材料强化基本原理
金属材料的四大强化机制

金属材料的四大强化机制金属材料的强化机制可真是个让人惊奇的领域,大家有没有想过,金属为什么有的坚固得像铁桶一样,而有的却软得像泥巴?今天就来聊聊这四大强化机制,轻松一下,顺便长长见识。
首先说说固溶强化,这东西听起来挺高大上的,实际上就是把不同的原子混在一起,让金属更坚固。
想象一下,一个本来单打独斗的铁小子,突然被一群不同的小伙伴包围,变得威风凛凛。
这就是固溶强化的魅力,杂质原子进入金属的晶格中,打乱了原本的规律,使得金属的位移变得困难,强度自然就上来了,嘿,这就是一招不错的组合拳。
要知道,金属的晶格就像是一座座房子,杂质原子就像是搬进来的新住户,虽然一开始可能有点不和谐,但久而久之,大家就能和谐共处,形成一种新的平衡。
接下来要说的是第二种,叫做强化相,听起来是不是也很神秘?其实它的原理也不复杂。
想象一下,如果金属的内部长出了“贵族”般的强化相,那就意味着这金属在碰到外力时,不容易被击垮。
强化相就像是战士们在金属的内部组成的小团队,它们能有效阻挡外部的侵袭,像是给金属穿上了一层厚厚的铠甲,让它看起来更强大。
这种机制通常在合金中比较常见,金属与金属之间相互作用,形成不同的相,增强了整体的强度。
这样的金属材料,仿佛就像是一个披着迷彩的超级英雄,随时准备迎接挑战。
再说说第三种机制,叫做析出强化,听上去是不是有点像古代的军队在战斗?其实就是在金属中让一些小颗粒析出来,形成一种“埋伏”,这些颗粒就像是潜伏在战场上的小兵,外力一来,它们就会瞬间出击,增加金属的强度。
这样一来,金属的内部就形成了一个坚固的网络,极大地提升了抗拉强度,嘿,有点像是给金属增添了几分底气。
析出强化的好处在于,不需要太高的温度就能达到预期效果,真是个省事儿的好办法。
最后一个就是叫做晶粒细化,听着是不是像是一道菜的做法?其实这也是强化金属的重要手段。
想象一下,如果金属的晶粒变得更小,就像是把一个大蛋糕切成很多小块,这样一来,每一块蛋糕都更坚韧。
细晶强化的原理

细晶强化的原理
细晶强化是一种材料强化技术,通过在材料结构中形成细小晶粒,提高材料的强度和硬度。
该技术的原理是通过控制材料的热处理过程和添加合适的合金元素,使晶粒尺寸显著减小。
在材料加热过程中,晶粒会开始生长,并逐渐增大。
晶粒的尺寸直接影响材料的力学性能,通常情况下,晶粒尺寸越小,材料的强度和硬度越高。
因此,通过控制加热温度和保温时间,可以限制晶粒生长的速率,使晶粒尺寸保持在一个较小的范围内。
此外,通过添加合适的合金元素,可以进一步限制晶粒的生长。
合金元素可以在晶界处形成所谓的强化相,阻碍晶粒的生长,从而细化晶粒尺寸。
强化相的形成可以通过固溶、析出和相变等方式实现。
细晶强化技术有助于提高材料的强度和硬度,同时还可以改善材料的塑性和耐磨性等性能。
然而,过度细化晶粒可能导致材料的韧性下降,因此在实际应用中需要综合考虑材料的各种性能要求。
总结而言,细晶强化通过控制材料的热处理过程和添加合适的合金元素,使晶粒尺寸减小,从而提高材料的强度和硬度。
这一技术在材料科学和工程领域具有广泛的应用前景。
复合材料增强原理
