齿轮齿条的设计
齿轮齿条传动设计计算
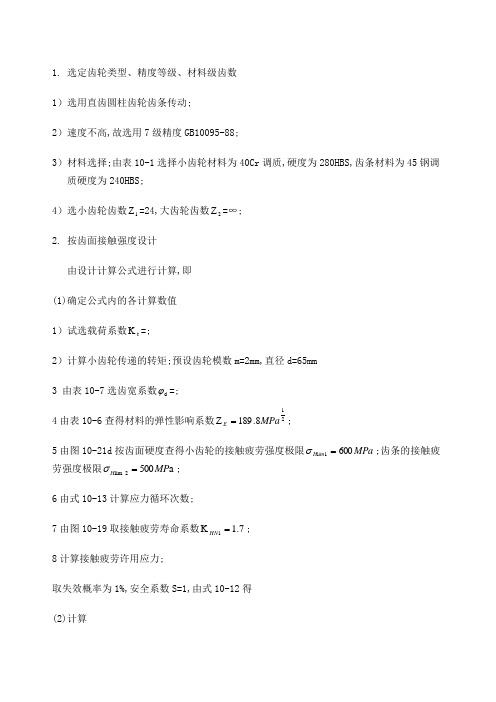
1. 选定齿轮类型、精度等级、材料级齿数1)选用直齿圆柱齿轮齿条传动;2)速度不高,故选用7级精度GB10095-88; 3)材料选择;由表10-1选择小齿轮材料为40Cr 调质,硬度为280HBS,齿条材料为45钢调质硬度为240HBS;4)选小齿轮齿数1Z =24,大齿轮齿数2Z =∞;2. 按齿面接触强度设计由设计计算公式进行计算,即(1)确定公式内的各计算数值1)试选载荷系数t K =;2)计算小齿轮传递的转矩;预设齿轮模数m=2mm,直径d=65mm3 由表10-7选齿宽系数d ϕ=;4由表10-6查得材料的弹性影响系数218.189MPa E =Z ;5由图10-21d 按齿面硬度查得小齿轮的接触疲劳强度极限MPa im H 6001l =σ;齿条的接触疲劳强度极限a 5002 lim MP H =σ;6由式10-13计算应力循环次数;7由图10-19取接触疲劳寿命系数7.11=K HN ;8计算接触疲劳许用应力;取失效概率为1%,安全系数S=1,由式10-12得(2)计算1)试算小齿轮分度圆直径1d t ,代入[]1H σ;2)计算圆周速度v;3计算齿宽b;4计算齿宽与齿高之比;模数齿高5)计算载荷系数;根据,7级精度,由图10-8查得动载荷系数1=V K ;直齿轮,1==ααF H K K ;由表10-2查得使用系数5.1=A K ;由表10-4用插值法查得7级精度、小齿轮为悬臂布置时250.1=βH K ; 由33.5=hb ,250.1=βH K 查图10-13得185.1=βF K ;故载荷系数 6)按实际的载荷系数校正所算得的分度圆直径,由式10-10a 得7计算模数m;3. 按齿根弯曲强度设计由式10-5得弯曲强度设计公式为(1) 确定公式内各计算数值1)由图10-20c 查得小齿轮的弯曲疲劳强度极限a 5501MP FE =σ;齿条的弯曲强度极限a 3802MP FE =σ;2)由图10-18取弯曲疲劳寿命系数1.11=FN K ,2.12=FN K ;3)计算弯曲疲劳许用应力;取弯曲疲劳安全系数S=,由式10-12得4计算载荷系数K;5查取齿形系数;由表10-5查得65.21a =F Y ,06.22a =F Y ;6查取应力校正系数;由表10-5查得58.11a =S Y ,97.12a =S Y ;7)计算齿轮齿条的[]F Sa Fa Y Y σ并加以比较;齿条的数值大;(2) 设计计算由于齿轮模数m 的大小主要决定弯曲强度,而齿面接触疲劳强度主要取决于齿轮直径;可由弯曲强度算得的模数并就近圆整为标准值m=4mm,按接触强度算得的分度圆直径mm d 84.771=,算出齿轮齿数以上计算过程验证了模数m=2,直径d=65的齿轮是符合强度要求的。
直齿轮与齿条设计案例
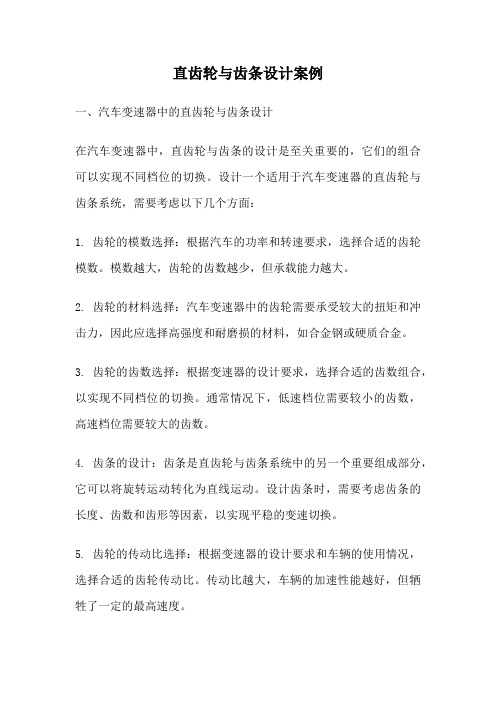
直齿轮与齿条设计案例一、汽车变速器中的直齿轮与齿条设计在汽车变速器中,直齿轮与齿条的设计是至关重要的,它们的组合可以实现不同档位的切换。
设计一个适用于汽车变速器的直齿轮与齿条系统,需要考虑以下几个方面:1. 齿轮的模数选择:根据汽车的功率和转速要求,选择合适的齿轮模数。
模数越大,齿轮的齿数越少,但承载能力越大。
