精密超精密加工和特种加工方法
9精密加工与特种加工简介

9.1.2 精密加工和超精密加工的特点
1. 加工方法 目前精密和超精密加工方法根据加工机理可分为四大类: 切削加工:精密切削、微量切削和超精密切削等; 磨削加工:精密磨削、微量磨削和超精密磨削等; 特种加工:电火花加工、电解加工、激光加工、电子束加工、离子束加工等; 复合加工:将几种加工方法复合在一起,如机械化学研磨、超声磨削、电解抛光 等。 在精密和超精密加工中特种加工和复合加工方法应用得越来越多。 2. 加工原则 一般加工时,机床的精度总是高于这被加工零件的精度,这一规律被称为“蜕化” 原则。而对于精密加工和超精密加工时,有时可利用低于工件精度的设备、工具, 通过工艺手段和特殊的工艺装备,加工出精度高于“母机”的工作母机或工件。 这种方法称为进化加工。 3. 加工设备 加工设备的几何精度向亚微米级靠近。关键元件,如主轴、导轨、丝杆等广泛采 用液体静压或空气静压元件。 定位机构中采用电致伸缩、磁致伸缩等微位移结构。 设备广泛采用计算机控制、适应控制、在线检测与误差补偿等技术。
2. 电火花加工的工艺特点 (1) 电火花可加工任何硬、脆、韧、软和高熔点的导电材料,在一定条件下,还 可加工半导体材料和非导电材料。 (2) 加工时无切削力,有利于小孔、薄壁、空槽以及各种复杂截面的型孔、曲线 孔和型腔等零件的加工,也适于精密细微加工。 (3) 当脉冲宽度不大时,对整个工件而言,几乎不受热影响,可提高加工质量, 适于加工热敏感性强的材料。 (4) 脉冲参数可任意调节,能在同一台机床上连续进行粗、半精、精加工。精加 工时精度为0.005mm,表面粗糙度Ra值为1.6~0.8μm,尺寸精度;精微加工时精度可 达0.002mm~0.001mm,表面粗糙度Ra值为0.05~0.01μm。 (5) 直接使用电能加工,易于实现自动化。
精密和超精密加工技术

本章内容
I. 特种加工技术概述 II. 电火花加工 III.电解加工 IV. 高能束加工
特种加工技术概述
➢ 非传统加工又称特种加工,通常被理解为别于传统切 削与磨削加工方法的总称。
➢非传统加工方法 产生于二次大战后。两方面问题传统 机械加工方法难于解决:
1)难加工材料的加工问题。宇航工业等对材料高强度、 高硬度、高韧性、耐高温、耐高压、耐低温等的要求,使 新材料不断涌现。
电火花加工工作要素
➢脉冲宽度与间隔——影响加工速度、表面粗糙 度、电极消耗和表面组织等。脉冲频率高、持 续时间短,则每个脉冲去除金属量少,表面粗 糙度值小,但加工速度低。通常放电持续时间 在2μs至2ms范围内,各个脉冲的能量2mJ到20J (电流为400A时)之间。
电火花加工类型
➢电火花成形加工:主要指孔加工,型腔加工等 ➢电火花线切割
➢ 拓宽现有非传统加工方法的应用领域。
➢ 探索新的加工方法,研究和开发新的元器件。
➢ 优化工艺参数,完善现有的加工工艺。
➢ 向微型化、精密化发展。 ➢ 采用数控、自适应控 2084 制、CAD/CAM、专家系统
等 技 术 , 提 高 加 工 过 程1104
70年代 80年代 90年代
自动化、柔性化程度。
232
424 244 142
441 321 214
353 252 316
激光加工 电火花加工 超声加工 电化学加工 EI 收录文章数比较
几种代表性特种加 工方法
电火花加工的原理示意 图
电火花加工
