3.74=8.26t(2)如果烧结矿定位4t 需减废钢Xt增加铁水y吨(103+ y)+(12-X)=115 ,14.5x+20y=4*43 得出x=4.98≈5t,y=4.98≈5t 即铁水调整为103+5=108t 废钢调整为12-5=7t.附表:各冷却剂降温值。
炼钢过程中的物料平衡与热平衡计算
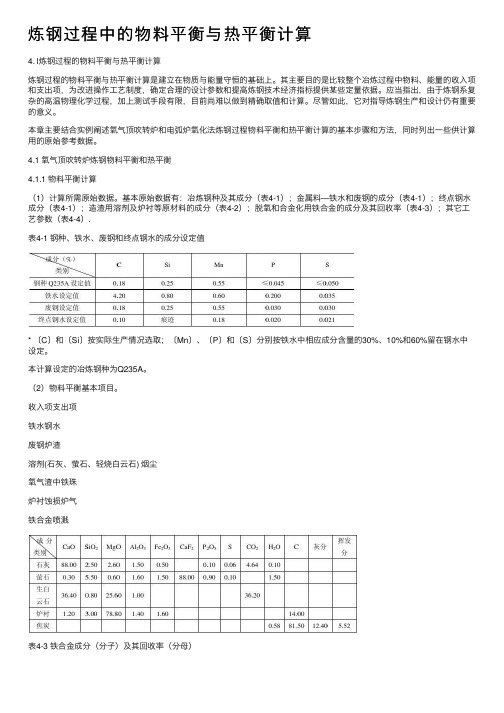
炼钢过程中的物料平衡与热平衡计算4. l炼钢过程的物料平衡与热平衡计算炼钢过程的物料平衡与热平衡计算是建⽴在物质与能量守恒的基础上。
其主要⽬的是⽐较整个冶炼过程中物料、能量的收⼊项和⽀出项,为改进操作⼯艺制度,确定合理的设计参数和提⾼炼钢技术经济指标提供某些定量依据。
应当指出,由于炼钢系复杂的⾼温物理化学过程,加上测试⼿段有限,⽬前尚难以做到精确取值和计算。
尽管如此,它对指导炼钢⽣产和设计仍有重要的意义。
本章主要结合实例阐述氧⽓顶吹转炉和电弧炉氧化法炼钢过程物料平衡和热平衡计算的基本步骤和⽅法,同时列出⼀些供计算⽤的原始参考数据。
4.1 氧⽓顶吹转炉炼钢物料平衡和热平衡4.1.1 物料平衡计算(1)计算所需原始数据。
基本原始数据有:冶炼钢种及其成分(表4-1);⾦属料—铁⽔和废钢的成分(表4-1);终点钢⽔成分(表4-1);造渣⽤溶剂及炉衬等原材料的成分(表4-2);脱氧和合⾦化⽤铁合⾦的成分及其回收率(表4-3);其它⼯艺参数(表4-4).表4-1 钢种、铁⽔、废钢和终点钢⽔的成分设定值* 〔C〕和〔Si〕按实际⽣产情况选取;〔Mn〕、〔P〕和〔S〕分别按铁⽔中相应成分含量的30%、10%和60%留在钢⽔中设定。
本计算设定的冶炼钢种为Q235A。
(2)物料平衡基本项⽬。
收⼊项⽀出项铁⽔钢⽔废钢炉渣溶剂(⽯灰、萤⽯、轻烧⽩云⽯) 烟尘氧⽓渣中铁珠炉衬蚀损炉⽓铁合⾦喷溅表4-3 铁合⾦成分(分⼦)及其回收率(分母)* 10%C与氧⽣产CO2表4-4 其它⼯艺参数设定值(3)计算步骤。
以100kg铁⽔为基础进⾏计算。
第⼀步:计算脱氧和合⾦化前的总渣量及其成分。
总渣量包括铁⽔中元素氧化、炉衬蚀损和加⼊溶剂的成渣量。
其各项成渣量分别列于表4-5、4-6和4-7。
总渣量及其成分如表4-8所⽰。
第⼆步:计算氧⽓消耗量。
氧⽓实际消耗量系消耗项⽬与供⼊项⽬之差,详见表4-9。
第三步:计算炉⽓量及其成分。
* 由CaO还原出的氧量,消耗的CaO量=0.009×56/32=0.016kg表4-7 加⼊溶剂的成渣量0.016+0.004+0.002+0.910=0.900kg;渣中已含(SiO2)=1.710+0.009+0.028+0.020=1.767kg.因设定的终渣碱度R=3.5;故⽯灰加⼊量为〔R∑(SiO)-∑(CaO)〕/(%CaO⽯灰-R×%SiO2⽯灰)=5.285/2(88.00%-3.5×2.50%)=6.67kg*2 为(⽯灰中CaO含量)—(⽯灰中S→CaS⾃耗的CaO量)。
转炉炼钢物料平衡计算
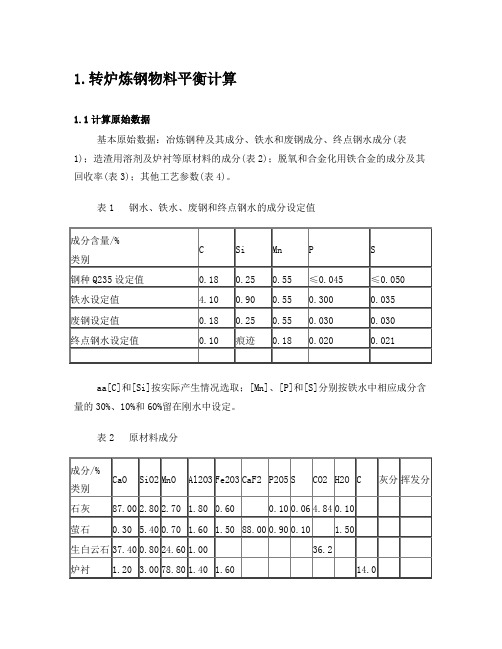
1.转炉炼钢物料平衡计算1.1计算原始数据基本原始数据:冶炼钢种及其成分、铁水和废钢成分、终点钢水成分(表1);造渣用溶剂及炉衬等原材料的成分(表2);脱氧和合金化用铁合金的成分及其回收率(表3);其他工艺参数(表4)。
表1 钢水、铁水、废钢和终点钢水的成分设定值aa[C]和[Si]按实际产生情况选取;[Mn]、[P]和[S]分别按铁水中相应成分含量的30%、10%和60%留在刚水中设定。
表2 原材料成分表3 铁合金成分(分子)及其回收率(分母)10%与氧生成CO2。
表4 其他工艺参数设定值1.2物料平衡基本项目收入项有:铁水、废钢、溶剂、氧气、炉衬损失、铁合金。
支出项有:钢水、炉渣、烟尘、渣中铁珠、炉气、喷溅。
1.3计算步骤以100kg铁水为基础进行计算。
