轴套零件工艺分析
毕业设计轴套--轴套零件的工艺分析
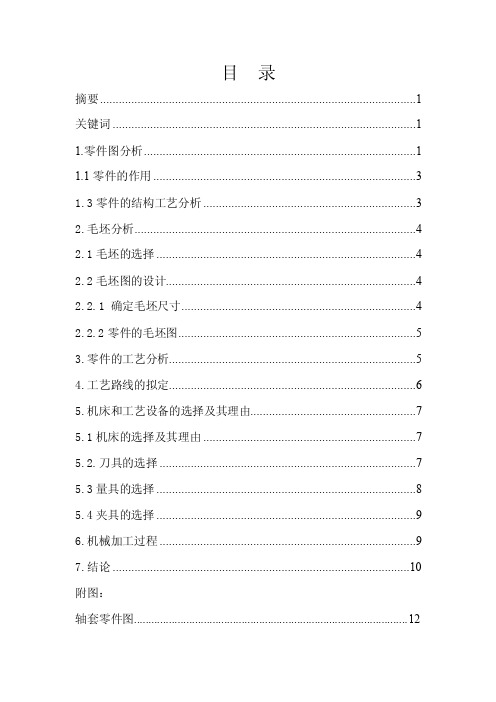
目录摘要 (1)关键词 (1)1.零件图分析 (1)1.1零件的作用 (3)1.3零件的结构工艺分析 (3)2.毛坯分析 (4)2.1毛坯的选择 (4)2.2毛坯图的设计 (4)2.2.1 确定毛坯尺寸 (4)2.2.2零件的毛坯图 (5)3.零件的工艺分析 (5)4.工艺路线的拟定 (6)5.机床和工艺设备的选择及其理由 (7)5.1机床的选择及其理由 (7)5.2.刀具的选择 (7)5.3量具的选择 (8)5.4夹具的选择 (9)6.机械加工过程 (9)7.结论 (10)附图:轴套零件图 (12)轴套毛坯图 (13)机械加工工艺过程卡1 (14)机械加工工艺过程卡2 (15)机械加工工序卡2 (16)机械加工工序卡3 (17)机械加工工序卡4 (18)机械加工工序卡5 (19)机械加工工序卡6 (20)机械加工工序卡7 (21)机械加工工序卡8 (22)机械加工工序卡9 (23)机械加工工序卡10 (24)机械加工工序卡11 (25)机械加工工序卡12 (26)机械加工工序卡13 (27)机械加工工序卡14 (28)机械加工工序卡15 (29)参考文献 (30)轴套零件的工艺分析摘要:轴套零件在机械中的作用主要是导正、限位、止转及定位作用。
本次毕业设计通过对轴套零件图的分析,确定了该零件的毛坯材料及尺寸规格,通过对零件的加工工艺分析,确定了该零件的加工工艺路线,编写了机械加工工艺过程卡片和工序卡片。
零件在加工中必须保证重要的尺寸精度和表面粗糙度,以及根据现有生产设备选择合理的机械加工路线。
关键词:轴套尺寸设备精度1.零件图分析轴套一般起滑动轴承作用,是在机械传动过程中起固定和减小载荷摩擦系数的部件。
图1轴套零件图该零件(图1)为轴套类零件。
表面由外圆柱面、轴肩退刀槽表面组成,其中2.0132±φmm ,60030.00φ+mm, 950022.0φ-mm 这三个直径尺寸有较高的尺寸精度和表面粗糙度要求,表面粗糙度要求为0.8,为了保证同轴度通常减小切削力和切削热的影响,粗精加工分开,使粗加工中的变形在精加工中得到纠正,要求尺寸较高为60030.00φ+mm 、950022.0φ-mm 、2.0132±φmm ,其表面粗糙度为Ra1.6µm、Ra0.8µm 零件的左端和有端有M6螺纹孔,深8mm 。
轴套零件的数控工艺分析与编程

轴套零件的数控工艺分析与编程轴套是一种常见的机械零件,广泛应用于各种机械设备中。
数控工艺分析与编程是指通过数控编程的方式对轴套的加工工艺进行分析,并编写相应的数控程序,以实现对轴套的高效、精确加工。
下面将详细介绍轴套零件的数控工艺分析与编程过程。
一、数控工艺分析数控工艺分析是指分析轴套零件的加工特点和要求,并确定相应的加工工艺路线和具体的加工参数。
