8D报告填写指南1
范本:8D报告格式及填写说明

D4: Identify Root Cause or Potential Cause:
Date:开会日期
-以4M要素方式检讨分析为什么造成此不良并于报告中填入数据或说明
-从检测方式﹑环境影响等差异分析为什么厂内QC无法发现此不良而流至亚旭﹐
并于报告中填入详细状况
-必要时画出流程图,以便说明
□Acceptance Inspection■Line Reject
□Field Return□Other
Supplier Reference No:
D1: DESCRIBE THE PROBLEM
Date:2006/1/9
此料在SMT ROHS制程过炉后本体保护胶带收缩并卷起.以下不良品图片
注:1.此不良将造成我司维修工时&费用将Charge贵司.
Date:
(QA主官确认审核处)
-Askey QA人员填写是否可结案
Approved by:Checked by:
-可贴上照片,如空冷焊….
Approved by:核准人员签名Checked by:审核人员签名
D5: PERMANENT CORRECTIVE ACTION PLAN
Date:对策日期
-必要时画出改善后的流程图,以便说明
-若有short term & long term solution时,请一并写出
Description:T/F,SMD12,T52079(RoHS),30~60Vdc (input) :10Vdc@1.5A & 18Vdc@20mA (bias) 275KHz 200uH@0.7A(peak),SPEC LIN
TotalQ’TY:44pcs
8D分析报告填写说明

8D 报告填写讲明PROBLESTATEMENT/DESCRIPTIO N第一步:问题的识不和评估This section should contain as much information possible about the concern encountered, the more detailed and accurate information obtained will help to give a better understanding of the problem and assist in investigations and resolution later on.Example:- Date(s) of failure(s).- Quantity of discrepant/suspect reject parts.- Where the problem was detected.- If applicable, carryout is/is-not analysis and attach to 8D.- Have we seen the problem before?1. 问题是什么或目前真实的情况?依照对象和缺陷来陈述。
2. 最早问题在哪里发觉的?3. 问题是如何发觉的?4. 发生的问题与标准有什么不同?规格是什么?如何会产生不同的?(检验规范、图纸、CATIA 文件、或不良极限样品)5. 产生问题的项目如何测量的?测量系统是什么?测量系统出了什么问题?重复性?精度?6. 目前的情况会阻碍多少产品或汽车?(VIN 编号,阻碍到的工厂顺序号或日期/时刻和班次)7. 目前在戴姆勒克莱斯勒的工厂中发生率是多少?在供应商工厂内?良品数?不良品数?第二步:CONTAINMENT ACTIO N临时措施This section should identify those actions that “contain ” the problem, ensuring no further defects are made and the customer is protected until permanent corrective actions are in place, an example may be to “hold ” all suspect stock or “100%sort ” for the defect condition.这一步应该识不包容问题的那些行动,保证不再产生进一步的不合格品并爱护客户,直到永久措施有效,例:保持所有可疑库存或100% 选择不合格品throughout the 讲明检查的如: 5/100 检Containment actions must be recorded on the standardContainment Instruction sheet. This instruction must include a date when the containment must be carried out until and the relevant approval signatories as agreement. 临时措施应该记录在标准临时措施指导书中。
