夹具设计步骤要点
夹具设计流程

夹具设计流程夹具设计是制造业中非常重要的一环,它直接关系到产品的加工质量和生产效率。
在夹具设计过程中,需要考虑多种因素,包括产品的形状、材料、加工工艺等。
下面将介绍夹具设计的整个流程。
首先,夹具设计的第一步是需求分析。
在这一阶段,设计师需要与客户充分沟通,了解客户对产品的要求和需求。
这包括产品的尺寸、形状、材料等方面的要求。
同时,还需要考虑产品的加工工艺,以及生产线的实际情况。
第二步是方案设计。
在这一阶段,设计师需要根据需求分析的结果,制定夹具的设计方案。
这包括夹具的整体结构设计、夹具的工作原理、以及夹具的材料选择等。
设计师需要充分考虑产品的特点,以及生产线的实际情况,制定出最合理的设计方案。
第三步是细化设计。
在这一阶段,设计师需要对夹具的各个部件进行细化设计。
这包括夹具的各个零部件的尺寸设计、结构设计、以及材料选择等。
设计师需要充分考虑夹具的使用情况,以及生产线的实际情况,制定出最合理的细化设计方案。
第四步是制造加工。
在这一阶段,设计师需要将设计方案转化为实际的夹具产品。
这包括对夹具各个部件的加工制造,以及对夹具的组装调试等。
设计师需要充分考虑夹具的制造工艺,以及生产线的实际情况,确保夹具的制造质量。
第五步是试用调整。
在这一阶段,设计师需要对制造好的夹具进行试用调整。
这包括对夹具的使用情况进行测试,以及对夹具的性能进行调整。
设计师需要充分考虑夹具的使用效果,以及生产线的实际情况,确保夹具的使用效果达到预期。
最后一步是完善改进。
在这一阶段,设计师需要根据试用调整的结果,对夹具进行完善改进。
这包括对夹具的各个部件进行改进设计,以及对夹具的制造工艺进行改进。
设计师需要充分考虑夹具的实际使用情况,以及生产线的实际情况,确保夹具的性能达到最佳状态。
总之,夹具设计是一个复杂而又重要的工作,需要设计师充分考虑产品的特点,以及生产线的实际情况,制定出最合理的设计方案。
只有这样,才能确保夹具的质量和性能达到最佳状态,为产品的加工质量和生产效率提供最大的保障。
夹具设计方案

夹具设计方案夹具设计在制造业中扮演着重要的角色,它们被广泛应用于生产过程中的材料管理和加工环节。
本文将讨论夹具设计的基本原则和步骤,以及如何根据具体需求制定夹具设计方案。
一、夹具设计的基本原则夹具设计的主要目标是提供良好的夹持力和稳定性,以确保工件在加工过程中保持确定位置和姿态。
以下是夹具设计的基本原则:1. 合理使用工件特征:夹具设计应充分考虑到工件的几何形状、材料和加工需求,选择适当的夹持方式和夹具结构。
不同形状和材料的工件可能需要不同的夹具形式,如机械夹持、磁性夹持或真空吸附等。
2. 保证夹具刚性:夹具设计应尽可能提高夹具的刚性和稳定性,以减少变形和振动对工件加工的影响。
合理选择材料和结构,增加横向支撑和加强结构的刚性,能够有效提升夹具的工作性能。
3. 优化夹持力分配:夹具设计应合理分配夹持力,避免因夹持力不均匀导致工件变形或失稳。
在夹具结构中增加调节装置,根据工件的形状和加工要求进行调整,能够提高夹持力的均匀分布。
4. 考虑夹具调节和固定:夹具设计应充分考虑调节和固定的需求,以适应不同尺寸、形状和数量的工件加工。
通过增加可调节的支撑和固定装置,能够提高夹具的灵活性和适应性。
二、夹具设计的步骤1. 确定需求:在进行夹具设计之前,需要明确工艺流程和工件加工的具体要求,了解工件的形状、尺寸和材料特性。
2. 进行夹具定位:根据工件的几何特征和加工要求,确定夹具的定位方式和位置,确保工件在加工过程中的稳定性和精度。
3. 设计夹具结构:根据工件的形状和尺寸,选择合适的夹持方式和夹具结构。
考虑夹具的刚性、稳定性和调整能力,进行夹具的整体设计。
4. 验证夹具设计:进行夹具设计的仿真分析或实际测试,验证夹具的夹持力和稳定性,确保夹具设计满足工件加工的需求。
