几类硬质薄膜的摩擦磨损性能测试
摩擦磨损测试方法

摩擦磨损测试方法摩擦磨损测试是指对材料在摩擦过程中的磨损性能进行评价和测试的方法。
通过摩擦磨损测试,可以了解材料的耐磨性能,为材料的选择和设计提供依据。
本文将介绍几种常见的摩擦磨损测试方法。
1. 磨损试验机法磨损试验机是一种用于模拟材料在实际工作条件下受到的摩擦磨损的设备。
常见的磨损试验机有球盘摩擦试验机、滚筒式摩擦试验机等。
在磨损试验机上进行测试时,将待测试材料与磨损试样接触,并施加一定的载荷和摩擦力,通过测量试样的磨损量来评估材料的耐磨性能。
2. 微观磨损测试法微观磨损测试法主要通过显微镜观察材料的磨损情况来评估其耐磨性能。
常用的微观磨损测试方法有扫描电子显微镜(SEM)观察法、显微硬度计观察法等。
这些方法可以观察到材料表面的微观磨损形貌,从而判断材料的抗磨损性能。
3. 滑动磨损测试法滑动磨损测试法是将待测试材料与磨损试样相对滑动,通过测量试样的磨损量来评估材料的耐磨性能。
常见的滑动磨损测试方法有平板摩擦试验法、圆盘摩擦试验法等。
在滑动磨损测试中,可以调整试样的载荷、速度和试样间的压力等参数,以模拟不同工况下的摩擦磨损情况。
4. 模拟实际工况测试法模拟实际工况测试法是将待测试材料置于模拟实际工况的环境中,通过观察材料在实际工况下的磨损情况来评估其耐磨性能。
常见的模拟实际工况测试方法有湿磨损测试法、高温磨损测试法等。
这些方法能够更真实地模拟材料在实际使用中受到的摩擦磨损,对于评估材料的实际耐磨性能具有重要意义。
5. 材料表面改性测试法材料表面改性测试法是通过对材料表面进行改性处理,以提高材料的抗磨损性能。
常见的表面改性方法有涂层处理、表面渗碳处理等。
通过对改性前后材料的摩擦磨损性能进行测试,可以评估改性方法的有效性,并指导材料的改进和设计。
摩擦磨损测试方法多种多样,每种方法都有其独特的优势和适用范围。
在进行摩擦磨损测试时,应根据具体的材料和应用场景选择合适的测试方法,以确保测试结果的准确性和可靠性。
TiN,TiC和Ti(C,N)涂层的性能及影响因素研究
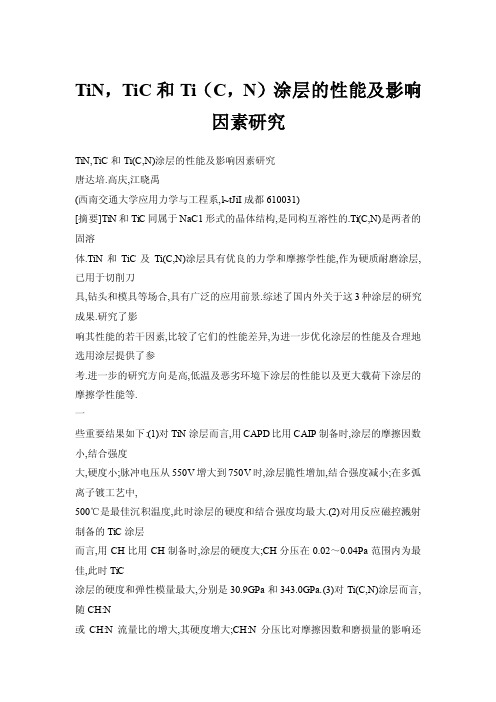
TiN,TiC和Ti(C,N)涂层的性能及影响因素研究TiN,TiC和Ti(C,N)涂层的性能及影响因素研究唐达培.高庆,江晓禹(西南交通大学应用力学与工程系,l~tJiI成都610031)[摘要]TiN和TiC同属于NaC1形式的晶体结构,是同构互溶性的.Ti(C,N)是两者的固溶体.TiN和TiC及Ti(C,N)涂层具有优良的力学和摩擦学性能,作为硬质耐磨涂层,已用于切削刀具,钻头和模具等场合,具有广泛的应用前景.综述了国内外关于这3种涂层的研究成果.研究了影响其性能的若干因素,比较了它们的性能差异,为进一步优化涂层的性能及合理地选用涂层提供了参考.进一步的研究方向是高,低温及恶劣环境下涂层的性能以及更大载荷下涂层的摩擦学性能等.一些重要结果如下:(1)对TiN涂层而言,用CAPD比用CAIP制备时,涂层的摩擦因数小,结合强度大,硬度小;脉冲电压从550V增大到750V时,涂层脆性增加,结合强度减小;在多弧离子镀工艺中,500℃是最佳沉积温度,此时涂层的硬度和结合强度均最大.(2)对用反应磁控溅射制备的TiC涂层而言,用CH比用CH制备时,涂层的硬度大;CH分压在0.02~0.04Pa范围内为最佳,此时TiC涂层的硬度和弹性模量最大,分别是30.9GPa和343.0GPa.(3)对Ti(C,N)涂层而言,随CH:N或CH:N流量比的增大,其硬度增大;CH:N分压比对摩擦因数和磨损量的影响还与载荷的大小有关;TiCN涂层的硬度和弹性模量随值而变化,当为0.6左右时,硬度取最大值45GPa,当值为0.43左右时,弹性模量取最大值630GPa.[关键词]涂层;TiN;TiC;Ti(C,N);性能;影响因素;硬度;摩擦因数[中图分类号]TG174[文献标识码]A[文章编号]1001—1560(2005)03—0042—05 0引言TiN涂层具有硬度高,韧性好,结合强度高,摩擦因数小和化学性能稳定等优点,作为涂层用于加工刀具大大提高了其使用寿命和被加工产品的质量¨.但是,随着机械制造业要求的提高,切削刀具存在高温抗氧化性不足,硬度不够高等缺点.在各种新的涂层材料中,TiC涂层具有较好的综合性能,并且硬度比TiN更高,已成为主要选择之一.20世纪90年代通过多组元涂层,多层涂层,复合涂层提高了TiN涂层工模具的性能,取得了相当大的进展.TiN,TiC同属于NaC1形式的晶体结构,两者的晶格常数相差不大,是同构互溶性的.Ti(C,N)是TiN和TiC的固溶体,具有两者的特性和优点,Ti(C,N)与TiN相比有更好的抗粘着磨损和抗磨粒磨损性能,更低的摩擦因数,可以进一步提高切削刀具的生产效率和使用寿命.Ti(C,N)涂层的基本性能如形貌,结构和[收稿日期]2004—10—26[基金项目]教育部优秀青年教师基金成分在20世纪80年代已开始研究,mj.迄今为止,对于TiN,TiC及Ti(C,N)涂层的性能进行了大量研究,发现涂层的组分,厚度及工艺条件(如沉积温度,速度,压力等)对涂层性能有较大的影响,涂层的使用工况(如温度,速度,气氛,载荷等)对涂层摩擦磨损等性能有较大的影响.本工作对3种涂层的性能研究进行了评述,重点研究影响其性能的各种因素,同时比较了3种涂层性能的差异, 为涂层的合理选用和设计提供了依据,最后提出了进一步的研究方向.1影响涂层性能的因素1,1制备工艺用于制备TiN,TiC及Ti(C,N)涂层的工艺有物理气相沉积,化学气相沉积及各种复合工艺,如等离子体化学气相沉积,射频溅射沉积,离子束增强沉积,空心阴极离子镀,阴极电弧等离子沉积,阴极电弧离子镀,直流反应磁控溅射等.工艺不同,涂层的性能也可能不同.用CAPD比用CAIP制备TiN,TiC和Ti(C,N)涂层的性能及影响因素研究的TiN涂层的摩擦因数要低¨,可是若TiN涂层下有Ti作为夹层时,这2种工艺制备的TiN涂层的摩擦因数无明显差异;用CAPD制备的TiN涂层的磨损率随滑动速度增加而增加,而用CAIP制备的TiN涂层则有相反的结论;用CAPD比用CAIP 制备的TiN涂层的结合强度要大,但硬度要小. 