汽车设计的未来趋势-轻量化材料
汽车车身设计及制造工艺新技术分析

汽车车身设计及制造工艺新技术分析随着汽车行业的不断发展,车身设计及制造工艺技术也在不断地更新和升级。
在这篇文章中,我们将对汽车车身设计及制造工艺新技术进行分析,探讨其对汽车行业的影响以及未来的发展趋势。
一、汽车车身设计新技术分析1. 轻量化设计技术随着环保意识的增强和能源危机的加剧,轻量化设计技术成为汽车行业的热门话题。
轻量化设计通过采用更轻、更坚固的材料来减轻车身重量,达到降低燃油消耗、提高能源利用率的目的。
目前,碳纤维复合材料、铝合金和镁合金等新材料的应用成为轻量化设计的主要趋势。
这些新材料具有密度低、强度高的特点,能够在保证车身安全性的前提下显著减少整车重量,提高汽车的动力性能和燃油经济性。
2. 智能化设计技术随着人工智能和大数据技术的快速发展,智能化设计技术也逐渐在汽车行业中得到应用。
智能化设计技术通过借助计算机仿真和虚拟现实技术,实现对车身结构的优化设计和自动化生产。
这种技术能够提高设计效率,降低成本,同时还能够更精确地预测车身在碰撞、扭曲等情况下的变形和破坏情况,为车身设计和工艺提供更科学的依据。
3. 模块化设计技术随着汽车产品线不断丰富和多样化,模块化设计技术成为一种普遍的设计趋势。
模块化设计技术能够将车身结构分割成不同的模块,并且通过标准化和通用化的设计,使得不同车型之间的共用率提高,降低制造成本。
模块化设计技术还能够提高生产效率,减少生产周期,更好地适应市场需求的快速变化。
二、汽车车身制造工艺新技术分析1. 激光焊接技术传统的汽车车身焊接工艺主要采用点焊和焊锡等方式,而激光焊接技术则是一种新型的高效、精确的焊接工艺。
激光焊接技术能够快速并且精确地完成焊接工作,焊接接头的质量更加可靠,焊接变形、气泡等缺陷减少,大大提高了车身的质量和稳定性。
与传统焊接相比,激光焊接技术还可以减少对环境的污染和对工人的伤害,是一种环保型的制造工艺。
2. 涂装技术涂装工艺是汽车制造过程中的重要环节,也是保证汽车外观质量和耐久性的关键。
汽车车身材料的发展趋势

汽车车身材料的发展趋势随着科技的不断进步和人们的需求不断变化,汽车车身材料也在不断发展和改进。
从最早的钢铁车身到现在的复合材料,汽车车身材料在轻量化、安全性和环保性方面有了巨大的进步。
本文将从这几个方面探讨汽车车身材料的发展趋势。
一、轻量化是汽车车身材料的发展方向之一。
轻量化能够减少汽车的重量,降低能耗,提高燃油经济性。
传统的钢铁材料在车身上占据了很大的比例,但其密度较高,重量较大。
为了实现轻量化,汽车制造商开始探索使用新型材料,如高强度钢、铝合金和碳纤维等。
高强度钢具有优异的强度和韧性,可以减少车身重量并提高碰撞安全性。
铝合金具有较低的密度和良好的成形性能,能够有效减轻车身重量。
碳纤维是一种轻质高强度的材料,具有优异的抗拉强度和刚度,但成本较高,限制了其在大规模生产中的应用。
二、安全性是汽车车身材料发展的另一个重要方向。
汽车车身在碰撞事故中起到保护车内乘员的作用。
传统的钢铁材料在碰撞时具有较好的塑性变形能力,但也存在一定的局限性。
为了提高车身的安全性,汽车制造商开始研发新型材料和结构设计。
高强度钢具有更好的抗撞性能,能够吸收和分散碰撞能量,提高车身的刚度。
同时,汽车制造商还采用了复合材料和蜂窝结构等新技术,提高车身的强度和刚度,进一步提高了车身的安全性能。
三、环保性是汽车车身材料发展的另一个重要方向。
随着人们对环境保护意识的增强,汽车制造商开始关注汽车的环保性能。
传统的钢铁材料在生产和回收过程中会产生大量的二氧化碳和废弃物,对环境造成一定的影响。
