调节阀检修规程(DOC)
阀门维修规程及技术措施
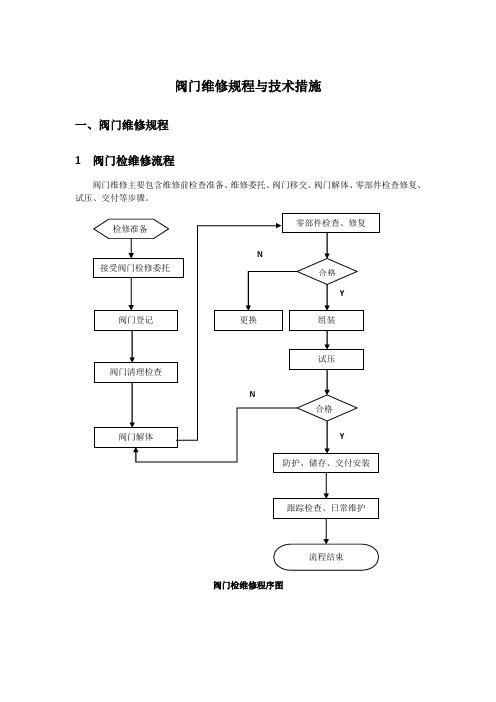
阀门维修规程与技术措施一、阀门维修规程1 阀门检维修流程阀门维修主要包含维修前检查准备、维修委托、阀门移交、阀门解体、零部件检查修复、试压、交付等步骤。
阀门检维修程序图二、阀门维修技术措施1 检维修准备1.1 技术准备1.1.1 根据检维修的内容,收集相关的技术资料及广西石化的相关管理规定,编写《阀门检维修规程》、《阀门检维修通用作业指导书》、《阀门检修专用作业指导书》等相关技术管理文件。
1.1.2 相关技术人员及施工人员认真阅读阀门技术文件和相关的技术规范,明确检维修范围、技术要求、各项技术指标。
1.1.3 填写阀门检修作业技术交底单和安全交底单,同时向检维修人员进行交底。
1.2 施工人员准备1.2.1 所有施工人员均经过三级安全教育培训,并体检合格,取得上岗证,特殊工种人员均已取得特种工证。
1.2.2 阀门检修作业人员根据阀门检修的需要、实际工程量及施工进度进行调配。
常规人员配备已满足日常阀门检维护的需要,装置大修时根据需要调配充足的作业人员,以满足检维修的需要。
1.2.3 日常检维护人员配置2 阀门一般性检查2.1 对送修阀门进行认真检查,包括阀门外观、手轮、铭牌、法兰面、阀杆、阀体锈蚀程度、螺栓锈蚀程度等。
并进行登记2.2 将阀门外部清理干净,进行外部检查,根据痕迹判断是否有外漏和裂纹,并查阅运行记录。
2.3 把阀门开关一次,松紧是否一致,判断阀杆是否弯曲、卡涩,置阀门于开启位置。
3 阀门解体检查3.1 拆检步骤3.1.1 用手轮将阀门摇开几圈,松开盘根压盖铰接螺栓,将填料压盖压板松活。
松盘根压盖螺母时要用专用标准扳手。
3.1.2 对于电动阀门取下电传动装置。
传动头取下后应水平放好,防止蜗轮箱内齿轮油漏入电动机里。
3.1.3 拆卸阀门框架。
a) 对于螺栓连接的截止阀,展平止动垫松开框架固定螺钉。
b) 对于丝扣连接的阀门,应用锯或剔的方法将框架与门体的焊点除去。
剔或锯时一定注意不要损坏门体和框架连接螺纹。
电动调节阀检修规程

电动调节阀检修规程
一.全厂分布情况
电动调节阀主要分布在氨法脱硫和汽机双减片区,以及除氧给水。
二.风险辨识及防范措施
三.检修注意事项
1.电动调节阀都为220v交流电源,检修时一定要断电后再作业。
2.遇到阀门卡死情况,不能盲目手动调试,要跟操作工沟通确认后在调
试,避免造成工艺问题。
3.检修时注意使用工具,避免工具伤人。
四.检修工具
万用表活动扳手梅花起子
五.检修过程
首先办理相应等级的票证,并与操作工联系确认能作业后,根据具体情况判断:
1.如果是DSC无法控制,关闭电动调节阀电源,并在现场用万用表监测,
确认无电后,将各个接头全部紧一遍,以免由于松动导致的断路,然
后可以给定一个值,然后检查有无输出信号且输出信号是否吻合,如
果不吻合就要检查控制室安全栅是否损坏,可更换一个后继续检查,
如果吻合,就可能是调节阀模块损坏。
2.如果是阀门调节到一个值就卡住,首先可以重复调试几次,观察是否
始终卡在一个值。
然后到现场,让操作工再次给个值,同时也顺着开
度方向一同手动开阀门,如果能完全打开阀门,就说明内部螺杆在某
个点卡住了,此时再让操作工重复开几次,观察是否仍然卡住不动,
如果仍然卡住就需要拆开阀门检查,如果损坏严重就需要更换。
