生产工艺英文版
生产工艺的英文
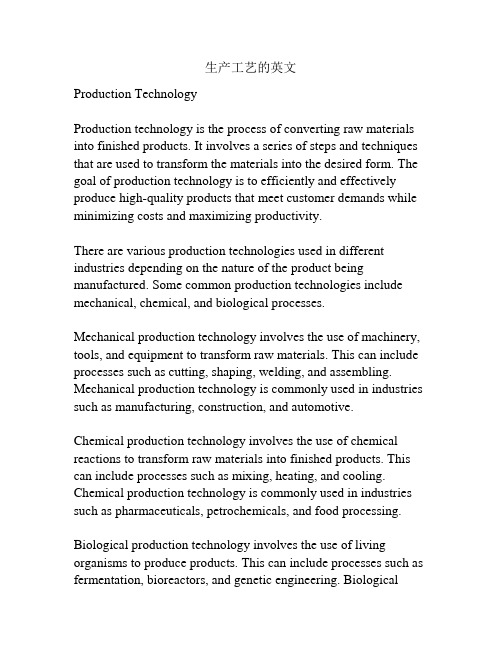
生产工艺的英文Production TechnologyProduction technology is the process of converting raw materials into finished products. It involves a series of steps and techniques that are used to transform the materials into the desired form. The goal of production technology is to efficiently and effectively produce high-quality products that meet customer demands while minimizing costs and maximizing productivity.There are various production technologies used in different industries depending on the nature of the product being manufactured. Some common production technologies include mechanical, chemical, and biological processes.Mechanical production technology involves the use of machinery, tools, and equipment to transform raw materials. This can include processes such as cutting, shaping, welding, and assembling. Mechanical production technology is commonly used in industries such as manufacturing, construction, and automotive.Chemical production technology involves the use of chemical reactions to transform raw materials into finished products. This can include processes such as mixing, heating, and cooling. Chemical production technology is commonly used in industries such as pharmaceuticals, petrochemicals, and food processing. Biological production technology involves the use of living organisms to produce products. This can include processes such as fermentation, bioreactors, and genetic engineering. Biologicalproduction technology is commonly used in industries such as biotechnology, agriculture, and food production.Regardless of the specific production technology used, there are several key steps involved in the production process. These steps include:1. Planning: This involves determining the product specifications, production volume, and scheduling of production activities.2. Sourcing: This involves acquiring the necessary raw materials, equipment, and resources needed for production.3. Processing: This involves converting the raw materials into finished products using the appropriate production technology.4. Quality Control: This involves inspecting and testing the products to ensure they meet quality standards.5. Packaging: This involves packaging the finished products in a suitable manner for storage and transportation.6. Distribution: This involves delivering the finished products to customers or retailers.7. Maintenance: This involves maintaining the production equipment and facilities to ensure their optimal performance.In addition to these steps, continuous improvement and innovation are also important aspects of production technology. This involvesconstantly evaluating and improving the production processes to increase efficiency, reduce waste, and improve product quality. Overall, production technology plays a crucial role in the manufacturing industry. It enables businesses to efficiently produce high-quality products that meet customer demands. By utilizing the appropriate production technology and continuously improving the production processes, businesses can achieve higher productivity, lower costs, and ultimately, greater success.。
蒸谷米生产工艺流程英文版

蒸谷米生产工艺流程英文版The production process of steamed glutinous rice includes several key steps.Firstly, the raw glutinous rice needs to be cleaned thoroughly to remove any impurities or foreign objects. This is an important step to ensure the quality and safety of the final product.After cleaning, the rice is soaked in water for a period of time to allow it to absorb moisture. This soaking process is crucial for achieving the desired texture and consistency of the steamed rice.Once the rice has been properly soaked, it is transferred to a steaming vessel where it is cooked under high temperature and pressure. This steaming process is essential for gelatinizing the starches in the rice, resulting in the characteristic sticky and chewy texture of glutinous rice.After steaming, the glutinous rice is spread out to cool and dry. This step allows excess moisture to evaporate, further enhancing the texture and shelf life of the final product.Once the rice has cooled and dried sufficiently, it can be packaged and stored for distribution and sale. Proper packaging is important for preserving the quality of the steamed glutinous rice and protecting it from contamination.In addition to these primary steps, quality control measures are also implemented throughout the production process to ensure that the steamed glutinous rice meets food safety and quality standards.Overall, the production of steamed glutinous rice involves a series of carefully controlled and coordinated processes to produce a safe, high-quality, and delicious final product.。