原理:利用工具电极与工件电极之间脉冲性火花放电, 产生瞬时高温,工件材料被熔化和气化。同时,该处绝 缘液体也被局部加热,急速气化,体积发生膨胀,随之 产生很高的压力。在这种高压作用下,已经熔化、气化 的材料就从工件的表面迅速被除去
精密和超精密加工复习整理资料

精密和超精密加⼯复习整理资料1.精密和超精密加⼯⽬前包含的三个领域:超精密切削、精密和超精密磨削研磨和精密特种加⼯2.超精密加⼯中超稳定的加⼯环境条件主要指(恒温)、(恒湿)、(防振)和(超净)四个⽅⾯的条件。
3.电⽕花型腔加⼯的⼯艺⽅法有:(单电极平动法)、(多电极更换法)、(分解电极法)、简单电极数控创成法等。
4.超精密加⼯机床的总体布局形式主要有以下⼏种:(T形布局)、(⼗字形布局)、(R-θ布局)、(⽴式结构布局)等。
5.实现超精密加⼯的技术⽀撑条件主要包括:(超精密加⼯机理与⼯艺⽅法)、(超精密加⼯机床设备)、(超精密加⼯⼯具)、(精密测量和误差补偿)、⾼质量的⼯件材料、超稳定的加⼯环境条件等。
6.激光加⼯设备主要包括电源、(激光器)、(光学系统)、(机械系统)、控制系统、冷却系统等部分。
7.精密和超精密加⼯机床主轴轴承的常⽤形式有(液体静压轴承)和(空⽓静压轴承)。
8.⾦刚⽯晶体的激光定向原理是利⽤⾦刚⽯在不同结晶⽅向上(因晶体结构不同⽽对激光反射形成不同的衍射图像)进⾏的。
9.电⽕花加⼯蚀除⾦属材料的微观物理过程可分为(介质电离击穿)、(介质热分解、电极材料熔化、⽓化)、(蚀除物抛出)和(间隙介质消电离)四个阶段。
10.超精密加⼯机床的关键部件主要有:(精密主轴部件)、(导轨部件)和(进给驱动系统)等。
11.三束加⼯是指电⼦束、离⼦束和激光束。
12.所谓空⽓洁净度是指空⽓中含尘埃量多少的程度。
13.⼯业⽣产中常见的噪声主要有空⽓动⼒噪声、机械噪声和电磁噪声。
14.纳⽶级加⼯精度包含:纳⽶级尺⼨精度、纳⽶级⼏何形状精度、纳⽶级表⾯质量。
15.超精密切削时积屑瘤的⽣成规律:1)在低速切削时,h0值⽐较稳定;在中速时值不稳定。
2)在进给量f很⼩时,h0较⼤3)在背吃⼑量a p<25um时,h0变化不⼤;在a p>25um时,h0将随a p的值增⼤⽽增⼤。
16.超精密切削时积屑瘤对切削过程的影响:积屑瘤⾼时切削⼒⼤,积屑瘤⼩时切削⼒⼩。
04精密加工和特种加工

抛光特点:
①方法简便、经济,不用特殊设备;
②容易对曲面进行加工;
③只能提高粗糙度,不能改变零件的尺寸精度、形状精度或位置精度;
④劳动条件差。
抛光应用: 抛光主要用于零件表面的装饰加工,或者利用抛光方法去除前道工序的加工
痕迹,提高零件的疲劳强度。
抛光零件表面的形状可以是平面、外圆、孔、以及各种成形表面等。 五、各种精密加工方法的比较:
用装有细磨粒、低硬度的油石磨头,在一定压力下 对工件表面进行光整加工的方法称为超级光磨 。
• 加工时工件旋转,油石以恒力轻压于工件表面, 在作轴向进给的同时作轴向微小振动,从而达到 对工件微观不平的表面进行光磨的效果。
超级光磨的特点 : ①加工余量极少,一般为3 ~ 10μm; ②生产率较高,一般加工时间只需30~60秒; ③表面质量好,Ra<0.012μm; ④设备简单,操作方便。 但是,超级光磨只能提高表面质量,不能提高尺寸精度和形位精度。
第二节 特种加工
特种加工是相对于传统的切削加工而言,传统的切削加工是用刀具靠机械 能去除工件表面的多余材料。当工件材料的强度、硬度、脆性、韧性过高, 或零件的结构过于复杂,或尺寸太小,或零件的刚度较差时,传统的切削加 工方法就难于实现。特种加工就是为解决这些难题而发展起来的一种新的加 工方法.