如果
手动仍然无法打开阀门,也需要拆开阀门检查,很可能是内部螺杆链
接摩擦损坏了。
六.常见故障
1.内部螺杆老化,卡住了
2.电路板,模块损坏
3.控制线路,安全栅损坏。
调节阀检修方案
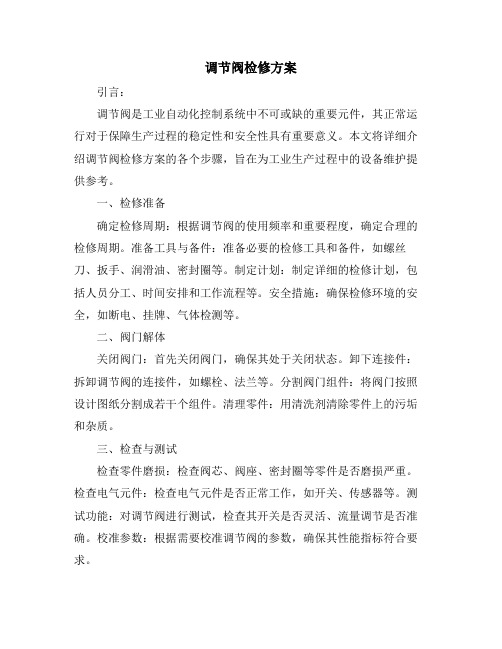
调节阀检修方案
引言:
调节阀是工业自动化控制系统中不可或缺的重要元件,其正常运行对于保障生产过程的稳定性和安全性具有重要意义。
本文将详细介绍调节阀检修方案的各个步骤,旨在为工业生产过程中的设备维护提供参考。
一、检修准备
确定检修周期:根据调节阀的使用频率和重要程度,确定合理的检修周期。
准备工具与备件:准备必要的检修工具和备件,如螺丝刀、扳手、润滑油、密封圈等。
制定计划:制定详细的检修计划,包括人员分工、时间安排和工作流程等。
安全措施:确保检修环境的安全,如断电、挂牌、气体检测等。
二、阀门解体
关闭阀门:首先关闭阀门,确保其处于关闭状态。
卸下连接件:拆卸调节阀的连接件,如螺栓、法兰等。
分割阀门组件:将阀门按照设计图纸分割成若干个组件。
清理零件:用清洗剂清除零件上的污垢和杂质。
三、检查与测试
检查零件磨损:检查阀芯、阀座、密封圈等零件是否磨损严重。
检查电气元件:检查电气元件是否正常工作,如开关、传感器等。
测试功能:对调节阀进行测试,检查其开关是否灵活、流量调节是否准确。
校准参数:根据需要校准调节阀的参数,确保其性能指标符合要求。
四、维修与更换
维修磨损零件:对磨损的阀芯、阀座、密封圈等进行修复或更换。
更换损坏件:更换损坏的电气元件和其他易损件。
涂装保护:对金属零件进行涂装保护,以防腐蚀。
参数调整:根据实际情况调整调节阀的参数,以提高其工作性能。
五、组装与调试
按图组装:按照设计图纸将分割的阀门组件重新组装起来。
安装连接件:将拆卸的连接件重新安装到调节阀上。
气动薄膜调节阀维护检修规程

气动薄膜调节阀维护检修规程1气动薄膜调节阀参数1.1 技术标准1.1.1外观零部件齐全,装配正确,紧固件不得有松动,损伤等现象,整体整洁。
1.1.2 气源压力最大值为500 KPa,额定值为250 KPa。
1.1.3输入信号范围1.1.3.1标准压力信号范围为20~100 KPa或40~200 KPa;1.1.3.2带有电/气阀门定位器时,标准信号范围为4~20mA DC;1.1.3.3两位式控制时,可在气源压力额定值内任意选取。
1.1.3.4执行机构室的密封性将设计规定的额定压力的气源通入封闭气室中,切断气源,5分钟内薄膜气室中的压力下降不得超过2.5 KPa1.1.3.5耐压强度调节阀应以1.5倍公称压力进行不少于3min的耐压试验,不应有肉眼可见的渗漏;1.1.3.6 填料函及其他连接处的密封性应保证在1.1倍公称压力下无渗漏;1.1.3.7泄露量调节阀在规定试验条件下的泄漏量应符合国家标准GB/T4213-92《气动调节阀》规定的要求。
2检查与校验2.1 外观检查按本节第1.1条要求,用肉眼观察的方法进行检查2.2 执行机构气室的密封性试验按本节1.4要求将额定压力(一般为140 KPa或250 KPa)的气源输入薄膜气室中,切断气源。
2.3 耐压强度试验按本节1.5要求,用1.5倍公称压力的室温水,在调节阀的入口方向输入阀体内,另一端封闭,使所有在运行中受压的阀腔同时承受5min的实验压力,试验期间调节阀应处于全开位置。