为了减少环境污染,汽车制造商开始使用可回收和可循环利用的材料,如铝合金和碳纤维等。
铝合金具有良好的回收性能,可以减少能源和资源的消耗。
碳纤维具有较长的使用寿命和较低的环境影响,是一种环保的材料。
汽车车身材料的发展趋势主要包括轻量化、安全性和环保性。
轻量化能够减少汽车的重量,提高燃油经济性;安全性能能够保护车内乘员的安全;环保性能能够减少对环境的污染。
随着科技的不断进步和人们对汽车的需求不断变化,相信未来汽车车身材料会继续发展和改进,为人们带来更加安全、环保和高效的出行方式。
汽车轻量化的未来趋势

汽车轻量化的未来趋势
汽车轻量化的未来趋势包括以下几个方面:
1. 材料的创新:以降低车身重量为目标,汽车制造商将采用更加轻量化的材料,如高强度钢、铝合金、镁合金和碳纤维等。
这些材料不仅具有较低的密度,还具有更好的强度和刚度,能够在不损害车辆安全性能的同时减轻车身重量。
2. 结构设计的优化:通过优化车身结构的设计,包括减少无关部分的负荷和提高结构强度等方式,可以实现汽车整体重量的降低。
例如,采用先进的设计和模拟技术,可以在车身结构中减少冗余材料和增加关键部位的强度,从而降低整车重量。
3. 模块化设计:通过模块化设计,汽车制造商可以在车辆组装过程中减少不必要的零部件和连接件,从而降低车辆的重量。
模块化设计还可以促进不同车型之间的共享部件,减少生产成本和资源浪费。
4. 新能源技术的应用:随着电动汽车和混合动力汽车的普及,传统的内燃机和传动系统可以被更轻量化和高效的电动机和电池系统所替代。
这将进一步减轻车辆的重量,并改善燃油效率和减少尾气排放。
5. 制造工艺的改进:通过引入先进的制造工艺和技术,如三维打印、激光焊接和精细成型等,可以减少材料和能源的消耗,提高生产效率,并降低车辆的重量。
总的来说,汽车轻量化是未来的发展趋势,它既可以提高燃油经济性和减少尾气排放,又可以提升车辆的性能和安全性。
随着科技和材料的进步,未来汽车的整体重量将进一步降低,为出行提供更加环保和高效的选择。
我国汽车材料的应用及未来发展趋势

我国汽车材料的应用及未来发展趋势1. 引言1.1 我国汽车材料的重要性1. 提高汽车的安全性能:汽车材料的选择直接影响到汽车的安全性能。
优质的汽车材料可以提高汽车的抗冲击性能、抗腐蚀性能和抗疲劳性能,从而保障车辆在行驶过程中的安全。
2. 优化汽车的性能与品质:不同种类的汽车材料具有不同的物理和化学性能,可以针对汽车设计的需要选择最适合的材料,以优化汽车的整体性能和品质。
3. 减轻汽车的重量:近年来,汽车轻量化已成为汽车制造行业的发展趋势。
采用轻量化材料可以降低汽车的整体重量,减少燃料消耗和排放,同时提高汽车的动力性能和经济性。
4. 推动材料工业的发展:汽车材料的需求驱动着我国材料工业的发展,促进了新型材料的研发和产业化,提高了材料产业的技术水平和竞争力。
我国汽车材料的选择和应用对于汽车制造行业的发展和提升具有重要意义,同时也对我国材料工业的发展起到了积极的推动作用。
1.2 汽车材料在汽车制造中的应用汽车制造中禤丰富多样,根据不同部位的功能需求、性能要求和安全标准,使用了各种不同的材料。
在汽车制造中,金属材料是最为常见和重要的材料之一。
汽车的车身骨架、发动机、悬挂系统等部件通常都采用金属材料制造,如钢铁、铝合金等。
这些金属材料具有优良的强度、刚度、导热性和耐久性,能够满足汽车在运行过程中的各种力学、热学和化学需求。
塑料材料在汽车制造中也扮演着重要角色。
塑料材料通常用于制造汽车的内饰、车身外部部件、隔音隔热材料等。
