硅铁生产工艺课件
硅铁合金生产工艺课件

未来,随着技术的进步和产业结构的调整,硅铁合金的生产将更加环保、高效,市场前景广 阔。
02
硅铁合金生产工艺流 程
原料准备
01
02
03
原料选择
3
混合均匀
采用合适的混合设备,将各种原料混合均匀,确 保生产出的硅铁合金成分稳定。
装炉与熔炼
装炉
将混合好的原料装入熔炼 炉中,注意避免炉内出现 空洞、偏析等现象。
熔炼
在高温下进行熔炼,使各 种原料充分熔化、反应, 形成硅铁合金。
除渣
熔炼过程中会产生杂质和 浮渣,需要进行除渣处理 ,以确保硅铁合金的质量 。
物理性能检测
对产品的物理性能进行检测,如硬度、抗拉强度 、延伸率等,确保产品质量达标。
不合格品处理
对不合格的产品进行追溯和处理,分析原因并采 取措施防止类似问题再次发生。
05
安全与环保
生产安全措施
严格遵守安全操作规程
确保所有操作符合国家和行业标准, 遵循安全操作规程,降低事故风险。
定期进行安全检查
硅铁合金生产工艺课件
目录
• 硅铁合金简介 • 硅铁合金生产工艺流程 • 硅铁合金生产设备与工具 • 硅铁合金生产质量控制 • 安全与环保 • 硅铁合金生产成本与经济效益分析
01
硅铁合金简介
硅铁合金的定义
硅铁合金是指以硅元素为主要成分的 铁合金,通常由硅、铁和其他杂质元 素组成。
硅铁合金的硅含量一般在45%-75%之 间,根据硅含量的不同,硅铁合金可 以分为低硅铁、中硅铁和高硅铁。
硅铁
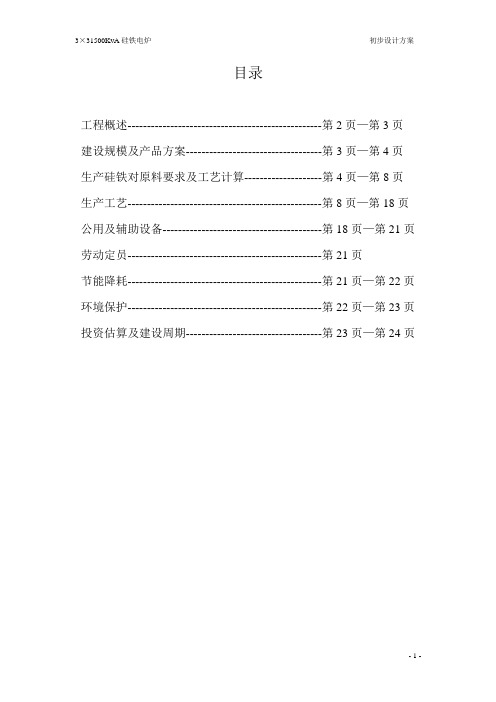
目录工程概述--------------------------------------------------第2页—第3页建设规模及产品方案-----------------------------------第3页—第4页生产硅铁对原料要求及工艺计算--------------------第4页—第8页生产工艺--------------------------------------------------第8页—第18页公用及辅助设备-----------------------------------------第18页—第21页劳动定员--------------------------------------------------第21页节能降耗--------------------------------------------------第21页—第22页环境保护--------------------------------------------------第22页—第23页投资估算及建设周期-----------------------------------第23页—第24页1、概述1.1本工程新建3座31.5KKVA硅铁电炉,并相应配套公共辅设施,设施年产量Q年=61500吨。
