汽车座椅精冲件质量问题及解决方案的探究
汽车冲压件回弹缺陷解决方法探讨

汽车冲压件回弹缺陷解决方法探讨摘要:在汽车制造过程中,冲压件的精度在整车精度方面至关重要的作用,这就要求冲压件符合性和一致性。
在实际生产中,有很多问题影响冲压件的质量,其中回弹问题就是冲压常见问题,也是比较复杂,难解决的问题。
回弹严重影响着冲压件的装配性能和使用性能,造成后序焊接困难,降低了生产效率和制约着整车品质。
冲压件回弹问题最佳的解决是在设计阶段,但是影响冲压件回弹有材料、模具、设备等很多因素,设计阶段是不能完全解决的。
很多冲压件回弹是在试制阶段发现,在试制阶段解决冲压件问题是也是经常采用的方法,本文主要探讨一下在试制阶段针对回弹缺陷的一些解决方法,一般从两个方面入手:产品设计和工艺设计,下面就从这两方面进行简述。
关键词:冲压件回弹解决方法产品设计工艺设计1.冲压件回弹缺陷的类型一般汽车冷冲压件的回弹缺陷有:正/负回弹、成型扭曲、多曲线形状扭曲、大曲线变化、棱线/面翘曲等2.影响回弹的主要因素对于冷冲压件来说,影响回弹缺陷的主要因素集中在这几个方面:冲压材料、弯曲部位R角、大弯曲率、零件形状、模具关键部位配合间隙、成型工艺等。
3.冲压件回弹缺陷解决方法主要简述一下在产品试制阶段对冲压件回弹缺陷的解决方法,分为产品设计和工艺设计:3.1产品设计方面:3.1.1更换冲压件材质、料厚材料在冲压件成型中起着至关重要的作用,钢板屈服强度越大,回弹量越大,钢板厚度越小,回弹量越大,在满足产品性能的要求下,可选择屈服强度小的钢板,或适当增加钢板料厚。
3.1.2设置防回弹筋防回弹筋是解决回弹的有效方法之一,在满足产品要求的情况下,增加防回弹筋,改变产品形状。
防回弹筋一般有三角筋和凸凹筋,可根据产品要求及回弹量的大小进行设置。
3.1.3减小弯曲部位R角弯曲部位R角对回弹的影响很大,R角越小,回弹量越小。
在满足产品要求的情况下,可通过减小R角解决回弹问题,一般冲压件弯曲部位R角应<8mm。
3.1.4冲压零件形状设计零部件形状对冲压件回弹影响很大,如一个折弯冲压件,设计成U型和设计成V型的回弹量就是显而易见的,后者可以有效的解决回弹问题。
汽车冲压常见质量问题及解决方法PPT课件

2019/9/19
20
2.1.3材料表面质量差-划痕引起应力集中、锈蚀增大后阻力。
2.1.4压料面的进料阻力过大-毛坯外形大、压料筋槽间隙小、凹 模圆角半径过小、外滑块调的过深、拉深筋过高、压料面和凹 模圆角半径光洁度差。
2.1.5局部拉深量太大,拉深变形超过了材料变形极限。
2.1.6在操作中,把毛坯放偏,造成一边压料过大,一边压料过小。 过大的一边则进料困难,造成开裂;过小的一边,进料过多, 易起皱,皱后进料困难,引起破裂。
b 模具装配误差-导向部分间隙大、凸凹模装配不同心等;
c 压力机精度差—如压力机导轨间隙过大,滑块底面与工作台表 面的平行度不好 ,或是滑块行程与压力机台面的垂直度不好, 工作台刚性差,在冲裁时产生挠度,均能引起间隙的变化;
d 安装误差—如冲模上下底板表面在安装时未擦干净或对大型冲 模上模的紧固方法不当,冲模上下模安装不同心(尤其是无导 柱模)而引起工作部分倾斜;
1.6 制件的工艺性差-形状复杂有凸出或凹入的尖角均
易因磨损过快而产生毛刺。
2019/9/19
6
小结:
毛刺的产生,不仅使冲裁以后的变形工序由于 产生应力集中而容易开裂,同时也给后续工序毛 坯的分层带来困难。大的毛刺容易把手划伤;焊 接时两张钢板接合不好,易焊穿,焊不牢;铆接 时则易产生铆接间隙或引起铆裂。
