转炉煤气全回收实验
转炉煤气净化回收技术规程
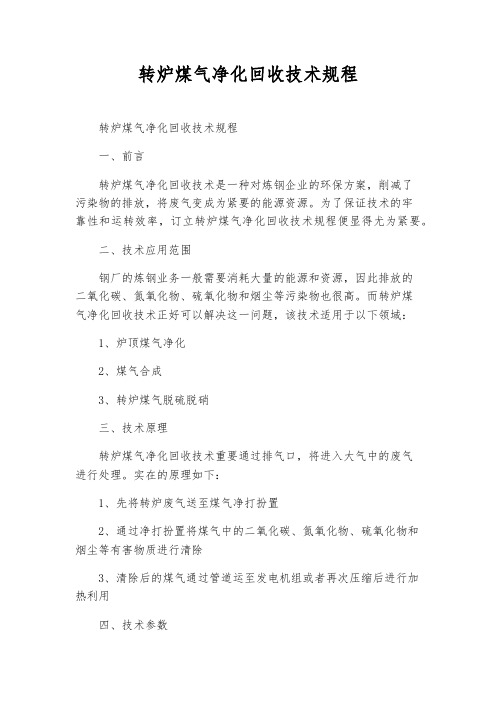
转炉煤气净化回收技术规程转炉煤气净化回收技术规程一、前言转炉煤气净化回收技术是一种对炼钢企业的环保方案,削减了污染物的排放,将废气变成为紧要的能源资源。
为了保证技术的牢靠性和运转效率,订立转炉煤气净化回收技术规程便显得尤为紧要。
二、技术应用范围钢厂的炼钢业务一般需要消耗大量的能源和资源,因此排放的二氧化碳、氮氧化物、硫氧化物和烟尘等污染物也很高。
而转炉煤气净化回收技术正好可以解决这一问题,该技术适用于以下领域:1、炉顶煤气净化2、煤气合成3、转炉煤气脱硫脱硝三、技术原理转炉煤气净化回收技术重要通过排气口,将进入大气中的废气进行处理。
实在的原理如下:1、先将转炉废气送至煤气净打扮置2、通过净打扮置将煤气中的二氧化碳、氮氧化物、硫氧化物和烟尘等有害物质进行清除3、清除后的煤气通过管道运至发电机组或者再次压缩后进行加热利用四、技术参数1、净化效率:90%2、最高煤气进口温度:800℃3、煤气出口温度:225℃4、系统压力:0.02-0.1MPa五、安全保障1、进行全面严密的安全风险评估2、对废气处理设备进行全面检查3、定期对煤气管道进行检测4、订立相关的应急预案六、技术进展展望随着市场经济的进展,环保形势持续严峻,转炉煤气净化回收技术将会得到越来越广泛的应用和推广。
同时,随着科技不断进展和技术不断进步,该技术也会不断完善,为环保事业贡献更大的气力。
七、总结转炉煤气净化回收技术在炼钢企业的环保方面发挥了巨大作用,具有很高的社会经济效益。
在技术的应用过程中,必需订立科学合理的技术规程,以确保技术的牢靠性和运转效率。
提高转炉煤气回收量实践-最新年文档

提高转炉煤气回收量实践随着钢铁工业对节能与环保需求的日益加剧,“转炉煤气回收量”成为衡量一个冶金企业节能环保水平的重要指标。
如何进行转炉煤气的极限回收和有效利用,对企业节能降耗、提高效益至关重要。
2014年一炼钢转炉煤气回收量平均为84m3/t,离国内先进水平有一定差距。
吨钢回收量低,放散量大,既浪费了能源,又严重污染了环境。
如何提高转炉煤气吨钢回收量,稳定地保持高水平的回收状态,解决供需不平衡等一系列矛盾,已成为需要迫切解决的难题。
1 转炉煤气系统组成及工艺流程一炼钢煤气回收系统主要设备包括:蒸发冷却器及喷淋系统、粗灰系统、静电除尘器、细灰系统、煤气风机、煤气冷却器、三通切换阀及水封逆止阀、V形水封、放散塔及煤气管道等。
2009年投产运行的一炼钢3座180吨转炉系统,配套建设了12万m?转煤煤气柜和加压机,能控中心转炉煤气柜及加压站主要承担转炉煤气的回收、储存、加压和输送。
转炉炼钢过程中,铁水中的碳在高温下和吹入的氧生成一氧化碳和少量二氧化碳的混合气体。
回收的顶吹氧转炉炉气含一氧化碳50~80%,二氧化碳15~20%,以及氮、氢和微量氧。
转炉煤气的发生量在一个冶炼过程中并不均衡,成分也有变化。