1.3.1计算脱氧和合金化前的总渣量及其成分总渣量包括铁水中元素氧化,炉衬蚀损和加入溶剂的成渣量。
其各项成渣量分别列于表5-表7。
总渣量及其成分如表8所示。
表5 铁水中元素的氧化产物及其成渣量由CaO还原出的氧量;消耗的CaO量=0.01×56/32=0.018kg。
表6 炉衬蚀损的成渣量表7 加入溶剂的成渣量石灰加入量计算如下:由表5—表7可知,渣中已含(CaO)=–0.018+0.004+0.002+0.935=0.923kg;渣中已含(SiO2)=1.860+0.009+0.027+0.020=1.916kg。
因设定的终渣碱度R=3.5,故石灰加入量为:[R∑ω(SiO2)-∑ω(CaO)]/[ω(CaO石灰)-R×ω(SiO2石灰)]=5.783/(87.0%-3.5×2.8%)=7.49kg。
(石灰中CaO含量)—(石灰中S—CaS自耗的CaO量)由CaO还原出来的氧量,计算方法同表5的注。
表8 总渣量及其成分总渣量计算如下:表8中除(FeO)和(Fe2O3)以外的渣量为:7.439+2.216+1.057+0.172+0.553+0.44+0.376+0.032=12.194kg,而终渣∑ω(FeO)=15%(表4),故总量为:12.194÷86.75%=14.056kg。
- 1、下载文档前请自行甄别文档内容的完整性,平台不提供额外的编辑、内容补充、找答案等附加服务。
- 2、"仅部分预览"的文档,不可在线预览部分如存在完整性等问题,可反馈申请退款(可完整预览的文档不适用该条件!)。
- 3、如文档侵犯您的权益,请联系客服反馈,我们会尽快为您处理(人工客服工作时间:9:00-18:30)。
第二章、转炉物料平衡和热平衡计算1、低磷生铁吹炼(单渣法)一、原始数据(一)铁水成分及温度(二)原材料成分(三)冶炼钢种及成分(四)平均比热(五)冷却剂用废钢做冷却剂,其成分与冶炼钢种中限相同。
(六)反应热效应反应热效应通常采用25℃为参考温度,比较常用的反应数据见表2-1-5(七)根据国内转炉实测数据选取1、渣中铁珠量为渣量的2.5%;2、金属中[C]假定85%氧化成CO,15%氧化成CO2;3、喷溅铁损为铁水量的0.3%;4、取炉气平均温度1450℃,自由氧含量0.5%,烟尘量为铁水量的1.8%,其中FeO=75%,Fe203=22%;5、炉衬侵蚀量为铁水量的0.15%;6、氧气成分为98.9% O2,1.5% N2。
根据铁水成分,渣料质量,采用单渣不留渣操作。
先以100公斤铁水为计算基础。
(一)炉渣及其成分的计算1、铁水中各元素氧化量表2-1-6成分,kgC Si Mn P S 合计项目铁水 4.36 0.57 0.62 0.07 0.05终点钢水0.13 痕迹0.13 0.008 0.019氧化量 4.23 0.57 0.49 0.062 0.031 5.308 [C]:取终点钢水含碳量0.15%;[Si]:在碱性氧气转炉炼钢中,铁水中的Si几乎全部被氧化;[Mn]:顶底复吹转炉残锰量取60%;[P]:采用低磷铁水吹炼,铁水中磷90%进入炉渣,10%留在钢中;[S]:氧气转炉去硫率不高,取40%。
2、各元素氧化量,耗氧量及其氧化产物量见表2-1-73、造渣剂成分及数量根据国内同类转炉有关数据选取1)矿石加入量及成分矿石加入量为1.00公斤/100公斤铁水,成分及重量见表2-1-82)萤石加入量及成分萤石加入量为0.30kg/kg铁水,其成分及重量见表2-1-93)炉衬侵蚀量为0.200公斤/100公斤铁水,其成分及重量见2-1-104)生白云石加入量及成分加入的白云石后,须保证渣中(MgO)含量在6—8%之间,经试算后取轻烧白云石加入量为1.2公斤/100公斤铁水。