3.1 模具刃口尺寸制造超差
3.2 冲裁过程中的回弹、上道工序的制件形状与下道工序模具工 作部分的支承面形状不一致,使制件在冲裁过程中发生变形,冲 裁完毕后产生弹性回复,因而影响尺寸精度。
3.3 板形不好。
3.4 多工序的制件由于上道工序调整不当或圆角磨损,破坏了变 形时体积均等的原则,引起了冲裁后尺寸的变化。
汽车冲压件缺陷分析及质量改进

汽车冲压件缺陷分析及质量改进作者:李靖来源:《科技创新与应用》2019年第25期摘; 要:在汽车制造领域中,超过60%的金属制件需要使用冲压工艺加工成形。
由于原材料性质、冲压模具状态和操作者人为因素等,可能会导致冲压件表面存在一定的质量缺陷。
文章从汽车冲压件起皱、开裂、回弹等典型缺陷切入,深入探讨了制件表面质量缺陷检测方法,并提出了相应的改进措施。
关键词:汽车冲压件;成型缺陷;质量标准;解决措施中图分类号:TG386; ; ; ; ;文献标志码:A; ; ; ; ;文章编号:2095-2945(2019)25-0114-02Abstract: In the field of automobile manufacturing, more than 60% of metal parts need to be formed by stamping process. Due to the nature of raw materials, the state of stamping die, and the human factors of the operator, there may be some quality defects on the surface of stamping parts. In this paper, from the typical defects such as wrinkling, cracking and springback of automobile stamping parts, the detection methods of surface quality defects are discussed in depth, and corresponding improvement measures are put forward.Keywords: automobile stamping parts; forming defects; quality standards; solutions引言冲压成形是指利用冲压设备对材料施加压力,使其产生塑性变形的过程。
汽车零件生产中的质量问题与解决方案

汽车零件生产中的质量问题与解决方案随着汽车产业的快速发展,汽车零件质量问题成为了人们关注的焦点。
在汽车生产过程中,零件质量直接影响着车辆的性能表现、使用寿命乃至驾驶者的安全,所以汽车制造商们一直以来都致力于提升零件质量。
然而,无论何种精密的制造工艺,总会出现偏差和不确定性,这就可能导致质量问题的出现。
针对这些问题,企业需要建立有效的解决措施和预防策略。
一、产生质量问题的原因首先,我们需要了解一下是什么原因导致汽车零件出现质量问题。
1. 设计缺陷:汽车零件的设计在一定程度上决定了其性能。
如果设计过程中没有考虑周全或者对某些特性理解不足,都可能导致设计出来的零件无法满足预期性能要求,从而出现质量问题。
2. 生产过程不规范:如果生产过程中没有按照标准化操作进行,也可能引起汽车零件的质量问题。
