美国海岸工程手册Part_I-Chap_1
MEPC.190(60)

附件11第MEPC.190(60)号决议2010年3月26日通过《〈1973年国际防止船舶造成污染公约〉1978年议定书》附则修正案(北美排放控制区)海上环境保护委员会,忆及《国际海事组织公约》关于防止和控制海洋污染的国际公约赋予海上环境保护委员会(本委员会)职责的第三十八条第(一)款,注意到《1973年国际防止船舶造成污染公约》(在下文称“1973年公约”)第16条、《〈1973年国际防止船舶造成污染公约〉的1978年议定书》(在下文称“1978年议定书”)第VI条和《〈1973年国际防止船舶造成污染公约〉的1997年议定书》(在下文称“1997年议定书”) 第4条共同规定了1997年议定书的修正程序,并赋予本组织适当机构审议和通过经1978和1997年议定书修订的1973年公约的修正案的职能,还注意到通过1997年议定书,为《1973年公约》增加了题为《防止船舶造成大气污染规则》的附则VI (在下文称“附则VI”),进一步注意到以第MEPC.176(58)号决议通过了经修订的附则VI,而且随着其在2010年1月1日视为被接受后,将于2010年7月1日生效,审议了所建议的《73/78年防污公约》附则VI的修正案草案,1. 按照《1973年公约》第16(2)(d)条,通过了《73/78年防污公约》附则VI的修正案,案文列于本决议的附件;2. 按照《1973年公约》第16(2)(f)(iii)条,决定该修正案须在2011年2月1日视为已被接受,除非在此日期前,有不少于三分之一的当事国或其合计商船队总吨位不少于世界商船队总吨位50%的当事国通知本组织其反对该修正案;3. 请当事国注意,按照《1973年公约》第16(2)(g)(ii)条,所述修正案在按照上文第2段被接受后,将于2011年8月1日生效;4. 要求秘书长遵照《1973年公约》第16(2)(e)条,将本决议和附件中所载的修正案的核正无误副本送发《73/78年防污公约》的所有当事国;并5. 进一步要求秘书长将本决议及其附件的副本送发非《73/78年防污公约》当事国的本组织会员国。
美国军方工程部水利结构强度设计手册

EM1110-2-210430June1992 US Army Corpsof EngineersENGINEERING AND DESIGNStrength Designfor Reinforced-ConcreteHydraulic StructuresDEPARTMENT OF THE ARMY EM1110-2-2104US Army Corps of EngineersCECW-ED Washington,DC20314-1000Engineer ManualNo.1110-2-210430June1992Engineering and DesignSTRENGTH DESIGN FORREINFORCED-CONCRETE HYDRAULIC STRUCTURES1.Purpose.This manual provides guidance for designing reinforced concrete hydraulic structures by the strength-design method.Plain concrete and prestressed concrete are not covered in this manual.2.Applicability.This manual applies to all HQUSACE/OCE elements,major subordinate commands,districts,laboratories,and field operating activities having civil works responsibilities.FOR THE COMMANDER:Colonel,Corps of EngineersChief of Staff______________________________________________________________________________ This manual supersedes ETL1110-2-312,Strength Design Criteria for Reinforced Concrete Hydraulic Structures,dated10March1988and EM1110-2-2103,Details of Reinforcement-Hydraulic Structures,dated21May1971.EM1110-2-210430Jun92CHAPTER1INTRODUCTION1-1.PurposeThis manual provides guidance for designing reinforced-concrete hydraulic structures by the strength-design method.1-2.ApplicabilityThis manual applies to all HQUSACE/OCE elements,major subordinate commands, districts,laboratories,and field operating activities having civil works responsibilities.1-3.Referencesa.EM1110-1-2101,Working Stresses for Structural Design.b.EM1110-2-2902,Conduits,Culverts,and Pipes.c.CW-03210,Civil Works Construction Guide Specification for Steel Bars,Welded Wire Fabric,and Accessories for Concrete Reinforcement.d.American Concrete Institute,"Building Code Requirements and Commentary for Reinforced Concrete,"ACI318,Box19150,Redford Station, Detroit,MI48219.e.American Concrete Institute,"Environmental Engineering Concrete Structures,"ACI350R,Box19150,Redford Station,Detroit,MI48219.f.American Society for Testing and Materials,"Standard Specification for Deformed and Plain Billet-Steel Bars for Concrete Reinforcement,"ASTMA615-89,1916Race St.,Philadelphia,PA19103.g.American Welding Society,"Structural Welding Code-Reinforcing Steel,"AWS D1.4-790,550NW Le Jeune Rd.,P.O.Box351040,Miami,FL33135.h.Liu,Tony C.1980(Jul)."Strength Design of Reinforced Concrete Hydraulic Structures,Report1:Preliminary Strength Design Criteria," Technical Report SL-80-4,US Army Engineer Waterways Experiment Station,3909Halls Ferry Road,Vicksburg,MS39180.i.Liu,Tony C.,and Gleason,Scott.1981(Sep)."Strength Design of Reinforced Concrete Hydraulic Structures,Report2:Design Aids for Use inthe Design and Analysis of Reinforced Concrete Hydraulic Structural Members Subjected to Combined Flexural and Axial Loads,"Technical Report SL-80-4,US Army Engineer Waterways Experiment Station,3909Halls Ferry Road, Vicksburg,MS39180.EM1110-2-210430Jun92j.Liu,Tony C.1981(Sep)."Strength Design of Reinforced Concrete Hydraulic Structures,Report3:T-Wall Design,"Technical Report SL-80-4,US Army Engineer Waterways Experiment Station,3909Halls Ferry Road, Vicksburg,MS39180.1-4.Backgrounda.A reinforced concrete hydraulic structure is one that will be subjected to one or more of the following:submergence,wave action,spray, chemically contaminated atmosphere,and severe climatic conditions.Typical hydraulic structures are stilling-basin slabs and walls,concrete-lined channels,portions of powerhouses,spillway piers,spray walls and training walls,floodwalls,intake and outlet structures below maximum high water and wave action,lock walls,guide and guard walls,and retaining walls subject to contact with water.b.In general,existing reinforced-concrete hydraulic structures designed by the Corps,using the working stress method of EM1110-1-2101,have held up extremely well.The Corps began using strength design methods in1981 (Liu1980,1981and Liu and Gleason1981)to stay in step with industry, universities,and other engineering organizations.ETL1110-2-265,"Strength Design Criteria for Reinforced Concrete Hydraulic Structures,"dated15September1981,was the first document providing guidance issued by the Corps concerning the use of strength design methods for hydraulic structures. The labor-intensive requirements of this ETL regarding the application of multiple load factors,as well as the fact that some load-factor combination conditions resulted in a less conservative design than if working stress methods were used,resulted in the development of ETL1110-2-312,"Strength Design Criteria for Reinforced Concrete Hydraulic Structures,"dated10March 1988.c.The revised load factors in ETL1110-2-312were intended to ensure that the resulting design was as conservative as if working stress methods were used.Also,the single load factor concept was introduced.The guidance in this ETL differed from ACI318Building Code Requirements and Commentaryfor Reinforced Concrete primarily in the load factors,the concrete stress-strain relationship,and the yield strength of Grade60reinforcement.ETL1110-2-312guidance was intended to result in designs equivalent to those resulting when working stress methods were used.d.Earlier Corps strength design methods deviated from ACI guidance because ACI318includes no provisions for the serviceability needs ofhydraulic structures.Strength and stability are required,but serviceability in terms of deflections,cracking,and durability demand equal consideration. The importance of the Corps’hydraulic structures has caused the Corps to move cautiously,but deliberately,toward exclusive use of strength design methods.e.This manual modifies and expands the guidance in ETL1110-2-312with an approach similar to that of ACI350R-89.The concrete stress-strain relationship and the yield strength of Grade60reinforcement given in ACI318 are adopted.Also,the load factors bear a closer resemblance to ACI318andare modified by a hydraulic factor,H,to account for the serviceabilityfneeds of hydraulic structures.f.As in ETL1110-2-312,this manual allows the use of a single load factor for both dead and live loads.In addition,the single load factor method is required when the loads on the structural component includereactions from a soil-structure stability analysis.1-5.General RequirementsReinforced-concrete hydraulic structures should be designed with the strength design method in accordance with the current ACI318,except as hereinafter specified.The notations used are the same as those used in the ACI318Code and Commentary,except those defined herein.1-6.Scopea.This manual is written in sufficient detail to not only provide the designer with design procedures,but to also provide examples of their application.Also,derivations of the combined flexural and axial load equations are given to increase the designer’s confidence and understanding.b.General detailing requirements are presented in Chapter 2.Chapter3presents strength and serviceability requirements,including load factors and limits on flexural reinforcement.Design equations for members subjected to flexural and/or axial loads(including biaxial bending)are given in Chapter 4.Chapter5presents guidance for design for shear,including provisions for curved members and special straight members.The appendices include notation,equation derivations,and examples.The examples demonstrate:load-factor application,design of members subjected to combined flexural and axial loads,design for shear,development of an interaction diagram,and design of members subjected to biaxial bending.puter ProgramsCopies of computer programs,with documentation,for the analysis and designof reinforced-concrete hydraulic structures are available and may be obtained from the Engineering Computer Programs Library,US Army Engineer Waterways Experiment Station,3909Halls Ferry Road,Vicksburg,Mississippi39180-6199. For design to account for combined flexural and axial loads,any procedurethat is consistent with ACI318guidance is acceptable,as long as the load factor and reinforcement percentage guidance given in this manual is followed. 