轧钢线材工艺操作规程
轧钢技术操作规程
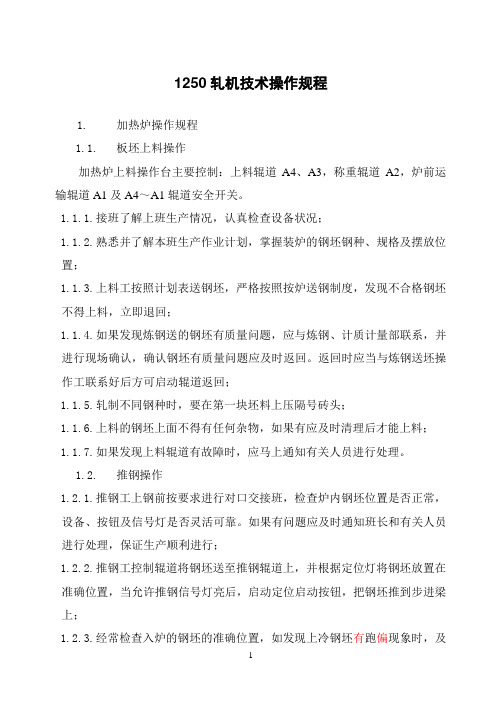
1250轧机技术操作规程1.加热炉操作规程1.1.板坯上料操作加热炉上料操作台主要控制:上料辊道A4、A3,称重辊道A2,炉前运输辊道A1及A4~A1辊道安全开关。
1.1.1.接班了解上班生产情况,认真检查设备状况;1.1.2.熟悉并了解本班生产作业计划,掌握装炉的钢坯钢种、规格及摆放位置;1.1.3.上料工按照计划表送钢坯,严格按照按炉送钢制度,发现不合格钢坯不得上料,立即退回;1.1.4.如果发现炼钢送的钢坯有质量问题,应与炼钢、计质计量部联系,并进行现场确认,确认钢坯有质量问题应及时返回。
返回时应当与炼钢送坯操作工联系好后方可启动辊道返回;1.1.5.轧制不同钢种时,要在第一块坯料上压隔号砖头;1.1.6.上料的钢坯上面不得有任何杂物,如果有应及时清理后才能上料;1.1.7.如果发现上料辊道有故障时,应马上通知有关人员进行处理。
1.2.推钢操作1.2.1.推钢工上钢前按要求进行对口交接班,检查炉内钢坯位置是否正常,设备、按钮及信号灯是否灵活可靠。
如果有问题应及时通知班长和有关人员进行处理,保证生产顺利进行;1.2.2.推钢工控制辊道将钢坯送至推钢辊道上,并根据定位灯将钢坯放置在准确位置,当允许推钢信号灯亮后,启动定位启动按钮,把钢坯推到步进梁上;1.2.3.经常检查入炉的钢坯的准确位置,如发现上冷钢坯有跑偏现象时,及时调整,避免发生事故;1.2.4.在推钢机推钢时,严禁启动辊道,必须待到推钢机零位后方可启动辊道送料,以免钢坯撞坏推钢机。
1.2.5.步进梁上升时,严禁推钢机推钢,以免撞坏步进梁;1.2.6.当推钢机出现故障后,按下急停,通知有关人员进行处理。
1.3.出钢操作1.3.1.出钢工在上岗前,除认真进行交接班,检查设备状况,了解生产情况外,还要侧重了解炉内钢种、规格及其分布和钢温等情况,熟悉当班作业计划,掌握加热炉的状况。
1.3.2.出钢信号灯亮时,并得到出钢通知后,及时出钢,根据轧制节奏和钢温状况均衡出钢。
轧钢线材工艺操作规程
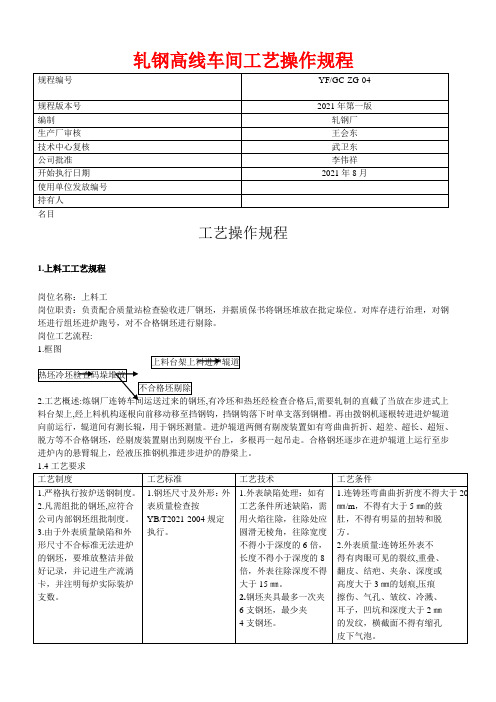
轧钢高线车间工艺操作规程名目工艺操作规程1.上料工工艺规程岗位名称:上料工岗位职责:负责配合质量站检查验收进厂钢坯,并据质保书将钢坯堆放在批定垛位。
对库存进行治理,对钢坯进行组坯进炉跑号,对不合格钢坯进行剔除。
岗位工艺流程:,需要轧制的直截了当放在步进式上料台架上,经上料机构逐根向前移动移至挡钢钩,挡钢钩落下时单支落到钢槽。
再由拨钢机逐根转进进炉辊道向前运行,辊道间有测长辊,用于钢坯测量。
进炉辊道两侧有剔废装置如有弯曲曲折折、超差、超长、超短、脱方等不合格钢坯,经剔废装置剔出到剔废平台上,多根再一起吊走。
合格钢坯逐步在进炉辊道上运行至步进炉内的悬臂辊上,经液压推钢机推进步进炉的静梁上。
1.依据生产指令和YB/T2021-2004标准,依据质保书认真核对到达钢坯的车号、支数,对外瞧质量进行检查,遇有疑咨询不清之处,立即寻有关人员联系解决并作好记录。
2.依据交接班记录和质保书,认真核对坯料的规格钢种、钢号、垛位层数、数量和顺序,并收好质量站制作,按炉送钢卡要逐项填写,字迹清晰,不得漏项,并于使用前10分钟发送到1#台输进生产治理系统终端、轧钢厂后部岗位,遇换号时,必须明确将所换新号第一支及时通知冷床工,不得混号。
3.卸车作业:从炼钢运送来的钢坯经核对后,指挥吊车吊运到指定垛位堆放整洁,上、下层互成90度,每垛高度不得超过1800mm,堆垛端部离铁路不得小于1500mm,堆垛质量执行厂有关规定。