、2.4 填料函及其它连接处的密封性实验。
按本节1.6条要求,用1.1倍公称压力的室温水,按规定的入口方向输入调节阀的阀体,另一端密封,同时使阀杆作1~3次往复动作,持续时间应少于5min观察调节阀的填料函及上、下阀盖与阀体的连接处。
2.5 泄漏量试验按本节1.7条要求,在薄膜气室中按不同作用方式输入一定的操作气压,使调节阀关闭。
将室温水以恒定压力按规定的入口方向输入调节阀,另一端放空,用秒表和量杯测量其1min的泄露量。
气动调节阀检修规程

1 目的为了加强调节阀的维护保养和检修质量,使调节阀能长寿命、稳定实现调节作用,特制定本规程。
2 适用围适用于公司中用于生产过程自动控制的由气动薄膜执行机构和阀体组成的气动调节阀,包括一般的单座阀、双座阀、套筒阀等的维护、保养、检修。
3 调节阀的概念调节阀是自控系统中的终端现场调节仪表。
它安装在工艺管道上,调节被调介质的流量、压力,按设定要求控制工艺参数。
调节阀直接接触高温、高压、深冷、强腐蚀、高粘度、易结晶结焦、有毒等工艺流体介质,因而是最容易被腐蚀、冲蚀、气蚀、老化、损坏的仪表,往往给生产过程的控制造成困难。
因此,必须充分重视调节阀的运行维护和检修工作。
4 运行维护4.1 调节阀运行4.1.1 调节阀在投入运行前需做系统联校。
4.1.2 调节阀在工作时,前后的切断阀应全开,旁路阀(副线阀)应全关。
整个管路系统中的其他阀门应尽量开大,通常调节阀应在正常使用围(20%—80%)工作。
4.1.3 使用带手轮的调节阀应注意手轮位置指示标记。
4.1.4 调节阀在运行过程中禁调整阀杆和压缩弹簧的位置。
4.2 日常巡检4.2.1 巡检时应检查各调节阀的气源压力是否正常、气路(仪表空气管经过滤减压阀、阀门定位器至气缸各部件、各管线)的紧固件是否松动、仪表空气是否有泄漏。
4.2.2 巡检时应检查填料函及法兰连接处是否有工艺介质泄漏,压兰及阀杆连接件是否紧固,阀杆是否有重的摩擦划痕或变形。
4.2.3 巡检时需检查仪表线路的防护情况,仪表进线口密封是否良好。
4.2.4 巡检时应检查阀杆运动是否平稳,行程与输出信号是否基本对应,阀门各部件有无锈蚀,重点是阀杆、紧固件、气缸等。
4.3 专项检查4.3.1 专项检查指不是日常巡检必须进行,但随季节变化或需期性进行的检查,比如仪表空气带水情况,阀门定位器防雨情况等。
4.3.2 仪表空气带水检查4.3.2.1 在夏季雨水较多和冬季结冰时段,需择机进行仪表空气带水情况检查,因为在夏季,空气湿度大,仪表空气带水会顺空气过滤减压阀、阀门定位器能到达气缸膜室,腐蚀弹簧、损伤膜片;冬季空气凝点低,仪表空气带水会堵塞气路,造成阀门失效。
调节阀阀体维护检修规程
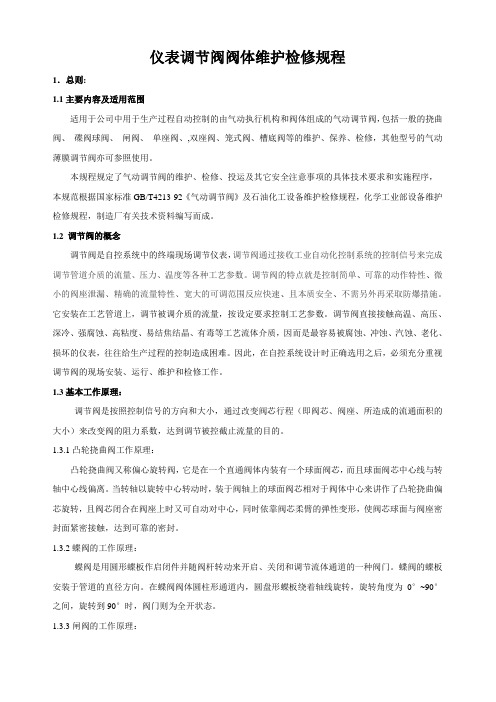
仪表调节阀阀体维护检修规程1.总则:1.1主要内容及适用范围适用于公司中用于生产过程自动控制的由气动执行机构和阀体组成的气动调节阀,包括一般的挠曲阀、碟阀球阀、闸阀、单座阀、,双座阀、笼式阀、槽底阀等的维护、保养、检修,其他型号的气动薄膜调节阀亦可参照使用。
本规程规定了气动调节阀的维护、检修、投运及其它安全注意事项的具体技术要求和实施程序,本规范根据国家标准GB/T4213-92《气动调节阀》及石油化工设备维护检修规程,化学工业部设备维护检修规程,制造厂有关技术资料编写而成。