1-8.RecissionCorps library computer program CSTR(X0066),based on ETL1110-2-312,is replaced by computer program CASTR(X0067).Program CASTR is based on this new engineer manual.CHAPTER2DETAILS OF REINFORCEMENT2-1.GeneralThis chapter presents guidance for furnishing and placing steel reinforcement in various concrete members of hydraulic structures.2-2.QualityThe type and grade of reinforcing steel should be limited to ASTM A615(Billet Steel),Grade60.Grade40reinforcement should be avoided since its availability is limited and designs based on Grade40reinforcement,utilizing the procedures contained herein,would be overly conservative.Reinforcement of other grades and types permitted by ACI318may be permitted for special applications subject to the approval of higher authority.2-3.Anchorage,Bar Development,and SplicesThe anchorage,bar development,and splice requirements should conform toACI318and to the requirements presented below.Since the development length is dependent on a number of factors such as concrete strength and barposition,function,size,type,spacing,and cover,the designer must indicate the length of embedment required for bar development on the contract drawings. For similar reasons,the drawings should show the splice lengths and special requirements such as staggering of splices,etc.The constructionspecifications should be carefully edited to assure that they agree with reinforcement details shown on the drawings.2-4.Hooks and BendsHooks and bends should be in accordance with ACI318.2-5.Bar Spacinga.Minimum.The clear distance between parallel bars should not beless than1-1/2times the nominal diameter of the bars nor less than1-1/2times the maximum size of coarse aggregate.No.14and No.18bars should not be spaced closer than6and8inches,respectively,center to center.When parallel reinforcement is placed in two or more layers,theclear distance between layers should not be less than6inches.In horizontal layers,the bars in the upper layers should be placed directly over the barsin the lower layers.In vertical layers,a similar orientation should be used.In construction of massive reinforced concrete structures,bars in a layer should be spaced12inches center-to-center wherever possible tofacilitate construction.b.Maximum.The maximum center-to-center spacing of both primary and secondary reinforcement should not exceed18inches.EM1110-2-210430Apr922-6.Concrete Protection for ReinforcementThe minimum cover for reinforcement should conform to the dimensions shown below for the various concrete sections.The dimensions indicate the clear distance from the edge of the reinforcement to the surface of the concrete.MINIMUM CLEAR COVER OF CONCRETE SECTION REINFORCEMENT,INCHESUnformed surfaces in contact with foundation4Formed or screeded surfaces subject to cavitation orabrasion erosion,such as baffle blocks and stillingbasin slabs6Formed and screeded surfaces such as stilling basinwalls,chute spillway slabs,and channel liningslabs on grade:Equal to or greater than24inches in thickness4Greater than12inches and less than24inchesin thickness3Equal to or less than12inches in thicknesswill be in accordance with ACI Code318.NOTE.In no case shall the cover be less than:1.5times the nominal maximum size of aggregate,or2.5times the maximum diameter of reinforcement.2-7.Splicinga.General.Bars shall be spliced only as required and splices shall be indicated on contract drawings.Splices at points of maximum tensilestress should be avoided.Where such splices must be made they should be staggered.Splices may be made by lapping of bars or butt splicing.pped Splices.Bars larger than No.11shall not be lap-spliced. Tension splices should be staggered longitudinally so that no more than halfof the bars are lap-spliced at any section within the required lap length.If staggering of splices is impractical,applicable provisions of ACI318should be followed.c.Butt Splices(1)General.Bars larger than No.11shall be butt-spliced.BarsNo.11or smaller should not be butt-spliced unless clearly justified bydesign details or economics.Due to the high costs associated with butt splicing of bars larger than No.11,especially No.18bars,carefulEM1110-2-210430Apr92consideration should be given to alternative designs utilizing smaller bars. Butt splices should be made by either the thermit welding process or an approved mechanical butt-splicing method in accordance with the provisions contained in the following paragraphs.Normally,arc-welded splices shouldnot be permitted due to the inherent uncertainties associated with welding reinforcement.However,if arc welding is necessary,it should be done in accordance with AWS D1.4,Structural Welding Code-Reinforcing Steel.Butt splices should develop in tension at least125percent of the specified yield ,of the bar.Tension splices should be staggered longitudinally strength,fyat least5feet for bars larger than No.11and a distance equal to the required lap length for No.11bars or smaller so that no more than half ofthe bars are spliced at any section.Tension splices of bars smaller than No.14should be staggered longitudinally a distance equal to the required lap length.Bars Nos.14and18shall be staggered longitudinally,a minimum of5feet so that no more than half of the bars are spliced at any one section.(2)Thermit Welding.Thermit welding should be restricted to bars conforming to ASTM A615(billet steel)with a sulfur content not exceeding0.05percent based on ladle analysis.The thermit welding process should bein accordance with the provisions of Guide Specification CW-03210.(3)Mechanical Butt Splicing.Mechanical butt splicing shall be made by an approved exothermic,threaded coupling,swaged sleeve,or other positive connecting type in accordance with the provisions of Guide SpecificationCW-03210.The designer should be aware of the potential for slippage in mechanical splices and insist that the testing provisions contained in this guide specification be included in the contract documents and utilized in the construction work.2-8.Temperature and Shrinkage Reinforcementa.In the design of structural members for temperature and shrinkage stresses,the area of reinforcement should be0.0028times the gross cross-sectional area,half in each face,with a maximum area equivalent toNo.9bars at12inches in each face.Generally,temperature and shrinkage reinforcement for thin sections will be no less than No.4bars at12inchesin each face.b.Experience and/or analyses may indicate the need for an amount of reinforcement greater than indicated in paragraph2-8a if the reinforcement is to be used for distribution of stresses as well as for temperature and shrinkage.c.In general,additional reinforcement for temperature and shrinkage will not be needed in the direction and plane of the primary tensile reinforcement when restraint is accounted for in the analyses.However,the primary reinforcement should not be less than that required for shrinkage and temperature as determined above.2-3EM 1110-2-2104Change 120 Aug 033-3. Required Strengtha. General. Reinforced concrete hydraulic structures and hydraulic structural members shall be designed to have a required strength, , to resist dead and live loads in accordance with the following provisions. The hydraulic factor is to be applied in the determination of required nominal strength for all combinations of axial load, moments and shear (diagonal tension). In particular, the shear reinforcement should be designed for the excess shear, the difference between the hydraulic factored ultimate shear force, , and the shear strength provided by the concrete, , where h U the uh V c V φφ is the concrete resistance factor for shear design. Therefore, the design shear for the reinforcement, , is given bys V ⎟⎟⎠⎞⎜⎜⎝⎛−≥φφc uh s V V V 3.1 (3.1)b. Single Load Factor Method. In the single load factor method, both the dead and live loads are multiplied by the same load factor.