炼钢过程中的物料平衡与热平衡计算复习课程
第2章炼钢过程的物料平衡和热平衡计算
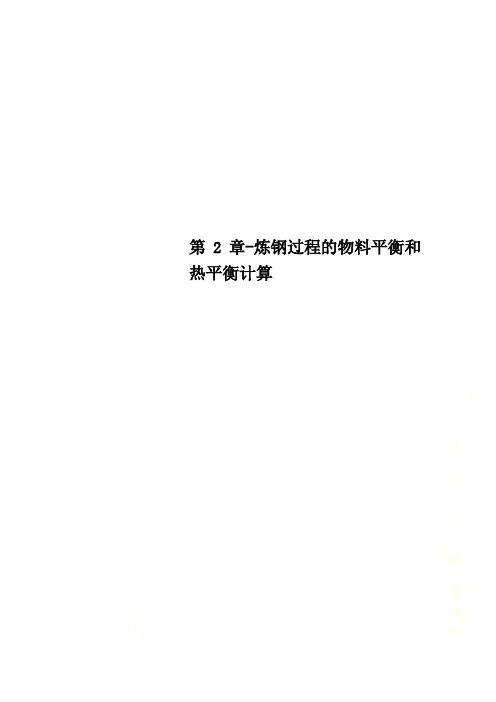
第2章-炼钢过程的物料平衡和热平衡计算第2章炼钢过程的物料平衡和热平衡计算炼钢过程的物料平衡和热平衡计算是建立在物质与能量守恒的基础上的。
其主要目的是比较整个过程中物料、能量的收入项和支出项,为改进操作工艺制度,确定合理的设计参数和提高炼钢技术经济指标提供定量依据。
由于炼钢是一个复杂的高温物理化学变化过程,加上测试手段有限,目前还难以做到精确取值和计算。
尽管如此,它对指导炼钢生产和设计仍有重要的意义。
2.1物料平衡计算2.1.1 计算原始数据基本原始数据有:冶炼钢种及其成分,铁水和废钢的成分,终点钢水成分(见表2.1);造渣用溶剂及炉衬等原材料的成分(见表2.2):脱氧和合金化用铁合金的成分及其回收率(表2.3);其他工艺参数(表2.4)。
表2-1 钢种、铁水、废钢和终点钢水的成分设定值类别C Si Mn P S成分含量%钢种Q235A设定值0.18 0.25 0.55 ≤0.045 ≤0.005 铁水设定值 4.2 0.50 0.75 0.20 0.025 废钢设定值0.20 0.25 0.43 0.020 0.032 终点钢水设定值0.10 痕迹0.250 0.015 0.002表2-2 原材料成分类别成分% CaO SiO2MgO Al2O3Fe2O3CaF2P2O5S CO2H2O C 灰分挥发分石灰88.66 2.70 2.60 1.50 0.50 0.10 0.064.64 0.10萤石0.30 5.50 0.60 1.60 1.50 88.00 0.90 0.11.50生石灰石36.400.80 25.61.00 36.2炉衬 1.20 3.00 78.81.40 1.60 14.0焦炭0.58 81.50 12.4 0表2.3 铁合金成分(分子)及其回收率(分母)类别成分含量/回收率/%C Si Mn Al P S Fe硅铁—73.00/75 0.50/80 2.50/0 0.05/100 0.03/100 23.92/100 锰铁 6.60/90 0.50/75 67.8/80 —0.23/100 0.13/100 24.74/1002表2.4 其他工艺参数设定值名称参数名称参数终渣碱度萤石加入量生白云石加入量炉衬蚀损量终渣∑(FeO)含量(按向钢中传氧量ω(Fe2O3)=1.35ω(FeO)折算)烟尘量喷溅铁损ω(CaO)∕ω(SiO2)=3.5为铁水量的0.5%为铁水量的2.5%为铁水量的0.3%15%,而ω(Fe2O3)/∑ω(FeO)=1/3,即ω(Fe2O3)=5%,ω(FeO)=8.25%为铁水量的1.5%(其中ω(FeO)为75%,ω(Fe2O3)为20%)为铁水量的1%渣中铁损(铁珠)氧气纯度炉气中自由氧含量气化去硫量金属中[C]的氧化产物废钢量为渣量的6%99%,余者为N20.5%(体积比)占总去硫量的1/390%的C氧化成CO,10%的C氧化成CO2由热平衡计算确定,本计算结果为铁水量的13.7%,即废钢比为12.05%2.1.2 物料平衡基本项目收入项有:铁水、废钢、溶剂(石灰、萤石、轻烧白云石)、氧气、炉衬蚀损、铁合金。
转炉炼钢物料平衡和热平衡计算 模板-
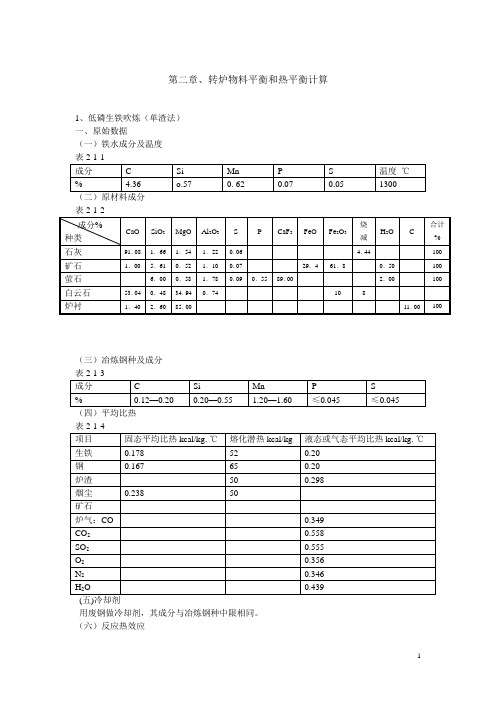
第二章、转炉物料平衡和热平衡计算1、低磷生铁吹炼(单渣法)一、原始数据(一)铁水成分及温度(二)原材料成分(三)冶炼钢种及成分(四)平均比热(五)冷却剂用废钢做冷却剂,其成分与冶炼钢种中限相同。