特种加工是直接利用电能、光能、声能、热能、化学能或多种能量复合形 式进行加工的方法。常用的特种加工有电火花加工、电解加工、超声波加工、 激光加工、电子束加工和离子束加工等。
精度为3~O.3 μm,粗糙度为O.3~O·03μm的叫精密加工;
精度为0.3~0.03 μm,粗糙度为0.03~0.005 μm的叫超精密加工,或亚微米 加工;
精度为0.03 μm(30纳米),粗糙度优于0.005 μm以上的则称为纳米(nm)加工。
精密加工和特种加工简介
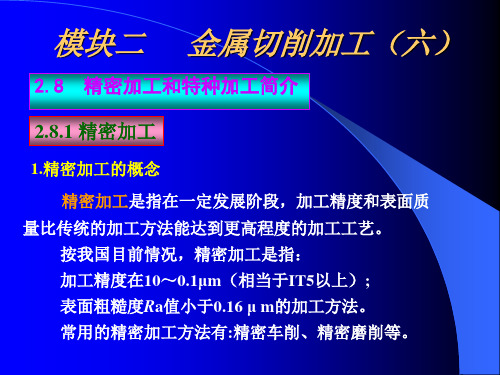
二. 相关知识
(一)精密加工 1、概述
精密加工中,精度高于0.1μm ,表面粗糙度Ra 值小于0.1μm的加工方法称为超精密加工。 常用的超精密加工方法有镜面车削、虹面车削, 超精密磨削、镜面磨削等。
(1)机床设备条件
精密加工必须在精密机床上进行。机床应具有 高的运动精度、刚度和转速,以及小的进给量。
用硬质合金精密车刀进行精密车削时,一般采用高 的切削速度:车铝合金材料vcmax=350m/min,车青铜等 铜合金材料vcmax=400m/min;车镁合金材料vcmax = 1000m/min。切削速度越高,获得的表面粗糙度值越小,
但刀具磨损及振动也随之加剧,所以应根据实际情况来
合理选择。一般取进给量ƒ=0.02~0.04 mm/r;背吃刀 量一般取aP =0· 2~0.3 mm。
(二) 特种加工 1.概述
(1)特种加工 特种加工是指除常规切削加工以 外的新的加工方法,这种加工方法利用电、磁、 声、光、化学等能量或其各种组合作用在工件的 被加工部位上,实现对材料的去除、变形、改变 性能和镀覆,从而达到加工目的。
(2)特种加工特点
1)不是主要依靠机械能,而是主要用其他能量(如 电、热、光、化学、声等)去除金属材料,这些能量的瞬 时能量密度很高,所以可加工任何高硬度的材料。 2)工具硬度可以低于被加工材料的硬度。 3)加工过程中,因工具与工件基本不接触,加工时 不存在显著的机械切削力。 4)加工机理不同于一般金属切削原理,不产生宏观切
超精加工的磨具为油石,选用细粒度, 以较低的压力和切削速度对工件表面进行 加工,加工时有三种运动,即工件的低速 回转、磨具的轴向进给运动和油石的高速 往复振动。油石振动的频率为10~25 Hz, 振幅为1~5mm,油石对工件表面的压力 Pa=15×104 Pa。
江苏自考02213 精密加工与特种加工

2213 精密加工与特种加工第一章概论 P1领会: 精密与特种加工技术基本概念,对材料可加工性和结构工艺性等的影响1.精密与特种加工技术基本概念精密加工含:微细加工、光整加工、精整加工特种加工(NTM):利用机、光、电、声、热、化学、磁、原子能的能源进行加工的非传统加工方法。
2.精密与特种加工对材料可加工性和结构工艺性的影响1)提高了材料的可加工性2)改变了零件的典型工艺路线3)大大缩短新产品试制周期4)对零件结构的设计产生很大的影响5)对传统的结构工艺性好与坏的衡量标准产生重要影响掌握: 精密与特种加工技术分类、应用特点1.按加工成形原理特点分类:1)去除加工(从工件上去除多余材料),分散流;2)结合加工(利用理化方法将不同材料结合在一起,分为附着<电镀、气相沉积>、注入<表面渗碳、离子注入>、连接 <焊接、粘接>),汇合流;3)变形加工——流动加工(利用力、热、分子运动等手段使工件产生变形改变其尺寸、形状、性能<锻造、锻造,液晶定向>),直通流。