4.上料作业:按照按炉送钢卡开出的组批炉罐号依次从垛位上将钢坯吊运到上料台架尾部,钢坯端头悬空长度相等,上料工明确指挥,做到轻落轻放,防止撞坏上料台架。
5.钢坯进炉过程中,应在炉批号的最后一根钢坯距端部放置隔号砖作为换号标志。
6.熟悉把握各种钢坯标准和技术要求、有关规定、通知、认真执行,认真作好各种记录,作好交接班工作,将炉内、台架、辊道上的炉号交接清晰。
特殊操作在台架上发觉超弯、超短、超长或炉内返回钢坯时与1#台联系,做好平安确认,上料工指挥行车将不合格钢坯吊到指定垛位,并作好记录。
轧机轧钢工安全技术操作规程范本(2篇)
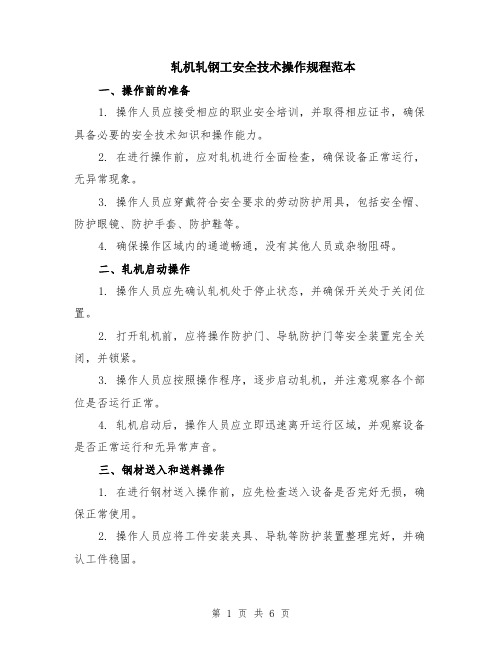
轧机轧钢工安全技术操作规程范本一、操作前的准备1. 操作人员应接受相应的职业安全培训,并取得相应证书,确保具备必要的安全技术知识和操作能力。
2. 在进行操作前,应对轧机进行全面检查,确保设备正常运行,无异常现象。
3. 操作人员应穿戴符合安全要求的劳动防护用具,包括安全帽、防护眼镜、防护手套、防护鞋等。
4. 确保操作区域内的通道畅通,没有其他人员或杂物阻碍。
二、轧机启动操作1. 操作人员应先确认轧机处于停止状态,并确保开关处于关闭位置。
2. 打开轧机前,应将操作防护门、导轨防护门等安全装置完全关闭,并锁紧。
3. 操作人员应按照操作程序,逐步启动轧机,并注意观察各个部位是否运行正常。
4. 轧机启动后,操作人员应立即迅速离开运行区域,并观察设备是否正常运行和无异常声音。
三、钢材送入和送料操作1. 在进行钢材送入操作前,应先检查送入设备是否完好无损,确保正常使用。
2. 操作人员应将工件安装夹具、导轨等防护装置整理完好,并确认工件稳固。
3. 钢材送入时,操作人员应注意观察钢材的大小、形状和位置,确保送入平稳无卡阻。
4. 进行钢材送料操作时,应保持手部和身体与运动部件的距离,避免伸入危险区域。
四、轧制操作1. 轧机操作人员应根据工艺要求选择合适的辊轧和压下程度。
2. 操作人员应随时观察轧机运行情况,确保钢材的轧制过程稳定、均匀。
3. 在轧制过程中,操作人员应随时监控轧制压力、轧制温度等参数,确保在正常范围内。
4. 减轻轧机负荷时,操作人员应逐步减小辊轧和压下程度,确保安全运行。
五、轧机停机操作1. 在轧机停机前,操作人员应提前关闭轧机辊轧和压下功能。
2. 轧机停机后,应迅速关断电源,关闭进料装置,并锁紧操作防护门和导轨防护门。
3. 停机后,操作人员应对设备进行全面检查,清理工作区域,排除设备故障和隐患。
4. 操作人员应记录轧机停机相关信息,包括停机时间、问题描述、解决方案等,以备后续分析和改进。
六、紧急情况应急处理1. 遇到火灾等紧急情况时,操作人员应立即关闭电源和气源,并使用灭火器材进行灭火。
轧钢生产线工艺流程图
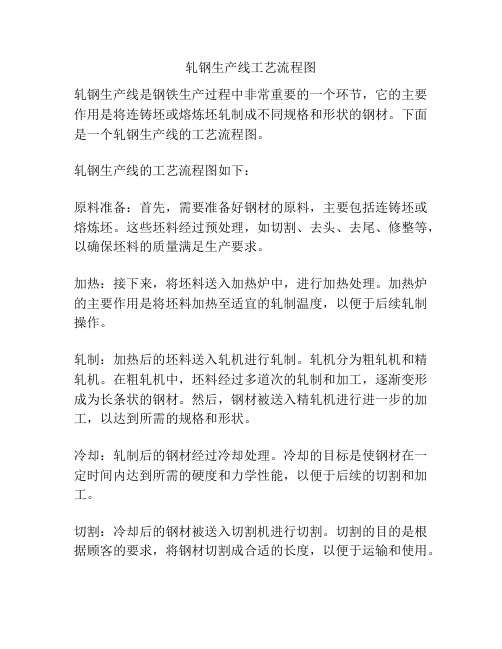
轧钢生产线工艺流程图
轧钢生产线是钢铁生产过程中非常重要的一个环节,它的主要作用是将连铸坯或熔炼坯轧制成不同规格和形状的钢材。
下面是一个轧钢生产线的工艺流程图。
轧钢生产线的工艺流程图如下:
原料准备:首先,需要准备好钢材的原料,主要包括连铸坯或熔炼坯。
这些坯料经过预处理,如切割、去头、去尾、修整等,以确保坯料的质量满足生产要求。
加热:接下来,将坯料送入加热炉中,进行加热处理。
加热炉的主要作用是将坯料加热至适宜的轧制温度,以便于后续轧制操作。
轧制:加热后的坯料送入轧机进行轧制。
轧机分为粗轧机和精轧机。
在粗轧机中,坯料经过多道次的轧制和加工,逐渐变形成为长条状的钢材。
然后,钢材被送入精轧机进行进一步的加工,以达到所需的规格和形状。
冷却:轧制后的钢材经过冷却处理。
冷却的目标是使钢材在一定时间内达到所需的硬度和力学性能,以便于后续的切割和加工。