(六)反应热效应反应热效应通常采用25℃为参考温度,比较常用的反应数据见表2-1-5(七)根据国内转炉实测数据选取1、渣中铁珠量为渣量的2.5%;2、金属中[C]假定85%氧化成CO,15%氧化成CO2;3、喷溅铁损为铁水量的0.3%;4、取炉气平均温度1450℃,自由氧含量0.5%,烟尘量为铁水量的1.8%,其中FeO=75%,Fe203=22%;5、炉衬侵蚀量为铁水量的0.15%;6、氧气成分为98.9% O2,1.5% N2。
根据铁水成分,渣料质量,采用单渣不留渣操作。
先以100公斤铁水为计算基础。
(一)炉渣及其成分的计算1、铁水中各元素氧化量表2-1-6成分,kgC Si Mn P S 合计项目铁水 4.36 0.57 0.62 0.07 0.05终点钢水0.13 痕迹0.13 0.008 0.019氧化量 4.23 0.57 0.49 0.062 0.031 5.308 [C]:取终点钢水含碳量0.15%;[Si]:在碱性氧气转炉炼钢中,铁水中的Si几乎全部被氧化;[Mn]:顶底复吹转炉残锰量取60%;[P]:采用低磷铁水吹炼,铁水中磷90%进入炉渣,10%留在钢中;[S]:氧气转炉去硫率不高,取40%。
2、各元素氧化量,耗氧量及其氧化产物量见表2-1-73、造渣剂成分及数量根据国内同类转炉有关数据选取1)矿石加入量及成分矿石加入量为1.00公斤/100公斤铁水,成分及重量见表2-1-82)萤石加入量及成分萤石加入量为0.30kg/kg铁水,其成分及重量见表2-1-93)炉衬侵蚀量为0.200公斤/100公斤铁水,其成分及重量见2-1-104)生白云石加入量及成分加入的白云石后,须保证渣中(MgO)含量在6—8%之间,经试算后取轻烧白云石加入量为1.2公斤/100公斤铁水。
铁冶金学18-物料平衡与热平衡
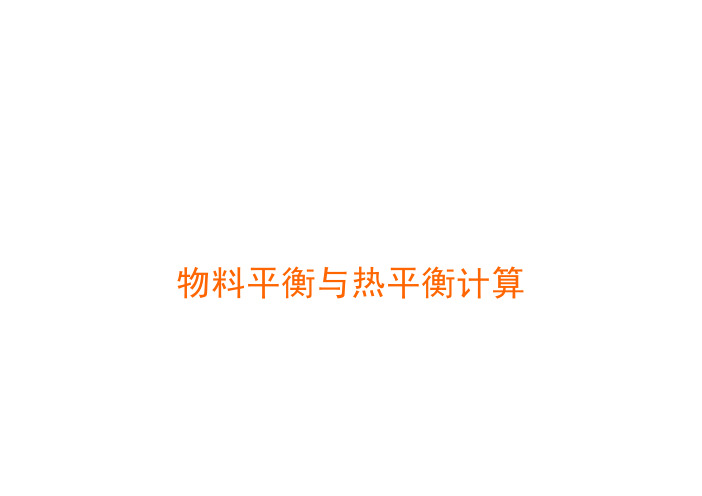
[Fe] =95.29% [C]=100―95.29―0.45―0.025―0.047―0.023=4.165 %
校核后生铁成分,%
Fe 95.29
Si 0.45
Mn 0.025
P 0.047
S 0.023
C 4.165
效验结果与预定生铁成分相符合,计算正确。若效验成分不符合时,可变更 C 量,或重新给定生铁成分,重新 计算。
以上碱度的计算需要考虑脱硫消耗的 CaO,即 脱硫所耗 CaO=3.218×56/32=5.63 kg, R= CaO/ SiO2=
114.57 5.63 1.207 90.23
校核生铁成分: [S]= 0.023%;LS= [Si]=0.45% [P]=1586×0.03%/1000=0.047% [Mn]=0.32×55/71×1/1000=0.025%
(4)直接还原消耗的 C 量 1)锰还原消耗的 C 量 GC 锰=1000×0.025×12/55=0.055 kg 2)磷还原消耗的 C 量 GC 磷=1000×0.047%×60/62=0.455 kg 3)铁还原消耗的 C 量 GC 铁=1000×95.29%×12/56×0.38=77.59 kg 4)硅还原消耗的 C 量 GC 硅=1000×0.45%×24/28=3.86 kg 故 GC 直=77.59+0.455+3.86+0.055=81.96 kg (5)炉渣脱硫用 C 量 GCS=3.218×12/32=1.21 kg (6)计算鼓风量 V 风 风口前燃烧的 C 量为=425.82-41.65-4.684-81.96=296.32 kg 1)鼓风中氧的浓度=21%(1—1.493%)+0.5×1.493%=21.43% 2)GC 燃燃烧所需要氧的体积 VO2=296.32×22.4/24=276.57m³ 3)煤粉带入氧体积 VO2=180×(2.33%+0.83%×16/18)×22.4/32=3.87 m³