比如,对生产设备的维护不到位,可能使设备在运行中出现故障,从而影响零件的制造质量。
3. 原材料问题:汽车零件的质量也和原材料的质量密切相关。
如果企业为了降低成本,使用了质量较差的原材料,那么制造出来的零件肯定无法保证其质量。
二、解决方案了解了汽车零件质量问题的原因后,我们可以从以下几个方面寻找解决方案。
1. 设计优化:改进汽车零件的设计,是解决其质量问题的一个重要方法。
企业可以通过运用现代的设计方法,如模拟工程、模型验证等,来优化零件设计,提高其性能。
2. 生产流程优化:制定严格的生产流程,并进行严格的执行,是保证汽车零件质量的重要措施。
企业需要建立一套完善的质量控制体系,确保每一个生产环节都能按照规定的标准进行。
3. 选择优质原材料:对于自身不能生产的零件,企业应从源头上把关,选用质量良好的原材料,减少质量问题的出现。
三、预防策略除了解决已经出现的质量问题,防止质量问题的产生也是至关重要的。
企业可以从以下几个方面进行预防。
1. 建立完善的质量管理体系:通过ISO等国际标准,建立公司内部的质量管理体系,确保质量控制流程的标准化和规范化。
汽车座椅行李箱冲击下的失效模式和对策分析

4结论
水史综舟J’也|J r扶的i J乍辅试骑.9j纳r儿剌-啦埘火破的试验J|I坫仟#敞火诎的纠-小
2010中国汽车安全技术国际研讨会
分析,总结了试验前期需要注意的事项以及标准GBl5083—2006的缺陷,来优化试验质量, 防止因为个别局部的原凶造成整体的失败,加大试验的成功率,降低研发和试验成本。
如超
鲫10一I Iq巩It宜十拙术qh』盯flf会
3分析与建议
3
I瑰阶段座椅试验方式
n先,n|I阿ir乍柑“I摘试骑t}I,土吐常址的打,℃订州种,j#、1f,JII Jf’i^?身为拽体(如 c¨,将测试庸椅世啵J J;*l J皿行动奎强,([榆测,近常性1二』会秉川这种冉』C,儿优点n r雕 椅立裂^使,JI小一*坚}4拟{r牟辅们南l【[,fIl如锵川J丌鼓巾的多次测试时圳aj要埘庠椅同 定点进行』r0腓加强。f,JII,j"为I 4.白迂☆J。台1:宜址儿q所,^理埘制以及姨必和宅化也需要较 K叶nU。jC。、足咀饪拟戍扳代忤I 11。身的^代(如A¨.这种矗』℃的好处n:J模拟底板本 身强』立商,rⅡ以咂缸使1 J,tt[J使模拟底扳^试验I・仃个别m“t#Ⅲ、,也ll儿l冉维修,¨造价 也较低、村l埘吐验玳蔷时州斯.试验教半较曲,柑比f6】。’.,咏倚J家股会聚川后 种方“。
艚词:钉乍辅冲IIf失效哑能强度
Solution and analysis ofear seare
mode Yin jiong
shanghai guanchi automobile
J
Hudi‘ Co.,Ltd,
safety technology
and…㈣inthe
1引言
songjiang,shanghai.201601
汽车座椅维修的常见问题分析

汽车座椅维修的常见问题分析汽车座椅作为驾驶员和乘客的重要保护装置,承受着长时间的使用和各种外界因素的冲击,因此在使用过程中会出现一些常见问题。
本文将对汽车座椅维修中的常见问题进行分析,以帮助车主更好地了解和解决这些问题。
1. 座椅材质磨损座椅材质磨损是汽车座椅维修中最常见的问题之一。
长时间的使用会导致座椅表面的织物、皮革或合成革磨损,出现裂纹、破损或褪色等情况。
对于这种问题,可以通过更换座椅套或进行修补来解决。
如果磨损较为严重,建议更换整个座椅套,以保证舒适度和外观。
