(第六章)刻蚀讲解
蚀刻原理

蚀刻原理在氯化铜溶液中加入氨水,发生络合反应, CuCl2+4NH3→Cu(NH3)4Cl2 在蚀刻过程中,基板上面的铜被〔Cu (NH3)4〕2+络离子氧化,其蚀刻反应:Cu(NH3)4Cl2+Cu→2Cu(NH3)2Cl所生成的〔Cu(NH3)2〕1+不具有蚀刻能力,在过量的氨水和氯离子存在的情况下,能很快地被空气中的氧所氧化,生成具有蚀刻能力的〔Cu(NH3)4〕2+络离子,其再生反应如下:2Cu(NH3)2Cl+2NH4Cl+2NH3+1/2O2 →2Cu(NH3)4Cl+H2O所以在蚀刻时,应不断补加氨水和氯化铵,也称子液.Cu(NH3)2Cl 氯化二氨合铜(I) 氯化亚铜氨Cu(NH3)4Cl2 氯化四氨合铜(II) 氯化铜氨氨水少量:CuCl2 + 2 NH3H2O = Cu(OH)2↓ + 2 NH4Cl Cu2+ + 2 NH3H2O = Cu(OH)2↓ + 2NH4+ 氨水过量:CuCl2 + 4 NH3H2O = [Cu(NH3)4]Cl2 + 2 H2O Cu2+ + 4 NH3H2O =[Cu(NH3)4]2+ + 2 H2O2014-12-04 2个回答氯化铜与氨气反应?应该是在溶液中反应吧。
溶液中反应有两种情况:一种是少量氨水:CuCl2+2NH3.H2O=2NH4Cl+Cu(OH)2↓,则有蓝色沉淀生成一种是氨水过量,则生成的沉淀会与氨水进一步生成络合物[Cu(NH3)4]Cl2,沉淀又会消失,方程式为:CuCl2+ ...2014-11-28 3个回答碱性与酸性蚀刻的特点时间:2011-07-20 23:54:09点击:YM-W235碱性蚀刻液为高速、高含铜量,针对细线路特别设计的电路板蚀刻液,药液稳定,且适合各种如锡、锡铅、镍、金等抗蚀刻材料。
使明1.高稳定性,不会沉淀,维护容易2.可调控高速蚀刻速率3.高铜含量4.良好的水洗YM-W235碱性蚀刻液为高速、高含铜量,针对细线路特别设计的电路板蚀刻液,药液稳定,且适合各种如锡、锡铅、镍、金等抗蚀刻材料。
蚀刻培训讲义
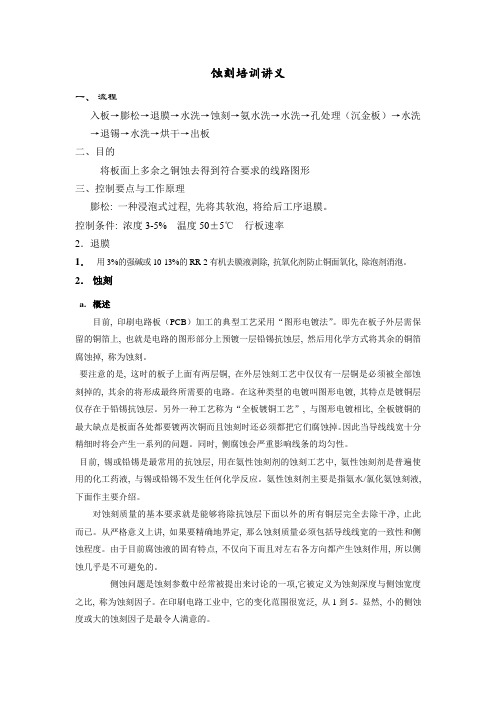
蚀刻培训讲义一、流程入板→膨松→退膜→水洗→蚀刻→氨水洗→水洗→孔处理(沉金板)→水洗→退锡→水洗→烘干→出板二、目的将板面上多余之铜蚀去得到符合要求的线路图形三、控制要点与工作原理膨松: 一种浸泡式过程, 先将其软泡, 将给后工序退膜。
控制条件: 浓度3-5% 温度50±5℃行板速率2.退膜1.用3%的强碱或10-13%的RR-2有机去膜液剥除, 抗氧化剂防止铜面氧化, 除泡剂消泡。
2.蚀刻a.概述目前, 印刷电路板(PCB)加工的典型工艺采用“图形电镀法”。