()L D U +=7.1 (3.2)whereU = factored loads for a nonhydraulic structureD = internal forces and moments from dead loadsL = internal forces and moments from live loads()[]L D H U f h +=7.1 (3.3)where= factored loads for a hydraulic structure h U = hydraulic factor.f HFor hydraulic structures the basic load factor, 1.7, is multiplied by a hydraulic factor, , f H where , except for members in direct tension. For members in direct tension, = 1.65. Other values may be used subject to consultation with and approval from CECW-ED. 3.1=f H f HAn exception to the above occurs when resistance to the effects of unusual or extreme loads such as wind, earthquake or other forces of short duration and low probability of occurrence are included in the design. For those cases, one of the following loading combinations should be used:3-2EM 1110-2-210430Jun 92CHAPTER 4FLEXURAL AND AXIAL LOADS4-1.Design Assumptions and General Requirementsa.The assumed maximum usable strain εc at the extreme concretecompression fiber should be equal to 0.003in accordance with ACI 318.b.Balanced conditions for hydraulic structures exist at a crosssection when the tension reinforcement ρb reaches the strain corresponding to its specified yield strength f y just as the concrete in compression reaches its design strain εc .c.Concrete stress of 0.85f ′c should be assumed uniformly distributedover an equivalent compression zone bounded by edges of the cross section and a straight line located parallel to the neutral axis at a distance a =β1c from the fiber of maximum compressive strain.d.Factor β1should be taken as specified in ACI 318.e.The eccentricity ratio e ′/d should be defined as (4-11)*e ′d M u /P u dh /2d where e ′=eccentricity of axial load measured from the centroid of thetension reinforcement4-2.Flexural and Compressive Capacity -Tension Reinforcement Onlya.The design axial load strength φP n at the centroid of compressionmembers should not be taken greater than the following:(4-12)φP n (max)0.8φ0.85f ′c (A g ρbd )f y ρbd b.The strength of a cross section is controlled by compression if the load has an eccentricity ratio e ′/d no greater than that given by Equation 4-3and by tension if e ′/d exceeds this value.______________________________________________________________________________*P u is considered positive for compression and negative for tension.EM 1110-2-210430Jun 92(4-13)e ′b d 2k b k 2b 2k b ρf y0.425f ′c where(4-14)k b βE εE s εc f yc.Sections controlled by tension should be designed so(4-15)φP n φ0.85f ′c k u ρf y bd and(4-16)φM n φ0.85f ′c k u ρf ye′d 1bd 2where k u should be determined from the following equation:(4-17)k u1d.Sections controlled by compression should be designed so(4-18)φP n φ0.85f ′c k u ρf s bdand(4-19)φM n φf′c k u ρf s e ′d 1bd 2EM 1110-2-210430Jun 92where(4-20)f su ≥f y and k u should be determined from the following equation by direct or iterative method:(4-21)k 3u 1k 2u E s εc ρe ′0.425f ′c d k uβ1E s εc ρe ′0.425f ′c d 0e.The balanced load and moment can be computed using eitherEquations 4-5and 4-6or Equations 4-8and 4-9with k u =k b ande ′b e ′d =d.The values of e ′b /d and k b are given by Equations 4-3and 4-4,respectively.4-3.Flexural and Compressive Capacity -Tension and Compression Reinforcementa.The design axial load strength φP n of compression members should not be taken greater than the following:(4-22)φP n (max)0.8φ0.85f ′c A g ρρ′bd f y ρρ′bdb.The strength of a cross section is controlled by compression if the load has an eccentricity ratio e ′/d no greater than that given by Equation 4-13and by tension if e ′/d exceeds this value.(4-23)e′b d 2k bk 2bc 2k b ρf y 0.425f ′c ρ′f ′s 0.425f ′c The value k b is given in Equation 4-4and f ′s is given in Equation 4-16with k u =k b .c.Sections controlled by tension should be designed soEM 1110-2-210430Jun 92(4-24)φP n φ0.85f ′c k u ρ′f ′s ρf y bd and(4-25)φM n φf ′c k u ρ′f ′s ρf ye ′d 1bd 2where(4-26)f ′sE s εy ≤f y and k u should be determined from the following equation by direct or iterative methods:(4-27)k 3u 1β1k 2u f y 0.425f ′c ρd ′d 1ρe ′d 2β11k u f y β10.425f ′cd ′d 1ρe ′d 0d.Sections controlled by compression should be designed so(4-28)φP n φ0.85f ′c k u ρ′f ′s ρf s bdEM 1110-2-210430Jun 92and(4-29)φM nφ0.85f ′c k uρ′f ′s ρf se ′d1bd 2where(4-30)fsu≥f yand(4-31)f ′su≤fyand k u should bedetermined from the following equation by direct or iterative methods:(4-32)k 3u 21k 2u E sεc0.425f ′cρρ′ρ′1k uβ1E sεc 0.425f ′cρd ′d1Design for flexure utilizing compression reinforcement is discouraged.However,if compression reinforcement is used in members controlled bycompression,lateral reinforcement shall be provided in accordance with the ACI Building Code.e.The balanced load and moment should be computed usinge ′b Equations 4-14,4-15,4-16,and 4-17with k u =k b and e ′d =.The values of e ′b /d and k b are given by Equations 4-13and 4-4,respectively.4-4.Flexural and Tensile Capacity a.The design axial strength φP n of tensile members should not be takengreater than the following:EM 1110-2-210430Jun 92(4-33)φP n (max)0.8φρρ′f y bdb.Tensile reinforcement should be provided in both faces of the memberif the load has an eccentricity ratio e ′/d in the following range:1≥e ′d≥0The section should be designed so(4-24)φP nφρf yρ′f ′s bdand(4-25)φM nφρf yρ′f ′s1e ′d bd 2with(4-26)f ′s f≥f yand k u should be determined from the following equation:(4-27)k uc.Sections subjected to a tensile load with an eccentricity ratioe ′/d <0should be designed using Equations 4-5and 4-6.The value of k u is(4-28)k u1d.Sections subject to a tensile load with an eccentricity ratioe ′/d <0should be designed using Equations 4-14,4-15,4-16,and 4-17if A ′s >0and c >d ′.4-5.Biaxial Bending and Axial Loada.Provisions of paragraph 4-5shall apply to reinforced concrete members subjected to biaxial bending.b.For a given nominal axial load P n =P u /φ,the followingnondimensional equation shall be satisfied:(4-29)(M nx /M ox )K(M ny /M oy )K ≤1.0whereM nx ,M ny =nominal biaxial bending moments with respect to the x and yaxes,respectively M ox ,M oy =uniaxial nominal bending strength at P n about the x and yaxes,respectivelyK = 1.5for rectangular members= 1.75for square or circular members= 1.0for any member subjected to axial tensionc.M ox and M oy shall be determined in accordance with paragraphs 4-1through 4-3.CHAPTER 5SHEAR5-1.Shear StrengthThe shear strength V c provided by concrete shall be computed in accordance with ACI 318except in the cases described in paragraphs 5-2and 5-3.5-2.Shear Strength for Special Straight MembersThe provisions of this paragraph shall apply only to straight members of box culvert sections or similar structures that satisfy the requirements of 5-2.a and 5-2.b.The stiffening effects of wide supports and haunches shall beincluded in determining moments,shears,and member properties.The ultimate shear strength of the member is considered to be the load capacity that causes formation of the first inclined crack.a.Members that are subjected to uniformly (or approximately uniformly)distributed loads that result in internal shear,flexure,and axial compression (but not axial tension).b.Members having all of the following properties and constructiondetails.(1)Rectangular cross-sectional shapes.(2)/d between 1.25and 9,wherenis the clear span.(3)f ′c not more than 6,000psi.(4)Rigid,continuous joints or corner connections.(5)Straight,full-length reinforcement.Flexural reinforcement shallnot be terminated even though it is no longer a theoretical requirement.(6)Extension of the exterior face reinforcement around corners suchthat a vertical lap splice occurs in a region of compression stress.(7)Extension of the interior face reinforcement into and through thesupports.c.The shear strength provided the concrete shall be computed as(5-1)V c11.5ndbdEM 1110-2-210430Apr 92at a distance of from the face of the support.d.The shear strength provided by the concrete shall not be takengreater than(5-2)V c212n d bd __and shall not exceed 10f ′c bd.5-3.Shear Strength for Curved MembersAt points of maximum shear,for uniformly loaded curved cast-in-place memberswith R/d > 2.25where R is the radius curvature to the centerline of the member:(5-3)V cbd __The shear strength shall not exceed 10f ′c bd.5-4.Empirical ApproachShear strength based on the results of detailed laboratory or field testsconducted in consultation with and approved by CECW-ED shall be considered a valid extension of the provisions in paragraphs 5-2and 5-3.。
美国海岸工程手册Part_I-Chap_4
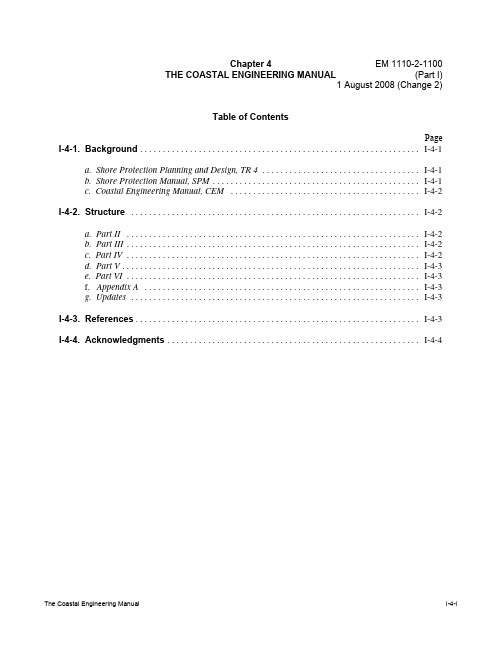
Chapter 4EM 1110-2-1100THE COASTAL ENGINEERING MANUAL(Part I)1 August 2008 (Change 2)Table of ContentsPage I-4-1. Background..............................................................I-4-1a. Shore Protection Planning and Design, TR 4...................................I-4-1b. Shore Protection Manual, SPM..............................................I-4-1c. Coastal Engineering Manual, CEM..........................................I-4-2 I-4-2. Structure................................................................I-4-2a. Part II.................................................................I-4-2b. Part III.................................................................I-4-2c. Part IV.................................................................I-4-2d. Part V..................................................................I-4-3e. Part VI.................................................................I-4-3f. Appendix A.............................................................I-4-3g. Updates................................................................I-4-3 I-4-3. References...............................................................I-4-3 I-4-4. Acknowledgments........................................................I-4-4EM 1110-2-1100 (Part I)1 Aug 08 (Change 2) Chapter I-4The Coastal Engineering ManualI-4-1. BackgroundDuring the 