管道外防腐统一技术规定
管道防腐前处理标准
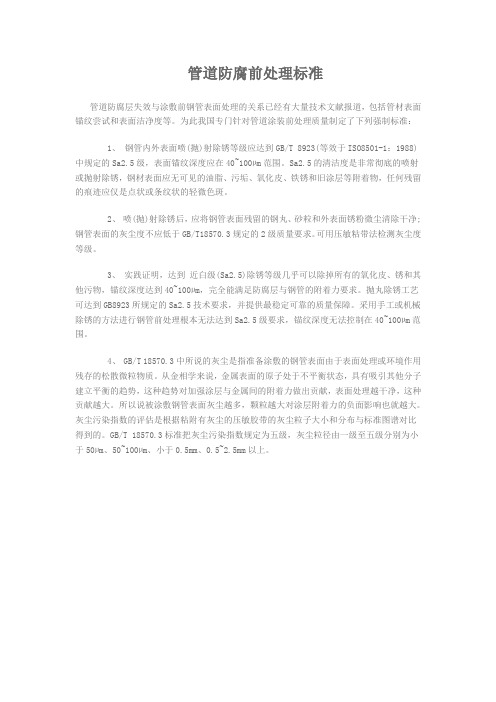
管道防腐前处理标准管道防腐层失效与涂敷前钢管表面处理的关系已经有大量技术文献报道,包括管材表面锚纹尝试和表面洁净度等。
为此我国专门针对管道涂装前处理质量制定了下列强制标准:1、钢管内外表面喷(抛)射除锈等级应达到GB/T 8923(等效于ISO8501-1:1988)中规定的Sa2.5级,表面锚纹深度应在40~100µm范围。
Sa2.5的清洁度是非常彻底的喷射或抛射除锈,钢材表面应无可见的油脂、污垢、氧化皮、铁锈和旧涂层等附着物,任何残留的痕迹应仅是点状或条纹状的轻微色斑。
2、喷(抛)射除锈后,应将钢管表面残留的钢丸、砂粒和外表面锈粉微尘清除干净;钢管表面的灰尘度不应低于GB/T18570.3规定的2级质量要求。
可用压敏粘带法检测灰尘度等级。
3、实践证明,达到近白级(Sa2.5)除锈等级几乎可以除掉所有的氧化皮、锈和其他污物,锚纹深度达到40~100µm,完全能满足防腐层与钢管的附着力要求。
抛丸除锈工艺可达到GB8923所规定的Sa2.5技术要求,并提供最稳定可靠的质量保障。
采用手工或机械除锈的方法进行钢管前处理根本无法达到Sa2.5级要求,锚纹深度无法控制在40~100µm范围。
4、 GB/T 18570.3中所说的灰尘是指准备涂敷的钢管表面由于表面处理或环境作用残存的松散微粒物质。
从金相学来说,金属表面的原子处于不平衡状态,具有吸引其他分子建立平衡的趋势,这种趋势对加强涂层与金属间的附着力做出贡献,表面处理越干净,这种贡献越大。
所以说被涂敷钢管表面灰尘越多,颗粒越大对涂层附着力的负面影响也就越大。
灰尘污染指数的评估是根据粘附有灰尘的压敏胶带的灰尘粒子大小和分布与标准图谱对比得到的。
GB/T 18570.3标准把灰尘污染指数规定为五级,灰尘粒径由一级至五级分别为小于50µm、50~100µm、小于0.5mm、0.5~2.5mm以上。
钢质管道内外防腐技术要求

钢质管道内外防腐技术要求1 除锈管道内外喷砂除锈达到GB/T 8923《涂装前钢材表面锈蚀等级和除锈等级》Sa2 .5级或St3级(相当于美国标准SSPC—SP10近白级)。
表面返锈前(最多为除锈后8h)进行刷喷涂防腐作业,如做不到,应涂底漆。
2 管道内防腐2.1材料品种环氧陶瓷涂料。
适用于饮用水管道(白色、无毒型),耐磨,耐化学腐蚀。
技术性能符合生产厂家产品技术标准《环氧陶瓷涂料》要求。
2.2内防腐层结构2.3环境。
环氧陶瓷内防腐作业宜在5ºC以上,空气相对湿度80ºC以下的环境施工。
如在露天作业,遇雨、雪、雾、扬沙等恶劣气候环境,应停止施工。
2.4材料用量按防腐面积乘以下列基数计算各种材料用量a) 环氧陶瓷涂料。
按涂敷遍数估算耗漆量,厚度150μm约为0.35㎏/㎡。
b) 稀释剂。
只作为施工时洗涤涂敷工具之用,可少量配料。
2.5 技术指标2.6内防腐施工钢管两端要留出焊接段(20cm左右)。
总厚度不低于300μm。
宜喷涂施工。
涂后静置自然固化。
按用户要求的总厚度或者涂刷遍数施工。
前遍表干后再涂后遍。
2.7检验对内防腐层进行外观、厚度、漏点、粘结力四项检查,应达到用户要求。