切割:冷却后的钢材被送入切割机进行切割。
切割的目的是根据顾客的要求,将钢材切割成合适的长度,以便于运输和使用。
检测:切割后的钢材需要进行质量检测,以确保其满足规定的质量标准。
这包括外观检查、尺寸测量、化学成分分析和力学性能测试等。
包装和运输:通过质量检测的钢材被包装起来,以便于运输和储存。
包装通常采用钢带或木托盘等材料,以确保钢材的安全和完整。
以上就是一个大致的轧钢生产线工艺流程图,从原料准备到最后的包装和运输,每个环节都十分重要。
在具体的生产过程中,还会包括其他辅助工艺和设备,如铁水处理、连铸、热处理等,以满足不同钢材品种和规格的生产需求。
1轧钢厂工艺操作规程

山西长信工业有限公司轧钢厂作业文件CX-ZY-16-001A/0版工艺操作规程受控状态:编制部门:轧钢厂审核人:荣鑫批准人:常元光2013-7-2批准2013-7-10实施更改状态表轧钢生产线工艺流程图注:“ ”关键工序质量控制点轧钢厂作业文件工艺操作规程CX-ZY-16-0011 生产工艺流程连铸坯→上料辊道→排齐→推钢机推入加热炉→加热→出钢机推出→出炉辊道→机前辊道→Φ550×2→Φ530×3→卡断剪→Φ400×4→切头剪→侧活套→Φ300×8→飞剪→Φ158×8精轧机组采用45度无扭转摩根轧机→穿水冷却(控轧控冷)→吐丝机→强风冷却→PF钩式输送系统→打包→卸卷→入库堆放。
2 原料、产品规格及技术标准2.1产品名称、规格、技术标准2.1.1产品标准名称、规格、国家标准号:2.1.2钢种2.2 原料截面尺寸、长度、技术条件:2.2.1钢坯截面尺寸及允许偏差:2.2.3连铸坯技术条件:2.2.3.1连铸坯表面不得有肉眼可见的裂纹、重皮、翻皮、结疤、夹杂、划痕、擦伤、气孔、皱纹、冷溅、耳子、凹坑、凸块和深度大于2mm的发纹。
连铸坯横截面不得有缩孔和皮下气泡。
2.2.3.2连铸坯的弯曲度每米不得大于20mm,总弯曲度不得大于总长度的2%。
2.2.3.3连铸坯不得有明显扭转。
2.2.3.4连铸坯端部火焰切割部分保持平整。
2.2.3.5连铸坯允许有鼓肚,但高度不得超过连铸坯边长的允许正偏差。
2.2.3.6连铸坯端部的斜割不得大于20mm。
坯料规格:150×150×6000mm。
轧钢厂使用钢坯长度范围:5m~6.2m。
3 原料工艺技术操作规程3.1正常生产时,连铸坯由炼钢连铸车间直接运至加热炉尾上料辊道上,热装入炉轧制。
3.2后道工序处理事故时间较长时,连铸钢坯需作冷坯处理,按炉批号堆放整齐,堆垛高度不得超过4m,垛与垛间距不小于0.5m。
轧钢生产线工艺流程

轧钢生产线工艺流程
轧钢是将钢坯通过轧机进行连续轧制,使其形状、尺寸和表面质量得到一定的变化和改善的工艺。
轧钢生产线是钢铁行业中一个非常重要的生产设备,它的工艺流程对于钢材的质量和性能有着至关重要的影响。
下面将详细介绍轧钢生产线的工艺流程。
1. 钢坯加热
首先,将冷的钢坯放入加热炉中进行加热处理。
加热的温度和时间是根据不同的钢种和轧制要求而定的,一般来说,加热温度在1100℃-1250℃之间。
2. 粗轧
经过加热处理的钢坯被送入粗轧机中进行粗轧。
在粗轧机上,钢坯经过多道次的轧制,逐渐变形成为所需的形状和尺寸。
3. 精轧
粗轧后的钢坯被送入精轧机中进行精轧。
精轧是在辊道上进行
的,使钢坯的尺寸更加精确,表面质量更好。
4. 冷却
经过精轧后的钢坯需要进行冷却处理,以使其温度降到适合进
行后续加工的温度。
5. 切割
冷却后的钢坯被送入切割机中进行切割,切割成所需的长度。
6. 包装
经过切割后的钢坯被送入包装区进行包装,以便于运输和储存。
以上就是轧钢生产线的工艺流程,通过这一系列的工艺处理,
钢坯最终成为我们所需的各种形状和尺寸的钢材。
轧钢生产线的工