8D报告填写标准

8D Type Cust InteSuppli Othe Num 8D 类别 客户 内部供应商 其他编号Contact 联系D1Setu Initiated Initia ted Initiated 发出人发出部门Retu rn D2Desc Affe cted 受影响产不良率Probl emD3Cont Date 日Res pon Resp onsibD4InveDate 日Res pon sibl e DepResp onsible Pers onD5PerDate 日Respon sibl e Dep t.负责Resp onsib le Pers on 责任人:D6Prev Date 日水平展开的必要性:□ 要 ▇不要(原因: 无库存 )Corrective Action Request-8-Discipline Worksheet (CAR-8D)纠正措施工作单 - 8步法( CAR-8D)Customer/Supplier Name 客户/供应商名称F i l l i n g b y t h e S u p p l i e rIR141013005CC抄送To:Team Members 致:小组成员Team Leader 小组组长Affected Total Quantity reject ratio受影响总数量“短期控制措施”填写需要确认以下内容:1. 库存数量?确认结果?处理方式?2. 在制半成品的数量?确认结果?处理方式?3. 原材料的数量?确认结果?处理方式?4. 产线是否正在生产,短期的预防不良流出的措施是什么?在尚未確定永久對策之前,先實施圍堵行動.“调查问题原因”填写需要确认以下内容:1. 问题发生的根本原因(4M1E 分析),从以下几个方面分析找原因:a. 操作人员; b. 作业技能/方法;c. 操作指导书; d. 设备与夹具; e. 物料; f. 其他(环境)2. 问题流出的根本原因(为什么产线测试/全检没发现,为什么品管没有检出来):a. 检验人员 b. 检验方法d. 检测设备 c. 检查指导书 f. 其他问题影响“永久性纠正措施”填写需要确认以下内容:1. 制定改善对策,防止不良再发生.(例如修改规格,调整机台参数,改变操作方法,增加检测设备,变更物料,人员培训等...).2. 对策要量化(要有对比数据,例如机台压力由100变更为120;手动操作改为由自动机操作等),不能用笼统的词汇(例如加强,加严,注意...等)3. 制定改善对策要考虑到防呆/防錯法, 如治具/設備/人员操作的防呆出錯;4. 對策的水平展開:有無水平展開到其它類似產品,.“预防措施”填写需要确认以下内容:1. 对改善对策的内容进行文件化/标准化.例如修改作业指导书(SOP),检验规范(SIP)等...8D 报告填写标准以下D3~D7是供应商必须填写的项目,请各厂商参考以下的填写标准. 2016.1.5 V0Responsibl e DepResp onsib le Pers onD7VeriVerificat ionPers onVerif icati on Date 确认D8ConVeri ficat Verif icatiF005-AF i l l i n g b y t h e C u s t o m e r1. 对改善对策的内容进行文件化/标准化.例如修改作业指导书(SOP),检验规范(SIP)等...2. 文件资料DCC 发行管制. “确认行动效果”填写需要确认以下内容:对改善对策的有效性进行验证,结果.例如: 小批量试做结果OK ; 试验和可靠性测试验证OK; 检验和量测OK. 等其它验证方式.。
8D改善报告的填写_确定版)
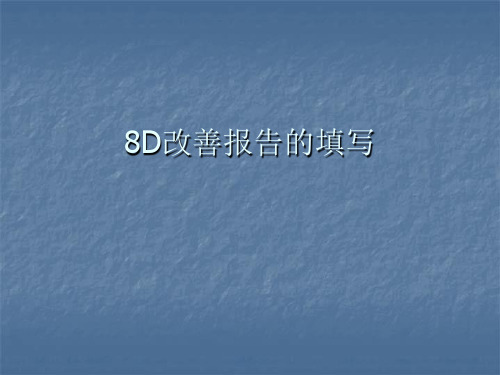
72小时内的原因分析、改善方案
在明确客户投诉内容的72小时内,组 织相关人员分析原因,明确责任人及应承 当的相关责任,组织填写相应的《8D改善 对策报告》,并由落实对策,明确对策责 任人和要求完成时间。
重新分析
日本电产客户于9月25日再次投诉9月20日发 出的2000PCS出现包装破损。
8D改善报告的关闭
e)8D预防再发阶段
一定要考虑横向展开,对所有可能产生同样问题的产品 /Package/设备/生产线/工序标准化和展开相关的纠正措施。
比如A工序的维修员在修了设备后有一个螺丝忘记拧了, 改善措施是建立一套设备维修以后针对设备/产品进行首 检的机制,那么我们当然要横向展开到所有的工序所有的 设备,同时还考虑到除了维修以后的验证,还有设备突然 停机(停电,停气,死机),更换产品品种,长期设备闲 置后开启等,这些建立的一整套的检查清单。
