铝镁合金设计要点
运载装备轻量化用铝、镁合金高效设计制造关键技术与产业化应用

运载装备轻量化用铝、镁合金高效设计制造关键技术与产业化应用1.引言概述部分的内容可以写成以下样式:1.1 概述近年来,随着工业技术的不断发展和运输需求的不断增加,轻量化设计制造成为了装备制造行业的热点话题。
轻量化装备能够有效减轻运载装备的重量,提高装备的性能和效率,同时降低能源消耗,减少环境污染,因此备受各个行业的青睐。
在轻量化设计制造中,铝合金和镁合金作为重要的材料成为了研究的重点。
铝合金具有优异的力学性能和良好的加工性能,而镁合金则具有较低的密度和较高的强度。
因此,研究和发展铝、镁合金的高效设计制造关键技术对于实现装备的轻量化具有重要的意义。
本文旨在系统总结铝、镁合金在运载装备轻量化设计制造中的关键技术,并探讨其产业化应用情况,以期为相关领域的研究提供参考。
在接下来的章节中,我们将分别介绍铝合金轻量化设计制造技术和镁合金轻量化设计制造技术的研究进展和应用情况,并对其发展趋势进行展望。
通过本文的阅读,读者可以了解到铝、镁合金在轻量化设计制造领域的应用前景和挑战,并为相关产业的发展提供技术支持和指导,推动装备制造行业向着更加高效、环保的方向发展。
文章结构部分主要介绍文章的整体框架和组织结构,下面是1.2文章结构部分的一个示例内容:1.2 文章结构本文将按照以下结构进行组织和呈现:第一部分为引言,主要对本文的主题进行概述,介绍运载装备轻量化用铝、镁合金高效设计制造关键技术与产业化应用的背景和意义。
此外,我们还会介绍本文的目的和论述方法。
第二部分为正文,主要分为两个章节,分别介绍铝合金轻量化设计制造技术和镁合金轻量化设计制造技术。
对于每种合金材料,我们将详细探讨其在运载装备轻量化方面的关键技术,包括材料性能特点、设计原则、制造工艺等。
同时,我们还将介绍相关技术的研究现状和进展,并提供一些具体的案例分析以便读者更好地理解和应用这些技术。
第三部分为结论,主要对本文进行总结,并展望运载装备轻量化用铝、镁合金高效设计制造关键技术与产业化应用的发展前景。
镁铝合金外观件之设计规范
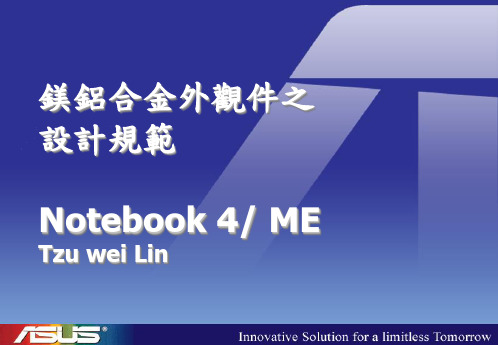
外觀
鎂鋁合金在噴漆,外觀修補痕跡,缺陷 等方面,均不同於一般塑膠及鈑金件, 宜另定新的外觀檢驗標準。
ห้องสมุดไป่ตู้
材料 1/2
一般使用的材料為AZ-91D,其成份及特性如下:
Magniesium Aluminum Zinc Manganese Iron Silicon Copper Nickel 90% 8.3~9.7% 0.35~1.0 % 0.15~0.5 % 0.005 % 0.10 % max 0.03 % max 0.002 % max
文字圖案: 成品文字圖案凹陷較不可行(除非線條寬度很大),以击起為可行 ,線條寬度b,線條高度h。 b≧0.5 mm h≦0.3 mm 但對表面烤漆件,為避免外觀不良無法處理,以印刷為宜。 考量模具壽命,不要設計公模斜梢之undercut,若無法避免,必須 以機械加工處理。 外滑塊可行,但拆模須延伸至Parting Line(隧道式滑塊不可行 )。 Rib 根部以R角與基材連接,可幫助充填及避免應力集中現象,一 般以R0.5~R2 為佳。Rib 寬度最小值小件如手機和PDA 應在0.6 mm 以上,大件如投影機和Notebook 應在0.8 mm以上,防止充填成形 不良。
