双酚A型环氧树脂的合成及复合材料制备(精)
双酚A型环氧树脂胶粘剂的合成及配制

双酚A型环氧树脂胶粘剂的合成及配制摘要以苯酚与丙酮为原料,以硫酸为催化剂,在助催化剂甲苯的作用下合成了2,2 -二羟苯基丙烷,即双酚A。
研究了硫酸的滴加速度、助催化剂甲苯的用量、反应温度、反应时间对双酚 A 收率的影响,并得出最佳的反应条件为:硫酸约每min 13 滴,甲苯与苯酚质量比为1∶4,反应时间为 2 h,反应温度为35℃。
收率为22.78%。
双酚 A 的熔点为154 ~158℃。
通过对所得产品的红外光谱与双酚 A 的标准红外光谱对比,可以基本证明所合成的产物就是双酚A。
利用所合成的双酚 A 与环氧氯丙烷反应,采用一步法合成路线,制备了双酚 A 型环氧树脂,合成过程中对双酚 A 与环氧氯丙烷的配比、碱的用量和反应温度等因素对其环氧值的影响进行了分析讨论。
所制备的环氧树脂的环氧值为0.475,配制的胶粘剂的室温固化时间为 3 h。
在外力作用下,两铝片粘结的固化时间为2.0 h,无外力作用时,两铝片粘结的固化时间为2. 5 h。
对玻璃与铜电极进行粘结的室温固化时间为3. 5 h,玻璃与铝电极粘结的固化时间为3. 5 h。
关键词双酚 A 环氧树脂胶粘剂环氧树脂胶粘剂又称环氧胶粘剂,简称环氧胶。
自20 世纪50 年代开始应用以来,发展迅速,已经众所周知,几乎无所不粘,一直受宠不衰,是性能较为全面、应用相对广泛的一类胶粘剂,素有“万能胶”和“大力胶”之美称。
在合成胶粘剂中环氧胶粘剂具有粘结力大、粘结强度高、固化收缩小、电性能优良、尺寸稳定好、抗蠕变性能强、耐化学介质、毒害性很低,无环境污染等优点。
对金属、木材、塑料、玻璃、陶瓷、复合材料、混凝土、橡胶、织物等多种材料都具有良好的粘结能力。
除了粘结性能之外,还有密封、堵漏、绝缘、防松、防腐粘涂、耐磨、导电、导磁、导热、固定、加固修补、装饰等作用。
因此在航空、机械、石油、轻工、水力、化工、冶金、农机、铁路、医疗器械、工艺美术、文物修复、文体用品、日常生活等诸多领域都得到了极为广泛和非常成功的应用[1]。
双酚a型环氧树脂的实验报告

双酚a型环氧树脂的实验报告双酚A型环氧树脂的实验报告一、引言双酚A型环氧树脂是一种重要的合成材料,在工业生产和科学研究中得到广泛应用。
本实验旨在通过合成双酚A型环氧树脂,并对其性质进行研究和分析,以期了解其在实际应用中的潜力和限制。
二、实验方法1. 材料准备:采购双酚A、环氧氯丙烷、氢氧化钠等试剂,并配备所需的实验器材。
2. 合成双酚A型环氧树脂:按照一定比例将双酚A和环氧氯丙烷加入反应容器中,加入适量的催化剂,并在恒温条件下进行反应。
3. 产品纯化:将反应产物进行过滤、洗涤和干燥处理,以获得纯净的双酚A型环氧树脂样品。
4. 性质测试:对合成的双酚A型环氧树脂样品进行物理性质测试,包括熔点、溶解性、硬度等。
三、实验结果与讨论1. 合成双酚A型环氧树脂的过程相对简单,反应时间较短,且产率较高。
这使得该树脂在工业生产中具有较高的经济性。
2. 双酚A型环氧树脂具有优异的物理性质,如高熔点、优良的溶解性和较高的硬度。
这些特性使得该树脂在涂料、粘合剂和复合材料等领域得到广泛应用。
3. 双酚A型环氧树脂的耐热性能较好,能够在高温环境下保持稳定。
这使得该树脂在航空航天等高温工艺中有着重要的应用前景。
4. 然而,双酚A型环氧树脂也存在一些问题。