具体分析如下:1.轴套的加工特点和要求:轴套通常由高强度的金属材料制成,具有高精度、高强度和耐磨损的特点。
在进行数控加工时,需要注意减小误差、提高加工精度和表面质量。
2.加工工艺路线:根据轴套的结构、尺寸和加工要求,确定加工工艺路线。
一般来说,轴套的加工工艺路线包括粗加工、精加工和表面处理等步骤。
-粗加工:主要包括车削、铣削、钻削等工艺,用于将原材料加工成近似形状的轴套毛坯。
-精加工:主要包括车削、钻削、拉削等工艺,用于将毛坯进一步加工成精确形状和尺寸的轴套。
-表面处理:主要包括抛光、热处理等工艺,用于提高轴套的表面质量和硬度。
3.加工参数确定:根据轴套的材料和加工要求,确定各工艺步骤对应的切削速度、进给速度、切削深度和切削用液等加工参数。
二、数控编程数控编程是指根据数控设备的编程语言和指令集,编写相应的数控程序,实现对轴套的自动化加工。
具体编程步骤如下:1.绘制零件图纸:根据轴套的几何形状和尺寸要求,绘制轴套的详细图纸。
图纸应包括轴套的三维模型、尺寸和加工要求等信息。
2.分析加工特点:根据轴套的加工特点和要求,对加工工艺进行分析,并确定加工工艺路线和加工参数。
3.编写数控程序:根据加工工艺路线和加工参数,编写数控程序。
数控程序是指通过一系列的数控指令,控制数控机床进行轴套的加工。
4.调试和优化:将编写好的数控程序输入数控机床,并进行调试和优化,确保加工过程的准确性和稳定性。
5.加工监控和质量检验:在整个加工过程中,需要进行对加工状态的监控和质量检验,确保轴套的加工质量符合要求。
轴套类零件加工工艺分析
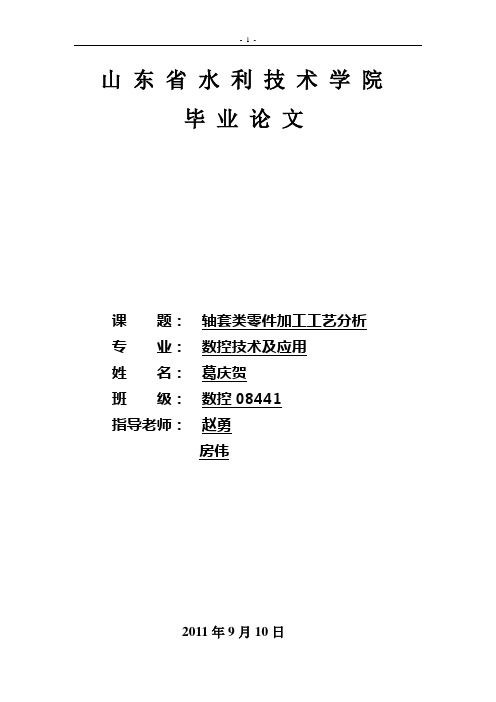
山东省水利技术学院毕业论文课题:轴套类零件加工工艺分析专业:数控技术及应用姓名:葛庆贺班级:数控08441指导老师:赵勇房伟2011年9月10日目录前言 (3)第一章零件结构及毛坯分析 (6)1.1零件结构及毛坯分析 (6)1.2材料分析 (6)1.3毛坯分析 (6)第二章零件结构工艺 (8)第三章选择加工设备与刀、夹具 (10)3.1 机床的选择 (10)3.2 刀具的选择 (11)3.3 夹具的选择 (12)第四章加工工艺分析 (14)4.1 夹紧方式 (14)4.2 定位基准的选择 (14)4.3 加工顺序的安排 (15)4.4 切削用量的确定及功率的校核 (16)4.5 切削液的选择 (18)第五章数控加工刀具卡 (20)第六章数控加工工序卡 (23)第七章程序的编制 (26)第八章加工步骤 (29)参考文献 (31)前言毕业设计是我们结束大学学习生活走向社会的一个中介和桥梁。
毕业设计是我们大学生才华的第一次显露,是向祖国和人民所交的一份有分量的答卷,是投身社会主义现代化建设事业的报道书。
撰写毕业设计是我们在校最后一次知识的全面检验,是对基本知识,基本理论和基本技能掌握程度的一次总测试。
