航空发动机机匣构件机械加工工艺优化
航空发动机机匣机械加工过程中变形因素分析及变形控制

航空发动机机匣机械加工过程中变形因素分析及变形控制摘要:伴随着我国航空事业的不断发展,越来越多的航空飞机都运用到了我们的日常生活中。
航空飞机的安全质量对于航空出行来说是至关重要的,如果航空飞机存在较为严重的安全隐患,就有可能会给旅行的乘客和机组人员带来严重的生命威胁,一旦发生机毁人亡的情况就会造成十分恶劣的社会影响。
航空发动机是飞机的重要核心动力零件,对于航空器飞行的过程发挥着十分重要的作用。
航空发动机机匣是发动机的重要组成部分,在发动机工作的过程中承担着受力的作用。
发动机机匣在制作的过程中需要进行机械加工,在金属材料的选择方面上,一般选用钛合金为主,如果遇到强烈的碰撞可能就会出现形变的情况,从而影响到航空发动机的正常运转。
关键词:航空飞机;发动机;机匣;变形因素前言经过我国在航空事业方面上的持续关注,我国的航空技术也在快速的崛起,已经开始在国际舞台上展现出了属于我国的航空实力。
为了确保我国的航空技术能够跟上世界的水平,我们也对航空技术提出了更高的要求。
在航空发动机机匣的加工过程中,所采用的加工技术是较为高端复杂的。
能够影响到航空发动机机匣加工质量的因素是比较多的,都存在着外部因素和内部因素,这些因素都在极大的程度上影响了航空发动机机械加工的质量,如果加工技术出现相应的误差,最终还会导致发动机机匣出现变形的情况。
为了能够促进当前航空发动机机械加工技术的发展,该专业的技术人员必须要针对发动机机匣机械加工工艺进行优化与完善,促进我国航空事业的飞速发展。
本文章将会针对航空发动机机匣的三个部位的变形因素进行分析探讨,并且采取相应的措施来提升我国发动机机匣加工技术水平,希望能够给航空企业一定的借鉴。
一、影响航空发动机机匣变形的因素(一)机匣毛坯形变发动机机匣的主要工作就是承载航空飞机的涡轮叶片,通过机匣能够与其他许多系统进行连接,例如冷却系统、油路系统和控制系统,从而更好的控制航空飞机的涡轮叶片。
也正是因为航空器发动机机匣功能的多样性,航空发动机机匣自身的几何形状是较为复杂的,能够帮助他在不同的工作环境下进行工作,在不同的方位还采用了不均匀的壁厚,从而适应涡轮叶片与外界系统的连接工作。
航空发动机机匣加工变形分析与控制
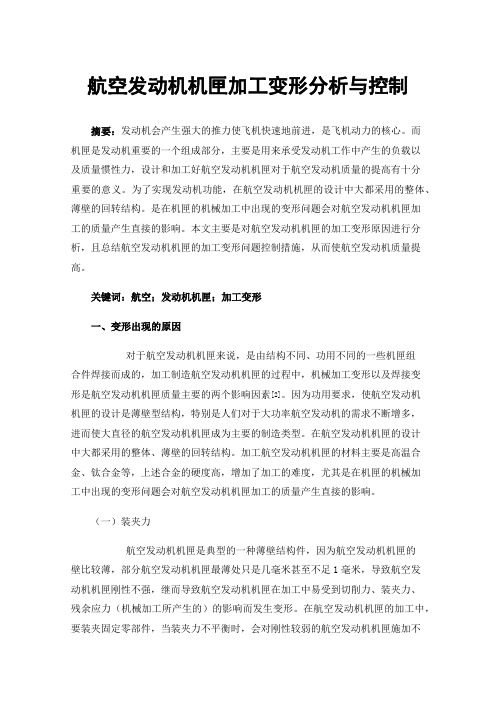
航空发动机机匣加工变形分析与控制摘要:发动机会产生强大的推力使飞机快速地前进,是飞机动力的核心。
而机匣是发动机重要的一个组成部分,主要是用来承受发动机工作中产生的负载以及质量惯性力,设计和加工好航空发动机机匣对于航空发动机质量的提高有十分重要的意义。
为了实现发动机功能,在航空发动机机匣的设计中大都采用的整体、薄壁的回转结构。
是在机匣的机械加工中出现的变形问题会对航空发动机机匣加工的质量产生直接的影响。
本文主要是对航空发动机机匣的加工变形原因进行分析,且总结航空发动机机匣的加工变形问题控制措施,从而使航空发动机质量提高。
关键词:航空;发动机机匣;加工变形一、变形出现的原因对于航空发动机机匣来说,是由结构不同、功用不同的一些机匣组合件焊接而成的,加工制造航空发动机机匣的过程中,机械加工变形以及焊接变形是航空发动机机匣质量主要的两个影响因素[2]。
因为功用要求,使航空发动机机匣的设计是薄壁型结构,特别是人们对于大功率航空发动机的需求不断增多,进而使大直径的航空发动机机匣成为主要的制造类型。
在航空发动机机匣的设计中大都采用的整体、薄壁的回转结构。
加工航空发动机机匣的材料主要是高温合金、钛合金等,上述合金的硬度高,增加了加工的难度,尤其是在机匣的机械加工中出现的变形问题会对航空发动机机匣加工的质量产生直接的影响。
