塑胶模具设计-脱螺纹模具设计讲义
机动脱螺纹注塑模结构讲解
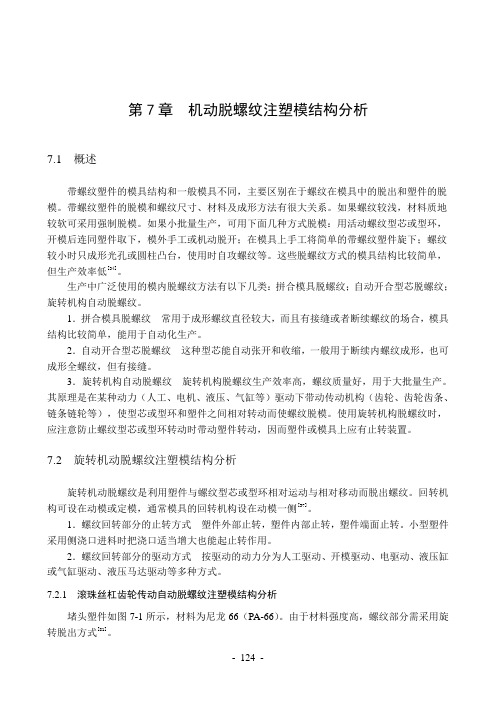
第7章机动脱螺纹注塑模结构分析7.1 概述带螺纹塑件的模具结构和一般模具不同,主要区别在于螺纹在模具中的脱出和塑件的脱模。
带螺纹塑件的脱模和螺纹尺寸、材料及成形方法有很大关系。
如果螺纹较浅,材料质地较软可采用强制脱模。
如果小批量生产,可用下面几种方式脱模:用活动螺纹型芯或型环,开模后连同塑件取下,模外手工或机动脱开;在模具上手工将简单的带螺纹塑件旋下;螺纹较小时只成形光孔或圆柱凸台,使用时自攻螺纹等。
这些脱螺纹方式的模具结构比较简单,但生产效率低[34]。
生产中广泛使用的模内脱螺纹方法有以下几类:拼合模具脱螺纹;自动开合型芯脱螺纹;旋转机构自动脱螺纹。
1.拼合模具脱螺纹常用于成形螺纹直径较大,而且有接缝或者断续螺纹的场合,模具结构比较简单,能用于自动化生产。
2.自动开合型芯脱螺纹这种型芯能自动张开和收缩,一般用于断续内螺纹成形,也可成形全螺纹,但有接缝。
3.旋转机构自动脱螺纹旋转机构脱螺纹生产效率高,螺纹质量好,用于大批量生产。
其原理是在某种动力(人工、电机、液压、气缸等)驱动下带动传动机构(齿轮、齿轮齿条、链条链轮等),使型芯或型环和塑件之间相对转动而使螺纹脱模。
使用旋转机构脱螺纹时,应注意防止螺纹型芯或型环转动时带动塑件转动,因而塑件或模具上应有止转装置。
7.2 旋转机动脱螺纹注塑模结构分析旋转机动脱螺纹是利用塑件与螺纹型芯或型环相对运动与相对移动而脱出螺纹。
回转机构可设在动模或定模,通常模具的回转机构设在动模一侧[37]。
1.螺纹回转部分的止转方式塑件外部止转,塑件内部止转,塑件端面止转。
小型塑件采用侧浇口进料时把浇口适当增大也能起止转作用。
2.螺纹回转部分的驱动方式按驱动的动力分为人工驱动、开模驱动、电驱动、液压缸或气缸驱动、液压马达驱动等多种方式。
7.2.1 滚珠丝杠齿轮传动自动脱螺纹注塑模结构分析堵头塑件如图7-1所示,材料为尼龙66(PA-66)。
由于材料强度高,螺纹部分需采用旋转脱出方式[81]。
塑料螺纹等结构设计讲课文档

图2—9 加强筋尺寸
图中2-9(a)的设计方案较好,而2-9(b)所示方案会使筋底与塑 件主体连接部位壁厚增加过多,因而不可取。
返回
现在二十八页,总共六十页。
图2—10 筋的方向应不妨碍塑料收缩
图2-10是对同一塑件端部筋条设计的两种方案比较,方案(a) 较好,方案(b)不可取,因为方案(b)中的筋条妨碍了塑料收 缩,会造成塑件内应力并引起塑件翘曲,固中箭头所示方向 为塑料收缩方向。
图2—20 细长型芯的支撑
现在四十三页,总共六十页。
返回
2.4.8 采用型芯拼合复杂型孔
图2-21 用拼合型芯成型复杂孔
现在四十四页,总共六十页。
返回
2.5 嵌件、螺纹等结构设计
2.5.1 带嵌件塑件设计 2.5.2 模塑螺纹的结构设计 2.5.3 塑料齿轮的设计 2.5.4 塑料铰链的设计 2.5.5 标记、符号、图案、文字