首先,由于其合成过程中使用的某些试剂可能对环境造成污染,因此在工业生产中需要采取相应的环保措施。
其次,该树脂在长期使用过程中可能会出现老化、劣化等问题,这需要在实际应用中进行更多的研究和改进。
四、结论通过本次实验,我们成功合成了双酚A型环氧树脂,并对其性质进行了初步的测试和分析。
双酚A型环氧树脂具有优异的物理性质和耐热性能,在工业生产和科学研究中具有广泛应用前景。
然而,该树脂也存在一些问题,需要进一步的研究和改进。
希望通过今后的努力,能够进一步挖掘双酚A型环氧树脂的潜力,为工业生产和科学研究提供更好的材料选择。
五、致谢在本次实验中,我们得到了指导老师的悉心指导和同学们的合作支持,在此表示衷心的感谢。
双酚A型环氧树脂的制备(精)

安全提示
环氧氯丙烷 发生中毒时,有眼睛刺痛、结膜炎、鼻炎、 流泪、咳嗽、疲倦、胃肠紊乱、恶心等症状。严重中 毒时,可引起麻醉症状,甚至引起肺、肝、肾的损伤。 人体吸入MLC0.00002。大鼠经口LD50为90mg/kg。 空气中最大容许浓度18mg/m3。生产设备要密闭,空 气要流通,操作人员要配戴防护用具。此外,环氧氯 丙烷有激烈的自聚趋向,不应在明火中加热,以防容 器爆烈。在用作试剂进行反应时,宜以惰性溶剂稀释, 并缓缓加入。环氧氯丙烷有中等程度燃烧危险,燃烧 后释放出氯化氢,光气和一氧化碳,危险品规程编号 为62008,属二级易燃液体。
C CH3
OH
H2C O
H H2 C C
O
CH3 C CH3
O
H2 C
H C OH
H2 C
CH3
n
O *
C CH3
O
H2 O C C CH2 H
+ (n+2)NaCl
+ (n+2)H2O
仪器和药品
三口烧瓶,冷凝管,分液漏斗,温度计(200℃),水 浴,电动搅拌器,真空蒸馏装置 双酚A(工业),环氧氯丙烷(工业),氢氧化钠,甲 苯
实验四 双酚A型环氧树脂的制备
实Байду номын сангаас目的
熟悉双酚A型环氧树脂的制备方法
实验概述
双酚A型环氧树脂由双酚A与过量的环氧氯丙烷及碱催 化聚合而成,其合成反应的机理,迄今尚未定论,一 般认为属于缩聚反应,总反应式如下:
CH3
(n+2) H2C
O
H C
CH2Cl + (n+2) NaOH + (n+1) HO
实验步骤
在装有搅拌器、温度计、分液漏斗、回流冷凝管的三 口烧瓶中,加入30克双酚A及34克环氧氯丙烷,搅拌并 加热,当温度升到50℃时开始由分液漏斗滴加 35ml30%NaOH水溶液,在50~60℃下于2小时内滴加 完毕,提高温度,于70~75℃保持1小时,得黄色粘稠 树脂,加入30ml蒸馏水,60ml甲苯,搅拌使树脂溶解, 趁热倒入分液漏斗,静止分层除去水层。 将树脂溶液倒回三颈瓶中,进行真空蒸馏,除去甲苯 及未反应的环氧氯丙烷,加热,开动真空泵(注意流 出速度),蒸馏到无流出物为止,控制蒸馏最终温度 为120℃,得到黄色透明树脂。
双酚A型环氧树脂的合成

双酚A型环氧树脂的合成环氧树脂的化学合成一、双酚A型环氧树脂的合成1.双酚A型环氧树脂的合成途径:①低分子量液态双酚A型环氧树脂由过量环氧氯丙烷(ECH)与双酚A(BA)在碱(NaOH)的存在下缩聚而成;另一个方法是由不饱和环状烃类的双键氯化而生成环氧环状物得到脂环族环氧。
②高分子量固态环氧树脂的途径:a.“太妃糖法”:双酚A与环氧氯丙烷在化学计算是碱存在下直接反应b.“熔融法”:以低分子量液态双酚A型环氧树脂为原料在催化剂存在下,用双酚A型扩展化学键得到聚合度较高(n>2000)的产物。