所以我们将转炉多次冶炼过程回收的煤气输入转炉煤气柜,混匀后再输送给用户。
转炉煤气由炉口喷出时,温度高达1450~1500℃,并夹带大量氧化铁粉尘,需经降温、除尘,方能使用。
净化有湿法和干法两种类型,我们是采用干法。
煤气经冷却烟道温度降至1000℃,然后用蒸发冷却器,再降至200℃,经干式电除尘器除尘,含尘量低于50毫克/立方米的净煤气,经抽风机送入储气柜。
工艺流程见下图1。
2 提高转炉煤气回收量的实践2.1 完善自动化系统(1)由于转煤煤气分析仪是精密仪器,对外围环境要求较高。
在落雨天,经常会出现煤气检测CO浓度含量达110%等检测误差,影响煤气正常回收。
为此,在检测转炉煤气探头的地方搭设了挡雨装置,避免雨水影响仪表检测精度,基本解决了由于下雨导致转炉煤气不能回收的情况。
转炉干法除尘系统煤气回收的分析与研究
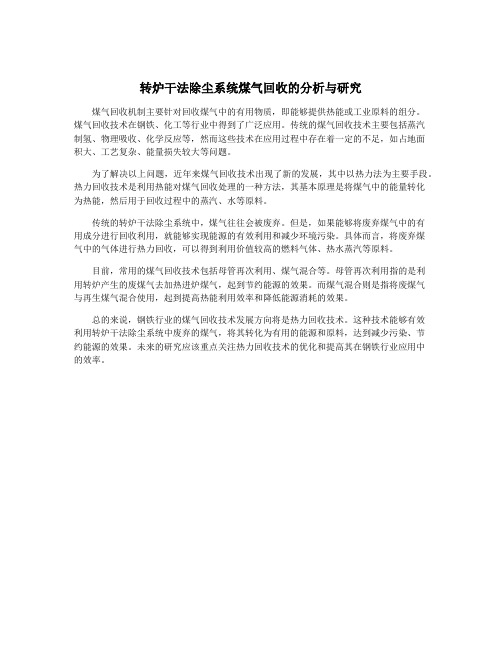
转炉干法除尘系统煤气回收的分析与研究
煤气回收机制主要针对回收煤气中的有用物质,即能够提供热能或工业原料的组分。
煤气回收技术在钢铁、化工等行业中得到了广泛应用。
传统的煤气回收技术主要包括蒸汽
制氢、物理吸收、化学反应等,然而这些技术在应用过程中存在着一定的不足,如占地面
积大、工艺复杂、能量损失较大等问题。
为了解决以上问题,近年来煤气回收技术出现了新的发展,其中以热力法为主要手段。
热力回收技术是利用热能对煤气回收处理的一种方法,其基本原理是将煤气中的能量转化
为热能,然后用于回收过程中的蒸汽、水等原料。
传统的转炉干法除尘系统中,煤气往往会被废弃。
但是,如果能够将废弃煤气中的有
用成分进行回收利用,就能够实现能源的有效利用和减少环境污染。
具体而言,将废弃煤
气中的气体进行热力回收,可以得到利用价值较高的燃料气体、热水蒸汽等原料。
目前,常用的煤气回收技术包括母管再次利用、煤气混合等。
母管再次利用指的是利
用转炉产生的废煤气去加热进炉煤气,起到节约能源的效果。
而煤气混合则是指将废煤气
与再生煤气混合使用,起到提高热能利用效率和降低能源消耗的效果。
总的来说,钢铁行业的煤气回收技术发展方向将是热力回收技术。
这种技术能够有效
利用转炉干法除尘系统中废弃的煤气,将其转化为有用的能源和原料,达到减少污染、节
约能源的效果。
未来的研究应该重点关注热力回收技术的优化和提高其在钢铁行业应用中
的效率。
转炉煤气回收和利用技术分析
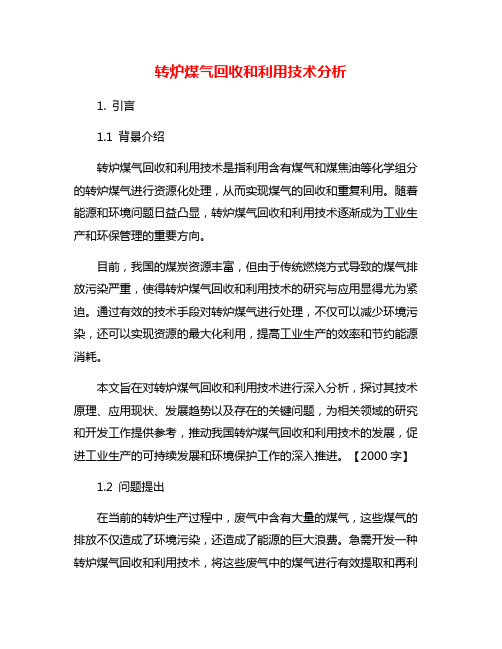
转炉煤气回收和利用技术分析1. 引言1.1 背景介绍转炉煤气回收和利用技术是指利用含有煤气和煤焦油等化学组分的转炉煤气进行资源化处理,从而实现煤气的回收和重复利用。
随着能源和环境问题日益凸显,转炉煤气回收和利用技术逐渐成为工业生产和环保管理的重要方向。
目前,我国的煤炭资源丰富,但由于传统燃烧方式导致的煤气排放污染严重,使得转炉煤气回收和利用技术的研究与应用显得尤为紧迫。
通过有效的技术手段对转炉煤气进行处理,不仅可以减少环境污染,还可以实现资源的最大化利用,提高工业生产的效率和节约能源消耗。