(一)装夹力航空发动机机匣是典型的一种薄壁结构件,因为航空发动机机匣的壁比较薄,部分航空发动机机匣最薄处只是几毫米甚至不足1毫米,导致航空发动机机匣刚性不强,继而导致航空发动机机匣在加工中易受到切削力、装夹力、残余应力(机械加工所产生的)的影响而发生变形。
在航空发动机机匣的加工中,要装夹固定零部件,当装夹力不平衡时,会对刚性较弱的航空发动机机匣施加不必要的附加力,进而致使在航空发动机机匣加工后出现变形。
由于装夹力致使的航空发动机机匣变形大都在航空发动机机匣的薄壁处以及端面等部位发生。
(二)切削力由于切削力导致航空发动机机匣加工变形的原因是刀具产生切削力对航发动机机匣产生作用,而出现让刀变形。
飞机发动机叶片机匣的高效加工
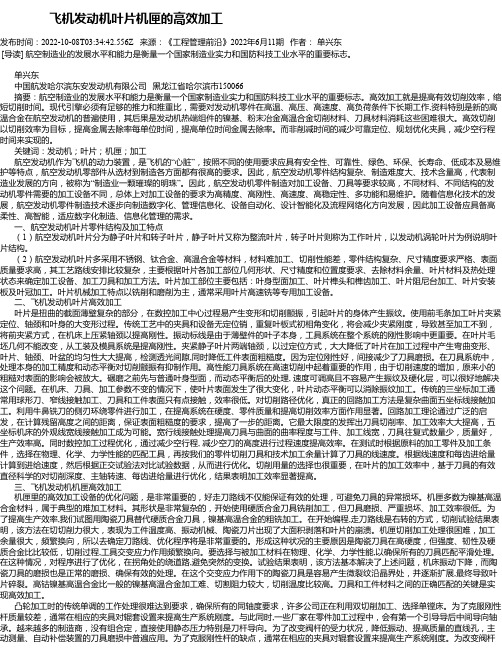
飞机发动机叶片机匣的高效加工发布时间:2022-10-08T03:34:42.556Z 来源:《工程管理前沿》2022年6月11期作者:单兴东[导读] 航空制造业的发展水平和能力是衡量一个国家制造业实力和国防科技工业水平的重要标志。
单兴东中国航发哈尔滨东安发动机有限公司黑龙江省哈尔滨市150066摘要:航空制造业的发展水平和能力是衡量一个国家制造业实力和国防科技工业水平的重要标志。
高效加工就是提高有效切削效率,缩短切削时间。
现代引擎必须有足够的推力和推重比,需要对发动机零件在高温、高压、高速度、高负荷条件下长期工作,资料特别是新的高温合金在航空发动机的普遍使用,其后果是发动机热端组件的镍基、粉末冶金高温合金切削材料、刀具材料消耗这些困难很大。
高效切削以切削效率为目标,提高金属去除率每单位时间,提高单位时间金属去除率。
而非削减时间的减少可靠定位、规划优化夹具,减少空行程时间来实现的。
关键词:发动机;叶片;机匣;加工航空发动机作为飞机的动力装置,是飞机的“心脏”,按照不同的使用要求应具有安全性、可靠性、绿色、环保、长寿命、低成本及易维护等特点,航空发动机零部件从选材到制造各方面都有很高的要求。
因此,航空发动机零件结构复杂、制造难度大、技术含量高,代表制造业发展的方向,被称为“制造业一颗璀璨的明珠”。
因此,航空发动机零件制造对加工设备、刀具等要求较高,不同材料、不同结构的发动机零件需要的加工设备不同,总体上对加工设备的要求为高精度、高刚性、高速度、高稳定性、多功能和易维护。
随着信息化技术的发展,航空发动机零件制造技术逐步向制造数字化、管理信息化、设备自动化、设计智能化及流程网络化方向发展,因此加工设备应具备高柔性、高智能,适应数字化制造、信息化管理的需求。
一、航空发动机叶片零件结构及加工特点(1)航空发动机叶片分为静子叶片和转子叶片,静子叶片又称为整流叶片,转子叶片则称为工作叶片,以发动机涡轮叶片为例说明叶片结构。
航空发动机机匣构件机械加工工艺优化 王小伟

航空发动机机匣构件机械加工工艺优化王小伟摘要:航空发动机是飞机的“心脏”,是一个国家加工制造技术的重要体现。
在航空发动机的加工制造过程中,航空发动机机匣构件是航空发动机制造的关键和难点之一。
在航空发动机机壳的加工制造过程中,由于材料的尺寸、机壳的结构等因素的影响,往往会导致发动机机匣加工后出现几何尺寸、形状和位置公差等问题。
严重影响了航空发动机机匣构件的加工质量,此外,航空发动机机壳部件的表面损伤将大大降低航空发动机机壳部件的使用寿命和强度,为了提高航空发动机机壳的表面加工质量,需要在分析影响航空发动机机壳表面完整性的因素的基础上,对航空发动机机壳部件的加工工艺进行优化。
改进了航空发动机机壳部件加工后的表面完整性,保证了航空发动机机匣构件的加工质量。
关键词:航空发动机机匣构件;机械加工;加工工艺;优化引言:航空发动机机壳部件是飞机发动机加工制造的关键部件。
高强度合金,如钛合金和高温合金,由于其拥有耐高温和高负荷的性质,因此被用作主要材料。