Lead time
鎂鋁合金生產不同於一般流程,一般而 言,而壓鑄成品,設計階段約10~14 天(加工治具Ready 的狀況下),量產則 需2~3 週,必須對庫存做良好的控制, EC 亦需慎重。
修模
鎂鋁合金模具硬度較高,經焊補修模後 ,大大降低模具壽命(一般約10 萬模), 設計變更應儘量減少焊補部份。
5~10% 10~15% 10~20% 15~20% 10% 30~40%
鎂鋁合金件在開發過程的重點
設計 / 試模階段:
镁合金压铸产品设计要点

镁合金压铸产品设计要求1、尺寸公差要求
4、散热齿高度、厚度及拔模斜度等要求
此项指标与铝合金相比,同等尺寸下,高度可以稍高一点、厚度薄一些、拔模斜度稍小一点可行,若按原铝合金设计生产镁没有问题。
5、凸台/凹槽要求
这些没有特殊要求,主要根据产品结构而定,按铝合金设计可以再优化一点。
6、后面机加需留的余量
加工余量根据产品结构和精度要求而定,一般留0.5mm左右即可。
7、其他与铝合金压铸产品不同,设计上需要注意的地方
从制造工艺上来讲,铝合金生产时需用水来冷却,镁合金需加热,贵司产品结构设计考虑功能要求,有点问题我们可以从工艺上进行改良。
铝型材设计要点
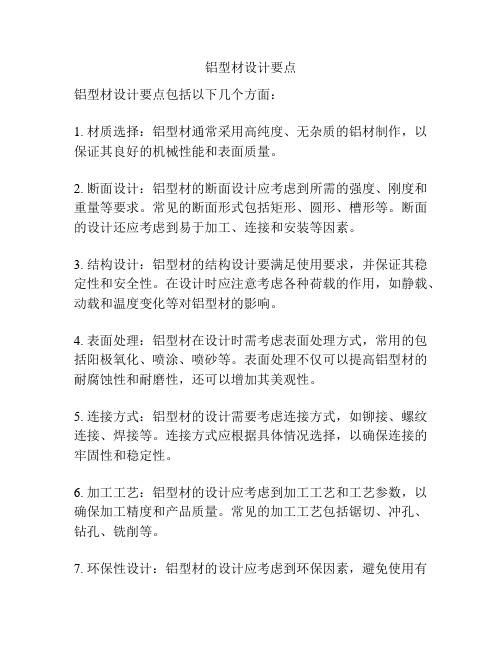
铝型材设计要点
铝型材设计要点包括以下几个方面:
1. 材质选择:铝型材通常采用高纯度、无杂质的铝材制作,以保证其良好的机械性能和表面质量。
2. 断面设计:铝型材的断面设计应考虑到所需的强度、刚度和重量等要求。
常见的断面形式包括矩形、圆形、槽形等。
断面的设计还应考虑到易于加工、连接和安装等因素。
3. 结构设计:铝型材的结构设计要满足使用要求,并保证其稳定性和安全性。
在设计时应注意考虑各种荷载的作用,如静载、动载和温度变化等对铝型材的影响。
4. 表面处理:铝型材在设计时需考虑表面处理方式,常用的包括阳极氧化、喷涂、喷砂等。
表面处理不仅可以提高铝型材的耐腐蚀性和耐磨性,还可以增加其美观性。
5. 连接方式:铝型材的设计需要考虑连接方式,如铆接、螺纹连接、焊接等。
连接方式应根据具体情况选择,以确保连接的牢固性和稳定性。
6. 加工工艺:铝型材的设计应考虑到加工工艺和工艺参数,以确保加工精度和产品质量。
常见的加工工艺包括锯切、冲孔、钻孔、铣削等。
7. 环保性设计:铝型材的设计应考虑到环保因素,避免使用有
害物质,如铅、汞等。
同时,设计还应考虑到铝型材的可回收性和可再利用性。
以上是铝型材设计的一些要点,设计过程中还需结合具体应用环境和要求进行综合考虑。
铝镁合金材料的特性分析及加工工艺研究

铝镁合金材料的特性分析及加工工艺研究铝镁合金是一种广泛应用于制造航空、汽车、电子和建筑等领域的高性能金属材料。
在铝镁合金中,铝是基体,镁是强化相,两者的共同作用使其拥有优异的机械性能、导电性能和抗腐蚀性能,并具有重量轻、强度高的优点。
本文将从铝镁合金材料的特性和加工工艺两方面进行探讨。
一、铝镁合金的特性1、机械性能铝镁合金的强度比普通铝合金高出很多,弹性模量也比较高。