主要组成系统有:1.1.1原料、配料、上料系统。
1.1.2电炉冶炼主系统:含熔炼、浇注、冷却、成品。
1.1.3除尘及余热利用设施系统。
1.1.4综合供水系统:含生产生活新水、制冷水、冷冻水及综合泵水房。
1.1.5区街给排水系统:含生产污水、生活污水、雨水收集。
1.1.6储备系统:含备品备件库房、机电修理间、电极糊库、微硅粉库、主材料库。
1.1.7综合配套系统:调度办公楼、化验室、食堂、宿舍、浴池等。
1.2硅铁是在电炉中用硅石、还原剂(蓝炭、冶金焦等)、铁料(碎屑)为主要原料用电为能源生产的产品。
高品质硅铁的生产方法

铁合金专利)高品质硅铁的生产方法(一)作者:所属系别:硅铁关键字:硅铁发布日期:2010年01月11日17:52编者按:本发明涉及高品质硅铁的生产方法。
目前国内高品质硅铁的生产方法,主要有5种,一是采用精选炉料生产高纯硅铁,二是采用炉外吹氯精炼的方法生产高纯及低碳硅铁,三是采用炉外顶吹氧气的方法生产高纯及低铝硅铁,四是采用热冲渣洗的方法生产高纯及低碳硅铁,五是采用精选炉料的方法生产低铝、低碳硅铁。
采用精选炉料的方法生产高纯硅铁主要是通过精选石英石和石油焦、木块、木炭以及硅钢片原材料进行冶炼生产、以达到降低产品中杂质元素含量的目的。
该方法由于存在着原材料质量波动较大,冶炼生产过程中难免带入一部分杂质,从而产品中杂质含量的降低率受到限制,产品质量不高,成品率较低,而且生产炉况较难维护、炉口操作难度较大,产品的生产成本和能耗较大,经济指标较差。
炉方法脱除钙、铝效果较好,但尾气较多、且生产中常常产生泄漏和吹氯石墨管折断而中止精炼等情况,从而严重地污染了环境,危害工人的身体健康,而且对生产设备腐蚀较大。
炉外顶吹氧的方法进行炉外精炼,对产品中杂质钙、铝、碳元素脱除也较好。
但在使用过程中,由于铁水翻腾剧烈、喷溅损失较大,铁水温度迅速下降,造成粘包、铁损失较大,资料统计损失在12%-20%。
吹氧用石墨管也经常发生折断事故而中止精炼、成品率低,经济上也很不合算。
精选炉料的方法生产低铝、低碳硅铁主要是通过精选还原剂,如兰碳、气煤焦等原材料进行冶炼生产,以达到降低产品中杂质元素,主要是铝含量的目的。
该方法由于存在着原材料成份波动较大,冶炼过程中难免带入一部分杂质,从而产品中的杂质含量的降低率有限,铝含量一般可降至1.6%,最多只能降至1.2%, 碳含量0.2%,只能生产部分品牌的产品。
本发明的目的是要克服上述几种方法的不足,提供一种高品质硅铁的生产方法,该方法实用于系列高品质硅铁的生产。
本发明的高品质硅铁的生产方法包括如下步骤:(1)筛选原料硅石、还原剂、钢悄或/硅钢屑,硅石为石英石或白硅石、黑硅石、还原剂为冶金焦和气煤焦,或者兰炭和气煤焦,兰炭和石油焦及木块、根据各种原料的准确成份含量和所要生产的品种对所有元素成份要求,按公知技术进行计算各原料量、配料混合后填入矿热炉内按通常冶炼硅铁合金的条件和操作进行冶炼。