现在十三页,总共六十页。
2.3 形状和结构设计
2.3.2 强制脱模
当塑件的内外侧凹陷较浅,同时成型塑件 的塑料为聚乙烯、聚丙烯、聚甲醛这类仍带 有足够弹性的塑料时,模具可采取强制脱模。
为使强制脱模时的脱模阻力不要过大引起 塑件损坏和变形,塑件侧凹深度必须在要求 的合理范围内,见图2—5下面的说明(公式), 同时还要重视将凹凸起伏处设计为圆角或斜 面过渡结构。
流程与制品壁厚成直线关系。制品壁厚愈
厚,所容许的流程愈长;反之,制品壁厚
愈薄,所容许的流程愈短。
如果不能满足要求,则需增大壁厚或 增设浇口及改变浇口位置,以满足模塑要 求。
现在二十五页,总共六十页。
制件最小壁厚与流程之间关系:
S( L 0.5)0.6 100
注塑内螺纹直接脱模结构设计方案

注塑内螺纹直接脱模结构设计方案一、整体思路。
咱们得想个办法,让带有内螺纹的塑料制品在注塑完后,能轻松地从模具里脱模,就像从被窝里钻出来一样容易,而且还不能把这个螺纹给搞坏喽。
二、具体结构设计。
1. 螺纹型芯部分。
首先呢,这个螺纹型芯不能是个死脑筋的结构。
咱们可以把它设计成两段式的。
就像火车有车头和车厢一样。
靠近模具型腔内部的那一段螺纹型芯,咱们可以让它稍微细一点,就像小一号的螺丝。
这一段的螺纹是完整的,用来成型产品的内螺纹。
然后外面再套上一段粗一点的“外套”,这个外套和里面的细螺纹型芯之间要有一定的间隙,这个间隙就像两个好朋友之间保持的小距离,不能太大也不能太小,大概在0.1 0.3毫米左右就行。
这个间隙是为了让里面的细型芯在脱模的时候有活动的空间。
2. 脱模动力装置。
为了让螺纹型芯能从产品里退出来,咱们得给它一个动力呀。
这时候可以在模具上安装一个小型的液压或者气动装置。
想象一下,这个装置就像一个小助手,在脱模的时候轻轻地推一下螺纹型芯。
不过这个推力得控制好,不能太猛,不然会把产品给弄坏的。
一般来说,根据产品的大小和材料的特性,这个推力在50 200牛顿之间比较合适。
另外,还可以在螺纹型芯上连接一个旋转机构。
这个旋转机构就像一个小陀螺,在液压或者气动装置推动螺纹型芯往外退的同时,让它慢慢地旋转。
因为内螺纹嘛,要是光直直地往外退,肯定会卡住的,就像你硬要把拧进去的螺丝直接拔出来一样困难。
这个旋转的速度也不能太快,每分钟大概转个5 10圈就差不多了。
3. 导向和限位结构。
在螺纹型芯的周围,要设置一些导向柱。
这些导向柱就像轨道一样,让螺纹型芯在脱模的时候只能按照规定的方向移动。
就像火车只能在铁轨上跑一样。
导向柱的表面要光滑得像溜冰场一样,这样可以减少摩擦,保证螺纹型芯移动得顺畅。
同时呢,还要有限位装置。
这个限位装置就像一个小警察,告诉螺纹型芯你只能移动到这个位置,不能再往前走了。
这样可以防止螺纹型芯过度脱模,把模具或者产品给损坏了。
塑料模具课件-脱摸机构图
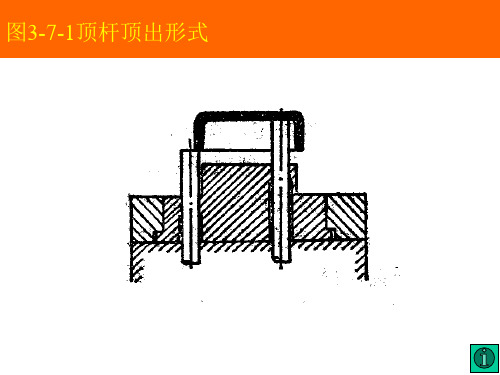
图3-7-55大升角螺杆结构
图3-7-56气(液)动形式
图3-7-57电动机驱动形式
脱摸力计算图
脱摸力计算图