其成分及重量见表2-1-11表2-1-8表2-1-9P以2[P]+5/2{O2}=(P2O5)的形式进行反应,其中生成(P2O5)的量为0.00165×142/62=0.004公斤,消耗氧量0.00165×80/62=0.002*被侵蚀的炉衬中C 的氧化,同金属中C 氧化成CO 、CO 2的比例相同,即:C----CO 0.022×88%×28/12=0.045 kg C----CO 2 0.022×12%×44/12=0.010 kg 消耗氧量为:0.145×16/28=0.026 kg 0.010×32/44=0.007 kg 共消耗氧气量为: 0.033 kg 表2-1-115) 炉渣碱度和石灰加入量 取终渣碱度2(%)3.5(%)CaO R SiO ==渣中已存在的∑(SiO 2)量=铁水中硅氧化生成的SiO 2量+炉衬带入的SiO 2量+矿石带入的SiO 2量+萤石带入的SiO 2量+白云石带入的SiO 2量=1.393+0.0052+0.056+0.018+0.0058=1.478kg 渣中已存在的∑(CaO )量=白云石带入的CaO 量+炉衬带入的CaO 量+矿石带入的CaO 量 -铁水中S 消耗的CaO -矿石中S 成渣消耗的CaO=0.6365+0.003+0.010-0.0193-0.002=0.622 kg222()()()()(%)(%)()3.5 1.4780.6225.32891.08% 3.5 1.66%R SiO CaO R SiO CaO CaO CaO R SiO kg⨯-⨯-==-⨯⨯-==-⨯∑∑∑∑有效石灰石灰石灰加入量加入石灰成分及重量见表2-1-12S以[S]+(CaO)=(CaS)+[O]的形式反应,其中生成CaS量为:0.003×72/32=0.007,生成氧量为0.003×16/32=0.0016kg,消耗(CaO)量为0.003×56/32=0.0056kg6)终点氧化铁的确定根据生产实践数据,当终渣碱度为3.5,含碳量为0.15%时,终渣中(Fe2O3)=4%和(FeO)=8%。
7)终渣量及成分表2-1-13中不计(FeO)、(Fe2O3)在内的炉渣重量为(CaO +MgO+SiO2+P2O5 +MnO+ Al2O3+ CaS+ CaF2+ CaS)=5.497+0.678+1.566+0.169+0.284+0.090+0.267+0.033=8.584 kg已知渣中FeO量为12%,则渣中其它成分之和为88%,故炉渣总重量为8.584/88%=9.754kg 由此可知:(FeO)重量=9.754×8%=0.780kg 其中铁重 =0.780×56/72=0.607kg(Fe2O3)重量=9.754×4%=0.390kg 其中铁重=0.390×112/160=0.273kg将(FeO)和(Fe2O3)的值分别填入表2-1-7表2-1-13(二)矿石、烟尘中铁及氧量矿石带入的Fe量=1.00×(29.04%×56/72+61.80%×112/160)=0.661 kg烟尘带走的铁量=1.60×(77%×56/72+20%×48/160)=1.182 kg矿石带入的氧量=1.00×(29.04%×16/72+61.80%×48/160)=0.251kg烟尘消耗的氧量=1.60×(77%×16/72+20%×48/160)=0.370 kg(三)炉气成分及重量(见表2-1-14)表2-1-14表2-1-14中各项计算如下:CO重量= 8.932+0.045=8.977kgCO2重量=铁水中C被氧化成CO2的重量+炉衬中C被氧化成CO2的重量+白云石烧减的重量+石灰烧减的重量=2.290kgSO2重量=铁水中S气化而生成的氧化物重量=2.290kgH2O重量=矿石带入水分+萤石带入水分=0.005+0.006=0.011kg炉气中自由氧的体积=0.042m3炉气中自由氧的重量=0.042×32/22.4=0.061 kg炉气中N2的体积=0.084 m3炉气中N2的重量=0.084×28/22.4=0.105(四)氧气消耗量计算消耗和带入氧气的项目为:元素氧化耗氧重量 7.686 kg烟尘中铁氧化耗氧重量 