5. 优化夹具设计:根据测试结果和实际使用情况,对夹具设计进行优化和改进。
通过调整夹具结构、材料和调节装置,提高夹具的工作效率和适应性。
三、夹具设计方案应根据具体的需求和工艺流程来制定。
夹具设计的要求方法和步骤

夹具设计的要求方法和步骤-CAL-FENGHAI-(2020YEAR-YICAI)_JINGBIAN夹具设计的要求方法和步骤一、夹具设计的要求夹具设计时,应满足以下主要要求:1.夹具应满足零件加工工序的精度要求。
特别对于精加玉工序,应适当提高夹具的精度,以保证工件的尺寸公差和形状位置公差等。
2.夹具应达到加工生产率的要求。
特别对于大批量生产中使用的夹具,应设法缩短加工的基本时间和辅助时间。
3.夹具的操作要方便、安全。
按不同的加工方法,可设置必要的防护装置、挡屑板以及各种安全器具。
4.能保证夹具一定的使用寿命和较低的夹具制造成本。
夹具元件的材料选择将直接影响夹具的使用寿命。
因此,定位元件以及主要元件宜采用力学性能较好的材料。
夹具的低成本设计,目前在世界各国都已相当重视。
为此,夹具的复杂程度应与工件的生产批量相适应。
在大批量生产中,宜采用如气压、液压等高效夹紧装置;而小批量生产中,则宜采用较简单的夹具结构。
5.要适当提高夹具元件的通用化和标准化程度。
选用标准化元件,特别应选用商品化的标准元件,以缩短夹具制造周期,降低夹具成本。
6.具有良好的结构工艺性,以便于夹具的制造、使用和维修。
以上要求有时是相互矛盾的,故应在全面考虑的基础上,处理好主要矛盾,使之达到较好的效果。
例如钻模设计中,通常侧重于生产率的要求;镗模等精加工用的夹具则侧重于加工精度的要求等。
二、夹具设计的方法夹具设计主要是绘制所需的图样,同时制订有关的技术要求。
夹具设计是一种相互关联的、工作,它涉及到很广的知识面。
通常,设计者在参阅有关典型夹具图样的基础上,按加工要求构思出设计方案,再经修改,最后确定夹具的结构。
其设计方法可用图5-1表示。
显然,夹具设计的过程中存在着许多重复的劳动。
近年来,迅速发展的机床夹具计算机辅助设计(CAD),为克服传统设计方法的缺点提供了新的途径。
三、夹具设计的步骤夹具的设计步骤可以划分为六个阶段:1.设计的准备这一阶段的工作是收集原始资料、明确设计任务。
机床夹具设计步骤和实例

机床夹具设计步骤和实例机床夹具是用于在机床上夹持工件或刀具的装置,用于保持工件的位置稳定,使其能够被加工。
机床夹具设计的步骤主要包括需求分析、夹具类型选择、夹具基础结构设计、夹具强度计算、夹具定位系统设计、夹具操作系统设计、夹具零件设计和夹具组装等。
以下为机床夹具设计步骤和一个实例:步骤1:需求分析首先,需要了解加工工件的要求和工艺流程。
通过与工艺人员或工程师的交流,了解工件的形状、材料、尺寸等特性,以及工件的精度要求、加工工艺和工时要求等。
根据需求分析,明确夹具的基本功能、定位方式和操作方式。
步骤2:夹具类型选择根据加工工件的特性和加工工艺的要求,通过参考手册或专业书籍选择合适的夹具类型。
常见的夹具类型包括平板夹具、顶升夹具、转角夹具、滑块夹具、气垫夹具等。
根据不同的工件形状和加工要求,选择适合的夹具类型。
步骤3:夹具基础结构设计根据工件的形状和夹持要求,设计夹具的基础结构。
夹具的基础结构通常由夹紧装置、支撑装置和定位装置组成。
夹紧装置主要用于夹持工件,支撑装置用于保持工件的平衡和稳定,定位装置用于确保工件的位置准确。
步骤4:夹具强度计算根据夹具类型和加工工件的特性,计算夹具的强度。
夹具的强度计算包括静态强度和动态强度两个方面。
静态强度主要考虑夹具在夹持工件时的受力情况,包括切削力、惯性力等;动态强度主要考虑夹具在工件加工过程中的振动和冲击力,保证夹具结构能够承受夹持工件时的各种力。
步骤5:夹具定位系统设计根据工件的定位要求,设计夹具的定位系统。
夹具的定位系统应能够满足工件的精度要求,并确保工件的位置准确。