即先在板子外层需保留的铜箔上, 也就是电路的图形部分上预镀一层铅锡抗蚀层, 然后用化学方式将其余的铜箔腐蚀掉, 称为蚀刻。
要注意的是, 这时的板子上面有两层铜, 在外层蚀刻工艺中仅仅有一层铜是必须被全部蚀刻掉的, 其余的将形成最终所需要的电路。
在这种类型的电镀叫图形电镀, 其特点是镀铜层仅存在于铅锡抗蚀层。
另外一种工艺称为“全板镀铜工艺”, 与图形电镀相比, 全板镀铜的最大缺点是板面各处都要镀两次铜而且蚀刻时还必须都把它们腐蚀掉。
因此当导线线宽十分精细时将会产生一系列的问题。
同时, 侧腐蚀会严重影响线条的均匀性。
目前, 锡或铅锡是最常用的抗蚀层, 用在氨性蚀刻剂的蚀刻工艺中, 氨性蚀刻剂是普遍使用的化工药液, 与锡或铅锡不发生任何化学反应。
氨性蚀刻剂主要是指氨水/氯化氨蚀刻液, 下面作主要介绍。
对蚀刻质量的基本要求就是能够将除抗蚀层下面以外的所有铜层完全去除干净, 止此而已。
从严格意义上讲, 如果要精确地界定, 那么蚀刻质量必须包括导线线宽的一致性和侧蚀程度。
由于目前腐蚀液的固有特点, 不仅向下而且对左右各方向都产生蚀刻作用, 所以侧蚀几乎是不可避免的。
侧蚀问题是蚀刻参数中经常被提出来讨论的一项,它被定义为蚀刻深度与侧蚀宽度之比, 称为蚀刻因子。
在印刷电路工业中, 它的变化范围很宽泛, 从1到5。
显然, 小的侧蚀度或大的蚀刻因子是最令人满意的。
刻蚀介绍.

聚合物(Polymer)的形成
聚合物是在刻蚀过程中由光刻胶中的碳并与刻蚀 气体和刻蚀生成物结合在一起而形成的;能否形 成侧壁聚合物取决于所使用的刻蚀气体类型。 聚合物的缺点:聚合物在刻蚀结束后难以去除;
在反应室的任何地方都有聚合物,影响纵向的刻
蚀速率,增加反应室的清洗工作。
8. 等离子体诱导损伤 等离子体诱导损伤有两种情况:
干法刻蚀的优点(与湿法腐蚀比)
1. 刻蚀剖面各向异性,非常好的侧壁剖面控制 2. 好的CD控制 3. 最小的光刻胶脱落或粘附问题 4. 好的片内、片间、批次间的刻蚀均匀性 5. 化学品使用费用低
干法刻蚀的缺点(与湿法腐蚀比)
1. 对下层材料的刻蚀选择比较差 2. 等离子体诱导损伤 3. 设备昂贵
光伏发电技术基础
山东理工职业学院
第六章
刻蚀
6.1 引 言
刻蚀的概念: 用化学或物理的方法有选择地去除硅片表面层材料的 工艺过程称为刻蚀。 刻蚀示意图:
Photoresist mask
Film to be etched
Photoresist mask
Protected film
(a) Photoresist-patterned substrate
(a)