本文旨在对转炉煤气回收和利用技术进行深入分析,探讨其技术原理、应用现状、发展趋势以及存在的关键问题,为相关领域的研究和开发工作提供参考,推动我国转炉煤气回收和利用技术的发展,促进工业生产的可持续发展和环境保护工作的深入推进。
【2000字】1.2 问题提出在当前的转炉生产过程中,废气中含有大量的煤气,这些煤气的排放不仅造成了环境污染,还造成了能源的巨大浪费。
急需开发一种转炉煤气回收和利用技术,将这些废气中的煤气进行有效提取和再利用,实现环境保护和资源节约的双重效果。
目前在转炉煤气回收和利用技术方面仍存在诸多问题,包括技术成本高、技术成熟度低、设备稳定性差等。
这些问题制约了转炉煤气回收和利用技术的进一步推广和应用。
急需对转炉煤气回收和利用技术进行深入研究和分析,找出存在的问题并提出解决方案,推动该技术的发展和应用,实现转炉生产过程的清洁生产和可持续发展。
【字数:201】1.3 研究意义转炉煤气回收和利用技术的研究意义主要体现在以下几个方面:1. 节约能源资源:煤气回收和利用是资源有效利用的重要手段,通过开发和应用煤气回收技术,可以有效节约能源资源,减少对传统能源的依赖,提高能源利用效率。
2. 减少环境污染:煤气回收和利用技术可以有效降低燃料燃烧过程中排放的废气中的有害物质浓度,减少空气污染和温室气体排放,保护环境,改善空气质量。
转炉干法除尘系统煤气回收的分析与研究

转炉干法除尘系统煤气回收的分析与研究随着经济和社会的发展,钢铁生产已经成为许多国家不可或缺的行业之一。
炼钢过程中,转炉炼钢是一个非常重要的工艺流程。
然而,炼钢过程中释放出大量的烟尘和废气,给环境造成了很大的污染。
因此,对炼钢生产过程中的污染治理工作是非常重要的。
本文将对转炉干法除尘系统煤气回收的分析与研究进行探讨。
一、转炉干法除尘系统的原理在炼钢废气治理中,转炉干法除尘系统是一种常用的治理方法。
该系统的主要原理是利用机械力和离心力将煤气中的粉尘和颗粒物脱除出来。
该系统通常由除尘器、旋风分离器、旋转式喷淋器、出水口等部分组成。
其主体部分是除尘器,其工作原理如下:废气从除尘器的进气管进入除尘器内部,在进入过程中经过了预处理段的净化。
落下的颗粒物通过旋风分离系统,沉下到料斗中。
此时废气已经分离了一定量的颗粒物,在旋风分离器内,煤气受到离心作用,使其速度降低,并将其中的颗粒物和粉尘分离出来。
随后,煤气流入旋转式唧筒中。
在这里,水通过压力喷嘴和旋转式喷淋器进行喷淋,与废气发生接触,使煤气中的颗粒物和粉尘被溶解并冲入水面中。
在煤气净化的过程中收集的毒物也被波浪冲走。
最后,净化后的废气通过排气管排放或再利用。
整个除尘系统的操作过程大大降低了煤气中污染物的浓度,达到了保护环境和节约能源的效果。
1、处理效率高:煤气经过除尘器的物理吸附、静电吸附与旋风分离,将微小的颗粒粉尘从煤气中分离出来,使其浓度和体积大大降低,达到高效的净化效果。