脱摸力计算图
脱摸力计算图
导柱的安装
导柱
导柱的安装
导柱的安装固定形式
导套
盲孔导套的侧壁开孔
导套与孔的固定
直导套的固定
导柱与导套的配合形式
导柱的布置形式
锥面定位
1-圆柱销 2-弹簧 3-摆杆 4-U形限制架 5-注射机顶杆 6-转动
图3-7-23 U形限制架式
图3-7-23 U形限制架式
图3-7-24滑块式二次脱模机构
1-型芯 2-顶出干 3-推板 4-顶杆 5-斜导柱 6-滑块
图3-7-24滑块式二次脱模机构
图3-7-24滑块式二次脱模机构
3-7-25滑块式二次脱模机构
锥面定位
顶杆的形状
顶管顶出机构
1 顶出板 2 顶管 3方销 4 型芯 5 塑件
顶管顶出机构
顶管顶出机构
推板脱模机构
推板脱模机构
带周边间隙的脱模板
进气装置
1 推板 2 顶杆 3弹簧
利用活动镶件脱出塑件
利用型腔的脱模结构
多元件综合脱模机构
讨论题目
请画出这两种顶杆的固定方式
讨论L和H的公差,并说明原因
图3-7-11双脱摸机构
1、型芯 2、型腔
图3-7-12气动双脱模机构
1、4-密封圈 2、3-空气阀门
图3-7-13弹簧顺序脱模机构
图3-7-14拉钩顺序脱模机构
1、压块 2-挡块 3-拉钩 4-拉板 5-弹簧 6-滚轮 7-定模
图3-7-15拉钩顺序脱模机构
1-定模板 2-定模型腔 3-动模板 4-凸块 5-转轴 6-拉钩 7圆销 8- 定伸弹簧 9-定距拉板
螺纹脱模
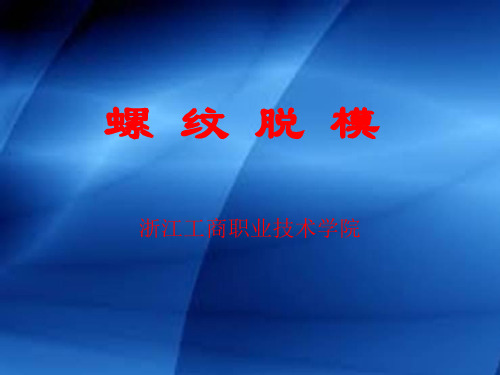
1) 对塑件的要求:由于螺纹表面有沟槽,所以,内螺纹必须 对塑件的要求:由于螺纹表面有沟槽,所以, 由螺纹型芯, 外螺纹必须由螺纹型环成型,而脱模时必 由螺纹型芯, 外螺纹必须由螺纹型环成型, 须从螺纹型芯或螺纹型环上脱出, 须从螺纹型芯或螺纹型环上脱出,两者之间必须作相对转 因此,塑件的外形或端面须有防止转动的花纹或图案, 动,因此,塑件的外形或端面须有防止转动的花纹或图案, 否则难以脱出。 否则难以脱出。 2) 对模具的要求:塑件不能转动,模具应有相应的防转措施 对模具的要求:塑件不能转动, 给予保证。当塑件型腔和螺纹型芯同在动模上时, 给予保证。当塑件型腔和螺纹型芯同在动模上时,型腔可 以保证不使塑件转动。但当型芯和型腔分别处在动、 以保证不使塑件转动。但当型芯和型腔分别处在动、定模 上时,开模后,塑件就离开定模型腔,此时, 上时,开模后,塑件就离开定模型腔,此时,即使塑件外 形有防转花纹也不起作用, 形有防转花纹也不起作用,塑件会留在动模型芯上和它一 起转动而无法脱模,因此在模具上要另设止转机构。 起转动而无法脱模,因此在模具上要另设止转机构。
螺 纹 脱 模
浙江工商职业技术学院
塑件螺纹
很多塑件上带有螺纹, 很多塑件上带有螺纹,螺紋的种类主 要有两大类:内螺纹和外螺纹。 要有两大类:内螺纹和外螺纹。螺纹表面 均带沟槽, 均带沟槽,因此脱模的方式与一般塑件不 它需要有特殊的脱模机构。 同。它需要有特殊的脱模机构。
设计螺纹脱模机构的注意点