2. 齿轮的材料选择:汽车变速器中的齿轮需要承受较大的扭矩和冲击力,因此应选择高强度和耐磨损的材料,如合金钢或硬质合金。
3. 齿轮的齿数选择:根据变速器的设计要求,选择合适的齿数组合,以实现不同档位的切换。
通常情况下,低速档位需要较小的齿数,高速档位需要较大的齿数。
4. 齿条的设计:齿条是直齿轮与齿条系统中的另一个重要组成部分,它可以将旋转运动转化为直线运动。
设计齿条时,需要考虑齿条的长度、齿数和齿形等因素,以实现平稳的变速切换。
5. 齿轮的传动比选择:根据变速器的设计要求和车辆的使用情况,选择合适的齿轮传动比。
传动比越大,车辆的加速性能越好,但牺牲了一定的最高速度。
6. 齿轮的装配与调试:在设计完成后,需要进行齿轮的装配与调试工作。
确保齿轮与齿条的啮合精度和传动效率达到设计要求,同时保证齿轮的运转平稳和噪音低。
二、工业机械设备中的直齿轮与齿条设计工业机械设备中常常使用直齿轮与齿条系统,实现运动传动和位置控制。
以下是一些工业机械设备中直齿轮与齿条的设计案例:1. CNC数控机床:CNC数控机床中的主轴传动系统通常采用直齿轮与齿条组合,实现工件的加工和运动控制。
通过设计合适的齿轮传动比和齿条长度,可以实现高精度的位置控制。
2. 输送机系统:在物流和生产线上,输送机系统常常使用直齿轮与齿条传动。
通过设计合适的齿轮和齿条参数,可以实现物料的平稳传送和定位。
3. 机械手臂:工业机械手臂中的关节传动通常采用直齿轮与齿条系统。
通过设计合适的齿轮模数和齿数,可以实现机械手臂的高精度运动和位置控制。
4. 提升机系统:在仓储和物流领域,提升机系统常常使用直齿轮与齿条传动。
齿轮齿条设计
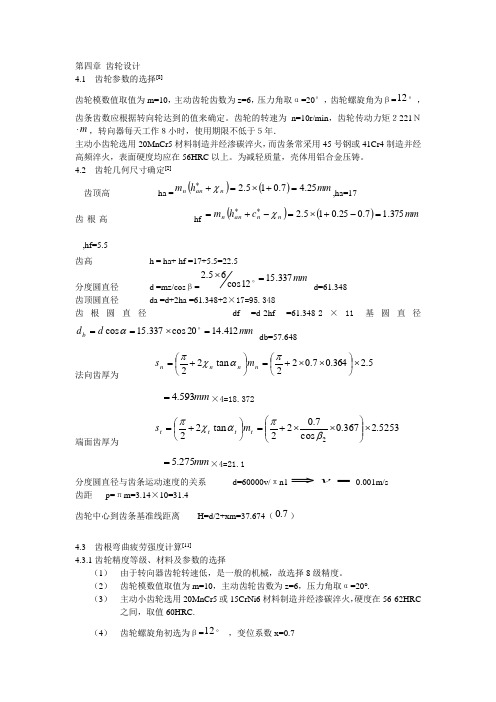
第四章 齿轮设计4.1 齿轮参数的选择[8]齿轮模数值取值为m=10,主动齿轮齿数为z=6,压力角取α=20°,齿轮螺旋角为β=12°,齿条齿数应根据转向轮达到的值来确定。
齿轮的转速为n=10r/min ,齿轮传动力矩2221Nm ⋅,转向器每天工作8小时,使用期限不低于5年. 主动小齿轮选用20MnCr5材料制造并经渗碳淬火,而齿条常采用45号钢或41Cr4制造并经高频淬火,表面硬度均应在56HRC 以上。
为减轻质量,壳体用铝合金压铸。
4.2 齿轮几何尺寸确定[2] 齿顶高 ha =()()mmh m n an n 25.47.015.2=+⨯=+*χ,ha=17齿根高 hf ()()mmc h m n n an n 375.17.025.015.2=-+⨯=-+=**χ,hf=5.5齿高 h = ha+ hf =17+5.5=22.5分度圆直径 d =mz/cos β=mm337.1512cos 65.2=⨯d=61.348齿顶圆直径 da =d+2ha =61.348+2×17=95.348齿根圆直径 df =d-2hf =61.348-2×11基圆直径mmd d b 412.1420cos 337.15cos =⨯== α db=57.648法向齿厚为 5.2364.07.022tan 22⨯⎪⎭⎫⎝⎛⨯⨯+=⎪⎭⎫ ⎝⎛+=παχπn n n n m smm 593.4=×4=18.372端面齿厚为 5253.2367.0cos 7.022tan 222⨯⎪⎪⎭⎫ ⎝⎛⨯⨯+=⎪⎭⎫⎝⎛+=βπαχπt t t t m smm 275.5=×4=21.1分度圆直径与齿条运动速度的关系 d=60000v/πn1=⇒v 0.001m/s齿距 p=πm=3.14×10=31.4齿轮中心到齿条基准线距离 H=d/2+xm=37.674(7.0)4.3 齿根弯曲疲劳强度计算[11]4.3.1齿轮精度等级、材料及参数的选择(1) 由于转向器齿轮转速低,是一般的机械,故选择8级精度。