特别提出:FMEA是一定需要进行评审的,通常也是需要
升版相关内容的,比如RPN的重新评价,更新控制措施等。
c)4D原因分析阶段 原因分析我们通常采用5WHY、鱼刺图、FTA的方法,个人觉得这些方 法是非常好的,可以找到真正的原因。我最恨的就是一句话两句话的 原因。原因分析不清,不管是对8D报告来说还是对问题解决来说,完 全失败。 很多偶发的问题可能是找不到原因的,那么FTA就提供了很好的帮助, 通过头脑风暴把大家的意见结合起来,对每个可能性进行排查。这些 可能性有的会被推翻,有的会被证实。证实还是证伪通常根据之前的 数据分析,历史记录和再现试验来验证,通常这样的发生率很小案列, 最终找不到原因的时候,都是挑一个可能发生的,公司容易改进的 (或者确实需要改进的),做为发生原因来回答客户。为了便于客户 的理解,我们可以制作一些图片来说明失效的机理,必要时候用动画 也是可以的。为了说明模具如何把产品冲偏,用动画或图片的效果要 远远好于文字说明。 需要注意的是,原因分析要和问题描述相吻合,也就是说,这个原因 确实可以引起这个现象,然后进行再现试验,再现之后,产品确实出 现了和投诉一样的失效模式和现象,这样我们才认可这个原因分析到 位了。当然,不合格的产品为什么从公司流出也是需要考量的,比如 有的缺陷在测试时候不能筛选,我们以后改善以后如何保证筛选出来。
8D报告(范本)

1.问题解决小组:组成日期: 4/18/2012** 事业部部长** 品质部部长** 生产部部长** 技术科经理** VGS线产品工程师2.问题描述:2.1 问题陈述:客户投诉4个产品短路。
2.2 问题描述详细信息:3.临时性纠正措施:3.1 库存/在制品检查:1.对在制品进行抽样测试IR,设定为VR=410V;IR<5uA,失效率为0/24K PCS.2.对库存进行抽样测试IR, 设定为VR=410V;IR<5uA,失效率为0/24K PCS.3.2 工艺制程/OQC限制措施:3.2.1查核2005年3月份PE1产品的可靠性监控情况,HTRB,PCT,TC和Forward Surge总共各做了7个批次,每种试验的抽样量为315支,全部合格。
3.2.2 查核2005年3月份UF4004产品的OQC的检验情况,无电性不良记录。
3.2.3将该产品列入OQC加严检验清单中,OQC对UF4004产品连续10个批次执行加严检验(3/28/2006)。
3.3 风险评估:风险评估水平为一般(50),不需要采取强制对策。
4.根本原因分析:4.1 退回样品的初始确认(外观/电性)(如适用):参照VGSC失效分析报告T061120。
4.2 退回样品的失效分析:4.2.1 失效分析结果总结:4.2.1.1.典型IMC失效-表面有氧化层,导致芯片烧毁。
4.2.2 失效分析详细状况:参照VGSC失效分析报告T061120。
(参考VGST提供的UG2 IR不良模拟试验及FA报告) 4.3 失效原因:4.3.1 失效机理:由于焊接炉温异常,导致焊接材料产生”IMC”现象,在后期器件应用中发生失效.(参考VGST提供的UG2 IR不良模拟试验及FA报告)4.3.2 可能的原因/要素:4.3.2.1 焊接炉温异常,导致焊接材料产生”IMC”现象.4.3.2.2晶粒制程异常,导致玻璃钝化层披覆不良4.4 根本原因:4.4.1 最可能原因的分析:焊接炉温异常,导致焊接材料产生”IMC”现象.4.4.2 根本原因的结论:同4.3.2.1经过模拟试验及排查, 最可能的原因是由于出炉材料在焊接炉出炉口未及时清理,导致焊接炉内部产生卡炉, 处于焊接炉高温区的材料产生”IMC”现象.正常炉温曲线: 峰值温度365C.卡炉后炉温异常曲线:峰值温度400C卡炉的原因如下图: 由于员工操作疏忽,未及时清理出炉材料.4.4.3 不良未发现/逃脱的原因:TMTT测试时,该支二极管尚未损坏,各项测试参数符合测试规范。
8D报告填写规范.
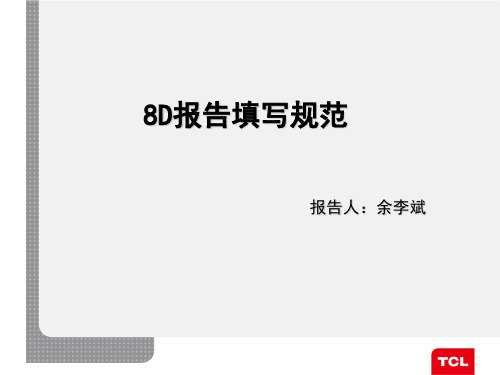
■ QE
XXX
■ SMT □ IQC □ 生产 □ 供应商 □ 研发 □ ____
XXX
■1个工作日
□3个工作日
□1周
□2周
□1个月以
□1个月以上
1、问题的解决不可能是一个人能解决: 2、获得领导认同和支持; 3、有利于争取各业务系统的资源; 4、减少扯皮和监督带来的成本;
5、有利于公司/个人经验的积累和成长。
D7 验证
Discipline 7 效果验证 附件 □有 ■无 填写人 余李斌 日期 20061108 1、人员恢复,能够继续活动; 2、按1.5M半径转弯5次未再发生翻车; ■临时验证OK (■及时 日期:20061108 ) 暂未关闭,待下次验证 □关闭( □及时 日期: )