这种工艺得到没有副产物的高纯产品,分子量分布窄,主要是抑制副反应,减少链支化。
2.双酚A型环氧树脂的合成反应双酚A型环氧树脂由ECH和BA经醚化和闭环两步反应制得。
3.双酚A型环氧树脂合成反应过程的副反应①水解:ECH水解成甘油,环氧基水解为2—乙二醇。
②环氧氯丙烷与存在于中间体的酸性羟基反应,形成被裹胁的氯。
③环氧氯丙烷与酚羟基的反常加成(β加成)④链支化反应:双酚A型环氧树脂的链支化:⑤脱HCl反应不完全,树脂残留可水解氯。
这些反应的产生使ECH消耗增大,环氧基含量降低,可水解氯使氯总含量增高,树脂质量不纯,粘度或熔点上升。
二、氯含量的影响环氧树脂中残存的氯以三种形式出现:氯离子(Cl-),可水解氯和不可水解氯。
Cl-是残留的NaCl离子,可水解氯和不可水解氯是副反应产物。
1. 氯含量的影响①可水解氯使脂肪多胺固化环氧体系的适用期大为缩短②熔融法制备较高分子量固态环氧树脂用的液态环氧树脂原料可以水解,氯含量使原反应速度降低。
因此原料树脂中可水解氯最好在0.03 wt%(300PPm)以下。
③层压材料中广泛采用的环氧树脂/双氰胺/苄基二甲胺,常遇到凝胶时间延长且波动幅度大的问题,这是由于树脂可水解氯含量高且氯含量波动大。
④可水解氯会腐蚀集成电路板上的接线,因此要求树脂中可水解氯含量≤0.03 wt%⑤在湿热条件下,可水解氯使树脂的电性能大大下降。
实验十一(选做)低分子量双酚A型环氧树脂的制备(精)

二、实验原理
双酚A型环氧树脂是是由双酚A和环氧氯丙烷
在氢氧化钠存在下反应生成的。其反应式如下:
高 分 子 化 学 实 验
2
University of Jinan
三、实验仪器和试剂
• 仪器:四口瓶,滴液漏斗,分液漏斗,电动搅拌 器,温度计,减压蒸馏装置,恒温水浴 • 试剂:环氧氯丙烷,双酚A,氢氧化钠,苯,去 离子水
University of Jinan
选 做 实 验 实验十一 低分子量双酚A型 环氧树脂的制备
一 、实验目的
1. 通过双酚A型环氧树脂的制备,掌握一般缩聚反应的原理 2. 熟悉低分子量环氧树脂的制备方法并了解其的用途 3. 熟悉环氧值的测定方法
高 分 子 化 学 实 验
1
University of Jinan
高 分 子 化 学 实 验
University of Jinan
四、实验步骤
将22 .0g双酚A(0.1mol)和28.0 g环氧氯丙烷(0.3mol)依次加 入装有搅拌器、滴液漏斗和温度计的250 mL四颈瓶中。用水 浴加热,升温至75℃,搅拌双酚A使其完全溶解。70℃下滴 加40 mL,20%的NaOH溶液,约0.5 h滴加完毕。在75~80 ℃ 继续反应1.5~2 h,此时溶液呈乳黄色,停止加热,降温。加 入苯60 mL,搅拌,使树脂溶解后移入分液漏斗,静置后分 去水层,再用水洗数次,直到洗涤水相呈中性及无氯离子(用 pH纸及AgNO3溶液检查),分出有机层。将上层苯溶液倒入 减压蒸馏装置中,先在常压下蒸去苯,然后在减压下蒸馏以 除去所有挥发物。趁热将烧瓶中的树脂倒出,冷却后得琥珀 色透明的、粘稠的环氧树脂,称重并计算产率。
高 分 子 化 学 实 验
4
双酚A型环氧树脂的合成

双酚A型环氧树脂的合成1、合成原理双酚A型环氧树脂是由二酚基丙烷(双酚A)和环氧氯丙烷在碱性催化剂(通常用NaOH)作用下缩聚而成。
其反应历程的说法不一,尚无定论,本书不作探讨。