航空发动机机壳加工中容易发生表面完整性的损伤,这对航空发动机机壳的使用寿命有很大的影响。
因此,有必要通过对航空发动机机壳部件加工工艺的优化,找出发动机机壳部件加工过程中的应力集中点。
改进航空发动机机壳加工过程中的应力分布,保证航空发动机机壳加工表面的完整性,提高航空发动机机壳的抗疲劳延长其寿命。
1制约航空发动机机匣构件机械加工的因素在航空机械加工过程中,制约机壳加工的因素很多。
有两个主要的制约因素。
首先是加工过程中使用的加工材料,其次是加工过程中的加工形式公差。
这些因素在很大程度上影响了套管的加工几何尺寸,对加工后的加工公差有很大影响。
在很大程度上影响了套管构件的加工质量和加工精度。
如果质量不够好,将给我国航空业带来严重的安全风险。
此外,机匣的外观和表面损伤也会影响机匣的使用寿命,机匣架的强度也会产生严重的影响。
因此,为了有效提高航空发电机组机壳的使用寿命和使用强度,我们在机械加工过程中要进行严格的质量控制,只有保证机壳机架的质量,才能给我航空业的进一步发展。
航空发动机机械加工工艺优化方法探讨
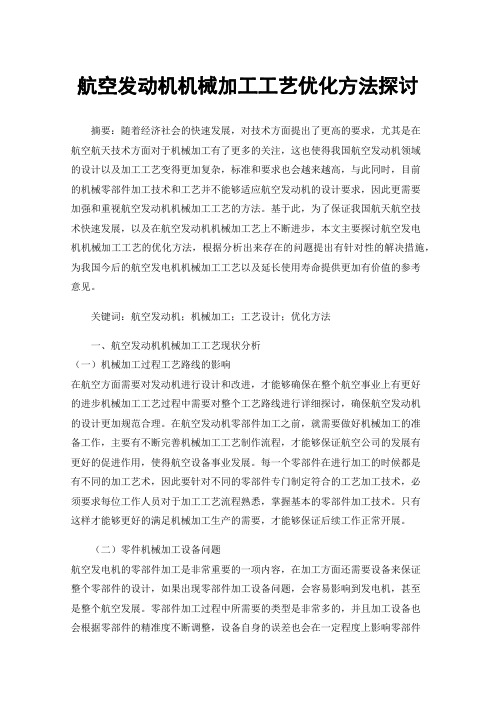
航空发动机机械加工工艺优化方法探讨摘要:随着经济社会的快速发展,对技术方面提出了更高的要求,尤其是在航空航天技术方面对于机械加工有了更多的关注,这也使得我国航空发动机领域的设计以及加工工艺变得更加复杂,标准和要求也会越来越高,与此同时,目前的机械零部件加工技术和工艺并不能够适应航空发动机的设计要求,因此更需要加强和重视航空发动机机械加工工艺的方法。
基于此,为了保证我国航天航空技术快速发展,以及在航空发动机机械加工艺上不断进步,本文主要探讨航空发电机机械加工工艺的优化方法,根据分析出来存在的问题提出有针对性的解决措施,为我国今后的航空发电机机械加工工艺以及延长使用寿命提供更加有价值的参考意见。
关键词:航空发动机;机械加工;工艺设计;优化方法一、航空发动机机械加工工艺现状分析(一)机械加工过程工艺路线的影响在航空方面需要对发动机进行设计和改进,才能够确保在整个航空事业上有更好的进步机械加工工艺过程中需要对整个工艺路线进行详细探讨,确保航空发动机的设计更加规范合理。
在航空发动机零部件加工之前,就需要做好机械加工的准备工作,主要有不断完善机械加工工艺制作流程,才能够保证航空公司的发展有更好的促进作用,使得航空设备事业发展。
每一个零部件在进行加工的时候都是有不同的加工艺术,因此要针对不同的零部件专门制定符合的工艺加工技术,必须要求每位工作人员对于加工工艺流程熟悉,掌握基本的零部件加工技术。
只有这样才能够更好的满足机械加工生产的需要,才能够保证后续工作正常开展。
(二)零件机械加工设备问题航空发电机的零部件加工是非常重要的一项内容,在加工方面还需要设备来保证整个零部件的设计,如果出现零部件加工设备问题,会容易影响到发电机,甚至是整个航空发展。
零部件加工过程中所需要的类型是非常多的,并且加工设备也会根据零部件的精准度不断调整,设备自身的误差也会在一定程度上影响零部件的精准度,从一定程度上造成了加工工艺技术的问题。
航空发动机机匣加工工艺研究

航空发动机机匣加工工艺研究摘要:随着我国综合国力的增强,同时也在促进国产发动机的性能逐渐朝着优良的方向不断发展。
近年来航空发动机的性能及设计结构在不断改进和提高,发动机机匣零件的材料、结构也发生了很大的变化。
本文就航空发动机机匣加工工艺展开探讨。
关键词:航空发动机;机匣;加工工艺1加工工艺特点机匣加工表面主要分为内、外两部分。
由于其外部需要连接到许多如电气、冷却、油路及管路等附件系统,导致其表面形状结构复杂,对机加要求比较高,尤其是对位置和尺寸精度要求较高;另外发动机机匣的内部主要是承载其压气机的涡轮叶片,包括动、静力叶片,这些都是其关键的动力输出部分,所以也对制造精度要求较高。