撰写毕业设计中需要将理论运用于实际操作中,并通过自己对知识的掌握和学习将零件的结构分析清楚。
并进一步对其进行工艺分析。
精密主轴的加工涉及到我们数控知识的很多方面。
首先必须能够作到1:合理选用材料和规定的相应热处理。
2:掌握基本指令的综合使用能力。
3:掌握综合轴类的加工工艺分析。
4:能设计简单的夹具并选择相应的机床。
5:能确定各工序有关的切削因素,能对加工质量进行分析处理。
6:能熟练掌握基准的选择,掌握保证尺寸精度的技能技巧。
此次设计的磨床主轴加工方案的技能点主要在于锥面的加工,带凹槽零件的编程,深孔的加工,内螺纹的加工,外圆的铣扁,高精度磨削。
这些都是我们学习三年数控必须掌握的基础知识,也是考验我们是否能学以至用的时候。
(完整版)轴套零件的工艺分析和编程毕业设计论文

(完整版)轴套零件的工艺分析和编程毕业设计论文优秀论文审核通过未经允许切勿外传零件图轴套三维图轴套三维图轴套类零件的工艺设计与加工摘要:随着数控技术的发展,数控技术的应用不但给传统制造业带来了革命性的变化,使制造业成为工业化的象征,而且随着数控技术的不断发展和应用领域的扩大,它对国计民生的一些重要行业的发展起着越来越重要的作用。
随着科技的发展,数控技术也在不断的发展更新,现在数控技术也称计算机数控技术,加工软件的更新快,CADCAM的应用是一项实践性很强的技术。
如像UG , PROE , Cimitron , MasterCAM ,CAXA制造工程师等。
数控技术是技术性极强的工作,尤其在模具领域应用最为广泛,所以这要求从业人员具有很高的机械加工工艺知识,数控编程知识和数控操作技能。
本文主要通过c车削加工配合件的数控工艺分析与加工,综合所学的专业基础知识,全面考虑可能影响在车削加工中的因素,设计其加工工艺和编辑程序,完成配合要求。
关键词: 车削;CADCAM;配合件零件加工前言毕业设计是专业教学工作的重要组成部分和教学过程中的重要实际性环节。
毕业设计的目的是:通过设计,培养我们综合运用所学的基础理论知识,专业理论知识和一些相关软件的学习,去分析和解决本专业范围内的一般工程技术问题的能力,培养我们建立正确的工艺设计思维,学会查找工具书,掌握数控工艺设计的一般程序,规范和方法。
本次设计选择的课题为轴类零件的车削加工工艺设计及其数控加工程序编制。
这次毕业设计让我们对机械制图的基础知识有了进一步的了解,同时也为我们从事绘图工作奠定了一个良好的基础。
并锻炼了自己的动手能力,达到了学以致用的目的。
它是一次专业技能的重要训练和知识水平的一次全面体验,是学生毕业资格认定的重要依据,同时也为我们将来走向工作岗位奠定了必要的理论基础和实践经验。