但是,大体上说来,在合成过程中主要的反应可能如下:(1)在碱催化下,双酚A的羟基与环氧氯丙烷的环氧基反应,生成端基为氯化羟基的化合物-开环反应。
(2)氯化羟基与NaOH反应,脱HCl再形成环氧基-闭环反应。
(3)新生成的环氧基与双酚A的羟基反应生成端羟基化合物-开环反应。
(4)端羟基化合物与环氧氯丙烷反应生成端氯化羟基化合物-开环反应。
(5)生成的氯化羟基与NaOH反应,脱HCl再生成环氧基-闭环反应。
在环氧氯丙烷过量情况下,继续不断地进行上述开环-开环-闭环反应,最终即可得到二端基为环氧基的双酚A型环氧树脂。
上述反应是缩聚过程中的主要反应。
此外还可能有一些不希望有的副反应,如环氧基的水解反映、文化反应、酚羟基与环氧基的反常加成反应等。
若能严格控制合适的反应条件(如投料配比,NaOH用量、浓度及投料方式,反应温度,加料顺序、含水量等),即可将副反应控制到最低限度。
从而能获得预定相对分子质量的、端基为环氧基的线型环氧树脂。
调节双酚A和环氧氯丙烷的用量比,可以制得平均相对分子质量不同的环氧树脂。
按照平均相对分子质量的大小可将双酚A型环氧树脂分为:液态双酚A型环氧树脂(低相对分子质量环氧树脂、软树脂)。
平均相对分子质量较低,平均聚合度n=0~1.8。
当n=0~l时,室温下为液体,如EP0144l-310(E-51),EP0l451-310(E-44),EP01551-310(E-42)等。
当n=1~1.8时为半固体,软化点<55℃,如E-3l。
固态双酚A型环氧树脂。
平均相对分子质量较高。
n=1.8~19。
当n=1.8~5时为中等相对分子质量环氧树脂。
软化点为55~95℃。
如EP0l661-310(E-20),EP01617-310(E-12)等。
双酚A型环氧树脂胶黏剂的合成及应用

双酚A型环氧树脂胶黏剂的合成及应⽤阻燃型四溴双酚A型环氧树脂胶黏剂的合成及配制⼀、实验⽬的1.培养学⽣查阅相关⽂献资料、设计实验⽅案、综合分析问题和解决问题的能⼒、独⽴操作实验能⼒以及创新意识和创新精神。
2.掌握胶黏剂⽤双酚A型环氧树脂的合成原理和合成⽅法。
3.熟悉环氧树脂胶粘剂的结构特征、固化原理、主要固化剂的品种和特性以及固化剂⽤量的理论计算⽅法。
4.熟悉和掌握环氧值的测定⽅法和⼀般环氧树脂胶黏剂的配制⽅法和使⽤条件以及实际应⽤。
5.了解环氧树脂胶粘剂的适⽤范围以及粘接的⼯艺要求。
⼆、实验原理1.主要性质和⽤途凡是含有环氧基团的⾼分⼦化合物,总称为环氧树脂。
环氧树脂品种很多,但以双酚A型环氧树脂综合性能最好,产量最⼤。
双酚A型环氧树脂占环氧树脂总量的90%,也是在环氧树脂胶黏剂中应⽤最普遍、⼯艺最成熟的⼀种环氧树脂,有通⽤环氧树脂之称。
双酚A型环氧树脂有低分⼦量、中等分⼦量和⾼分⼦量三种。
双酚A型低分⼦量环氧树脂,学名为双酚A⼆缩⽔⽢油醚,E型环氧树脂,为黄⾊或琥珀⾊⾼黏度透明液体,软化点低于50℃,相对分⼦量⼩于700,易溶于⼆甲苯、甲⼄酮等有机溶剂。
通常环氧树脂胶黏剂⼤多采⽤低分⼦量环氧树脂,⽽热熔胶采⽤⾼分⼦量环氧树脂。
环氧树脂胶黏剂可不⽤溶剂直接粘接,具有粘接强度⾼、固化收缩⼩、耐⾼温、耐腐蚀、耐⽔、电绝缘性⾼、易改性、毒性⼩和使⽤范围⼴等优点。
可粘接各种⾦属和⾮⾦属材料,⽤于层压材料,浇注电动机中的定⼦、电动机外壳和变压器。
还⼤量⽤于浇注层压模具,泡沫塑料,可⽤做绝热、吸⾳、防震和漂浮材料等。
因此,在各个领域都得到了⼴泛应⽤,有“万能胶”之称。