1.2择优取向TiN涂层因制备的方法不同,取向也有所不同,如PVD方法制备的TiN涂层取向一般为(111),(200),而CVD制备的TiN涂层为(200), (220)取向.涂层择优取向对其质量和性能有影响,具有强烈TiN(111)择优取向的涂层表面光亮,硬度高,耐磨性好,与基体有较高的结合强度¨.对TiC涂层而言,用CH气体沉积时择优取向为(111),而用C:H:气体沉积时却朝着(111)和(220)取向竞争生长,TiC涂层的高硬度取决于TiC(220)峰的峰度.Ti(C,N)涂层的取向主要是(111),(200), (220).由于择优取向本身也受多种因素(基体温度,沉积速度,气体组分与压强以及外加电压等)的影响.一般来讲,提高温度有利于获得好的择优取向,而沉积速率越大,晶粒中的择优取向愈不明显. 因此,为了获得好的择优取向,基体温度和沉积速率之间应有一个最佳配合.气体组分与压强会影响原子在基体表面上的粘附系数和表面迁移率,而外加电压也会影响到达基体表面的粒子行为,因为它们都影响择优取向的类型及程度.1.3沉积电压,气压,气体配比,化学组分提高沉积电压可以细化TiN涂层的柱状晶结构,增加TiN涂层的显微硬度和沉积速率.脉冲偏压幅值在500~1700V,脉宽比在125~25的范围内,沉积温度低于250℃时膜层组织主要由Ti,N和TiN相构成,随脉冲偏压幅值和脉宽比的增大,晶面的择优取向由Ti:N(200)向(002)转变,柱状晶生长减弱;膜层具有较高的显微硬度和耐磨性,但在过高的脉冲偏压和脉宽比的沉积条件下,膜层性能有下降的趋势¨.随脉冲电压在550~750V之间逐渐增大,TiN晶粒增大,膜层脆性增加,沉积速率提高, 但膜基结合强度下降;在650V以下膜基界面有一伪扩散层出现,超过650V后伪扩散层消失,这是改善膜基结合强度的关键因素Ⅲ.TiC的反应溅射可采用各种含碳气体,如甲烷,乙炔等.高活性的乙炔气体可得到高硬度的TiC薄膜,但工艺和质量的重复性较差.甲烷等化学稳定的碳源气体能够保证工艺过程的良好控制,但常常达不到硬质膜所必需的化学计量比,致使镀层性能达不到要求.在这些沉积方法中,反应气体的分压将对所形成薄膜的相组成,微结构和力学性能产生重要作用.低的甲烷分压下,制备的薄膜样品中含有钛相,薄膜的硬度和弹性模量较低; 甲烷分压提高到0.02~0.04Pa时,薄膜内形成晶粒细小的单相TiC,并获得最高的硬度30.9GPa和弹性模量343GPa;进一步提高甲烷分压,薄膜呈现非晶态,其硬度和弹性模量亦随之降低¨引.在用PCVD法沉积TiC膜的过程中,TiC1和CH的流量是重要的控制参数,在一定的范围内可以提高TiC膜的硬度和沉积速率,但过多的TiC1和CH 会给TiC膜的结合强度带来不利的影响,氩气虽然可以提高TiC膜的沉积速率,但同时也降低了膜基的结合强度.制备Ti(C,N)涂层时,反应气体通常用CH与N:按一定比例混合,或者C:H:与N:按一定比例混合,其混合比例对Ti(C,N)涂层性能有一定的影响.随CH:N:或C:H::N:流量比的增大,膜的硬度增大,膜表面的针孔变小变少,膜呈现较强的(111)择优取向,且随流量比的增大而下降,(220)取向有轻微上升¨.CH:N:分压比对Ti(C,N)涂层性能也有影响,随CH:N:分压比的增加,粗糙度增加,即从TiN到TiC,粗糙度变大,TiC涂层的粗糙度最大;CH:N:分压比对摩擦因数和磨损量的影响还与载荷有关,在低载荷(10 N)下,分压比对摩擦因数和磨损量的影响很小,且摩擦因数和磨损量均很低,但在中等载荷(15N)或较高载荷(25N)下,摩擦因数和磨损量随CH-N:分压比的增加而减小,尤其是当CH-N:分压比在0.8:1.0以上时,Ti(C,N)涂层的摩擦因数都较低,当CH-N分压比为1:0时摩擦因数和磨损量最低,并且摩擦因数受载荷的影响最小.Ti(C, N)涂层中C,N组分对涂层性能的影响较大,在WC一6%Co基体上电弧沉积了TiCxN.一x(0≤≤1)涂层,图1为TiCN一中值对硬度,弹性模量的影响曲线,从图1可知,在z≤0.6时,TiCN一的硬度随值增大而增大,在I>0.6时,TiN,TiC和Ti(C,N)涂层的性能及影响因素研究硬度随值增大而减小,在为0.6附近硬度取最大值45GPa,比TiN(即为0时)的硬度28GPa和TiC(即为1时)的硬度36GPa都大;弹性模量在为0.6时约为610GPa,在为0或1时,弹性模量分别约为610GPa和540GPa,在约为0.43时,出现最大值630GPa.凸_图1电弧沉积的TiCN一涂层中值对硬度和弹性模量的影响日据翅案1.4温度在气相沉积过程中,沉积温度是一个重要的工艺参数.如果沉积温度超过淬硬钢的回火温度,沉积后淬硬钢就会软化,若低于某一沉积温度,涂层的性能就会受到影响.研究不同沉积温度下TiN 涂层的性能,对确定最佳沉积温度,提高TiN涂层性能是很有意义的.孙伟等研究了多弧离子镀沉积温度对TiN涂层性能的影响,得出500℃附近是最佳沉积温度,当低于500℃时,TiN涂层的硬度和结合强度均随沉积温度升高而增大,超过500℃后,硬度和结合力则迅速减小,对涂层的性能不利.赵程等采用先沉积后热处理'J,发现对PCVD.TiN涂层进行热处理时,随热处理温度的提高,涂层的结晶度得到大幅度的改善,使其显微结构向有利于提高涂层性能的方向发展,热处理温度对涂层的硬度有较大影响,但在900℃时,PCVD. TiN涂层的显微硬度有一个最低值.宋人娟对多弧离于镀TiN低温涂层进行了研究,得出低温涂层硬度在2000HV以上,比高温涂层的硬度低, 但低温TiN涂层具有低的摩擦因数,高的耐磨性和膜基结合强度.对PVD硬涂层来说,热稳定性是重要的影响因素.在不锈钢上用PVD沉积了TiN涂层,研究了热处理对其摩擦特性的影响,结果表明,TiN的硬度和摩擦因数在450℃前基本无变化.Tamu. ra等的研究表明,Ti(C,N)涂层经500℃焖火后,仍保持其硬度,而TiC涂层经400℃焖火后其硬度快速下降.