专用夹具设计步骤.
专用夹具设计

二、专用夹具设计的方法步骤
1、已知条件:工艺人员提出的夹具设计任务书, 内容主要包含:工序加工尺寸、位置精度要求;定 位基准;夹紧力作用点、方向;机床、刀具、辅具; 所需夹具数量。
2、设计方法步骤
夹具设计生产过程一般可简单表示成下面框图
⑴准备阶段:明确设计要求、掌握第一 手资料
①收集各种图纸和技术资料 ②了解生产批量和夹具需要量 ③收集有关机床的资料 ④收集有关刀具方面的资料 ⑤收集有关夹具零部件标准 ⑥了解有关本单位制造和使用夹具的情况 ⑦收集国内外同类夹具的资料
④ 钻套下端面与工件加工面之间的空隙S确定
加工脆材:S=(0.3~0.6)d
加工塑材:S=(0.5~1)d
材料愈硬、S愈小;d愈小、S愈大 特殊情况: 在斜面上钻孔,S取小值;孔位精度高时、S=0; 钻L/d>5的深孔、S=1.5d
⑵ 钻模板:安装钻套的板
①固定式钻模板
② 铰链式钻模板
③ 可卸式钻模板
+0.025 +0.014
+0.039 +0.022
+0.029 +0.016
+0.045 +0.026
H9级精度铰刀
+0.025 +0.014
+0.030 +0.017
+0.036 +0.020
+0.044 +0.025
+0.052 +0.030
+0.062 +0.036
+0.073 +0.042
带导柱铰刀 1-切削部分 2-钻套 3-导柱
b) 钻套导引刀具刃部时
工序
导孔基本 尺寸
夹具设计方案

夹具设计方案夹具设计在制造业中扮演着重要的角色,它们被广泛应用于生产过程中的材料管理和加工环节。
本文将讨论夹具设计的基本原则和步骤,以及如何根据具体需求制定夹具设计方案。
一、夹具设计的基本原则夹具设计的主要目标是提供良好的夹持力和稳定性,以确保工件在加工过程中保持确定位置和姿态。
以下是夹具设计的基本原则:1. 合理使用工件特征:夹具设计应充分考虑到工件的几何形状、材料和加工需求,选择适当的夹持方式和夹具结构。
不同形状和材料的工件可能需要不同的夹具形式,如机械夹持、磁性夹持或真空吸附等。
2. 保证夹具刚性:夹具设计应尽可能提高夹具的刚性和稳定性,以减少变形和振动对工件加工的影响。
合理选择材料和结构,增加横向支撑和加强结构的刚性,能够有效提升夹具的工作性能。
3. 优化夹持力分配:夹具设计应合理分配夹持力,避免因夹持力不均匀导致工件变形或失稳。
在夹具结构中增加调节装置,根据工件的形状和加工要求进行调整,能够提高夹持力的均匀分布。
4. 考虑夹具调节和固定:夹具设计应充分考虑调节和固定的需求,以适应不同尺寸、形状和数量的工件加工。
通过增加可调节的支撑和固定装置,能够提高夹具的灵活性和适应性。
二、夹具设计的步骤1. 确定需求:在进行夹具设计之前,需要明确工艺流程和工件加工的具体要求,了解工件的形状、尺寸和材料特性。
2. 进行夹具定位:根据工件的几何特征和加工要求,确定夹具的定位方式和位置,确保工件在加工过程中的稳定性和精度。
3. 设计夹具结构:根据工件的形状和尺寸,选择合适的夹持方式和夹具结构。
考虑夹具的刚性、稳定性和调整能力,进行夹具的整体设计。
4. 验证夹具设计:进行夹具设计的仿真分析或实际测试,验证夹具的夹持力和稳定性,确保夹具设计满足工件加工的需求。
5. 优化夹具设计:根据测试结果和实际使用情况,对夹具设计进行优化和改进。
通过调整夹具结构、材料和调节装置,提高夹具的工作效率和适应性。
三、夹具设计方案应根据具体的需求和工艺流程来制定。