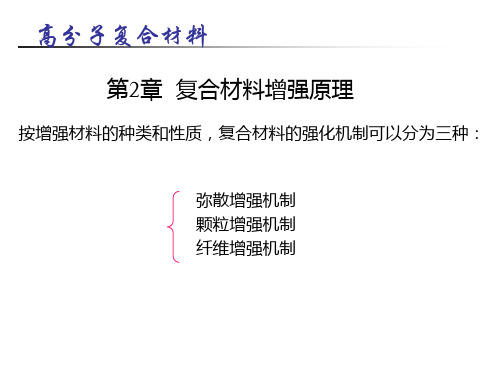
高分子复合材料
图2.4 短纤维周围的应变
高分子复合材料
裂纹扩展方向
纤维断裂
当材料受到较大应力时,一些有裂纹的纤维可能断裂,但基 体能阻碍裂纹扩展并改变裂纹扩展方向。
高分子复合材料
当纤维与基体有适当的界面结合强度时,纤维受力断裂后被从 基体中拔出,需克服基体对纤维的粘接力,使材料的断裂强度 提高。
高分子复合材料
为了达到纤维增强的效果,须遵循以下原则:
纤维的强度和弹性模量应远高于基体; 纤维与基体间应有一定的界面结合强度,以保证基体所承 受的载荷能通过界面传递给纤维,并防止脆性断裂; 纤维的排列方向要与构件的受力方向一致; 纤维与基体的热胀系数应匹配; 纤维与基体不能发生使结合强度降低的化学反应; 纤维所占体积分数、纤维长度和直径及长径比等必须满足 一定要求。
图2.1 颗粒起着阻碍基体位错运动作用示意图
高分子复合材料
颗粒增强机制 颗粒增强复合材料:尺寸较大(>1μm)的坚硬颗粒及基体 复合而成 粒子直径为1~50μm,体积分数>20% 机理: 颗粒阻碍基体位错运动强化
不均匀变形引起位错增殖强化
与弥散增强机制的不同点: 载荷主要由基体承担,但颗粒也承受载荷并约束变形 强化效果:取决于粒子直径、体长度Lc和长径比Lc/d
高分子复合材料
在单向连续纤维增强复合材料中,复合材料中组分承 载应力表达式:
f Af V f E f Pm m Am Vm Em
Pf
纤维/基体弹性模量↑,纤维体积含量↑,则纤 维承载越大
金属材料的四种强化方式最全总结
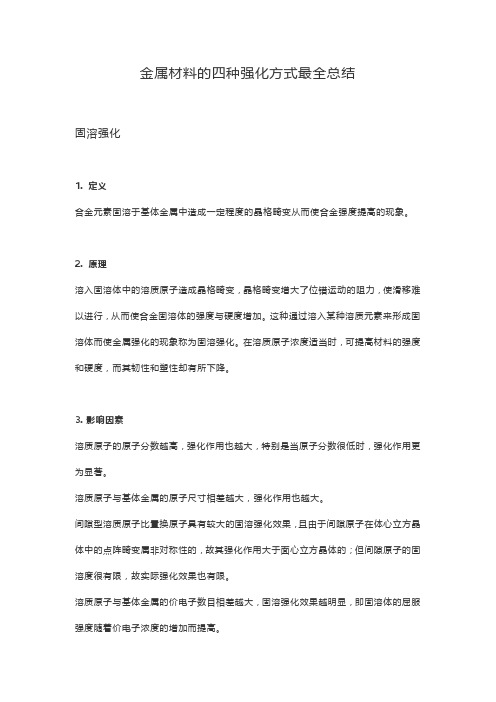
金属材料的四种强化方式最全总结固溶强化1. 定义合金元素固溶于基体金属中造成一定程度的晶格畸变从而使合金强度提高的现象。
2. 原理溶入固溶体中的溶质原子造成晶格畸变,晶格畸变增大了位错运动的阻力,使滑移难以进行,从而使合金固溶体的强度与硬度增加。
这种通过溶入某种溶质元素来形成固溶体而使金属强化的现象称为固溶强化。
在溶质原子浓度适当时,可提高材料的强度和硬度,而其韧性和塑性却有所下降。
3. 影响因素溶质原子的原子分数越高,强化作用也越大,特别是当原子分数很低时,强化作用更为显著。
溶质原子与基体金属的原子尺寸相差越大,强化作用也越大。
间隙型溶质原子比置换原子具有较大的固溶强化效果,且由于间隙原子在体心立方晶体中的点阵畸变属非对称性的,故其强化作用大于面心立方晶体的;但间隙原子的固溶度很有限,故实际强化效果也有限。
溶质原子与基体金属的价电子数目相差越大,固溶强化效果越明显,即固溶体的屈服强度随着价电子浓度的增加而提高。
4. 固溶强化的程度主要取决于以下因素基体原子和溶质原子之间的尺寸差别。
尺寸差别越大,原始晶体结构受到的干扰就越大,位错滑移就越困难。
合金元素的量。
加入的合金元素越多,强化效果越大。
如果加入过多太大或太小的原子,就会超过溶解度。
这就涉及到另一种强化机制,分散相强化。
间隙型溶质原子比置换型原子具有更大的固溶强化效果。
溶质原子与基体金属的价电子数相差越大,固溶强化作用越显著。