艺流程严格控制每一个环节,以确保钢材的质量和性能达到要求。
同时,随着科技的不断发展,轧钢生产线的工艺流程也在不断地进
行创新和改进,以满足市场对于钢材的不断提高的需求。
希望通过
不断的努力和创新,轧钢生产线的工艺流程能够更加完善,为钢铁
行业的发展做出更大的贡献。
轧钢工艺操作规程
轧钢工艺操作规程1. 引言轧钢工艺是指通过金属材料在轧机上进行连续轧制,使其形成符合要求的产品的过程。
本文档旨在规范轧钢工艺操作,确保生产过程的顺利进行和产品质量的稳定提升。
2. 设备准备在进行轧钢工艺操作之前,需进行设备准备工作,包括但不限于以下内容: -检查轧钢机械设备的各部位是否正常运转,如有异常情况及时排除; - 确认轧机辊道、液压系统、输入电源等设备的电源、气源、液压油等是否正常供应,如有异常及时处理; - 检查辊道间隙设置是否符合要求,并进行调整; - 确保安全防护措施完备,如安装护罩、防护栏等。
3. 原材料准备在进行轧钢工艺操作之前,需进行原材料准备工作,包括但不限于以下内容:- 根据生产任务单,准确核对和确认原材料规格、数量等信息; - 对原材料进行外观检查,必要时进行缺陷剪修或标记; - 将合格原材料送至轧钢机辊道入口,并保持一定的连续供给速度。
4. 工艺操作4.1 轧制前的准备•打开轧钢机电源,并进行必要的预热操作,使轧机达到正常工作温度;•检查轧机润滑系统油位,并及时补充润滑油;•启动轧机辊道系统,并保持合适的转速;•调整辊道间隙,确保符合工艺要求。
4.2 开始轧制•将原材料送入辊道入口,并确保顺利通过辊道,防止堵塞和反弹;•根据工艺要求,调整轧机辊道速度、压力等参数;•观察金属材料的轧制过程,确保其真伪、质量等符合要求;•根据轧制情况,及时调整轧机参数,以获得理想的轧制效果。
4.3 轧制结束•轧制完成后,关闭轧机电源,并进行必要的冷却操作;•清理轧机辊道和工作台面上的杂物和金属屑;•检查轧制产品的外观质量,并进行必要的修整;•对轧机设备进行巡视、检查和保养,确保其处于良好的工作状态。
5. 安全措施在进行轧钢工艺操作时,必须严格遵守安全操作规程,确保操作人员和设备的安全。
以下为常见的安全措施: - 操作人员必须身穿符合要求的工作服、安全鞋等个人防护装备; - 确保轧机设备的安全防护设施完好,并按规定使用; - 在轧制过程中,严禁将手部或其他身体部位伸入轧机辊道; - 禁止将金属材料超过规定长度送入轧机; - 轧制现场禁止吸烟、吃东西等不安全行为。
轧钢操作工安全技术操作规程(3篇)
轧钢操作工安全技术操作规程轧钢操作工是钢铁行业中非常重要的一环,其工作涉及到高温、重物、机械设备等各种安全风险。
为了保障轧钢操作工的人身安全,公司制定了一套严格的安全技术操作规程。
下面将详细介绍这套规程的相关内容。
一、工作前准备1. 首先,操作工必须穿戴符合要求的个人防护装备,包括防护服、安全鞋、手套、防护眼镜等。
2. 进入轧钢区域前,必须进行安全教育和培训,并通过相关考试。
3. 在工作前,要检查和维护轧钢设备,确保其正常运行并具备安全性。
4. 在操作之前,要对工作区域进行清理,移除可能存在的障碍物和危险品。
二、操作规程1. 操作工必须严格按照操作规程进行操作,不得随意修改或忽略任何步骤。
2. 操作工在进行设备操作时,必须使用符合标准的工具,并确保其完好无损。
3. 在操作设备时,必须保持专注,不得受其他事物干扰,并负责任地完成每一步操作。
4. 操作工必须熟悉并掌握相关机械设备的使用方法,遵守设备的使用说明和注意事项。
5. 在使用气动工具时,必须确保空压机工作正常,管路无漏气和松动,使用合适的气密性工具。
三、安全防护1. 操作工在操作过程中,应时刻保持安全意识,注意观察周围环境,并及时发现和排除安全隐患。