目录前言第一章零件工艺分析 (1)1.1零件的分析 (1)1.1.1零件的结构分析 (1)第二章毛坯的选择 (5)2.1毛坯的种类 (5)2.2选择毛坯的原则 (5)第三章数控加工工艺设计 (6)3.1定位基准的确定 (6)3.1.1基准的概念及分类 (6)3.1.2定位基准的选择 (8)3.2工艺路线的拟订 (8)3.2.1表面加工方法的选择 (8)3.3机床设备与工艺装备的选择 (10)3.4加工阶段的划分 (10)3.5工序的划分 (11)3.6工序顺序的安排 (11)3.7加工余量的确定 (13)3.7.1影响加工余量的因素 (15)3.7.2加工余量的确定——计算法、查表法和经验估计法16第四章工序卡制定 (17)第五章数控程序编制 (18)参考文献 (19)谢辞 (20)附表1 (21)附表2 (25)附表3 (33)附表4 (35)第一章零件工艺分析1.1零件的分析1.1.1零件的结构分析该零件为轴类零件。
轴套零件车削工艺分析
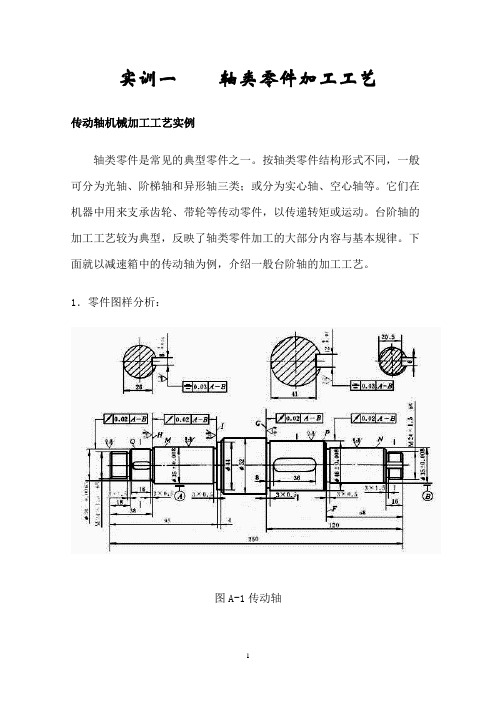
实训一轴类零件加工工艺传动轴机械加工工艺实例轴类零件是常见的典型零件之一。
按轴类零件结构形式不同,一般可分为光轴、阶梯轴和异形轴三类;或分为实心轴、空心轴等。
它们在机器中用来支承齿轮、带轮等传动零件,以传递转矩或运动。
台阶轴的加工工艺较为典型,反映了轴类零件加工的大部分内容与基本规律。
下面就以减速箱中的传动轴为例,介绍一般台阶轴的加工工艺。
1.零件图样分析:图A-1传动轴图A-1所示零件是减速器中的传动轴。
它属于台阶轴类零件,由圆柱面、轴肩、螺纹、螺尾退刀槽、砂轮越程槽和键槽等组成。
轴肩一般用来确定安装在轴上零件的轴向位置,各环槽的作用是使零件装配时有一个正确的位置,并使加工中磨削外圆或车螺纹时退刀方便;键槽用于安装键,以传递转矩;螺纹用于安装各种锁紧螺母和调整螺母。
根据工作性能与条件,该传动轴图样(图A-1)规定了主要轴颈M,N,外圆P、Q 以及轴肩G、H、I有较高的尺寸、位置精度和较小的表面粗糙度值,并有热处理要求。
这些技术要求必须在加工中给予保证。
因此,该传动轴的关键工序是轴颈M、N和外圆P、Q的加工。
2.确定毛坯:该传动轴材料为45钢,因其属于一般传动轴,故选45钢可满足其要求。
本例传动轴属于中、小传动轴,并且各外圆直径尺寸相差不大,故选择¢60mm的热轧圆钢作毛坯。
3.确定主要表面的加工方法:传动轴大都是回转表面,主要采用车削与外圆磨削成形。
由于该传动轴的主要表面M、N、P、Q的公差等级(IT6)较高,表面粗糙度Ra值(Ra=0.8 um)较小,故车削后还需磨削。
外圆表面的加工方案(参考表A-3)可为:粗车→半精车→磨削。
4.确定定位基准:合理地选择定位基准,对于保证零件的尺寸和位置精度有着决定性的作用。
由于该传动轴的几个主要配合表面(Q、P、N、M)及轴肩面(H、G)对基准轴线A-B均有径向圆跳动和端面圆跳动的要求,它又是实心轴,所以应选择两端中心孔为基准,采用双顶尖装夹方法,以保证零件的技术要求。
轴套类零件加工工艺分析