5. 效果屈服强度、拉伸强度和硬度都要强于纯金属;大部分情况下,延展性低于纯金属;导电性比纯金属低很多;抗蠕变,或者在高温下的强度损失,通过固溶强化可以得到改善。
加工硬化1. 定义随着冷变形程度的增加,金属材料强度和硬度提高,但塑性、韧性有所下降。
2. 简介金属材料在再结晶温度以下塑性变形时强度和硬度升高,而塑性和韧性降低的现象。
又称冷作硬化。
产生原因是,金属在塑性变形时,晶粒发生滑移,出现位错的缠结,使晶粒拉长、破碎和纤维化,金属内部产生了残余应力等。
第十章 材料的强化

第十部分材料的强化韧性是材料变形和断裂过程中吸收能量的能力,它是强度和塑性的综合表现;强度是材料抵抗变形和断裂的能力,塑性则表示材料断裂时总的塑变程度.材料在塑性变形和断裂全过程中吸收能量的多少表示韧性的高低.金属材料缺口试样落锤冲击试验侧得的韧性指标称为冲击韧性.高分子材料冲击试验的韧性指标通常称为冲击强度或冲击韧度.第一节材料强化基本原理1、固溶强化纯金属经适当的合金化后强度、硬度提高的现象根据强化机理可分为无序固溶体和有序固溶体固溶强化的特点:(1)溶质原子的原子数分数越大,强化作用越大;(2)溶质原子与基体金属原子尺寸相差越大,强化作用越大;(3)间隙型溶质原子比置换原子有更大的固溶强化作用;(3)溶质原子与基体金属的价电子数相差越大,固溶强化越明显。
2、细晶强化多晶体金属的晶粒通常是大角度晶界,相邻取向不同的的晶粒受力发生塑性变形时,部分晶粒内部的位错先开动,并沿一定晶体学平面滑移和增殖,位错在晶界前被阻挡,当晶粒细化时,需要更大外加力才能使材料发生塑性变形,从而达到强化的目的。
霍尔-佩奇公式:σs=σ+K y d-1/23、位错强化(1)晶体中的位错达到一定值后,位错间的弹性交互作用增加了位错运动的阻力。
可以有效地提高金属的强度。
流变应力τ和位错密度的关系:(2)加工硬化定义:金属经冷加工变形后,其强度、硬度增加、塑性降低。
单晶体的典型加工硬化曲线:τ~θ 曲线的斜率θ=d τ/d θ称为“加工硬化速率”·曲线明显可分为三个阶段:I.易滑移阶段:发生单滑移,位错移动和增殖所遇到的阻力很小,θI很低,约为10-4G数量级。
II.线性硬化阶段:发生多系滑移,位错运动困难,θII远大于θI约为G/100—G/300 ,并接近于一常数。
III.抛物线硬化阶段:与位错的多滑移过程有关,θIII随应变增加而降低,应力应变曲线变为抛物线。
4、沉淀相颗粒强化当第二相以细小弥散的微粒均匀分布在基体相中时,将产生显著的强化作用,通常将微粒分成不可变形的和可变形的两类。
金属材料的喷丸强化原理及其强化机理综述
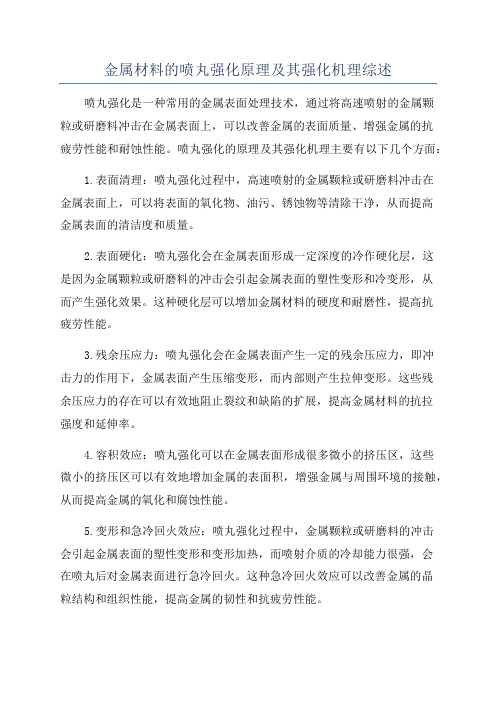
金属材料的喷丸强化原理及其强化机理综述喷丸强化是一种常用的金属表面处理技术,通过将高速喷射的金属颗粒或研磨料冲击在金属表面上,可以改善金属的表面质量、增强金属的抗疲劳性能和耐蚀性能。
喷丸强化的原理及其强化机理主要有以下几个方面:1.表面清理:喷丸强化过程中,高速喷射的金属颗粒或研磨料冲击在金属表面上,可以将表面的氧化物、油污、锈蚀物等清除干净,从而提高金属表面的清洁度和质量。