【精品】物料平衡与热平衡计算
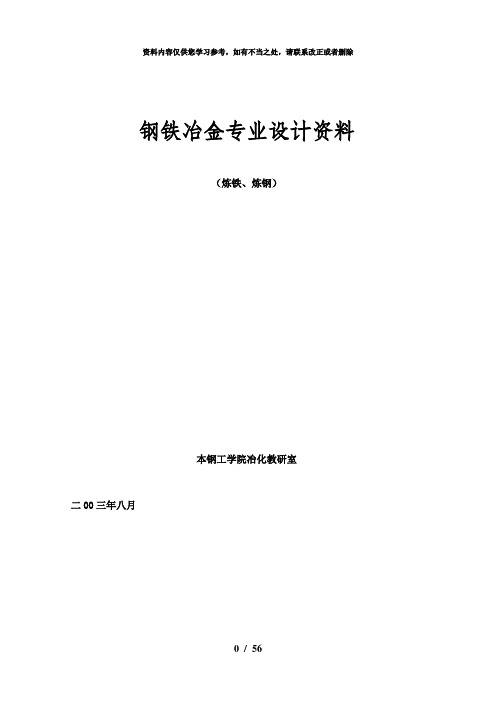
钢铁冶金专业设计资料(炼铁、炼钢)本钢工学院冶化教研室二00三年八月第一章物料平衡与热平衡计算物料平衡和热平衡计算是氧气顶吹转炉冶炼工艺设计的一项基本的计算,它是建立在物质和能量不灭定律的基础上的。
它以转炉作为考察对象,根据装入转炉内或参与炼钢过程的全部物料数据和炼钢过程的全部产物数据,如图1—1-1所示的收入项数据和支出项数据,来进行物料的重量和热平衡计算.通过计算,可以定量地掌握冶炼工重要参数,做到“胸中有数”.对指导生产和分析研究改进冶炼工艺,设计转炉炼钢车间等均有其重要意义.由于转炉炼钢过程是一个十分复杂的物理化学过程,很显然,要求进行精确的计算较为困难,特别是热平衡,只能是近似计算,但它仍然有十分重要的指导意义。
物料平衡和热平衡计算,一般可分为两面种方案.第一种方案是为了设计转炉及其氧枪设备以及相应的转炉炼钢车间而进行的计算,通常侧重于理论计算,特别是新设计转炉而无实际炉型可以参考的情况下;另一种方案是为了校核和改善已投产的转炉冶炼工艺参数及其设备参数或者采用新工艺新技术等,而由实测数据进行的计算,后者侧重于实测.本计算是采用第一种方案。
目前,我国顶吹转炉所采用的生铁基本上为低磷的(0.10~0。
40%)和中磷的(0.40~1。
00%)两种,对这两种不同含磷量生铁的冶炼工艺制度也不相同。
因此,下面以50吨转炉为例,分别就低磷生铁和高磷生铁两种情况,进行物料平衡和热平衡计算.1.1原始数据1。
1.1铁水成分及温度表1—1—11.1.2原材料成分表1-1—2原材料成分2 / 563 / 563 / 56表2—1-1铁水成分与温度转炉冶炼钢种常为普通碳素钢和低合金钢,在此以要求冶炼BD 3钢考虑,其成分见表2—1—31。
1。
4平均比热表1-1-41.1。
5冷却剂用废钢作冷却剂,其成份与冶炼钢种成份的中限相同。
(见表1-1-3)1。
1。
6反应热效应虽然炉内化学反应,实际上是在炉料温度和炉内上部气相温度之间的任一温度发生的,但反应热效应通常仍采用25℃作为参考温度,值得指出的是,反应热还与组分在铁水中存在形态有关,至今对参与化学反应有关的实际组成物还有不同的看法.但是,比较常用的反应热数据见表1-1—5。
炼铁物料平衡及能量平衡计算

矿石(混合矿)消耗量: Fe平衡方程
PFe%矿 + Fe熔 + Fe废 + Fe焦 + Fe喷 = Fe生 + Fe渣 + Fe尘
P
Fe生 Fe渣 Fe尘 Fe熔 Fe废 Fe焦 Fe喷 Fe% 矿
Fe熔 = 熔剂量 Fe%熔 Fe焦 = 干焦比(55.85/71.85FeO%焦灰+55.85/87.85FeS%焦灰) Fe喷 = 喷吹量(111.7/159.7Fe2O3%喷+55.85/71.85FeO%喷 +55.85/87.85FeS%喷) Fe废 = 废铁量 Fe%废 Fe生 = 1000 [Fe%] = 10 [Fe] Fe渣 = 1000[Fe%]Fe Fe (=0.002~0.003,=0.998~0.997) Fe尘 = 炉尘量 Fe%尘