齿轮齿条设计

4.1 齿轮参数的选择[8]齿轮模数值取值为m=4, 齿轮齿数为z=150, 压力角取α=20°,标准齿轮各部分尺寸都与模数有关, 且都与模数成正比。
规定齿顶高ha=h m, h 和c 分别称为齿顶高系数和顶隙系数。
正常齿制齿轮h =1, c =0.25。
齿轮选用20MnCr5材料制造并经渗碳淬火, 而齿条常采用45号钢或41Cr4制造并经高频淬火, 表面硬度均应在56HRC 以上。
为减轻质量, 壳体用铝合金压铸。
4.2 齿轮几何尺寸确定[2]齿顶高 h a =h *a m=1×4, h a =4 mm齿根高 h =( h + c )m, h =(1+0.25)×4=5 mm齿高 h = h + h =4+5, h=9 mm分度圆直径 d =mz d=4×150=600 mm齿顶圆直径 d a =d+2 h a d a =608 mm齿根圆直径 d f = d-2 h f =600-2×5=590mm基圆直径 d b =d αcos =564mm齿厚为 s=p/2=πm/2=6.28齿槽宽 e= p/2=πm/2=6.28齿距 p=πm=3.14×4=12.564.3 齿根弯曲疲劳强度计算[11]4.3.1齿轮精度等级、材料及参数的选择(1) 由于转向器齿轮转速低, 是一般的机械, 故选择8级精度。
(2) 齿轮模数值取值为m=4, 齿轮齿数为z=150, 压力角取α=20°.齿轮选用20MnCr5或15CrNi6材料制造并经渗碳淬火, 硬度在56-62HRC 之间, 取值60HRC.4.3.2齿轮的齿根弯曲强度设计。
σF =z bm KT22Y F Y S ≤[σF ]m ≥32][2F S F d Y Y z KT σψ• T=9.55×106×ωωn P [σF ]=FF N S Y lim σ 式中 K —载荷因数, 由表7—8, 取K=1.2;T —齿轮的理论转矩, T=105845N ·mσF —齿根实际最大弯曲应力(Mpa )[σF ]—齿轮的许用弯曲应力(Mpa )b —轮齿的工作宽度(mm )—齿宽因数, 见表7-12Y —齿形修正因数, 见表7-11Y —应力修正因数, 见表7-11Y —弯曲疲劳寿命因数, 见图7-30—弯曲疲劳极限, 见图7-31S —弯曲疲劳强度安全因数, 见表7-10取齿宽系数 d ψ=0.8齿轮齿数 z=150许用弯曲应力 201.25MpaσF =189≤201.25= [σF ]m ≥4, 取m=44.3.3齿面接触疲劳强度校核校核公式为σH =3.53Z E μμ121±⨯bd KT ≤[σH ] 式中K 为载荷因数, 见表7-8, 取K=1.2Z —材料的弹性因数 , 见表7-9, 取 Z =144σH —齿面的实际最大接触应力μ—齿数比[σH ]=HH N S Z lim σ 式中[σH ]—齿轮的许用接触应力—接触疲劳寿命因数, 如图7-27取 =1.6—接触疲劳极限, 如图7-28, 取 =600—接触疲劳强度安全因数, 见表7-10, 取 =1.2[σH ]=800MpaσH =600Mpa ≤[σH ]=800Mpa第五章 齿条的设计5.1齿条的设计[6]根据齿轮齿条的啮合特点:(1) 齿轮的分度圆永远与其节圆相重合,而齿条的中线只有当标准齿轮正确安装时才与其节圆相重合.