2、应用广泛:该系统不仅适用于钢铁、建筑等重工业中的烟雾净化,还适用于煤矿,化工等其他制造业中的废气净化。
3、维护简单:转炉干法除尘系统的维护操作相对比较简单,易于维护。
4、技术成熟:该系统的技术已经相对成熟,大部分钢铁企业已经普及了该除尘系统,也具备了一定的经济效益。
三、煤气回收技术的分析在钢铁生产中,煤气是非常宝贵的资源。
随着技术的不断革新,将废气回收并再利用,已成为炼钢业的一种新技术。
转炉煤气回收技术的研究与应用9.26
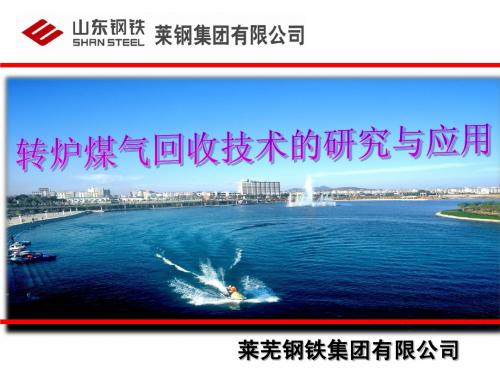
Page 24
五、经济效益
2、社会效益:
通过这次技术研究,转炉煤气回收技术取得重大
突破,煤气回收量达到了国内同类转炉先进水平,有 效减少了煤气放散对大气的严重污染及对周围人群的 毒害,同时也减少了对煤气设备的损失及放散能源的 消耗,提高了二次能源的利用率。
Page 25
炼钢大学堂
莱芜钢铁集团有限公司炼钢厂
γ:废钢中 碳含量
0.25%
每炉钢可回收转炉煤气 (m3/炉) 吨钢可回收转炉煤气量(m3/t)
17113
125
Page 12
三、具体方案措施
4.对转炉煤气回收量相应参数进行研究 第一步:对转炉煤气回收量提高途径的理
论分析图进行研究,提高煤气回收量就是
要增加烟气量,提高 CO 含量。转炉煤气回
收量提高途径分析如下图3 :
Page 6
二、现状分析 (二)目前并网的有利条件
条件一:2012年2月,能源动力厂新增转炉煤气并特钢
和宽厚板管线,开发了转炉煤气新用户。
条件二:当前钢铁市场形势严峻,降低钢铁生产成本, 就要从各个环节入手,而二次能源的利用,更是经济效益 挖潜的强力股。 条件三:公司对于能源管理的重视,加大了对煤气的产 生和消耗的整体调度。
并且 CO 含量在 22% 启动压差调节,大于 24%
开始回收,回收后期CO小于20%开始放散,
扩大了回收区间。
Page 16
三、具体方案措施
4.对转炉煤气回收量相应参数进行研究 第四步:调整副枪测温时间。 转炉煤气回收后期,因副枪测温, O2 含 量
迅速提升,此时CO含量一般在45%左右,通过采取
Page 4
二、现状分析 (一)并网受限的主要原因
转炉煤气回收和利用技术分析
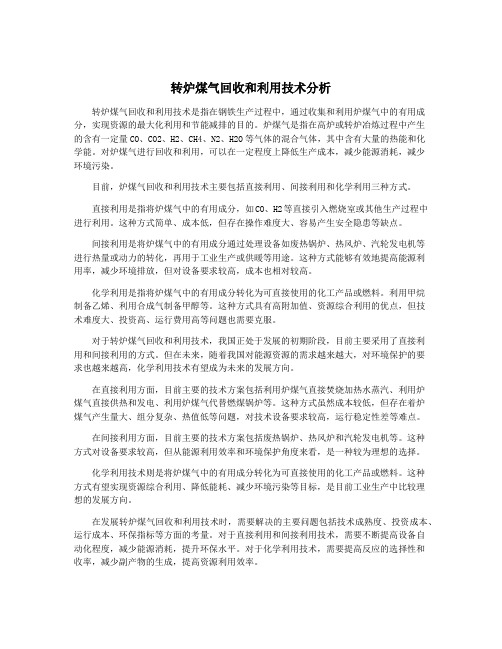
转炉煤气回收和利用技术分析转炉煤气回收和利用技术是指在钢铁生产过程中,通过收集和利用炉煤气中的有用成分,实现资源的最大化利用和节能减排的目的。
炉煤气是指在高炉或转炉冶炼过程中产生的含有一定量CO、CO2、H2、CH4、N2、H2O等气体的混合气体,其中含有大量的热能和化学能。
对炉煤气进行回收和利用,可以在一定程度上降低生产成本,减少能源消耗,减少环境污染。
目前,炉煤气回收和利用技术主要包括直接利用、间接利用和化学利用三种方式。
直接利用是指将炉煤气中的有用成分,如CO、H2等直接引入燃烧室或其他生产过程中进行利用。
这种方式简单、成本低,但存在操作难度大、容易产生安全隐患等缺点。
