哈尔滨工业大学科技成果——大型铝合金制件液态模锻精密成形技术
液态压铸锻造双控一次成型技术通过科技成果鉴定

( ) 空 回火 炉停 用 时 , 真 空度 抽 至极 限 , 且 美表 面状 态 遭 到 破坏 ,并 且 工 件 回火后 存 在 色质 差 、 7真 将 并 ( ) 空 淬 火 工 件 出 炉 时 , 作 者 戴 干 净 白纱 手 现 在 国 产 真 空 回火 炉 包 括 进 口真 空 回 火 炉都 存 在 因 8真 操 通 过 以上 一 系列 的点 检 、维 护 及 保 养 ,U  ̄ 0 良的 机 械性 能 , 疲 劳 性 能 、 腐 蚀 性 能 、 面 硬 度 、 S S4C 如 耐 表 及 S M9 A 7再 次经 真 空 回火 炉 回火 后 ,虽 然 着 色 情 况 耐 磨 性 等 , 有 通 过 真 空 回火 才 能 完 美 呈 现 , 别 是 只 特 比 以前 有 所好 转 , 仍 有 轻 度 着 色 , 但 同样 S S 4 C比 需采 用 二 次硬 化 温 度 多 次 回火 的 精 密工 件 更 应 如此 . U  ̄0
( ) N 中加入 1%的 H:使 对 流加 热 混合 气呈 2充 : O ,
,
以及 炉 内结 构材 料所 吸 附 的 氧 和水 份 等 。这些 吸 附 的 还 原 性 气 氛 将 炉 内的 弱 氧 化 性 气 氛 与 H 中和 , 成 形 氧 和水份 虽 然在 排气 时 因退 吸现 象 而 被抽 走 。但 一经 弱还 原 性气 氛 。 加 热 升 温 , 件上 附 着 的 各类 物 质 发 生 挥 发 和 残 存气 工 () 可能 不 用 吸 附性 和 吸湿 性 强 的结构 材 料 。 3尽
维普资讯
・
模 具 材 料 及 热 处 理 技 术 ・
@
S E ON TL G 网
哈工大和哈工大深研院在超精密加工方面的状况
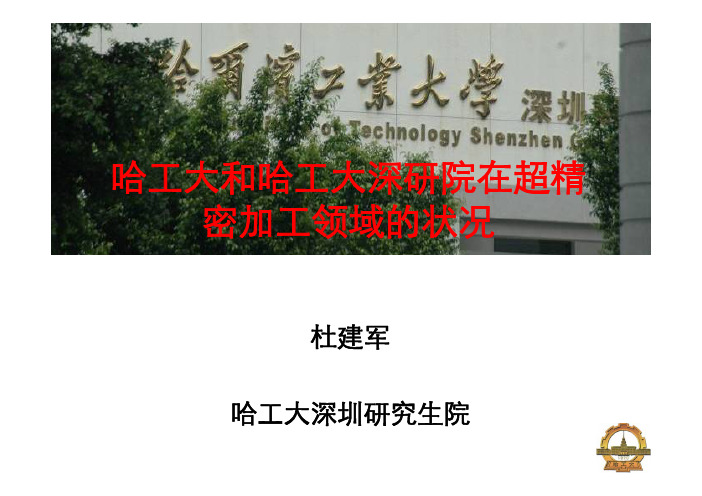
2
Harbin Institute oபைடு நூலகம் Technology Shenzhen Graduate School
1 哈工大深研院在超精密加工领域的状况
哈工大深研院在精密超精密加工方面开展了深入的研究,开展了用于超精密 和超高速加工领域的气体润滑技术研究,开发了超精密机床的精密气浮主轴、精密 气浮导轨、超高速气浮电主轴,以及单点金刚石超精密数控车床和基于并联机构的 抛光机等等,建立了相应的实验和检测环境。
8
Harbin Institute of Technology Shenzhen Graduate School
1 哈工大深研院在超精密加工领域的状况
超精密车床其它辅助技术的研究
真空吸盘采用如下图 (a)所示的结构示意图,可以吸附不同直径的工 件、吸附能力强等优点。刀架采用如下图 (b)所示的结构示意图,具有可微 调刀具的高度、夹持刚性强等优点。