对以热作模具钢3Cr2W8V为基体的气相沉积的Ti(c,N)和TiN硬质镀层的热磨损性能进行了试验研究J,结果表明,Ti(C,N)和TiN镀层都具有良好的高温耐磨性,在850℃以上的高温条件下,几种有镀层试样的热冲击磨损量都明显地比无镀层3Cr2W8V试样的磨损量低;镀层的高温软化和氧化都不明显;只有当模基界面结合不良或模基体系的承载能力不足时,才会发生镀层的剥落或碎裂.1.5涂层厚度,层数,涂层顺序TiN涂层厚度对涂层结合强度有影响,若涂层太薄(≤1.5m),在外力作用下涂层容易变形剥落,若涂层太厚(I>4.7m),涂层应力增加,其抗变形,抗剥落能力也会下降,涂层厚度在2.5—3.5 m为最佳.对单层和双层涂层及其厚度对涂层性能作了研究,结果表明,对单层TiN涂层来说,其结合强度随厚度的增加而减小,但对有下层Ti膜存在的Ti/TiN双层涂层来说,当上层的TiN 涂层的厚度从1m变到5m时,未见结合强度减小,然而极厚的下层Ti涂层也会引起上层TiN 结合强度的减小;在较高的滑动速度下,增加下层Ti膜的厚度会导致试样的硬度变小,增加上层TiN 膜的厚度会导致试样的硬度变大,上下两层厚度的变化对试样的摩擦因数影响很有限.加J.用Ti(C,N)作为上层涂层比用TiN作为上层涂层时,其厚度对结合强度的影响,前者要小;Ti (C,N)涂层厚度对其硬度的影响极大,当下层Ti厚度不变时,微硬度随上层Ti(C,N)厚度的增加而增加,当上层Ti(C,N)厚度不变时,微硬度随下层Ti厚度的增加而减小.涂层的厚度及层数主要取决于工况条件,不一定是层数越多性能愈好,膜层过厚会处于高的应力状态,涂层变脆,使其寿命缩短,通常单一硬质PVD或CVD涂层的厚度在1—10m之间,多层涂层的单层厚度一般不超过5m.研究表明,以TiN为顶层的Ti/Ti(C,N)/TiN多层膜,其自身的硬度及与基体的复合硬度均比以Ti(C,N)为顶层的Ti/,TiN/Ti(C,N)多层膜的高;但前者的临界摩擦力比后者小;前者的微凸体的数量随涂层厚度的增加而增加,而后者的微凸体的数量随涂层厚度的增加而减少.1.6基体涂层使用性能的好坏不仅取决于涂层本身的性能,而且还和基体材料的性能有关,尤其是基体TiN.TiC和Ti(C,N)涂层的性能及影响因素研究材料的硬度,只有建立在比较坚硬的基体材料上, 硬质涂层才能发挥出其优越的耐磨性能.基体材料硬度不同,则TiN涂层与基体的结合强度亦不同,基体硬度越大,TiN涂层与基体的结合越好圳,在实际应用中,要尽量使基体材料在沉积温度下保持高的硬度以提高涂层质量.基体表面粗糙度越小,涂层与基体的结合强度越高,基体表面粗糙度以抛光为佳.同样组分的TiCN涂层,在基体Si(100)上比在基体Ti-0.2Pd上其硬度和弹性模量都要高.高速钢W.Mo-V+si上的TiN和Ti(C,N)涂层比普通的烧结钢ASP23, ASP30上的涂层的结合性能要好.1.7载荷,滑动速度法向荷载对摩擦和磨损都有影响,随着法向荷载的增大,摩擦因数和磨损量都相应增大,其增大的幅度随碳含量的增多而减小L2.滑动速度的增加会导致摩擦因数和磨损率的减小.2展望研究更大载荷范围内涂层的摩擦,磨损及力学性能;进一步研究高/低温,恶劣环境下涂层的性能;涂层的影响因素较多,且很复杂,许多因素又存在相互影响,需系统地研究涂层的结构,界面特性及沉积工艺,参数对涂层的力学性能及摩擦学性能等的影响,为设计性能优良的涂层提供数据和理论依据;从微观方面上研究涂层的摩擦学特性及摩擦磨损机理,注重摩擦学特性与功能性的有机结合; TiN,TiC及Ti(C,N)3种涂层作为硬质耐磨涂层已显示出其优越性,应在保持其优良的摩擦学,力学性能的基础上,进一步研制与其他涂层的复合,扩大其应用范围;开发新的涂层试验研究方法,为涂层性能检测和微观形貌,结构及成分分析提供有力的支持;进一步开发新的涂层制备工艺和设备,以便更好地控制涂层的结构和组成.目前评价涂层摩擦磨损性能的好坏大多是做对比性试验研究,缺乏统一的标准.因此,对现象, 数据进行深人分析,从微观角度研究其基本的理论模型,为涂层的摩擦磨损建立起总体的,普遍适用的理论已成为一个亟待解决的课题.[参考文献][1]DiserensM,PatscheiderJ,LevyF.MechanicalProp—ertiesandOxidationResistanceofNanocompositeTiN.穗SiNxPhysica1.V apor.DepositedThinFilms[J].Sur- faceandCoatingTechnology,1990(120/121):158~165.SproulWD.TurningTestsofHighRateReactively Sputter.CoatedT.15HSSInserts[J].Surfaceand CoatingTechnology,1987,3(133):1~4. GroningP,NowakS,SchallerE,eta1.InitialStages ofTitaniumCarbideGrowthbyPlasma?SputterDeposi? tiononStainlessSteel[J].AppliedSurfaceScience, 1993(68):327~333.KnotekO,LoefflerF,KraemerG.ProcessandAdvan? tageofMuhicomponentandMuhiplayerPVDCoatings [J].SurfaceandCoatingTechnology,1993,59(14):l~3.HolleckH,SchierV.MuhilayerPVDCoatingsfor WearProtection[J].SurfaceandCoatingTechnology, 1993(328):76~77.胡树兵,崔岜.物理气相沉积TiN多元涂层和多层涂层的研究进展[J].