间接利用是将炉煤气中的有用成分通过处理设备如废热锅炉、热风炉、汽轮发电机等进行热量或动力的转化,再用于工业生产或供暖等用途。
这种方式能够有效地提高能源利用率,减少环境排放,但对设备要求较高,成本也相对较高。
化学利用是指将炉煤气中的有用成分转化为可直接使用的化工产品或燃料。
利用甲烷制备乙烯、利用合成气制备甲醇等。
这种方式具有高附加值、资源综合利用的优点,但技术难度大、投资高、运行费用高等问题也需要克服。
对于转炉煤气回收和利用技术,我国正处于发展的初期阶段,目前主要采用了直接利用和间接利用的方式。
但在未来,随着我国对能源资源的需求越来越大,对环境保护的要求也越来越高,化学利用技术有望成为未来的发展方向。
在直接利用方面,目前主要的技术方案包括利用炉煤气直接焚烧加热水蒸汽、利用炉煤气直接供热和发电、利用炉煤气代替燃煤锅炉等。
这种方式虽然成本较低,但存在着炉煤气产生量大、组分复杂、热值低等问题,对技术设备要求较高,运行稳定性差等难点。
在间接利用方面,目前主要的技术方案包括废热锅炉、热风炉和汽轮发电机等。
这种方式对设备要求较高,但从能源利用效率和环境保护角度来看,是一种较为理想的选择。
化学利用技术则是将炉煤气中的有用成分转化为可直接使用的化工产品或燃料。
提高转炉煤气回收实践-精品文档资料
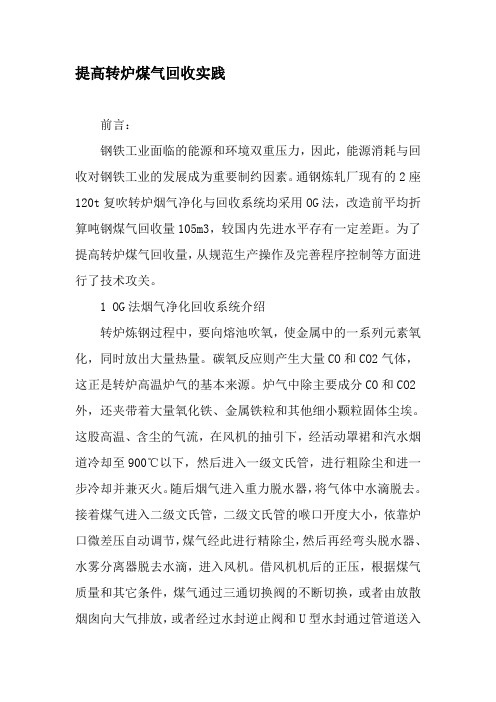
提高转炉煤气回收实践前言:钢铁工业面临的能源和环境双重压力,因此,能源消耗与回收对钢铁工业的发展成为重要制约因素。
通钢炼轧厂现有的2座120t复吹转炉烟气净化与回收系统均采用OG法,改造前平均折算吨钢煤气回收量105m3,较国内先进水平存有一定差距。
为了提高转炉煤气回收量,从规范生产操作及完善程序控制等方面进行了技术攻关。
1 OG法烟气净化回收系统介绍转炉炼钢过程中,要向熔池吹氧,使金属中的一系列元素氧化,同时放出大量热量。
碳氧反应则产生大量CO和CO2气体,这正是转炉高温炉气的基本来源。
炉气中除主要成分CO和CO2外,还夹带着大量氧化铁、金属铁粒和其他细小颗粒固体尘埃。
这股高温、含尘的气流,在风机的抽引下,经活动罩裙和汽水烟道冷却至900℃以下,然后进入一级文氏管,进行粗除尘和进一步冷却并兼灭火。
随后烟气进入重力脱水器,将气体中水滴脱去。
接着煤气进入二级文氏管,二级文氏管的喉口开度大小,依靠炉口微差压自动调节,煤气经此进行精除尘,然后再经弯头脱水器、水雾分离器脱去水滴,进入风机。
借风机机后的正压,根据煤气质量和其它条件,煤气通过三通切换阀的不断切换,或者由放散烟囱向大气排放,或者经过水封逆止阀和U型水封通过管道送入煤气柜。
通钢炼轧厂OG法图如图1:2.确定分时段煤气回收控制参数转炉炼钢按其吹炼时间不同可分为三个时段,即吹炼前期、吹炼中期和吹炼末期,冶炼前期,熔池温度低,铁水中硅、锰等元素含量较高,主要是硅锰的氧化,脱碳速度很慢,因而CO的生成量亦相应较少,炉口易形成大负压。
冶炼中期,是碳激烈氧化阶段,CO的生成量达到最大值,脱碳速度主要受供氧强度的影响。