本提升项目的技术指标为: z 加工零件的表面粗糙度:30nm; z 主轴回转精度:轴向<50nm,径向<50nm; z 主轴最高转速:2000rpm; z X轴、Z轴行程:140mm; z 直线光栅分辨率:1nm; z 导轨直线度(敏感方向):0.3μm/全行程;
5
Harbin Institute of Technology Shenzhen Graduate School
1 哈工大深研院在超精密加工领域的状况
总体布局图
Z X
(a)俯视图
主轴
X
Z
主轴
刀具(如想快刀加 工,安装FTS模块) (b)前视图
ω 主轴
导轨 床身
工件
刀具
c) 三维视图
哈尔滨工业大学科技成果——特种泵阀工业用材料及相关铸造技术

哈尔滨工业大学科技成果——特种泵阀工业用材料
及相关铸造技术
主要研究内容本项目针对特种泵和阀门工业用耐磨耐蚀抗冲击高铬铸铁,采用近净成形铸造技术,生产抗硬料或软料磨蚀,在PH 值3-9范围内工作的泵体、阀门和叶轮等铸件,材质采用课题组自行研制的新型高铬耐磨耐蚀铸铁,近期发展方向:火力发电厂脱硫渣浆泵阀门、黄河水利枢纽调水调砂泵阀、医学制药小型泵阀(不锈钢类)、石油开采原油输送泵阀;中长期发展方向:船用泵阀、海洋工程、海水淡化工程(特种不锈钢、钛合金等)。
该技术的主体部分包括新材料研制和铸造、热处理和修复工艺研发,在技术层面上与山东双轮集团有限公司和温州宣达实业公司进行了广泛合作,其中“脱硫渣浆泵用新型钛氮共添加高铬铸铁及其铸造工艺”已在双轮集团进行了产业化转化,该材质被企业列入技术标准,而且在特种泵阀用材料及工艺项目研发上签署了合作协议,因此可以看出技术具有很高的成熟度,实现其产业化是可行的。
主要应用火力水利发电、石油开采、精细化工、生物制药、水利工程、排水灌溉、船舶工程、海洋开发、海水淡化。
主要技术指标
1、新型高铬铸铁的拉伸强度大于650MPa;抗弯强度大于1100MPa;冲击韧性大于9J/cm2。
2.新型高铬铸铁在PH=4的模拟工况腐蚀液中的腐蚀速率小于0.015mm/a。
SiCp_ZL102复合材料液态模锻的研究

锻压技术 2001年 第6期SiC p/Z L102复合材料液态模锻的研究哈尔滨工业大学威海分校(264209) 韩 飞3陕西工学院 解念锁 王永善 摘要 采用机械搅拌法液态模锻成形工艺,制取了5%SiC 颗粒增强铸铝基复合材料。
研究了比压对其抗拉强度、塑性和硬度的影响,并分析了其显微组织和力学性能。
关键词 复合材料 液态模锻 力学性能3男,39岁,副教授收稿日期:2000211229一、引言颗粒增强铝基复合材料率先在航空、航天和核能等高新技术领域内应用,在民用工业中的应用也日益增多。
由于SiC p 价格便宜、易于获得,而且它的弹性模量、密度、膨胀系数,与铝合金的相容性等易满足要求,因此人们对它进行了大量研究。
SiC p 增强铝基复合材料在基础理论、制备工艺、性能水平等方面已有较多的研究[1~8],但SiC p 增强Z L102复合材料的液态模锻研究尚未见报道。
本文以工业上常用的Z L102作为基体,SiC p 为增强相,将经过预处理的SiC p 加入到铸铝合金液体中加以搅拌。