硅铁冶炼
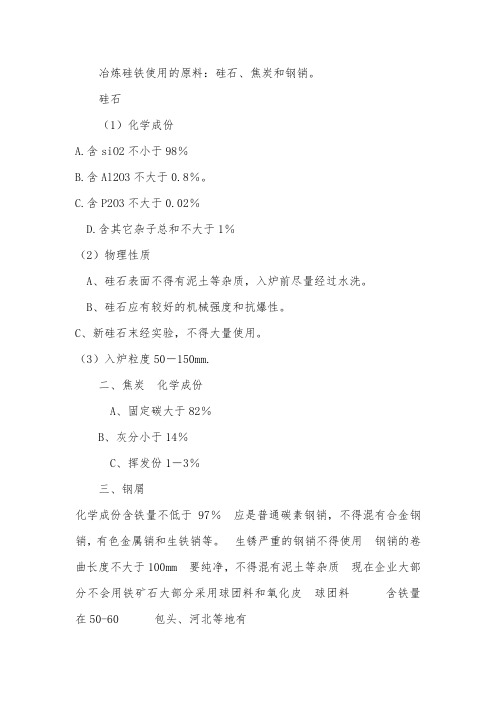
冶炼硅铁使用的原料:硅石、焦炭和钢销。
硅石(1)化学成份A.含siO2不小于98%B.含Al2O3不大于0.8%。
C.含P2O3不大于0.02%D.含其它杂子总和不大于1%(2)物理性质A、硅石表面不得有泥土等杂质,入炉前尽量经过水洗。
B、硅石应有较好的机械强度和抗爆性。
C、新硅石末经实验,不得大量使用。
(3)入炉粒度50-150mm.二、焦炭化学成份A、固定碳大于82%B、灰分小于14%C、挥发份1-3%三、钢屑化学成份含铁量不低于97%应是普通碳素钢销,不得混有合金钢销,有色金属销和生铁销等。
生锈严重的钢销不得使用钢销的卷曲长度不大于100mm 要纯净,不得混有泥土等杂质现在企业大部分不会用铁矿石大部分采用球团料和氧化皮球团料含铁量在50-60 包头、河北等地有氧化皮含铁量在65-72 包头、河北、山西等地有铁矿石生产原料生产工艺(如下)冷压块简单工艺过程破碎粘结铁矿石筛分干燥混合筛分压块入炉四、铁矿石工业品位对于含铁量较低或含铁量虽高但有害杂质含量超过规定要求的矿石或含伴生有益组分的铁矿石,均需进行选矿处理,选出的铁精粉经配料烧结或球团处理后才能入炉使用。
需经选矿处理的铁矿石要求:磁铁矿石TFe≥25%,mFe≥20%;赤铁矿石TFe≥28%~30%;菱铁矿石TFe≥25%;褐铁矿石TFe≥30%。
对需选矿石工业类型划分,通常以单一弱磁选工艺流程为基础,采用磁性铁占有率来划分。
根据我国矿山生产经验,其一般标准是:矿石类型mFe/TFe(%)单一弱磁选矿石≥65其他流程选矿石<65对磁铁矿石、赤铁矿石也可采用另一种划分标准:mFe/TFe≥85磁铁矿石mFe/TFe85~15混合矿石mFe/TFe≤15赤铁矿石。
硅铁生产工艺ppt课件

硅铁化学成分:Si Fe Al Ca P S C 硅铁物理性质: 熔点:72#-80#硅铁熔点1290℃-1360℃ 75#硅铁熔点1300℃ 硅铁的密度取决于硅铁的含硅量,它的密度随合金中含硅量的增加而
精品课件
6
兰炭:
1)、固定碳含量≥82%
2)、粒度:小料8-18mm 筛下物:≤5%
3)、水份:≤16.0%
.
4) 、挥发份含量:小料≤8.0% 5)、灰份含量:≤8.0%
精品课件
7
电极糊(焙烧电极):
1)、灰份:≤6.0%
2)、挥发份:夏季:11.2≤挥发份≤12.5
冬季:11.0≤挥发份≤12.3
2200mm
炉嘴:长1600-1700mm,高度:650mm;宽度: 670mm
电极直径:ø1050mm,电极分布圆直径:ø2500士100
冷却循环水系统
电极把持器系统
电极升降系统
除尘系统
出铁系统
精品课件
11
感谢亲观看此幻灯片,此课件部分内容来源于网络, 如有侵权请及时联系我们删除,谢谢配合!