可参照SY/T 0457-2000《钢制管道液体环氧涂料内防腐层技术标准》的5.3.2~5.3.5条要求进行。
2.8 修补补口修补。
用砂轮机将检查出的表面缺陷(如:杂质、气泡等)清除掉,将缺陷点及周围约50㎜的内衬层打毛,然后涂环氧陶瓷涂料,使修补处表面平整、厚度相同、外观一致。
不合格管返工。
补口。
作业在施工现场进行,据不同管径可以使用手动工具除锈和手工涂刷施工,或使用机械喷涂施工,所使用的涂料和涂层结构应与管体相同。
3埋地管道外防腐3.1材料品种环氧煤沥青冷缠带。
由基带和定型胶两部分组成,应为同一公司产品。
基带为特加强级带。
标准宽度为125㎜、250㎜、和400㎜。
定型胶由分装的A、B等量组份组成。
组合厚度≥600μm。
焊接钢管防腐规范
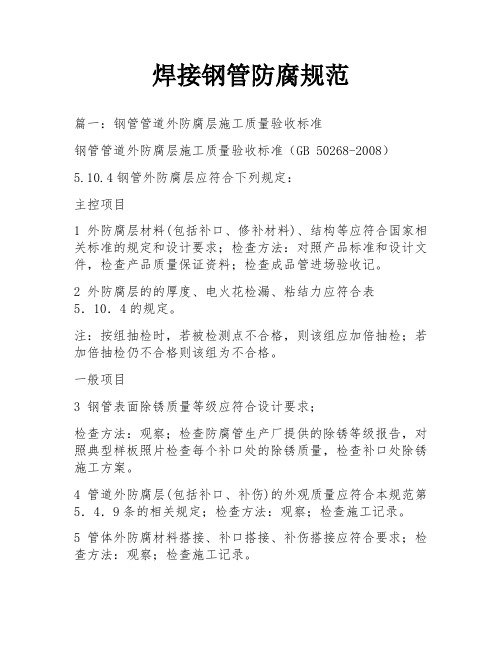
焊接钢管防腐规范篇一:钢管管道外防腐层施工质量验收标准钢管管道外防腐层施工质量验收标准(GB 50268-2008)5.10.4钢管外防腐层应符合下列规定:主控项目1 外防腐层材料(包括补口、修补材料)、结构等应符合国家相关标准的规定和设计要求;检查方法:对照产品标准和设计文件,检查产品质量保证资料;检查成品管进场验收记。
2 外防腐层的的厚度、电火花检漏、粘结力应符合表5.10.4的规定。
注:按组抽检时,若被检测点不合格,则该组应加倍抽检;若加倍抽检仍不合格则该组为不合格。
一般项目3 钢管表面除锈质量等级应符合设计要求;检查方法:观察;检查防腐管生产厂提供的除锈等级报告,对照典型样板照片检查每个补口处的除锈质量,检查补口处除锈施工方案。
4 管道外防腐层(包括补口、补伤)的外观质量应符合本规范第5.4.9条的相关规定;检查方法:观察;检查施工记录。
5 管体外防腐材料搭接、补口搭接、补伤搭接应符合要求;检查方法:观察;检查施工记录。
5.4.9 外防腐层的外观、厚度、电火花试验、粘结力应符合设计要求,设计无要求时应符合表5.4.9的规定。
篇二:管道防腐标准管道及设备防腐工艺标准实施日期:2000年1月1日1范围本工艺标准适用于室内外管道、设备和容器的防腐工程。
2施工准备2.1 材料要求:2.1.1 防锈漆、面漆、沥青等应有出厂合格证。
2.1.2 稀释剂:汽油、煤油、醇酸稀料、松香水、酒精等。
2.1.3 其它材料:高岭土、七级石棉、石灰石粉或滑石粉、玻璃丝布、矿棉纸、油毪、牛皮纸、塑料布等。
2.2 主要机具:2.2.1 机具:喷枪、空压机、金钢砂轮、除锈机等。
2.2.2 工具:刮刀、锉刀、钢丝刷、砂布、砂纸、刷子、棉丝、沥青锅等。
2.3 作业条件:2.3.1 有码放管材、设备、容器及进行防腐操作的场地。
2.3.2 施工环境温度在5℃以上,且通风良好,无煤烟、灰尘及火汽等。
气温在5 ℃以下施工要采取冬季施工措施。
防腐涂漆规定
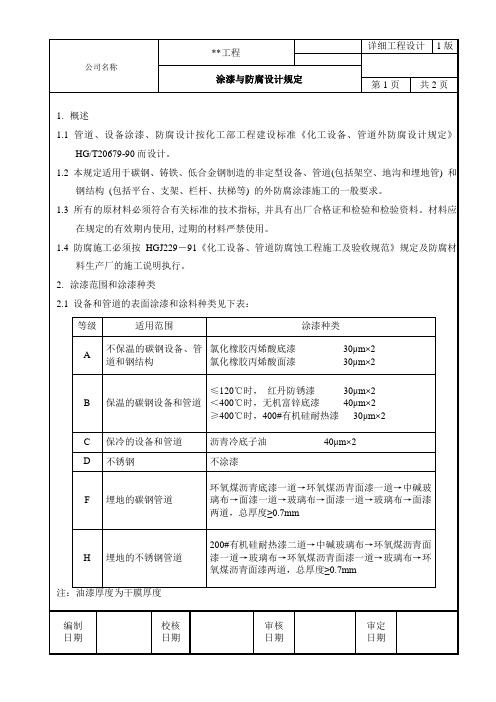
2.2 对于铝材、塑料类的设备、管道以及制造厂已提供完整底漆和面漆的机电设备、机泵、电器设备、开关柜、仪表盘等均不需涂漆。
如有破损,只需涂修补漆。