生产工艺规程 英文

生产工艺规程英文Production Process Specification.Introduction.The Production Process Specification (PPS) is a crucial document that outlines the step-by-step procedures, methods, and requirements for manufacturing a product. It ensures consistency, quality, and safety in the production process, meeting both customer and industry standards. This document serves as a roadmap for production teams, guiding them through every stage of the manufacturing process.Importance of Production Process Specification.A PPS is essential for any manufacturing business as it:1. Ensures Quality: By defining specific methods and parameters, it ensures that the final product meets the required quality standards.2. Improves Efficiency: By providing a clear roadmap, it helps in reducing wasted time, resources, and effort.3. Enhances Safety: It ensures that all safety regulations and best practices are followed, minimizing the risk of accidents or injuries.4. Facilitates Training: Serves as a training manualfor new employees, providing them with a comprehensive understanding of the production process.5. Promotes Consistency: Ensures that all products are manufactured to the same high standards, maintaining consistency across batches.Components of a Production Process Specification.A PPS typically includes the following components:1. Process Flow Diagram: A visual representation of the entire production process, outlining the sequence ofoperations and the interaction between different departments.2. Raw Materials Specification: Details of the raw materials required, including their quality standards, suppliers, and storage requirements.3. Equipment and Machinery Specification: Specifies the type, capacity, and maintenance requirements of the equipment and machinery used in the production process.4. Operating Procedures: Detailed step-by-step instructions for each operation in the production process, including the methods, techniques, and parameters to be followed.5. Quality Control Measures: Details of the quality checks, tests, and inspections to be performed during and after the production process to ensure product quality.6. Safety Precautions: Guidelines for ensuring the safety of employees, equipment, and the environment duringthe production process.7. Training Requirements: Specifies the training and qualifications required for employees involved in the production process.8. Documentation and Record-Keeping: Details of the documentation and record-keeping requirements, including production logs, quality inspection reports, and maintenance records.Development of a Production Process Specification.Developing a PPS involves the following steps:1. Identifying the Need: Understanding the product's requirements, target market, and industry standards.2. Gathering Information: Collecting data on raw materials, equipment, and processes used in similar products.3. Designing the Process: Creating a detailed process flow diagram, outlining the sequence of operations and interactions between departments.4. Defining Operating Procedures: Developing step-by-step instructions for each operation, including methods, techniques, and parameters.5. Identifying Quality Control Measures: Determining the quality checks, tests, and inspections to be performed during and after production.6. Identifying Safety Precautions: Outlining the safety guidelines to be followed by employees and measures to ensure the safety of equipment and the environment.7. Defining Training Requirements: Specifying the training and qualifications required for employees involved in the production process.8. Documenting and Updating: Documenting the PPS in a format that is easy to understand and update as needed.Conclusion.A Production Process Specification is a crucial document for any manufacturing business. It ensures consistency, quality, and safety in the production process, meeting both customer and industry standards. By defining specific methods, parameters, and requirements, it guides production teams through every stage of the manufacturing process, ensuring that the final product meets the desired quality and safety standards.。