一次电流:250-270A,三相电流保持平衡;入炉深度:15001800mm;均匀加料,保持料面透气性良好;正确处理刺火、 大塌料现象。
3、炉前操作
深堵眼;勤清流槽,处理假口;控制铁钎使用量;保证铁水包烘 烤彻底,锭模干净、干燥
4、综合操作要求
精品课件
10
热矿炉主要设备
炉体:
炉壳:外径7600mm,高度4200mm;炉膛深度:
硅铁

构成
铁和硅组成的铁合金(以硅石、钢、焦碳为原料,经过1500-1800度高温还原的硅熔于铁液中,形成硅铁合 金)。是冶炼行业重要的合金品种。
硅铁按硅及其杂质含量,分为21个牌号,其化学成分如下表:(根据GB/T 2272-2009)
用途
(1)在炼钢工业中用作脱氧剂和合金剂。为了获得化学成分合格的钢和保证钢的质量,在炼钢的最后阶段必 须进行脱氧,硅和氧之间的化学亲和力很大,因而硅铁是炼钢较强的脱氧剂用于沉淀和扩散脱氧。在钢中添加一 定数量的硅,能显著的提高钢的强度、硬度和弹性,因而在冶炼结构钢(含硅0.40-1.75%)、工具钢(含 SiO.30-1.8%)、弹簧钢(含SiO.40-2.8%)和变压器用硅钢(含硅2.81-4.8%)时,也把硅铁作为合金剂使用。 同时改善夹杂物形态减少钢液中气体元素含量,是提高钢质量、降低成本、节约用铁的有效新技术。特别适用于 连铸钢水脱氧要求,实践证明,硅铁不仅满足炼钢脱氧要求,还具有脱硫性能且具有比重大,穿透力强等优点。
硅铁
铁和硅组5 冶炼
目录
02 构成 04 标准 06 应用
硅铁就是铁和硅组成的铁合金。硅铁是以焦炭、钢屑、石英(或硅石)为原料,用电炉冶炼制成的铁硅合金。 由于硅和氧很容易化合成二氧化硅,所以硅铁常用于炼钢时作脱氧剂,同时由于SiO2生成时放出大量的热,在脱 氧的同时,对提高钢水温度也是有利的。同时,硅铁还可作为合金元素加入剂,广泛应用于低合金结构钢、弹簧 钢、轴承钢、耐热钢及电工硅钢之中,硅铁在铁合金生产及化学工业中,常用作还原剂。
GB/T 3650铁合金验收、包装、储运、标志和质量证明书的一般规定 GB/T 4010铁合金化学分析用试样的采取和制备(GB/T 4010-1994,neq ISO 4552:1987) GB/T 4333.1硅铁化学分析方法高氯酸脱水重量法测定硅量 GB/T 4333.2硅铁化学分析方法铋磷钼蓝光度法测定磷量 GB/T 4333.3硅铁化学分析方法铋磷钼蓝光度法测定磷量 GB/T 4333.4硅铁化学分析方法铬天青S光度法、EDTA测定法和火焰原子吸收光谱法(GB/T 4333.42007,ISO 4139,1987 ) GB/T 4333.6硅铁化学分析方法二苯基碳酰二肼光度法测定铬量 GB/T 4333.
硅铁精炼
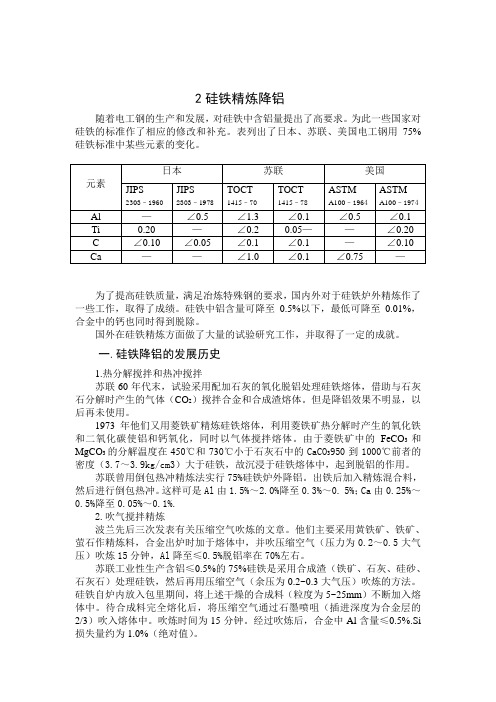
2硅铁精炼降铝随着电工钢的生产和发展,对硅铁中含铝量提出了高要求。
为此一些国家对硅铁的标准作了相应的修改和补充。
表列出了日本、苏联、美国电工钢用75%硅铁标准中某些元素的变化。
为了提高硅铁质量,满足冶炼特殊钢的要求,国内外对于硅铁炉外精炼作了一些工作,取得了成绩。
硅铁中铝含量可降至0.5%以下,最低可降至0.01%,合金中的钙也同时得到脱除。
国外在硅铁精炼方面做了大量的试验研究工作,并取得了一定的成就。