2. 座椅调节系统故障座椅调节系统故障是另一个常见的座椅问题。
座椅调节系统包括座椅前后调节、靠背角度调节、座椅高低调节等功能。
如果发现座椅无法正常调节或调节困难,可能是由于座椅调节机构损坏或控制开关故障引起的。
这种情况下,需要将座椅拆解检查,修复或更换故障部件。
3. 座椅加热和通风系统故障座椅加热和通风系统故障是高档车型常见的问题。
这些系统通过座椅内部的加热或通风装置提供舒适的温度和通风效果。
如果发现座椅加热或通风功能失效,可能是由于加热或通风装置损坏或电路故障引起的。
要解决这个问题,需要检查座椅内部的装置和相关的电路,进行修复或更换。
4. 座椅弹簧断裂座椅弹簧断裂是座椅维修中的另一个常见问题。
长时间的使用和外界冲击会导致座椅弹簧断裂,进而影响座椅的舒适度和支撑性。
如果发现座椅变得松弛或不稳定,可能是由于座椅弹簧断裂引起的。
这种情况下,需要将座椅拆解检查,修复或更换断裂的弹簧。
5. 座椅安全气囊故障座椅安全气囊故障是座椅维修中较为严重的问题。
座椅安全气囊是汽车被动安全系统的重要组成部分,能够在碰撞时提供额外的保护。
如果发现座椅安全气囊报警灯亮起或无法正常充气,可能是由于气囊模块损坏或电路故障引起的。
这种情况下,需要将座椅拆解检查,修复或更换故障部件。
综上所述,汽车座椅维修中的常见问题包括座椅材质磨损、座椅调节系统故障、座椅加热和通风系统故障、座椅弹簧断裂以及座椅安全气囊故障等。
汽车后座椅骨架行李冲击分析与结构优化
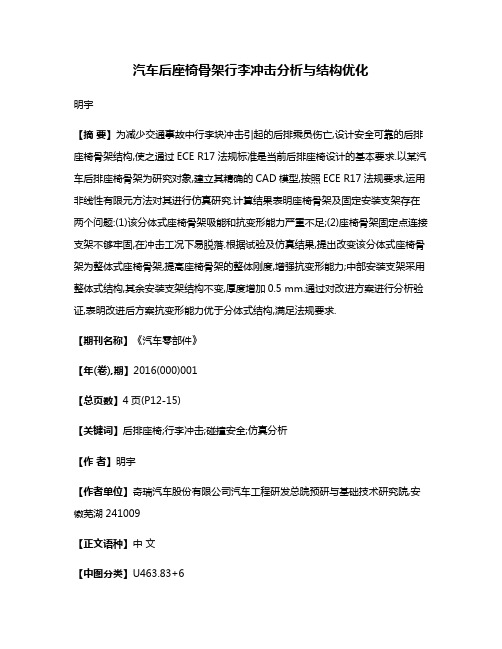
汽车后座椅骨架行李冲击分析与结构优化明宇【摘要】为减少交通事故中行李块冲击引起的后排乘员伤亡,设计安全可靠的后排座椅骨架结构,使之通过ECE R17法规标准是当前后排座椅设计的基本要求.以某汽车后排座椅骨架为研究对象,建立其精确的CAD模型,按照ECE R17法规要求,运用非线性有限元方法对其进行仿真研究.计算结果表明座椅骨架及固定安装支架存在两个问题:(1)该分体式座椅骨架吸能和抗变形能力严重不足;(2)座椅骨架固定点连接支架不够牢固,在冲击工况下易脱落.根据试验及仿真结果,提出改变该分体式座椅骨架为整体式座椅骨架,提高座椅骨架的整体刚度,增强抗变形能力;中部安装支架采用整体式结构,其余安装支架结构不变,厚度增加0.5 mm.通过对改进方案进行分析验证,表明改进后方案抗变形能力优于分体式结构,满足法规要求.【期刊名称】《汽车零部件》【年(卷),期】2016(000)001【总页数】4页(P12-15)【关键词】后排座椅;行李冲击;碰撞安全;仿真分析【作者】明宇【作者单位】奇瑞汽车股份有限公司汽车工程研发总院预研与基础技术研究院,安徽芜湖241009【正文语种】中文【中图分类】U463.83+6在交通事故中,汽车后排座椅将会受到行李块的巨大冲击载荷,座椅骨架结构往往产生变形甚至断裂,增加后排乘员的伤亡事故。
因此后排座椅作为降低乘员损伤的安全部件,首先要能够保证车辆在碰撞时后排乘员具有一定的生存空间,防止其他车载体(如行李等)进入到生存空间,且能确保乘员在碰撞事故发生时保持一定姿态,防止后排乘员向前排发生二次撞击。
因此ECE R17法规明确规定后排座椅的行李冲击强度的要求,导致了用传统方法设计开发的座椅质量和成本的增加。
关于汽车座椅的安全性,当前的研究方向主要有碰撞过程中座椅系统对乘员承受能量的分散作用、新型材料和新加工成型技术的应用对座椅性能的影响,以及质量、成本的节约问题等[1-3]。