设计带螺纹塑件的脱模机构应注意的问题
螺纹脱模方式
带螺纹塑件的脱模方式
对带螺纹塑件的脱模方式主要有以下几种。 对带螺纹塑件的脱模方式主要有以下几种。 1) 手动脱螺纹,这是在塑件成型、开模后,用 手动脱螺纹,这是在塑件成型、开模后, 手工或简单工具将型芯或型环从塑件上旋出。这 手工或简单工具将型芯或型环从塑件上旋出。 类模具的结构简单,易于制造,但劳动强度大, 类模具的结构简单,易于制造,但劳动强度大, 生产效率低。 生产效率低。 2) 强制脱螺纹,这是利用塑件的弹性或型芯的 强制脱螺纹, 弹性,使塑件或型芯与螺纹产生轴向移动, 弹性,使塑件或型芯与螺纹产生轴向移动,强行 将型芯或塑件拉离螺纹而脱模。这类模具结构也 将型芯或塑件拉离螺纹而脱模。 较简单,主要用于螺纹精度要求不高, 较简单,主要用于螺纹精度要求不高,螺紋形状 比较容易脱出的塑件。 比较容易脱出的塑件。
自动脱螺纹注塑模设计[1].pdf
![自动脱螺纹注塑模设计[1].pdf](https://img.taocdn.com/s3/m/2cee183b87c24028915fc368.png)
自动脱螺纹注塑模设计田福祥 贺 斌(青岛理工大学,青岛 266033) 摘要 给出了链轮传动自动脱螺纹注塑模结构。
该模具采用热流道针阀式点浇口进料,无流道废料;通过链条传动使螺纹型芯转动,同时利用端面止转,实现自动脱螺纹;在动、定模型腔及螺纹型芯上分别设置三套冷却系统,使模具充分冷却。
模具结构紧凑、工作可靠、操作方便、运转平稳、冷却效果好、劳动强度低、生产效率高,生产的塑料件精度高。
关键词 热流道 自动脱螺纹 针阀式点浇口 注塑模 带有螺纹的塑料件注塑模设计的关键是塑料件螺纹的脱模问题。
通常有两种螺纹脱模方法:一是在塑料件及其材料允许的情况下,强行推出;二是对于螺纹较深、精度要求高、强度高的塑料件,旋转脱出。
旋转脱螺纹又分为手动脱出和自动脱出。
手动脱螺纹适合小批量生产,生产效率低,但模具结构简单;自动脱螺纹用于大批量生产,生产效率高,塑料件螺纹精度高。
笔者设计了链轮传动自动脱螺纹模具。
1 塑料件工艺分析塑料密封盖的形状及尺寸见图1。
塑料件形状简单,但壁厚不均匀,内径为矩形螺纹,没有止转圈,外观及螺纹精度要求较高,需求量大。
所用材料高密度聚乙烯(H DPE )是半结晶材料,流动性好,但成型收缩率较大(1.5%~4%),易发生应力开裂。
图1 塑料密封盖零件图2 模具结构及工作过程根据该塑料件特点及要求,设计的模具结构如图2所示。
模具为1模1腔,采用热流道针阀式点浇口进料,通过链条传动实现自动脱螺纹。
1—动模座板;2—链轮;3—水套;4—轴承;5—垫板;6—动模;7—螺纹型芯;8—气塞;9—垫板;10—垫块;11—定模座板;12—热喷嘴;13—隔热板;14—导套;15—集流腔板;16—型芯镶件;17—定模;18—衬套;19—限位螺钉;20—滚柱;21—弹簧;22—冷却水管;23—衬套;24—垫块;25—密封圈图2 塑料密封盖模具结构图2.1 浇注系统浇口位置及浇口种类决定了熔料在型腔中的流 收稿日期:200420820515田福祥,等:自动脱螺纹注塑模设计动方向与路径,如果浇口位置设置不当或浇口种类选用不合适,则可能使塑料件的形状变形或某些尺寸超差。