3.表面处理3.1 表面处理要求设备、管道和钢结构表面应无可见的油脂和污垢,并且没有附着不牢的氧化皮、铁锈和油漆涂层等附着物,即达到《化工设备、管道外防腐设计规定》HG/T20679-90中的ST3级。
3.2 为了使处理后的金属表面不致再锈蚀和粘上油污,在表面处理后,必须在不迟于3小时内涂刷第一道底漆。
3.3 法兰密封面以及其他密封面不得使用机械清理,而应采用手工清理。
4.设备和管道表面涂色说明4.1 为了统一全厂各设备、管道的表面涂色,使其整齐美观,便于识别和保证生产操作的安全,故对全厂各个设备、管道的表面涂色作如下规定:4.1.1 UF/RO膜架碳钢结构一律涂成银色,其设备附件的涂色与本体相同。
4.1.2 鼓风机/泵等设备及其附件一律为出厂色。
加药装置的碳钢结构框架/CIP罐一律涂成银色。
其它材质为不锈钢/PE的设备,保持本色,不涂色。
电控柜/仪表柜一律为海灰色。
4.1.3 用黑色喷写设备位号,字体要整齐、大小适当、醒目。
4.1.4 对消防设施如消火栓、消防箱等采用大红色+黄色,危险设施如射线源等涂成黄色与黑色间隔斜条。
4.1.5 对于不保温的管道按照CJ/T158-2002中管道涂色要求执行,以便于识别管内介质的种类和状态。
4.2 保温管道的保护层表面,应涂刷识别色环,色环的尺寸大小要求参见CJ/T158-2002中的相关要求。
4.3 为有利于识别介质种类、压力和流向,在主要管道上应标出介质的流向,并注明按照〈管道命名表〉的管道编号。
这样当遇到紧急情况时,能够迅速找到并及时关闭阀门,以控制事态的发展。
箭头标志一般用铁皮镂空制成模板,然后喷涂识别漆,识别漆的颜色及箭头的尺寸大小要求参见CJ/T158-2002中的相关要求。
编制日期校核日期审核日期审定日期。
《城镇燃气埋地钢质管道腐蚀控制技术规章》CJJ95

城镇燃气埋地钢质管道腐蚀控制技术规程CJJ95Technical specification for external corrosion control of buried steel pipeline for city gas1 总则1.0.1 为使城镇燃气埋地钢质管道(以下简称管道)腐蚀控制工程达到统一标准、合理设计、规范施工、科学管理的目的,制定本规程。
1.0.2 本规程适用于城镇燃气埋地钢质管道外腐蚀控制工程的设计、施工、验收和管理。
1.0.3 腐蚀控制工程应做到技术可靠、经济合理、保护环境;并应不断采用新技术、新设备、新材料、新工艺,满足腐蚀控制要求,提高经济效益、环境效益和社会效益。
1.0.4 管道腐蚀控制工程除应符合本规程外,尚应符合国家现行有关标准的规定。
2 术语2.0.1 腐蚀corrosion金属与环境介质间的物理——化学相互作用,其结果使金属的性能发生变化,并常可导致金属、环境或由它们组成的作为部分技术体系的功能受到的损伤。
2.0.2 腐蚀速率corrosion rate单位时间内金属遭受腐蚀的质量损耗量或深度损耗量,常以mm/a或g/m2·h表示。
2.0.3 腐蚀控制corrosion control人为改变金属的腐蚀体系要素,以降低金属的质量损耗和对环境介质的影响,保障管道的服役功能。