相比于金属材料,塑料材料具有更轻、易加工、隔热、耐腐蚀等特点,能够降低汽车的整体重量,提高燃油经济性和行驶性能。
复合材料在汽车制造中也得到越来越广泛的应用。
复合材料通常是由两种或两种以上的不同材料在一定比例下结合而成,具有优良的强度、刚度和轻量化特点,能够满足汽车在结构设计和性能需求上的多样化要求。
复合材料被广泛应用于汽车的车身、碳纤维材料制动系统、车顶等部件,以提高汽车的整体性能和安全性。
汽车轻量化的发现趋势
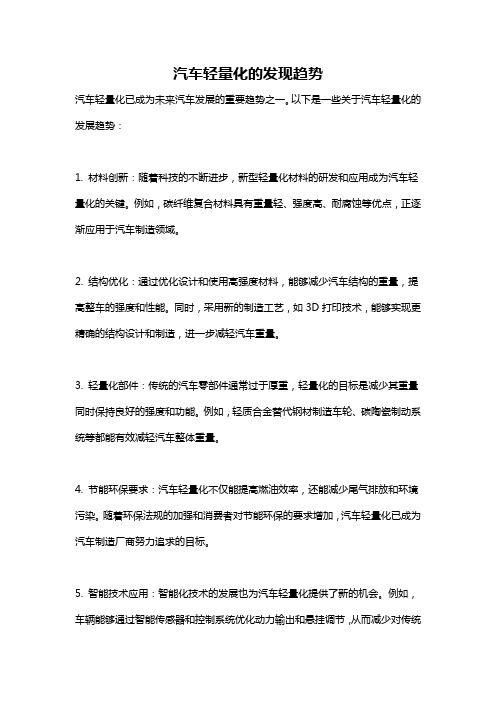
汽车轻量化的发现趋势
汽车轻量化已成为未来汽车发展的重要趋势之一。
以下是一些关于汽车轻量化的发展趋势:
1. 材料创新:随着科技的不断进步,新型轻量化材料的研发和应用成为汽车轻量化的关键。
例如,碳纤维复合材料具有重量轻、强度高、耐腐蚀等优点,正逐渐应用于汽车制造领域。
2. 结构优化:通过优化设计和使用高强度材料,能够减少汽车结构的重量,提高整车的强度和性能。
同时,采用新的制造工艺,如3D打印技术,能够实现更精确的结构设计和制造,进一步减轻汽车重量。
3. 轻量化部件:传统的汽车零部件通常过于厚重,轻量化的目标是减少其重量同时保持良好的强度和功能。
例如,轻质合金替代钢材制造车轮、碳陶瓷制动系统等都能有效减轻汽车整体重量。
4. 节能环保要求:汽车轻量化不仅能提高燃油效率,还能减少尾气排放和环境污染。
随着环保法规的加强和消费者对节能环保的要求增加,汽车轻量化已成为汽车制造厂商努力追求的目标。
5. 智能技术应用:智能化技术的发展也为汽车轻量化提供了新的机会。
例如,车辆能够通过智能传感器和控制系统优化动力输出和悬挂调节,从而减少对传统
零部件的依赖,减轻整车重量。
总的来说,汽车轻量化是一项多领域、多技术协同发展的工作。
它不仅能够提高汽车性能和节能环保,还能推动新材料、新工艺的研发和应用,进一步推动汽车产业的发展。
新能源汽车的车身轻量化设计与材料创新

新能源汽车的车身轻量化设计与材料创新在当今环保和能源压力日益增大的背景下,新能源汽车作为汽车行业的未来发展方向,正逐渐走入人们的生活。
而新能源汽车的车身轻量化设计与材料创新,成为了提升其性能、续航里程和市场竞争力的关键因素。
新能源汽车之所以需要轻量化的车身设计,主要源于其自身的特点和需求。
与传统燃油汽车相比,新能源汽车的电池重量较大,这在一定程度上增加了车辆的整体重量。
较重的车身会导致能耗增加,从而影响续航里程。
此外,轻量化设计还能提升车辆的加速性能、操控性能和制动性能,为驾驶者带来更好的驾驶体验。
要实现车身轻量化,材料的创新是重中之重。
高强度钢在新能源汽车车身中的应用日益广泛。
高强度钢具有出色的强度和韧性,通过合理的结构设计和制造工艺,可以在保证车身强度的前提下减轻重量。
例如,采用热成型高强度钢制造车身的关键部件,能够显著提高车身的抗碰撞性能,同时降低车身重量。
铝合金是另一种在新能源汽车车身中得到大量应用的材料。
铝合金的密度约为钢的三分之一,具有良好的耐腐蚀性和成型性。
通过采用铝合金挤压型材、压铸铝合金零件等技术,可以制造出轻巧而坚固的车身结构。
不仅如此,铝合金还能够通过回收再利用,符合可持续发展的理念。
碳纤维增强复合材料(CFRP)是一种具有极高强度和轻质特性的新型材料。
虽然其成本较高,但在高端新能源汽车中已经开始崭露头角。
CFRP 可以通过编织和树脂浸渍等工艺,制成各种复杂形状的零部件,大大减轻车身重量。
同时,其优异的力学性能还能提高车身的整体刚性和安全性。
除了材料的选择,车身结构的优化设计也是实现轻量化的重要途径。