1 V V2O5渣 = 182 10 [V] 102
1 Mn 71 10 [Mn] 55 Mn
FeO渣 =
1 Fe 71.85 10 [Fe] 55.85 Fe
(K+Na)2O渣 = ( (K+Na)2O矿 + (K+Na)2O熔 + (K+Na)2O废 + (K+Na)2O焦灰 + (K+Na)2O喷 (K+Na)2O尘
要求:实际(RO) = (CaO)+(MgO)+(MnO)+(FeO) (RO)min 。 按沃斯柯博依尼科夫经验公式计算硫分配比 LS (见p.178): 要求:实际 LS = (S) [S] LS
物料平衡与热平衡计算
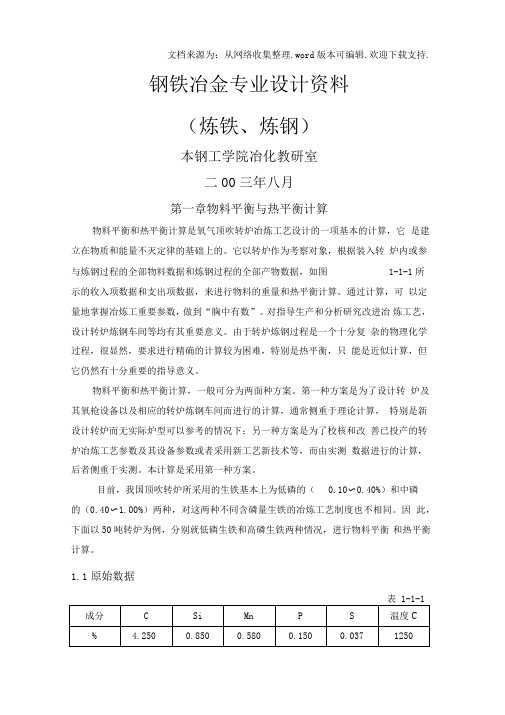
文档来源为:从网络收集整理.word版本可编辑.欢迎下载支持.钢铁冶金专业设计资料(炼铁、炼钢)本钢工学院冶化教研室二00三年八月第一章物料平衡与热平衡计算物料平衡和热平衡计算是氧气顶吹转炉冶炼工艺设计的一项基本的计算,它是建立在物质和能量不灭定律的基础上的。
它以转炉作为考察对象,根据装入转炉内或参与炼钢过程的全部物料数据和炼钢过程的全部产物数据,如图1-1-1所示的收入项数据和支出项数据,来进行物料的重量和热平衡计算。
通过计算,可以定量地掌握冶炼工重要参数,做到“胸中有数”。
对指导生产和分析研究改进冶炼工艺,设计转炉炼钢车间等均有其重要意义。
由于转炉炼钢过程是一个十分复杂的物理化学过程,很显然,要求进行精确的计算较为困难,特别是热平衡,只能是近似计算,但它仍然有十分重要的指导意义。
物料平衡和热平衡计算,一般可分为两面种方案。
第一种方案是为了设计转炉及其氧枪设备以及相应的转炉炼钢车间而进行的计算,通常侧重于理论计算,特别是新设计转炉而无实际炉型可以参考的情况下;另一种方案是为了校核和改善已投产的转炉冶炼工艺参数及其设备参数或者采用新工艺新技术等,而由实测数据进行的计算,后者侧重于实测。
本计算是采用第一种方案。
目前,我国顶吹转炉所采用的生铁基本上为低磷的(0.10〜0.40%)和中磷的(0.40〜1.00%)两种,对这两种不同含磷量生铁的冶炼工艺制度也不相同。
因此,下面以50吨转炉为例,分别就低磷生铁和高磷生铁两种情况,进行物料平衡和热平衡计算。
1.1原始数据表 1-1-1表1-1-2原材料成分表2-1-1铁水成分与温度转炉冶炼钢种常为普通碳素钢和低合金钢,在此以要求冶炼BD3钢考虑,其成分见表2-1-31-1-4用废钢作冷却剂,其成份与冶炼钢种成份的中限相同。
(见表1-1-3)虽然炉内化学反应,实际上是在炉料温度和炉内上部气相温度之间的任一温度发生的,但反应热效应通常仍采用25 C作为参考温度,值得指出的是,反应热还与组分在铁水中存在形态有关,至今对参与化学反应有关的实际组成物还有不同的看法。
电炉炼钢设计(物料平衡+热平衡)
炼钢过程的物料平衡与热平衡计算是建立在物质
生铁
锰铁硅铁
物料平衡计算前,必须确定冶炼设备和方法以及炉
现代电弧炉冶炼工艺与传统三段式有较大的变化
火砖块是浇铸系统的废弃品,它的
配碳比钢种规格中线高0.70%,焦炭的收得率按75%计(7-28)
熔化期脱碳量30%,
CO:CO2=7:3,下同
Fe含量见表7-29
余见注释
焦炭中C含量
烧损率为25%
石灰中的S含
量为0.06%
(3)确定炉渣量:炉渣源于炉料中Si、Mn、P、Fe等元素的氧化产物,炉顶和炉衬的蚀损,焦炭和电极中的灰分,以及加入的各种溶剂。
结果见表7-32.