专用夹具设计方法【步骤】

以下为专用夹具的设计方法,一起了解一下吧。
一、专用夹具的设计步骤(一).研究原始资料明确任务书中的设计要求,收集下列资料:1) 工件图、毛坯图和工艺规程等技术文件。
了解该工序的加工技术要求,定位和夹紧方案,毛坯情况,加工时使用的机床、刀具、加工和切削用量等2) 了解生产批量和对夹具的需用情况,以确定所采用夹具结构的合理性和经济性。
3) 了解机床的主要技术参数、规格、安装夹具的有关连接部分的尺寸等。
4) 了解刀具的主要结构尺寸、制造精度、主要技术条件等。
5) 收集有关夹具零部件标准(国标、部标、企标、厂标),典型夹具结构、夹具设计资料等。
6) 了解本公司制造夹具能力和经验,了解用户有无压缩空气站等。
7) 3D图形的转换。
(二)确定夹具的结构1 定位要则1) 选择合理的定位基准——定位基准必须与工艺基准重合,并尽量与设计基准重合,以减小定位误差,获得最大加工允差,降低夹具制造精度。
当定位基准和工艺基准或设计基准不重合时,需进行必要的加工尺寸及其允差的换算。
——应选择工件上最大的平面,最长的圆柱面或圆柱轴线为定位基准,以提高定位精度,并使定位稳定、可靠。
——在选择定位元件时,要防止出现过定位现象。
——在工件各加工工序中,力求采用同一基准,以必免因基准更换而降低工件各表面相互位置的准确度。
——当铸、锻件以毛坯面作为第一道工序的基准时,应选用比较光整表面作基准面,避开浇冒口或分型面等凸起不平整的部位。
2) 限制工件的自由度——工件在夹具上进行定位时,为保证加工面位置尺寸或位置精度,以及承受切削力和夹紧力等的需要,必须限制住工件的六个自由度。
——如果工件以已加工过的光滑平面定位,必要时可以用六个以上的点定位,但各定位面上支承点的表面必须在同一平面上,或其中的几个支承点采用辅助支承。
3) 对定位元件的要求——工件定位基准与定位元件接触或配合后,能限制住必须由其限制的工件的自由。
——由其产生的定位误差最小。
——定位表面应具有较高的尺寸精度、配合精度、表面粗糙度和硬度。
专用夹具设计方法和步骤

1、明确设计任务,收集设计资料
2、拟订夹具结构方案,绘制夹具草图
(1)确定工件的定位方案,设计定位装置,并对夹紧力进行估算,以确保夹紧可靠
(2)确定工件的夹紧方案,设计夹紧装置
(3)确定刀具的引导方式,选择或设计引导元件或对刀元件
(4)确定其他元件或装置的结构形式,如定位键、分度装置等
(5)确定夹具的总体结构及夹具在机床上的安装方式。
对夹具的总体结构最好能拟订出几个不同的方案,画出草图,经过分析比较,选择最佳方案
3、绘制夹具总图
(1)选择操作者工作时正对的位置为主视图
(2)用双点划线将工件的外形轮廓、定位基面、夹紧表面以及加工表面画在各视图相应的位置上,待加工面上的加工余量可用网纹线表示。
在夹具总图中,工件可看作透明体,不遮挡后面的线条
(3)依次画出定位、夹紧、导向元件或装置的具体结构,再画出夹具体,将各元件或装置连成一个整体
(4)在总图上标注尺寸(包括轮廓尺寸、联系尺寸、重要的配合尺寸等)、公差和技术要求
(5)绘制夹具零件图。
在夹具中的非标准零件都要绘制零件图,并按总图要求确定零件的尺寸、公差及技术条件
三、夹具总图技术要求的制订
1、夹具总图上应标注的尺寸和公差
(1)夹具外形的最大轮廓尺寸
(2)影响定位精度的尺寸
(3)影响对刀精度的尺寸和公差
(4)影响夹具在机床上安装精度的尺寸和公差
(5)影响夹具精度的尺寸和公差