这使得它可以满足在高温、高压等恶劣环境下所需的机械性能要求。
同时,它的韧性也比较好,不易出现脆性断裂。
2、导电性能铝镁合金具有很好的导电性能,可以广泛应用于电子工业。
在电子元器件的制造中,铝镁合金作为电路板的基底材料,能够有效提高电路板的导热性能和机械性能,从而提高整个电子设备的工作稳定性。
3、抗腐蚀性能铝镁合金的抗腐蚀性能也非常出色。
随着氧化膜的形成,其表面会形成一层坚固的氧化膜,具有很好的防腐蚀性能,可以在某些恶劣环境下长期使用。
4、重量轻相比于普通的钢材,铝镁合金的密度更小,重量更轻。
这使得使用铝镁合金可以有效降低产品的自重,节约能源,从而实现制造轻量化工业。
二、铝镁合金的加工工艺1、挤压加工挤压是铝镁合金加工中比较常用的一种工艺。
它可以有效地制造出长条状或复杂形状的产品。
在挤压过程中,铝镁合金经过高温加热,然后通过模具挤出成型。
挤压可以实现批量生产,并且生产的产品质量稳定,表面光滑,尺寸精度高。
2、铸造加工铸造是另一种常用的铝镁合金加工工艺。
它可以通过铸造模具,将铝镁合金熔融后倾入模具内进行凝固形成。
铸造加工具有生产效率高、成本低、适用于大件生产等特点,是制造大型零件或精密零件时常用的工艺。
3、冷变形加工冷变形加工是通过对铝镁合金进行冷加工,从而改善材料性能。
常见的冷变形加工工艺包括冷轧、冷拔和冷挤压。
由于冷变形加工可以改善铝镁合金的力学性能、表面结构和织构特性,因此在某些场合下,这可以是最好的选择。
以上几种铝镁合金加工工艺虽然各有优缺点,但在实际应用中,却是互相补充。
设计铝合金与镁合金铸件结构应注意的八个基本事项
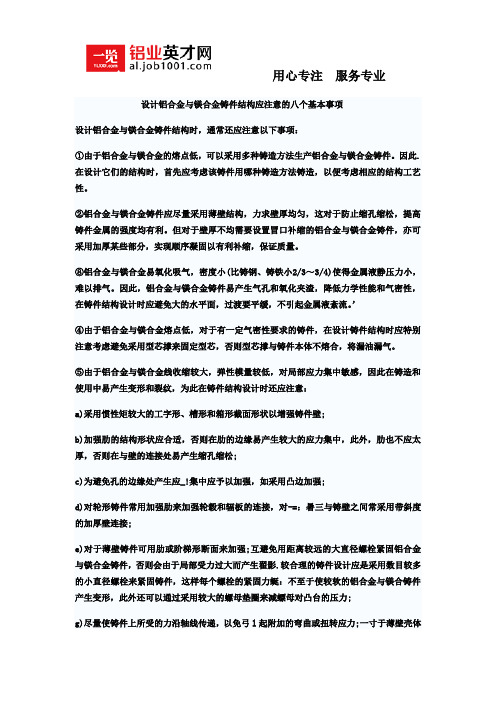
设计铝合金与镁合金铸件结构应注意的八个基本事项设计铝合金与镁合金铸件结构时,通常还应注意以下事项:①由于铝合金与镁合金的熔点低,可以采用多种铸造方法生产铝合金与镁合金铸件。
因此.在设计它们的结构时,首先应考虑该铸件用哪种铸造方法铸造,以便考虑相应的结构工艺性。
②铝合金与镁合金铸件应尽量采用薄壁结构,力求壁厚均匀,这对于防止缩孔缩松,提高铸件金属的强度均有利。
但对于壁厚不均需要设置冒口补缩的铝合金与镁合金铸件,亦可采用加厚某些部分,实现顺序凝固以有利补缩,保证质量。
⑧铝合金与镁合金易氧化吸气,密度小(比铸钢、铸铁小2/3~3/4)使得金属液静压力小,难以排气。
因此,铝合金与镁合金铸件易产生气孔和氧化夹渣,降低力学性能和气密性,在铸件结构设计时应避免大的水平面,过渡要平缓,不引起金属液紊流。
’④由于铝合金与镁合金熔点低,对于有一定气密性要求的铸件,在设计铸件结构时应特别注意考虑避免采用型芯撑来固定型芯,否则型芯撑与铸件本体不熔合,将漏油漏气。
⑤由于铝合金与镁合金线收缩较大,弹性模量较低,对局部应力集中敏感,因此在铸造和使用中易产生变形和裂纹,为此在铸件结构设计时还应注意:a)采用惯性矩较大的工字形、槽形和箱形截面形状以增强铸件壁;b)加强肋的结构形状应合适,否则在肋的边缘易产生较大的应力集中,此外,肋也不应太厚,否则在与壁的连接处易产生缩孔缩松;c)为避免孔的边缘处产生应_!