(4)确定金属量:金属量Qi=金属炉料重+矿石带入的铁量-炉料中C、Si、Mn、P和Fe的烧损量+焦炭配入得碳量
炉顶、炉衬消耗
量见表7-28
烧损的Fe,其中20%进入渣中,其中75%为Fe2O3,25%为FeO
引起氧化期物料波动的因素有:扒除熔化渣,造新渣;金属中
还原期采用白渣操作,引起该期物料变化的因素有:。
第2章炼钢过程的物料平衡和热平衡计算
第2章炼钢过程的物料平衡和热平衡计算炼钢是通过将生铁加热到高温,然后进行氧化还原反应来去除杂质的过程。
在炼钢过程中,物料平衡和热平衡是非常重要的计算,以确保过程的稳定性和效率。
首先,让我们来看一下炼钢过程中的物料平衡计算。
物料平衡是指在炼钢过程中输入和输出物料的量之间的平衡。
在炼钢过程中,主要的输入物料是生铁、石灰石、废钢等,而主要的输出物料是炼钢渣、废气和钢水等。
物料平衡计算可以通过考虑每个输入和输出物料的质量来完成。
首先需要确定每个输入物料的质量,并计算出每个输入物料的总量。
然后需要确定每个输出物料的质量,并计算出每个输出物料的总量。
最后,通过比较输入和输出物料的总量,可以确定物料平衡是否达到。
在炼钢过程中,石灰石主要用于吸附硫化物和冶炼渣的形成,废钢用于加碳和提供合金元素。
当炼钢渣形成时,一些杂质也会被吸附在渣中,从而净化钢水。
因此,通过控制输入物料的质量,并进行物料平衡计算,可以确保炼钢过程中的物料平衡。
其次,让我们来看一下炼钢过程中的热平衡计算。
热平衡是指在炼钢过程中输入和输出热量之间的平衡。
在炼钢过程中,主要的输入热量是燃料的燃烧热量,而主要的输出热量是废气和钢水。
热平衡计算可以通过考虑每个输入和输出热量的量来完成。
首先需要确定每个输入热量的量,并计算出每个输入热量的总量。
然后需要确定每个输出热量的量,并计算出每个输出热量的总量。
最后,通过比较输入和输出热量的总量,可以确定热平衡是否达到。
在炼钢过程中,需要控制燃料的燃烧速率和炉内气体的流动速率,以确保输入和输出热量的平衡。
此外,还可以通过热回收和余热利用来提高热平衡效果。
例如,可以使用余热回收装置来回收废气中的热能,并将其用于加热其他冷却介质。
综上所述,物料平衡和热平衡计算是炼钢过程中非常重要的计算。
通过控制输入物料的质量和量,并考虑输入和输出热量的平衡,可以确保炼钢过程的稳定性和效率。
此外,还可以使用其他技术和设备来提高物料平衡和热平衡效果,以进一步提高炼钢过程的效率。
《物料平衡和热平衡》课件
热平衡描述的是一个系统或环境在不受外界影响或外界影响可以忽略不计的情况下,热量自然传递和分布达到的稳定状态。在这种状态下,系统内部各部分之间的温度差很小,系统内部热量的传递速率与外界对系统热量传递的速率相等,系统内部温度呈现均匀分布。
详细描述
总结词:热平衡的应用非常广泛,涉及到工业生产、环境保护、能源利用等多个领域。例如,在工业生产中,需要控制温度、压力等参数以达到最佳的生产效果;在环境保护中,需要研究大气、水体等自然环境的热平衡状态,以了解其对人类生存的影响;在能源利用中,需要研究各种能源转换和利用过程中的热平衡问题,以提高能源利用效率。
总结词
在环境科学领域,物料平衡和热平衡是研究污染物迁移转化机制的重要工具。
详细描述
在环境科学研究中,物料平衡和热平衡技术被广泛应用于污染物迁移转化机制的研究。通过物料平衡分析,可以了解污染物在环境中的分布和迁移规律,预测其对生态系统的影响。热平衡技术则可以帮助研究污染物在环境中的扩散、吸附、降解等过程,为污染治理和环境保护提供科学依据和技术支持。
数据处理
使用数据采集和处理系统,对实验数据进行处理和分析,得出实验结果。
实验总结
根据实验结果,总结实验结论,评估实验效果,提出改进意见。
物料平衡和热平衡的实际应用
总结词
在化工生产中,物料平衡和热平衡是关键的工艺控制要素,对产品的质量和产量具有重要影响。
要点一
要点二
详细描述
在化工生产过程中,需要精确控制原料的投入和产物的输出,以实现最佳的工艺效果。物料平衡通过对原料和产物的数量和质量进行监测和控制,确保生产过程中的物质守恒,从而提高产品的纯度和收率。热平衡则涉及到反应过程中的热量传递和利用,通过对温度、压力等工艺参数的调节,优化反应条件,提高能源利用效率和产品质量。
转炉炼钢物料及热平衡
物料及热量平衡计算(一)、工艺条件及工艺要求1、铁水条件:化学成分:碳:4.5% 硅:0.5% 锰:0.20% 硫:0.045% 磷:0.110%,铁水温度:1350℃2、炉渣成分:碱度3.0,氧化镁10%,3、各辅料成分:石灰(CaO)85% ,二氧化硅1.50%;轻烧白云石:氧化镁28%,氧化钙48%;镁球:氧化镁:65%4、总装入量115吨5、出钢温度:1680℃(二)废钢比计算:1、设上述条件下:铁水x吨废钢y吨X+Y==115设冶炼钢种HRB335,成分:【C】0.21% [Si]0.35% [Mn]1.35% [S]0.030% [P]0.035%2、热收入2.1、铁水物理热:按常温下25℃计算铁的熔点Tf=1539-(100*4.5+8*0.5+5*0.2+30*0.15+25*0.045+7)=1080℃铁的物理热=X*1000[0.744*(1080-25)+217.486+0.8368*(1350-1080)]=1228342X