采用一体化压铸技术,可以将多个零部件整合为一个大型压铸部件,减少了零部件的数量和连接点,从而减轻重量并提高生产效率。
例如,特斯拉的 Model Y 后车身就采用了一体化压铸技术,大大简化了车身结构。
拓扑优化设计是一种基于数学算法的结构优化方法。
通过对车身在不同工况下的受力分析,确定材料的最优分布,从而在保证强度的前提下去除多余的材料,实现轻量化。
汽车轻量化发展趋势

汽车轻量化发展趋势汽车轻量化是当前汽车行业的发展趋势之一,其在提高燃油经济性、降低碳排放、增加车辆安全性等方面具有重要作用。
本文将从材料、设计和制造三个方面探讨汽车轻量化的发展趋势。
首先,材料方面。
传统车辆使用的钢材在强度和重量之间存在着矛盾,而高强度钢、铝合金和复合材料则成为了汽车轻量化的主要材料。
高强度钢具有较高的强度和良好的塑性,可以减少车身重量,并提高车辆的碰撞安全性。
铝合金具有较低的密度和良好的刚性,可以减轻车身重量,并提高车辆的燃油经济性。
复合材料具有较低的密度和良好的强度,可以减轻车身重量,并提高车辆的刚性和安全性。
因此,未来汽车轻量化的发展将趋向于采用高强度钢、铝合金和复合材料。
其次,设计方面。
为了实现汽车轻量化,设计上需要减少车辆的自重和空气阻力。
通过减少车身和车架的重量,采用流线型的外观设计以降低空气阻力,可以有效减少车辆的能耗。
此外,还可以采用轮胎、传动系统和悬挂系统等部件的轻量化设计,减少车辆的重量和能耗。
另外,应注重车辆的空气动力学性能,减小空气阻力,提高车辆的燃油经济性。
最后,制造方面。
制造技术的发展对汽车轻量化起到关键作用。
通过采用更先进的成型技术,如热冲压、激光焊接、点胶和铆接等,可以实现车身结构的精确成型和连接。
此外,应注重材料的再利用和循环利用,通过回收利用废旧车辆和零部件,减少资源的消耗和环境的污染。
综上所述,汽车轻量化是当前汽车行业的发展趋势之一,其在提高燃油经济性、降低碳排放、增加车辆安全性等方面具有重要作用。
未来汽车轻量化的发展将趋向于采用高强度钢、铝合金和复合材料,减少自重和空气阻力,采用更先进的制造技术。
随着技术的发展和创新的不断推进,相信汽车轻量化将为人们带来更加高效、环保和安全的出行方式。
轻量化材料在汽车工业中的应用前景与发展趋势

轻量化材料在汽车工业中的应用前景与发展趋势引言随着汽车工业的飞速发展,轻量化已成为当今汽车工业界最火热的话题之一。
汽车轻量化最直接的好处就是能节约燃料、减少排放,提高车辆性能。
为此,汽车制造商们开始寻找各种轻量化材料来用在车身、底盘等汽车重要零部件上,以此来提高整车的轻量化程度。
轻量化材料范围很广泛,如有机高分子材料、纳米材料、纤维增强复合材料、金属陶瓷复合材料等。
本文将着重介绍轻量化材料在汽车工业中的应用前景以及发展趋势。
第一章轻量化材料在汽车工业中应用前景1.1 燃料消耗降低汽车制造商们需要使用各种材料来轻量化汽车,以降低燃料消耗。
当车子重量降低了10%,则可以提高1%的燃油效率。
而在电动汽车方面,轻量化可以增加电动汽车耐用程度并使电池续航里程加长。
1.2 环境保护与减少尾气排放全球汽车工业都面临着严格的排放标准,而轻量化使诸如燃油效益提高、尾气排放减少等的环保影响绘上显著的底色。
1.3 安全性轻量化材料不仅仅能趋近于传统材料的强度,甚至有时强于传统材料。
许多新材料,例如复合材料和高强度异种金属连接材料等,都带来了新的成分和功能,也提高了整车级安全性。
例子包括“航空级”铝合金,这种材料在力学和化学性能都优秀,并已经应用于许多轻型汽车中。
第二章轻量化材料在汽车工业中的发展趋势2.1 碳纤维复合材料碳纤维复合材料的研究和生产技术不断地发展,可替代传统钢铁材料用于汽车部件。