4. 选择比 选择比:指在同一刻蚀条件下,刻蚀一种材料对另 一种材料的刻蚀速率之比。 高选择比: 意味着只刻除想要刻去的膜层材料,而 对其下层材料和光刻胶不刻蚀。 SiO2对光刻胶的选择比=(ΔTsio2/t1)/(ΔT胶/t1)b)t1时刻
5. 均匀性 刻蚀均匀性是指刻蚀速率在整个硅片或整批硅片上 的一致性情况。非均匀性刻蚀会产生额外的过刻蚀。 ARDE效应-微负载效应:Aspect Ratio Dependence Etching
蚀刻基础知识
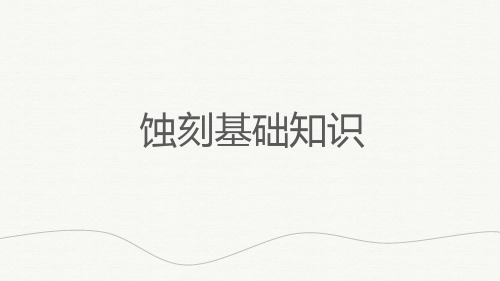
等离子体
等离子体
Plasma : plasma叫等离子体。 众所周知,固体,液体和气体是物质的三种常见状态。我们可以通过增加或减少能量 (例如加热/冷却)在两种状态之间移动。如果我们继续增加足够的能量,气体分子将被 电离(失去一个或多个电子),并因此携带净正电荷。如果将足够多的分子离子化, 以影响气体的整体电学特性,则该结果称为等离子体。因此,等离子通常被称为物质 的第四态。
刻蚀速率=(刻蚀前厚度-刻蚀后厚度)/刻蚀时间 问题:如果热氧化层的厚度为5000A,经过30s等离子体刻蚀后,厚度变为2400A,求刻蚀 速率。 答:刻蚀速率=(5000A-2400A)/0.5min=2600A/0.5min=5200A/min
蚀刻基础名词解释
➢ 蚀刻选择比:图形化刻蚀通常包含三种材料:光刻胶、被刻蚀的薄膜及衬底。刻蚀过 程中,这三种材料都会受刻蚀剂的化学反应或等离子体刻蚀中离子轰击的影响。不 同材料之间的刻蚀速率差就是所谓的选择性。
蚀刻基础概念➢ 蚀刻的分类:湿蚀刻、干法蚀刻➢ 湿法蚀刻:湿法蚀刻是用含有蚀刻化学物质的溶液蚀刻晶圆,依靠化学反应去除晶 圆表面上的材料,不过这种蚀刻是一种各向同性蚀刻。湿法蚀刻需要有较高的蚀刻 选择比,同时湿法蚀刻需要有干燥步骤,这也增加了图形坍塌的风险。
➢ 干法蚀刻:干法蚀刻是采用等离子体进行进行蚀刻,干法蚀刻通常采用蚀刻气体生 成等立体,在对晶圆表面进行蚀刻,形成特定的形状,干法蚀刻一般是化学蚀刻和 物理轰击形成的。物理轰击可以形成特定垂直的图案
等离子体相关概念
➢ 气体平均分子自由程的影响因素: 1、压力越小,气体分子越少,平均分子自由程越长
2、气体分子多时,平均自由程短
等离子体相关概念
➢ 气体平均分子自由程一般可以按以下公式计算
刻蚀培训
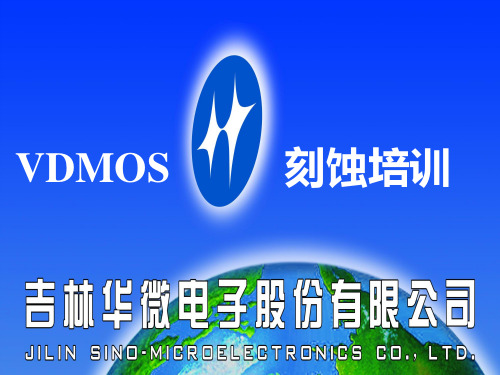
2013-8-9 17