自动脱螺纹的注塑模设计

1塑件与注塑工艺分析
பைடு நூலகம்根
图1 气 ,采 用 侧 浇 口 进料 浇 注 的 方 式 ,在 主浇 口和 分 流道 设 置 冷 料 穴 以防 浇 口被熔 融 的流 体 前 段 的 冷料 堵 塞 。分 流道 设 计 成 直 径
为 6 m的 圆 型流 道 。为 便 于 定模 弯 销 的 抽芯 ,浇 口套前 端 设 计 a r
tra h e d.Pr du ton e i i nc f t e de a t s g e ty i r a e n o c i t e t f pe s nn l r d ce i g fe t f c e o c i f c e y o hr a d p r s i r a l nc e s d a d pr du ton sr ng h o r o e e u d by usn e c s o or pu ln i x d m o d si l k a d yd a lc p l g va f e i i l l de b oc n h r u i um p.Ac o di o pr uc i ld to c r ng t od ton vai a i n,t s m o d sr t e p ov de t b e a e i b e hi l tuc ur r i s sa l nd r l l a a to n o e v c ie.Pr uc i n pr e s i e s a l nd pr duc e t he t c ni a e ie e s hr g c i ns a d l ng s r i e lf od t o oc s sr a on b e a o t m e s t e h c lr qu r m nt,t ou h wh c t ur i h he p pos f eo
塑料模具课件_脱模机构
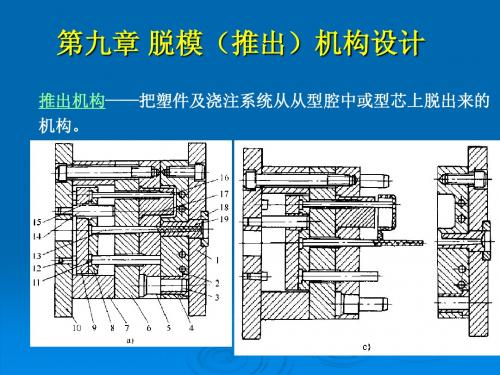
3.模内旋转的脱模方式
(1)螺纹塑件的止转形式
模具设自动脱螺纹机构时塑件外形有止转结构,通常为花纹。
常用模内旋转脱螺纹机构主要有手动脱螺纹和机动脱螺 纹两种。
(2) 手动脱螺纹机构
(3) 机动脱螺纹机构
原理:利用开模时的直线运动,通过齿轮齿条的运动,使 螺纹型芯作回转运动而脱离塑件。 图为,锥齿轮脱螺纹型 芯结构,它用于侧浇口多 型腔模,螺纹型芯只要作 回转运动就可脱出塑件。
p—因塑件收缩对型芯产生的单位正压力(12~20MPa) A—塑件包紧型芯的侧面积(mm2)
F脱= pA(f·cosα-sinα)
总脱模力等于F总=F脱+F大气(大气压力影响:引气、不引气) 以上对脱模力的计算是一种比较粗略的方法。 计算脱模力是为了校核设备的顶出力是否足够,以及校核推出 元件的刚度强度及可靠性。