综上所述,机匣制造加工工艺的难点主要体现在材料切除率高、薄壁易变形、材料难切削和对刀具切削性能要求高等多个方面。
2.1轴数控铣削机匣型面的成形,国内通常是通过在多轴数控铣削设备上加工完成的。
数控机床的出现以及带来的巨大利益,引起世界各国科技界和工业界的普遍重视。
在航空机闸机械加工中,发展数控机床是当前我国机械制造业技术改造的必由之路,是未来工厂自动化的基础。
数控机床的大量使用,需要大批熟练掌握现代数控技术的人员。
数控技术的应用不但给传统制造业带来了革命性的变化,使制造业成为工业化的象征,而且随着数控技术的不断发展和应用领域的扩大,它对国计民生的一些重要行业的发展起着越来越重要的作用。
机匣零件外环形面共分二级,分布有二条环形凸缘,下部有1个纵向小凸缘,两个纵向凸缘对称分布。
由于机匣毛坯是自锻件,加工余量很大,且零件材料难切削,为了保证尺寸加工精度和表面加工质量,防止加工后零件变形。
其外型面加工分层、分块进行,采取合理的走刀路径,采用对称的切削加工余量。
分几次走刀加工到最后尺寸的方法,以减少加工后的变形。
因此,该机匣加工划分三个主要阶段并附加特征工序热处理,以去除材料内应力,防止零件变形。
2.2磨粒流加工磨粒流加工就是用流体作为载体,将具有实际切削技术性能的末了悬浮于其中,形成一个流体磨料,依靠末了相对于被加工材料表面的流动提供能量进行加工分析的一种技术。
航空发动机机匣加工工艺探讨
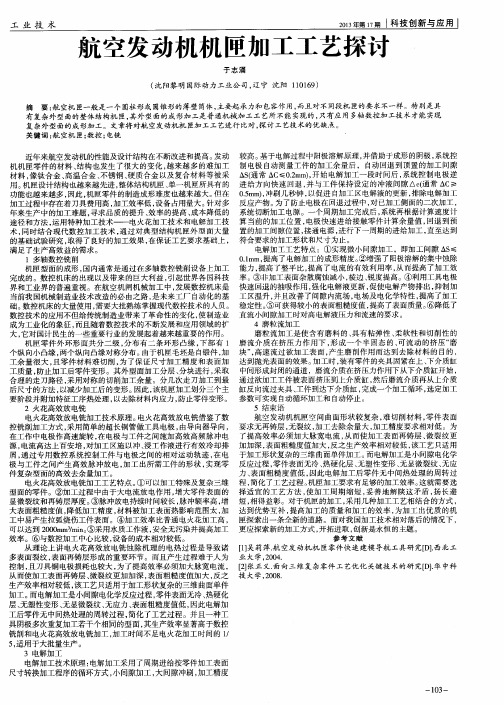
航 空发动机机 匣加工工艺探讨
于 志 涌
( 沈 阳黎 明 国 际动 力 工 业公 司 , 辽宁 沈 阳 1 1 0 1 6 9 )
摘 要: 航空机 匣一般是一 个圆柱形或 圆锥 形的薄壁筒体 , 主要起承力和包容作用, 而且对不同段机 匣的要求不一样。特别是具 有复 杂外型面的整体结构机 匣, 其外型面的成形加工是普通机械加工工艺所不能 实现 的, 只有应用 多轴数控加工技术才能实现 复杂外型面的成形加工。文章将对航空发动机机 匣加工工艺进行比对 , 探讨工艺技术的优缺点。
关键 词 : 航 空机 匣; 数控 ; 电铣
近年来航空发动机 的性能及设计结构在不断改进和提高 。 发动 机 机 匣零 件 的材 料 、 结 构 也发 生 了很 大 的变 化 , 越来 越 多 的难 加 工 材料 , 像钛合金 、 高温合金 、 不锈钢 、 硬质合金以及复合材料等被采 用。 机匣设计结构也越来越先进 , 整体结构机匣、 单一机匣所具有的 功能也越来越多 , 因此 , 机匣零件的制造成形难度也越来越大 。 但在 加工过程中存在着刀具费用高 , 加工效率低, 设备 占用量大。 针对多 年来生产 中的加工难题 , 寻求品质的提升 、 效率的提高 、 成本降低的 途径和方法 , 运用 特 种 加 工技 术 —— 电火 花 加 工 技术 和 电解 加 工技 术, 同时结合现代数控加工技术 , 通过对典型结构机 匣外 型面大量 的基础试 验研究 , 取得了 良好 的加工效果 , 在保证工艺要求基础上 , 满 足 了生 产高 效 益 的需 求 。 1多轴 数 控铣 削 机匣型面 的成形 , 国内通常是通 过在多轴数控铣 削设备上加工 完 成 的 。数 控 机床 的 出现 以及 带来 的 巨大 利 益 , 引起 世 界 各 国科技 界 和 工业 界 的普 遍 重视 。在航 空机 闸机 械 加 工 中 , 发展 数 控 机 床是 当前 我 国机 械 制 造业 技 术 改 造 的必 由之 路 , 是 未 来工 厂 自动 化 的基 础。 数控机床 的大量使用 , 需要大批熟练掌握现代数控技术的人员 。 