2.0.4 腐蚀电位corrosion potential在开路条件下,处于电介质中的腐蚀表面相对于参比电极的电位,也称为静止电位(rest potential)、开路电位(open-circuit potential)或自然腐蚀电位(freely corroding potential)。
2.0.5 防腐层coating涂覆在管道及其附件表面上,使其与腐蚀环境实现物理隔离的绝缘材料层。
2.0.6 漏点holiday防腐层的不连续处(孔),导致未被保护的表面暴露于环境中。
2.0.7 电绝缘electrical isolation管道与相邻的其他金属物或环境物质之间,或在管道的不同管段之间呈电气隔离的状态。
管道及管件外防腐施工技术要求

管道及管件外防腐施工技术要求(1)除锈应严格按照GB8923-88《涂装前钢材表面处理规范》中的规定,对钢管表面进行机械抛丸除锈,处理后的钢管表面最低要求应达到Sa2.5级,表面粗糙度宜在40-50 。
钢管表面处理后,其表面的灰尘应清除干净,焊缝应处理至无焊瘤、无棱角、无毛刺。
(2)涂底漆不锈钢管除锈合格后,应尽快涂刷底漆,间隔时间不得超过8小时,大气环境恶劣时间隔应进一步缩短。
底漆涂料干膜厚度应不小于25um。
每根管两端各预留裸管150mm左右,只涂底漆,不刷面漆,以便焊接。
(3)打腻子钢管外防腐层采用玻璃布作加强基布时,在底漆表干后,对高于钢管表面2mm的焊接两侧,应抹腻子使其形成平滑过度面。
腻子由配好固化剂的面漆加入滑石粉调匀制成,调制时不应加入稀释剂,调好的腻子宜在4h内用完。
(4)涂面漆和缠玻璃布底漆或腻子表干后,固化前涂第一道面漆,要求涂刷均匀,不得漏涂。
对普通级防腐层,每道面漆实干后、固化前涂下一道面漆,直至达到规定层数。
对加强级防腐层,第一道面漆实干后、固化前涂第二道面漆,随即缠绕玻璃布。
玻璃布要接紧、表面平整、无皱折和鼓包,压边宽度为20-25mm,布头搭接长P为100-150mm。
玻璃布缠绕后即涂第三道面漆实干后(也可用浸满面漆的玻璃布进行缠绕,代替第二道面漆、玻璃布和第三道面漆),待其实干后,涂最后一道面漆。
(5)养护及注意事项①环氧煤沥青玻璃布涂料的养护时间为10℃以下养护7-10天,10℃-30℃养护5-7天,30℃以上养护3-5天。
未达到养护时间要求的管道不得提前使用②除非采取特殊措施外,严禁在雨、雾、雪和大风中进行露天作业③已涂抹环氧煤沥青的管道在炎热天气应防止阳光直接照射。
雨天予以遮护,不锈钢法兰。
④防腐层所有缺陷和在检查中破坏的部位在管道被运至埋设现场前应彻底修补好并经过重新检查。
2.7.4.2 管道接口处的外防腐施工技术要求(1)管子接口处的外防腐应在回填土前和焊缝试验后迅速进行。
污水管线外防腐隐患治理技术要求范本(2篇)

污水管线外防腐隐患治理技术要求范本一、引言污水管线的外防腐隐患治理是确保污水系统运行安全可靠的重要环节。
为了保障污水管线的长期稳定运行,必须对其进行定期维护和检修工作,及时修复存在的外防腐隐患,防止腐蚀引起的管线损坏并保护环境安全。
二、技术要求1. 管线材料选用(1) 污水管线外壁材料在选用时应具有较好的耐腐蚀性能和持久性。
(2) 优先选用密闭性好、抗腐蚀性强的材料,如玻璃钢管、塑料管等,以减少腐蚀的发生。