定位系统常采用定位销、定位块等形式,根据工件的形状和加工特点选择合适的定位方式。
步骤6:夹具操作系统设计根据夹具的使用要求,设计夹具的操作系统。
夹具的操作系统主要包括夹紧装置的控制方式和操作机构的设计。
根据夹紧力的大小和控制精度的要求,选择合适的液压夹紧系统或气动夹紧系统。
步骤7:夹具零件设计根据夹具的基础结构、定位系统和操作系统的设计要求,设计夹具的各个零件。
专用夹具设计方法和步骤

1、明确设计任务,收集设计资料
2、拟订夹具结构方案,绘制夹具草图
(1)确定工件的定位方案,设计定位装置,并对夹紧力进行估算,以确保夹紧可靠
(2)确定工件的夹紧方案,设计夹紧装置
(3)确定刀具的引导方式,选择或设计引导元件或对刀元件
(4)确定其他元件或装置的结构形式,如定位键、分度装置等
(5)确定夹具的总体结构及夹具在机床上的安装方式。
对夹具的总体结构最好能拟订出几个不同的方案,画出草图,经过分析比较,选择最佳方案
3、绘制夹具总图
(1)选择操作者工作时正对的位置为主视图
(2)用双点划线将工件的外形轮廓、定位基面、夹紧表面以及加工表面画在各视图相应的位置上,待加工面上的加工余量可用网纹线表示。
在夹具总图中,工件可看作透明体,不遮挡后面的线条
(3)依次画出定位、夹紧、导向元件或装置的具体结构,再画出夹具体,将各元件或装置连成一个整体
(4)在总图上标注尺寸(包括轮廓尺寸、联系尺寸、重要的配合尺寸等)、公差和技术要求
(5)绘制夹具零件图。
在夹具中的非标准零件都要绘制零件图,并按总图要求确定零件的尺寸、公差及技术条件
三、夹具总图技术要求的制订
1、夹具总图上应标注的尺寸和公差
(1)夹具外形的最大轮廓尺寸
(2)影响定位精度的尺寸
(3)影响对刀精度的尺寸和公差
(4)影响夹具在机床上安装精度的尺寸和公差
(5)影响夹具精度的尺寸和公差
(6)其他装配尺寸及公差
2、夹具总图上公差值的确定
(1)与加工尺寸有直接对应关系的夹具公差δJ (2)其他装配尺寸的配合性质及公差等级
3、夹具总图上应标注
4、的技术要求。
夹具设计课程设计
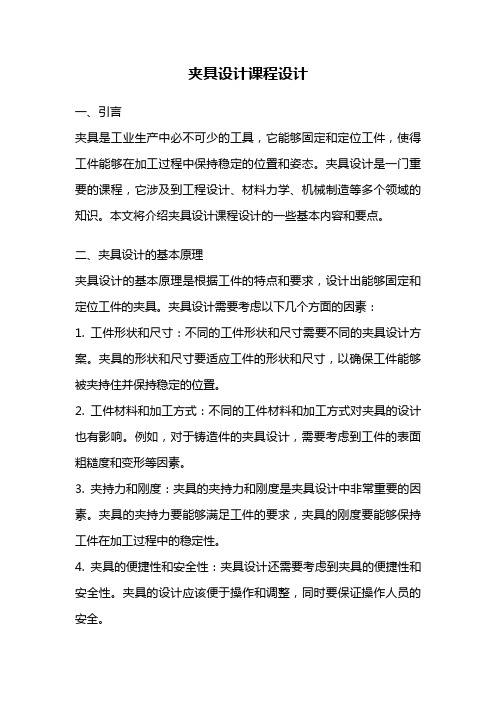
夹具设计课程设计一、引言夹具是工业生产中必不可少的工具,它能够固定和定位工件,使得工件能够在加工过程中保持稳定的位置和姿态。
夹具设计是一门重要的课程,它涉及到工程设计、材料力学、机械制造等多个领域的知识。
本文将介绍夹具设计课程设计的一些基本内容和要点。
二、夹具设计的基本原理夹具设计的基本原理是根据工件的特点和要求,设计出能够固定和定位工件的夹具。
夹具设计需要考虑以下几个方面的因素:1. 工件形状和尺寸:不同的工件形状和尺寸需要不同的夹具设计方案。
夹具的形状和尺寸要适应工件的形状和尺寸,以确保工件能够被夹持住并保持稳定的位置。
2. 工件材料和加工方式:不同的工件材料和加工方式对夹具的设计也有影响。
例如,对于铸造件的夹具设计,需要考虑到工件的表面粗糙度和变形等因素。
3. 夹持力和刚度:夹具的夹持力和刚度是夹具设计中非常重要的因素。
夹具的夹持力要能够满足工件的要求,夹具的刚度要能够保持工件在加工过程中的稳定性。
4. 夹具的便捷性和安全性:夹具设计还需要考虑到夹具的便捷性和安全性。
夹具的设计应该便于操作和调整,同时要保证操作人员的安全。
三、夹具设计的步骤夹具设计通常包括以下几个步骤:1. 分析工件特点和要求:首先需要对工件的特点和要求进行分析,包括工件的形状、尺寸、材料、加工方式等因素。
2. 确定夹具类型:根据工件的特点和要求,确定适合的夹具类型,例如夹盘式夹具、夹具夹持夹具、夹具卡盘夹具等。
3. 设计夹具结构:根据夹具类型和工件特点,设计夹具的结构,包括夹具的底座、夹持装置、工件定位装置等。
4. 计算夹具参数:根据工件的特点和夹具结构,计算夹具的夹持力、刚度等参数,以确保夹具能够满足工件的要求。