为减少脱模过程中推件板与型芯之间的摩擦,两者之间留有0.2~ 0.25mm的间隙,并采用锥面配合,以防止推件板 偏斜溢料,锥面 的斜度约取3~5˚左右,图 (b)。
引气装置: 对于大型深腔薄壁容器,推板脱模时 塑件部易形成真空, 使脱模困难,甚至还会使塑件变形或损坏,应在凸模上附设引 气装置,如图(推件板引气)。(推件板不引气)
加粗,增加刚性。
顶盘式推杆:锥面推杆,推出面积较大,适合于深筒形塑件 推出。
b)
c)
d)
2.推杆的固定及配合
(1)推杆的固定
2.推杆的配合
推杆固定板上的孔为d+1mm;推杆台阶部分的直径为
d+5mm;推杆固定板上的台阶孔为d+6mm。推杆与固定 板配合长度为S(一般采用H8/f8配合)
S 可取12~15mm;当d>5mm时, S=(2~3)d (d为推杆直径),配合部分表面Ra=0.8μm。 推杆与塑料接触并与孔经常摩擦,因此多采用热处理后硬度 高的材料制作。推杆材料常用T8A、T10A等碳素工具钢 (50 ~ 54HRC自制推杆)或65Mn (46 ~ 50HRC市场上的 推杆标准件)
- 1、下载文档前请自行甄别文档内容的完整性,平台不提供额外的编辑、内容补充、找答案等附加服务。
- 2、"仅部分预览"的文档,不可在线预览部分如存在完整性等问题,可反馈申请退款(可完整预览的文档不适用该条件!)。
- 3、如文档侵犯您的权益,请联系客服反馈,我们会尽快为您处理(人工客服工作时间:9:00-18:30)。
自动卸螺纹模具设计初级教程
BY WELLDESIGN17.Nov,04
前言:
塑胶产品螺纹分外螺纹和内螺纹两种,精度不高的外螺纹一般用哈夫块成型,而内螺纹则大多需要卸螺纹装置。
今天简单介绍内螺纹脱模方法,重点介绍齿轮的计算和选择。
一、卸螺纹装置分类
1、按动作方式分
①螺纹型芯转动,推板推动产品脱离;
②螺纹型芯转动同时后退,产品自然脱离。
2、按驱动方式分
1油缸+齿条
2油马达/电机+链条
3齿条+锥度齿轮
4来福线螺母
二、设计步骤
1、必须掌握产品的以下数据(见下图)
①“D”——螺纹外径
②“P”——螺纹牙距
③“L”——螺纹牙长
4螺纹规格/方向/头数
5型腔数量
2、确定螺纹型芯转动圈数
U=L/P+Us
U螺纹型芯转动圈数
Us安全系数,为保证完全旋出螺纹所加余量,一般取0.25~1
3、确定齿轮模数、齿数和传动比
模数决定齿轮的齿厚,齿数决定齿轮的外径,传动比决定啮合齿轮的转速。
在此之前有必要讲一下齿轮的参数和啮合条件。
三、齿轮的参数和啮合条件
模具的卸螺纹机构中大多应用的是直齿圆柱齿轮,而且一般都是渐开线直齿圆柱齿轮,因此下面就以渐开线直齿圆柱齿轮为研究对象。
1、齿轮传动的基本要求
①要求瞬时传动比恒定不变
②要求有足够的承载能力和较长的使用寿命
2、直齿圆柱齿轮啮合基本定律
两齿轮廓不论在何处接触,过接触点所作的两啮合齿轮的公法线,必须与两轮连心线相交于一点“C”,这样才能保证齿轮的瞬时传动比不变。
将所有“C”点连起来就成了2个外切圆,称之为分度圆,分度圆圆心距即齿轮圆心距。