2.表面硬化:喷丸强化会在金属表面形成一定深度的冷作硬化层,这是因为金属颗粒或研磨料的冲击会引起金属表面的塑性变形和冷变形,从而产生强化效果。
这种硬化层可以增加金属材料的硬度和耐磨性,提高抗疲劳性能。
3.残余压应力:喷丸强化会在金属表面产生一定的残余压应力,即冲击力的作用下,金属表面产生压缩变形,而内部则产生拉伸变形。
这些残余压应力的存在可以有效地阻止裂纹和缺陷的扩展,提高金属材料的抗拉强度和延伸率。
4.容积效应:喷丸强化可以在金属表面形成很多微小的挤压区,这些微小的挤压区可以有效地增加金属的表面积,增强金属与周围环境的接触,从而提高金属的氧化和腐蚀性能。
5.变形和急冷回火效应:喷丸强化过程中,金属颗粒或研磨料的冲击会引起金属表面的塑性变形和变形加热,而喷射介质的冷却能力很强,会在喷丸后对金属表面进行急冷回火。
这种急冷回火效应可以改善金属的晶粒结构和组织性能,提高金属的韧性和抗疲劳性能。
总之,喷丸强化通过冲击、压缩、冷变形和急冷回火等机制,对金属材料的表面和组织进行改善和增强,从而达到提高金属的性能和延长使用寿命的目的。
这种技术在航空、航天、能源、汽车等领域有着广泛的应用前景。
弥散强化的原理
弥散强化的原理弥散强化是一种材料强度增强的方法,通过在材料中引入弥散相来增强材料的性能。
在材料科学和工程中,弥散强化是一种常见的技术,可以显著提高材料的力学性能和耐磨性。
本文将就弥散强化的原理进行详细介绍。
弥散强化的原理主要是利用弥散相对基体材料起到阻碍位错运动和提高位错密度的作用,从而增强材料的强度。
弥散相可以是固溶体、粒子或纤维等,其尺寸通常在纳米尺度或微米尺度。
当材料受到外力作用时,弥散相可以阻碍位错的移动,使得材料的塑性变形受到限制,从而提高材料的强度和硬度。
在弥散强化的过程中,弥散相的尺寸和分布对材料性能起着至关重要的作用。
通常情况下,弥散相的尺寸越小,分布越均匀,对材料的强化效果就越显著。
此外,弥散相与基体材料之间的界面结合情况也对强化效果有着重要影响。
良好的界面结合可以有效传递外力,提高材料的强度和韧性。
弥散强化的原理还包括位错密度的增加。
当弥散相存在于材料中时,它可以吸引位错并增加位错密度,从而阻碍位错的移动,提高材料的强度。
此外,弥散相还可以在材料中引起应力场的分布不均匀,从而影响位错的运动和堆积,对材料的强化起到重要作用。
弥散强化的原理不仅适用于金属材料,还适用于陶瓷、聚合物等材料。
在不同类型的材料中,弥散强化的原理可能会有所不同,但其基本原理都是利用弥散相对基体材料的强化作用。
因此,弥散强化是一种普遍适用的强化方法,可以在不同材料中发挥重要作用。
总的来说,弥散强化的原理是通过引入弥散相来阻碍位错的移动和增加位错密度,从而提高材料的强度和硬度。
弥散相的尺寸、分布和界面结合情况对强化效果起着重要作用。
弥散强化是一种重要的材料强化方法,可以广泛应用于各种材料中,对提高材料的性能具有重要意义。
弥散强化的原理是材料科学和工程领域的重要内容,对于材料的设计和应用具有重要意义。
通过深入理解弥散强化的原理,可以更好地指导材料的设计和制备,提高材料的性能和可靠性。
因此,对弥散强化的原理进行深入研究具有重要的理论和实际意义。
材料强化的4种方法原理