5. 绘制夹具图纸:根据夹具设计的结果,绘制夹具的详细图纸,包括三视图、剖视图、部件图等。
6. 制造夹具:根据夹具图纸,制造夹具的各个部件,并进行装配和调试。
四、夹具设计的案例分析以一个简单的工件为例,设计一个夹具来固定和定位该工件。
夹具设计步骤范文
夹具设计步骤范文夹具设计是一门综合性比较强的工程技术,它是物质生产设备和加工自动化的重要组成部分。
夹具设计步骤十分复杂,需要考虑多个因素,如工件的形状、尺寸、材质,加工方式,使用环境等等。
下面将详细介绍夹具设计的步骤。
第一步:明确设计目标和限制条件在开始夹具设计之前,需要明确设计的目标和限制条件。
设计目标可以是提高生产效率、降低成本、改善工作环境等,而限制条件包括工件的尺寸、材质、形状,加工方式,工艺流程等。
第二步:收集和分析工艺信息在进行夹具设计之前,需要收集和分析与工艺相关的信息。
这些信息可以来自工艺工程、制造工程和质量工程等。
通过分析这些信息,可以了解加工过程中夹具所起的作用和工件的具体要求,有助于夹具设计的决策。
第三步:定义工艺方案根据工艺信息的分析结果,可以定义出适合的工艺方案。
工艺方案可以包括夹具的类型、结构、布局和位置等。
需要根据工件的形状、尺寸和要求确定夹具的结构特点和机构形式。
第四步:进行夹具定型设计在夹具定型设计中,首先进行夹具的分段设计。
根据工艺方案,将夹具划分为若干个模块,并确定每个模块的功能和位置。
然后进行夹具的刚度计算和刚度校核,以保证其稳定性和刚性。
第五步:进行夹具的选择和优化在进行夹具选型和优化时,需要根据工件的特点和加工方式,选择适合的夹具类型和结构。
同时可以优化夹具的设计,减少夹具的重量和材料消耗,提高夹具的使用寿命和可靠性。
第六步:进行夹具的详细设计和制造在夹具的详细设计和制造过程中,需要进行夹具的零部件设计和装配设计。
可以使用计算机辅助设计(CAD)软件进行夹具的三维建模和装配。
然后根据夹具的设计图纸进行夹具的制造和装配。
第七步:进行夹具的试用和调试在夹具的试用和调试阶段,需要进行夹具的功能验证和性能测试。
可以通过对夹具的各个部位和功能进行测试,评估其工作的稳定性和可靠性。
同时还需要对夹具进行优化和改进,以满足加工要求。
第八步:进行夹具的验收和使用在夹具的验收和使用阶段,需要对夹具进行全面的检查和测试,确保其符合设计要求和技术规范。
机床夹具的设计步骤
机床夹具的设计步骤一、夹具的设计步骤1.设计准备工作——研究原始资料,明确设计要求和生产条件(1)生产纲领(生产类型)——了解生产批量和对夹具的需用情况;(2)零件图及工序图——了解工件情况、工序要求和加工状态;(3)零件的工艺规程——了解所用机床、刀具等的情况;(4)夹具制造能力——了解夹具制造车间的生产条件和技术现状(5)典型夹具结构及标准——同类型产品的夹具结构、有关夹具标准。
2.确定夹具的结构方案(总体方案)主要包括:(1)确定工件的定位方案,设计定位装置。
根据六点定位原理,确定工件的定位方式,选择和设计定位元件,计算定位误差。
(2)确定工件的夹紧方案,设计夹紧装置。
确定夹紧力、夹紧机构及动力装置。
(3)确定对刀或导向方案,设计对刀或导向装置。
对刀块或钻套、镗套等的设计。
(4)确定其它元件或装置的结构形式。
定位键、分度装置、连接元件等。
(5)协调各装置、元件的布局,确定夹具在机床上的安装方式以及夹具体的结构型式。
3.绘制夹具装配图按照国家制图标准绘制,应清楚表达出夹具的结构及各装置、元件之间的位置关系。
主视图应取操作者实际工作时的位置。
具体方法和步骤如下:(1)在装配图上,工件看作透明体,用双点划线将工件的外形轮廓、定位基面、夹紧表面及加工表面绘制在各个视图的合适位置上。
(2)依次绘出定位元件或装置、夹紧元件或装置、对刀或导向元件、其它元件、夹具体及连接元件。
(3)标注必要的尺寸、公差和技术要求。
(4)编制夹具明细表及标题栏。
图5-69 实例4.绘制夹具零件图。