(2)齿轮与齿条的啮合角永远等于压力角. 因此,齿条模数m=4, 压力角齿条断面形状选取圆形选取齿数z=60齿顶高系数1= *anh顶隙系数25.0=*nC齿顶高ha =h*am=1×4, ha=4 mm齿根高h =( h + c )m, h =(1+0.25)×4=5 mm 齿高h = h + h =4+5, h=9 mm最终确定齿条为650mm长。
齿轮齿条传动设计计算

1.选定齿轮类型、精度等级、材料级齿数1)选用直齿圆柱齿轮齿条传动。
2)速度不高,应选用7级精度〔GB10095—88〕。
3)材料选择。
由表10-1选择小齿轮材料为40Cr〔调质〕,硬度为280H BS,齿条材料为45钢〔调质)硬度为240HBS.4)选小齿轮齿数=24,大齿轮齿数=∞。
1Z 2Z 2.按齿面接触强度设计由设计计算公式进展计算,即(1)确定公式内的各计算数值1)试选载荷系数=1。
3。
t K 2)计算小齿轮传递的转矩.〔预设齿轮模数m=2m m,直径d =65mm)3〕 由表10—7选齿宽系数=0。
5。
d ϕ4〕由表10—6查得材料的弹性影响系数.218.189MPa E =Z 5〕由图10—21d按齿面硬度查得小齿轮的接触疲劳强度极限;齿条的接触疲劳强度极限。
MPa im H 6001l =σa 5002lim MP H =σ6〕由式10—13计算应力循环次数。
7〕由图10-19取接触疲劳寿命系数。
7.11=K HN 8)计算接触疲劳许用应力。
取失效概率为1%,平安系数S=1,由式〔10-12〕得(2)计算1)试算小齿轮分度圆直径,代入。
1d t []1H σ2)计算圆周速度v.3〕计算齿宽b.4)计算齿宽与齿高之比。
模数齿高5)计算载荷系数.根据,7级精度,由图10—8查得动载荷系数;1=V K 直齿轮,;1==ααF H K K 由表10—2查得使用系数;5.1=A K 由表10-4用插值法查得7级精度、小齿轮为悬臂布置时。
250.1=βH K 由,查图10—13得;故载荷系数33.5=hb 250.1=βH K 185.1=βF K 6)按实际的载荷系数校正所算得的分度圆直径,由式(10—10a 〕得7〕计算模数m 。
3.按齿根弯曲强度设计由式〔10—5〕得弯曲强度设计公式为(1)确定公式内各计算数值1)由图10—20c 查得小齿轮的弯曲疲劳强度极限;齿条的弯曲a 5501MP FE =σ强度极限;a 3802MP FE =σ2)由图10—18取弯曲疲劳寿命系数,;1.11=FN K2.12=FN K 3)计算弯曲疲劳许用应力.取弯曲疲劳平安系数S =1。
齿轮齿条的设计
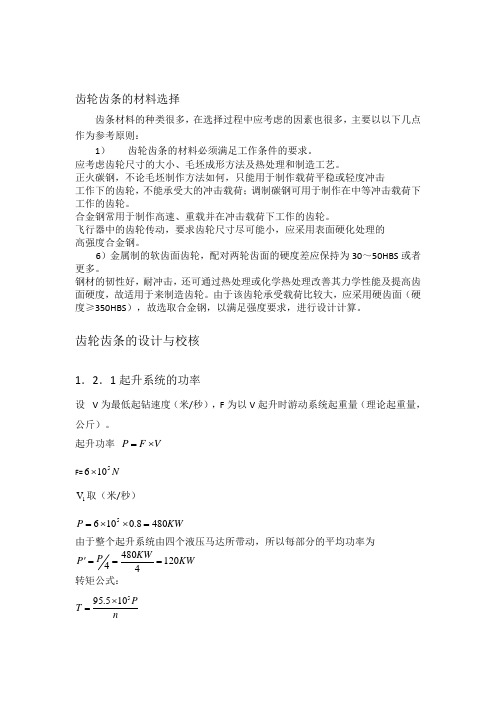
齿轮齿条的材料选择齿条材料的种类很多,在选择过程中应考虑的因素也很多,主要以以下几点作为参考原则:1) 齿轮齿条的材料必须满足工作条件的要求。
应考虑齿轮尺寸的大小、毛坯成形方法及热处理和制造工艺。