材料保护,2001,34(10): 24~27.ErtuerkE,KnotekO,BergrnerW,eta1.Ti(C,N) CoatingsUsingtheArcProcess[J].SurfaceandCoat? ingTechnology,1991,46(1):39.GhoshSK,KohlerMS.StudyoftheRelativeWear andAbrasionResistanceofTi(C,N)andCoatings [J].SurfaceandCoatingTechnology,1992,54—55(1~3):466.ChengDJ,SunWP,HonMH.TheMorphologyandStructureofChemicalV aporDepositedTi(C,N) Coating[J].ThinSolidFilms,1987,146(1):45. GabrielHM,KloosKH.MorphologyandStructure ofIon?PlatedTiN,TiCandTi(C,N)Coating[J].Thin SolidFilms,1984,1I8(3):243.Y eongYG,JenFL.TheTribologicalCharacteristicsof TitaniumNitrideCoatings,PartII:ComparisonsofTwo DepositionPmcess[J].Wear,1996(194):22~29.宫秀敏,叶卫平,孙伟,等.TiN涂层中的择优取向及其对涂层性能的影响[J].机械工程材料, 2000,24(1):20~22.辛煜,程珊华,宁兆元,等.不同沉积气体对多弧法制备TiC膜的影响[J].功能材料,2000,31(3): 33l~332.辛煜,范叔平,甘肇强,等.多弧法沉积Ti(C,N)膜中的CN相[J].功能材料,1997,28(6):612~614.赵程,彭红瑞,谢广文,等.沉积电压对辅助加热PCVD—TiN涂层的影响[J].青岛化工,2000,2l(2).1J]J]J]J]J]J]J]J]J]J]J]J]J]J23456789m¨rLrLrLrLrLrLrLrLrLrLrLrLrLrL[16][17][18][19][20][21][22][23][25][26][27][28][29][30][31]TiN,TiC和Ti(C,N)涂层的性能及影响因素研究曾鹏,胡社军,谢光荣,等.脉冲偏压对真空电弧沉积TiN薄膜组织与性能的影响[J].材料热处理,2001,22(3):62~66.马胜利,李雁淮,徐可为.脉冲电压幅值对等离子化学气相沉积TiN薄膜膜基结合行为的影响[J]. 金属,2000,36(1):77~80.闻立时,黄荣芳.离子镀硬质膜技术的最新进展和展望[J].真空,2000(1):1~11.邵楠,梅芳华,董云杉,等.反应溅射TiC薄膜的微结构及力学性能[J].表面技术,2003,32(3):10~l2.赵程,彭红瑞,李世直.碳化钛膜的制备和应用研究[J].表面技术,1998,27(2):40~42.辛煜,范叔平,吴建新,等.c:H/N:流量比对沉积Ti(C,N)薄膜影响的研究[J].真空科学与技术,1997,17(5):351~354.HuaugSW,NgMW,SamandiM,eta1.Tribological BehaviourandMicrostructureofTiCxN1一xCoatingsDepositedbyFilteredArc[J].Wear,2002(252):566579.SennaLF,AcheteCA,HirschT,eta1.Structur—al,Chemical,MechanicalandCorrosionResistance CharacterizationofTiCNCoatingsPreparedbyMagne—tronSputtering[J].SurfaceandCoatingTechnology, 1997(94~95):390—397.马胜利,马大衍,王昕,等.脉冲直流等离子体辅助化学气相沉积TiN和TiCN薄膜摩擦磨损特性研究[J].摩擦学,2003,23(3):179~182.KarlssonL,HultmanL,JohanssonMP,eta1.Growth, MicrostructureandMechanicalPropertiesofArcEvapo? ratedTiCxNl—x(o≤x≤1)Films[J].Surfaceand CoatingTechnology,2000(126):1~l4.孙伟,宫秀敏,叶卫平,等.多弧离子镀沉积温度对TiN涂层性能的影响[J].电加工与模具,2000 (5):26~28.赵程,彭红瑞,谢广文,等.离子体化学气相沉积TiN涂层的后热处理技术研究[J].真空科学与技术,2000,20(5):366~369.宋人娟.多弧离子镀TiN低温涂层的研究[J].金属热处理,1994(6):17~20.McConnellML,DowlingDP,DonnelyN,eta1. TheEffectofThermalTreatmentsontheTribological PropertiesofPVDHardCoatings[J].Surfaceand CoatingTechnology,1999(116—119):1133—1137.李文梅,何家文.气相沉积TiN和Ti(C,N)镀层的热磨损性能[J].摩擦学,1994(3):5~8.孙伟,宫秀敏,叶卫平,等.多弧离子镀TiN涂层结[32][33][34][35][36][37][38][39][40]合力的影响因素[J].材料保护,2000,33(8):31~32. parisonoftheTribological CharacteristicsofTitaniumNitrideandTitaniumCar—bonitrideCoatingFilms[J].SurfaceandCoating Technology,1996(85):146~155.