当刻蚀气体被通入刻蚀反应腔中,在射频电场的作用下产生等离子体辉 光放电,反应气体分解成各种中性的化学活性基团,分子、电子、离子; 由于电子和离子的质量不同使得质量较轻的电子能够响应射频电场的变 化而离子却不能,正是这种差异在电极上产生负偏压 Vdc(Negative DC bias) ,离子在负偏压的加速下轰击硅片表面形成反应离子刻蚀;一个持 续的干法刻蚀必须要满足这些条件:在反应腔内有源源不断的自由基团; 硅片必须靠等离子体足够近以便反应基团可以扩散到其表面;反应物应 被硅片表面吸附以持续化学反应;挥发性的生成物应可从硅片表面解吸 附并被抽出反应腔。上面的任一种条件末达到刻蚀过程都会中断。刻蚀 的具体过程可描述为如下六个步骤: 1. 刻蚀物质的产生;射频电源施加在一个充满刻蚀 气体的反应腔上,通 过等离子体辉光放电产生电子、离子、活性反应基团。 2. 刻蚀物质向硅片表面扩散; 3. 刻蚀物质吸附在硅片表面上; 4. 在离子轰击下刻蚀物质和硅片表面被刻蚀材料发生反应; 5. 刻蚀反应副产物在离子轰击下解吸附离开硅片表面; 6. 挥发性刻蚀副产物和其它未参加反应的物质被真空泵抽出反应腔。
2013-8-9 8
SiO2湿法腐蚀
金属湿法腐蚀
金属旋转腐蚀: 设备:SPW-612-A,要改造成6寸的 TEMP:53±1℃ 腐蚀液:H3PO4:HNO3:HAC:H2O=80:5:5:10 工艺程序:
ITEM/STEP N T C V unit RPM sec 喷液 9.6 0 1 600 166 1 3 2 700 5 0 3 800 168 1 4 900 5 0 5 60 5 6
2013-8-9
19
(第六章)刻蚀全解

6.2 刻蚀参数
为了复制硅片表面材料上的掩膜图形,刻蚀必须满
足一些特殊的要求,包括以下几个刻蚀参数。
刻蚀参数
1. 刻蚀速率 2. 刻蚀剖面 3. 刻蚀偏差 4. 选择比 5. 均匀性 6. 残留物 7. 聚合物 8. 等离子体诱导损伤 9. 颗粒沾污和缺陷
1. 刻蚀速率 刻蚀速率是指刻蚀过程中去除硅片表面材料的速度。 刻蚀速率=ΔT / t (Å/min) 其中,ΔT=去掉的材料厚度( Å 或 μm) t=刻蚀所用时间(min)
干法刻蚀过程
1. 刻蚀气体进入反应腔 2. RF电场使反应气体分解电离 3. 高能电子、离子、原子、自由基等结合产生等离子体 4. 反应正离子轰击表面-各向异性刻蚀(物理刻蚀) 5. 反应正离子吸附表面 6. 反应元素(自由基和反应原子团)和表面膜的表面反 应-各向同性刻蚀(化学刻蚀) 7. 副产物解吸附 8. 副产物去除
介质的干法刻蚀
1. 氧化硅的刻蚀 工艺目的:刻蚀氧化硅通常是为了制作接触孔和通孔 刻蚀工艺
1)刻蚀气体:两种(CF4+H2+Ar+He)
或(CHF3 +Ar+He)
2)刻蚀机理:物理和化学刻蚀,物理溅射离子:Ar+、 CF3+等,CF3是刻蚀SiO2的主要活性基,加入H2后以 HF的形式除去一些腐蚀Si的活性基(F原子)提高对 下层Si的选择比,He为稀释剂改善刻蚀均匀性。