生产工艺 英文
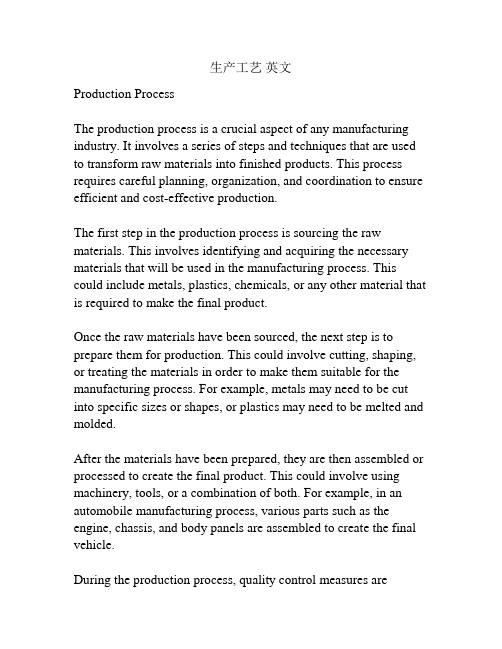
生产工艺英文Production ProcessThe production process is a crucial aspect of any manufacturing industry. It involves a series of steps and techniques that are used to transform raw materials into finished products. This process requires careful planning, organization, and coordination to ensure efficient and cost-effective production.The first step in the production process is sourcing the raw materials. This involves identifying and acquiring the necessary materials that will be used in the manufacturing process. This could include metals, plastics, chemicals, or any other material that is required to make the final product.Once the raw materials have been sourced, the next step is to prepare them for production. This could involve cutting, shaping, or treating the materials in order to make them suitable for the manufacturing process. For example, metals may need to be cut into specific sizes or shapes, or plastics may need to be melted and molded.After the materials have been prepared, they are then assembled or processed to create the final product. This could involve using machinery, tools, or a combination of both. For example, in an automobile manufacturing process, various parts such as the engine, chassis, and body panels are assembled to create the final vehicle.During the production process, quality control measures areimplemented to ensure that each product meets the required standards. This could involve inspecting and testing the products at various stages of production. Any defects or issues that are identified are addressed and corrected before the products are sent for final inspection.Once the products have been manufactured, they are then packaged and prepared for distribution. This involves placing the products into appropriate containers, such as boxes or bags, and labeling them with information such as the product name, quantity, and barcode. They are then stored in a warehouse until they are ready to be shipped to the customers.The final step in the production process is distribution. This involves coordinating the transportation and delivery of the finished products to the customers. This could be done through various means, such as using trucks, ships, or planes, depending on the location and quantity of the products.In conclusion, the production process is a complex and essential part of any manufacturing industry. It involves sourcing raw materials, preparing them for production, assembling or processing them, implementing quality control measures, packaging the products, and distributing them to customers. By carefully planning and managing each step of the process, manufacturers can ensure efficient and cost-effective production.。
生产工艺英文文案
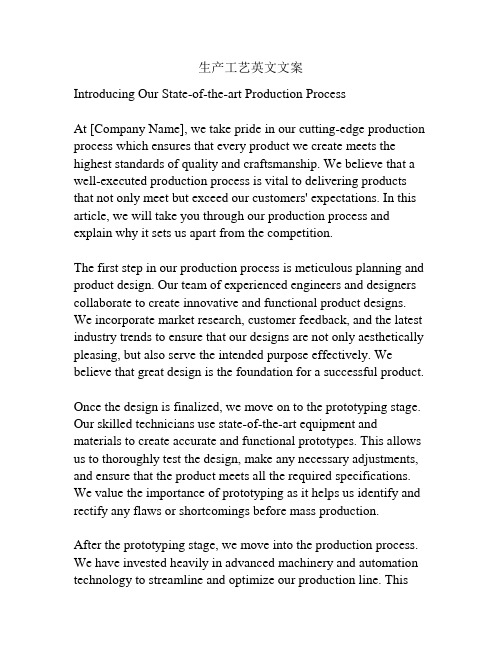
生产工艺英文文案Introducing Our State-of-the-art Production ProcessAt [Company Name], we take pride in our cutting-edge production process which ensures that every product we create meets the highest standards of quality and craftsmanship. We believe that a well-executed production process is vital to delivering products that not only meet but exceed our customers' expectations. In this article, we will take you through our production process and explain why it sets us apart from the competition.The first step in our production process is meticulous planning and product design. Our team of experienced engineers and designers collaborate to create innovative and functional product designs. We incorporate market research, customer feedback, and the latest industry trends to ensure that our designs are not only aesthetically pleasing, but also serve the intended purpose effectively. We believe that great design is the foundation for a successful product.Once the design is finalized, we move on to the prototyping stage. Our skilled technicians use state-of-the-art equipment and materials to create accurate and functional prototypes. This allows us to thoroughly test the design, make any necessary adjustments, and ensure that the product meets all the required specifications. We value the importance of prototyping as it helps us identify and rectify any flaws or shortcomings before mass production.After the prototyping stage, we move into the production process. We have invested heavily in advanced machinery and automation technology to streamline and optimize our production line. Thisenables