Kj2.2、元素放热:钢水终点【C】0.1%,锰按氧化40%计算,碳氧化成90%CO,10%CO2计算C—CO(4.5-0.1)%*90%*10940*X*1000=433220X KjC—CO2(4.5-0.1)%*10%*34220*X*1000=150570X KjSi—SiO2 0.5%*28314*X*1000=141570*XMn—MnO (0.2-40%*0.2)%*7020*X*1000=8424X KjP—P2O5 0.11*75%*18923*X*1000=15610X Kj实际生产中【P】按氧化75%计算3、热支出3.1、钢熔点Tf=1539—(65*0.21+5*0.35+5*1.35+30*0.035+25*0.030+7)=1508℃装入量115T按实际出钢量108T计算3.2、钢水的物理热=108*1000【0.699*(1508-25)+271.96+0.8368(1680-1508)】=156870756 Kj3.3、钢渣的物理热=115*1000*11%【1.247(1680-25)+209.2】=28753260Kj (渣量按装入量的11%计算)3.4、炉气的的物理热:主要按炉气生成CO和CO2计算,炉气温度1450℃【C】+1/2O2=CO (4.5-0.1)%*90%*28/12=0.0924Kg【C】+1/2O2=CO2 (4.5-0.1)%*90%*44/12=0.0161Kg 则炉气物理热=(0.0924+0.0161)*1.136*(1450-25)*X*1000=175639.8X Kj4、热收入=热支出则得出1977736X=156870756+287532260.25+175639.8X解得铁水=103废钢y==12t(二) (1)铁水【Si】波动0.1%,调整废钢量【Si】波动0.1%则放热波动如下:103*1000*0.1%*28314=2916342K j 根据资料这部分热量的70%用于熔池有效升温每公斤废钢的冷却效应(按出钢温度1680℃,废钢熔点1500℃)Q 废=1*【0.699(1500-25)+271.96+0.8368(1680-1500)】=1453.609Kj/Kg 则得出铁水【Si】波动0.1%,调整废钢量为:2916342*70%/1453.609=1400Kg=1.4t(2) 每吨废钢的降温值(出钢量108t)1453.609*1000=108*1000*0.8368*△t △t=16.1℃.根据经验与资料取△t=14.5℃(3)铁水温度波动10℃调整废钢量,铁水温度波动10℃,则带入的物理热波动为103*1000*0.8367*10=861801Kj 70%用于有效升温则调整废钢量为861801*70%/1453.609=415Kg(4)增加1t铁水,则带入的物理热为1000*【0.744(1080-25)+217.486+0.8368(1350-1080)】=1228342(Kj)元素放热增加如下:C—CO 433220Kj C—CO2 150570Kj Si—SiO2 141570Kj Mn—MnO 8424Kj P—P2O5 15610Kj 总计 621974Kj增加1t铁水总计增加的热量1228342+621974Kj=1850316Kj 70%用于有效升温,则能使钢水升温△t℃则得出:1228342*70%+621947*70=108*1000*0.8368*△t △t=20℃(三)(1)如果每炉烧结矿定为3吨,则需减废钢Xt,增加铁水y吨(103+y)+(12-x)=115,14.5x+20y=3*43 得出x=y=3.74吨即铁水调整为103+3.74=106.74t 废钢调整为12—3.74=8.26t(2)如果烧结矿定位4t 需减废钢Xt增加铁水y吨(103+ y)+(12-X)=115 ,14.5x+20y=4*43 得出x=4.98≈5t,y=4.98≈5t 即铁水调整为103+5=108t 废钢调整为12-5=7t.附表:各冷却剂降温值。
- 1、下载文档前请自行甄别文档内容的完整性,平台不提供额外的编辑、内容补充、找答案等附加服务。
- 2、"仅部分预览"的文档,不可在线预览部分如存在完整性等问题,可反馈申请退款(可完整预览的文档不适用该条件!)。
- 3、如文档侵犯您的权益,请联系客服反馈,我们会尽快为您处理(人工客服工作时间:9:00-18:30)。
炼钢过程中的物料平衡与热平衡计算炼钢过程的物料平衡与热平衡计算炼钢过程的物料平衡与热平衡计算是建立在物质与能量守恒的基础上。
其主要目的是比较整个冶炼过程中物料、能量的收入项和支出项,为改进操作工艺制度,确定合理的设计参数和提高炼钢技术经济指标提供某些定量依据。
应当指出,由于炼钢系复杂的高温物理化学过程,加上测试手段有限,目前尚难以做到精确取值和计算。