正火碳钢,不论毛坯制作方法如何,只能用于制作载荷平稳或轻度冲击工作下的齿轮,不能承受大的冲击载荷;调制碳钢可用于制作在中等冲击载荷下工作的齿轮。
合金钢常用于制作高速、重载并在冲击载荷下工作的齿轮。
飞行器中的齿轮传动,要求齿轮尺寸尽可能小,应采用表面硬化处理的 高强度合金钢。
6)金属制的软齿面齿轮,配对两轮齿面的硬度差应保持为30~50HBS 或者更多。
钢材的韧性好,耐冲击,还可通过热处理或化学热处理改善其力学性能及提高齿面硬度,故适用于来制造齿轮。
由于该齿轮承受载荷比较大,应采用硬齿面(硬度≥350HBS ),故选取合金钢,以满足强度要求,进行设计计算。
齿轮齿条的设计与校核1.2.1起升系统的功率设V 为最低起钻速度(米/秒),F 为以V 起升时游动系统起重量(理论起重量,公斤)。
起升功率 VF P ⨯=F=N 5106⨯ 1V 取(米/秒)KW P 4808.01065=⨯⨯=由于整个起升系统由四个液压马达所带动,所以每部分的平均功率为KW KW P P 12044804===' 转矩公式:595.510P T n⨯=所以转矩 T=mm N n.120105.955⨯⨯ 式中n 为转速(单位r/min )1.2.2 各系数的选定计算齿轮强度用的载荷系数K ,包括使用系数A K 、动载系数V K 、齿间载荷分配系数K α及齿向载荷分配系数K β,即K=A V K K K K αβ1)使用系数A K是考虑齿轮啮合时外部因素引起的附加载荷影响的系数。
该齿轮传动的载荷状态为轻微冲击,工作机器为重型升降机,原动机为液压装置,所以使用系数A K 取。
2)动载系数V K齿轮传动不可避免地会有制造及装配误差,轮齿受载后还要产生弹性变形,对于直齿轮传动,轮齿在啮合过程中,不论是有双对齿啮合过渡到单对齿啮合,或是有单对吃啮合过渡到双对齿啮合的期间,由于啮合齿对的刚度变化,也要引起动载荷。
齿轮齿条的设计计算与校核
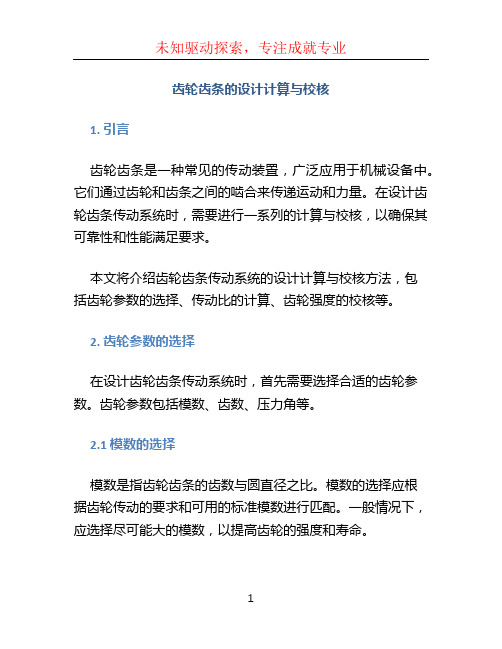
齿轮齿条的设计计算与校核1. 引言齿轮齿条是一种常见的传动装置,广泛应用于机械设备中。
它们通过齿轮和齿条之间的啮合来传递运动和力量。
在设计齿轮齿条传动系统时,需要进行一系列的计算与校核,以确保其可靠性和性能满足要求。
本文将介绍齿轮齿条传动系统的设计计算与校核方法,包括齿轮参数的选择、传动比的计算、齿轮强度的校核等。
2. 齿轮参数的选择在设计齿轮齿条传动系统时,首先需要选择合适的齿轮参数。
齿轮参数包括模数、齿数、压力角等。
2.1 模数的选择模数是指齿轮齿条的齿数与圆直径之比。
模数的选择应根据齿轮传动的要求和可用的标准模数进行匹配。
一般情况下,应选择尽可能大的模数,以提高齿轮的强度和寿命。
2.2 齿数的选择齿数的选择主要考虑齿轮传动的传动比和齿轮的工作条件。
传动比是指齿轮输入轴的转速与输出轴的转速之比。
2.3 压力角的选择压力角是指齿轮齿条啮合面上法线与齿轮轴线之间的夹角。
压力角的选择应根据齿轮传动的要求和可用的标准压力角进行匹配。
一般情况下,应选择尽可能小的压力角,以减小齿轮齿条的侧向力和噪声。
3. 传动比的计算传动比是齿轮齿条传动系统中重要的性能指标之一,它影响着输出轴的转速和扭矩。
传动比的计算可以根据齿轮齿数的比值来确定。
4. 齿轮强度的校核齿轮强度是齿轮齿条传动系统设计中关键的校核指标之一,它决定了齿轮的承载能力和寿命。