材料强化的4种方法原理材料强化是通过各种手段提高材料力学性能的方法,常用的强化方法有四种:一、固溶强化固溶强化是在基体金属内溶解强化元素,生成固溶体的一种强化手段。
由于不同原子大小不同,溶质原子的存在會對基体金属矩阵产生扭曲应力和扰动,增加材料的抗变形能力。
常见的固溶强化系统有:铁素体中的碳原子生成碳素体、铜中的锌生成黄铜、铝中的镁生成的析出硬化铝镁合金等。
固溶强化的机理是:溶质原子置换矩阵原子后,由于原子大小差异,会对周围基体原子产生弹性变形场,使位错运动难度增加,从而提高合金的力学性能。
一般来说,溶质原子与基体原子大小相差不超过15%,溶解度不超过几个原子百分比时,固溶强化效果最好。
二、析出强化析出强化是通过在基体金属中生成细小、分散的第二相颗粒来达到强化目的。
析出相颗粒的存在能够阻碍位错运动,提高合金的强度。
析出相的大小、形态、分布状况等参数对强化效果有重要影响。
析出强化的典型合金系统有铝钢中的硝基碳窜、铝合金中的Mg2Si相等。
析出相颗粒一般维持在10-100纳米大小范围,既能提供强化效果,又不损害塑性。
过度析出会导致合金脆化。
合理控制热处理工艺是获得优良析出强化的关键。
三、纤维强化纤维强化是在基体金属中添加高强度、高模量的纤维材料,利用纤维阻挡裂纹扩展来提高力学性能。
常用的纤维有碳纤维、玻璃纤维等。
根据纤维在基体中的分散情况,可分为不连续增强和连续增强两种。
纤维强化复合材料中,载荷主要由纤维承担,基体起固定纤维、传递载荷的作用。
强化效果与纤维量、长度、取向等参数有关。
纤维与基体的界面粘结力也会显著影响材料强度。
四、粒界强化粒界强化是通过细化晶粒尺寸来提高力学性能。
根据哈尔-佩奇关系,随着晶粒尺寸的减小,合金的屈服强度会提高。
这是因为粒界能阻碍位错在晶粒内的运动,使材料变形难度增加。
常见的粒界强化方法有合金元素微合金化、热处理调质、严重塑性变形等。
新兴的奥氏体不锈钢即采用了超细晶粒结构来达到高强度。
金属材料的喷丸强化原理及其强化机理综述
金属材料的喷丸强化原理及其强化机理综述1 喷丸强化原理喷丸强化(Peening)是一种表面处理技术,该技术可以使金属或非金属材料表面几乎承受和耐受机械强度的变化和维护的方法。
它通过喷丸装置形成的动态压痕来改善材料的性能,以降低环境和表面潜在的威胁,从而提高整体结构的强度和寿命。
喷丸强化是在表面处理中使用力学加工的过程,可以应用于铝合金、碳钢、不锈钢和双向淬火钢等金属材料,它可以有效地提高材料的表面硬度和强度。
喷丸强化的原理是,使用压痕和动能来改变和完善表面,从而改善该表面的性能和机械性能,可以解决多种结构和断裂的问题,并可以提高外形精度和耐磨持久性。
2 喷丸强化机理喷丸强化机理涉及多种因素,如极化物质,弹性能,光反射表面,颗粒聚集度,弹性和摩擦力等。
其中,极化物质是喷丸强化的重要机理,极化物质可以将形成的压痕向四周传播以改善表面外观,并增强表面的硬度。
通过电荷分布模式的形成,还可以改变结构的几何维度,使表面形成不同形状的压痕,从而改善材料的表面硬度和耐久性。