2. 在高温区域工作时,操作工必须穿戴防火服,并注意自身的防热措施,避免烫伤或烧伤。
3. 在操作重物时,操作工应采取正确的姿势和操作方法,以避免背部或其他身体部位受伤。
4. 在操作设备时,必须及时切断电源和气源,并采取相应的安全措施,防止设备突然启动或运行。
四、紧急情况处置1. 操作工在紧急情况下,要冷静应对,迅速采取适当的紧急停工措施,并及时向上级报告。
2. 在发生意外事故时,操作工应迅速启动应急预案,并协助救援人员进行紧急救援和处理。
3. 在发生火灾时,操作工要立即使用灭火器进行扑灭或引导他人撤离,并报告消防人员。
五、日常维护1. 操作工应保持设备的常规维护,包括设备清洁、润滑和紧固件的检查和更换。
邯钢的线材轧制工艺流程
邯钢的线材轧制工艺流程
邯钢是中国一家知名的钢铁企业,其线材轧制工艺流程是相当重要的一环。
线材轧制工艺是将连铸坯通过加热、轧制等一系列的工艺操作,将其变成直径细小的钢线材。
下面我们将详细介绍邯钢的线材轧制工艺流程。
首先,邯钢的线材轧制工艺流程从加热开始。
连铸坯先经过热轧加热炉加热至适当温度,以保证后续的轧制顺利进行。
加热的温度和时间由具体钢材种类和规格决定。
接下来是粗轧阶段。
连铸坯在一台粗轧机上进行初步的轧制,通过冷却卷取者将坯料一次次的压制成较大直径的钢线材。
此阶段主要目的是破碎和疏松连铸坯的内部气体,为后续轧制做准备。
然后是中轧阶段。
粗轧后的钢线材在中轧机上得以进一步的轧制。
通过逐步减小轧机的辊缝宽度,将钢线材的直径逐渐缩小,达到所需的规格。
在这个阶段,需要进行适当的冷却和表面处理,以确保线材的质量。
最后是精轧阶段。
经过中轧后的钢线材在精轧机上进行最后一道工序的轧制。
通过减小辊缝和增大轧制压力,进一步细化钢线材的直径,提高线材的表面光洁度和机械性能。
整个线材轧制工艺流程中,邯钢不仅注重机械设备的选用和工艺参数的控制,还十分重视质量管理。
钢材在每个工序都要通过质量检验,以保证最终产品的质量符合标准。
以上是对邯钢线材轧制工艺流程的简要介绍。
通过精细调控每个环节,邯钢能够生产出高质量的钢线材产品,满足市场需求。
轧钢工安全操作规程
轧钢工安全操作规程一、总则为确保轧钢工操作过程中的安全和顺利生产,制定本安全操作规程,对所有操作人员实行规范化、标准化管理。
同时,本规程也作为轧钢工的操作指南,使操作更加规范、安全。
二、作业环境与设施1. 作业现场应干燥、通风、无积水,并保持良好的照明条件。
2. 作业设备应处于稳定的状态。
在操作前,必须检查轧机、输送带、绞车等设备的工作情况,并做好润滑、清理、检修工作。
3. 危险区域应设置警示标志,例如轧辊喜鹊和轧头棒标识等。
4. 操作人员应穿着合适的劳动保护用品,例如防护衣、防护鞋、安全带、手套等,以减少在操作过程中与设备的接触造成的人员伤害。
5. 只有经过专业技术培训的人员才能进入危险区域,并在其监督下进行操作。
同时,不能同时进入轧钢机的多名操作人员,以减少人员伤害的风险。
三、操作规程1. 操作前必须对所有设备进行检查,并在时钟上标记下检查时间。
2. 严格遵守操作顺序,不能在操作过程中改变操作程序或顺序。
3. 维护所有操作记录。
4. 进行小修或大修前和卸下轧辊时,严禁轧钢机部件未停止运转。
5. 当轧钢机运行时,不得在轧辊和工件中间伸手、放置手臂和其他物体。
6. 在轧钢机工作过程中,不得在轧辊和工件之间的升降板上站立。
7. 应避免特殊情况,例如异物进入轧辊、轧辊停滞等,并应立即采取必要的措施。
四、应急处理1. 当发现轧钢机工作异常时,应立即停止设备。
2. 在情况严重时,应紧急切断电源,以避免危险。
3. 故障修理时,应按照操作规程中的程序进行操作。
在修理时,应戴上带有防眩手套的眼镜或面具,避免烟尘和碎片等伤害人员。