齿轮强度的校核可以通过齿轮的材料强度和几何参数来确定。
4.1 齿轮模数的校核齿轮模数的校核可以通过计算齿轮的接触应力和弯曲应力来进行。
应保证齿轮的接触应力和弯曲应力不超过齿轮材料的强度极限。
4.2 齿轮齿数的校核齿轮齿数的校核可以通过计算齿轮的接触比和模数来进行。
应保证齿轮的接触比和模数满足设计要求。
4.3 齿轮强度的校核齿轮强度的校核可以通过计算齿轮的接触疲劳寿命来进行。
应保证齿轮的接触疲劳寿命不低于设计要求。
5. 结论齿轮齿条的设计计算与校核是确保齿轮齿条传动系统可靠性和性能的重要环节。
第2章齿轮齿条的设计

第2章齿轮齿条的设计齿轮齿条是机械传动中常用的一种传动方式,其主要作用是将马达的旋转运动转化为直线运动或反之。
齿轮齿条的设计涉及到几个重要的参数,包括齿轮模数、齿数、压力角等。
首先是齿轮的设计。
齿轮的齿数和模数是两个重要的参数,齿数决定了齿轮的直径和齿面宽度,而模数影响了齿轮的齿面高度和齿轮的强度。
在齿轮设计中,通常采用的是标准模数,如1、1.5、2、3等,齿数一般也是标准值,如10、20、30等,一方面是为了生产方便,另一方面也是为了保证齿轮的传动效率和稳定性。
另外,在齿轮设计时还需要考虑齿轮的压力角,它是齿轮齿面与径向线之间的夹角,一般取20°,有时也可以取25°或30°,过大的压力角会增加齿轮变形和噪音,过小的压力角则可能降低齿轮的承载能力。
齿轮齿条的设计还需要考虑到齿轮的齿面形状和材料选择。
齿轮的齿面形状通常采用直齿或斜齿,直齿更常见,斜齿适用于高速和大功率传动。
齿轮齿面的加工通常采用滚削和磨削等工艺,以保证齿轮的精度和质量。
另外,齿轮的材料选择也十分重要,一般采用合金钢或硬质合金,以保证齿轮的强度和耐磨性。
齿轮齿条的设计还需要考虑到齿轮的传动比和传动效率。
传动比是指齿轮的转速之比,传动效率是指齿轮传动中能量转化的比例,通常在95%以上。
传动比的选择要根据具体的传动需求和机械的运行条件,一般齿轮齿条传动的传动比不宜过大,以避免齿轮的滑动和磨损。
同时,还需要考虑齿轮的配合间隙和啮合角等参数,以保证齿轮的正常运行和传动的可靠性。
此外,齿轮齿条的设计还需要考虑到齿轮的轴向力和径向力等受力情况。
齿轮在运行过程中会产生轴向力和径向力,这些力对齿轮的强度和耐久性都有影响,因此需要在设计时进行合理的计算和选择。
如需特殊传动,也可以采用斜齿轮等结构,以减小轴向力和径向力。
综上所述,齿轮齿条的设计需要考虑多个因素,包括齿轮的齿数、模数、压力角、齿面形状、材料选择、传动比、传动效率以及受力情况等。
- 1、下载文档前请自行甄别文档内容的完整性,平台不提供额外的编辑、内容补充、找答案等附加服务。
- 2、"仅部分预览"的文档,不可在线预览部分如存在完整性等问题,可反馈申请退款(可完整预览的文档不适用该条件!)。
- 3、如文档侵犯您的权益,请联系客服反馈,我们会尽快为您处理(人工客服工作时间:9:00-18:30)。
1.1.2齿轮齿条的材料选择
齿条材料的种类很多,在选择过程中应考虑的因素也很多,主要以以下几点作为参考原则:
1)齿轮齿条的材料必须满足工作条件的要求。
2)应考虑齿轮尺寸的大小、毛坯成形方法及热处理和制造工艺。
3)正火碳钢,不论毛坯制作方法如何,只能用于制作载荷平稳或轻度冲击 工作下的齿轮,不能承受大的冲击载荷;调制碳钢可用于制作在中等冲击载荷下工作的齿轮。