1970s, ‘80s, and ‘90s, coastal engineering practice by the U.S. Army Corps of Engineers (USACE) and standard engineering for most coastal projects throughout the world have been based, wholly or in part, on the Shore Protection Manual (SPM). Since the SPM was last updated in 1984, the coastal engineering field has witnessed many technical advances and increased emphasis on computer modeling, environmental restoration, and project maintenance applications. The BEB produced the first standardized guidance on coastal structure design in 1954, Shore Protection Planning and Design, also known as TR-4. This was the forerunner of the SPM that was first published by CERC in 1973, and revised in 1975, 1977, and 1984. These documents present the methodology that guided coastal structure and beach fill design for most of the projects constructed to date. The USACE traditionally is responsible for constructing and maintaining United States Federally authorized coastal civil works projects including harbor entrance channels, navigation channels and structures, coastal storm damage reduction and shore protection projects. Therefore, the USACE is primarily responsible for developing the principles of coastal engineering as they are practiced in the United States.a.Shore Protection Planning and Design, TR 4. The methodologies of TR-4 emphasized designing coastal structures for stability against wave forces. The technology available at that time provided little means to address the functional performance of structures, nor provide any guidance for predicting the performance or stability of a beach fill. Beach and dune design was only qualitatively addressed. Simple linear wave theory, static terrestrial structural engineering principles, and trail-and-error experiential data were used to develop the empirical relationships and rules-of-thumb presented in TR-4. Beach fills of this era were not usually designed to perform a particular function, but were typically placed as an added feature to increase the sediment supply in the area of interest and to reduce wave energy striking the protective structures (the primary project feature).b.Shore Protection Manual, SPM. The SPM was a significant advancement over TR-4 in that it used the results of physical model tests to develop principles of wave-structure interaction, advancements in wave theory, and statistics and other data from various projects. The SPM provided significantly more guidance in the positioning and intent of groins and breakwaters, predicting the flood control benefits of seawalls, and predicting the stability of beach fills. At 1,160 pages, the first edition of the SPM was almost three times the length of the 20-year-older TR-4 (Camfield 1988). The SPM and beach fill projects of the 1970s and early ‘80s were designed around the objective of beach erosion control and recreational use. The quantity of material to be placed was computed based on the long-term recession rates, and the amount of surface area desired to support recreational needs. The SPM presented guidance to assist in predicting maintenance nourishment quantities based on the grain size of the placed fill and its projected stability relative to the native material grain size. Neither the SPM nor the projects constructed during this time concerned themselves with the performance of the beach fill template during a particular storm. At that time, beach fills were not usually designed with a primary purpose of providing flood control benefits.The SPM is commonly used as a university textbook and as a training aid for apprentice engineers. It is also a convenient reference for empirical procedures to compute a particular design parameter. Approximately 30,000 copies have been sold through the U.S. Government P rinting Office. Translations into other languages, including Chinese and Catalonnian (Spanish), further attest to the SPM’s role as an international standard guidance for professional coastal engineers (Pope 1993, 1998). Even though the SPM is a generalEM 1110-2-1100 (Part I)1 Aug 08 (Change 2)coastal engineering reference, some aspects of navigation and harbor design are not included and its primary focus is shore protection.c.Coastal Engineering Manual, CEM. The advent of numerical models, reliable field instrumentation techniques, and improved understandings of the physical relationships which influence coastal processes lead to more sophisticated approaches in shore protection design in the later 1980s and 90s. Numerous guidance and analytical tools have been developed over the last 15 years to assist the coastal engineer in predicting not only the stability of a beach fill, but also its performance during extreme events. Cross-shore and alongshore change models, hydrodynamic hind cast data bases, and stochastic statistical approaches have been developed to provide the practicing coastal engineer with procedures for quantifying the flood control benefits of a proposed design. The functional interaction of beach erosion control structures (i.e., groins and breakwaters) can be analyzed with numerical simulation. Seawalls can be designed not only for stability, but also physically modeled to predict various elements of the wave-structure interaction including scour and overtopping. A “modern” technical document incorporating all the tools and procedures used to plan, design, construct, and maintain coastal projects was needed. The USACE tasked the Coastal Engineering Research Center and, later, the Coastal and Hydraulics Laboratory with producing a new reference incorporating established science and much of this new technology, to be called the Coastal Engineering Manual (CEM). Included in the CEM are the basic principles of coastal processes, methods for computing planning and design parameters, and guidance on how to develop and conduct studies in support of coastal storm damage reduction, shore protection, and navigation projects. Broader coverage of all aspects of coastal engineering are provided, including new sections on navigation and harbor design, dredging and dredged material placement, structure repair and rehabilitation, wetland and low energy shore protection, cohesive shores, risk analysis, numerical simulation, the engineering process, and other topics.I-4-2. StructureThe CEM contains two major subdivisions: science-based parts and engineering-based parts. The science-based parts include “P art II - Coastal Hydrodynamics,” “P art III – Coastal Sediment P rocesses,” and “Part IV – Coastal Geology.” These provide the scientific foundation on which the engineering-based parts rely.a.Part II. “Coastal Hydrodynamics” is organized to lead the reader from the fundamental principles of linear and other wave theories, including irregular waves and spectral analysis, to ocean wave generation and through the process of transformation as the wave approaches and reacts with the coastline. Analysis of water level variations including astronomical tides and storm surges are presented along with the hydrodynamics of coastal inlets and harbors are included in other chapters.b.Part III. “Coastal Sediment Processes” includes chapters on sediment properties, along shore and cross-shore transport, as well as chapters on wind transport, cohesive sediment processes and shelf transport.c.Part IV. “Coastal Geology” includes chapters on terminology, geomorphology, and morphodynamics.The two engineering-based parts, Part V – “Coastal Project Planning and Design” and Part VI – “Design of Coastal Project Elements” are oriented toward a project-type approach, rather than the individual structure design approach that characterized the SPM. The architecture and substance of the engineering-based parts is the result of an internationally-attended workshop in February 1994. A logical systems-based approach is used for the engineering structure of the CEM. This mirrors the engineering process with guidance inEM 1110-2-1100 (Part I)1 Aug 08 (Change 2) selecting and using various planning and design tools as appropriate for the project at hand. The engineering tools are presented in a modular grouping to allow for future updates as the technology continues to advance.d.Part V. “Coastal Project Planning and Design” starts with chapters discussing the planning and design process and site characterization. Following these general chapters are ones discussing the planning and design of shore protection projects (including coastal armoring, beach restoration, beach stabilization and coastal flood protection projects), beach fill, navigation projects (including defining the fleet, entrance channel, inner harbor elements, structures, sedimentation, maintenance, and management), and environmental enhancement projects (including laws, regulations, and authorities, issues, alternative approaches, planning, and design). A final chapter outlines conditions and regulations unique to USACE projects in