尽管如此,它对指导炼钢生产和设计仍有重要的意义。
本章主要结合实例阐述氧气顶吹转炉和电弧炉氧化法炼钢过程物料平衡和热平衡计算的基本步骤和方法,同时列出一些供计算用的原始参考数据。
1.1 物料平衡计算(1)计算所需原始数据。
基本原始数据有:冶炼钢种及其成分(表1);金属料—铁水和废钢的成分(表1);终点钢水成分(表1);造渣用溶剂及炉衬等原材料的成分(表2);脱氧和合金化用铁合金的成分及其回收率(表3);其它工艺参数(表4).表1 钢种、铁水、废钢和终点钢水的成分设定值①本计算设定的冶炼钢种为H15Mn。
②[C]和[Si]按实际生产情况选取;[Mn]、[P]和[S]分别按铁水中相应成分含量的30%、10%和60%留在钢水中设定。
表2 原材料成分表3 铁合金成分(分子)及其回收率(分母)①10%C与氧生产CO2表4 其它工艺参数设定值(2)物料平衡基本项目。
收入项有:铁水、废钢、溶剂(石灰、萤石、轻烧白云石)、氧气、炉衬蚀损、铁合金。
支出项有:钢水、炉渣、烟尘、渣中铁珠、炉气、喷溅。
(3)计算步骤。
以100kg铁水为基础进行计算。
第一步:计算脱氧和合金化前的总渣量及其成分。
总渣量包括铁水中元素氧化、炉衬蚀损和加入溶剂的成渣量。
其各项成渣量分别列于表5、6和7。
总渣量及其成分如表8所示。
第二步:计算氧气消耗量。
氧气实际消耗量系消耗项目与供入项目之差,详见表9。
表5 铁水中元素的氧化产物及其成渣量①由CaO还原出的氧量,消耗的CaO量=0.013×56/32=0.023kg表6 炉衬蚀损的成渣量表7 加入溶剂的成渣量石灰加入量计算如下:由表5~7可知,渣中已含(CaO)= -0.455+0.004+0.002+0.910=0.461kg;渣中已含(SiO2)=0.857+0.009+0.028+0.022=0.914kg.因设定的终渣碱度R=3.5;故石灰加入量为: [R∑w(SiO2)-∑w(CaO)]/[w(CaOR×w(SiO2石灰)]= 2.738/(88.00%-3.5×2.50%)=3.45kg石灰)-②为(石灰中CaO含量)—(石灰中S→CaS自耗的CaO量)。
②由CaO还原出的氧量,计算方法同表5之注。
表8 总渣量及其成分总渣量计算如下:因为表8中除(FeO)和(Fe 2O 3)以外的渣量为:5.965+1.700+1.102+0.124+0.615+0.440+0.540+0.038=7.100kg,而终渣∑w(FeO)=15%(表4-4),故总渣量为7.1/86.75%=8.184kg ③ w(FeO)=8.184×8.25%=0.675kg.④ w(Fe 2O 3)=8.184×5%—0.017—0.005—0.008=0.379kg.表9 实际耗氧量①为炉气中N 2之重量,详见表10 第三步:计算炉气量及其成分。
炉气中含有CO 、CO 2、O 2、N 2、SO 2和H 2O 。
其中CO 、CO 2、SO 2和H 2O 可由表4-5~4-7查得,O 2和N 2则由炉气总体积来确定。
现计算如下。
炉气总体积V ∑:g s x 122.40.5%G 0.5%9932V V V V V ∑∑∑⎛⎫=+++-⎪⎝⎭V ∑ =990.7 98.50g s xV G V +-=998.6190.78.1860.00222.4/3298.50⨯+⨯-⨯ =8.721 m 3式中V g —CO 、CO 2、SO 2和H 2O 诸组分之总体积,m 3。
本计算中,其值为8.950×22.4/28+2.837×22.4/44+0.002×22.4/64+0.011×22.4/18=8.619 m 3G—不计自由氧的氧气消耗量,kg。
本计算中,其值为7.851+0.062+0.23=8.619 m3(见表S9);V—铁水与石灰中的S与CaO反应还原出的氧量,m3。
本计算中,其值为0.002kg(见表9) X0.5%—炉气中自由氧含量,m3;99—由氧气纯度为99%转换得来。
计算结果列于表10表10 炉气量及其成分①炉气中O2体积为8.384×0.5%=0.042 m3 ;质量为0.042×32/22.4=0.062 kg。
②炉气中N2的体积系炉气总体积与其他成分的体积之差;质量为0.052×28/22.4=0.065kg。
第四步:计算脱氧和合金化前的钢水量。
=铁水量—铁水中元素的氧化量—烟尘、喷溅和渣中的铁损钢水量Qg=100-5.699-﹝1.00×(75%×56/72+20%×112/160)+1+8.184×6%﹞=91.725kg据此可以编制脱氧和合金化前的物料平衡表(表11)。
表11 未加废钢时的物料平衡表注:计算误差为(114.25—114.34)/114.25×100%= -0.010%第五步:计算加入废钢的物料平衡。
如同“第一步”计算铁水中元素氧化量一样,利用表1的数据先确定废钢中元素的氧化量及其耗氧量和成渣量(表12),再将其与表11归类合并,遂得加入废钢后的物料平衡表13和表14表12 废钢中元素的氧化产物及其成渣量表13 加入废钢的物料平衡表(以100kg铁水为基础)注:计算误差为(125.238—125.358)/125.238×100%= —0.1%表14 加入废钢的物料平衡表(以100kg(铁水+废钢)为基础)第六步:计算脱氧和合金化后的物料平衡。