五、结论上述规程旨在让操作人员意识到安全的重要性,规范操作程序,从而降低操作过程中发生的安全事故的发生率。
操作人员应这样要时刻认真执行规程,并提高安全意识,以确保轧钢工的高效、安全生产。
- 1、下载文档前请自行甄别文档内容的完整性,平台不提供额外的编辑、内容补充、找答案等附加服务。
- 2、"仅部分预览"的文档,不可在线预览部分如存在完整性等问题,可反馈申请退款(可完整预览的文档不适用该条件!)。
- 3、如文档侵犯您的权益,请联系客服反馈,我们会尽快为您处理(人工客服工作时间:9:00-18:30)。
轧钢高线车间工艺操作规程目录1.上料工工艺规程 22.一号台操作工工艺规程 33.二号台操作工工艺规程 54.加热工工艺规程 65.三号台操作工工艺规程 196.粗轧调整工工艺规程 327.高线中轧调整工工艺规程 358. 高线预精轧350轧机调整工工艺规程 379. 高线预精轧2架轧机及精轧调整工工艺规程 3910 A线双模块轧钢调整工工艺规程 5411导卫工工艺规程 5812装配工工艺规程 6213风冷线管理工工艺规程 6514集卷双芯棒操作工工艺规程 6615头尾在线剪切工工艺规程 6716打捆工工艺规程 6817.盘卷称重工工艺规程 6918标牌打印工工艺规程 7019挂牌工工艺规程 7020卸卷操作工工艺规程 7121成品管理与码垛工工艺规程 7122轧辊车工工艺规程 7223铣工工艺规程 7524样板工工艺规程 7725辊环磨工工艺规程 78工艺操作规程1.上料工工艺规程1.1岗位名称:上料工1.2岗位职责:负责配合质量站检查验收入厂钢坯,并据质保书将钢坯堆放在批定垛位。
对库存进行管理,对钢坯进行组坯入炉跑号,对不合格钢坯进行剔除。
1.3岗位工艺流程:1.框图2.工艺概述:炼钢厂连铸车间运送过来的钢坯,有冷坯和热坯经检查合格后,需要轧制的直接放在步进式上料台架上,经上料机构逐根向前移动移至挡钢钩,挡钢钩落下时单支落到钢槽。
再由拨钢机逐根转入进炉辊道向前运行,辊道间有测长辊,用于钢坯测量。
入炉辊道两侧有剔废装置如有弯曲、超差、超长、超短、脱方等不合格钢坯,经剔废装置剔出到剔废平台上,多根再一起吊走。
合格钢坯逐步在入炉辊道上运行至步进炉内的悬臂辊上,经液压推钢机推入步进炉的静梁上。
1.4工艺要求1.5正常操作1.根据生产指令和YB/T2011-2004标准,根据质保书认真核对到达钢坯的车号、支数,对外观质量进行检查,遇有疑问不清之处,立即找有关人员联系解决并作好记录。
2.依据交接班记录和质保书,认真核对坯料的规格钢种、钢号、垛位层数、数量和顺序,并收好质量站制作,按炉送钢卡要逐项填写,字迹清楚,不得漏项,并于使用前10分钟发送到1#台输入生产管理系统终端、轧钢厂后部岗位,遇换号时,必须明确将所换新号第一支及时通知冷床工,不得混号。
3.卸车作业:从炼钢运送来的钢坯经核对后,指挥吊车吊运到指定垛位堆放整齐,上、下层互成90度,每垛高度不得超过1800mm ,堆垛端部离铁路不得小于1500mm ,堆垛质量执行厂有关规定。
4.上料作业:按照按炉送钢卡开出的组批炉罐号依次从垛位上将钢坯吊运到上料台架尾部,钢坯端头悬空长度相等,上料工明确指挥,做到轻落轻放,避免撞坏上料台架。
5.钢坯入炉过程中,应在炉批号的最后一根钢坯距端部放置隔号砖作为换号标志。
6.熟悉掌握各种钢坯标准和技术要求、有关规定、通知、认真执行,认真作好各种记录,作好交接班工作,将炉内、台架、辊道上的炉号交接清楚。
1.6特殊操作在台架上发现超弯、超短、超长或炉内返回钢坯时与1#台联系,做好安全确认,上料工指挥行车将不合格钢坯吊到指定垛位,并作好记录。