1.2 调节阀的概念调节阀是自控系统中的终端现场调节仪表,调节阀通过接收工业自动化控制系统的控制信号来完成调节管道介质的流量、压力、温度等各种工艺参数。
调节阀的特点就是控制简单、可靠的动作特性、微小的阀座泄漏、精确的流量特性、宽大的可调范围反应快速、且本质安全、不需另外再采取防爆措施。
它安装在工艺管道上,调节被调介质的流量,按设定要求控制工艺参数。
调节阀直接接触高温、高压、深冷、强腐蚀、高粘度、易结焦结晶、有毒等工艺流体介质,因而是最容易被腐蚀、冲蚀、汽蚀、老化、损坏的仪表,往往给生产过程的控制造成困难。
因此,在自控系统设计时正确选用之后,必须充分重视调节阀的现场安装、运行、维护和检修工作。
1.3基本工作原理:调节阀是按照控制信号的方向和大小,通过改变阀芯行程(即阀芯、阀座、所造成的流通面积的大小)来改变阀的阻力系数,达到调节被控截止流量的目的。
1.3.1凸轮挠曲阀工作原理:凸轮挠曲阀又称偏心旋转阀,它是在一个直通阀体内装有一个球面阀芯,而且球面阀芯中心线与转轴中心线偏离。
当转轴以旋转中心转动时,装于阀轴上的球面阀芯相对于阀体中心来讲作了凸轮挠曲偏芯旋转,且阀芯闭合在阀座上时又可自动对中心,同时依靠阀芯柔臂的弹性变形,使阀芯球面与阀座密封面紧密接触,达到可靠的密封。
1.3.2蝶阀的工作原理:蝶阀是用圆形蝶板作启闭件并随阀杆转动来开启、关闭和调节流体通道的一种阀门。
调节阀检维修规程

第四篇执行器第一节气动薄膜调节阀1 总则1.1 主题内容与适用范围本节规程是气动薄膜调节阀的维护、检修通用规定。
适用于石化企业中用于生产过程自动控制的由气动薄膜执行机构和阀体组成的气动调节阀,包括一般的单座阀、双座阀、角型阀、套筒阀、三通阀等。
以下简称调节阀。
1.2 编写修订依据中华人民共和国国家标准GB/T4213-92《气动调节阀》;调节阀使用说明书;现场运行技术资料。
2 概述2.1 调节阀是自动系统中的终端现场调节仪表。
它安装在工艺管道上,调节被调介质的流量,按设定要求控制工艺参数。
调节阀直接接触高温、高压、深冷、强腐蚀、高粘度、易结焦结晶、有毒等工艺流体介质,因而是最容易被腐蚀、冲蚀、气蚀、老化、损坏的仪表,往往给生产过程的控制造成困难。
因此,在自控系统设计时正确选用之后,必须充分重视调节阀的现场安装、运行维护和检修工作。
3 技术标准3.1 外观:零件齐全,装备正确,紧固件不得有松动、损伤等现象,整体洁净。
3.2 气源压力:最大值为500KPa,额定值250KPa。
3.3 输入信号范围3.3.1 标准压力信号范围为20-100KPa或40-200KPa。
3.3.2 带有电/气阀门定位器时,标准电信号范围为0-10Ma DC或4-20Ma DC。
3.3.3 两位式控制时,可在气源压力额定值内任意选取。
3.4 执行机构气室的密封性将设计规定的额定压力的气源通入密封气室中,切断气源,5min时间内薄膜气室中的压力下降不得超过2.5kpa。
3.5 基本误差:不应超过表4-1-1的规定。
它用调节阀的额定行程的百分数表示。
表4-1-1 各类气动薄膜调节阀基本参数3.6 回差不应超过表4-1-1的规定。
它用调节阀的额定行程的百分数表示。
3.7 始终点偏差当输入气动薄膜执行机构中的信号为上下限时,调节阀的始终点偏差应不超过表4-1-1的规定。
它用调节阀的额定行程的百分数表示。