弹性能的改善是另一个重要的强化机理,喷丸可以形成压痕磨损表面,从而改善不同表面的弹性能,降低撞击速度对材料的损失,使材料的表面更加平滑,增强材料的机械强度和耐久性。
光反射表面的改善是另一个喷丸强化机理,由于喷丸刻蚀表面形成了凹凸不平表面,使反射光线传播和反射更多,以提高表面的亮度和抗反射能力。
最后,喷丸强化还可以改变表面的密度,材料的密度是影响机械强度的重要因素。
而喷丸处理可以改变表面结构和形状,从而提高表面的密度,并使其结构更加均匀,从而提高材料的机械强度和耐久性。
3 总结喷丸强化是一种常用的表面处理技术,可以有效地提高金属材料表面的硬度和强度,对材料表面的耐磨性有良好的改善作用。
它主要依靠极化物质、弹性能、光反射表面和密度等机制来改善材料表面的性能,从而提高材料的用途和加工性。
二强玻璃强化原理
二强玻璃强化原理二强玻璃是一种具有更高强度和耐冲击性能的特种玻璃材料。
它在建筑、汽车和电子设备等领域得到广泛应用。
那么,二强玻璃的强化原理是什么呢?二强玻璃的强化原理主要涉及到热处理过程中的快速冷却和表面压应力的形成。
下面我们将详细介绍二强玻璃的强化原理。
二强玻璃的制备过程中需要进行热处理。
热处理是通过加热和冷却玻璃来改变其物理特性的一种方法。
在二强玻璃的制备中,玻璃首先被加热到接近软化温度,然后迅速冷却。
这种快速冷却过程被称为淬火。
淬火可以使玻璃表面形成压应力,从而增强其强度。
淬火过程中形成的压应力是二强玻璃强化的关键。
在加热过程中,玻璃表面的温度升高,而内部温度升高相对较慢。
当玻璃迅速冷却时,内部和表面的温度差异导致玻璃表面形成压应力。
这种压应力可以抵消外部冲击力,使玻璃具有更高的抗冲击性能。
二强玻璃的强化原理还涉及到玻璃化转变温度。
玻璃化转变温度是指玻璃从液态过渡到固态的温度范围。
在加热过程中,当玻璃的温度超过玻璃化转变温度时,玻璃的分子排列会发生改变,形成一种类似于固态的非晶态结构。
这种非晶态结构具有更高的强度和硬度。
二强玻璃的强化原理主要包括快速冷却和表面压应力的形成。
通过加热和迅速冷却的方式,使玻璃表面形成压应力,从而增强玻璃的强度和耐冲击性能。
这种强化原理使得二强玻璃在各个领域得到广泛应用,为人们的生活和工作带来了更大的安全性和便利性。
值得注意的是,虽然二强玻璃具有更高的强度和耐冲击性能,但在使用过程中仍需注意避免过度冲击和剧烈温度变化,以免造成破裂或损坏。
此外,在二强玻璃的制备和使用过程中,也需要控制好热处理的温度和时间,以确保玻璃的质量和性能。
二强玻璃的强化原理是通过加热和快速冷却的方式,使玻璃表面形成压应力,从而增强其强度和耐冲击性能。
这种强化原理使得二强玻璃成为一种重要的特种玻璃材料,在建筑、汽车和电子设备等领域得到广泛应用。
在使用二强玻璃时,我们需要注意避免过度冲击和剧烈温度变化,以确保其安全性和可靠性。
- 1、下载文档前请自行甄别文档内容的完整性,平台不提供额外的编辑、内容补充、找答案等附加服务。
- 2、"仅部分预览"的文档,不可在线预览部分如存在完整性等问题,可反馈申请退款(可完整预览的文档不适用该条件!)。
- 3、如文档侵犯您的权益,请联系客服反馈,我们会尽快为您处理(人工客服工作时间:9:00-18:30)。