一.硅铁降铝的发展历史1.热分解搅拌和热冲搅拌苏联60年代末,试验采用配加石灰的氧化脱铝处理硅铁熔体,借助与石灰石分解时产生的气体(CO2)搅拌合金和合成渣熔体。
但是降铝效果不明显,以后再未使用。
1973年他们又用菱铁矿精炼硅铁熔体,利用菱铁矿热分解时产生的氧化铁和二氧化碳使铝和钙氧化,同时以气体搅拌熔体。
由于菱铁矿中的FeCO3和MgCO3的分解温度在450℃和730℃小于石灰石中的CaCO3950到1000℃前者的密度(3.7~3.9kg/cm3)大于硅铁,故沉浸于硅铁熔体中,起到脱铝的作用。
苏联曾用倒包热冲精炼法实行75%硅铁炉外降铝。
出铁后加入精炼混合料,然后进行倒包热冲。
这样可是Al由1.5%~2.0%降至0.3%~0. 5%;Ca由0.25%~0.5%降至0.05%~0.1%.2.吹气搅拌精炼波兰先后三次发表有关压缩空气吹炼的文章。
他们主要采用黄铁矿、铁矿、萤石作精炼料,合金出炉时加于熔体中,并吹压缩空气(压力为0.2~0.5大气压)吹炼15分钟,Al降至≤0.5%脱铝率在70%左右。
苏联工业性生产含铝≤0.5%的75%硅铁是采用合成渣(铁矿、石灰、硅砂、石灰石)处理硅铁,然后再用压缩空气(余压为0.2~0.3大气压)吹炼的方法。
硅铁自炉内放入包里期间,将上述干燥的合成料(粒度为5~25mm)不断加入熔体中。
待合成料完全熔化后,将压缩空气通过石墨喷咀(插进深度为合金层的2/3)吹入熔体中。
硅铁冶炼原理
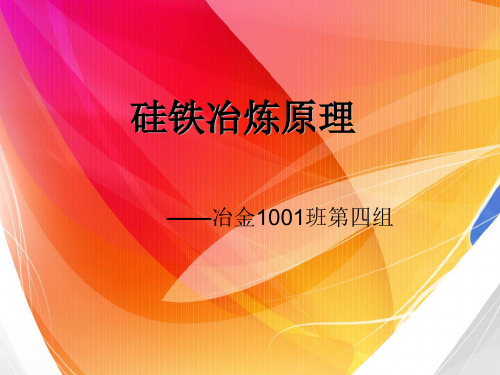
实际上SiO2的还原反应很多,我们只看 主要反应。炉内主要反应区简单概括为SiC 的生成区及其分解区,如下页图:
(1)SiC的生成区
• SiC的生成温度范围在1000~2100K。在此 区域内也同时生成Si。此区域内的主要反 应是SiO的分解和吸附,并生成SiC。
• 电极插入浅时,高温区上移,炉底温度低, 熔渣排出少,假炉底厚,导致出铁口上移, 电极上抬,出铁困难,炉况恶化。一定的假 炉底对护炉有一定好处。
分析可知
• 炉内预热区和烧结区为SiC的形成区 • 坩埚区为SiC的分解区
避免形成大块的SiC 为使SiC连续形成和分解,减少SiO的挥 发损失必须有: ①电极深而稳插炉料内,高温区在底部, 炉料上层冷料层要厚; ②炉料透气性要好,炉气均匀溢出; ③SiC形成和分解时间要短,避免形成大 块SiC,保证炉温分布不受破坏。
Si02(1)+2SiC(s)=3Si(l)+2CO(g) △GT0=937006-438.19T(J/mol) T开=2138K
上述二式的综合式为: 3SiO2(1)+2SiC(s) =Si(1)+4SiO(g)+2CO(g) △GT0=1992636-920.89T(J/mol) T开=2164K
•气态的SiO与SiC相互作用,其反应式是:
SiO(g)+SiC(s)=2Si(1)+CO
△GT0=306892-147.63T(J/mol) T开=2079K
• SiC的分解和SiO及Si的生成是同时进 行的。这些反应进行时需要消耗大量 的热能,而且当温度大于2100K时,才 能顺利进行。
• 没有参加反应的SiO离开炉料,在大气 中氧化成Si02。