等离子体干法刻蚀系统的基本部件包括:发生刻蚀 反应的反应腔、一个产生等离子体的射频电源、气 体流量控制系统、去除刻蚀生成物和气体的真空系 统。 干法等离子体反应器的类型: 圆桶式等离子体反应器;顺流刻蚀系统(化学作用) 离子铣 (物理作用) 平板反应器;三级平面反应器;反应离子刻蚀 (RIE);高密度等离子体刻蚀机(物理+化学作用)
刻蚀相关知识点总结

刻蚀相关知识点总结刻蚀技术主要分为湿法刻蚀和干法刻蚀两种。
湿法刻蚀是在溶液中通过化学反应去除材料表面的工艺,而干法刻蚀是在气相中通过物理或化学反应去除材料表面的工艺。
下面将详细介绍刻蚀的相关知识点。
一、刻蚀的基本原理1. 湿法刻蚀原理湿法刻蚀是利用化学溶液对材料表面进行腐蚀或溶解的工艺。
湿法刻蚀的原理是在溶液中加入具有特定功能的化学试剂,使其与被刻蚀物质发生化学反应,从而去除材料表面的部分物质。
湿法刻蚀通常可以实现较高的刻蚀速率和较好的表面质量,但需要考虑溶液中的成分和温度对环境的影响。
2. 干法刻蚀原理干法刻蚀是利用气相中的等离子体或化学反应对材料表面进行腐蚀或清除的工艺。
干法刻蚀的原理是在高能离子束或化学气体的作用下,使被刻蚀物质表面发生物理或化学反应,从而去除材料表面的部分物质。
干法刻蚀通常可以实现更高的加工精度和更好的表面质量,但需要考虑设备的复杂性和成本的影响。
二、刻蚀的工艺参数1. 刻蚀速率刻蚀速率是刻蚀过程中单位时间内去除的材料厚度,通常以单位时间内去除的厚度为单位。
刻蚀速率的选择需要综合考虑刻蚀材料的性质、刻蚀条件、刻蚀设备和加工要求等因素。
2. 刻蚀选择性刻蚀选择性是指在多种材料叠加或混合结构中选择性地去除某一种材料的能力。
刻蚀选择性的选择需要考虑被刻蚀材料和其它材料之间的化学反应性和物理性质的差异,以实现精确的刻蚀。
3. 刻蚀均匀性刻蚀均匀性是指在整个刻蚀过程中去除材料的厚度分布情况。
刻蚀均匀性的选择需要考虑刻蚀设备和刻蚀条件对被刻蚀物质的影响,以实现均匀的刻蚀。
4. 刻蚀深度控制刻蚀深度控制是指在整个刻蚀过程中去除材料的深度分布情况。
刻蚀深度控制的选择需要综合考虑刻蚀设备和刻蚀条件对被刻蚀物质的影响,以实现精确的刻蚀深度。
5. 刻蚀环境控制刻蚀环境控制是指在整个刻蚀过程中对刻蚀环境(如溶液中的成分、气相中的气体、温度和压力等)的控制。
刻蚀环境控制的选择需要考虑被刻蚀材料的特性和加工的要求,以实现良好的刻蚀效果。
蚀刻详解

c.
拱形 Kapton5 p0 Q4 z; C2 I, x8 k4 y, h
Kapton 难以应用
最佳拱高难以达到
对糊胶敏感
d. 拱形 HAA
最佳拱高难以达到
对糊胶敏感 0 W' Z( y- q0 ^) e
对聚合物淀积敏感
e.