the United States.e.Part VI. “Design of Coastal Project Elements” includes chapters discussing philosophy of coastal structure design, the various types and function of coastal structures, site conditions, materials, design fundamentals, reliability, and the design of specific project elements (including a sloping-front structure, vertical-front structure, beach fill, floating structure, pile structure, and a pipeline and outfall structure.f.Appendix A. The “Glossary of Coastal Terminology” has been compiled from numerous sources and lists terms found throughout the CEM. Note that there is no single, comprehensive list of mathematical terms and symbols. Each CEM chapter has its own symbol list.g.Updates. The CEM is intended to be a “living document” and to be updated periodically as advances in the field render the existing chapters obsolete or inadequate. Comments and suggestions should be addressed to the Coastal and Hydraulics Laboratory, CEERD-HN-CE. Corrected or modified chapters will be posted on the CHL web page.I-4-3. ReferencesCamfield 1988Camfield, F. E. 1988. “Technology Transfer – The Shore Protection Manual,” Journal of Coastal Research, 4(3), pp 335-338.Pope 1993Pope, J. 1993. “Replacing the SPM: The Coastal Engineering Manual.” The State of the Art of Beach Nourishment, Proceedings, 6th Annual National Conference on Beach Preservation Technology, Florida Shore and Beach Preservation Association, Tallahassee, FL, pp 319-334.Pope 1998Pope, J. 1998. “Replacing the SPM: The Coastal Engineering Manual.” PIANC Bulletin, No. 97, pp 43-46. USACE 1954USACE 1954. Shore Protection Planning and Design, Technical Report No. 4, Beach Erosion Board, U.S. Government Printing Office, Washington, DC.Shore Protection Manual 1984Shore Protection Manual, 4th ed., 2 Vol., U.S. Army Engineer Waterways Experiment Station, U.S. Government Printing Office, Washington, DC, 1,088 p.EM 1110-2-1100 (Part I)1 Aug 08 (Change 2)I-4-4. AcknowledgmentsAuthors of Chapter I-4, “The Coastal Engineering Manual:”Joan Pope, U.S. Army Engineer Research and Development Center, Vicksburg, Mississippi. John H. Lockhart, Jr., Headquarters, U.S. Army Corps of Engineers, Washington, DC, (retired). Reviewer:Andrew Morang, Ph.D., CHL。
美军土木工程教程US Army Course—— DESIGN FORMS FOR AN OVERHEAD CONCRETE SLAB

SUBCOURSE EDITION EN5153A DESIGN FORMS FOR AN OVERHEADCONCRETE SLABDESIGN FORMS FOR THE OVERHEAD CONCRETE SLABSubcourse EN5153EDITION AUnited States Army Engineer SchoolFort Leonard Wood, Missouri 654732 Credit HoursEdition Date: August 1995SUBCOURSE OVERVIEWThis subcourse addresses the principles of designing forms for an overhead concrete slab. As an engineer carpenter, you must understand the basic principles concerning the design of overhead concrete slabs that will support the weight of concrete placed in/on them.There are no prerequisites for this subcourse.The lesson in this subcourse reflects the doctrine which was current at the time it was prepared. In your own work situation, always refer to the latest official publications.Unless otherwise stated, the masculine gender of singular pronouns is used to refer to both men and women. TERMINAL LEARNING OBJECTIVE:ACTION:You will describe procedures to design wooden forms for an overhead concrete slab. CONDITION:You will be given the material contained in this subcourse.STANDARD:To demonstrate competency of this task you must achieve a minimum of 70 percent on the subcourse examination.i EN5153TABLE OF CONTENTSSection Page Subcourse Overview (i)Grading and Certification Instructions (iii)Lesson: Design Forms for the Overhead Concrete Slab.....................................................................................1-1 Part A: Select Proper Materials............................................................................................................1-2 Part B: Determine the Total Unit Load on the Floor Form..................................................................1-4 Part C: Determine the Maximum Joist Spacing...................................................................................1-6 Part D: Determine the Uniform Load on a Joist...................................................................................1-9 Part E: Determine the Maximum Stringer Spacing............................................................................1-10 Part F: Determine the Uniform Load on the Stringer.........................................................................1-12 Part G: Determine the Maximum Shore Spacing...............................................................................1-13 Practice Exercise..................................................................................................................................1-15 Answer Key and Feedback..................................................................................................................1-18 Appendix A: List of Common Acronyms.........................................................................................................A-1 Appendix B: Recommended Reading List........................................................................................................B-1 Student Inquiry SheetEN5153iiLESSONDESIGN FORMS FOR AN OVERHEAD CONCRETE SLABCritical Task: 051-199-4014OVERVIEWLESSON DESCRIPTION:In this lesson, you will learn to design forms for an overhead concrete slab.TERMINAL LEARNING OBJECTIVE:ACTION: You will describe procedures to design wooden forms for an overhead concrete slab. CONDITION: You will be given subcourse booklet EN5153.STANDARD: Complete the lesson and the practical exercise.REFERENCES: The material contained in this lesson was derived from Field Manuals (FMs) 5-34, 5-426, and 5-742; Soldier Training Publications (STPs) 5-12B24-SM-TG; and 5-51B12-SM-TG.INTRODUCTIONAs a carpenter, one of your concerns is to ensure that the forms you design will support the weight of concrete placed in or on them. This lesson shows you how to properly design these forms.1-1EN5153PART A: SELECT PROPER MATERIALSYou will need to specify the materials you use for constructing the overhead roof slab when designing forms. Anyone using your design must know exactly which materials to use for each of the structural members as shown in Figure 1-1.Sheathing. Sheathing is the first covering of boards or of waterproof materials on the outside wall of a frame structure or on a timber roof. Sheathing shapes and holds the concrete. Plywood or solid sheet metal is the best choice of material to use. The materials to be used are normally 1- by 4- or 1- by 6-inch boards and 5/8- or 3/4-inch plywood.Joist. A joist is any small timber or metal beam that is ranged parallel from wall to wall in a structure to support a floor or ceiling. Joists support the sheathing to prevent movement. When possible, use 2- by 4-inch, 2- by 6-inch, or 4- by 4-inch material.Stringer. A stringer is a long horizontal timber connecting uprights in a frame or supporting a floor. Stringers support the joists and prevent movement. When possible use material at least 2 inches thick.Shore. A shore is a piece of lumber at least as great in size as the stringer. It is used to support or brace the stringer. A shore performs the same function as ties perform in a wall form; it also supports the concrete at the desired elevation above ground. Use lumber at least as large as the stringer, but never smaller than 4- by 4-inch lumber.Lateral Bracing. Lateral bracing may be required between adjacent shores to keep shores from bending under the load. When possible use 1- by 6-inches or larger material for bracing material. Cross or "X" bracing of some type will always be required to support the formwork materials.EN51531-2Figure 1-1. Elements of supported slab formwork1-3EN5153PART B: DETERMINE THE TOTAL UNIT LOADON THE FLOOR FORMYou will need to understand the following terms and formulas to determine the total unit load on floor forms: Determine total unit load (TL) by summing the result for dead load and live load. TL is measured in pounds per square feet (psf).Dead load (DL). Dead load is the weight of ordinary concrete and is estimated at 150 pounds per cubic foot (lb/cu ft).To determine DL, use this formula:Live Load (LL). You must also consider an additional live load of construction workers and materials. This LL is generally 50 psf. However, if you use powered concrete buggies, the LL would be 75 psf.Now that you know how to determine DL and LL it is time to determine TL.To determine TL, use this formula:TL = DL + LLEXAMPLE:Determine the TL on the form if the slab thickness is 5 inches and you are using nonpowered equipment.TL = DL + LLTL = (150 x 0.42) + 50TL = 63 + 50TL = 113 psfEN51531-4Work the following problem to see how well you understand the concepts you have just reviewed.PROBLEM-1:Determine the TL load on the form if the slab thickness is 4 inches and you are using a powered concrete buggy.A. 50B. 75C. 125D. 150See page 1-14 for the solution to this problem.1-5EN5153PART C: DETERMINE THE MAXIMUM JOIST SPACINGJoist spacing depends on the type of sheathing used-boards or plywood. Joist spacing, like stud spacing, is found by using either Table 1-1 for board sheathing or Table 1-2 for plywood sheathing. Be sure to use the correct one.NOTE:All plywood sheathing problems and practice exercises will be using the Strong Way column in Table 1-2.Table 1-1. Maximum stud or joistspacing for support of board sheathingTo find the maximum joist space using Table 1-1 or 1-2-∙Find the TL in the left column. If the value is not listed, round up the load to the next value on the table;for example, for 138 psf use 150 psf.