4)合金钢常用于制作高速、重载并在冲击载荷下工作的齿轮。
5)飞行器中的齿轮传动,要求齿轮尺寸尽可能小,应采用表面硬化处理的 高强度合金钢。
6)金属制的软齿面齿轮,配对两轮齿面的硬度差应保持为30~50HBS 或者更多。
钢材的韧性好,耐冲击,还可通过热处理或化学热处理改善其力学性能及提高齿面硬度,故适用于来制造齿轮。
由于该齿轮承受载荷比较大,应采用硬齿面(硬度≥350HBS ),故选取合金钢,以满足强度要求,进行设计计算。
1.2齿轮齿条的设计与校核
1.2.1起升系统的功率
设V 为最低起钻速度(米/秒),F 为以V 起升时游动系统起重量(理论起重量,公斤)。
起升功率 V
F P ⨯=
F=N 5
106⨯
1V 取0.8(米/秒)
KW P 4808.01065=⨯⨯=
由于整个起升系统由四个液压马达所带动,所以每部分的平均功率为
KW KW
P P 1204
4804==='
转矩公式:
595.510P T n
⨯=N.mm
所以转矩 T=
mm N n
.120
105.955⨯⨯ 式中n 为转速(单位r/min )
1.2.2 各系数的选定
计算齿轮强度用的载荷系数K ,包括使用系数A K 、动载系数V K 、齿间载荷分配系数K α及齿向载荷分配系数K β,即
K=A V K K K K αβ 1)使用系数A K
是考虑齿轮啮合时外部因素引起的附加载荷影响的系数。
该齿轮传动的载荷状态为轻微冲击,工作机器为重型升降机,原动机为液压装置,所以使用系数A K 取1.35。
2)动载系数V K
齿轮传动不可避免地会有制造及装配误差,轮齿受载后还要产生弹性变形,对于直齿轮传动,轮齿在啮合过程中,不论是有双对齿啮合过渡到单对齿啮合,或是有单对吃啮合过渡到双对齿啮合的期间,由于啮合齿对的刚度变化,也要引起动载荷。
为了计及动载荷的影响,引入了动载系数V K ,如图2-1所示。
图2-1动载系数V K
由于速度v 很小,根据上图查得,V K 取1.0。
3)齿间载荷分配系数K α
一对相互啮合的斜齿(或直齿)圆柱齿轮,有两对(或多对)齿同时工作时,则载荷应分配在这两对(或多对)齿上。
对于直齿轮及修形齿轮,取1H F K K αα==。
4)齿轮载荷分布系数K β
当轴承相对于齿轮做不对称配置时,受灾前,轴无弯曲变形,齿轮啮合正常,两个节圆柱恰好相切;受载后,轴产生弯曲变形,轴上的齿轮也就随之偏斜,这就使作用在齿面上的载荷沿接触线分布不均匀。
计算齿轮强度时,为了计及齿面上载荷沿接触线分布不均匀的现象,通常以系数K β来表征齿面上载荷分布不均匀的程度对齿轮强度的影响。
根据机械设计表10-4取H K β=1.37。
综上所述,最终确定齿轮系数K=A V K K K K αβ=1.35⨯1⨯1⨯1.37=1.8
1.2.3 齿轮传动的设计参数、许用应力的选择
1.压力角α的选择
我国对一般用途的齿轮传动规定的标准压力角为α=20°。
2.齿数z 的选择
为使齿轮免于根切,对于α=20°的标准直齿轮,应取z ≥17,这里取z=20。
17
3.齿宽系数d φ的选择
由于齿轮做悬臂布置,取d φ=0.6 4.预计工作寿命
10年,每年250个工作日,每个工作日10个小时
h L =10⨯250⨯10=25000h
5.齿轮的许用应力 按下式计算
[]N lim
K S
σσ=