2.合成原理四溴双酚A型环氧树脂是由四溴双酚A(由双酚A溴化制得,它⼴泛⽤作反应型阻燃剂以制造含溴环氧树脂和含溴聚碳酸酯以及作为中间体合成其他复杂的阻燃剂,也作为添加型阻燃剂⽤于ABS、HIPS、不饱和聚酯、硬质聚氨酯泡沫塑料、胶黏剂以及涂料等)与环氧氯丙烷在氢氧化钠作⽤下⽽制得。
双酚A型环氧树脂胶粘剂的合成及配制
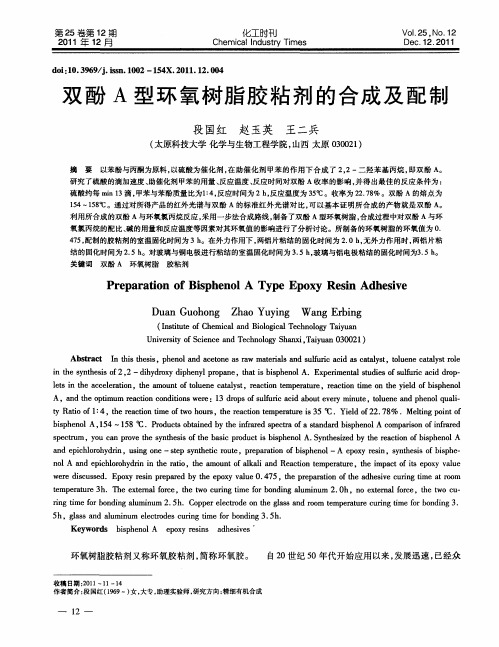
金、 农机、 铁路 、 医疗器械、 工艺美术、 文物修复 、 文体 用品、 常生活等诸多领域都得到了极为广泛和非常 日
成功 的应 用 。
将 2 双酚 A 2 环氧氯丙烷加入装有搅拌 2g ,8g 器 、 液漏 斗 、 滴 回流冷凝 管及 温度 计 的三 口烧 瓶 中 , 搅 拌并加热至 7 ℃, O 使双酚 A全部溶解 ; 称取 8g 氢氧 化钠溶解在 2 L水中, 0m 倾人 6 L滴液漏斗中, 0m 慢 慢滴加氢氧化钠溶液至三 口烧瓶 中, 保持反应液温度
关键词 双 酚 A 环氧树脂 胶粘剂
Pr p r to fBip e o Ty e Ep x sn Ad e ie e a a in o s h n lA p o y Re i h sv
Du n Gu h n Z a yn W a g E b n a o o g h o Yu i g n rig
双 酚 A型 环 氧树 脂 胶 粘 剂 的 合成 及 配 制
段 国红 赵 玉英 王二兵
( 太原科技大学 化学与生物工程学 院, 山西 太原 0 02 ) 30 1
摘 要 以苯酚与丙酮为原料 , 以硫酸为催化 剂 , 在助催 化剂 甲苯的作用 下合成 了 2 2一二 羟苯基丙 烷 , , 即双酚 A 。
馏水和6 L苯 , 0m 充分搅拌 , 倒人分液漏斗, 静止分层 后, 分去水层 ; 油层用蒸馏水洗涤数次 , 直至分出的水 相 中呈中性无氯离子 ; 先常压蒸馏 , 除去苯 ; 然后减压 蒸馏 , 除去苯 、 水及未反应 的环氧氯丙烷。得到淡黄
- 1、下载文档前请自行甄别文档内容的完整性,平台不提供额外的编辑、内容补充、找答案等附加服务。
- 2、"仅部分预览"的文档,不可在线预览部分如存在完整性等问题,可反馈申请退款(可完整预览的文档不适用该条件!)。
- 3、如文档侵犯您的权益,请联系客服反馈,我们会尽快为您处理(人工客服工作时间:9:00-18:30)。
双酚 A 型环氧树脂的合成及复合材料制备
姓名:贾训祥
学号:0840605115
专业:高分子材料与工程一、实验目的:
1. 了解逐步聚合预聚体的合成方法和环氧树脂的实验室制法。
2. 了解环氧树脂复合材料的制备方法。
3. 掌握复合材料样条的制备与其力学性能的测试过程。
二、实验原理:
环氧树脂是指那些分子中至少含有两个反应性的环氧基团的树脂化合物。
环氧树脂经固化后有许多突出的优异性能, 如对各种材料特别是对金属的粘着力很强, 有卓越的耐化学腐蚀性,力学强度很高,电绝缘性好,耐腐蚀,等等。
此外,环氧树脂可以在相当宽的温度范围内固化, 而且固化时体积收缩很小。
环氧树脂的上述优异特性使它有着许多非常重要的用途。
广泛用于粘合剂(万能胶 ,涂料、复合材料等方面。
合成环氧树脂的方法大致可分两类。
一类是用含有环氧基团的化合物(如环氧氯丙烷或经化学处理后能生成环氧基的化合物(如 1.3-二氯丙醇和二元以上的酚(醇聚合而得。