张绪寿,余来贵,陈建敏.表面工程摩擦学研究进展[J].摩擦学,2000,20(2):156~160.韩修训,阎逢元,阎鹏勋,等.多层涂层的摩擦学研究进展[J].机械工程材料,2002,26(5):1~5. WeiCH,LinJF,JiaugTH,AiCF.Tribological CharacteristicsofTitaniumNitrideandTitaniumCarbo—nitrideMuhiplayerFilms,PartII:TheEffectofCoating SequenceonTribologicalProperties[J].ThinSolid Films,2001(381)94~103.孙伟,宫秀敏,叶卫平,等.基体材料硬度和化学成分对TiN涂层结合力的影响[J].金属热处理, 2000(8):13~14.FornA,PicasJA,FuentesGG,eta1.Mechanical andTribologicalPropertiesofTiCxNl—xWearResistantCoatings[J].InternationalJournalofRefractoryMetals&HardMaterials,2001(19):507~513. DobrzanskiLA,AdamiakM.StructureandProperties oftheTiNandTi(C,N)CoatingsDepositedinthePVD ProcessonHigh—SpeedSteels[J].JournalofMaterials ProcessingTechnology,2003(133):50—62. GuuYY,parisonoftheTriblological CharacteristicsofTitaniumNitrideandTitaniumCarbo. nitrideCoatingFilms[J].SurfaceandCoatingTech—nology,1996(85):146~155.GuuYY.LinJF.AiCF.TheTribologicalCharac? teristicsofTitaniumNitrideCoatings.PartI.Coating ThicknessEffects[J].Wear,1996(194):12~21.[编辑:王宇]本技术相关链接:1.《中国表面工程》,2004(2):18.2.《电镀与精饰》,2004(2):31.江苏兴化冶理水污染成果显着水乡江苏省兴化市打响了一场以农村水污染治理为重点的"环保整治战".2004年以来,全市共整治乡镇企业474家,关停4l家,投入整治资金1.03亿元.这是兴化历史上投入环保资金最多的一年.兴化市环保局局长赵诗坤介绍,去年,某乡镇经过艰苦谈判,引来了一笔2200多万元的电镀项目.但我们发现这个项目对河流污染比较大,随后向市领导提出否定的意见.市领导只回复了一句话,"招商引资可以无门槛,但环境保护必须有关口."(摘自中国表面工程信息网)。
GB 10006与ASTM D 1894塑料薄膜摩擦系数测定方法的比较

GB 10006与ASTM D 1894塑料薄膜摩擦系数测定方法的比较摘要:摩擦系数是造成自动包装线薄膜拉断、打滑等问题的主要原因,这与薄膜生产过程中润滑剂、抗粘连剂等添加剂的使用,以及生产线高温环境有着很大关系。
因此薄膜摩擦系数的测试变得愈加重要。
根据GB 10006与ASTM D 1894两项标准,介绍了塑料薄膜摩擦系数的测定方法及两标准的异同,对于选择相应测试仪器也提出了几点建议。
关键词:薄膜、摩擦系数、GB 10006、ASTM D 1894目前,薄膜、复合膜在机械技术的飞速发展下实现了自动化包装,伴随效能大幅提高的同时,质量问题愈加凸显。
包装薄膜拉断、打滑,进而导致包装线断流的事件时有发生,给包装生产、印刷企业造成了巨额经济损失。
其主要原因在于企业对塑料薄膜的摩擦系数没有做到合理的控制。
1 塑料薄膜的摩擦系数摩擦系数是对两个接触表面摩擦力的一种量度。
在微观世界中,材料表面是凹凸不平的,当两种材料相互接触时,真正接触的只有凸处,凸处原子紧密接触,形成很强的相互作用力。
当接触面发生相对移动时,这种作用力将被硬性剪切,两接触面凸处相互碰撞而发生断裂、磨损,形成对物体运动的阻碍,而平行于接触面、破坏凸处的剪切力,即为摩擦力。
摩擦力包括静摩擦力和动摩擦力。
静摩擦力是两接触表面在相对移动开始时的最大阻力,其与垂直于物体接触面的力之比就是静摩擦系数;动摩擦力是两接触表面以一定速度相对移动时的阻力,其与垂直于物体接触面的力之比就是动摩擦系数。
在实际包装中的摩擦力常常既是拖动力又是阻力,因此必须有效地控制摩擦系数的大小,使它在适当的范围内。
包装机运转过程中,一般要求薄膜内层摩擦系数比较小,但不能过小,否则可能引起制袋成型时叠料不稳定而产生错边;而薄膜外层与包装机拖动金属面摩擦系数需适中,太大会引起包装过程中阻力过大致使材料拉伸变形,太小可能又会引起拖动机构打滑造成电眼跟踪和切断定位不准。
对此,通常在薄膜中加入爽滑剂控制薄膜表面的摩擦系数[1]。
润滑条件下金刚石薄膜及石墨/金刚石复合薄膜的摩擦学性能
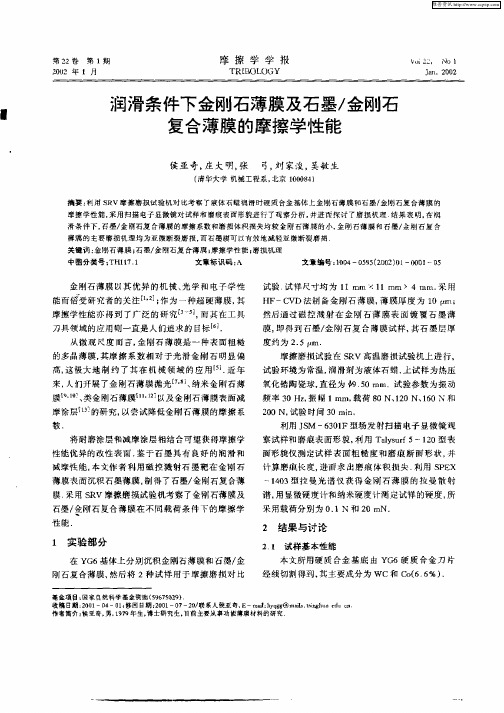
的多 晶薄膜 . 其摩 擦 系 数相 对 于 光滑 金 刚石 明显 偏
摩擦磨 损试 验在 S V 高温 磨损 试验机 上进 行, R 试 验环境为 常温 . 润滑剂 为液体 石 蜡 , 试样为 热压 上 氧化 锆陶 瓷球 , 径为 .0mm.试验 参数 为 振动 直 5
频率 3 0Hz振 幅 1mm, , 载荷 8 ON、 2 1 0N、 6 10N和 2 0N, 验时 间 3 n 0 试 0mi, 利用 J M 一6 0 F型场 发射扫描 电子 显微镜 观 S 31
膜 采用 S V 摩擦磨 损试 验机考察 了金 刚 石薄 膜 及 R 石墨 / 金剐 石复合 薄 膜在 不 同载 荷 条 件 下的 摩擦 学
性能 .