∙Move across the row to the column headed by the sheathing thickness. The intersecting number is the maximum joist spacing.EN51531-6Table 1-2. Maximum stud or joistspacing for support of plywood sheathingEXAMPLE:Determine the maximum joist spacing if the TL is 150 psf and the plywood sheathing is 5/8-inch material.19 inches1-7EN5153Work this problem to see how well you understand the concept you have just reviewed. PROBLEM-2:Determine the maximum joist spacing if the sheathing is 3/4-inch plywood and the TL is 125 psf.A. 20B. 22C. 23D. 24See page 1-14 for the solution to this problem.EN51531-8PART D: DETERMINE THE UNIFORM LOAD ON A JOISTThe uniform load on a joist is calculated the same way as the uniform load on structural members in wall-form designs. The unit of measurement is pounds per linear foot (lb/lin ft).To determine uniform load on a joist, use this formula and the procedures following:∙Use the actual TL, not the rounded up figure, to obtain the maximum joist spacing.∙Divide before multiplying.∙Round up your answer to the next whole number.EXAMPLE:Determine the uniform load on the joist if the TL is 133 psf and the maximum joist spacing is 28 inches.Work this problem to see how well you understand this concept you just reviewed.PROBLEM-3:Determine the uniform load on the joist if the TL is 113 and the joist spacing is 44 inches.A. 410B. 414C. 424D. 426See page 1-14 for the solution to this problem.1-9EN5153PART E: DETERMINE THE MAXIMUM STRINGER SPACINGTo find the maximum stinger spacing, use Table 1-3 and the following procedures:∙Find the uniform load on the joist in the left column. If the value is not listed, round up the load to the next value on the table; for example, if the value is 113 lb/lin ft, use 125.∙Move across the row to either the single or double-members section. Then locate the joist size that you will be using. The intersecting number is the maximum spacing of the stringers.Table 1-3. Maximum safe spacing of supporting members(wales, ties stringers, 4- by 4-inch and larger shores)EN51531-10EXAMPLE:Determine the maximum spacing of single stringers if you use 4-by-4 joists and a uniform load of the joists of 200 lb/lin ft.65 inchesWork this problem to see how well you understand the concepts you have just reviewed.PROBLEM-4:Determine the maximum single-stringer spacing if the uniform load on the joist is 165 lb/lin ft and you are using 2-by-4 material.A. 45B. 49C. 77D. 85See page 1-14 for the solution to this problem.1-11EN5153PART F: DETERMINE THE UNIFORM LOAD ONTHE STRINGERTo determine uniform load on a stringer, use this formula:EXAMPLE:Determine the uniform load on the stringer if the TL is 350 and the maximum stringer spacing is 50 inches.Work the following problem to see how well you understand the concept you just reviewed.PROBLEM-5:Determine the uniform load on the stringer if the TL is 250 psf and the maximum stringer spacing is 85 inches.A. 1,250B. 1,540C. 1,680D. 1,770See page 1-14 for the solution to this problem.EN51531-12PART G: DETERMINE THE MAXIMUM SHORE SPACINGThe maximum shore spacing is based on the stringer strength. To find the maximum shore spacing, use Table 1-3, page 1-10, and the procedures following:∙Find the uniform load on the stringer in the left column. If the value is not listed, round up the load to the next value on the table; for example, if the value is 113 lb/lin ft, use 125.∙Move across the row to the column headed by the stringer size, depending on whether single stringers or double stringers will be used. The intersecting number is the maximum spacing of the shores. EXAMPLE:Determine the maximum shore spacing if the uniform load on the stringers is 825 lb/lin ft and the single stringers are 4 by 6 inches.48 inchesWork the following problem to see how well you understand of the concept you just reviewed.PROBLEM-6:Determine the maximum shore spacing if the uniform load on the stringer is 720 lb/lin ft and the single stringers are 4 by 6 inches.A. 48B. 51C. 56D. 80See page 1-14 for the solution to this problem.1-13EN5153LESSON PROBLEMSANSWER KEY AND FEEDBACK Problem Correct Answer1. C. 125 psf (page 1-4)2. C. 23 psf (page 1-7)3. B. 414 lb/lin ft (page 1-9)4. A. 45 inches (page 1-10)5. D. 1,770 lb/lin ft (page 1-12)6. B. 51 inches (page 1-13)EN51531-14PRACTICE EXERCISEThe following items will test your knowledge of the material covered in this lesson. Circle your answer for each item on the practice exercise page. When you have completed the exercise, check your answers with the key that follows. If you answer any item incorrectly, study again that part which contains the portion involved.1. Determine the TL on the form, in psf, if it has a 6-inch-thick slab and you use nonpowered equipment.A. 50B. 110C. 125D. 1502. Determine the maximum joist spacing if the sheathing thickness is 1 1/2-inch boards and the total unit load is 125 psf.A. 33B. 37C. 39D. 41EN51531-153. Determine the uniform load on the joist if the total unit load is 150 psf and the joist spacing is 22 inches.A. 150B. 260C. 275D. 3304. Determine the maximum single-stringer spacing if the uniform load on the joist is 900 lb/lin ft and you are using 4-by-6 material.A. 46B. 48C. 51D. 68EN51531-165. Determine the uniform load on the stringer if the TL is 125 psf and the maximum stringer spacing is 54 inches.A. 125B. 563C. 660D. 7626. Determine the maximum shore spacing if the uniform load on the stringer is 560 lb/lin ft and the double stringer are 4 by 4 inches.A. 37B. 53C. 63D. 711-17EN5153PRACTICE EXERCISEANSWER KEY AND FEEDBACK Item Correct Answer1. C. 125 (page 1-4)2. C. 39 (page 1-6)3. C. 275 (page 1-9)4. B. 48 (page 1-10)5. B. 563 (page 1-12)6. B. 53 (page 1-13)EN51531-18。
美国旧金山海湾海岸带恢复工程

➢低盐度的河口生境上溯了15千米,从而导致湾区几种 鱼类的数量减少了三倍。
(三)水质下降
➢污染物对海湾周围的动植物、人居生 活造成影响,同时也降低了生态系统的 生产力以及健康状况。
➢有毒化学污染物影响海湾水质。
(四)食物网受损
由于20世纪70年代中期的淡水补给 减少以及外来物种的入侵,导致:
从1976年至今,苏珊湾的浮游生物 量降低了80%; 小型浮游动物在1974 ~ 2001年间减 少了98%;
此外,着眼于加强与保护根本的生态系统过程与结构特征,而不是只保护特 定的几个物种。
(三)全流域水资源管理
必须从生态系统层面上开展恢复与管理。
州政府和联邦政府合作制定完成CALFED计划,通过对海湾-三角洲及其支流进
行统一管理,从而缓和水资源矛盾。包括了1000多个计划和工程,主要解决
水质、供水保障、生态系统恢复、流域水利工程4个领域的问题,以维持依赖
美国海湾海岸带恢复工程
目录
contents
Part one
1 背景介绍
04
Part two
2 旧金山海湾三角区的区位功能
06
Part three
3 海湾的生态环境问题
13
Part four
4 海湾生态恢复的目标
15
Part five
5 海湾生态恢复的主要技术方法
22
Part six
6 生态恢复的成效
(一)湿地恢复
保护、恢复及增加湿地、河岸生态系统以 及相关高地面积。加强对海湾生境、季节 性湿地、河湖和相关高地的管理。支持生 态恢复项目的监测与评估,以及相关的研 究,以提高未来恢复与增强海湾生态系统 的能力。
(二)生态系统恢复
swachhata engineer app 用户手册说明书

Swachhata Engineer App User ManualDevote 100 hours every year towards the cause of cleanlinessPrime Minister Shri. Narendra ModiContents04 Introduction to Swachhata Engineer App05 Registration Process06 Verification Process08 Using the application11 Complaints Management14 Frequently Asked Questions (FAQs)AbstractThis document is the user manual for the Swachhata - Engineer app: a step towards making India cleaner and healthier. This app is designed for municipal sanitary engineers, to facilitate their work by incorporating the ease of technology into their jobs.The app allows sanitary engineers to connect directly with citizens who report sanitation and public health related issues through the Swachhata – Citizen app and address citizen grievances in real time.This guide will provide in depth instruction on who the app is for, how to install it, how to use it, explain its features, functions and also frequently asked questions regarding the app.IntroductionWho can use the app?The Swachhata - Engineer app is exclusively designed for municipal sanitary engineers.As a result, any sanitary engineer who is registered with a ULB can use this app. Individuals who are not registered as sanitary engineers will n ot be able to register as users for the app.How to install the app?The respective ULB will send an SMS to the engineer’s phone with the link to Swachhata - Engineer application. Clicking on the link will navigate to the Google Play Store/Apple App store from where an engineer can download the application.The engineer can also search for the app on Play store and App store and download the same.Phone requirementsThis app is available for download on both Android & iOS platforms. This app is compatible with versions as below:•For