另一类是使含有双键的聚合物(如聚丁二烯或小分子(如二环戊二烯环氧化而得。
双酚 A 型环氧树脂是环氧树脂中产量最大,使用最广的一个品种,它是由双酚 A 和环氧氯丙烷在氢氧化钠存在下反应生成的:
原料配比不同,反应条件不同(如反应介质,温度和加料顺序 ,可制得不同软化点, 不同分子量的环氧树脂。
式中 n 一般在 0到 25之间。
根据相对分子质量大小,环氧树脂可以分成各种型号。
一般低相对分子质量环氧树脂的 n 平均值小于 2、软化点低于 50℃, 也称为软环氧树脂; 中等相对分子质量环氧树脂的 n 值在 2~5之间、软化点在 50℃~95℃之间; 而 n 大于 5的树脂(软化点在 100℃以上称为高分子量树脂。
相对分子质量对软化点的影响见图 1。
图 1
在环氧树脂的结构中有羟基(>CH-OH 、醚基(-O -和极为活泼的环氧基存在。
羟基、醚基有高度的极性, 使环氧分子与相邻界面产生了较强的分子间作用力, 而环氧基团则与介质表面, 特别是金属表面上的游离键起反应, 形成化学键。
因而, 环
氧树脂具有很高的粘合力,用途很广,商业上称作“万能胶” 。
此外,环氧树脂还可作涂料、层压材料、浇铸、浸渍及模具等用途。
复合材料是由两种或两种以上不同性质的材料, 通过物理或化学的方法, 在宏观上组成具有新性能的材料。
各种材料在性能上互相取长补短, 产生协同效应, 使复合材料的综合性能优于原组成材料而满足各种不同的要求。
为了增强环氧树脂的性能, 本实验在环氧树脂固化的同时加入玻璃纤维,制取复合材料,并测试其力学性能。
三、化学试剂和仪器:
四口烧瓶,回流冷凝管,分液漏斗,滴液漏斗,玻璃棒,烧杯,温度计(200℃ , 刷子,电热套,电动搅拌器,真空蒸馏装置,制样机,万能电子力学试验机。
双酚 A , 环氧氯丙烷,氢氧化钠,甲苯,丙酮,三乙烯四胺。
四、实验步骤:
1. 环氧树脂的制备:搭接好反应装置。
将 30g 双酚 A 和 34g 环氧氯丙烷依次加入四口烧瓶中,打开搅拌器升温至 70~75 o C ,使双酚 A 全部溶解。
待其完全溶解之后缓慢滴加 78g(氢氧化钠质量分数为 16%氢氧化钠溶液,注意温度保持在 70度左右。
滴加完毕之后, 在 75到 80度之间继续反应 2小时左右, 可观察到反应混合物呈乳黄色。
停止加热, 冷却至室温,向反应瓶中加入 30mL 蒸馏水和 60mL 苯,充分搅拌后,倒入 250mL 的分液漏斗中, 静置,分去水层,油层用蒸馏水洗涤数次,取油层。
将树脂溶液进行真空蒸馏,除去甲苯及未反应的环氧氯丙烷,加热,开动真空泵(注意流出速度 ,蒸馏到无流出物为止,控制蒸馏最终温度为 120℃,得到黄色透明树脂。
2. 复合材料制备:以玻璃纤维布为增强材料,三乙烯四胺为固化剂,制备环氧树脂复合材料, 并测试其力学性能。
具体步骤是将经过真空蒸馏后所得到的树脂置于烧杯中, 加入 12%的固化剂,搅拌均匀。
①在桌面铺一层保鲜膜,将已经准备好的玻璃
纤维(长 25厘米, 宽 15厘米铺在其上,再用刷子将树脂均匀涂于玻璃纤维的两面。
②涂完后,再取一片玻璃纤维覆盖其上,压实。
再用刷子将树脂均匀涂在玻璃纤维上。
,
此次只涂朝上的一面。
重复②的步骤一次。
这样便做好一份,连续做三份。
将做好的放入烘箱内,在 90度的温度下保温一个半小时。
取出, 用制样机将其制成样品。
对于要做拉伸测试的样品, 在其每个样条的两边在涂上三层的玻璃纤维并将其放入烘箱, 在 90度的温度下保温一个小时。