谱, 用显微硬 度计 和纳米 硬度 计测 定试样 的硬度 , 所
采 用载荷分 别为 0. N和 2 N. 1 0r a
薄膜动摩擦系数测试方法

薄膜动摩擦系数测试方法薄膜动摩擦系数是描述薄膜材料与其他物体之间滑动摩擦特性的重要参数。
准确测量薄膜动摩擦系数对于材料研究和工程应用具有重要意义。
本文将介绍几种常用的薄膜动摩擦系数测试方法,并对其原理和步骤进行详细阐述。
一、概述薄膜动摩擦系数是指材料在与其他物体相互接触并施加一定压力下,两者之间的滑动阻力大小。
薄膜动摩擦系数的测量通常需要考虑到摩擦试样的表面状态、试样材料、压力、温度等因素的影响。
下面将介绍几种常用的薄膜动摩擦系数测试方法。
二、倾斜面法倾斜面法是一种简单而常用的测量薄膜动摩擦系数的方法。
该方法主要通过测量在一定斜角下试样在重力作用下下滑动的速度,计算出薄膜动摩擦系数。
步骤如下:1.准备试样:将具有平整表面的薄膜材料切割成标准大小的试样。
2.设置倾斜角度:使用可调节的倾斜台,将试样放在倾斜台上,并调整合适的倾斜角度。
3.施加压力:在试样上施加一定的压力,保证试样与倾斜台之间有足够的接触力。
4.释放试样:释放试样,测量试样在倾斜台上滑动的速度。
5.计算摩擦系数:根据斜角、试样质量、试样滑动速度等数据,计算薄膜动摩擦系数。
三、球面摩擦法球面摩擦法是通过在薄膜表面放置一个球形体,施加一定压力并使其在薄膜表面滚动,在滚动过程中测量球体的速度,从而计算薄膜动摩擦系数。
步骤如下:1.准备试样:将薄膜材料制备成平整、干净的表面。
2.放置球体:在薄膜表面放置一个合适大小的球形体,并施加一定的压力。
3.测量球体速度:测量球体在薄膜表面滚动的速度。
4.计算摩擦系数:根据球体速度、压力等数据,计算薄膜动摩擦系数。
四、纳米压痕法纳米压痕法是一种高精度的测试方法,适用于测量薄膜材料的动摩擦系数。
该方法通过在薄膜表面施加一小块硬物,并测量其在薄膜表面滑动时的力和位移,从而计算薄膜动摩擦系数。
步骤如下:1.准备试样:将薄膜材料制备成平整、干净的表面。
2.搭建测试装置:选择适当的纳米压痕仪,搭建测试装置。
3.施加载荷:在薄膜表面位置施加一小块硬物。
钳工测试题(附参考答案)

钳工测试题(附参考答案)一、单选题(共50题,每题1分,共50分)1、CPS的11大要素中与生产制造密切相关的要素是()A、培训B、制造工程C、物流及计划管理D、领导能力正确答案:B2、()类硬质合金(YG)是由Wc,Co组成的,其韧性、磨削性能和导热性好。
A、钨钴B、45#C、钨钛钽钴D、钨钴钛正确答案:A3、()为变值系统误差。
A、工件材料不均匀引起的变形B、刀具的制造误差C、刀具线性磨损D、调整误差正确答案:C4、机床传动链的误差分析中,如果是升速运动,传动件的误差()。
A、被放大B、恒定C、产生波动D、被缩小正确答案:D5、圆锥销可()拆装而不影响零件的定位精度。
A、多次B、一次C、二次D、三次正确答案:A6、利用样板对工件进行找正定位时样板上的孔一般要比工件上的对应孔尺寸大5~10mm。
()A、全面质量管理B、质量管理C、全员质量管理正确答案:C7、蜗杆涡轮副在传动中具有(),只能由蜗杆传动涡轮。
A、传动功能B、重载功能C、负载功能D、自锁功能正确答案:D8、一个工厂的哪些地方需要整理、整顿:()A、食堂B、全工厂的每个地方C、工作现场正确答案:B9、制造机床床身应选用()。
A、灰铸铁B、球墨铸铁C、可锻铸铁正确答案:A10、在高速大功率和低速重载的工作条件下,宜采用(),因为它能耐冲击和震动。
A、滚动轴承B、轴C、轴套D、滑动轴承正确答案:D11、测绘已磨损的机械零件需要运用公差与配合的原理和标准,还原已损失的()。
A、公差和尺寸B、公差C、尺寸D、最小极限尺寸12、当工件以窄长的平面为定位基准时,可选择()个支撑钉定位。
A、3B、1C、2正确答案:C13、米制梯形内螺纹小径的计算公式是:D1=()。
A、d-1.05PB、d-1.825PC、d-PD、d-1.5P正确答案:C14、目前中小立式加工中心刀库的容量在()把刀具之间。
A、14~30B、10~15C、15~20D、5~10正确答案:A15、进行细刮时,推研后显示出有些发亮的研点,应()。
塑料材料的摩擦磨损试验
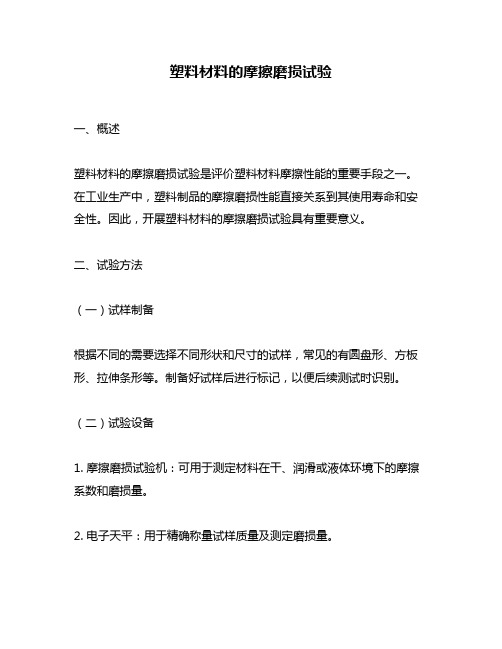
塑料材料的摩擦磨损试验一、概述塑料材料的摩擦磨损试验是评价塑料材料摩擦性能的重要手段之一。
在工业生产中,塑料制品的摩擦磨损性能直接关系到其使用寿命和安全性。
因此,开展塑料材料的摩擦磨损试验具有重要意义。
二、试验方法(一)试样制备根据不同的需要选择不同形状和尺寸的试样,常见的有圆盘形、方板形、拉伸条形等。
制备好试样后进行标记,以便后续测试时识别。
(二)试验设备1. 摩擦磨损试验机:可用于测定材料在干、润滑或液体环境下的摩擦系数和磨损量。
2. 电子天平:用于精确称量试样质量及测定磨损量。
3. 显微镜:用于观察试样表面形貌及分析磨损机理。
(三)试验步骤1. 在摩擦片表面涂上润滑剂或加入液体环境中进行测试。
2. 将待测材料与摩擦片紧密接触,施加一定的载荷,进行往复滑动。
3. 测量摩擦系数和磨损量,并记录试样表面形貌。
(四)试验参数1. 载荷:根据试样的硬度和强度确定载荷大小。
2. 滑动速度:根据实际使用条件确定滑动速度大小。
3. 滑动距离:根据实际使用条件确定滑动距离大小。
4. 环境温度和湿度:根据实际使用条件确定环境温度和湿度。
三、试验结果分析(一)摩擦系数摩擦系数是指材料在接触过程中所产生的阻力与垂直于接触面的力之比。
摩擦系数越小,说明材料具有较好的自润滑性能和耐磨性能。
反之,摩擦系数越大,则说明材料具有较差的自润滑性能和耐磨性能。
(二)磨损量磨损量是指试样在摩擦过程中所失去的质量或体积。
磨损量越小,说明材料具有较好的抗磨损性能。
反之,磨损量越大,则说明材料具有较差的抗磨损性能。
(三)表面形貌观察试样表面形貌可以了解其摩擦磨损机理,常见的磨损形貌有划痕、剥落、疲劳等。
四、注意事项1. 试样制备应尽量保证一致性,以减小实验误差。
2. 润滑剂和液体环境应选择与实际使用条件相符合的条件进行测试。
3. 测试过程中应注意控制环境温度和湿度,以免影响测试结果。