数控技术 的应用不但给传统制造业带来 了革命性 的变化 , 使制造业 成 为 工业 化 的象 征 , 而 且 随着 数 控技 术 的不 断 发 展 和应 用 领 域 的扩 大, 它 对 国 计 民生 的一 些重 要 行业 的发 展起 着 越 来越 重 要 的作 用 。 机匣零件外环形面共分二级 , 分布有二条环形 凸缘 , 下部有 1 个 纵 向小 凸缘 , 两 个 纵 向 凸缘 对称 分 布 。 由 于机 匣 毛坯 是 自锻件 , 加 工余量很大 , 且零件材料难切削 , 为了保证 尺寸加工精度 和表 面加 工质量 , 防 止加 工 后 零件 变 形 。其外 型面 加 工 分 层 、 分 块进 行 , 采取 合理的走刀路径 , 采用对称 的切削加工余量 。分几次走刀加工到最 后尺寸的方法 , 以减少加工后的变形 。 因此 , 该机匣加工划分三个主 要 阶段 并 附加 特征 工 序 热 处理 , 以去 除 材料 内应 力 , 防止 零 件 变形 。
航空发动机机匣高效加工方法研究
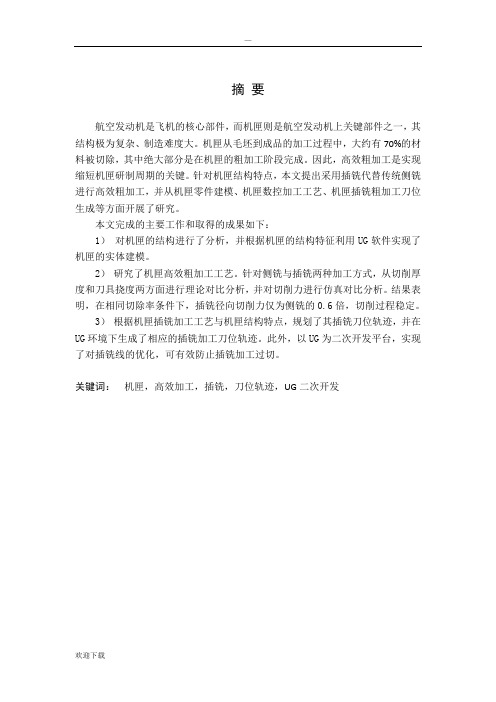
摘要航空发动机是飞机的核心部件,而机匣则是航空发动机上关键部件之一,其结构极为复杂、制造难度大。
机匣从毛坯到成品的加工过程中,大约有70%的材料被切除,其中绝大部分是在机匣的粗加工阶段完成。
因此,高效粗加工是实现缩短机匣研制周期的关键。
针对机匣结构特点,本文提出采用插铣代替传统侧铣进行高效粗加工,并从机匣零件建模、机匣数控加工工艺、机匣插铣粗加工刀位生成等方面开展了研究。
本文完成的主要工作和取得的成果如下:1)对机匣的结构进行了分析,并根据机匣的结构特征利用UG软件实现了机匣的实体建模。
2)研究了机匣高效粗加工工艺。
针对侧铣与插铣两种加工方式,从切削厚度和刀具挠度两方面进行理论对比分析,并对切削力进行仿真对比分析。
结果表明,在相同切除率条件下,插铣径向切削力仅为侧铣的0.6倍,切削过程稳定。
3)根据机匣插铣加工工艺与机匣结构特点,规划了其插铣刀位轨迹,并在UG环境下生成了相应的插铣加工刀位轨迹。
此外,以UG为二次开发平台,实现了对插铣线的优化,可有效防止插铣加工过切。
关键词:机匣,高效加工,插铣,刀位轨迹,UG二次开发ABSTRACTAero-engine is the core component of the aircraft, and the casing which is a key part of the engine is difficult to manufacture because its extremely complicate structure. About 70% of the material is removed from blank to finished product, while the most material is removed in rough milling of casing. Therefore, high efficiency roughing of the casing is a key technology to realizing higher efficiency manufacturing and shorter developing cycle. Based on characteristics of casing, plunge milling was proposed to instead of traditional layered flank milling in this paper. And the part modeling, the CNC machining process modeling, the cut-location generation of the plunge milling in