3.8 死区用调节阀输入信号量程的百分数表示,它应不超过3%。
第七章 仪控调节阀门校验规程

第七章仪控调节阀门校验规范第七章仪控调节阀门校验规范1 目的为规范在线使用的仪控调节阀门(气动薄膜调节阀、气动活塞式调节阀及阀门定位器)的校验工作,特制定本规范。
2 适用范围本规范适用于本公司所有在线使用的仪控调节阀门(气动薄膜调节阀、气动活塞式调节阀、电动调节阀及阀门定位器)。
3 主要内容仪控阀门在安装后投运前必须进行校验调整后方能启用。
在正常运行中校验周期一般为每年一次,若中途发现开度偏差过大,也应及时给予测试调整,以确保仪控阀门动作正常,满足工艺控制要求。
3.1 仪控阀门的检查3.1.1检查仪控阀门表面清洁,零部件齐全,无锈迹,定位器气源压力正常,反馈杆和连接件的紧固件无松动。
检查调节阀所用的气源的质量是否符合要求,气源带油雾分离系统的需进行排污。
3.1.2检查调节阀是否有泄漏现象,检查的方面包括气源管路、执行机构、填料室压盖,与工艺管道的连接等。
3.1.3 检查定位器恒流孔、喷嘴挡板、放大器是否堵塞。
3.2带非智能阀门定位器的仪控阀门校验3.2.1 常用的定位器调校步骤3.2.1.1使阀杆位于行程中点,调整定位器与反馈杠杆成90°角,并将螺钉固定;3.2.1.2将零点、量程分别置于中间位置;3.2.1.3输入4mA DC信号,使调节阀开始动作,调节零点,使零点达到要求;3.2.1.4输入20mA DC信号,看其行程是否达到要求,如没达到,则调量程,使其达到要求;3.2.1.5重复3、4两步,使零点和量程均达到要求。
3.2.2 常用调校方法不能完成校验时的解决办法自动化设备检测与校验手册3.2.2.1 常用调校方法不足在通常情况下,调零弹簧工作在线性区域,其长度的变化范围是有限的,而调量程机构其机械位置是受到限制的,因此调零弹簧长度和量程调整机构的放大系数的值就会受到限制,当调节阀的KV很大或很小时,用常用的调校方法是不可能将定位器校准的,而这种情况在实际工作中经常遇到,所以需要用其他方法来调校阀门定位器。
- 1、下载文档前请自行甄别文档内容的完整性,平台不提供额外的编辑、内容补充、找答案等附加服务。
- 2、"仅部分预览"的文档,不可在线预览部分如存在完整性等问题,可反馈申请退款(可完整预览的文档不适用该条件!)。
- 3、如文档侵犯您的权益,请联系客服反馈,我们会尽快为您处理(人工客服工作时间:9:00-18:30)。
自编维护检修规程总纲QJ/DSH 0246.001-19981。
适用范围本规程适用于独石化乙烯厂各车间生产过程检测,控制等自动化仪表设备的日常维护和检修。
2。
编写原则本规程主要以本厂的仪表设备为对象,根据国家现行规范和标准,结合仪表制造厂所提供的使用说明书和多年来的使用经验进行编写。
本规程不包括非在线使用的实验室仪器。
3。
自动化仪表设备大,中,小修标准的划分。
3。
1 大修仪表所有部件全部解体清洗,除垢,必要的部件检查并测试其性能,更换主要零部件或易损件,总装润滑,恢复外观,整体修复,总体(整机)性能试验,使其主要技术指标达到出厂要求。
3。
2 中修主要部件检查鉴定,更换修理,清扫润滑,调校。
3。
3 小修校验,调整及一般故障处理。
4。
标准仪器的选用原则:4。
1 标准仪器的准确度等级必须高于被校表准确度等级。
4。
2 标准仪器必须符合国家计量法的有关规定,经计量部门鉴定有效期使用。