拱形—刻槽 HAA3 l3 \+ y: h9 s" a% ^6 |6 h6 y
到证明。所有的高 clamp 漏率并不说明 clamp 有问题。Edge(硅片边缘),下电极,硅片对 中和硅片的不同都影响 clamp 的漏率。
# ~3 T2 D- l: u' {% j0 g
8. Clamp 降压 加工后氦气冷却区域必须在 clamp 升起前降压。) `" b/ @* B! | 在 4500 或者配有低于室温电极的反应室内,clamp 只有在排除反应室内剩余蚀刻气体后才
同心圆印痕的要求:4 K& j1 _- z) v7 U" w I
硅片对中性良好 9 v3 w0 V+ X- k/ R. N7 K, M! _7 ` clamp 尺寸合适 @/ z% Z; M7 P2 i+ e 差的 clamp 印痕常常伴随着差的蚀刻速率均匀性或者产生糊胶。0 l$ N! X6 p- B8 k9 A/ x 通常,反应室关闭后 clamp 应当定中心,这是在反应室内无硅片的情况下抽真空后通过多次
污硅片。7 |! Y, K1 E3 c+ u6 x c. VESPEL(Insert)$ A. ?+ |/ ^& R% d! S8 z 迄今为止,大多数对于 VESPEL clamp 的尝试都不令人满意,VESPEL 在某些工艺条件下会变
- 1、下载文档前请自行甄别文档内容的完整性,平台不提供额外的编辑、内容补充、找答案等附加服务。
- 2、"仅部分预览"的文档,不可在线预览部分如存在完整性等问题,可反馈申请退款(可完整预览的文档不适用该条件!)。
- 3、如文档侵犯您的权益,请联系客服反馈,我们会尽快为您处理(人工客服工作时间:9:00-18:30)。
End of etch
2. 刻蚀剖面
刻蚀剖面是指被刻蚀图形的侧壁形状 两种基本的刻蚀剖面: 各向同性和各向异性刻蚀剖面
Isotropic etch - etches in all directions at the same rate
Resist
Film Substrate
湿法各向同性化学腐蚀
Anisotropic etch - etches in only one direction
Resist Film Substrate
具有垂直刻蚀剖面的 各向异性刻蚀
湿法刻蚀和干法刻蚀的侧壁剖面
刻蚀类型 侧壁剖面 湿法腐蚀 各向同性
示意图
各向同性(与设备和参数有关)
干法刻蚀
各向异性 (与设备和参数有关) 各向异性– 锥形
第六章 刻蚀
6.1 引 言
刻蚀的概念: 用化学或物理的方法有选择地去除硅片表面层材料的 工艺过程称为刻蚀。
刻蚀示意图:
Photoresist mask
Photoresist
Film
mask
to be etched
Protected film
(a) Photoresist-patterned substrate
干法刻蚀的缺点(与湿法腐蚀比) 1. 对下层材料的刻蚀选择比较差 2. 等离子体诱导损伤 3. 设备昂贵
干法刻蚀过程
1. 刻蚀气体进入反应腔 2. RF电场使反应气体分解电离 3. 高能电子、离子、原子、自由基等结合产生等离子体 4. 反应正离子轰击表面-各向异性刻蚀(物理刻蚀) 5. 反应正离子吸附表面 6. 反应元素(自由基和反应原子团)和表面膜的表面反
③达到一定的负电荷数量后电子会被电极排斥,产生 一个带正离子电荷的暗区(即离子壳层);
④等离子体相对于接地电极产生正电势电位。电源电 极自偏置电压的大小取决于RF电压的幅度、频率和 上下电极面积的比值。
= ΔTsio2/ΔT胶
(a)0时刻
(b)t1时刻
5. 均匀性 刻蚀均匀性是指刻蚀速率在整个硅片或整批硅片上 的一致性情况。非均匀性刻蚀会产生额外的过刻蚀。
ARDE效应-微负载效应:Aspect Ratio Dependence Etching