(6)其他装配尺寸及公差
2、夹具总图上公差值的确定
(1)与加工尺寸有直接对应关系的夹具公差δJ (2)其他装配尺寸的配合性质及公差等级
3、夹具总图上应标注
4、的技术要求。
专用夹具设计范文
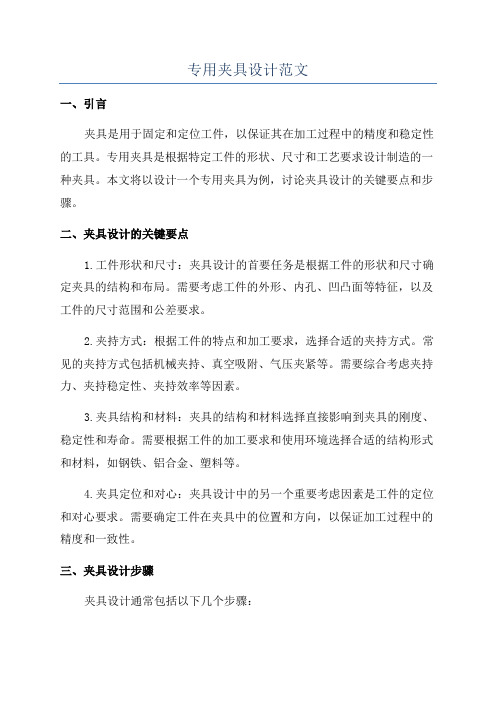
专用夹具设计范文一、引言夹具是用于固定和定位工件,以保证其在加工过程中的精度和稳定性的工具。
专用夹具是根据特定工件的形状、尺寸和工艺要求设计制造的一种夹具。
本文将以设计一个专用夹具为例,讨论夹具设计的关键要点和步骤。
二、夹具设计的关键要点1.工件形状和尺寸:夹具设计的首要任务是根据工件的形状和尺寸确定夹具的结构和布局。
需要考虑工件的外形、内孔、凹凸面等特征,以及工件的尺寸范围和公差要求。
2.夹持方式:根据工件的特点和加工要求,选择合适的夹持方式。
常见的夹持方式包括机械夹持、真空吸附、气压夹紧等。
需要综合考虑夹持力、夹持稳定性、夹持效率等因素。
3.夹具结构和材料:夹具的结构和材料选择直接影响到夹具的刚度、稳定性和寿命。
需要根据工件的加工要求和使用环境选择合适的结构形式和材料,如钢铁、铝合金、塑料等。
4.夹具定位和对心:夹具设计中的另一个重要考虑因素是工件的定位和对心要求。
需要确定工件在夹具中的位置和方向,以保证加工过程中的精度和一致性。
三、夹具设计步骤夹具设计通常包括以下几个步骤:1.工件分析:分析工件的形状、尺寸和加工要求,了解工件的特点和关键要求。
如有必要,可以通过测量和三维建模来获取准确的工件数据。
2.夹具结构设计:根据工件分析的结果,确定夹具的结构形式和布局。
考虑夹持方式、夹持力、夹持稳定性等因素,设计夹具的主要部件,如夹持装置、定位装置等。
3.夹具材料选择:根据夹具的结构和使用要求,选择合适的材料。
考虑刚度、耐磨性、耐腐蚀性等因素,选择适合的材料,如优质钢材、铝合金等。
4.夹具定位和对心设计:确定工件在夹具中的位置和方向。
根据工件的形状和加工要求,设计适当的定位和对心装置,以确保工件在加工过程中的精度和一致性。
5.夹具制造和调试:根据设计图纸制造夹具的主要部件,进行组装和调试。
在调试过程中,需要检验夹具的夹持力、夹持稳定性和定位精度等指标,以确保夹具的性能符合设计要求。
四、结论夹具设计是一项复杂的工程任务,需要综合考虑工件的形状、尺寸和加工要求,选择合适的夹持方式和材料,设计合理的结构和定位装置。
工装设计【夹具设计】

工装夹具课程设计说明书题目:夹具设计学号:姓名:班级:指导老师目录第一章 -------------------------夹具的总体方案设计第二章 ---------------------------夹具设计的步骤第三章---------------------------------夹具零部件的结构选择第四章 ------------------- 夹具精度的分析计算及校核第五章 ---------------------------------结论第六章 --------------------------------参考文献前言随着科学技术的发展,各种新材料、新工艺和新技术的不断涌现,机械制造工艺正向着高质量、高生产率和低成本方向发展。
各种新工艺的出现,已突破传统的依靠机械能、切削力进行切削加工的范畴,可以加工各种难加工材料、复杂的型面和某些具有特殊要求的零件。
数控机床的问世,提高了更新频率的小批量零件和复杂的零件加工的生产率及加工精度。