rough machining were studied.The main work and achievements of this thesis are as follows:1) The casing structure is analyzed, and on this basis, the entity model of casing is established using UG.2) The efficient rough machining of casing is studied for process planning. Between the side milling and plunge milling methods, cutting thickness and tools deflection were contrasted in theory and the cutting force were contrasted in simulation. The results show that, under the same resection rate, the radial cutting force of the plunge is only 0.6 times than the side milling, and the process is stable.3) According to the Plunge milling process and the structure characteristics of casing, the plunge milling cutter path was planned, which is then generated in UG. Additionally, aiming at overcut in plunge milling process, the optimization of the plunge milling line has been implemented using UG secondary development.Key words: Casing, Efficient processing, Plunge milling, tool path, UG Secondary development目录摘要 (I)ABSTRACT........................................................ I I第一章绪论 (1)1.1研究背景 (1)1.2国内外研究现状 (2)1.2.1 复杂结构类零件粗加工技术 (2)1.2.2 插铣工艺技术 (3)1.3 论文主要内容及章节安排 (5)第二章机匣造型 (7)2.1基于特征的建模方法 (7)2.2建模平台选择 (8)2.3机匣造型 (9)2.3.1 机匣模型分析 (9)2.3.2 机匣实体建模 (10)第三章机匣数控加工工艺 (15)3.1工艺规程编制原则 (15)3.2机匣零件的工艺特征 (15)3.3机匣加工工艺阶段的划分 (16)3.4机匣加工工艺路线制定 (16)3.5机匣粗加工工艺方案分析 (18)第四章机匣插铣粗加工刀具轨迹 (25)4.1 UG数控加工 (25)4.2刀具轨迹规划原则 (25)4.3刀具轨迹生成 (27)4.3.1 加工环境设定 (27)4.3.2 刀具轨迹生成 (27)4.3.3 程序后置处理 (33)4.4基于UG的插铣线优化 (35)总结 (38)致谢 (39)参考文献 (40)第一章绪论1.1研究背景航空发动机是飞机的“心脏”,其内部温度高,转速高,压力大,使用寿命长,构件的机械负荷和热负荷大,工作条件十分苛刻和复杂,其研究和发展工作的技术难度大,耗资多,周期长,是一个世界公认的、复杂的多学科综合性系统工程[1]。