4. 测试前应对设备进行校准和检查,确保测试结果准确可靠。
塑料薄膜摩擦系数标准

塑料薄膜摩擦系数标准
塑料薄膜的摩擦系数通常由摩擦测试标准来评估。
以下是一些可能用于评估塑料薄膜摩擦系数的国际标准:
1.ASTM D1894 - Standard Test Method for Static and Kinetic
Coefficients of Friction of Plastic Film and Sheeting:
•ASTM D1894 是美国材料和试验协会(ASTM)发布的标准,用于测定塑料薄膜和片材的静摩擦系数和动摩擦系数。
2.ISO 8295 - Plastics - Film and sheeting - Determination of
the coefficients of friction:
•ISO 8295 是由国际标准化组织(ISO)发布的标准,用于测定塑料薄膜和片材的摩擦系数。
3.ASTM D618 - Standard Practice for Conditioning Plastics for
Testing:
•ASTM D618 也是ASTM发布的标准,虽然主要用于塑料的物理性能测试之前的条件处理,但在一些测试中也可能
涉及到摩擦系数的测定。
这些标准通常规定了测试的条件、设备、程序和报告方法,以确保测试的准确性和可重复性。
在进行摩擦系数测试时,需要注意所使用的标准和测试条件,以便结果的可比性。
同时,不同类型的塑料和不同的表面处理可能导致不同的摩擦特性,因此在实际应用中,还应考虑材料的具体特性和使用环境。
- 1、下载文档前请自行甄别文档内容的完整性,平台不提供额外的编辑、内容补充、找答案等附加服务。
- 2、"仅部分预览"的文档,不可在线预览部分如存在完整性等问题,可反馈申请退款(可完整预览的文档不适用该条件!)。
- 3、如文档侵犯您的权益,请联系客服反馈,我们会尽快为您处理(人工客服工作时间:9:00-18:30)。
几类硬质薄膜的摩擦磨损性能测试华敏奇1 张广安1袁振海2张莎莎31、中国科学院兰州化学物理研究所2、广州有色金属研究院3、兰州华汇仪器科技有限公司摘要:采用摩擦磨损试验机考察了几类复合硬质薄膜的摩擦磨损行为,结果表明:复合薄膜的摩擦磨损性能均极大提高。
CrN基复合薄膜的硬度与抗磨损性能均较CrN薄膜有极大提高;Al/AlN纳米多层膜具有软质Al层和硬质AlN层的交替结构,在摩擦过程中,硬质AlN层可以起到良好的承载作用,软质层可以起到良好的减摩作用,有效的降低了Al/AlN 纳米多层膜的摩擦和磨损,具有非常优异的摩擦学性能;Ti-DLC薄膜与S i3N4、钢、Ti-DLC 对摩时,均表现出良好的耐磨减摩性能,但摩擦系数与磨损率各不相同。
硬质薄膜材料包括难溶化合物(氮化物、碳化物、氧化物等)、类金刚石碳膜及硬质合金等硬度高、耐磨性好,已经取得了广泛的应用。
但如何评价硬质薄膜的摩擦磨损行为,已经成为研究此类硬质薄膜的关键问题,主要包括研制各种新型的摩擦学薄膜材料及摩擦学性能评价、薄膜的摩擦磨损原理及指导实际工况材料的摩擦学设计。
本文考察了几类物理气相沉积(PVD)复合硬质涂层的摩擦磨损行为,并探讨了其摩擦磨损机制。
1.实验过程采用自制的摩擦磨损试验机评价薄膜的摩擦学性能, 采用往复滑动方式, 频率为5Hz,单次滑动行程为6mm,,对偶件为GCr15钢球、氮化硅陶瓷球。
采用JSM-5600LV型电子显微镜(SEM)观测磨痕表面形貌。
采用MicroXam型三维表面形貌仪测量磨痕轮廓,并计算得到薄膜的磨损率。
2.结果与讨论2.1 CrN基复合薄膜采用中频反应磁控溅射制备了CrN与CrSiN、CrAlN复合薄膜。
通过EDS检测CrSiN 复合薄膜中Si/Si+Cr的相对含量为12.6%,CrAlN复合薄膜中Al/Al+Cr的相对含量为48.4%。
所制备的薄膜均呈现柱状生长, 且连接紧密, 间距很小, 结构密实, 薄膜的厚度约为1-1.5μm。
Si 与Al的复合对薄膜的断面形貌没有明显的影响, 但薄膜更加致密, 柱状晶粒明显细化, XRD结果也说明薄膜晶粒细化。
CrN 薄膜的硬度为13.9GPa ,复合薄膜硬度极大提高,CrSiN 薄膜硬度达25.6GPa ,CrAlN 薄膜硬度高达33.4GPa 。
图1 CrN 、CrSiN 、CrAlN 薄膜同GCr15钢球对磨的摩擦系数曲线 图2 CrN 、CrSiN 、CrAlN 薄膜同GCr15钢球对磨的磨痕轮廓图图4为CrN 、CrSiN 、CrAlN 薄膜在1 N 载荷下,滑动频率为5Hz ,同GCr15钢球对磨时的摩擦系数随滑动时间变化的关系曲线。
从图中可以看出,复合薄膜的摩擦系数较CrN 薄膜的摩擦系数稳定,CrAlN 薄膜的摩擦系数与CrN 薄膜相近;而CrSiN 薄膜的摩擦系数明显降低,主要是由于在摩擦过程中薄膜与摩擦副之间形成稳定的转移膜与具有润滑特性的化学组织(SiO2、Si(OH)4等),薄膜的摩擦系数降低,达到稳定磨损后摩擦系数约为0.25。
图2为CrN 、CrSiN 、CrAlN 薄膜同GCr15钢球对磨的摩擦系数曲线磨痕轮廓图,可从图中看出CrN 薄膜的墨痕深度达1.4μm ,薄膜几乎被磨穿,而CrSiN 与CrAlN 薄膜表面的墨痕很浅,仅有几十nm ,CrSiN 薄膜的磨损率约为CrN 薄膜的1/20,而CrAlN 薄膜则没有计算出磨损率,说明复合薄膜的抗摩擦磨损性能优异。
(a) CrN (b) CrSiN (c) CrAlN 图3 CrN 、CrSiN 、CrAlN 薄膜同GCr15钢球对磨的磨痕形貌图3为CrN 、CrSiN 、CrAlN 薄膜磨痕形貌CrN 薄膜表面严重磨损,出现明显的剥落痕迹CrSiN 与CrAlN 表面则没有出现明显的剥落痕迹,仅有少量划痕,说明薄膜自身的强度及韧性非常高,在摩擦磨损过程中煤观察到薄膜局部的破裂及剥落,其优异的摩擦磨损性能归因于复合薄膜致密的结构与高硬度。
2.2 Al/AlN纳米多层膜采用磁控溅射系统制备Al、AlN单层膜与Al/AlN纳米多层膜,其中薄膜厚度约为300-400nm之间,Al/AlN多层膜调制周期为4nm,每个周期中Al/AlN厚度为2.9nm/1.1nm。