特别是计算机技术的迅速发展,极大的推动了机械加工工艺的进步使工艺过程的自动化达到了一个新的阶段。
工具是人类文明进步的标志。
自20世纪末以来,现代制造技术与机械制造工艺自动化得到了很好的发展。
但工具(含刀具、夹具、量具与辅具等)在不断的革新中,起功能仍然十分显著。
机床夹具是一种装夹工件的工艺设备,它广泛地应用于机械制造过程的切削加工、热处理、装配、焊接和检测等工艺过程中。
在各种金属切削机床上用于装夹工件的工艺设备成为机床夹具,如车床上使用的三爪自定心卡盘、四爪卡盘,铣床上使用的平口虎钳等。
现代生产中,机床夹具是一种不可缺少的工艺装备,它直接影响着工件的加工精度、劳动生产率和产品的制造成本等。
因此,无论是在传统制造还是现代制造工艺系统中,夹具都是重要的工艺装备。
第一章夹具的总体方案设计1.1 对工件进行分析轴承盖的作用一是为了固定轴承进行轴向定位,二是起密封保护作用,防止轴承进入尘土等进入轴承造成损坏。
机床夹具设计步骤和实例

第2节机床夹具设计实例一、钻夹具的设计实例图2-2-20所示为杠杆类零件图样;图2-2-21所示为本零件工序图;1.零件本工序的加工要求分析①钻、扩、铰φ10H9孔及φ11孔;②φ10H9孔与φ28H7孔的距离为80±0. 2mm;平行度为;③φ11孔与φ28H7孔的距离为15±0. 25mm;④φ11孔与端面K距离为14mm;本工序前已加工的表面如下;①φ28H7孔及两端面;②φ10H9两端面;本工序使用机床为Z5125立钻,刀具为通用标准工具;2.确定夹具类型本工序所加工两孔φ10H9和φ11,位于互成90°的两平面内,孔径不大,工件质量较小、轮廓尺寸以及生产量不是很大,因此采用翻转式钻模;3.拟定定位方案和选择定位元件1定位方案;根据工件结构特点,其定位方案如下;①以φ28H7孔及一组合面端面K和φ10H9一端面组合而成为定位面,以φ10H9孔端外缘毛坯面一侧为防转定位面,限制六个自由度;这一定位方案,由于尺寸885.0mm公差大,定位不可靠,会引起较大的定位误差;如图2-2-22a②以孔φ28H7孔及端面K 定位,以φ11孔外缘毛坯一侧为防转定位面,限制工件六个自由度;为增加刚性,在φ10H9的端面增设一辅助支承,如图2-2-22 b 所示;比较上述两种定位方案,初步确定选用图2-2-22b 所示的方案; 2选择定位元件;①选择带台阶面的定位销,作为以φ28H7孔及其端面的定位元件,如图2-2-23所示;定位副配合取6728g H φ;②选择可调支承钉为φ11孔外缘毛坯一侧防转定位面的定位元件,如图2-2-24a 所示;也可选择如图2-2-24 b 所示移动V 形块;考虑结构简单,现选用图2-2-24a 所示结构;3定位误差计算①加工φ10H9孔时孔距尺寸80±mm 的定位误差计算;由于基准重合,故ΔB =0;基准位移误差为定位孔φ38021.00+mm 与定位销φ38007.0002.0--mm 的最大间隙,故ΔY=+0. 007+mm =;由此可知此定位方案能满足尺寸80±mm 的定位要求; ②加工φ10H9孔时轴线平行度的定位误差计算; 由于基准重合,故ΔB =0;基准位移误差是定位孔φ28H7与定位面K 间的垂直度误差;故ΔY =0.此方案能满足平行度0. 3mm 的定位要求;③加工φ11孔时孔距尺寸15±mm;加工φ11孔时与加工φ10H9孔时相同;此方案能满足孔距15± mm 的定位要求; 4.确定夹紧方案参考夹具资料,采用M12螺杆在φ28H7孔上端面夹紧工件; 5.