第十章材料的强韧化节材料强化基本原理结合键和原子排列方式的不同,是金属材料、陶瓷材料、高分子材料力学性能不同的根本原因。
通过改变材料的内制材料性能的目的。
不同种类的材料,提高其强度的机理、方法也不同。
一、金属材料的强化原理纯金属经过适当的合金化后强度、硬度提高的现象,称为固溶原因可归结于溶质原子和位错的交互作用,这些作用起源于溶质引发的局变。
固溶体可分为无序固溶体和有序固溶体,其强化机理也不相同。
(1)无序固溶强化固溶强化的实质是溶质原子的长程位错的交互作用导致致错运动受阻。
溶质相位错的交互作用是二者应力场用。
作用的大小要看溶质本身及溶质与基体之间的交互作用,这种作用使成弯曲形状。
如图10—l所示.图中的A、B、C表示溶质原子强烈地钉扎了位错。
x—x',A的乎直位错线,被钉后呈观曲线形状。
处于位错线上的少数溶质原子与位互作用很强,这些原子允许位错线的局部曲率远大于根据平均内应力求出钉扎的第一个效应就是使位错线呈曲折形状。
相对于x—x'的偏离为x在方向的外加切应力τ作用下,由于B点位错张力的协助作用,将使ABC段AB'C,在B'处又被钉扎起来。
位错之所以能够这样弯曲,其原因是因位增加而升高的弹件能被强钉扎所释放的能量抵偿旧有余,位错的弹性能反低.位错经热激活可以脱钉,因而被钉扎时相对处于低能态。
在切应力τ动到AB'C.ABC和AB'C是相邻的平衡位置,阻力最大在位错处于中间位置AC时产生,外加切应力要克服这样的阻。
若AC≈2y,ABC比2y略大,近似地当作2y。
由ABC变为AC方面要脱钉需要能量,另一方面要缩短位错长度释放是位错脱扎所需能量;EI为单位长度位错由于加长而升高的能量,EI与Eb相比小而略去。
由ABC变为AC,平均位力需要做功为τb(2y)·x/2,故1看,沿着xx'方向,单位长度上有1/y个溶质原子。
用柯氏气团的概念,如果位错和溶质原子交互作用能为U0,溶质钉扎将降低的能量为所以设C为溶质原子百分数,在滑移面单位面积上有1/62个原子,其中有C/62个为溶质原子。
又注意到面积xy上所以C/b2≈1/xy,所以式(10—4)可写为此式表明在强钉扎下,推动位错所需的临界切应力既与溶质-位错相互作用能U0。
成正比也与溶质浓度C成正比。
合金在常温下的固溶强化符合这样的规律。
序固溶强化当一个位错在具有短程有序因溶体中运动时,由异类原子对构成的局部有序受到破坏,引起能量升高,必须付出破量的代价,位错才能运动。
若位错扫过单位面积而增高的能量为E,则位错运动的阻力是设固溶体短程有序度为a,N为二元合金的原子总数,x为B组元的摩尔分数,l-x为A组元的摩尔分数,w是原子对于面心立方结构的短程有序固溶体,位错扫过(111)上的单位面积提高的能量是位晶胞参数。
位错所遇到的阻切应力应等于E/b,故21/2。
这是面心立方结构二元合金具有短程有序度a时所产生的强化作用。
晶强化多晶体金属的晶粒边界通常是大角度晶界,相邻的不同取向的晶粒受力产生塑性变形时,部分施密特(Schmid,E.)错源先开动,并沿一定晶面产生滑移和增殖。
滑移至晶界前的位错被晶界阻挡。
这样一个晶粒的塑性变形就无法直接中去,且造成塑变晶粒内位错塞积。