文中以某汽车后排座椅为研究对象,建立该座椅骨架的精确三维CAD模型,按照ECE R17法规要求,进行非线性有限元分析,依据分析结果给出改进方案,并对改进方案进行分析验证,表明改进方案满足法规要求。
汽车高强板冲压件质量问题解决方法的研究
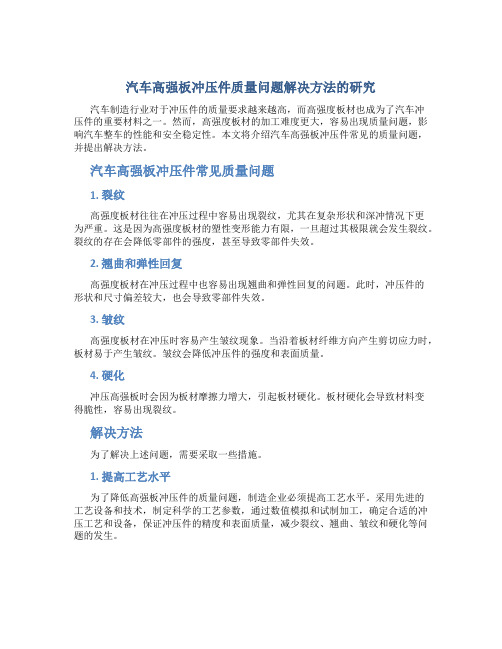
汽车高强板冲压件质量问题解决方法的研究汽车制造行业对于冲压件的质量要求越来越高,而高强度板材也成为了汽车冲压件的重要材料之一。
然而,高强度板材的加工难度更大,容易出现质量问题,影响汽车整车的性能和安全稳定性。
本文将介绍汽车高强板冲压件常见的质量问题,并提出解决方法。
汽车高强板冲压件常见质量问题1. 裂纹高强度板材往往在冲压过程中容易出现裂纹,尤其在复杂形状和深冲情况下更为严重。
这是因为高强度板材的塑性变形能力有限,一旦超过其极限就会发生裂纹。
裂纹的存在会降低零部件的强度,甚至导致零部件失效。
2. 翘曲和弹性回复高强度板材在冲压过程中也容易出现翘曲和弹性回复的问题。
此时,冲压件的形状和尺寸偏差较大,也会导致零部件失效。
3. 皱纹高强度板材在冲压时容易产生皱纹现象。
当沿着板材纤维方向产生剪切应力时,板材易于产生皱纹。
皱纹会降低冲压件的强度和表面质量。
4. 硬化冲压高强板时会因为板材摩擦力增大,引起板材硬化。
板材硬化会导致材料变得脆性,容易出现裂纹。
解决方法为了解决上述问题,需要采取一些措施。
1. 提高工艺水平为了降低高强板冲压件的质量问题,制造企业必须提高工艺水平。
采用先进的工艺设备和技术,制定科学的工艺参数,通过数值模拟和试制加工,确定合适的冲压工艺和设备,保证冲压件的精度和表面质量,减少裂纹、翘曲、皱纹和硬化等问题的发生。
2. 选择合适的材料制造企业应选择优质的高强板材料。
目前市面上有多种类型的高强板材,包括普通高强度钢板、高强度热轧钢板、高强度镀锌板等。
通过合理选择和与零部件的结构匹配,可以有效减少生产过程中的质量问题。
3. 优化模具设计优化模具设计可以有效地减少冲压件的翘曲、皱纹等缺陷。
设计合适的凸模和凹模,配合适当的角度和半径,可以有效地降低材料的应力和变形,减少冲压件的变形和瑕疵。
4. 实现控制系统的数字化采用数字化控制系统可以优化控制过程,提高加工精度和稳定性。
数字化控制系统可以实现对冲压力、冲程、冲频等参数的精确控制,避免人为干涉和误操作导致的质量问题。
- 1、下载文档前请自行甄别文档内容的完整性,平台不提供额外的编辑、内容补充、找答案等附加服务。
- 2、"仅部分预览"的文档,不可在线预览部分如存在完整性等问题,可反馈申请退款(可完整预览的文档不适用该条件!)。
- 3、如文档侵犯您的权益,请联系客服反馈,我们会尽快为您处理(人工客服工作时间:9:00-18:30)。
汽车座椅精冲件质量问题及解决方案的探究
摘要:精冲件广泛用于汽车座椅调节机构的生产,对产品形状、尺寸精度及断面质量的要求均很高。
本文列举了汽车座椅精冲件生产中存在的典型的质量问题,并分析探讨了问题产生的原因,提出了解决问题的方法。
关键词:精冲工艺;精冲;冲裁质量;解决方案
引言
精密冲裁是一种有别于普通冲裁的先进加工方法,它利用专用压力计(精冲机),通过专用的精密冲裁模具,在强力压料状态下对金属板料进行冲压,使金属塑形变形一直延伸到剪切结束。
通过精冲所获得的零件具有精度高、光洁度好、平面度高、垂直度好,并拥有光洁的剪切面等优质特性,多年来,精冲技术备受汽车制造业的青睐,尤其在汽车座椅零件的生产上得到了很好的推广。