将混合均匀的液态复合浆料,浇入模具中,使液态复合浆料在较高的机械压力下凝固成形,制备出组织致密、性能高的复合材料,研究了不同比压对抗拉强度、塑性和硬度的影响,分析了其显微组织和力学性能,为碳化硅增强铸铝基复合材料的生产应用提供参考。
二、试验方法11原材料基体材料采用某厂生产用的Z L102合金,增强体材料为市售SiC p 磨料,名义尺寸为20μm 。
21SiCp 预处理将SiC p 放在高温箱式电阻炉中,升温到500℃,保温1h ,去除表面油污、气体等,然后升温到800℃,保温3h ,进行表面氧化处理。
31Z L102合金熔炼和复合浆料搅拌将Z L102锭块放入电阻坩锅炉中,加热熔化,在580℃,将自制搅拌器夹持在钻床夹头上,将搅拌器沉入液态合金中,搅拌速度为480r/min ,将经过预处理的5%SiC p ,由炉盖小孔加入液态合金中,搅拌20min ,升温至620℃待浇注。
大型高质量铝合金铸件控压成型关键技术及应用
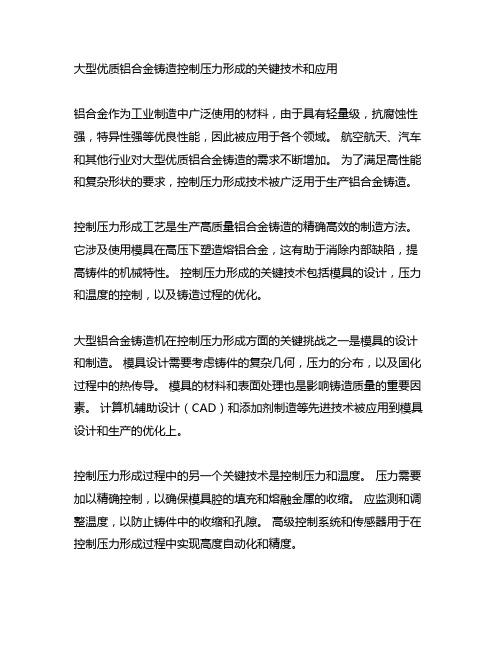
大型优质铝合金铸造控制压力形成的关键技术和应用铝合金作为工业制造中广泛使用的材料,由于具有轻量级,抗腐蚀性强,特异性强等优良性能,因此被应用于各个领域。
航空航天、汽车和其他行业对大型优质铝合金铸造的需求不断增加。
为了满足高性能和复杂形状的要求,控制压力形成技术被广泛用于生产铝合金铸造。
控制压力形成工艺是生产高质量铝合金铸造的精确高效的制造方法。
它涉及使用模具在高压下塑造熔铝合金,这有助于消除内部缺陷,提高铸件的机械特性。
控制压力形成的关键技术包括模具的设计,压力和温度的控制,以及铸造过程的优化。
大型铝合金铸造机在控制压力形成方面的关键挑战之一是模具的设计和制造。
模具设计需要考虑铸件的复杂几何,压力的分布,以及固化过程中的热传导。
模具的材料和表面处理也是影响铸造质量的重要因素。
计算机辅助设计(CAD)和添加剂制造等先进技术被应用到模具设计和生产的优化上。
控制压力形成过程中的另一个关键技术是控制压力和温度。
压力需要加以精确控制,以确保模具腔的填充和熔融金属的收缩。
应监测和调整温度,以防止铸件中的收缩和孔隙。
高级控制系统和传感器用于在控制压力形成过程中实现高度自动化和精度。
优化铸造工艺对确保生产质量和效率也至关重要。
铝合金的选择、熔金属的预处理和铸件的后处理,都对产品的最终性质有重大影响。
要成功应用控制压力形成技术,就必须全面了解物质行为和过程参数。
主要飞机制造商空中客车一直利用控制压力形成技术为其飞机部件生产大型铝合金铸造。
通过实施先进的模具设计和制造技术,精确控制压力和温度,优化铸造工艺,空中客车在铝合金铸造生产质量和效率上取得了显著提高。
大型优质铝合金铸造控制压力形成的关键技术和应用,在满足各行业对轻量级和高性能组件日益增长的需求方面发挥了关键作用。
控制压力形成技术的持续进步将进一步促进具有复杂形状和优越性能的铝合金铸造的发展。
哈尔滨工业大学科技成果——大尺寸微结构滚筒模具超精密加工技术与装备