2.一号台操作工工艺规程2.1岗位名称: 一号台操作工 2.2岗位职责:钢坯经上料台架进入上料辊道,测长辊道,炉内辊道经推钢机推入炉内梁,也可操作步进梁将钢坯在炉内移动及剔除缺陷钢坯或退出加热炉钢坯。
2.3岗位工艺流程: 1.框图↓2.工艺概述: 行车将钢坯放在步进式上料台架上,一号台操作工启动按纽,台架动梁开始运动,将钢坯送往挡钢钩处,将挡钢钩抬起使钢坯两端在台架确保顺直,然后放下挡钢钩动梁继续动作将钢坯放在拨钢叉上,然后拨钢叉抬起将钢坯放在上料辊道上,开动上料辊道将弯曲严重的钢坯在自动翻钢叉处翻转然后将钢坯送入炉内悬臂辊道上。
钢坯在炉内悬臂辊道上对准位置后由推钢机将钢坯推到炉内静梁上,最后开动动梁将钢坯往前移动。
2.5正常操作1.备料备料包括坯料从上料辊道至测长和在悬臂辊道上定位等的一系列过程。
当坯料进行装炉时,坯料在炉后的对中定位由电气定位控制完成。
2.装炉当坯料完成在悬臂辊道上的对中后,悬臂辊道停止转动,推正机按设定行程将坯料推正。
3.步进当物料跟踪系统判断悬臂辊上无料且系统接到要料信号时,且装炉推正机处在后位,此时步进梁可上升至“后上”A位,接着前进至“前上”B位,再下降至“前下”C位,以及后退至“后下”位即“原点“O位,至此,完成一个步进周期(升、进、降、退)。
2.6特殊操作1.炉内倒料退钢操作从炉内梁上至悬臂辊钢坯启动装料炉门至上极限,启动装料悬臂辊和测长辊反转,启动装料辊道反转至钢坯退出停止,剔除,同时装料炉门下降至极限,上料台架动作进行装钢作业,采用手动完成。
2.禁止装料若需要停止装料(即要求空炉或在钢坯间留出一段空隙等等),应按动设置在主控台上的“禁止装料开/关”闪光按钮,在执行“禁止装料”方式过程中,信号灯闪亮;消除该方式时,再按一次该按钮。
当执行“禁止装料”方式时,它允许在“第一坯料位空”的条件下启动执行步进正循环。
3.步进梁自动踏步在相邻两次“轧钢要钢信号间隙时间超过5min时,应该执行自动踏步程序,使炉内坯料周期地进行升降运动。
执行踏步模式的条件:步进梁在原点位置(O位),并没有进行自动步进正循环;物料输送系统处于自动控制状态(包括半自动和全自动两种状态)步进梁自动踏步周期可由人工设定。
4.步进梁的几种控制方式自动1:在自动1状态下,步进梁依据联锁条件,由PLC自动依照设定的步进周期进行循环运行。
自动2.用于逆循环,按照进炉步料间距的步距进行逆循环,每启动一次开/关按钮,完成一个逆循环周期(属于半自动方式)自动3:用于正循环一周,使用开/关按钮进行控制。
(属于半自动方式)手动控制:设置手动控制按钮用于启动步进梁运行周期的四种分解动作,即对步进梁的“上升”,“前进”、“下降”、“后退”分别设有开/关按钮,每启动一次开/关按钮,即完成一个动作,每个动作的启动都有与设备性能相适应的条件,在手动状态下步进梁可执行:正循环:上升→前进→下降→后退逆循环:前进→上升→后退→下降踏步:上升→下降→上升→下降……点动控制:设置机旁点动控制按钮,用于控制步进梁的“上升”、“前进”、“下降”、“后退”等动作,每一个点动动作的启动都应有与之相适应的条件。
自动踏步:根据轧制节奏,如果出钢间隔大于5min,PLC自动输出踏步指令,踏步周期可由人工设定,这种控制方式在自动2及自动3状态时无效。
中间保持,根据轧制节奏,如果出钢间隔大于30min,PLC自动输出中间保持指令,即步进梁上升到与固定梁同一高度的位置保持不动。
3.二号台操作工工艺规程3.1岗位名称:二号台操操作工3.2岗位职责:操作出料炉门、出料悬臂辊道,出料辊道、出炉剔除装置的相应操作功能,将钢坯从出钢槽送至轧区并对加热工所属设备作相应了解。