精冲件的质量,主要指剪切面上光亮带质量、垂直度、毛刺、塌角、平直度和尺寸精度。
精冲件的质量主要取决于模具的结构是否合理、模具的制造精度、刃口的状况、被冲材料的塑性和金相组织、零件几何形状的复杂程度、工艺润滑剂、力能参数以及压力机的调整等。
2.质量问题产生的原因及解决方案
2.1.毛刺和塌角
精冲件一般带有较小的毛刺,高度一般为0.1~0.3mm,当凸、凹模磨损严重后,也会产生较大的毛刺,并且外形毛刺比内形毛刺大。
如果工件的一侧毛刺比较厚,这就可能是凸、凹模间隙小了,可以尝试调整模具间隙即可消除。
在实际生产中,对于精冲件上根部较薄的毛刺采用滚筒清理和振动清理的方法;对于根部较厚的毛刺采用沙带磨光机去毛刺。
精冲件的塌角用深度a和宽度c测量,深度一般为材料厚度的20%,宽度c=1.5a。
精冲件棱角部位的塌角除了与材料厚度有关外,还与棱角部位的夹角有关,夹角越小,塌角越大。
若塌角过大则可能是凹模圆角过大造成的,凹模圆角过大会使工件在压力下处于弯曲状态而被拉入凹模,从而拉塌且造成工件不平。
修整凹模刃口即可改善。
2.2.光亮带质量不好
在正常的情况,精冲件剪切面的光亮带可占料厚的90%以上;当处于负间隙时,可达100%。
在实际生产中,由于各方面的原因,很难使模具始终保持最佳状态。
如剪切断面有鱼鳞片裂纹、水波纹,在断面中部出现撕裂,以及光洁面粗糙等缺陷。
鱼鳞片裂纹产生的原因有以下几种:①被冲材料不合适;②冲孔凸模或落料凹模的圆角太小;③润滑不够。
解决方法对应的是:①更换塑性更好的材料,或者对材料进行球化退火处理;②适当的增大圆角半径,并使圆角半径均匀;③更改润滑剂或加大润滑面,使模具充分润滑。
水波纹产生的原因是凹模圆角较大,而凸、凹模之间间隙又较小,使精冲接近冷挤压状态。
解决的方法是:调整凹模的圆角半径和模具间隙,充分考虑间隙和料厚的比值关系。
断面中部出现撕裂,原因主要是应力集中。
应从以下几方面进行排除:①凹模圆角是否过小或者不均匀;②V形齿圈压力是否太小,或者压边圈齿形是否合适;③材料是否塑性不够;④工件是否存在尖角过渡,或圆角半径太小。
2.3.剪切面出现较大的锥度
断面有锥度产生的原因主要是凹模的圆角半径过大,从而使得过多的材料被拉入了凹模中。
此外,凹模不可见的弹性变形也会对锥度有影响,如果是机械加工制造的凹模,则需磨凹模的底部,增加预紧力;如果是电加工制造的凹模,则可以采用预紧套。
2.4.精冲件平面度不好
精冲件平面度不好的主要原因有以下几种:①原材料平直度较差,冲压所产生的应力遗留在了精冲件上;②润滑油过多;③材料晶粒方向不合理;④顶板出件时,作用力不均匀。
对应的措施可以从以下几方面着手:①对原材料进行较平,或采用正火的材料;②在V形齿上开槽对润滑油引流;③增大反压力,并检查顶件板厚度、平行度和顶杆长度;④改变排样方式;
3.结束语
我公司生产的精冲件配套用于多个车型的轿车座椅调角器和滑轨机构。
质量因是“生存之本”而备受关注,在多年的实际生产中,我们遇到了很多问题,我们也积累了丰富的经验。
当然,产品缺陷的原因也不是单一的,而是综合了多个因素,需要我们技术人员一一排查,对症下药,这样才能顺利的解决问题,降低生产成本,在市场的竞争中获得更大的利润。
参考文献
[1]周开华,陈幼琳. 精冲技术图解. 北京:国防工业出版社,2008.
[2]周开华. 简明精冲手册. 北京:国防工业出版社,2006.
[3]温莉敏,王贤才,王益民等. 间隙与精冲质量的关系研究. 模具工业,2010,36(2):33~35.。