- 1、下载文档前请自行甄别文档内容的完整性,平台不提供额外的编辑、内容补充、找答案等附加服务。
- 2、"仅部分预览"的文档,不可在线预览部分如存在完整性等问题,可反馈申请退款(可完整预览的文档不适用该条件!)。
- 3、如文档侵犯您的权益,请联系客服反馈,我们会尽快为您处理(人工客服工作时间:9:00-18:30)。
航空发动机机匣构件机械加工工艺优化
摘要:航空发动机是飞机的“心脏”也是一个国家加工制造技术的重要体现,在航
空发动机的加工制造过程中,航空发动机机匣构件是航空发动机加工制造的重点
也是难点之一,在航空发动机机匣构件的加工制造过程中由于其材料、机匣的机
构尺寸等的因素常常导致在航空发动机机匣构件加工完成后出现几何尺寸、形位
公差超差等的问题,严重影响了航空发动机机匣构件的加工质量,此外,航空发
动机机匣构件加工表面损伤会导致航空发动机机匣构件的使用寿命和使用强度等
都大打折扣,为提高航空发动机机匣构件的表面加工质量,需要在总结分析影响
航空发动机机匣构件表面完整性因素的基础上,做好对于航空发动机机匣构件加
工工艺的优化,提高航空发动机机匣构件加工后的表面完整性,确保航空发动机
机匣构件的加工质量。
关键词:航空发动机机匣构件;机械加工;加工工艺;优化
前言
航空发动机机匣构件是飞机发动机加工制造中的关键构件,由于其需要承受
极高的温度和负载力因此多使用钛合金、高温合金等的高强度合金作为其主要的
材质。
现今在航空发动机机匣构件的机械加工中容易出现表面完整性损伤,从而
对航空发动机机匣构件的使用寿命造成较大的影响,因此,应当通过对航空发动
机机匣构件的加工工艺进行优化,找出航空发动机机匣构件机械加工过程中的应
力集中点,改善航空发动机机匣构件机械加工过程中的应力分布以确保航空发动
机机匣构件加工表面的完整性,提高航空发动机机匣构件的抗疲劳使用寿命。
1 问题的提出和依据
航空工艺设计成本高、周期长,这两个特点不仅增加了传统工艺设计的难度,而且是传统工艺无法根本解决的。
因此,对发动机关键零部件传统工艺采用数字
化手段进行优化改造势在必行。
数字化的工艺系统可以保证在技术层面上制定产
品制造工艺时随时地、充分地考虑企业的制造环境,作业调度,车间底层控制,
工装夹具的配套以及毛坯的设计制造等所有工艺信息,将有关信息及时反馈到设
计单位并及时得到响应,生成适应性加工工艺,使制造过程达到全局优化,这是
未来航空发动机工艺的重要发展方向之一。
2 机匣工序优化的原则和要求
2.1 加工工序划分的一般原则
在数控机床上特别是在加工中心上加工零件,相对于传统机械加工方法,可
以做到工序相对集中,许多零件只需在一次装夹中就能完成全部工序加工。
但零
件的粗加工,特别是铸、锻零件的基准平面、定位面等部位的加工可先在普通机
床上完成,这样有利于发挥数控机床的特点、保持其精度、延长其使用寿命并降
低加工成本。
2.2 机匣工序优化的一些要求
工序相对集中是最有效的提高加工效率的措施,工序相对集中有利于发挥加
工中心的加工能力。
机匣加工的绝大多数金属去除量采用数控手段去除,军工企
业新引大量进口加工中心设备。
加工方案的确定可以说是由设计图纸的工艺性分
析和工序划分过程组成。
首先,设计图纸的工艺性分析重点在于零件进行数控加
工的方便性和可能性分析两个方面进行。
比如说,零件设计图制是否便于编制NC 程序,尺寸标注方面是否适应数控加工特点,以及尺寸要素提供是否充分,看是
否缺尺寸或给了封闭尺寸。
分析零件的加工精度能否得到满足。
其次分析零件各
个加工部位结构的工艺性是否符合数控加工的特点。
3 机匣数控加工工艺的优化概述
3.1 数控加工工艺优化途径
在整个机匣的加工过程中,数控加工工序是技术难度最大、加工耗时最长、