3.3 二号台操操作工岗位工艺流程1.框图↓↓2.工艺概述:在炉内经过加热炉均匀加热的钢坯从均热段由动梁移到悬臂辊道上,根据轧线生产节奏的要求,由悬臂辊道把钢坯带出炉内经出炉辊道输送到高压水除鳞处由带有四面喷嘴的除鳞装置将钢坯表面的炉生氧化铁皮用高压水打掉,然后继续由输送辊道将钢坯送入1#轧机进行轧制,如遇轧线生产不顺或堆钢时,将1#轧机前待轧钢坯推到剔除台架上进行回炉组坯再轧制。
3.5正常操作接到“加热炉出钢”信号,并且具备钢坯准备出炉信号,出料炉门上升至上位,炉门开启完成,然后启动悬臂辊道将坯料送出加热炉,由出炉辊道输送通过除磷装置,坯料进入除磷后辊道时辊道自动运转输送到1号轧机,坯料咬入后除磷后辊道自动停转。
3.6特殊操作1.出炉的红钢坯禁止再次返回加热炉。
2.当轧线因故等轧,可将停留在辊道上或末咬入的坯料通过出炉剔除装置剔除回炉。
4.加热工工艺规程4.1岗位名称:加热工4.2岗位职责:主要负责调整好用于加热的助燃风机和煤气装置,加热炉温度控制,炉膛压力调节,炉温与燃烧比例调节,炉区设备巡检,紧急情况事故处理,炉渣清除,地坑抽水并对2#台操作工作所属设备作相应了解。
4.3岗位工艺流程 1.框图↓2.工艺概述:加热工根据加热炉各段炉温情况,在2#台上调整助燃风机的风量,然后调整空气阀门和煤气阀门的流量,确保炉内微正压燃烧,空煤比适当,各段加热温度满足轧制要求,用测温枪定期测量钢坯出钢温度,生产稳定时定期点检炉区设备,并做好相应的点检记录。
4.4岗位区域设备及性能参数4.5炉前管路系统简介1.煤气管路系统高炉煤气来自厂房外的煤气管网,总管直径DN1500mm,压力约5—15KPa,先经过电动蝶阀和盲板阀,再经过煤气快速切断阀和煤气稳压阀。
从煤气主管分出三路,分别经过三通阀进入二加热段、一加热段和均热段的分配管,每路管道上均设有电动蝶阀和电动盲板阀及流量孔板和气动调节阀。
从炉子各段分配管引出若干根支管,每个支管经过煤气密封蝶阀,接入煤气蓄热式烧嘴。
另外,加热炉在建设完成后,需要进行烘炉,采用点火烧嘴烘炉,燃料为高炉煤气。
2.空气管路系统燃烧用空气由鼓风机(一用一备)供给,鼓风机进口设多页阀,风机采用变频调速控制风量。
空气总管直径DN1320mm,经空气主管分出三路,分别经过三通阀进入预热段、加热段和均热段的分配管,每路管道上均设有流量孔板和气动流量调节阀。
从炉子各段分配管引出若干根支管,每个支管经过对夹式空气蝶阀,将空气接入空气蓄热式烧嘴.3.煤气系统吹扫与放散管路本炉采用氮气吹扫,在厂房外煤气总管的盲板阀和快速切断阀之间设有氮气接入点,接管管径DN50。
从炉子各段分配管末端接DN50放散支管汇总炉子两侧的DN80的放散管上,两根DN80的放散管最后汇集到一根DN100的放散总管上;放散支管上设有DN50的截止阀,DN100的放散管上装有两台DN100的截止阀。
在炉子两侧的每一段煤气分配管的末端都设有煤气取样管以便吹扫后取样试验。
4.废气管路系统炉子两侧空气—废气三通换向阀后的废气集中后,由一根DN1320mm空气—废气总管进入空气引风机,引风机进口设多页阀(电动执行机构驱动),出口烟管接入空气废气烟囱。
炉子两侧煤气—废气三通换向阀后的废气集中后,由一根DN1620mm煤气—废气总管进入煤气引风机,引风机进口设多页阀(电动执行机构驱动),出口烟管接入煤气废气烟囱。
每一个段的煤气—废气及空气—废气支管上均设有电动调节阀,用以调节烟气量,引风机进口的多页阀用以调节炉压。
5.氮气管路系统氮气(总管直径DN80)接至储气罐(1.5m3)向炉子各用户点供气,用作各种气动阀门、其它气动元件的动力源。
主要包括气动三通换向阀、气动调节阀、气动切断阀和炉内高温摄像头等设备驱动。
另外还用作煤气管路及点火煤气管路的吹扫放散。
6.步进系统采用液压传动,双轮斜轨式结构,步进时以矩形轨迹运行,即分别进行升、进、降、退的连贯动作,在水平运动和升降运动过程中支行速度是变化的,确保缓起缓停,轻托轻放。