us to achieve high levels of precision and efficiency, resulting in consistent and reliable product quality. Our production process also emphasizes strict quality control measures at every stage to identify and eliminate any defects or deviations from the specifications.To further enhance the quality of our products, we follow rigorous testing procedures. Our dedicated quality assurance team conducts thorough performance, endurance, and reliability tests to ensure that our products can withstand the most demanding conditions. We understand that our customers rely on our products in critical applications, and we are committed to delivering products that they can trust and depend on.In addition to prioritizing quality, we also value sustainability and environmental responsibility. We have implemented eco-friendly measures in our production process, such as reducing waste, energy, and water consumption. We strive to minimize our carbon footprint and contribute to building a more sustainable future.At [Company Name], our production process is not just about creating products; it is about creating value for our customers. We utilize the latest technology, industry best practices, and a highly skilled workforce to ensure that every product we produce is of exceptional quality, durability, and functionality. We are continuously improving and evolving our production process to stay ahead in an ever-changing market. Trust us to deliver products that will delight and exceed your expectations.。
包包生产工艺流程英文版
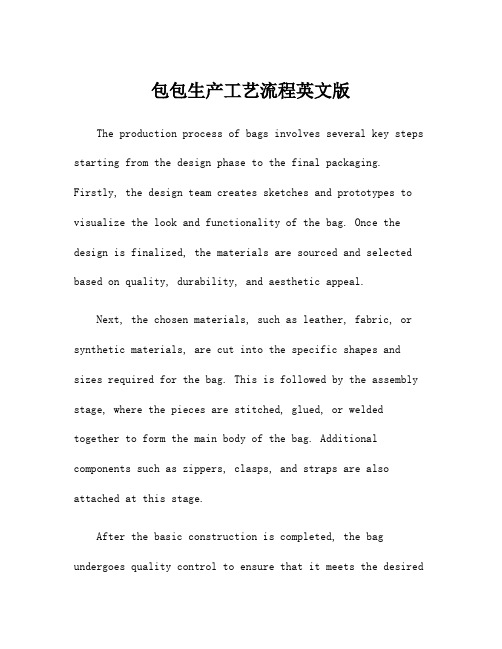
包包生产工艺流程英文版The production process of bags involves several key steps starting from the design phase to the final packaging. Firstly, the design team creates sketches and prototypes to visualize the look and functionality of the bag. Once the design is finalized, the materials are sourced and selected based on quality, durability, and aesthetic appeal.Next, the chosen materials, such as leather, fabric, or synthetic materials, are cut into the specific shapes and sizes required for the bag. This is followed by the assembly stage, where the pieces are stitched, glued, or welded together to form the main body of the bag. Additional components such as zippers, clasps, and straps are also attached at this stage.After the basic construction is completed, the bag undergoes quality control to ensure that it meets the desiredstandards in terms of stitching, alignment, and overall appearance. Any necessary adjustments or repairs are made before moving on to the finishing stage.During the finishing stage, the bag is cleaned, polished, and treated with protective coatings to enhance itsdurability and appearance. This may involve techniques such as dyeing, embossing, or applying decorative elements.Finally, the finished bags are inspected one last time before being packaged and prepared for shipping. The packaging process involves inserting any additional materials such as dust bags or care instructions, as well as labeling and tagging each bag for identification.Overall, the production process of bags requires meticulous attention to detail, skilled craftsmanship, and quality materials to ensure that the end product meets the expectations of both the manufacturers and the consumers. From the initial design to the final packaging, each step inthe process plays a crucial role in creating a functional and stylish bag.。
瓦楞纸箱生产工艺流程英文版

瓦楞纸箱生产工艺流程英文版The corrugated cardboard production process involves several steps that are necessary to manufacture corrugated cardboard boxes. Corrugated cardboard boxes are widely used for packaging purposes across various industries. The following is a general description of the production process.1. Paper preparation: The first step in the production process is the preparation of paper. This involves selecting the appropriate types of paper to make the corrugated cardboard. The most common papers used are kraft linerboard and medium paper.2. Corrugating: In the next step, the medium paper is passed through a corrugating machine, which adds fluting to one side of the paper. The fluting is responsible for the strength and rigidity of the final corrugated cardboard.3. Adhesive application: To create the corrugated cardboard, the corrugated medium paper is glued to the kraft linerboard. Adhesive is applied to the flutes of the medium paper, which are then pressed onto the linerboard.4. Molding