5。
质量验收5。
1 仪表检修质量应符合本维护检修规程或仪表使用说明书规定的技术标准。
5。
2 仪表检修实行三级质量验收制度。
5。
2。
1 需进行质量验收的仪表,首先由检修人员自行检验合格,并填写检修记录,签字;第二,由班组的对口技术人员或班组长验收,填写验收意见,签字;第三,重要仪表应由厂或车间技术负责人验收签字。
5。
2。
2 经过更改的仪表及系统,应有明确的记录,要及时修改和收集有关资料,并验收存档。
6。
校验单的填写各规程中的表格及校验单仅为参考,最终记录以乙烯厂颁发的标准表格为准,格式可能有改变。
气缸式切断阀、调节阀通用维护检修规程1.总则1.1主题内容与运用范围1.1.1主题内容本节规程是气缸式调节阀、切断阀的维护、检修通用规定。
1.1.2适用范围气缸式执行机构一般可分为单作用有弹簧式机构, 双作用无弹簧式机构, 双作用有弹簧式机构, 本节规程适用于石化企业中用于生产过程自动控制的单/ 双作用有弹簧式气缸执行机构和阀体组成的气缸式调节阀、切断阀,包括一般的单座阀、双座阀、角阀、套筒阀等。
1.1.3编写依据中国石油化工总公司所制定的石油化工设备维护检修规程第七册<<仪表>>中的第五篇<<执行器>> ( SHSO7005- 92) ;VALTEK调节阀操作使用说明书;FISHER控制阀的的说明使用及维修;现场运行技术资料。
2.概述调节阀是自控系统的终端现场调节仪表。
它安装在工艺管道上,调节被调介质的流量,按设定要求控制工艺参数。
调节阀直接接触高温、高压、深冷、强腐蚀、高粘度、易结焦结晶、有毒等工艺流体,因而是最容易被腐蚀、冲涮、气蚀、老化、损坏的仪表,往往给生产过程的控制造成困难。
因此,在自控系统设计时正确选用之后,必须充分重视调节阀的现场安装,运行维护和检修工作。
气缸式执行机构比膜片式执行机构重量轻、体积小,与膜片式执行机构相比重心较低。
降低管线上所受动态和静态负载,而且它还具有高刚性,大推力的特点,是一种应用言广泛,且维修简单的执行器。
3.主要技术指标3.1外观零部件齐全,装配关系正确,紧固件不得有松动现象,整体洁净。
3.2气源压力30-150psi/2.8-10.3kg/cm23.3输入信号3.3.1标准压力信号范围为20-100kpa3.3.2带有电/ 气阀门定位器时,标准信号范围为4-20MA.10-50MA 3.3.3两位式控制( 切断方式) 时,可在气源压力范围内任意选取。
3.4执行机构气室的密封性加入600KPa的气压在5 分钟时间内气缸室中的压力下降不得超过2.5kp 。
3.5. 基本误差不应超过表1-1-1 的规定。
它用调节阀的额定行程的百分数表示。
始│气│ 始点│ 5 │ 1终│ ├───┼───────┼──── 点│关│ 终点│ 2.5 │ 1 偏├─╀───┼───────┼──── 差│气│ 始点│-2.5 │ 1│ ├───┼───────┼────%│开│ 终点│ 5 │ 1表1-1-13.6回差不应超过表1-1-1 规定。
它用调节阀额定行程的百分数表示。
3.7始终点偏差当输入气缸式执行机构中的信号为上下限值时,调节阀的始终点偏差应不超过表1-1-1 的规定。
它用调节的额定行程的百分数表示。
3.8死区用调节阀输入信号量程的百分数表示,它不应超过2%。
此项要求上做抽查。
3.9调节阀在安装前或阀体检修后应进行耐压强度试验,不应有渗漏。