哈尔滨工业大学科技成果——大尺寸微结构滚筒模具超精密加工技术与装备主要研究内容在国家“高档数控机床与基础制造装备”科技重大专项课题的支持下,科研团队在国内率先开展了大尺寸微结构滚筒模具超精密加工的关键技术攻关,突破了基于光栅衍射原理的微金刚石刀具磨损状态在线监控、低转速条件下的高精度在线动平衡技术、正交叠加静压导轨的动刚度解耦等关键技术,研发成功了国内第一台大尺寸微结构辊筒模具超精密加工机床。
目前,该机床装备已经进入实用化测试阶段,已经与国内的多家棱镜膜片生产厂家合作,利用该机床开展相关的工艺研究,争取尽快实现对昂贵的进口设备的替代,打破国外的技术垄断。
该项技术为国内首创的自主研发技术,技术优势明显,相关行业需求迫切,市场前景良好。
获得一定量的资金和配套场地、技术人员,采用关键核心部件自行生产、非关键核心部件外委加工的生产方式,可以快速实现该技术的商品化和产业化,作为Roll-to-Roll制造工艺的上游核心装备与技术,可以促进大尺寸微结构滚筒模具的Roll-to-Roll 制造工艺在液晶面板制造、聚光太阳能发电装置制造、具有隐身及减阻功能的智能蒙皮制造、道路照明等领域快速发展,带动国家的一个战略性产业。
主要应用面向液晶面板制造、聚光太阳能发电装置制造、具有隐身及减阻功能的智能蒙皮制造、道路照明等领域,有着广泛的应用需求,是一个国家的战略性产业技术。
国内行业需求迫切、未来增长趋势明显。
主要技术指标大尺寸微结构滚筒模具超精密加工机床主要技术指标:1、机床加工的工件尺寸:最大直径Ф400mm;最大长度1400mm;2、工件的重量:1000Kg;3、机床坐标轴的行程:X轴240mm;Z轴1500mm;4、主轴:径向刚度大于6000N/μm;轴向刚度大于5000N/μm;5、主轴静态回转精度:小于0.5μm;6、坐标轴的运动控制分辨率:50nm;7、微结构的表面粗糙度:Ra不大于10nm;8、微结构的最小尺寸:不大于100μm。
哈尔滨工业大学科技成果——非金属增材制造(3D打印)关键技术与装备
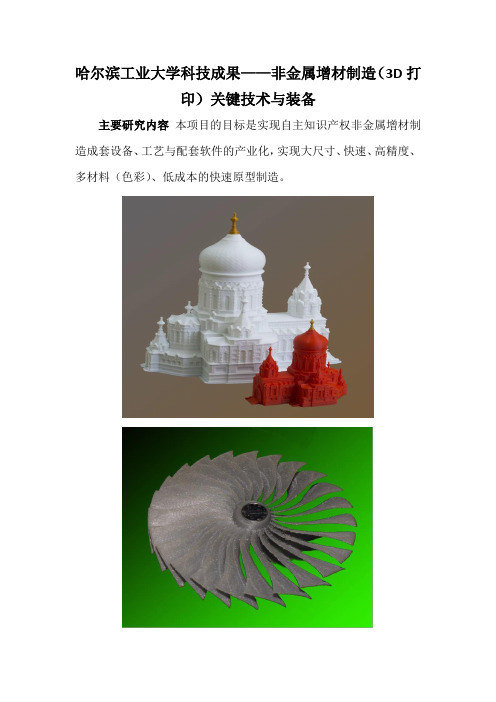
哈尔滨工业大学科技成果——非金属增材制造(3D打
印)关键技术与装备
主要研究内容本项目的目标是实现自主知识产权非金属增材制造成套设备、工艺与配套软件的产业化,实现大尺寸、快速、高精度、多材料(色彩)、低成本的快速原型制造。
主要应用建筑、机械设计验证、零件与模具制造、辅助诊疗与手术规划、文物保护等。
主要技术指标
1、FDM原理快速成型设备:支持最大尺寸不小于500mm的零件制造,支持水溶性材料与多色制造,最高尺寸精度达到0.1mm,制造速度不低于15g/h。
2、光敏固化快速成型机:分层精度不大于0.05mm,最高成型速度达到30mm/h,支持多模型自动空间分配,树脂利用系数不大于0.5。
压铸、挤压铸造液态模锻及半固态加工的适应性分析[1]
![压铸、挤压铸造液态模锻及半固态加工的适应性分析[1]](https://img.taocdn.com/s3/m/8771ee41be1e650e52ea9970.png)