and drying: After the adhesive application, the glued paper is passed through a set of heated rollers. The heat helps in the drying process and ensures that the adhesive is properly bonded with the linerboard.5. Cutting and scoring: Once the corrugated cardboard sheet is dry, it is cut into large sheets of standardized sizes. This cutting process is typically done using a high-speed rotary cutter. In addition tocutting, the sheets are also scored to create fold lines for easy assembly.6. Printing and die-cutting: At this stage, the large sheets of corrugated cardboard can be printed with designs, logos, or product information using a flexographic printing process. After printing, the sheets can be die-cut into specific shapes and sizes using sharp metal dies.7. Box assembly: The die-cut corrugated cardboard sheets are then folded and glued to form the desired box shape. This assembly process can be done manually or by using specialized machines for higher volumes.8. Quality control: Throughout the production process, quality checks are performed to ensure that the corrugated cardboard meets the required standards. These checks include measuring the strength, thickness, and overall durability of the boxes.9. Packaging and distribution: After passing the quality control checks, the finished corrugated cardboard boxes are packaged and prepared for distribution. They are often stacked and secured on pallets for easy transportation.The above steps provide a general overview of the production process for corrugated cardboard boxes. It is important to note that specific details and variations may exist depending on the manufacturer and the intended use of the boxes.。
铝的生产工艺流程英文版

铝的生产工艺流程英文版The production process of aluminum involves several stages. The first step is the extraction of bauxite ore, which contains aluminum oxide, from the earth. This ore is then refined using the Bayer process to produce alumina, or aluminum oxide. The next step is the smelting of alumina to produce aluminum metal. This is done in large industrial electrolytic cells, where a direct current is passed through a bath of molten cryolite, causing the aluminum oxide to decompose and the aluminum metal to collect at the bottom of the cell. The aluminum metal is then cast into ingots or blocks for further processing.After the smelting process, the aluminum is subjected to various treatments to improve its strength, ductility, and other properties. These treatments may include alloying with other metals, heat treatment, and mechanical working such asrolling or extrusion. The final step in the production process is the finishing of the aluminum product, which may involve machining, surface treatment such as anodizing or painting, and quality control testing.Overall, the production of aluminum involves a complex and energy-intensive process, but the resulting metal is lightweight, strong, and corrosion-resistant, making it an essential material for a wide range of applications in industry, construction, and transportation. The ongoing development of new recycling technologies also contributes to the sustainability of aluminum production, as recycled aluminum can be used to produce new products with a lower environmental impact.。
- 1、下载文档前请自行甄别文档内容的完整性,平台不提供额外的编辑、内容补充、找答案等附加服务。
- 2、"仅部分预览"的文档,不可在线预览部分如存在完整性等问题,可反馈申请退款(可完整预览的文档不适用该条件!)。
- 3、如文档侵犯您的权益,请联系客服反馈,我们会尽快为您处理(人工客服工作时间:9:00-18:30)。
生产工艺英文版Pyrometallurgical:Also known as dry smelting, the ore and the necessary additives together in a furnace heated to high temperatures, melting into a liquid to produce the required chemical reactions, thereby separating the crude metal, and then rough metal refining.Hydrometallurgy):Is acid. Base. Salt water solution, using chemical methods to extract the required metal from ore components, and then use various methods of electrolytic solution Preparation of metal, the main application of this method is difficult in low capacity of taste or slightly powdered ore.Chapter I: Copper Production TechnologyCopper raw material: 1> Natural Copper: 99% coppercontent, but very few reserves.2 "copper oxide: number not more.3 "copper sulfide: the most widely distributed, is the main raw material for copper.Pyrometallurgical: calcination (roasting )----- melting (smelting) --- blowing (blowing) --- refining (refining)Roasting: Remove some of concentrate sulfur, arsenic and other volatile parts of the impurities ------.