0.370 kg炉衬中C氧化耗氧重量 0.033 kg萤石中磷氧化耗氧重量 0.002 kg炉气中自由氧含量 0.061 kg炉气中N2的重量 0.105 kg矿石分解带入及其中的硫把氧化钙还原出来的氧的重量:1.00×(61.8%×48/160+29.40%×16/72)+0.001=0.252 kg石灰中S把氧化钙还原出的氧重量0.002kg故氧气实际消耗量为:7.686+0.370+0.033+0.002+0.061+0.105-0.252-0.002=8.004kg换算成体积=8.004×22.4/32=5.603标m3 /kg铁水(五)钢水量的计算吹损包括下列组成项目:化学损失量 6.188kg烟尘中铁损 1.182kg渣中铁珠损失量 9.754×3%=0.293kg喷溅铁损失量 0.3kg矿石带入铁量 0.661kg故钢水重量为:100-(6.188+1.182+0.293+0.3)+0.661=92.995kg即钢水收得率为92.995%(六)物料平衡表以100公斤铁水为基础(见表2-1-15)表2-1-15计算误差=(收入项-支出项)/收入项×100%=(116.032-116.397)/116.032×100% =-0.145%三、热平衡计算为简化计算,取冷料入炉温度均为25℃(一)热收入相1、铁水物理热铁水熔点=1536-(4.5×100+0.65×8+0.55×5+0.08×30+0.04×25) -7=1067.65℃式中100、8、5、30、25分别是C、Si、Mn、P、S增加1%含量降低铁水的熔点值;7为O、H、N共降低铁水的熔点值;1563为纯铁熔点,取铁水温度为1350℃。
则:铁水物理热=100×{0.178×(1067.65-25)+52+0.2×(1350-1089)}=29406.17 kcal2、铁水中各元素氧化放热及成渣热C-----CO 3.828×2616.9=10017.5 kcalC-----CO20.522×8250.7=4306.9 kcalSi---SiO2 0.65×6767.2=4398.7 kcalMn---MnO 0.22×1677.9=369.1 kcalFe--- FeO 0.607×1150.5=698.4 kcalFe---- Fe2O3 0.273×1758.1=480.0 kcalP---- P2O5 0.072×4522.6=325.6 kcalP2O5----4 CaO. P2O5 0.165×1162.1=197.7 kcalSiO2---------2 CaO SiO2. 1.393×495.0=689.5 kcal共计 21483.4 kcal3、烟尘氧化放热1.6 ×(77%×56/72×1150.5+20%×112/160×1758.1)=1496.2 kcal则热收入总量:29406.2+21483.4+1496.2=52832.4kcal(二)热支出项1、钢水物理热钢水熔点=1536-(0.150×65+0.33×5+0.008×30+0.024×25)-7=1517℃式中65、5、30、25分别为钢中元素C、Mn、P、S增加1%时钢水熔点的降低值,℃。
确定出钢温度:(1)钢水过热度取20—30℃,取25℃;(2)△t1为出钢温度损失。
取出钢时间为5min,平均温降10℃/min,则出钢温降为50℃;(3)△t2为吹Ar搅拌温度损失,转炉吹Ar一般为3—5min,取4min,温降5℃/min,则吹温降为20℃;(4)△t3为钢水罐在停留时间内的温降,取12℃;(5)△t4为钢水罐在浇注时间内的钢水温度损失,取40℃.则出钢温度=1517+25+50+20+12+40=1664℃则钢水物理热=92.995×[0.167×(1517-25)+65+0.20×(1664-1517)]=31949.73kcal2、炉渣物理热取终点炉渣温度与钢水温度相同,即1664℃。