集中应予以加强,如采用凸边加强;d)对轮形铸件常用加强肋来加强轮毂和辐板的连接,对-=:暑三与铸壁之间常采用带斜度的加厚壁连接;e)对于薄壁铸件可用肋或阶梯形断面来加强;互避免用距离较远的大直径螺栓紧固铝合金与镁合金铸件,否则会由于局部受力过大而产生翟影.较合理的铸件设计应是采用数目较多的小直径螺栓来紧固铸件,这样每个螺栓的紧固力蜒:不至于使较软的铝合金与镁合铸件产生变形,此外还可以通过采用较大的螺母垫圈来减螵母对凸台的压力;g)尽量使铸件上所受的力沿轴线传递,以免弓l起附加的弯曲或扭转应力;一寸于薄壁壳体形的铝合金与镁合金铸件,不应具有突变的外形;i)由于铝合金与镁合金的弹r^竺囔量小易变形,因此对于有压配合关系的铝合金与镁合金铸件,在设计铸件结构时必须考虑,至j变形和多次拆装后产生的间隙,同理,铝合金与镁合金铸件上的螺纹孔应比铸铁件和铸钢件孵嗓纹孔适当加长,对于铝合金铸件取L(长度)脑(直径)一2,对于镁合金铸件取L/d:2.5。
铝镁合金管型母线结构

铝镁合金管型母线结构一、引言铝镁合金管型母线是一种电力传输和分配装置,广泛应用于电力系统中。
它由铝镁合金管和连接件组成,具有轻质、高强度、导电性好等特点,适用于高压、大电流的输电和配电场合。
本文将从材料特性、结构设计、应用领域等方面介绍铝镁合金管型母线的相关知识。
二、材料特性1. 铝镁合金管铝镁合金是一种由铝和镁组成的合金材料。
铝具有良好的导电性和导热性,而镁具有较低的密度和良好的机械性能。
铝镁合金管采用该材料制成,具有轻质、高强度、耐腐蚀等特点,适用于长距离输电和分配电流较大的场合。
2. 连接件连接件是将铝镁合金管连接成母线系统的重要组成部分。
常见的连接件有接头、接箍、接线夹等。
这些连接件采用高强度的材料制成,能够确保母线系统的稳定性和可靠性。
三、结构设计1. 母线管铝镁合金管型母线采用管状结构,能够有效降低电阻损耗和热损耗。
母线管的截面形状可以根据实际需求进行设计,常见的有圆形、方形和矩形等。
不同形状的母线管适用于不同的场合,可以满足不同的电流传输需求。
2. 连接方式铝镁合金管型母线的连接方式多样,常见的有焊接、螺栓连接和插接等。
这些连接方式具有连接牢固、电阻低、可靠性高等优点。
根据实际情况选择合适的连接方式,能够确保母线系统的稳定运行。
四、应用领域铝镁合金管型母线广泛应用于电力系统中的输电和配电场合。
具体应用领域包括:1. 高压输电线路铝镁合金管型母线适用于高压输电线路,能够承受较大的电流负荷,减少输电损耗,提高能源利用效率。
2. 变电站铝镁合金管型母线用于变电站的电流传输和分配,能够满足变电站对高强度、大电流的要求,确保电力系统的安全稳定运行。
3. 工业用电铝镁合金管型母线广泛应用于工业领域的电力供应系统,能够满足工业设备对大电流供电的需求,提高工业生产效率。
4. 建筑电力铝镁合金管型母线用于建筑领域的电力供应,能够满足建筑物对电力的稳定供应需求,确保建筑物内部各项设备的正常运行。
五、总结铝镁合金管型母线作为一种重要的电力传输和分配装置,具有轻质、高强度、导电性好等特点,广泛应用于电力系统中。
铝镁合金设计要点

镁压铸品尺寸公差 (2/9)
分模面公差: (ADCI-E2-65)(表3)
镁压铸品投影面积 320cm2以下 320cm2 ~650cm2 650cm2~1300cm2 1300cm2~2000cm2 公差量 (mm) ± 0.13 ± 0.20 ± 0.30 ± 0.40