Android, Version 4.3 and above•For iOS, Version 13.0 and aboveRegistration ProcessHow to register?Once the engineer user (municipal sanitary engineers / sanitary inspector) has successfully downloaded the app, they can open it and the registration p rocess will begin automatically.Language settingsThe engineers can begin the registration by choosing their preferred language for the app. There are nine languages available to choose from: English, Hindi, Tamil, Malayalam, Kannada, Telugu, Marathi, Oriya and Bengali.Please note that if an engineer wishes to change the language at any point after registering, they must log out of the app and log in again. They will be prompted to choose their language every time during logging in.After having chosen their preferred language, they will be directed to the verification process.Click hereto selectpreferredlanguageSelect fromthe list of 9languagesVerification ProcessNumber verificationThe engineer has to verify his/her registered mobile number by receiving an OTP during registration.The engineer has to ensure that the mobile number they enter is the same number that is registered with their respective ULB. If not, the engineers are advised to request their ULB nodal officer to add their number at the backend.If the engineer’s mobile number is registeredUpon entering the registered mobile number, the engineer will receive an OTP. The engineer will be required to enter it in the box “Enter OTP”, as depicted below.If the phone does not automatically receive the OTP, please try pressing the “Re - s end Code” button below the OTP entry box.Enter mobile numberIf the engineer’s mobile number is not registeredIn case, if the engineer’s mobile number is not registered with the ULB, their number can be registered and added through ULB login in Swachh.city portal. The engineer should contact the respective ULB officer to register and add their number.Enter OTPreceived through SMSUsing the application Home Page: Complaints listingOn completing the registration process, the engineer will be taken to the complaints listing page which is also the home page.This page comprises of the following:•Category of Complaints: Assigned, High Priority, On the job, Reopened, Resolved and Rejected•Left Menu: a drop-down menu on the top left-hand corner of the screen•An in-app notification button (the bell), on the top right-hand corner of the pageThe seven different categories of complaints in the home page are explained below:Left menuOn clicking the top left menu, the app displays the following:a) Rate Us on Playstore/Appstore: This rating will help the developers understand if the engineersare happy, s atisfied or dissatisfied with the app. Feedback in the form of detailed comment(s) is appreciated.b) Report a Bug: In the event, the engineer has issues using the app, he/she can bring theproblems to the attention of the developers by reporting a bug. This will help developers improve the app for hassle-free usage.c) Privacy Policy: The privacy policy of the application is mentioned in detail.d) Profile: On clicking their name, the engineer will be able to view their profile.e) Logout: clicking this button will log the engineer out of the app. The engineer need not logoutafter every session they use the app. Closing the app will not automatically log them out. Please note that if the engineer chooses to log out, they will need to choose their preferred language settings while logging in again.In-app notificationsThe bell on the top right-hand side of the Complaints Listing Page indicates the number of unread notifications. On clicking the bell, the engineer will be navigated to the notifications page. If the engineer wants to view previous notifications, they should click on the “Previously Read” button at the bottom of the screen.Complaints Management Complaints explainedA complaint is created when a citizen/user uploads a description of a sanitary or publichealth related issue through the Swachhata - Citizen App. Citizens are required to explain the nature of the issue, tag the location with an accurate address, and upload a picture of the issue reported.Each complaint is equipped with a comments button, on the bottom of every complaint. Both citizens and engineers will be able to view and post comments on individual complaints.Complaints’ glossary1. Open: a complaint is posted by a citizen and needs the engineer’s attention.2. On the Job: a complaint that the engineer is currently working on. An engineer canhave multiple complaints simultaneously for which the statuses are “On the Job”.3. Resolved: a complaint that the engineer has resolved.Please note - only when an engineer uploads a relevant image as a proof of complaint resolution, the status of complaint can now be changed to “Resolved”in the Engineer App and through Swachh.City portal.4. Rejected: a complaint that the engineer has rejected.Please note that the engineer can only reject complaints in circumstances such as if the details of the complaint (location, picture, or issue) are not clear or if the complaint does not belong to their ward.5. Re-opened: a complaint where the citizen is not satisfied with the resolution of thecomplaint and wishes to have the issue addressed once more.Changing the status of complaintsOpening a complaint enables an engineer to view the details of the complaint as well as changing its status as shown in image below.All complaints are declared as “Open” once posted.o“Open” or "Reopened" complaints can be changed to either “On the Job” or “Rejected” statuseso“On the Job” complaints can be changed to either “Resolved” or "Rejected" statuses o"Rejected" complaints cannot be changed to any other statuses.In order to change the status of a complaint to “Resolved” an engineer must post a picture of the complaint as a proof of resolution and post a comment indicating that the complaint has been resolved.Once the engineer changes the status of a complaint, the complainant will get a notification. The complainant also can post their feedback based on their satisfaction regarding resolution.The engineer also can reject any citizen’s application if it satisfies any of the following threeconditions:• Complaint out of the city• Image of the complaint not clear• Location of the complaint not clear14FAQsCan an engineer share the app download link with other people?Yes, an engineer can share the app download link with other people. However, onlyregistered sanitary engineers will be granted access to the app.Is there a time limit in which an engineer needs to use the app download link?No, the link is valid for as long as an engineer has it. They can use it whenever they want to.Can an engineer update their mobile number in Swachhata Platform?An engineer should be using only the mobile number that is registered with the ULB. Incase if they want to update their mobile number, they should contact their respectiveULB Nodal Officer.What are the different modes through which an engineer can address complaint ofcitizens?An engineer can resolve citizens’ complaints through the following modes:• Through Swachhata Engineer mobile application• Through Swachh.city portal• Through third party local city apps integrated with Swachhata.What are the requirements of a local third-party city app to be integrated to Swachhata Platform?The code and documentation required for API integration for integrating the city appwith Swachhata is available in through the following link:http://swachh.city/assets/files/Integrate_With_Swachhata_App_v2.pdf .Local Apps can be integrated to Swachhata App via API, if• Complaint categories and respective SLAs (Service Level Agreements) aresimilar to Swachhata• Live pushing of complaints and resolution integrated to Swachhata• API validation added for mandatory image upload for resolutionDoes an engineer have to upload the picture of complaint as a proof of resolution?Yes, as a part of 360-degree complaints resolution of the application, it is nowmandatory for an engineer to upload a complaint resolution image as a proof ofcomplaint resolution. An engineer can either click a new picture and upload or elseselect an image from the gallery and click resolve.If the citizen is not satisfied with the resolution, they can provide feedback bycommenting on the complaint and declare the complaint as “Re -opened”.Ek Kadam Swachhata Ki Aur.inFor any questions on the Swachhata Engineer App or Swachhata Technology Platform, write in to connect with us at***************************Swachhata Technology Platform powered byJanaagraha Centre for Citizenship and Democracy。
海岸防护课件
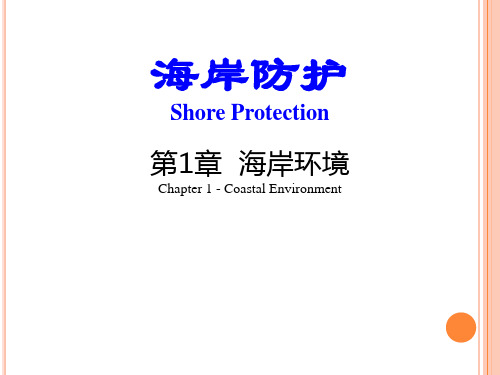
§1.1.3 海岸带
全国海岸带和海涂资源综合调查
调查时间:1980~1985年 调查范围:从海岸线向内陆延伸10 km,向海延伸至10~15
m等深线,总面积约35万平方公里 调查成果:
全国海岸带面积约2.5×105 km2,其中潮上带占37%,潮间带占 7%,潮下带占56%
潮间带海涂面积2×104 km2 海岸线长度山东最长,福建次之 海岸带面积江苏最大,山东第二 海岸带宽度上海和江苏最大 海涂面积江苏最大,山东第二 海岸带宽度与面积最大、海涂最宽阔的地方正反映出黄河口和
热带气旋、台风或飓风
热带气旋是一种发生在热带或副热带海洋上的气旋性漩涡(北 半球逆时针)