确定引导元件钻套的类型及结构尺寸 ⑴对φH9孔,为适应钻、铰选用快换钻套;主要尺寸由机床夹具零、部件国家标准GB/T2263-80, GB/T2265-80选取;钻孔时钻套内径φ10028.0013.0++mm 、外径φ15012.0001.0++mm ;衬套内径φ15034.0014.0++mm,衬套外径φ22028.0015.0++mm;钻套端面至加工面的距离取8mm;麻花钻选用φ9. 80022.0-mm;2对φ11孔,钻套采用快换钻套;钻孔时钻套内径φ11034.0016.0++mm 、外径φ18012.0001.0++mm,衬套内径φ18034.0016.0++mm,外径φ26028.0015.0++mm ;钻套端面至加工面间的距离取12mm;麻花钻选用φ10. 80027.0-mm;各引导元件至定位元件间的位置尺寸分别为15±mm 和18±0. 05mm,各钻套轴线对基面的直线度允差为;6.夹具精度分析与计算由图2-2-22可知,所设计夹具需保证的加工要求有:尺寸15±mm ;尺寸80±mm ;尺寸14mm 及φ10H9孔和φ28H7孔轴线间平行度允差等四项;除尺寸14mm,因精度要求较低不必进行验算外,其余三项精度分别验算如下;1尺寸80±mm的精度校核;定位误差ΔD,由前已计算,已知Δ=;定位元件对底面的垂直度误差ΔA=;钻套与衬套间的最大配合间隙ΔT1=0. 033mm;衬套孔的距离公差ΔT2=;麻花钻与钻套内孔的间隙X2=;衬套轴线对底面F的垂直度误差ΔT3=0. 05mm;因而该夹具能保证尺寸80±0. 2mm的加工要求;2尺寸15±0. 25mm的精度校核;ΔD=0. 041mm,ΔA=0. 03mm,ΔT1=0. 033mm;衬套孔与定位元件的距离误差ΔT2=;麻花钻与钻套内孔的间隙X=;因而尺寸15±mm能够保证;3φ10H9轴线对φ25H7轴线的平行度的精度校核;ΔD=0. 03mm,ΔA=0. 03mm;衬套对底面F的垂直度误差ΔT=0. 05mm;因而此夹具能保证两孔轴线的平行度要求;7.绘制夹具总图根据已完成的夹具结构草图,进一步修改结构,完善视图后,绘制正式夹具总装图,如图2-2-23所示;8.绘制夹具零件图样从略;9.编写设计说明书 从略;二、铣床夹具设计实例图2-2-25所示为轴套类零件的零件图样;现需设计铣两槽52.00+mm 的铣夹具;1.零件本工序的加工要求分析本工序的加工要求,在实体上铣出两通槽,槽宽为52.00+mm,槽深为2703.0-mm,两槽在圆周方向互成60°±30′角度,表面粗糙度为Ra1. 25μm;本工序之前,外圆φ60021.0002.0++mm 、内孔φ32039.00+mm 及两端面均已加工完毕; 本工序采用φ5mm 标准键槽铣刀在X5l 立式铣床上,一次装夹六件进行加工; 2.确定夹具类型本工序所加工的是两条在圆周互成60°角的纵向槽,因此宜采用直线进给带分度装置的铣夹具;3.拟定定位方案和选择定位元件 1定位方案;①以φ32039.00+mm 内孔作为定位基准,再选孔端面为定位基准,限制工件五个自由度;如图2-2-26a 所示;为定②以φ60021.0002.0++mm 外圆位基准 以长V 形块为定位元件,限制4个自由度;如图2-2-26 b 所示;方案②由于V 