2.按加工方法机理分类:传统加工(使用刀具进行切削加工)、非传统加工(利用机、电、声、热、化学、磁、原子能等能源进行加工)、复合加工(采用多种加工方法)3.技术特点:1)不主要依靠机械能,而主要依靠其他能量去除工件材料2)工具的硬度可低于被加工工件材料的硬度,有些不需要工具;3)加工过程中,工具与工件之间没有显著的机械切削力,适合精密加工低刚度零件;4.特种加工技术的应用:1)难切削材料的加工;2)特殊复杂型面的加工;3)各种超精密、光整零件的加工;4)特殊要求零件的加工。
可以加工任何硬度、强度、韧性、脆性的金属、非金属、复合材料,适合于加工复杂、微细表面、低刚度的零件,有些还进行超精密加工、镜面加工、光整加工及纳米级加工。
第二章金刚石刀具精密切削加工 P11领会:精密切削加工方法、种类及其实现条件,超精密机床组成及其关键部件1.超精密加工方法1)按加工方式分为:切削加工、磨料加工<固结磨料、游离磨料>、特种加工、复合加工;2)按机理分类:去除加工、结合加工、变形加工,还可分为传统加工(指利用刀具切削加工、固结磨料和游离磨料加工)、非传统加工(指利用电、磁、声、光、化学、核等能量对材料进行加工处理)、复合加工(多种加工方法结合),目前以切削、磨削、研磨的传统方法占主导。
2.3精密和超精密加工技术
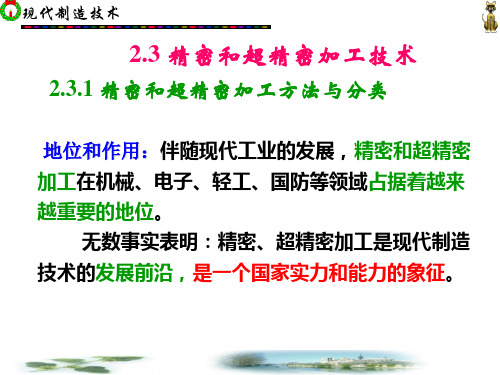
现代制造技术
2. 非机械超精密加工技术——特种精密加工方法
包括精密电火花加工、精密电解加工、精密超声加工、
电子束加工、离子束加工、激光束加工等一些非传统加工方 法;
3. 复合超精密加工方法
传统加工方法的复合 特种加工方法的复合 传统加工方法和特种加工方法的复合
(例如机械化学抛光、精密电解磨削、精密超声珩磨等)。
1~0.1 0.1~ 0.001 0.1~ 0.01 1~0.1 1~0.1 5 5 1~0.1
0.025~ 0.008 0.025~ 0.008 0.025~ 0.008 0.01 0.01 0.01 0.01~ 0.02 0.01~ 0.008
黑色金属、铝合金 黑色金属、非金属 材料 黑色金属、非金属 材料、有色金属 黑色金属、非金属 材料 黑色金属、非金 属材料、有色金属 黑色金属等 黑色金属等 黑色金属、非金属 材料、有色金属
发展:超精密磨削应用比较成熟的首推金刚石微粉砂轮 超精密磨削。
现代制造技术 1)金刚石微粉砂轮 采用粒度为F240~F1000的金刚石微粉作为磨料,树脂、 陶瓷、金属为结合剂烧结而成;也可采用电铸法和气相沉积 法制作。 用筛选法分级,粒度号以磨粒通过的筛网上每英寸长度 内的孔眼数来表示。如60 # 的磨粒表示其大小刚好能通过每 英寸长度上有60孔眼的筛网。对于颗粒尺寸小于40 μ m的磨 料,称为微粉。 • 用显微测量法分级,用W和后面的数字表示粒度号,其W后 的数值代表微粉的实际尺寸。如W20表示微粉的实际尺寸为 20 μ m
• 精密加工是指加工精度达到1~0.1μm,表面粗
糙度Ra在0.1~0.01μm的加工工艺。
• 超精加工则是指加工尺寸精度高于0.1μm,表 面粗糙度Ra小于0.025μm的精密加工方法。
精密加工和特种加工