画出夹具中非标零件图,并按夹具装配图的要求确定零件的尺寸、公差及技术要求。
——尺寸及公差、形位公差、表面粗糙度等标注要完整、正确。
二、夹具精度校核使用专用夹具加工工件时,影响加工精度的误差因素主要有三个方面:①工件在夹具中的安装误差,包括定位误差、夹紧误差(工件及夹具的夹紧变形)、夹具制造误差、导向误差等;②对定误差,即夹具在机床上的安装误差;③加工过程误差,与切削过程有关的误差。
毕业夹具设计
毕业夹具设计夹具是指为了完成某一种或多种工艺过程,夹住工件和工艺工具,使之具有一定空间和方位关系,并在加工过程中保证工件位置、工艺工具位置、相互位置精度均保持稳定的装置。
夹具设计作为制造工艺的重要环节,直接影响着加工质量和效率。
下面我将介绍一下夹具设计的一般步骤和注意事项。
1. 夹具设计的一般步骤夹具设计的一般步骤包括以下几个方面:确定夹持原则、确定夹持形式、确定夹具类型、确定夹具定位原理、确定夹具结构、进行夹具零件设计、进行夹具总装。
2. 夹具设计的注意事项(1)确定夹持原则:根据工件的特点和工艺要求,确定夹持原则是夹具设计的第一步。
夹持原则直接影响着夹具的使用效果和加工质量。
在确定夹持原则时,需要考虑工件形状、尺寸、材料等因素。
(2)确定夹持形式:夹具的夹持形式多种多样,常见的有机械夹持、液压夹持、真空吸盘夹持等。
在确定夹持形式时,需要考虑工件的特点和工艺要求,选择最适合的夹持方式。
(3)确定夹具类型:根据工件的特点和工艺要求,选择适合的夹具类型。
常见的夹具类型有万能夹具、专用夹具、定位夹具等。
在确定夹具类型时,需考虑夹具的灵活性、可靠性和成本等因素。
(4)确定夹具定位原理:夹具的定位原理是夹具设计的重要环节,它直接影响着工件的定位精度和加工质量。
在确定夹具定位原理时,需要考虑工件的特点、加工要求和夹具结构等因素。
(5)确定夹具结构:夹具结构是夹具设计的核心内容,直接关系到夹具的使用效果和加工质量。
在确定夹具结构时,需要考虑夹具组成部件的形状、尺寸、材料等因素。
同时,还需要考虑夹具的拆装、调整和维护等方面的要求。
(6)进行夹具零件设计:夹具零件设计是夹具设计的具体实施过程,包括夹具底座、夹具活动件、夹具固定件等零部件的设计。
在进行夹具零件设计时,需要考虑夹具的材料、加工工艺和力学性能等因素。
(7)进行夹具总装:夹具总装是将夹具零部件按照设计要求进行装配组装的过程。
在进行夹具总装时,需要保证夹具组成部件之间的精度和配合度,确保夹具的使用效果和加工质量。
夹具设计步骤要点
一、机床夹具设计要求1.保证工件加工的各项技术要求要求正确确定定位方案、夹紧方案,正确确定刀具的导向方式,合理制定夹具的技术要求,必要时要进行误差分析与计算。
2.具有较高的生产效率和较低的制造成本为提高生产效率,应尽量采用多件夹紧、联动夹紧等高效夹具,但结构应尽量简单,造价要低廉。
3.尽量选用标准化零部件尽量选用标准夹具元件和标准件,这样可以缩短夹具的设计制造周期,提高夹具设计质量和降低夹具制造成本。
4.夹具操作方便安全、省力为便于操作,操作手柄一般应放在右边或前面;为便于夹紧工件,操纵夹紧件的手柄或扳手在操作范围内应有足够的活动空间;为减轻工人劳动强度,在条件允许的情况下,应尽量采用气动、液压等机械化夹紧装置。
5.夹具应具有良好的结构工艺性所设计的夹具应便于制造、检验、装配、调整和维修。
二、机床夹具设计的内容及步骤1.明确设计要求,收集和研究有关资料在接到夹具设计任务书后,首先要仔细阅读加工件的零件图和与之有关的部件装配图,了解零件的作用、结构特点和技术要求;其次,要认真研究加工件的工艺规程,充分了解本工序的加工内容和加工要求,了解本工序使用的机床和刀具,研究分析夹具设计任务书上所选用的定位基准和工序尺寸。
2.确定夹具的结构方案1〕确定定位方案,选择定位元件,计算定位误差。
2〕确定对刀或导向方式,选择对刀块或导向元件。