Emax:最大刻蚀速率 Emin:最小刻蚀速率 Eave:平均刻蚀速率
应-各向同性刻蚀(化学刻蚀)
7. 副产物解吸附 8. 副产物去除
干法刻蚀过程 硅片的等离子体刻蚀过程图
刻蚀作用
等离子体的电势分布
①当刻蚀机电极加上射频功率后,反应气体电离形成 辉光放电的等离子体;
②在正负半周的射频电压作用下,快速运动的电子离 开等离子体轰击上下电极,使接电源的电极产生一 个相对地为负的自偏置直流电压;
✓ 湿法刻蚀:把要腐蚀的硅片放在化学腐蚀液里去除 表面层材料的工艺过程。大于3微米
按被刻蚀的材料分:金属刻蚀、介质刻蚀、硅刻蚀 有图形刻蚀和无图形刻蚀
6.2 刻蚀参数
为了复制硅片表面材料上的掩膜图形,刻蚀必须满 足一些特殊的要求,包括以下几个刻蚀参数。
刻蚀参数 1. 刻蚀速率 2. 刻蚀剖面 3. 刻蚀偏差 4. 选择比 5. 均匀性 6. 残留物 7. 聚合物 8. 等离子体诱导损伤 9. 颗粒沾污和缺陷
✓ 聚合物是在刻蚀过程中由光刻胶中的碳并与刻蚀 气体和刻蚀生成物结合在一起而形成的;能否形 成侧壁聚合物取决于所使用的刻蚀气体类型。
✓ 聚合物的缺点:聚合物在刻蚀结束后难以去除; 在反应室的任何地方都有聚合物,影响纵向的刻 蚀速率,增加反应室的清洗工作。
8. 等离子体诱导损伤 等离子体诱导损伤有两种情况: 1)等离子体在MOS晶体管栅电极产生陷阱电荷引 起薄栅氧化硅的击穿。 2)带能量的离子对暴露的栅氧化层或双极结表面 上的氧化层进行轰击,使器件性能退化。
Resist
Film
Undercut
Overetch
Resist Film
Substrate (a)
Substrate (b)
4. 选择比 选择比:指在同一刻蚀条件下,刻蚀一种材料对另
一种材料的刻蚀速率之比。 高选择比: 意味着只刻除想要刻去的膜层材料,而
对其下层材料和光刻胶不刻蚀。 SiO2对光刻胶的选择比=(ΔTsio2/t1)/(ΔT胶/t1)
硅槽
湿法刻蚀是各向同性腐蚀, 干法刻蚀有各向同性腐蚀,也
不能实现图形的精确转移, 有各向异性腐蚀。各向异性腐
一般用于特征尺寸较大的
蚀能实现图形的精确转移,是
情况(≥3μm) 。
集成电路刻蚀工艺的主流技术。
3. 刻蚀偏差
刻蚀偏差是指刻蚀以后线宽或关键尺寸的变化 刻蚀偏差=Wa-Wb
Wb
Wa
Bias
(b) Substrate after etch
6.1 引 言
刻蚀的工艺目的: 把光刻胶图形精确地转移到硅片上,最后达到复制 掩膜版图形的目的。它是在硅片上复制图形的最后 主要图形转移工艺。
刻蚀工艺分类:干法刻蚀和湿法刻蚀
✓ 干法刻蚀:把要刻蚀的硅片放在具有反应气体的等 离子体真空腔中去除表面层材料的工艺过程。亚微 米
9. 颗粒沾污 颗粒沾污和缺陷由等离子体产生,是刻蚀中经常 遇到的问题,应尽量减少。
列举刻蚀的9个重要参数? 思考:残留物和颗粒沾污的区别?
6.3 干法刻蚀
干法刻蚀的优点(与湿法腐蚀比) 1. 刻蚀剖面各向异性,非常好的侧壁剖面控制 2. 好的CD控制 3. 最小的光刻胶脱落或粘附问题 4. 好的片内、片间、批次间的刻蚀均匀性 5. 化学品使用费用低
微负载效应
6. 残留物 刻蚀残留物是刻蚀以后留在硅片表面不想要的材料。
残留物的去除:湿法去胶时去除
7. 聚合物 聚合物的形成有时是有意的,是为了在刻蚀图形的 侧壁上形成抗腐蚀膜从而防止横向刻蚀,这样能形 成高的各向异性图形,增强刻蚀的方向性,从而实 现对图形关键尺寸的良好控制。
✓ 聚合物(Polymer)的形成
1. 刻蚀速率
刻蚀速率是指刻蚀过程中去除硅片表面材料的速度。 刻蚀速率=ΔT / t (Å/min)
其中,ΔT=去掉的材料厚度( Å 或 μm) t=刻蚀所用时间(min)T = chan来自e in thickness T
光刻胶 被刻蚀材料
t = elapsed time during etch
Start of etch