先根据钢种成分设定值(表1)和铁合金成分及其烧损率(表3)算出锰铁和硅铁的加入量,再计算其元素的烧损量。
将所得结果与表14归类合并,既得冶炼一炉钢的总物料平衡表。
锰铁加入量W Mn为:W Mn =[][]w Mn w Mnn nM M-⨯钢种终点锰铁含量回收率×钢水量=0.95%0.21%67.80%80%-⨯×92.02=1.255kg硅铁加入量W Si为:W Si=[][][]FeMn (w Si w Si)SiSi Si-⨯⨯钢种终点加锰铁后的钢水量-硅铁含量回收率=()0.03%92.021.0760.00573.00%75%⨯+-⨯=0.042kg铁合金中元素的烧损量和产物量列于表15。
表15 铁合金中元素烧损量及产物量①可以忽略脱氧和合金化后的钢水成分如下:w(C)=0.08%+0.07593.129×100%=16%w(Si)=0.0050.02393.129+×100%=0.03%w(Mn)=0.210%+0.6810.000293.129+×100%=0.94%w(P)=0.019%+0.00393.129×100%=0.022%w(S)=0.016%+0.00293.129×100%=0.018%可见,含碳量尚未达到设定值。
为此需在钢包内加焦粉增碳。
其加入量W1为W 1 =()0.170.16%C C-⨯⨯钢水量焦炭含量回收率=0.01%93.12981.50%75%⨯⨯=0.015kg焦炭生成的产物如下:①CO2、H2O和挥发份之总和(未计挥发份燃烧的影响)由此可得冶炼过程(即脱氧和合金化后)的总物料平衡表16表16 总物料平衡表注:计算误差为(114.21—114.28)/114.21×100%= —0.1%①可以近视认为(0.082+0.008)的氧量系出钢水二次氧化所带入。
1.2 热平衡计算(1)计算所需原始数据。
计算所需基本原始数据有:各种入炉料及产物的温度(表17);物料平均热容(表18);反应热效应(表19);溶入铁水中的元素对铁熔点的影响(表20)。
其它数据参照物料平衡选取。
表17 入炉物料及产物的温度设定值①纯铁熔点为1536℃表18 物料平均热容表19 炼钢温度下的反应热效应}表20 溶入铁中的元素对铁熔点的降低值(2)计算步骤。
以100kg 铁水为基础。
第一步:计算热收入Q s 。
热收入项包括:铁水物理热;元素氧化热及成渣热;烟尘氧化热;炉衬中碳的氧化热。
(1)铁水物理热Q w :先根据纯铁熔点、铁水成分以及溶入元素对铁熔点的降低值(表17、1和20)计算铁水熔点T t ,然后由铁水温度和生铁比热(表17和18)确定Q w 。
T t =1536-(4.2×100+0.4×8+0.45×5+0.12×30+0.06×25)-6=1099.45℃ Q w =100×〔0.745×(1082-25)+218+0.837×(1300-1082)〕=118632.56KJ(2)元素氧化热及成渣热Q y :由铁水中元素氧化量和反应热效应(表19)可以算出,其结果列于表21。
表21 元素氧化热和成渣热(3)烟尘氧化热Q c :由表4中给出的烟尘量参数和反应热效应计算可得。
Q C =1.5×(75%×56/72×4250+20%×112/160×6460)=5075.35KJ (4)炉衬中碳的氧化热Q I :根据炉衬蚀损量及其含碳量确定。
I =0.314%90%11639+0.314%10%34834=586.25KJQ⨯⨯⨯⨯⨯⨯故热收入总值为 :QS=Q W+Q Y+Q C+Q I=227582.40KJ第二步:计算热支出Q Z。
热支出项包括:钢水物理热;炉渣物理热;烟尘物理热;炉气物理热;渣中铁珠物理热;喷溅物(金属)物理热;轻烧白云石分解热;热损失;废钢吸热。
(1)钢水物理热Q g:先按求铁水熔点的方法确定钢水熔点T g;再根据出钢和镇静时的实际温降(通常前者为40~60℃,后者约3~5℃/min,具体时间与盛钢桶大小和浇注条件有关)以及要求的过热度(一般为50~90℃)确定出钢温度T z;最后由钢水量和热容算出物理热。
Tg=1536-(0.10×65+0.18×5+0.020×30+0.021×25) -6=1520℃(式中:0.08、0.21、0.019和0.016分别为终点钢水C、Mn、P和S的含量)Tz=1520+50+50+70=1690℃(式中,50、50和70分别为出钢过程中的温降、镇静及炉后处理过程中的温降和过热度)Qg=91.725×[0.699×(1520-25)+272+0.837×(1690-1520)]=133853.834KJ(2)炉渣物理热Q r:令终渣温度与钢水温度相同,则得:Qr=8.184×[1.248×(1690-25)+209]=18716.153KJ(3)炉气、烟尘、铁珠和喷溅金属的物理热Q x。