3〕确定夹紧方案,选择夹紧机构。
4〕确定夹具其他组成部分的结构形式,例如分度装置、夹具和机床的连接方式等。
5〕确定夹具体的形式和夹具的总体结构。
在确定夹具结构方案的过程中,应提出几种不同的方案进行比较分析,选取其中最为合理的结构方案。
3.绘制夹具的装配草图和装配图夹具总图绘制比例除特殊情况外,一般均应按1:1绘制,以使所设计夹具有良好的直观性。
总图上的主视图,应尽量选取与操作者正对的位置。
绘制夹具装配图可按如下顺序进行:用双点划线画出工件的外形轮廓和定位面、加工面;画出定位元件和导向元件;按夹紧状态画出夹紧装置;画出其他元件或机构;最后画出夹具体,把上述各组成部分联结成一体,形成完整的夹具。
- 1、下载文档前请自行甄别文档内容的完整性,平台不提供额外的编辑、内容补充、找答案等附加服务。
- 2、"仅部分预览"的文档,不可在线预览部分如存在完整性等问题,可反馈申请退款(可完整预览的文档不适用该条件!)。
- 3、如文档侵犯您的权益,请联系客服反馈,我们会尽快为您处理(人工客服工作时间:9:00-18:30)。
一、机床夹具设计要求1.保证工件加工的各项技术要求要求正确确定定位方案、夹紧方案,正确确定刀具的导向方式,合理制定夹具的技术要求,必要时要进行误差分析与计算。
2.具有较高的生产效率和较低的制造成本为提高生产效率,应尽量采用多件夹紧、联动夹紧等高效夹具,但结构应尽量简单,造价要低廉。
3.尽量选用标准化零部件尽量选用标准夹具元件和标准件,这样可以缩短夹具的设计制造周期,提高夹具设计质量和降低夹具制造成本。
4.夹具操作方便安全、省力为便于操作,操作手柄一般应放在右边或前面;为便于夹紧工件,操纵夹紧件的手柄或扳手在操作范围内应有足够的活动空间;为减轻工人劳动强度,在条件允许的情况下,应尽量采用气动、液压等机械化夹紧装置。
5.夹具应具有良好的结构工艺性所设计的夹具应便于制造、检验、装配、调整和维修。
二、机床夹具设计的内容及步骤1.明确设计要求,收集和研究有关资料在接到夹具设计任务书后,首先要仔细阅读加工件的零件图和与之有关的部件装配图,了解零件的作用、结构特点和技术要求;其次,要认真研究加工件的工艺规程,充分了解本工序的加工内容和加工要求,了解本工序使用的机床和刀具,研究分析夹具设计任务书上所选用的定位基准和工序尺寸。
2.确定夹具的结构方案1)确定定位方案,选择定位元件,计算定位误差。
2)确定对刀或导向方式,选择对刀块或导向元件。
3)确定夹紧方案,选择夹紧机构。
4)确定夹具其他组成部分的结构形式,例如分度装置、夹具和机床的连接方式等。
5)确定夹具体的形式和夹具的总体结构。
在确定夹具结构方案的过程中,应提出几种不同的方案进行比较分析,选取其中最为合理的结构方案。
3.绘制夹具的装配草图和装配图夹具总图绘制比例除特殊情况外,一般均应按1:1绘制,以使所设计夹具有良好的直观性。
总图上的主视图,应尽量选取与操作者正对的位置。
绘制夹具装配图可按如下顺序进行:用双点划线画出工件的外形轮廓和定位面、加工面;画出定位元件和导向元件;按夹紧状态画出夹紧装置;画出其他元件或机构;最后画出夹具体,把上述各组成部分联结成一体,形成完整的夹具。
在夹具装配图中,被加工件视为透明体。
4.确定并标注有关尺寸、配合及技术要求1)夹具总装配图上应标注的尺寸① 工件与定位元件间的联系尺寸,例如,工件基准孔与夹具定位销的配合尺寸。
② 夹具与刀具的联系尺寸,例如,对刀块与定位元件之间的位置尺寸及公差,钻套。
锤套与定位元件之间的位置尺寸及公差。
③ 夹具与机床联接部分的尺寸,对于铣床夹具是指定位键与铣床工作台T 型槽的配合尺寸及公差,对于车、磨床夹具指的是夹具联接到机床主轴端的联接尺寸及公差。
④ 夹具内部的联系尺寸及关键件配合尺寸,例如,定位元件间的位置尺寸,定位元件与夹具体的配合尺寸等。
⑤ 夹具外形轮廓尺寸。