取出即可。
3. 复合材料力学性能的测试:利用型号为 CM4303的万能电子力学试验机进行复合材料的弯曲与拉伸性能的测定。
①、弯曲性能的测定:选择好试验的方式,设定试验参数,将其下降速度设为
2mm 每分钟,试样跨度设为 20mm 。
将条形样品装入万能电子力学试验机,固定好。
连接好各种传感器。
将显示屏上的数据清零。
点击开始试验,直至样品断裂,停止试验。
重复上述过程, 将全部的样品测试完,生成报告。
②、拉伸性能的测定:选择好试验的方式,设定试验参数,将其上升速度设为
2mm 每分钟, 将哑铃型样品装入万能电子力学试验机, 固定好。
连接好各种传感器。
将显示屏上的数据清零。
点击开始试验, 直至样品断裂, 停止试验。
重复上述过程, 将全部的样品测试完, 生成报告。
五、讨论:
1. 合成:在实验中,再加料时,应该要先加环氧氯丙烷,再加入双酚 A 。
这样可以加快双
酚 A 的溶解。
如果反过来,就可能要发比较多的时间等待其溶解。
在二者完全溶解之后, 滴加氢氧化钠溶液是要注意速度, 过快将是反应加快, 放出大量的热, 是反应的环境温度迅速上升, 这导致冷凝液上层水相中的环氧氯丙烷含量会增多, 随水分离而损失, 致使参加反应的环氧氯丙烷减少, 物料比例发生变化, 产物也将发生变化。
本实验的环氧树脂合成产率比较低, 主要原因是原料的投入比较少, 生成的产物由于具有一定的粘度使得在萃取和真空抽滤过程来回转移中使产物有部分损失,这些致使产率降低。
2. 力学性能 :
(1弯曲性能测试:
表一
理可知:平均弯曲模量 Ef :3131.082Mpa ;平均弯曲强度σfM :214.123Mpa ;平均规定挠度时的弯曲应力σfc :157.229Mpa ;平均断裂弯曲应力σfB :157.229Mpa 。
图 2
复合材料的弯曲性能讨论:复合材料的断裂面并不平整, 有好几个都是藕断丝连。
这实验过程中可以了解到样品的厚度与宽度都是影响复合材料弯曲性能的重要因素。
不过造成材料性能差异的主要是在铺层的时候没有铺均匀, 在制备样品是裁剪的线条与玻璃纤维的纹路相交错程度也会很大地影响到材料的性能。
不过由图 2可以看出, 在这些因素的影响下, 虽然应力的大小有变化,但是对于应变来说,材料的断裂弯曲应力所对的应变的变化并不是很大。
在实验中也可以看出,在其他条件相同的情况下,多铺一层树脂可以增加复合材料的韧性, 和硬度,提升材料的力学性能。
复合材料拉伸性能测试:
图 3
厚度:1.88mm ; 宽度:24.82mm 。
拉伸强度:114.57Mpa ;最大承受的力
为:5325.18N ; 最大拉伸位移:3.93mm 。
最大应变:7.85%。
复合材料拉伸性能讨论:在拉伸实验中, 所得到的应力——应变曲线是一条接近直线的曲线, 如图 3。
而且在拉伸条件下,纤维聚合物复合材料的泊松比并非不变值,而是随着载荷的增加而减小, 有时会出现负的泊松比。
其主要原因是泊松比的符号取决于增强纤维的铺设方向和顺序, 反映在边缘效应上。
因此, 对增强纤维的横向相对应变进行测量时困难。
在试验中可以看出, 纤维含量低的材料, 聚合物基体在增强纤维断裂之前破坏; 二维纤维复合材料上的载荷与纤维方向有夹角时,破坏随角度而变化:1、小角度时,由于剪切以及平行于增强纤维方向的聚合物基体剥离,而是材料开始破坏; 2、角度加大时,由于拉应力起着主要作用,极端情况下,因聚合物基体横向断裂而破坏。