(3) 管线材料应符合相关标准要求,并具有耐化学药品侵蚀的能力。
2. 防腐涂层施工(1) 防腐涂层的施工应符合相关标准要求,并按照厂家提供的技术规范进行操作。
(2) 施工前应对管线外壁进行彻底清洁,并确保其表面干燥、无杂质和油污等。
(3) 防腐涂层应均匀、牢固地涂覆在管线外壁上,确保涂层的厚度符合设计要求。
(4) 施工后应进行质量检验,检测涂层的附着力、耐压和耐化学药品侵蚀性能,确保其完好有效。
3. 防腐层检测与修补(1) 定期对污水管线的防腐层进行检测,及时发现腐蚀、破损或剥落等问题。
(2) 对于检测发现的防腐层问题,应立即进行修补。
修补材料应与原材料相匹配,具有相同的性能和耐腐蚀能力。
(3) 修补后应进行质量验收,确保修补部位与管线表面的结合紧固、牢固。
4. 管道防腐检查井设置(1) 污水管线中应合理设置检查井,便于检修和维护工作的进行。
(2) 检查井应具有良好的密封性能和防腐蚀能力,以防止污水渗漏和腐蚀侵蚀。
(3) 检查井的材料选用应符合防腐要求,并具有良好的耐化学药品侵蚀性能。
5. 排水工程(1) 污水管线的排水工程应合理设计,确保排水顺畅,避免积水导致管线腐蚀。
(2) 排水设施应设置防腐蚀措施,如防腐涂层、防腐层修补等,保证其长期使用效果。
6. 环境保护(1) 污水管线外防腐治理过程中应减少对环境的污染。
(2) 废弃的防腐涂层、修补材料等应妥善处理,避免对周围环境造成污染。
(3) 污水管线附近的土壤和地下水应定期检测,确保无污染。
管道防腐

管道防腐施工工艺及质量验收控制标准1. 施工部署1.1 外壁除锈采用砂轮除锈方法,除锈标准达到St2级;内壁采用喷砂除锈方法,喷砂除锈标准达到Sa2.5级标准。
1.2 外壁施工时管道架起高度不应小于50cm;单独施工内壁时以支起管道离开地面为宜。
1.3 管道接口部位应预留足够的焊接长度,待安装完成及各类试验结束后再进行现场防腐。
1.4 根据现场施工作业量及施工工期合理安排施工机械及劳动力资源。
1.5 为保证工程工期将管道分为内壁施工与外壁施工可同时进行两部分。
配合制作、安装单位,适当利用起重机械对管道进行翻身、挪动以提高工作效率。
1.6 外壁两布三油防腐层施工采用分层贴衬法;内壁一底两面防腐施工采用手工滚涂法进行施工。
1.7 直径小于1米的管道内壁喷砂时采用内壁喷砂设备,不再采用人员进入法进行施工。
1.8 管道内壁施工时如一根管道长度大于6米时必须配备通风设备。
1.9 制定事故应急预案,采取安全保证措施;确保施工无任何安全事故发生。
2. 施工工序2.1 管道外壁防腐施工工序:架起被防腐管道――搭设脚手架――砂轮机除锈――检查合格――清除表面灰尘――涂刷环氧煤沥青漆、缠绕玻璃丝布一层(预留接口)――检查合格――涂刷环氧煤沥青漆、缠绕玻璃丝布一层(预留接口)――检查合格――涂刷环氧煤沥青漆一遍――检查合格――拆除脚手架――交付安装――焊口补敷――清理施工现场。
2.2 管道内壁防腐施工工序:架起被防腐管道――喷砂除锈――检查合格――清除表面灰尘――涂刷环氧煤沥青底漆二遍(预留接口)――检查合格――涂刷环氧煤沥青面漆二遍(预留接口)――检查合格――交付安装――焊口补敷――清理施工现场。