形块的特性,所以较易保证槽的对称度要求,但对于实现多件夹紧和分度较困难;方案①的不足之处是由于心轴与孔之间有间隙、不易保证槽的对称度,且有过定位现象;但本工序加工要求井不高,而工件孔和两端面垂直精度又较高,故过定位现象影响不大;经上述分析比较,确定采用方案①;2选择定位元件;根据定位方式,采用带台肩的心轴;心轴安装工件部分的直径为φ32g6009.0025.0--mm,考虑同时安装6个工件,所以这部分长度取112mm,由于分度精度不高,为简化结构,在心轴上做出六方头,其相对两面间的距离尺寸取28g6007.0020.0+-mm,与固定在支座上的卡块槽28H7021.00+mm 相配合;加工完毕一个槽后,松开并取下心轴,转过相邻的一面再嵌入卡块槽内即实现分度;心轴通过两端φ25H6mm 柱部分安装在支座的V 形槽上,并通过M16螺栓钩形压板及锥面压紧,压紧力的方向与心轴轴线成45°角;mm 定位误差分析如下;3定位误差计算;工序尺寸270-5.0由于基准重合ΔB=0由于定位孔与心轴为任意边接触,则因此定位精度足够;由于加工要求不高,其他精度可不必计算;4.确定夹紧方案根据图2-2-26所示心轴结构,用M30螺母把工件轴向夹紧在心轴上;心轴的具体结构如图2-2-27所示;5.确定对刀装置1根据加工要求,采用GB/T2242-80直角对刀块;塞尺符合GB/T2244-mm;80,基本尺寸及偏差20014-.02计算对刀尺寸H和B如图2-2-28所示,计算时应把尺寸化为双向对称偏差,即6.夹具精度分析和计算本夹具总图上与工件加工精度直接有关的技术要求如下;定位心轴表面尺寸φ32g6;定位件与对刀间的位置尺寸±mm,±mm;定位心轴安装表面尺寸φ25h6;mm;对刀塞尺厚度尺寸20-014.0分度角度60°±10′;定位心轴轴线与夹具安装面、定位键侧平面间的平行度公差为0. lmm;分度装置工作表面对定位表面的对称度公差为0. 07mm;分度装置工作表面对夹具安装面垂直度公差为;对刀装置工作表面对夹具安装面的平行度和垂直度公差为0. 07mm;mm的精度分析;1尺寸270-5.0ΔD=0. 064mm定位误差前已计算;ΔT=0. 16mm定位件至对刀块间的尺寸公差;ΔA=1.0×20mm=定位心轴轴线与夹具底面平行度公差对工件尺寸的影233响;mm尺寸;故此夹具能保证270-5.02对60°±30′的精度分析;分度装置的转角误差可按下式计算;故此分度装置能满足加工精度要求;7.绘制夹具总图图2-2-27所示为本夹具的总装图样;8.绘制夹具零件图样从略;9.编写设计说明书从略;。
机床夹具设计步骤

主要特点是:结构简单轻巧,清除切屑方便,但每次须从工 件上装拆、比较费时。
对于体积大而笨重的工件,采用盖板式钻模尤为适宜。
五、滑柱式钻模
滑柱式钻模是一种标准化、规格化的通用钻模。钻模体可以 通用于较大范围的不同工件。设计时,只需根据不同的加工 对象设计相应的定位、夹紧元件。因此,可以简化设计工作。 另外,这种钻模不需另行设计专门的夹紧装置,夹紧工件方 便、迅速。
钻床夹具设计要点
3、当加工几个不在同心圆周上的平行孔系时,如工 件和夹具的总重量超过150N,宜采用固定式钻模在 摇臂钻床上加工。 4、对于孔的垂直度和孔距精度要求不高的中小型工 件,宜优先采用滑柱式钻模,以缩短夹具的设计周 期。如孔的垂直度公差小于0.1mm,孔距位置公差 小于±0.15mm时,如不采取特殊措施,一般不宜 采用这类钻模。
钻模的结构形式很多,按工件的结构形状、大小
和钻模的结构特点,钻模可分为以下几种:
一、固定式钻模
这类钻模在使用过程 中是被固定在机床工 作台上,因此这种钻 模的夹具体上,设有 专供夹压用的凸缘或 凸边。 一般用在立式钻床上 加工单孔或摇臂钻床 上加工轴线相互平行 的孔系。