D8长期对策
Discipline 8 CHECKLIST及相应培训 填写人 余李斌 日期 20061108 骑双人自行车在转弯时,要至少以1.5m的半径进行。
故障描述
不良现象
不良严重程度 Discipline 参与部门 团队成员 计划完成时间 Discipline 3 2 组长:PE
A类:
□
B类:
□C类:日期□ Nhomakorabea团队组成
□ QE
□ SMT □ IQC □ 生产 □ 供应商 □ 研发 □ ____
□1个工作日
围堵措施
□3个工作日
□1周
附件 □有
□2周
□无
□1个月以
8D报告填写规范
报告人:余李斌
8D简介
• 8D——又称团队导向问题解决步骤,最初是福特公司提 出的处理问题的一种方法,适用于制程能力指数低于其 应有值时有关问题的解决。 • 后来推广应用到包括重大客户及所有不良改善活动, 强调的是团队协作,是一个符合逻辑思维的方法。与 6SIGMA是一脉相承的,从故障说明、理解分析、处理 解决到预防避免逐步的推进。 • 此方式是以团队运作为导向,以事实为基础、数据为 依据,避免个人主见的介入,使问题的解决能更具条理。 • 此方式宜由公司各业务部门人员的共同投入,求得创 造性及永久性的解决方案。 • 此方式可适用于任何问题,而且能促进相关目标的各部 门间有效的沟通。
富士康富士康富士康8D报告填写说明
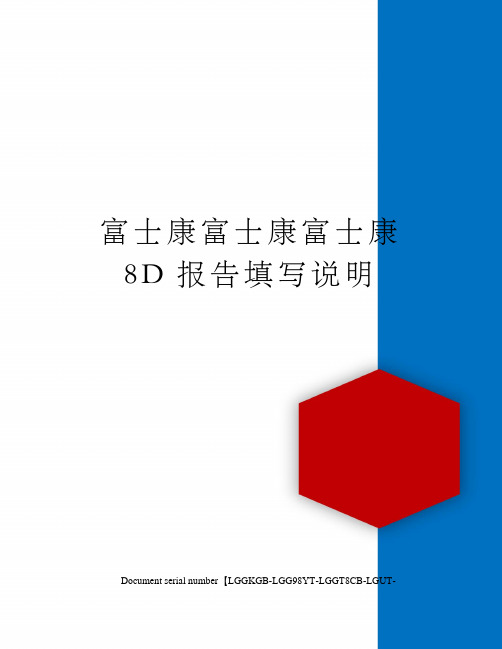
日期:
相关人员签字:
根本原因定义前需要检验所有的潜在不合格原因并对相关数据进行分析(例如:根本原因消除前,不合格产品比率为22%而根本原因消除后,不合格产品比率为0)。为了找到根本原因,在原因分析阶段应使用 “五个为什么”工具,必要时,不限于究问五次为什么。哪里发生了变化这是引起不合格的原因吗消除这个原因后,不合格产品会消除吗根本原因分析是否已经完成(我们是否需要知道这个根本原因是怎么发生的)
富士康富士康富士康8D报告填写说明
公司商标
8-D报告
编号
版本
修订日期
8D序号:
提出日期:
最后更新日期:
问题主题:
D1小组成员:
组长:组长应负责带领小组完成8D报告。组长的主要职责包含但不限于:带领小组完成8D、制定各项活动及会议日程并管理团队。
组员:组员负责响应小组各项活动。组员选择应基于其专业与技能。组员的主要责任包含但不限于:问题调查、结论分析与措施执行。
D2问题描述:
问题定义应包含“4W2H”,即“where,when,who,what,how many,how much”。即发生时间、发生地点、汇报人、问题描述、不合格数量或价值。”以上信息需要在第一时间通知客户。需定义“是什么”或“不是什么”。
D3制定短期纠正措施,也称为临时措施、围堵措施、遏制措施(ICA):
同时将纠正预防措施固化下来,将预防措施更新到相应的FMEA/CP/WI/工艺等文件中,防止未来再次出现类似问题。
8D报告填写范本-8d报告填写范本

1. 到对策实施即使需要一段时间,也一定要跟踪。 2. 效果确认就是设定符合对策前的发生率的样品数。 3. 效果确认是将对策前后的数据进行比较,如对策不充分,再次实施对策。 4. 确认对策有没有对作业带来负面影响。 5. 效果确认要经过相当一段时间的验证,彻底防止再发。 防止再次流出措施Escape
2、团队成员应能够从客户的角度思考问题; 3、通常核心团队的组成应在4-10人; 4、团队外的专家可作为团队的外围予以支持; 5、应由客户或供应商的参与(不一定总适用); 6、根据8D进展的不同阶段可进行成员的调整。
查,并明确化。 WHAT(什么)→问题的内容,现象(尽可能地用图表示) WHY(为什么)→为什么被视为问题(被视为问题的内容) WHEN(何时)→问题发生的年月日 WHERE(何地)→问题的场所(市场、工厂内) WHO(谁)→问题发生的对象品、对象者、发现者
认ERA能够起作用。
填写经过确认的有效
程度,用百分比体现
D1-小组(姓名、部门、电话)Team Name, Role, Phone)
D2-问题描述Problem Description
1、团队成员由跨职能的人员组成,且掌握过程或系统所需要的知识; 在把握事实的基础上,将必要的情报以5W2H的方式无遗漏地调
系统、逻辑地将发生的原因清楚地记述在这里。 (通常通常确定根本原因的工具: 流程图;头脑风暴 法;鱼刺图;5Whys分析)
影响比例%Affect
Percent
体系的Systemic 允许发生原因Why did our system
allow the problem to occur ?