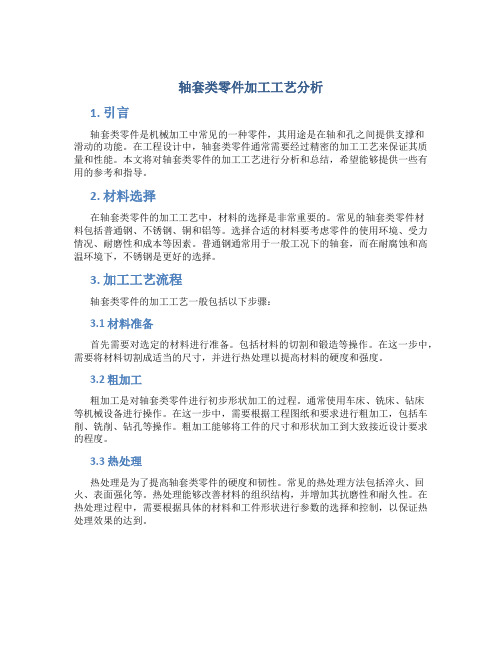
轴套类零件加工工艺分析1. 引言轴套类零件是机械加工中常见的一种零件,其用途是在轴和孔之间提供支撑和滑动的功能。
在工程设计中,轴套类零件通常需要经过精密的加工工艺来保证其质量和性能。
本文将对轴套类零件的加工工艺进行分析和总结,希望能够提供一些有用的参考和指导。
2. 材料选择在轴套类零件的加工工艺中,材料的选择是非常重要的。
常见的轴套类零件材料包括普通钢、不锈钢、铜和铝等。
选择合适的材料要考虑零件的使用环境、受力情况、耐磨性和成本等因素。
普通钢通常用于一般工况下的轴套,而在耐腐蚀和高温环境下,不锈钢是更好的选择。
3. 加工工艺流程轴套类零件的加工工艺一般包括以下步骤:3.1 材料准备首先需要对选定的材料进行准备。
包括材料的切割和锻造等操作。
在这一步中,需要将材料切割成适当的尺寸,并进行热处理以提高材料的硬度和强度。
3.2 粗加工粗加工是对轴套类零件进行初步形状加工的过程。
通常使用车床、铣床、钻床等机械设备进行操作。
在这一步中,需要根据工程图纸和要求进行粗加工,包括车削、铣削、钻孔等操作。
粗加工能够将工件的尺寸和形状加工到大致接近设计要求的程度。
3.3 热处理热处理是为了提高轴套类零件的硬度和韧性。
常见的热处理方法包括淬火、回火、表面强化等。
热处理能够改善材料的组织结构,并增加其抗磨性和耐久性。
在热处理过程中,需要根据具体的材料和工件形状进行参数的选择和控制,以保证热处理效果的达到。
3.4 精密加工精密加工是将轴套类零件的尺寸和形状加工到精确的设计要求的过程。
精密加工通常包括数控加工、磨削、线切割等操作。
数控加工能够实现高精度的加工,磨削能够提高零件的表面质量和几何精度,线切割能够加工出复杂的内部结构。
3.5 表面处理表面处理是为了提高轴套类零件的表面质量和耐腐蚀性。
常见的表面处理方法包括电镀、喷涂、氮化等。
表面处理能够在一定程度上提高轴套类零件的耐磨性和使用寿命。
4. 加工工艺优化为了提高轴套类零件的加工效率和质量,可以对加工工艺进行优化。
轴套类零件加工工艺分析
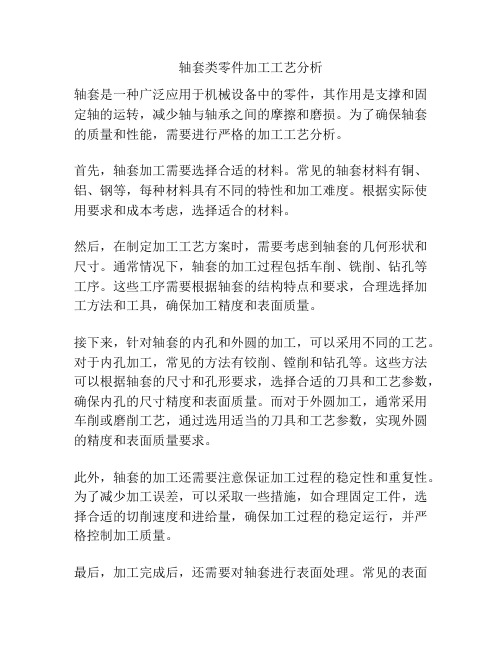
轴套类零件加工工艺分析轴套是一种广泛应用于机械设备中的零件,其作用是支撑和固定轴的运转,减少轴与轴承之间的摩擦和磨损。
为了确保轴套的质量和性能,需要进行严格的加工工艺分析。
首先,轴套加工需要选择合适的材料。
常见的轴套材料有铜、铝、钢等,每种材料具有不同的特性和加工难度。
根据实际使用要求和成本考虑,选择适合的材料。
然后,在制定加工工艺方案时,需要考虑到轴套的几何形状和尺寸。
通常情况下,轴套的加工过程包括车削、铣削、钻孔等工序。
这些工序需要根据轴套的结构特点和要求,合理选择加工方法和工具,确保加工精度和表面质量。
接下来,针对轴套的内孔和外圆的加工,可以采用不同的工艺。