供氧强度越大,脱碳速度也越大(但过大易产生喷溅)。
复吹转炉由于FeO控制得较低,最大速度不及顶吹转炉,吹炼中不易喷溅但全程的平均速度较之还要大些。
在吹炼末期,当钢液含碳量降低到一定程度时,碳的扩散成为限制性环节,脱碳速度取决于熔池搅拌情况。
转炉炼钢中,脱碳反应速度由氧的扩散控制转成由碳的扩散控制时的钢液含碳量称为临界含碳量。
- 1、下载文档前请自行甄别文档内容的完整性,平台不提供额外的编辑、内容补充、找答案等附加服务。
- 2、"仅部分预览"的文档,不可在线预览部分如存在完整性等问题,可反馈申请退款(可完整预览的文档不适用该条件!)。
- 3、如文档侵犯您的权益,请联系客服反馈,我们会尽快为您处理(人工客服工作时间:9:00-18:30)。
2015年12月8日下午,能源管理中心邬琦、苗亚君在炼钢厂风机房刘主任的配合下,对炼钢厂转炉煤气全回收项目进行第一次实验,实验对象为炼钢1#转炉,1#转炉回收煤气期间,其他两座转炉停止回收煤气,实验期间1#转炉共回收四炉煤气,具体数据如下:
序号回收起点(co
回收量(m³)Co平均浓度吹炼时间浓度)
1 20%802140%13分27秒
2 16%810048%
3 16%807048.2%13分54秒
4 16%808752.8%
根据实验数据可知,以co浓度为16%开始回收时,回收量在8000~8100m³之间,此时吨钢回收量为95m³/t左右,炼钢风机房co分析仪显示平均co浓度在48%-52.8%之间(第一组数据co浓度40%为人工选取三个节点计算,存在误差),四炉回收结束后,在煤气柜内取样化验co浓度,结果为40%(人工化验),与炼钢分析仪存在差异。
炼钢厂通过对第一次实验报告数据进行统计分析后,认为在吹炼过程中实时调节二文喉口开度可提高转炉煤气回收量,具体改进方案如下:
将吹炼过程分为四个阶段,每个阶段喉口开度通过自动化程序设定一个固定值,如下表。
吹炼时间(min)喉口开度(mm)
0-4 200
4-12 260
12-停吹260
停吹后190
通过以上改进措施,炼钢厂风机房工作人员和能管中心相关人员于2015年12月13日下午对炼钢1#转炉进行第二次回收实验,具体数据如下:
回收量(m³)Co平均浓度吹炼时间序号回收起点(co
浓度)
1 16%7801 47% 12分22秒
2 16%772
3 46.3% 12分58秒
3 16%8145 48.3% 12分31秒备注:煤气柜人工化验co浓度为43%
通过对比两次实验数据可知,在回收起点相同的前提下,回收煤气量与co平均浓度与第一次实验数据差异不大,但是第二次实验吹炼时间与第一次实验相比,缩短一分钟,所以可推导出结论:若在同时保证回收起点和吹炼时间相等的条件下,第二次实验每炉可多回收煤气1000-1100m³(回收瞬时流量为65000-68000m³/h),此时吨钢回收转炉煤气量约为107-110m³/t,所以,通过对喉口开度的改进,使吨钢回收量提高约12m³/t(co平均浓度由50%下降到47%)。