适用范围:它是压铸和热模锻的一种工艺补充。即对于
形状复杂(或厚壁件)而性能有一定要求的制件,采用热
模锻难以成形,而采用压铸或罔铸造缺陷难以消除(如
壁厚不均匀)件,或因力学性能达不到的这类制件要求,
完全可以选用挤压铸造(液态模锻)”j。
收稿日期:2u07—04—1 3 作者简介:笋守靖,爿.1939年出牛,教授.嵴尔滨工业凡学材料科学与1_程学院.晴尔滨(1 50001).}U活0451—8 64j 8 72 3,F_malI:Iuos】@hit edu cn
特种铸造及有色合金
图7挤压铸造(液态摸锻)成形件
图8 uBE流变设备
图9半固态压铸设备
图1()采用半圆态加工生产的汽车零件 釜山近净成形厂工艺配置:以压铸为主体,辅以挤 压铸造(液态模锻)和半固态加工,兼顾使用性和经济 性,使产品成形L艺确极大的选择空间。在推进交通运 输机械零件轻量化方面,极具竞争力。
Alloys and(10nlpos Ltes,Tonno】taly,Swpt.2000:22l一225. :11]王益忐半同志成形中的某些关键技术:J:.特种铸选及有色台金,
2002‘压铸专刊):1 92 104
L12j罗守靖,杜之明,姜巨福.复合制料和半固态加工技术[j]特种蒋
造及有色合金,2∞3(s):290 292
参考文献 一]]罗守靖,何蜊兀,f尔德.等镧质液态模锻[M]哈尔淡暗尔滨
D咿大学出版社,19。。
[2j nJlHqK址】_1 BM山Ta姗oB髓Ⅱ3 H(Ⅱt£Koro 1ⅥeTa且胍[M Ma山Hll旷
Tp㈣e,]964
[3j谢水生,黄声宏、#固悫金届加1:技术及其应用:M]北京:冶金 _E、『k出版朴。19§9
- 1、下载文档前请自行甄别文档内容的完整性,平台不提供额外的编辑、内容补充、找答案等附加服务。
- 2、"仅部分预览"的文档,不可在线预览部分如存在完整性等问题,可反馈申请退款(可完整预览的文档不适用该条件!)。
- 3、如文档侵犯您的权益,请联系客服反馈,我们会尽快为您处理(人工客服工作时间:9:00-18:30)。
哈尔滨工业大学科技成果——大型铝合金制件液态
模锻精密成形技术
项目简介
随着我国交通运输业,武器装备向现代化、高速化方向发展,轻量化要求日趋强烈,特别是轻量化程度要求高的飞机、航天器、高速列车、汽车、舰艇、火炮、坦克以及机械设备等重要受力部件和结构件,需要大量使用铝合金锻件和模锻件以替代原来的钢结构件。
而传统的铸造和模锻技术已不能完全满足这些铝合金关键零部件的制造需求和使用性能,正是这种需求使得大型铝合金制件液态模锻精密成形技术的研究。
成型制件
2000年哈尔滨工业大学液态模锻课题组开展了大型铝合金负重轮液态模锻精密成形技术的研究工作,2003年成功地实现了铝合金负重轮本体与局部(钢质材料或复合材料)耐磨增强一体化精密成形,各项静态和里程试验性能指标均达到设计要求,与钢制轮盘相比,质
量减轻了40%,经检验后取得成功应用。
该成形技术操作方便,成本低,产品综合性能良好,填补了国内液态模锻生产铝合金负重轮的空白。
成形技术的推广应用。