> ___ sulfur concentrate smelting ----.> 1. Sulfur content is low, get blister copper, sulfur for a long time, the generated matte, copper (40% - 55%), 2. slag material: copper generally 0.4% - 0.5%.Matte ---- --- à blowing by blister, copper 95% -98%, residue materials: containing lead, zinc, lead flue gas. Sulfur. Zn. Blister-à refined by copper concentrate (99% -99.9%), slag: copper higher.Wet Copper: roasting (roasting) --- leaching purification (leaching) --- Electrolyzation (electrowinning)Sulfide copper concentrate (20% -30 %)--- roasting -> besoluble in dilute sulfuric acid, copper sulfate, sulfur from flue gas of lead, copper slag containing lead and zinc. Copper sulfate leach purification- ----- purpose to remove iron, then power integral method, by Ingredients: electric copper: 99.5% -99.95%, slag material: platinum metal with gold and silver, leadChapter II: lead smelting production processFire refining of lead: lead sulfide concentrate roasting ---- sintering - à be agglomeration of lead, lead 40% -50%, slag material: lead. Copper., Smoke containing lead and zinc. --- Lead Sinter changes into Crude lead through smelting reduction. lead about 98% .slag (slag): Some Gold and other metals of lead zinc, lead flue gas. --- Fire refining of crude lead à be refined lead (99.9%), slag material: Copper: 0.001% - 0.002%, Zn: 0.6% -0.7%.Wet smelting of lead: lead sulfide concentrate roasting àlead sulfate --- --- Blast Furnace (blast furnace) by crudelead (98%), slag: copper (in the form of ice recovery of copper), zinc (smoke method recovery), blister - electrowinning refinery -> get 99.9% of lead concentrates, slag: platinum group metals including gold, silver, copper and zinc.Chapter III: zinc production processFire Zinc:--- Flash flotation concentrate. Calcination (flotation.roasting) by main ingredient, zinc oxide, flue gas sulfur, lead. Slag: copper with zinc. Zinc oxide - blast furnace (blast furnace) by Ingredients: Crude zinc, lead flue gas, copper slag compound. Zn,Crude Zinc - Zinc Electrowinning be refined à concentrate, slag: copper not more than 2%, lead is not more than 3%.Hydrometallurgy;Zinc sulfide concentrates - are roasting à Ingredients: Zinc agglomeration, slag material: containing lead, zinc, lead and zinc sulfur from flue gas. --- Agglomeration of zinc leaching (leaching) of zinc sulfate solution by the slag material: zinc, lead. --- Is purified zinc sulfate solution (refining) emulsion in the lead of copper, zinc sulfate solution --- clean-àelectrowinning of zinc concentrate (zinc concentrate)Chapter IV: refined nickel production technologyFire refining nickel;Nickel sulfide roasting à Ni --- --- Blast Furnace Sinter à get low ice nickel, the total content of nickel and copper -25% 8% slag: Nickel. Zinc oxide, lead oxide. Low ice Nickel - blowing -> Ingredients: high ice nickel, copper and nickel 70% -75%, slag material: nickel. Copper and nickel matte - Mill Run àcrude nickel (67% -68%) - electrolytic refining à Nickel concentrate (99.85% - 99.99%)Wet Lian Ni:Nickel sulfide - pressure acid leaching of nickel sulfate-àà-àcrude reduction smelting of nickel -.> electrolytic refining -> Electric Nickel.Chapter V: lead-zinc production processZinc oxide is the main stone extraction of lead. Zinc metal, one of the important basic raw material--- Blast Furnace à ore was enriched ore, slag compound zinc (4.3% - 4.5%), lead (0.82% - 0.84%),Rich ore - furnace blowing smoke -.> Java compound zinc (1.0% -1.5%), lead (0.1% - 0.15%). Ingredients: zinc oxide dust lead concentrate-à germaniumChapter VI: brass factory production processBrass is composed of copper and zinc alloy. If it is only copper and zinc on the composition of the brass called ordinary brass. If two or more from a variety of elements called special brass alloy. As the lead, tin, manganese, nickel, lead, iron, silicon copper alloy composed of Pyrometallurgical copper is usually a few percent or the first few thousandths of the original ore, by dressing up to 20-30%, as copper concentrate, in the smelting furnace, reverberatory furnace, stove or furnace to create Flash matte smelting, melting output matte (matte) and then were blown into the converter to Make blister, and then in another reflection off the furnace after oxidation refining complex, or the cast anode plate electrolytic, 99.9% were grade of electrolytic copper.归纳:Jeffery2010-7-9。