详见下图
3、渐开线直齿圆柱齿轮参数
分度圆直径------“d”表示
分度圆周长--------“S”表
示
齿轮齿距--------“p”表示
齿轮齿厚--------“sk”表
示
齿轮齿槽宽--------“ek”
表示
齿轮齿数--------“z”表示
齿轮模数--------“m”表示
齿轮压力角--------“ɑ”表示
齿轮传动比--------“i”表示
齿轮中心距--------“l”表示
4、计算公式如下:
①齿距=齿厚+齿槽宽即:p=sk+ek
②模数的由来
因为S=Z x P=πx d
d=P/πx Z
π是无理数,为计算方便,将P/π规定为常数,即模数,用m表示,故有公式如下:d=m x z
即:分度圆直径等于模数乘以齿数。
我国规定模数有2个系列,优先采用第一系列。
模数第一系列:1、1.25、1.5、2、2.5、3、4、5、68、10…模数第二系列:1.75、2.25、2.75、3.25、3.5、4.5、5.5、7…
③压力角
我国规定:分度圆处的压力角为标准压力角,其值20°。
④传动比
当模数一定时,传动比就等于齿数比,即i=Z1/Z2
⑤中心距
当齿数确定时,中心距I=(Z1+Z2)/2*m
5、齿轮啮合条件
模数和压力角相同的齿轮都可以正确啮合。
四、现在回到二、3,怎样在实际应用中确定齿轮的模数、齿数和传动比。
1.齿数
当传动中心距一定时,齿数越多,传动越平稳,噪音越低。
但齿数多,模数就小,齿厚也小,致使其弯曲强度降低,因此在满足齿轮弯曲强度条件下,尽量取较多的齿数和较小的模数。
为避免干涉,齿数一般取Z≥17,螺纹型芯的齿数尽可能少,但最少不少于14齿,且最好取偶数。
2.模数
工业用齿轮模数一般取m≥2。
英制齿轮采用径节制,径节齿轮把齿数z与分度圆直径d之比定为径节,以”P”表示,即
p=z/d,1/in
径节与模数的换算公式为
m=25.4/p,mm
3.传动比
传动比在高速重载或开式传动情况下选择质数,目的为避免失效集中在几个齿上。
传动比还与选择哪种驱动方式有关系,比如用齿条+锥度齿或来福线螺母这两种驱动时,因传动受行程限制,须大一点,一般取1≤i≤4;当选择用油缸或电机时,因传动
无限制,既可以结构紧凑点节省空间,又有利于降低马达瞬间启动力,还可以减慢螺纹型芯旋转速度,一般取0.25≤i≤1。
五、卸螺纹机构其它配件
1.轴承选择
①深沟球轴承------主要承受径向负荷也可承受一定轴向负荷
②圆锥滚子轴承------可以同时承受径向和轴向负荷
③推力球平面轴承------只承受轴向负荷
2.链轮选择
链轮参数有:p--------节距
d--------分度圆直径
z--------链轮齿数链轮分度圆计算公式:d=p/sin(180゜/z)
节距为标准值,如下:8,9.525,12.7,15.875,
19.05,25.4,31.75,38.1,44.45,50.8…
六、附录
附录包括模具结构实例和HASCO标准件目录。
实例1
实例
2
UG全套学习视频免费赠送加扣275-140-4682。