3.10调节阀安装前或更换密封填料后应进行填料函及其它连接处的密封性试验。
应保证在公称压力下无渗漏。
3.11泄漏量调节阀在安装前或阀体检修后要进行泄漏量试验。
调节阀在规定试验条件下的泄漏量应符合要求。
4.检查与调校标准仪器:标准直流信号发生器4.1外观检查按3.1 要求,用肉眼观察的方法进行检查。
4.2执行机构气室的密封性试验按3.4 条件要求,在气源压力范围内输入气缸中,切断气源。
4.3基本误差校验按3.5 条将规定的输入信号平稳地按增大和减小方向输入气缸(或定位器),测量各点所对应的行程值,按下式计算实际“信号-行程”关系与理论关系之间的各点误差。
其最大值即为基本误差。
δi=(li-Li)/L*100%式中: δi=第i 点的误差;li= 第i 点的实际行程;Li= 第i 点理论行程;L= 调节阀的额定行程;试验点为输入信号范围的0%、25%、50%、75%、100% 五个点。
4.4回差校验按3.6 条要求,校验方法同第4.3 条,在同一输入信号所测得的正反行程的最大差值即为回差。
4.5始终点偏差校验按3. 7 条要求,将输入信号的上、下限值分别加入气缸(或定位器),测量相应的行程值,按1-1-1 式计算始终点偏差。
要特别注意到保证气开式调节阀的始点、气关式调节阀的终点在阀关位置上。
4.6死区校验按3.8 条要求,在输入信号量程的25%、50%、75%、三点上进行校验,其方法为缓慢改变(增大和减小)输入信号,直到观察出一个可察觉的行程变化(0.1mm),此点上正、反两方向的输入信号差值即为死区。
4.7耐压强度试验按3.9 条要求,用1.5 倍公称压力的室温水,在调节阀的入口方向输入阀体内,另一端封闭,使所有在运行中受压的阀腔同时承受5 分钟的试验压力。
试验期间,调节阀应处于全开位置。
4.8填料函及其它连接处的密封性试验。
按3.10 条要求,用1.1 倍公称压力的室温水,按规定的入口方向输入调节阀的阀体,另一端封闭,同时使阀杆作1-3 次往复动作,持续时间不应少于5 分钟,观察调节阀的填料函及上、下阀盖与阀体的连接处。
4.9泄漏量试验按3.11 条要求,在气缸内按不同的作用方式输入一定的操作气压,使调节阀关闭。
将温度为室温的相对恒定的水压,按规定的入口方向输入调节阀,另一端放空,用秒表和量杯测量其一分钟的泄漏量。
4.9.1试验水压p4.9.1.1双座类调节阀为400kp。
4.9.1.2单座类调节阀a. 为400kp 或小于400kp 的最大允许差压。
b. 调节阀的最大工作压差。
4.9.2泄漏量的计算公式为:4.9.2.1双座阀类Qr=5*10-3 阀的额定容量=5*10-3*c*(p/r)(1/2)*103/60(L/min) =0.16*c(L/min)(1-1-2)式中:C- 调节阀的额定流量系数(Cv=1.17C)P- 调节阀的进口水压(kg/cm2) ,此处p =400kp=4(kg/cm2)r- 试验液体的重度,g/cm3,此处水r 为1 。
4.9.2.2单座阀类Ql=10-4* 阀的额定容量=1.67*10-3*c*(p)1/2(L/min)(1-1-3)式中的c、p、r 含义同第4.9.2.1 条5.运行维护。
5.1调节阀在投入运行前应做系统联试。
5.2调节阀工作时,前后切断应全开,副线阀应全关。