借助其单向向性和热性能对材料性质的特别优化,它们能够实现极大的自重降低。
在未来的研究中,预计碳纤维复合材料将会取代部分金属法兰板,可用于制造轻量化车身以及一些结构件,例如架构和车门等。
2.2 纳米材料现在应用最广泛的纳米材料之一就是纳米粘土,利用了其优异的障碍性,它不仅可以增加陶瓷材料的刚性和牢度,还可以使其耐力的提高。
此外,纳米铁氧体材料也成为了研究的热点。
InorgaMatik AG等公司已经将其运用于汽车制造中,用于汽车加热器中的泵和阀门件中。
- 1、下载文档前请自行甄别文档内容的完整性,平台不提供额外的编辑、内容补充、找答案等附加服务。
- 2、"仅部分预览"的文档,不可在线预览部分如存在完整性等问题,可反馈申请退款(可完整预览的文档不适用该条件!)。
- 3、如文档侵犯您的权益,请联系客服反馈,我们会尽快为您处理(人工客服工作时间:9:00-18:30)。
辽宁科技学院学报
文章编号: 1008- 3723( 2009) 04- 0010- 05
轻量化材料在(同济大学 汽车学院 , 上海 2018042)
摘要: 轻量化材料在汽车领域的应用, 是降低车身重量的重要方式之一, 可以有 效地降低废 气排放, 节约能 源。轻量化材
现代汽车车身除满足强度 和使用寿命的要求外, 还 应该 满足基本性能、外观、安全、价格、环 保、节 能等 方面 的需要。 在 九 十年 代 以 前, 以 轿车 为 例, 其 整 车质 量 中, 钢 铁 占 有 80% , 铝占 3% , 树脂占 4% 。 由于能 源价 格不断 上升, 作 为 轻量化材料的高强 度钢板、表面 处理钢 板用量 逐年 上升, 有 色金属材料的用量 也在不 断增加, 其中, 铝合 金材 料的应 用 明显增加, 非金属材料也逐步增加。本文主要就车身轻 量化 材料的发展做研究。
30 03、30 04、300 5 40 32、40 43、434 3
100- 300
50 52、50 82、518 2、508 3
100- 400
日 用品、散 热 片、罩盖、铭 牌、包 装、建 材、印刷板、电线、装饰品、反 射板 日用品、散热片、包 、罐、建材 、彩铝
活塞、气缸盖、热交 换器、焊条、建材 建 材、车辆、船 舶、照 相机、扣钉、低 温 油箱、压力容器
), 男, 山东烟台市人, 同济大 学汽
度钢和超高强度钢、铝合 金、镁合金、塑料和复合材料的用量 将有较大的增长, 铸铁和 中、低强度钢的比例将会逐步 下降, 但载重车的用材变化不如轿车明显;
( 3)轻量化材料技术与汽车 产品设 计、制 造工艺 的结合 将更为密切, 汽车车身结 构材料将趋向多材料设计方向;
12
辽宁科技学院学报
第 11卷
续表 3: 合金 主要合金成 分 典型合金型号
热
200 0 系
处
理
型
600 0 系
合
金
700 0 系
Cu、、Mg M g、Si Zn、M g
拉伸强度 (MP a) 20 11、20 17、202 4
60 61、60 63、626 2 70 03、7N0 1、707 5
钢板厚 板质量 铝板厚 板质量 轻量化率 零件名称
( mm ) ( kg) ( mm ) ( kg) ( % )
发动机罩外板 0. 75 8. 50 1. 00 3. 90
54
发动机罩内板 0. 75 10. 47 1. 00 4. 50
54
日本住友轻金属工 业公司 与美国 雷诺尔兹 铝制 品公司 共同开发出一种代号为 SG112- T4A 的车身 铝合金板 材, 硬 度比普通铝板高 1. 5倍, 同时也具有良好的冲 压加工性。此 种材料在冲压 加工 时较 软便 于拉 延, 而通 过涂 装 即热 处理 后, 硬度提高近 1倍 ( 表 2) 。