二、翻转式钻模
这类钻模的特点就是整个工件和夹具可以一起翻转,可以 用来加工同方向的平行孔系,也可以用来加工不同方向的孔。
可换钻套用于大批量生产中, 由于钻套外圆与衬套内孔采用间 隙配合的关系,其加工精度不如 固定式钻套。
3、快换钻套
快换钻套更换迅速,只要将钻套逆时针转动一下,即 可从钻模板中取出。他与衬套的配合采用F7/m6或 F7/k6的间隙配合。
适用于在一个工序中使用 几种刀具(如钻、扩、铰) 依次连续加工的情况。
- 1、下载文档前请自行甄别文档内容的完整性,平台不提供额外的编辑、内容补充、找答案等附加服务。
- 2、"仅部分预览"的文档,不可在线预览部分如存在完整性等问题,可反馈申请退款(可完整预览的文档不适用该条件!)。
- 3、如文档侵犯您的权益,请联系客服反馈,我们会尽快为您处理(人工客服工作时间:9:00-18:30)。
设
H=30mm,h=12mm,B=18mm代
计
入,可求出e=0.038mm;
返回本节
未完待续……
返回主页
退出
夹具精度的验算
夹具精度验算实例:工件和夹具装配图
(一)验算中心距 120 0.05
影响此项精度的因素:
机
(5)刀具引偏量计算图
床
由于上述各项都是按最大的误差计算,实际上各
夹
项误差也不可能同时出现最大值,各误差方向也
机床夹具设计
主讲 毛国平
机械制造装备设计的典型步骤
第
二
1、需求分析
章
2、调查研究
机
(一)产品规划阶段 3、预测
械
4、可行性分析 5、编制设计任务书
制 造 装
备
1、对设计任务的抽象
设
2、建立功能结构 图1
计 方
(二)方案设计阶段 3、寻求原理解与解决方法
法
4、初步设计方案的形成 图3
5、初步设计方案的评价与筛选
返回本节
下一页
返回主页
退出
机械制造装备设计的典型步骤
第
二
章
1、确定结构原理方案
机
(三)技术设计阶段 2、总体设计
械
3、结构设计
制 造
装
备
1、零件图设计
设
2、完善装备图 (四)施工设计阶段 3、商品化设计
计 方 法
4、编制技术文档
返回本节
下一页
返回主页
退出
机床夹具设计步骤
退出
一、机床专用夹具的设计步骤
夹
(2)钻模板衬套中心与定位销中心距误差,
具
装配图标注尺寸为 120 ,0误.0差1m为m0.02mm;
设
(3)钻套与衬套的配合间隙 ,由 28H可6知/ g5
计
最大间隙为0.029mm;
(4)钻套内、外圆的同轴度误差,对于标准钻套
,精度较高,此项可以忽略。
返回本节
未完待续……
返回主页
退出
夹具精度的验算
具
很可能不一致,因此综合误差按概率法求和
设
0.052 0.022 0.0292 02 0.0352 mm 0.07mm
计
该项误差略大于中心距允差0.1 mm的2/3,勉强可 用。就减小定位和导向的配合间隙。
返回本节
下一页
返回主页
退出
夹具精度的验算
夹具精度验算实例:工件和夹具装配图
间位置精度;
夹
(3)定位表面与导向元件工作面间的位置精度;
具 设
(4)各导向元件工作面间的位置精度;
计
(5)定位表面、导向工作面与检测基准的位置精度。
返回本节
下一页
返回主页
退出
典型机床夹具的设计要求
退出
一、钻床夹具 二、镗床夹具 三、铣床夹具 四、车床夹具
机 床 夹 具 设 计
设 计
式中, 为 1max 3处6H最7大/ g间6隙(mm);
H1
为定位销轴定位面长度(mm).