对于内孔加工,常见的方法有铰削、镗削和钻孔等。
这些方法可以根据轴套的尺寸和孔形要求,选择合适的刀具和工艺参数,确保内孔的尺寸精度和表面质量。
而对于外圆加工,通常采用车削或磨削工艺,通过选用适当的刀具和工艺参数,实现外圆的精度和表面质量要求。
此外,轴套的加工还需要注意保证加工过程的稳定性和重复性。
为了减少加工误差,可以采取一些措施,如合理固定工件,选择合适的切削速度和进给量,确保加工过程的稳定运行,并严格控制加工质量。
最后,加工完成后,还需要对轴套进行表面处理。
常见的表面处理方法有硬化、镀铜、喷涂等,这些处理可以增加轴套的硬度、耐磨性和防腐蚀性,提高轴套的使用寿命和性能。
综上所述,轴套类零件加工工艺分析需要考虑材料选择、加工方案设计、加工方法选择、加工参数控制以及表面处理等方面的因素。
只有通过科学、严谨的加工工艺分析和操作实施,才能保证轴套的质量和性能,满足实际使用的要求。
使用字数较多的订单可能会影响响应速度。
然而,我将提供大致的文章结构和提示,以帮助你纳入所需的内容。
1. 引言(介绍轴套及其重要性)- 简要介绍轴套是什么,其在机械设备中的重要作用。
2. 材料选择(包括性能要求和材料选型)- 详细描述轴套所需的性能要求,并介绍适用的材料选项。
轴套加工工艺

2.1 套类零件工 艺分析 (3)先完成外圆加工,然后以外圆为精基准加工内
孔。一般卡盘安装误差较大,使得加工后工件的相
互位置精度较低。如果欲使同轴度误差较小,则须
采用定心精度较高的夹具,如弹性膜片卡盘、液性
塑料夹头、经过修磨的三爪自定心卡盘和软爪等。
2.1 套类零件工 2、减少变形 艺分析
套筒类零件的结构特点是壁薄,在切削加工中常 由于夹紧力、切削力、内应力和切削热等因素的影 响而产生变形。为此,应注意将粗、精加工分开进 行,应尽量减少加工余量,增加走刀次数。同时,应 改善夹持方式,减小夹紧力。例如,采用过渡套或弹 簧套来夹持,或者夹持工艺凸台或工艺螺纹(见表63工序2,工序4),加工完后再切去(工序5)。另外,应 该尽量减小热处理变形对加工过程的影响,将热处 理放在粗加工和精加工之间进行,让精加工切除热 处理的残留变形量
2.2 套类零件材料及毛 3、套类零件的材料、毛坯及热处理 坯选择
套类零件的材料
套筒类零件的材料以钢、铸铁、青铜或黄铜为主,也有 采用双金属结构(即在钢或铸铁套的内壁上浇注一层轴承合金 材料)的。
套类零件的毛坯
1)孔径较大(如d>20mm)时,常采用无缝钢管或带孔的铸件和 锻件; 2)孔径较小时,多选用热轧或冷拉棒料,也可采用实心铸件; 3)大批量生产时,可采用冷挤压棒料、粉末冶金棒料。
2.4 套类零件加工工艺 3.加工路线的拟定 编制举例
为保证套筒内外圆的同轴
度要求和A、B端面对轴心线的 垂直度,采用在一次装夹中先
粗、精车端面A,
φ 外圆和B端面, 的孔。
再钻、扩、铰φ