从体系角度考虑“发生原因”会发生的 填写该原因对问题发生
- 1、下载文档前请自行甄别文档内容的完整性,平台不提供额外的编辑、内容补充、找答案等附加服务。
- 2、"仅部分预览"的文档,不可在线预览部分如存在完整性等问题,可反馈申请退款(可完整预览的文档不适用该条件!)。
- 3、如文档侵犯您的权益,请联系客服反馈,我们会尽快为您处理(人工客服工作时间:9:00-18:30)。
主题Title:
初级从动齿轮质量事故Quality problems for clutch gear
开始日期Opened Date :2006-12-24
G8D 状态Status :D2
产品/过程Product/Process :
完成日期Closed Date :
问题类型Type :制造及检验问题Manufacturing and inspection
更新日期Last Update:
D0-现象Symptom
有效率%
Efficiency Percent:
实施日期
Implemented Date:
D1-小组(姓名、部门、电话)Team Name, Role, Phone)D2-问题描述Problem Description
姓名部门电话
D3-临时的纠正措施Interim Containment Action
有效率%Efficiency Percent:实施日期Implemented Date:
D4-根本原因Root Cause
影响比例%Affect Percent
D5/D6-永久性的纠正措施/验证Permanent Corrective Action/Validation
有效率%
Efficiency Percent:实施日期
Implemented Date :
D7-预防措施Prevent Recurrence Actions:
实施日期
Implemented Date :
D8-受表彰的小组和个人Recognize Team and Individual Contributions
报告人Author :
时间Date :
12月24日LONCIN 工艺样机装配,10台中有一台发动机分离行程短,经过对问题离合器的分析及测量,发现离合器齿轮尺寸存在问题,尺寸30.4(-0.1,0)实际尺寸为30.6,同批次产品在LONCIN 库房中已经没有,但在离合器厂家成都FCC 还有110件等待工艺样件离合器装配.
In the pre process series engine assembly in LONCIN, 1 of 10
engiens can not separate in clutch seperation test. After analysis and measurement of cluthes which cause the problem, found one dimension of clutch gear was not ok, the dimension in drawing is 30.4(-0.1,0) ,but actual value is 30.6,there are no clutches from the same batch in LONCIN stock, But there are 110 gears from the same batch for process series in clutch supplier ChengDu FCC
8D 编号8D NO.:
8D 报告8D REPORT
D0-应急反应活动Emergency Response Action
编号:LX/J-LXTJ-XXX xxxxxxxx公司(传真号:(xxx)xxxxxxxx)
组织Organization:隆鑫LK15业务部
隆鑫工艺样机装配阶段,在进行离合器分离测试时,10台机器中发现有1台离合器分离行程短.
In the pre process series engine assembly in LONCIN, One of ten engiens can not separate smoothly in clutch seperation test.
问题解决日期
措施等更新日期
零部件或某道工艺
紧急措施,如停止发运;空运、隔离等。
紧急措施
效果
利用团队力量解决问题,指定组长牵头完成。
临时的纠正措施(针对
整个环节:用户生产线上零件、库房零件、在途零件、自己库房零件),措施全选,清退、
效果怎样(针对每项措施都有一百分比)。
根本原因,5W ,即5个为什么,寻根问底。
质量问题-碰伤-包装不合理-没设计包装,考虑不周,或没有包装指导书,工人没
针对该问题的影响(针对每项措施都有一百分比)。
针对每个根本原因采取纠正措施。
验证效果百分比。
解决后写下该报告存档作为经验教训,如有PFMEA 则更新,同时针对类似产品彻底清查并写
如重大立功则给予奖励。