式中:S ——疲劳强度安全系数。
对于接触疲劳强度计算时,取S=1;进行
齿根弯曲疲劳强度计算时,取S=1.25~1.5。
N K ——考虑应力循环次数影响的系数,称为寿命系数。
应力循环次数N 的计算方法是:设n 为齿轮的转速(单位为r/min );j 为齿轮每转一圈时,同一齿面啮合次数;h L 为齿轮工作寿命(单位为h ),则齿轮工作应力循环次数N 按下式计算:
N=60nj h L
n 暂取10,则N=60⨯10⨯25000=1.5⨯710。
查机械设计表10-18可得N K =1.3。
lim σ——齿轮疲劳极限。
弯曲疲劳极限用FE σ代入;接触疲劳极限用Hlim σ代入,查机械设计图10-21得Hlim σ=980。
1500
HN K =1.3 S=1
[]HN Hlim H K 1.3980
1274MPa S 1
σσ•⨯=
== 1950
780FE MPa σ= 850 1FN K = S=1.4
[]7801
557.11.4
HF FE F K MPa S σσ•⨯=
== 607.1 (双向工作乘以0.7)424.97
当齿数z=20 17 时,齿形系数Fa Y =2.8 2.97 应力校正系数Sa Y =1.55 1.52
基本参数选择完毕
1.2.4 齿轮的设计计算
齿轮的设计计算公式:
[]
32
2Fa Sa
d F Y Y KT m z φσ≥•
3
2
1]
[2F Sa
Fa d m Y Y z T K K m σφ⨯⨯⨯⨯⨯≥……………K m —开式齿轮磨损系数,K m =1.25(机械设计手册(3卷)14-134)
转矩 595.510P T n
⨯=N.mm (1式)
601000n mz v π=⨯⨯
所以238.8
n m
= v=0.8 n=899.2/m (2式)
将1式、2式及各参数代入计算公式得:
≥2
m 8
.2381.557206.055.18.2120105.958.122
5⨯⨯⨯⨯⨯⨯⨯⨯⨯ 解得:72.23≥m ;20 取m=25 那么n=9.5,取n=10
5510146.110
120105.95⨯=⨯⨯=T N.m
齿面接触疲劳强度计算公式:[]
E 3
d H Z KT u 12.32u d φσ±≥•2
()式中[]H σ的单位为Mpa ,d 的单位为mm ,其余各符号的意义和单位同前。
由于本传动为齿轮齿条传动,传动比近似无穷大,所以
u
1
u
±=1 E Z 为弹性影响系数,单位12
MPa ,其数值查机械设计表,取E Z =189.812
MPa ,
如表2-1所示:
表2-1 材料特性系数E Z
计算,试求齿轮分度圆直径:
[]E 3d H Z KT u 12.32u d φσ±≥•2()32.2=⎪⎭
⎫
⎝⎛⨯⨯⨯32
5
12748.1896.010146.18.1456.75mm
通过模数计算得:m=25,z=20 所以分度圆直径d=25⨯20=500mm 所以取两者偏大值d=500mm
计算齿宽 b=d d φ•=0.6⨯500=300mm 齿高 h=2.25m=2.25⨯25=56.25mm 最终确定齿轮数据:
模数m=25 齿数z=20
分度圆直径d=500mm 齿高h=56.25mm 齿宽b=300mm 转速n=10r/min
因此齿轮齿条的最终设计图形如图2-2所示:
图2-2 齿轮齿条的设计图。