整个管路系统中的其它阀门应尽量开大,通常调节阀应在正常开度范围(20 %-80 %) 内工作。
5.3使用带手轮的调节阀应注意手轮位置指示标记。
5.3.1在侧面安装的,应在中间或"自动"位置。
5.3.2在顶部安装的,应在最高位置。
5.3.3作限位用的,应在预定位置。
5.4调节阀在运行中严禁调整阀杆和压缩/ 伸长弹簧的位置。
5.5经常检查调节阀及定位器等附属设备。
5.5.1气源及输入、输出信号是否正常。
5.5.2阀杆运动是否平稳,行程与输出是否基本对应。
5.5.3连接管路是否严密不漏。
5.5.4填料函及法兰连接处有无介质外漏,检查中发现的问题要及时作技术性处理,以保证调节阀正常运行。
5.5.5定期清扫、保持整洁、特别是阀杆、定位器的反馈杆等活动部位,需要加润滑油的填料,应定时、定量加注润滑油。
5.6需在生产现场对调节阀阀杆进行解体检查时,必须经工艺车间同意后再将调节阀两边的截止阀关闭,并加紧盲板,待阀内介质降温,放空降压后方可进行。
5.7 控制阀的维护修理类别:5.7.1 保养:日常检查,及时发现异常现象,紧固松动零件5.7.2 小修:清洗检查阀杆和执行机构推杆,更换损坏附件5.7.3 中修:包括小修的内容。
研磨密封面,更换密封件5.7.4 大修:包括中修的内容。
修补阀体,修理或更换执行机构损坏零件,更换执行机构弹簧等5. 8 控制阀常见故障分析6.检修控制阀的检修流程:6.1停工检修时,在调节阀离线前,应将放空阀打开,降温、降压。
经生产装置有关人员确认可离线检修,方可检修。
6.2检修的一般程序:打标记→ (下线)→清洗→解体→零部件检修→研磨→装配→调校与试验→ (上线)→动作检查→回路联校→开车保运。
6.3打标记为保证调节阀离线检修后能正确复位,应重视打标记程序。
其手段可用与调节阀不同颜色的油漆画出,应能清晰地标明。
6.3.1调节阀阀体法兰与管道法兰的连接复位。
6.3.2阀体与上、下阀盖及其执行机构的连接复位。
6.3.4 清冼滞留在阀体腔内的某些工序前必须以水或蒸汽吹扫的方法,将调节阀被工艺介质浸渍的部件洗干净。
6.5解体6.5.1对于阀体上的连接部位(为各部紧固件),应喷洒松动剂,使解体工作省时省力。
6.5.2将阀体与气缸或执行机构分离时,应首先将执行器推杆与阀杆的连接部件松开。
6.5.3气开式调节阀须加入适当气压信号,使阀芯与阀座脱离接触后,方能旋转阀杆,使之与执行机构的推杆分离。
6.5.4每一台调节阀分解后所得的零部件应集中存放在商行塑料箱内,以防散失或碰伤。
6.6零部件检修6.6.1生锈或脏污的零部件要以合适的手段进行去锈和清洗,要注意清洁好机加面,特别要保护好阀杆、阀芯和阀座的密封面。
6.6.2重点检查部位6.6.2.1阀体:阀体的内壁和连接阀座的内螺纹处易受流体介质的腐蚀和冲蚀。
阀座:密封面和与阀体连接的外螺纹处易受到腐蚀和汽蚀。
气缸:气缸式执行机构中的弹簧一般比薄膜式执行机构的弹簧大的多,因此拆卸时一定要首先松开预紧弹簧,否则可能会造成不必要的伤害. 然后松开气缸底部的涨圈或螺栓,将活塞盘拿出,检查后更换"0" 型圈,加入气缸油,同时将上,下的密封圈更换,安装好,再进行试漏.6.6.2.3 阀芯/ 阀杆组件:阀芯的密封面和调节曲面以及导向圆柱面处均是易受腐蚀和磨损的;阀杆上部与密封填料接触亦是易受腐蚀和磨损的;还应注意检查阀芯与阀杆连接不得松动,阀杆不得弯曲(同心度要求≤ 0.05mm)。