图 1 采用全铝结构的奥迪 A8轿车车身
图 2是北美近年来轿车 所用铝 材的发 展变化。 而且 铝质汽 车零件基本上都可回收;
图 2 典型轿车所用材料变化 情况 回收再生所需要能源 少, 并 且铝 可以多 次循 环再生, 对 其性能来讲没有多大 变化。对于 两个特 定的车 身覆 盖件采
用铝板后与采用钢板的对比结果列入表 1。 表 1 轻量化实例
目前, 车身轻量化的主要 途径 有 2条: 效 果比 较明显 的 是用轻型材料 (如镁、铝、塑料盒复合 材料等 )替 代车身 骨架 及内、外壁板原有的钢材, 目前 已制造出部分产品; 另一 种有 效的方法是通过优化车身结构 实现轻量化, 其代表性成 果为 ULSAB( U ltra L ight Steel Auto Body)项目 112。
表 2 SG112- T4A 铝板与普通铝板硬度比较
材料 SG112 - T4A涂装前 SG112- T4A涂装后 普通铝板
硬度 MP a
11 0
21 0
14 0
虽然 SG112- T4A的板材价 格是钢板的 2 倍, 但 质量可 减轻 50% , 并且点焊工作量也 减少 30% 以上, 是一 种很理想 的车身用铝板。
汽车用铝在日本已经制 定了 JISH4000 标准, 从 1000到 7000进行了分类, 用于汽车的铝合金, 包括热处理型 6000系 列和非热处理型 5000 系列 , 其中 5038和 5183是 汽车 车身 最常用的型号。表 3列出日本的铝合金分类和特性, 表 4是 主要铝合金板的机械性能及其与冷轧钢板的比较。
1 国际汽车用材料的发展现状与趋势
当前世界汽车材 料技术发展的主要特征如下: ( 1)轻量化与环 保是当今汽车材料发展的主要方向; ( 2)尽管近阶段 钢铁材料仍保 持主导地 位, 但各种 材料 在汽车上的应用比例 正在发生变化。主要变化趋势是高强
交稿日期: 2009- 10- 21 作者简介: 石秀忠 ( 1976车学院工程硕士.
2 国内发展状况分析
我国汽车材料是伴随着汽车工业的发展而发展起 来的。
尤其是在 / 七五 0至 / 九 五 0期间, 我 国通过 合资 的方 式引进 了国外先进的 汽车 产品 技术, 缩 短了 与发 达国 家 之间 的差 距。在引进技术的带动下, / 九五 0期间 / 轿车新材料 技术开 发 0被列入国家科技 攻关计 划, 同 时在国 家 863高技 术计划 新材料领域的支持下, 先后开发出 了一批轿车国产化急需的 金属材料和非金属材料, 促 进了国产 汽车材 料的 技术进 步。 但是, 同国外相比, 我国汽车工业整体技术水平还比较 落后, 汽车材料领域 的差 距更 大。主 要表 现 为: 企业 开 发能 力不 足, 缺乏创新、竞争能力; 技术与管理水平落 后, 生产规 模小, 劳动生产率低, 产品 质量差; 产品 结构 不合理, 技 术含量 低, 低档产品过剩, 高端 产品依 靠进口; 汽车 行业采 用的 材料系 列与品种繁杂、数量 少, 使 汽车专 用材料 的产量 难以 达到经 济规模; 汽车材料基 础技术 研究薄弱, 缺 少材料 评价 技术与 体系, 材料技术标准混乱, 基础数据贫乏。从总体上看, 国内