AlN单层膜的硬度较高,约为13 GPa左右;Al单层薄膜的硬度较低,约为4 GPa左右,但比块体的硬度高得多,主要是由于薄膜中的晶粒比较小,存在大量的晶界,起到明显的强化,又由于纳米压痕的压入深度仅仅是在几十个纳米,所以薄膜表面的轻微氧化也将导致Al单层膜的硬度值升高;Al/AlN纳米多层薄膜的硬度为8.8GPa,远高于采用混合法则计算出的硬度值(6.62GPa),这说明Al/AlN纳米多层膜中大量的界面能显著提高薄膜的整体硬度。
图4 Al、AlN单层膜与Al/AlN多层膜同GCr15钢球对磨的摩擦系数曲线图4为Al、AlN单层膜与Al/AlN多层膜在1 N载荷下,滑动频率为5Hz,同GCr15钢球对磨时的摩擦系数随滑动时间变化的关系曲线。
可以看出Al与AlN单层薄膜的摩擦系数很高,摩擦系数波动幅度也很大,而且在很短的时间内薄膜的摩擦系数开始增大,而Al/AlN 多层膜的摩擦系数很稳定,没有出现很明显的波动,摩擦系数低于0.2,显示出优异的减摩性能。
(a) Al单层膜(b) AlN单层膜(c) Al/AlN多层膜图5 Al、AlN单层膜、Al/AlN多层膜同GCr15钢球对磨后磨损表面形貌单层Al膜的摩擦系数随着滑动次数的增加逐渐升高,这是由于Al单层膜硬度比对偶GCr15钢球低得多, 在法向载荷和剪切力(摩擦力)作用下Al薄膜很容易发生变形和剥落,并向对偶球表面转移, Al磨屑在摩擦过程中起磨料作用, 从而加剧薄膜的磨损,摩擦系数随着滑动时间逐渐增大,表面的磨痕很宽并且有很深的犁沟,呈现出磨粒磨损和粘着磨损特征(图5(a))。
而AlN单层膜的摩擦系数在20s时开始剧烈波动,30s时薄膜的摩擦系数急剧增大,摩擦系数达到0.6,这说明对于硬度高的单层AlN陶瓷膜,随着时间的增加积累了较高的内应力,又由于薄膜比较脆,导致薄膜表面破裂,相应的摩擦系数剧烈波动,然后突然升高,表明薄膜完全破裂,磨穿到硅基底;图5(b)为薄膜磨损表面形貌SEM照片,AlN单层膜磨痕表面存在很深的犁沟,由于AlN薄膜硬度比较高,磨痕很窄,磨损破裂的大量AlN屑在摩擦过程中起到犁削作用,导致磨痕很深,呈现出严重的磨粒磨损特征。
Al/AlN纳米多层薄膜的摩擦系数很低,维持在0.15左右,波动很小,随着滑动时间的增加没有很明显的变化。
纳米多层膜同GCr15钢球对磨时显示出了奇特的减摩效应,即金属/陶瓷软硬度交替纳米多层膜的摩擦系数远远低于单层金属或陶瓷薄膜的摩擦系数,分析认为这是由纳米多层薄膜的特殊结构而决定的。
Al/AlN纳米多层膜具有软质的Al金属层和硬质的AlN陶瓷层交替结构,硬质的AlN 层可以起到良好的承载作用,软质Al层易于屈服,同时具有很好的延展性,从而使接触面积增加,降低了接触应力和摩擦可以起到良好的减摩作用,有效的降低多层膜的应力和应变。
同时纳米多层薄膜具有很好的整体韧性,在整个对磨过程中主要是GCr15钢球的挤压,无明显的犁沟出现,从而有效克服了软金属的粘着磨损和硬陶瓷的脆性断裂磨损。
这种抗磨性的增加,也与多层膜中的界面行为有关,裂纹在通过界面区时会被阻止和反射,从而使能量在层间消失,而整个镀层不易失效,也有利于降低磨损。
同时薄膜也具有较高的硬度,这在一定程度上也能提高薄膜的耐磨性能。
Al/AlN多层膜是非晶的,没有沿晶界的裂纹传播,也一定程度上提高膜的耐磨性。
多层膜磨损表面虽然很宽,但没有出现明显的犁沟,磨痕表面也没有明显的磨屑(图5(c))。
2.3 Ti-DLC薄膜图6 Ti-DLC薄膜的断面形貌图7 Ti-DLC薄膜的Raman 光谱本实验采用中频孪生靶非平衡磁控溅射系统沉积含Ti类金刚石(Ti-DLC)复合薄膜。
图6为所沉积的Ti-DLC膜层断面形貌图,从图中可以看出,该薄膜厚度约为2μm,薄膜结构致密,且与基底结合良好。
图7为所制备的Ti-DLC薄膜的Raman光谱,为DLC薄膜拉曼光谱特征。
图8 Ti-DLC薄膜与不同对偶材料对摩的摩擦系数曲线比较摩擦实验采用往复摩擦磨损试验机测定薄膜的摩擦系数,测试参数:往复频率5Hz、振幅5mm、载荷2N,对偶件选用尺寸为Ф5mm的Si3N4球、钢球及表面沉积Ti-DLC的钢球。
图8为沉积Ti-DLC在大气环境下与不同材料(Si3N4、钢、Ti-DLC)的摩擦系数曲线,从图8可以看出,Ti-DLC与三种对偶材料对摩的摩擦系数都比较低,说明该薄膜具有较好的减摩性能。
但该薄膜与三种对偶材料对摩的摩擦系数具有明显不同。
Ti-DLC与钢对摩的摩擦系数最高,约为0.13左右,并且摩擦曲线有明显波动;Ti-DLC与Si3N4对摩的摩擦系数最低,40min 后进入稳定阶段,稳定值约为0.07;Ti-DLC与Ti-DLC对摩的摩擦系数在140min后进入稳定阶段,稳定值约为0.10。
以上结果表明,Ti-DLC薄膜的摩擦系数与对偶材料有较大的关系。
(a) Si3N4(b) 钢(c) Ti-DLC图9 Ti-DLC薄膜与不同材料对摩磨痕的三维形貌比较由图9可见,经240min摩擦试验后,Ti-DLC薄膜磨痕表面光滑,磨痕深度均未超过1μm(薄膜厚度为2μm左右),薄膜没有被磨穿,说明该薄膜具有良好的耐磨性能。
所沉积的Ti-DLC薄膜与Si3N4对摩,磨损率为 4.5×10-7mm3/Nm;与钢球对摩,磨损率为1.6×10-7mm3/Nm;而与Ti-DLC对摩时磨损率最低,磨损率为4.9×10-8mm3/Nm,比Ti-DLC与Si3N4对摩时的磨损率低了一个量级。
以上结果表明,Ti-DLC薄膜的磨损率与对偶材料有关。
3.结论通过复合化与多层化的设计,合理调整材料的结构与组分,获得了几类高性能的复合薄膜,并利用摩擦磨损试验机考察了硬质薄膜的摩擦磨损行为,结果表明:1. CrN基复合薄膜的硬度与抗磨损性能均较CrN薄膜提高,薄膜在磨损过程中没有发现明显的剥落;2. Al/AlN纳米多层膜具有软质Al层和硬质AlN层的交替结构,在摩擦过程中,硬质AlN层可以起到良好的承载作用,软质层可以起到良好的减摩作用,有效的降低了Al/AlN 纳米多层膜的摩擦和磨损,具有非常优异的摩擦学性能;3. Ti-DLC薄膜与S i3N4、钢、Ti-DLC对摩时,均表现出良好的耐磨减摩性能,但摩擦系数与磨损率各不相同,与Ti-DLC对摩时磨损率最低,达到4.9×10-8mm3/Nm。