薄膜作为成形材料。 69. SLS(选择性激光粉末烧结成形)工艺是利用粉末材料(金属粉末或非金属粉末)在激 光照射下烧结的原理,在计算机控制下逐层堆积成形。 70. SL(液相光敏树脂固化成形)工艺的成形材料称为光固化树脂(或称光敏树脂) 。 71. 磨料硬度愈高,加工速度愈快;磨料粒度愈粗,加工速度愈快,但精度和表面粗糙度则 变差。 72. 超声加工时并不是整个变幅杆和工具都是在作上下高频振动,它和低频或工频振动的概 念完全不一样;超声波在金属棒杆内主要以纵波形式传播。 73. 为了使弹性杆处于最大振幅共振状态,应将弹性杆设计成半波长的整数倍;而固定弹性 杆的支持点,应该选在振动过程中的波节处,这一点不振动。 74. 当频率超过 16000Hz 超出一般人耳听觉范围,就称为超声波。 75. 离子刻蚀是从工件上去除材料,是一个撞击溅射过程。 76. 目前用于改变零件尺寸和表面物理力学性能的离子束加工有:用于从工件上去除加工的 离子刻蚀加工; 用于给工件表面涂覆的离子镀膜加工; 用于表面改性的离子注入加工等。 77. 离子束加工是所有特种加工方法中最精密、 最微细的加工方法, 是当代纳米加工的基础。 78. 离子束加工的原理:粒子束加工的原理和电子束加工基本类似,也是在真空条件下,将 离子源产生的离子束经过加速聚焦,使之撞击到工件表面。不同的是离子带正电荷,其 质量比电子大数千、数万倍,如氩离子的质量是电子的 7.2 万倍,所以一旦离子加速到 较高速度时离子束比电子束具有更大的撞击功能,它是靠微观的机械撞击能量,而不是 靠动能转化为热能来加工的。 79. 电子束加工按其功率密度和能量注入时间的不同,可用于高速打孔、加工型孔及特殊表 面、刻蚀、焊接、热处理、电子束光刻。 80. 电子束加工的基本组成:电子枪、真空系统、控制系统和电源等部分组成。 81. 电子束加工是在真空条件下。 82. 一般激光的实际焦点在工作的表面或略微低于工件表面为宜。 83. 利用激光几乎可在任何材料上打微型小孔。 84. 激光加工机的组成部分:激光器、激光器电源、光学系统、机械系统。 85. 光既有波动性,又有微粒性,即光具有波粒二象性。 86. 电解加工工艺:深孔扩孔加工,型孔加工,型腔加工,套料加工。 87. 电解液的净化方法很多,用得比较广泛的是自然沉淀法;介质过滤法也是常用的方法之 一。 88. 点解加工的基本设备包括直流电源,机床及电解液系统三大部分。 89. 电解液可分为中性盐溶液,酸性溶液与碱性溶液。最常用的有 NaCL、NaNO3、 NaClO3 三种电解液。 90. 电解加工的主要缺点和局限性: (1) 不易达到较高的加工精度和加工稳定性; (2) 电极工具的设计和修正比较麻烦,因而很难适用于单件生产;(3)点解加工的附属设 备较多,占地面积大,机床要有足够的刚性和防腐性能,造价较高;(4)点解产物需 要进行妥善的处理,否则将污染环境。 91. 电解加工与其他加工方法相比较,具有下述特点:(1)加工范围广;(2)点解 加工的生产率较高; (3)可以达到较好的表面粗糙度; (4)不会引起残余应力和变形, 没有飞边毛刺;(5)点解加工过程中阴极工具在理论上不会耗损,可长期使用。 92.电解加工是利用金属在电解液中的电化学阳极溶解,将工件加工成形的。 93.电化学加工的分类:第一类是利用电化学阳极溶解来进行加工;第二类是利用电化学阴