车C面及φ54外圆,钻、扩、铰内孔,刨D面;
5
6 7 8
钻-拉
(钻)-粗镗-半精镗 (钻)-粗镗-半精镗-精镗 (钻)-粗镗-半精镗-磨
- 1、下载文档前请自行甄别文档内容的完整性,平台不提供额外的编辑、内容补充、找答案等附加服务。
- 2、"仅部分预览"的文档,不可在线预览部分如存在完整性等问题,可反馈申请退款(可完整预览的文档不适用该条件!)。
- 3、如文档侵犯您的权益,请联系客服反馈,我们会尽快为您处理(人工客服工作时间:9:00-18:30)。
零件工艺分析
零件图纸:
一、零件结构工艺分析
1.零件的选材;
1) 通过图纸可知,零件需要渗碳处理,且对渗碳层深度有要求,
2)图纸给出,该零件有焊接的需要,
3)图纸上零件给出的材料是20Cr,
4)图纸给出代用材料,允许使用20CrMo ,
5)20Cr晶粒为粗晶粒,20CrMo晶粒为细晶粒,材料性能更好,
6)20CrMo淬透性较高,无回火脆性,焊接性相当好,形成冷裂的倾向很小,可切削性及冷应变塑性良好。
相比20Cr,材料具有更好的韧性且满足材料代用原则,
7)考虑到零件是成批生产,为了提高加工的效率,考虑选用铸件或者锻件,
8)图纸零件并不复杂,用模锻可以满足零件毛坯要求。
同时锻件相比于铸件的力学性能更好。
9)综上所述分析,零件材料选用20CrMo带孔锻件毛坯。
2.零件结构工艺分析,零件的主要、次要表面划分;
(1)、零件结构工艺分析
由轴套零件图可知。
轴套属于一个轴类零件,它的外表面上有3个平面需要进行加工,中心有一个通孔。
因此可将其分为两组组加工表面。
它们相互间有一定的位置要求。
现分析如下
1)、以外圆面为主要加工表面的加工面。
这一组加工表面包括:φ42.2外圆面、φ32外圆面、φ27外圆面的加工;其中φ42.2表面粗糙度要求为0.8Ram,其余为1.6Ram。
2)、φ20孔为主要加工表面的孔,粗糙度为1.6Ram,以φ20孔轴线为基准的两端面。
(2)、零件的主、次要表面划分
主要表面:①φ42.2的外圆表面,②φ20孔,③φ32孔,
次要表面:①φ27外圆面,②两端面,③各台阶面
3.机械加工的工序基准选择。
粗基准选择:主要支承孔作为主要基准。
即以轴套的输入轴和输出轴的支承孔作为粗基准
精基准选择:精基准的选择应能保证轴套在整个加工过程中基本上都能用统一的基准定位,选择设计基准作为精基准
①以轴套端面为基准加工φ20孔轴线;
②以φ20孔轴线为基准,加工以外圆面为主要加工表面的加工面。
二、零件技术分析
1.尺寸精度分析
φ42.2的外圆表面、φ32的外圆表面、φ22的内孔、26的尺寸精度的精度等级为IT7级。
2.形状与位置精度分析;
①、图中有以内孔轴线为基准的垂直度0.02的要求,其精度等级为IT8级。
②、图中有以内孔轴线为基准的同轴度φ0.015的要求,其精度等级为IT7级。
3.表面质量、有无特殊要求分析.