对加工质量影响最大的环节。
因此,在整个机匣加工工艺的优化的过程中,数控
加工工艺的优化占举足轻重的地位,数控加工工艺优化是整个机匣制造过程中最
见效益的一个环节。
3.2 仿真加工
在实际加工一个零件之前,利用软件在计算机上虚拟这个制造过程即为加工
仿真,它可以模拟整个机床加工过程,查出机床的不同部位、零件、工装夹具和
刀柄等之间是否会出现碰撞,模拟采用同机床控制系统一样的逻辑来操作,其运
行就像真实机床一样,同时在干涉校验方面也最具准确性,它作用包括清除编程
错误和改进切削效率,提高数控程序对硬材质零件、薄壁零件的切削性能。
4 机匣精车工序工艺性分析
4.1 机匣结构特点及其加工工艺性
机匣精车工序尺寸多达100多个、尺寸精度高、技术要求严格;内部构形复杂、环形槽区域狭窄,环形槽槽宽最小处仅为17.07mm,容刀空间狭小;环形槽
部位壁厚最小处仅为2.5mm,壁厚也不均匀;零件装夹方式采用下方几点压紧,
悬出部分高达400mm。
以上因素使得机匣零件在加工过程中的稳定性和刚性较差,抵抗径向变形的能力更差。
4.2 车加工加工刀具的选择
为确保加工过程和产品质量的稳定,前机匣精车工序采用专业刀具生产商提
供的机夹刀具,在选择过程中综合考虑了以下几个方面的问题:
(1)刀杆有足够的稳定性、刚性;(2)刀片有足够的强度、硬度和耐用度;(3)刀片尽可能采用标准刀片。
在此基础上确定以下几种刀杆:
(1)32×32×230 车刀刀杆配80度菱形刀片,用于粗加工端面、外圆及内孔;(2)32×32×230车刀刀杆配35度菱形刀片,用于精加工端面、外圆及内孔;(3)32×32×230 槽刀刀杆,用于加工各级环形槽;(4)32×32×230 T形槽刀杆共六种,分别加工各级T形槽;(5)32×32×230 45度刀杆,用于加工六级环形槽上部槽。
相应配置刀片均为标准型机夹刀片。
由于钛合金材料加工时具有弹性恢复大、化学亲和性高、导热性能差等特点,切削时热量主要由刀具传出、切削温度高、
粘刀现象严重。
刀具粘接磨损及扩散磨损较突出。
因此,选择不带镀覆层的机夹
刀片。
为避免加工过程中刀具的切削刃与零件的接触面积过大而产生的零件变形,切槽刀片宽度选择3mm、4mm、5mm为主,刀尖圆角不大于0.8mm。
4.3 UG-CAM车削加工模块在机匣精车加工中的应用
数控车削加工是一种重要的数控加工方法,主要用于轴类、盘类等回转类零
件的加工。
在数控车削程序设计过程中,最重要的两个环节是:一方面确保加工
路线合理,数控程序准确和完整;另一方面要求选择可靠的刀具和合理的切削参数。
考虑到机匣内腔型面包括六级环形槽、环形槽上下表面的T型槽及其环形槽
之间的型面,在进行UG-CAM车加工数控程序设计时主要应用其中的车端面、粗车、精车、车槽等几种车削加工操作。
5延伸机匣加工工艺优化的目标
工艺方案技术经济性分析的一个重要应用方面是在工艺流程设计过程中,对
不同的工艺方案进行评价。
对绝大多数产品来说,工艺过程有许多可变因素,在
工艺设计中,如何确定这些可变因素,使制造过程最合理,这就是工艺过程优化
研究的问题。
机械制造工艺过程除要保证制造质量之外,还必须实现高的生产效
率和低的生产成本,这就是工艺过程优化的主要目标。
6结束语
航空发动机机匣构件的加工是发动机加工中的重点也是难点,本文在分析航
空发动机机匣构件加工中各加工因素对于加工精度影响的基础上,通过对航空发
动机机匣构件的加工工艺进行优化,以提高航空发动机机匣构件加工后的表面完
整性,提高加工质量。
参考文献:
[1]王晓静,张松,贾秀杰.航空发动机整体机匣铣-车复合加工工艺优化[J].计
算机集成制造系统,2011,17(7):1460-1465.
[2]李国明.航空发动机机匣加工工艺研究[J].中国新技术新产品,2012(13):120.。