热带气旋分为六级(中国气象局):
热带低压:平均最大风力小于8级(风速U≤17.1m/s) 热带风暴:平均最大风力达8~9级(风速17.2≤U≤24.4m/s) 强热带风暴:平均最大风力达10~11级(风速24.5≤U≤32.6m/s) 台风:平均最大风力达12~13级(风速32.7≤U≤41.4m/s) 强台风:平均最大风力达14~15级(风速41.5≤U≤50.9m/s) 超强台风:平均最大风力大于16级(风速U≥51.0m/s)
海岸防护
Shore Protection
第1章 海岸环境
Chapter 1 - Coastal Environment
§1 海岸环境
§1.1 §1.2 §1.3
海岸线与海岸带 海岸类型 海岸环境特征
§1.1 海岸线与海岸带
§1.1.1 海岸线 §1.1.2 特征潮位和高程基准面 §1.1.3 海岸带 §1.1.4 浅海海域
平均坡度0.1°
§1.2.1 基岩海岸(港湾海岸)
开发利用:
USCG 具体要求
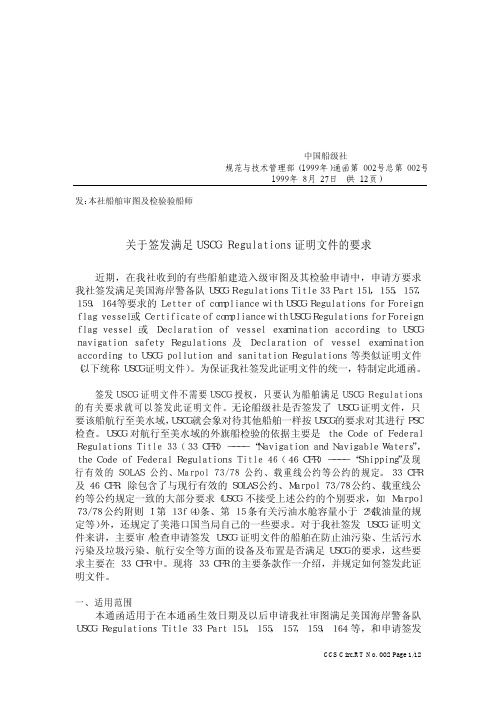
CCS通 函Circular中国船级社规范与技术管理部(1999年)通函第002号总第002号1999年8月27日 (共12页)发:本社船舶审图及检验验船师关于签发满足USCG Regulations证明文件的要求近期,在我社收到的有些船舶建造入级审图及其检验申请中,申请方要求我社签发满足美国海岸警备队USCG Regulations Title 33 Part 151, 155, 157,159, 164等要求的Letter of compliance with USCG Regulations for Foreignflag vessel 或Certificate of compliance with USCG Regulations for Foreignflag vessel 或Declaration of vessel examination according to USCGnavigation safety Regulations及Declaration of vessel examinationaccording to USCG pollution and sanitation Regulations等类似证明文件(以下统称USCG证明文件)。
为保证我社签发此证明文件的统一,特制定此通函。
签发USCG证明文件不需要USCG授权,只要认为船舶满足USCG Regulations的有关要求就可以签发此证明文件。
无论船级社是否签发了USCG证明文件,只要该船航行至美水域,USCG就会象对待其他船舶一样按USCG的要求对其进行PSC检查。
USCG对航行至美水域的外旗船检验的依据主要是the Code of FederalRegulations Title 33(33 CFR)---- “Navigation and Navigable Waters”,the Code of Federal Regulations Title 46(46 CFR)---- “Shipping”及现行有效的SOLAS公约、Marpol 73/78公约、载重线公约等公约的规定。
- 1、下载文档前请自行甄别文档内容的完整性,平台不提供额外的编辑、内容补充、找答案等附加服务。
- 2、"仅部分预览"的文档,不可在线预览部分如存在完整性等问题,可反馈申请退款(可完整预览的文档不适用该条件!)。
- 3、如文档侵犯您的权益,请联系客服反馈,我们会尽快为您处理(人工客服工作时间:9:00-18:30)。
Chapter 1EM 1110-2-1100INTRODUCTION(Part I)1 August 2008 (Change 2)Table of ContentsPage I-1-1. Purpose and Scope.......................................................I-1-1 I-1-2. Applicability.............................................................I-1-1 I-1-3. Definitions...............................................................I-1-1a. Coastal.................................................................I-1-1b. Coastal engineering.......................................................I-1-1c. Coastal science..........................................................I-1-2 I-1-4. Bibliography.............................................................I-1-2 I-1-5. References...............................................................I-1-2 I-1-6. Acknowledgments........................................................I-1-4EM 1110-2-1100 (Part I)1 Aug 08 (Change 2) Chapter I-1IntroductionI-1-1. Purpose and ScopeThe Coastal Engineering Manual (CEM) assembles in a single source the current state-of-the-art in coastal engineering to provide appropriate guidance for application of techniques and methods to the solution of most coastal engineering problems. The CEM provides a standard for the formulation, design, and expected performance of a broad variety of coastal projects. These projects are undertaken to provide or improve navigation at commercial harbors, harbor works for commercial fish handling and service facilities, and recreational boating facilities. As an adjunct to navigation improvements, shore protection projects are often required to mitigate the impacts of navigation projects. Beach erosion control and hurricane or coastal storm protection projects provide wave damage reduction and flood protection to valuable coastal commercial, urban, and tourist communities. Environmental restoration projects provide a rational layout and proven approach to restoring the coastal and tidal environs where such action may be justified, or required as mitigation to a coastal project’s impacts, or as mitigation for the impact of some previous coastal activity, incident, or neglect. As the much expanded replacement document for the Shore Protection Manual (1984) and several other U.S. Army Corps of Engineers (USACE) manuals, the CEM provides a much broader field of guidance and is designed for frequent updates.I-1-2. ApplicabilityThis manual is applicable to U. S. Army Corps of Engineers (USACE) Commands having civil works responsibility. It is anticipated that the comprehensive scope and instructions of this manual will warrant its use by a broad spectra of coastal engineers and scientists beyond the bounds of the USACE. Although this broad application has been considered throughout the development of the CEM, some sections are specific to the mission, authority, and operation of the USACE.I-1-3. DefinitionsDefinitions are listed throughout the manual when terms are first introduced. In addition, a glossary of terms is provided in the appendix, and Table IV-1-1 lists definitions of common coastal geologic features. However, a few basic definitions will help the novice to better understand and grasp the purpose and scope of the CEM. Part IV, Chapter 2 defines types of coastal structures.a.Coastal. Referring to the zone where the land meets the sea, a region of indefinite width that extends inland from the sea to the first major change in topography. In this manual, “coastal” will refer to shores that are influenced by wave processes (oscillatory flow dynamics). Bays, and lakes, and estuaries are included, but rivers, primarily influenced by generally unidirectional currents, are generally beyond the scope of this manual. Estuaries, including that part of rivers subject to the ebb and flow of the tide are covered by this manual.b.Coastal engineering. One of several specialized engineering disciplines that fall under the umbrella of civil engineering. It is a composite of many physical science and engineering disciplines having application in the coastal area. It requires the rational interweaving of knowledge from a number of technical disciplines to develop solutions for problems associated with natural and human induced changes in theEM 1110-2-1100 (Part I)1 Aug 08 (Change 2)coastal zone, the structural and non-structural mitigation of these changes, and the positive and negative impacts of possible solutions to problem areas on the coast. Coastal Engineers may utilize contributions from the fields of geology, meteorology, environmental sciences, hydrology, physics, mathematics, statistics, oceanography, marine science, hydraulics, structural dynamics, naval architecture, and others in developing an understanding of the problem and a possible solution. The Coastal Engineer must consider the processes present in the area of interest such as:•Environmental processes (chemical, ecological).•Hydrodynamics processes (winds, waves, water level fluctuations, and currents).•Seasonal meteorological trends (hurricane season, winter storms).•Sediment processes (sources, transport paths, sinks, and characteristics).•Geological processes (soil and strata characteristics, stable and migrating sub-aerial and sub-aqueous features, rebounding or subsiding surfaces).•Long-term environmental trends (sea level rise, climate change).•Social and political conditions (land use, development trends, regulatory laws, social trends, public safety, economics).Harbor works, navigation channel improvements, shore protection, flood damage reduction, and environmental preservation and restoration are the primary areas of endeavor.c.Coastal science. This field is a suite of interdisciplinary technologies applied to understanding processes, environments, and characteristics of the coastal zone. Coastal Engineers use these understandings to develop physical adaptations to solve problems and enhance the human interface with the coast.I-1-4. BibliographyTechnical and scientific literature cited in each chapter is listed in the chapter references.I-1-5. ReferencesThe following are official USACE engineer regulations (ER), engineer manuals (EM), engineer pamphlets (EP), and technical manuals (TM) found in the bibliographies following each chapter. They are highlighted here for easy USACE use.TM 5-850-1Engineering and Design of Military PortsER 1105-2-100Planning Guidance NotebookEP 1165-2-1Digest of Water Resources Policies and AuthoritiesEM 1110-2-1100 (Part I)1 Aug 08 (Change 2) EM 1110-1-1802Geophysical Exploration for Engineering and Environmental InvestigationsEM 1110-1-1804Geotechnical InvestigationsEM 1110-2-1204Environmental Engineering for Coastal Shore ProtectionEM 1110-2-1415Hydrologic Frequency AnalysisEM 1110-2-1613Hydraulic Design of Deep-Draft Navigation ProjectsEM 1110-2-1615Hydraulic Design of Small Boat HarborsEM 1110-2-1906Laboratory Soils TestingEM 1110-2-2301Test Quarries and Test FillsEM 1110-2-2302Construction with Large StoneEM 1110-2-5025Dredging & Dredged Material DisposalEM 1110-2-5026Beneficial Uses of Dredged MaterialEM 1110-8-1 (FR)Winter Navigation on Inland WaterwaysEM 1110-2-1100 (Part I)1 Aug 08 (Change 2)I-1-6. AcknowledgmentsAuthors of Chapter I-1:Joan Pope, U.S. Army Engineer Research and Development Center, Vicksburg, Mississippi. John H. Lockhart, Jr., Headquarters, U.S. Army Corps of Engineers, Washington, DC, (retired). Reviewer:Andrew Morang, Ph.D., CHL。