少汽车总重量具有 双重的 效应, 是汽车 轻量化 的重 要途径。 车身轻量化 的研 究是 现代 车身 设 计的 一 大主 流。当 前, 节 能、环保、安全、舒适、智能和网络是汽车技术发展 的总趋势, 尤其是节能 和环 保更 是关 系人 类可 持续 发展 的 重大 问题。 汽车油耗与车重关 系密切, 汽车 行驶过 程中受 到空 气阻力、 轮胎阻力、加速阻力和爬 坡阻力 等, 其 中后面 三项 均与车 身 本身的重量成正比, 这直接影响轿车的油耗, 因此, 降低 燃油 消耗、减少向大气 排出 CO2 和有 害气 体及 颗粒 已成 为汽 车 界主要的研究课题。 减小汽车 自身质 量是汽 车降 低燃油 消 耗及减少排放的最 有效措 施之一。尤 其是当 前全 球能源 缺 少的危机之下, 轻量 化技术 对于 未来 轿车发 展有 着巨大 的 意义。实现轻质车身, 最主要就是大量应用使车身轻量 化的 材料, 同时进行车身轻量化的结构设计等。
德国汽车车身用铝已经规范化, 应用实例见表 5。
合金 主要合金成 分 典型合金型号
非
100 0 系
热
处
300 0 系
理
型
400 0 系
合
金
500 0 系
Fe、S i、Cu Mn Si Mg
表 3 铝合金的种类和特性
拉伸强度 (MP a)
用途
10 70、10 50、110 0、120 0
50- 200
料的应用也从另一面 推动了车身结构设计的优化, 推动了汽车领域的发展 。
关键词: 轻量化材料; 铝合 金材料; 车身; 重量
中图分类号: TG14
文献标识码: A
汽车车身、底盘 (含悬挂系 统 )、发动 机三大 件约占 一辆 轿车总重量的 65% 以 上。其 中车 身外、内 覆盖 件的 重量 又 居首位。因此减少汽 车车身重 量对降 低发动 机的 功耗和 减
70% 的油耗是用在车身质量上的, 所以汽车车身的铝化 对减 轻汽车自重, 提高整车燃料经济性至关重要。铝合金材 料在 现代汽车轻量已经 显示出 非常重 要的作 用。车身 用铝合 金 必要的性能有: 强 度、成 形性 、耐蚀 性、焊 接性、表 面 处理 性 等, 产品要有刚性、耐撞凹性、耐久性等 122。制约铝合金在汽 车上大量应用的主要原因之一 是其价格比钢材高, 为了 促进 铝在汽车上的应用, 必须降低材料成本。除开发低成本 的铝 合金和先进的铝合金成型工艺 外, 回收再生技术可进一 步降 低铝的成本, 铝合金是最 常见的 汽车用 轻金属, 而 且在汽 车 上使用较早, 相对比较成熟。现代轿车发动机活塞几乎 都用 铸铝, 这是因为活塞作为主要的往复运动件要靠减重来 减小 惯性, 减轻曲轴配 重, 提 高效 率, 并需 要 材料 有良 好 的导 热 性, 较小的热膨胀 系数, 以 及在 350e 左右 有较 好的 力学 性 能, 而铸铝能符合这些 要求。同时 由于活 塞、连杆 采用了 铸 铝件, 减轻了重量, 从 而减少 发动机 的振动, 降 低了 噪声, 使 发动机的油耗下降, 这也符合了汽车的发展趋势。像上 海通 用新 项目投 入的 L850全 铝发动 机。德国 Audi汽 车公司 已 经将铝合金车身用于 成批生产的 轿车, Aud iA8 车身已 经采 用 了 第 一 代 铝 合 金 空 间 构 架 ASF ( A lum in ium - Space F rame) 132。 ASF 车身超过了现 代轿车 钢板车 身的 强度和 安 全水平, 但汽车自身的重量减轻了大 约 40% 。 2002年, 奥迪 铝材及轻量设计中心 又见 证了第 二代 奥迪 A8的诞 生, 图 1 示。
用途 300- 500 150- 400 350- 700
飞 机、气缸 盖、活 塞、电位 器、钢 钉、油 压部件 建材、车辆、家 俱、船舶、家电、照相 机、 电线、网球拍 飞机、车辆、船舶、散热片、垒 球棒