3. 主要施工方法3.1 架起管道:外壁施工时,先根据每段焊制管道的长度用两到三根管道将被施工管道架起,并在管道下部打掩,以防在施工时发生滚动。
承重管道的长度应是架起管道周长的12-1.5倍;架起高度不应小于50cm。
3.2 脚手架搭设:由于本工程所涉及的管道直径不大于2米,故脚手架采用简易式的平台脚手架;其特点搭拆方便、牢固实用。
- 1、下载文档前请自行甄别文档内容的完整性,平台不提供额外的编辑、内容补充、找答案等附加服务。
- 2、"仅部分预览"的文档,不可在线预览部分如存在完整性等问题,可反馈申请退款(可完整预览的文档不适用该条件!)。
- 3、如文档侵犯您的权益,请联系客服反馈,我们会尽快为您处理(人工客服工作时间:9:00-18:30)。
219
6
50
331
6
DN250
273
8
50
385
6
DN300
325
8
50
441
8
DN350
377
9
50
493
8
DN400
426
9
50
542
8
3
北京首钢设计院
4.2 130℃/80℃高温水采暖外线管道采用耐高温型预制直埋保温管, 耐高温型预制直埋保温管钢管采用无缝钢管,保温层第一层采用硅酸 钙,第二层采用聚氨酯,保温后的保护层(防腐层)采用高密度聚乙 烯保护层,各规格及厚度需满足下表:
40
50
264
4
DN80
89
3.5
40
50
277
4
DN100
108
4
40
50
296
4
DN125
133
4
40
50
323
5
DN150
159
4.5
40
50
359
5
DN200
219
6
40
50
415
8
DN250
273
8
40
50
469
8
DN300
325
8
60
50
565
10
DN350
377
9
60Hale Waihona Puke 5061710
DN400
426
9
60
50
666
10
DN450
480
9
60
50
724
12
5 热力专业 压缩空气同氧气、氮气专业做法。蒸汽管道不做防腐。
4
标称 管径
无缝钢管
外径
壁厚
(mm) (mm)
保温层厚度
高密度聚乙烯保护层(防腐)
硅酸钙
聚氨酯
外径
壁厚
(mm) (mm)
(mm)
(mm)
DN25
32
2.5
30
40
179
3.5
DN32
38
2.5
30
40
185
3.5
DN40
45
2.5
30
40
192
3.5
DN50
57
3.5
40
50
204
3.5
DN65
76
3.5
直埋热水采暖外线管道防腐要求,按温度不同:
2
北京首钢设计院
4.1 95℃/70℃热水采暖外线管道及空调外线管道采用预制直埋保温 管;保温后的保护层(防腐层)采用高密度聚乙烯保护层,各规格及 厚度需满足下表:
标称
无缝钢管
保温层厚度 高密度聚乙烯保护层(防腐)
管径
外径(mm) 壁厚(mm) 聚氨酯(mm) 外径(mm) 壁厚(mm)
北京首钢设计院
本规定给出区域埋地和架空管道外防腐具体做法,由于动力专业 管道类型较多,介质也各不相同,包括水、煤气、氧气、氮气、蒸汽 等,并且管道所处位置也各不相同,因此,具体分为车间内部架空和 车间外部架空及车间区域埋地管道。以下按照专业不同一一列出。 1 给排水专业