返回本节
未完待续……
返回主页
退出
夹具精度的验算
夹具精度验算实例:工件和夹具装配图
(二)验算两孔平行度精度
工件要求 孔1全8H长7上允差0.05mm。
导致产生两孔平行度误差的因素有:
机
(2)定位销轴中心线对夹具底平面的垂直度 , 2
计
(mm),m为ax 刀具与钻套间的最大间隙。
上述各量可参见刀具引偏量计算图
返回本节
未完待续……
返回主页
退出
夹具精度的验算
夹具精度验算实例:工件和夹具装配图
(一)验算中心距 120 0.05
影响此项精度的因素:
机
(5)刀具引偏量计算图
床
夹
该例中,设刀具与钻套的配合为 18H6 / g5
具
可知 =0m.a0x 25mm;将
具
(3)夹具总体形式 。
设
(三)绘制夹具装配图
计
主视图按操作实际位置布置
三视图要清楚表达夹具工作原理与结构
(四)绘制夹具零件(非标准件)
夹具设计过程示例
返回本节
下一页
返回主页
退出
5
夹具精度的验算
影响位置精度的主要因素:
(1)工件在夹具中的安装误差:定位误差和夹紧误差
机
(2)夹具在机床上对定误差
下一页
返回主页
退出
夹具装配图上应标注的尺寸和技术条件
目的:为了检验本工序零件加工表面的形状,位置和尺
寸精度在夹具中是否可以达到;为了设计夹具零件图;
也为了夹具装配和装配精度的检测。
(一)尺寸标注
机
(1)轮廓尺寸 ;
床
(2)与机床的联系尺寸(安装);
夹
(3)与刀具的联系尺寸 ;
具
(4)配合尺寸、种类、精度 ;
机
二、夹具精度的验算
床
夹
三、夹具装配图上应标注的尺寸和技术条件
具 设
计
返回本章
上一页
返
下一页
回
主
页
一、机床专用夹具的设计步骤
(一)准备工作
(1)明确工件的年生产纲领 ;
(2)熟悉工件零件图和工序图 ;
(3)了解本工序的加工内容。 (二)总体方案的确定
(1)定位方案 ;
机 床 夹
(2)夹紧方案(力的作用点、方向、大小;机构);
夹具精度验算实例:工件和夹具装配图
(一)验算中心距 120 0.05
影响此项精度的因素:
机
(5)钻头与钻套间的间隙会引偏刀具,产生中心
床
距误差E,由下式求出 e ( H h B) max
夹
2
H
具
式中,e为刀具引偏量(mm),H为排屑空间,钻
设
套下端面与工件间的空间高度(mm),B为钻孔
图中没有注明。
床 夹
(3)钻套孔中心与定位销轴的平行度源自标注为0.02mm,3
0.02 rad 30
,图3中
具 设 计
(4)刀具引偏量e产生的偏斜角 因此,总的平行度误差
,4 刀H偏max计算图 。
(12
22
32合 格 4 2。) 12 ,
2,
3
返回本节
设
(5)各关键元件装配后的位置尺寸及公差。
计
上述联系尺寸和位置尺寸的公差,一般取工件的相应
公差1/3-1/10,最常用的是1/3。
返回本节
下一页
返回主页
退出
夹具装配图上应标注的尺寸和技术条件
(二)技术要求标注
(1)定位元件的定位表面间相互位置精度;
(2)定位元件的定位表面与夹具安装基面、定向基面
机 床
(二)验算两孔平行度精度
工件要求 1孔8H全7长上允差0.05mm。
机
导致产生两孔平行度误差的因素有:
床
(1)设计基准与定位基准重合,没有基准转换误
夹
差,但 36H配7合/ g间6 隙及孔与端面的垂直度
具
误差会产生基准位置误差,定位销轴中心与大头
孔中心的偏斜角 (r1ad)为
1
1max H1
床
(3)加工过程中出现的误差
夹 具
设
计
夹具精度验算:是指前两项,其和不大于工件允差的
2/3为算合格。
返回本节
未完待续……
返回主页
退出
夹具精度的验算
夹具精度验算实例:工件和夹具装配图
(一)验算中心距 120 0.05
影响此项精度的因素:
机
(1)定位误差主要是定位孔 3与6H定7位销
床
3的6间g 6隙产生,最大间隙为0.05mm;