2)确定夹具技术条件在装配图上需要标出与工序尺寸精度直接有关的下列各有关夹具元件之间的相互位置精度要求。
① 定位元件之间的相互位置要求。
② 定位元件与联接元件(夹具以联接元件与机床相联)或找正基面间的相互位置精度要求。
③ 对刀元件与联接元件(或找正基面)间的相互位置精度要求。
④ 定位元件与导向元件的位置精度要求。
5.绘制夹具零件图绘制装配图中非标准零件的零件图,其视图应尽可能与装配图上的位置一致。
6.编写夹具设计说明书§4—1 夹具的对定一、夹具的对定概念:使夹具相对于机床、相对于机床上的刀具、相对于机床上刀具的切削成型运动,处于正确的空间位置的过程。
夹具在机床上的对定(对定装置实现)包括三方面的内容夹具的对刀(对刀块实现)夹具的转位及其分度位置的确定(设计)二、夹具与机床的连接两种连接形式:1、安装在工作台面上——有工作台的机床如铣床夹具1)、用定位键为了确定夹具与机床工作台的相对位置,在夹具体的底面上应设置定位键。
用沉头螺钉固定在夹具体底面纵向槽的两端,通过定位键与铣床工作台上的T 形槽配合,确定了夹具在机床上的正确位置。
两定位键的距离尽可能布置得远些。
定位键可承受铣削产生的扭转力矩,减轻夹具的螺栓的负荷,夹具体也装有定位键。
定位键有矩形和圆形两种,如图12-34所示。
常用的是矩形定位键,其结构尺寸已标准化,可参阅“夹具标准”(GB/T2206—91)。
⑴矩形定位键矩形定位键有两种结构型式:A型(图12-34a)和B型(图12-34b)。
A型定位键的宽度,按统一尺寸B制作,其公差为h6或h8,适用于夹具的定向精度要求不高场合,B型定位键的侧面开有沟槽,沟槽的上部与夹具体的键槽配合,其宽度尺寸B按H7/ h6或JS6/h6与键槽相配合,沟槽的下部宽度为B1,与铣床工作台T形槽配合,因为T形槽公差为H8或H7,故B1一般按h8或h6制造,为了提高夹具的定位精度,在制造定位键时,B1应留有磨量0.5mm,以便与工作台T形槽修配。
⑵圆形定位键如图12-34d所示,圆形定位键小型夹具中,这种定位键制造方便,但容易磨损,定位稳定性不如矩形定位键好,故应用不多。
2)、定向键与定位键不同的是:定位键安装在夹具体上,专用;定向键安装在机床的T 形槽中。
3)、直接调装用找正夹具的方法安装(需找正三个方向),需实际工作经验,费时,但精度高(可消除其他中间环节的影响)。
2、安装在机床主轴上(以车床为例)因为夹具的回转精度主要是由夹具同车床主轴的联接精度来决定的。
所以,要求夹具的回转轴线与车床主轴轴线,有尽可能高的同轴度。
根据车床夹具径向尺寸大小,其在机床主轴的安装一般有两种方式:(1)用锥柄联接对于径向尺寸D小于140mm,或D<(2-3)d的小型夹具,一般通过锥柄安装在车床主轴锥孔中,并用螺栓拉紧。
这种联接方式定心精度较高。
(2)用过渡盘联接(CA6140、CW6140等新式车床的连接形式)对于径向尺寸较大的夹具,一般通过过渡盘与车床主轴轴颈联接。
这种联接结构如图所示。
夹具体通过定位面按最小间隙为零的间隙配合(H7/h6)或者过渡配合(H7/js6)装配在过渡盘的凸缘上,然后用螺钉紧固。
过渡盘与车床主轴的联接形式取决车床主轴的前端结构。
图b的联接形式是:过渡盘上与机床主轴相配合的定位内孔按(H7/h6)或(h7/js6)与主轴轴颈相配合,并同时有螺纹与主轴相联接。
为了安全,可在此基础上采用其它措施,把过渡盘和主轴固紧在一起,防止倒车时使过渡盘与主轴的联接松开。
1—过渡盘2—平键3—螺母 4—夹具 5—主轴如果主轴前端为圆锥体并有凸缘结构,如图c所示,则过渡盘1以锥体定心,用套在主轴上的螺母3锁紧。
旋转运动的转矩则由平键2传递给过渡盘。
这种结构定心精度高。
(3)用平面短销连接C620、C630车床用这种连接形式。
(4)平面短锥销连接利用主轴前端的短锥体及轴肩端面实现的对定连接,而且是利用重复定位实现两者间的稳固连接。