钢材表面清除油污,喷砂除锈等级应达到国家规定的 Sa21/2 级或 St3 级。钢管除锈后,按位置不同,方案不同,可按需要选择任一种 使用,但车间内、外部涂漆类型应保持一致。分别如下: 1.1 车间内部管道 1.1.1 明装管道先刷环氧富锌底漆两道,再刷环氧彩漆两道。共 160μm。 1.1.2 无机富锌底漆 1×50μm,中间 1×120μm,面漆 1×80μm,共计 250μm。 1.2 车间外部架空管道 1.2.1 水性无机富锌涂料+环氧玻璃鳞片+聚氨酯面漆,共 320μm。 1.2.2 无机富锌底漆 1×50μm,中间 1×120μm,面漆 1×80μm,共计 250μm。 1.2.3 环氧富锌底漆两道,再刷环氧彩漆两道,共 200μm。 1.3 车间内外部管廊
聚乙烯胶粘带防腐层技术标准》<SY/T0414-1998>,搭接宽度>25mm, 其等级采用加强级。 2 燃气专业
钢材表面清除油污,喷砂除锈等级应达到国家规定的 Sa21/2 级或 St3 级。钢管除锈后,按位置不同进行防腐。 2.1 车间内部管道
无机富锌底漆 2 道,干膜厚度 40,环氧云铁中间层漆 2 道,干膜 厚度 140,可复涂聚氨脂面漆 1 道,干膜厚度 50,共计 5 道,总干膜 厚度 230,寿命大于 10 年。 2.2 车间外部管道
无机富锌底漆 2 道,干膜厚度 40,环氧云铁中间层漆 2 道,干膜 厚度 140,可复涂聚氨脂面漆 2 道,干膜厚度 100,共计 6 道,总干膜 厚度 280,寿命大于 10 年。 3 氧气及氮气专业
管道、管件及支架的涂漆应按国家现行标准《钢结构、管道涂装 技术规程》(YB/T9256-1996)及本工程涂漆统一规定中的有关规定执 行,工业及海洋大气环境,涂料品种为环氧富锌底漆及氯化橡胶防腐 漆,涂层厚度为 210μm。 4 暖风专业
具体做法同车间内部管道。 1.4 车间区域埋地管道 1.4.1 采用无溶剂环氧煤沥青防腐涂料,埋地管道采用特加强级(详 见产品说明书),参照 SY/T0447-1996《埋地钢质管道环氧煤沥青防 腐层技术标准》验收。 1.4.2 钢管道外壁采用聚乙烯丁基胶粘带防腐,执行标准《钢质管道
1
北京首钢设计院
首钢京唐钢铁联合有限责任公司 管道外防腐统一技术规定
北京首钢设计院
2007 年 7 月
目录
北京首钢设计院
1 给排水专业……………………………………………………………1 2 燃气专业………………………………………………………………2 3 氧气及氮气专业………………………………………………………2 4 暖风专业………………………………………………………………2 5 热力专业………………………………………………………………4
DN25
32
2.5
40
119
3.5
DN32
38
2.5
40
125
3.5
DN40
45
2.5
40
132
3.5
DN50
57
3.5
50
164
3.5
DN65
76
3.5
50
184
4
DN80
89
3.5
50
197
4
DN100
108
4
50
216
4
DN125
133
4
50
243
5
DN150
159
4.5
50
269
5
DN200