浇,流道系统设计(8/10)
浇口与铸件接合之方式
端部充填:使熔汤容易往上充填,适用於深槽压铸件 使熔汤容易往上充填,
浇,流道系统设计(9/10)
浇口与铸件接合之方式
对合充填:适用於圆筒形压铸件
浇,流道系统设计(10/10)
浇口与铸件接合之方式
垫形充填:适用於平板压铸件及整缘容易要求铸件
模具分割面设定要因 (1/7)
圆角
当T1=最小壁厚时
当T型相交时,则R1=1~1.25 T1 型相交时, 当T2 > T1时,则R1=2/3( T1+T2) & R2=0~(R1+T2) 当十字或Y型相接时
当Θ=90°时,则 R1= T1 当Θ=45°时,则 R1= 0.7 T1 & R2= 1.5 T1 当Θ=30°时,则 R1= 0.5 T1 & R2= 2.5 T1
镁合金压铸件成品设计要点 (4/4)
拔模角(依ADAC建议)
一般拔模角 D = L / C ,θ = ( D / L ) / 0.01746 度 精级拔模角 D = 0.8( L / C ) , θ = (D / L) / 0.01746度
一般级拔模角所需C值 一般级拔模角所需 值 内表面(单边 单边)=7 内表面 单边 外表面(单边 单边)=14 外表面 单边 全部)=4.76 孔(全部 全部 精级拔模角所需C值 精级拔模角所需 值 内表面(单边 单边)=7.8 内表面 单边 外表面(单边 单边)=15.6 外表面 单边 全部)=5.3 孔(全部 全部
- 1、下载文档前请自行甄别文档内容的完整性,平台不提供额外的编辑、内容补充、找答案等附加服务。
- 2、"仅部分预览"的文档,不可在线预览部分如存在完整性等问题,可反馈申请退款(可完整预览的文档不适用该条件!)。
- 3、如文档侵犯您的权益,请联系客服反馈,我们会尽快为您处理(人工客服工作时间:9:00-18:30)。
熱室壓鑄機構造
在此比例下應不會產生縮水痕,但非必
⇨拔模角(依ADAC 建議)
⇨一般拔模角, 度精級拔模角, C L D /=01746.0/)/(L D =θ)/(8.0C L D =01746.0/)/(L D =θ
●
扇形澆口系統設計
⇨扇形澆口系統適用於澆口長度受限的鑄件⇨扇形澆口其特性中央速度高,兩端速度較小
⇨扇形澆口兩端夾角應小於90°,如開的太大兩側並無熔湯射出
⇨扇形澆口其特性就是由較窄的流道轉變到較寬的澆口⇨扇形澆口截面積由進口到出口其截面的寬與深建議比例如下:
▪流道面積:澆口面積= 1.5: 1▪流道厚度:澆口厚度= 3: 1▪扇形長度:澆口寬度= 1.34: 1
澆、流道系統設計(4/10)
錐形流道藉控制流動角的大小,便可控制充填模式
端部充填:使熔湯容易往上充填,適用於深槽壓鑄件對合充填:適用於圓筒形壓鑄件墊形充填:適用於平板壓鑄件及整緣容易要求鑄件
動模,而使壓鑄件開模時附著於可動模。
及排氣溝順利排出使熔液的流動性較佳。
B部份仍會發生龜裂及熔損等現象。
表3)
之公差,追加垂直於分模面
4)
之公差追加於表4之公差
450cm2, A為20mm則
其公差值應為±0.10,活動
⇨超過75mm每25mm追加公差……………0.04mm ⇨超過75mm每25mm追加公差……………0.075mm。