§4—2 夹具的对刀夹具一般多用于大批量、高效率生产中,而高效率往往伴随着刀具的高效磨损,特别是在工件粗加工过程当中,换刀、调刀对刀成为正常生产的主要内容。
1、定义:夹具的对刀:是指夹具的定位系统相对刀具应满足本工序对刀尺寸的要求。
这一工作称为夹具的对刀。
2、对刀方法:找正调整对刀专用样板调刀试件检验对刀专门对刀装置对刀3.对刀装置(以铣床夹具为例)对刀装置(根据情况,自行设计)1)、组成专用对刀块(可采用标准对刀块,亦可自行设计)对刀塞尺2)、对刀元件对刀元件是用来确定刀具与夹具的相对位置的元件。
其由对刀块和塞尺寸组成。
如(4-1)中铣床对刀块2。
常见标准对刀块有:方形对刀块图b,调整铣刀两相互垂直凹面。
直角对刀块图c调整刀具两相互垂直凸面,侧装对刀块图d,装在夹具侧面,在加工两相互垂直面或铣槽时作对刀用。
具体结构尺寸可参阅“夹具标准”(铣刀不能与对刀块的工作表面直接接触,以免损坏切削刃或造成对刀块过早磨损,而应通过塞尺来校准它们之间的相互位置,即将塞尺放在刀具与对刀图表示各种对刀块使用情况。
图cd是用于铣成形面的特殊对刀块。
下图cd是用于铣成形面的特殊对刀块。
各种对刀块使用举例对于加工精度要求较高的工件,要检首件,最后确定刀具的位是否准确置。
或者不设置对刀元件采用找正法确定定位元件相对刀具位置,或采用试切法。
4、对刀塞尺:可自行设计,也可采用标准塞尺(P118 图4-7)对刀平塞尺(JB/T8032。
1——1995)厚度:1、2、3、4、5mm公差取h8对刀圆塞尺(JB/T8032。
2——1995):应用于曲面或成型刀具对刀的场合。
d=3~5mm,公差取h8。
对刀用的标准塞尺5、夹具的对定误差:△≦1/3T△=△+△≦1/3T这是夹具调装精度及对刀精度要求。
6、小结§4—3 夹具的转位及其对定机构一、常用转位分度及其对定机构1、夹具的转位问题的提出像这样的工件:沿着直线方向等距分布着一些等径的孔或槽,在同一圆周上分布着的等径的孔或槽,要求工件在一次装夹的情况下将所有的孔或槽全部加工完,这时夹具就要带动工件进行数次的移动或转动,完成工件的加工,夹具所具有的这种功能称为夹具的转位。
定义:夹具带动工件所进行的加工位置转换动作称为夹具的转位。
直线移动分类回转运动2、夹具的分度工件在一次装夹中.每加工完一个表面之后,通过夹具上可动部分连同工件一起转过一定的角度或移动一定距离,以改变加工表面的位置。
实现上述分度要求的装置称为分度装置。
分度装置能使工序集中,减少安装次数,从而减轻劳动强度和提高生产率,因而广泛用于钻、铣、车、镗等加工中。
①定义:把对转位的严格控制称为夹具的分度。
②作用:对工件一次装夹实现多工位加工。
夹具的分度是靠专门设置的分度装置来完成的,而对分度运动部件相对夹具体的位置,是靠夹具的分度对定机构来完成的。
分度装置直线分度: 对直线尺寸进行分度,适用于沿直线分度的孔和槽回转分度: 对圆周角进行分度,适用于沿圆周分度的孔和槽生产实践中以回转式分度装置应用较多,故本章主要介绍回转式分度装置。
3、回转分度装置的一般结构组成:转动部分、分度对定机构、抬起与锁紧机构、固定部分、润滑部分1)、转位分度机构:分度装置的运动件,包括分度盘、衬套和转轴(转动部分)等。
材料:45#、 40Cr淬火HRC40—4520钢渗碳淬火,HRC58—632)、分度对定机构分度对定机构确保是转动部分相对固定部分得到一个正确的定位。
如图4-12所示件2、4,分度对定销5等组成了分度对定销机构。
分度盘与分度装置的转动部分相连,对定销与分度装置的固定部分相连。
(1)构成:操纵组件、对定销(2)作用:对分度盘进行定位3)、分度盘抬起(大型分度机构)与锁紧机构分度装置经分度以后,锁紧机构应使夹具的转动部分锁紧在固定部分。
其目的是为了增强分度装置工作时的刚性及稳定性,防止加工时受切削力引起振动。
如图4-12所示,螺母1就起锁紧作用。