φ22内孔粗糙度为1.6Ram,φ32的外圆表面粗糙度为1.6Ram,端面的粗糙度为1.6Ram,精度等级为IT7级。
φ42.2的外圆表面的粗糙度为0.8Ram精度等级为IT7级。
特殊要求:要求渗碳,渗碳层深0.8-1.2,表面硬度58-64HRC,芯部硬度30-45HRC,但φ32外圆及端面A、B倒角C1区域不能有渗碳层。
三、毛坯成型的选择:
毛坯选择锻件,采用模锻成型
四、热处理工艺的安排:
1、完全退火:获得接近平衡状态的组织。
可以均匀组织,消除内应力,降低硬度,便于切削加工,并为加工后零件的热处理作好组织准备。
工序安排的位置:粗加工之前
2、渗碳处理:使零件表层得到高含碳量和一定的浓度梯度,提高表面的硬度、耐磨性及疲劳强度,而心部仍保持良好的塑性及韧性。
工序安排的位置:精车之后,磨削加工之前
五、零件加工工艺方案的拟定
1、方案的选择:
方案一、
模锻锻造毛坯→毛坯完全退火→粗车φ42外圆及右端面→精车φ42外圆及右端面→粗车φ32外圆、粗车φ27外圆及左端面→精车φ32外圆、精车φ27外圆及左端面→精车A、B面→精车φ22内孔→粗磨φ22内孔→渗碳处理→低温回火→倒角C1、R1→精磨φ42外圆→钳工去毛刺→检验入库
方案二、
模锻锻造毛坯→毛坯完全退火→粗车φ42外圆及右端面→精车φ42
外圆及右端面→粗车φ32外圆、粗车φ27外圆及左端面→精车φ32外圆、精车φ27外圆及左端面→渗碳处理→低温回火→精车A、B面→精车φ22内孔→粗磨φ22内孔→倒角C1、R1→精磨φ42外圆→钳工去毛刺→检验入库
方案三、
模锻锻造毛坯→完全退火→粗车φ42外圆及右端面→精车φ42外圆及右端面→精车φ22内孔→粗车φ32外圆、φ27外圆及左端面→精车φ27外圆及φ32外圆和左端面→倒C1、R1→渗碳处理→低温回火→磨φ32外圆→粗磨A、B面及倒角→粗磨φ22内孔→精磨φ42外圆→修磨C1倒角→检验入库
综上所述,结合生产批量、结构工艺性、技术要求等方面,最终选定使用工艺方案三。
2、零件名称:从动齿轴套
材料牌号:20CrMo
3、毛坯种类:锻件
毛坯尺寸:φ46×φ30×30
4、零件表面加工方法的选择:
φ22内孔,φ32的外圆表面:采用粗车、精车、磨削加工
φ42.2的外圆表面:采用粗车、精车、表面渗碳、磨削加工
A、B面:采用车削与磨削
倒角C1及圆角R1:采用车削与铣
5、加工设备的选择
粗车:CA6140 精车:CA6140
磨削:M1432A 热处理:WH-VI-160
六、检验工序的安排
1、检验工序的安排:每道工序自检,加工完成后抽检
2、量具的选择
测量外圆轮廓尺寸:外径千分尺
R倒角:R规
轴向尺寸:游标卡尺0-100 精度0.02
同轴度、垂直度、其他:三坐标测量仪。