在外力作用下,晶界上的位错塞积产生一个应力场,可以作为激活相邻晶粒内位。
当应力场作用于位错源的作用力等于位错开动的临界应力时,相邻晶粒内的位错源开动、滑移与增殖,造成塑件形场强度与塞积位错数目和外加切应力值有关,而塞积位错数目正比于晶粒尺寸,因此当金属材料的晶粒变细时,必须激活相邻晶粒内位错源,这就意味着,细晶粒产生塑性受形要求更高的外加作用力,也就体现了细晶粒对金属材料强在霍尔—佩奇(Hall,E,O-Petch,N.J.)公式。
中为晶粒平均直径,Ky反映了位错被溶质原子的订扎程度和塑性形变时可以参加滑移的滑移系数目,滑移系少则Ky大。
应该指出,霍尔—佩奇(Hall,E,O-Petch,N.J.)公式适用的晶粒尺寸有一个界限,例如0.3—400μm。
因为d<0.的晶粒内提供不出足够数量的位错,以构成足够强度的应力集中应力场,而比400μm更为粗大的晶粒再多些塞积位中应力场强度的影响也不大。
3.位错强化从金属晶体完整的概念出发.提高强度最为直接的方法是消除其中所存在的缺陷,主要是消除位错,制造完整晶体陷理论又指出,晶体中的位错密度ρ达到一定值后也可以有效地提高金属的强度。
位借间的弹性交互作用可造成位错为强度的增高。
通过热处理和冷塑性变形以提高位错密度是钢材强化的重要手段之一。
的位错的分布比较均匀时,流变应力τ和位错密度间存在培莱-赫许(Bailey,J.E-Hirsch,P.B)关系式.即为位错密度;G为切变模量;b为柏氏矢量;a为系数,多晶体铁素体a=0.4;参量τ0表示位错交互作用以外的因成的阻力。
由上式可见.当ρ增高时,τ也增大。
在金属晶体受到外力作用时,内部增殖大量位错。
位错的增殖是塑以流变应力的增大率与塑性应变的增大率有关,即流变应力的增大率取决于塑性形变引起的位错密度的增大率。
4.沉淀相颗粒强化多相合金的高强度基础是由位错与沉淀析出相的交互作用而产生的,弥散分布的沉淀相颗粒是阻碍位错运动的最有效的障碍物。
当强化效果等效于固溶强化时,它对塑性的削弱作用用比较小。
沉淀相颗粒强化效果视颗粒在钢材屈服时本身可否塑变而定,另外,第二相的分布方式也可有不同的强化效应。
(1)可形变颗粒的强化作用所谓可形变颗粒系指这沉淀相通常处于与母相共格状态。
颗粒尺寸小<15nm,可为运动的位错所切割。
因此可变形颗粒的强化效应与以下几个方面有关:①第二相颗粒具有不同于基体的点阵结构和点阵常数,当位错切过共格颗粒时,在滑移面上造成错配的原子排列,因而增大位错运动的作功;②沉淀相颗粒的共格应力场与位错的应力场之间产生弹性交互作用,位错通过共格应变区时,会产生一定的强化效应;③位错切过颗粒后形成滑移台阶,增加界面能,加大位错运动的能量消耗;④当颗粒的弹性切变模量高于基体时,位错进入沉淀相便增大位错自身的弹性畸变能,引起位错的能量和线张力变大,位错运动遇到更大的阻力.述分析表明:与基体相完全共格的沉淀相颗粒具有显著的强化效应。
(2)不可形变颗粒的强化作用不可变形颗粒具有较高硬度和一定尺寸并与母相部分共格或非共格的沉淀相颗粒。
位错遇到这类颗粒无法切过颗粒,只能沿着颗粒围绕,绕过的最大角θ可达到π,每一条位错绕过粒颗后留下一个位错圈(环),面后恢复平直状态,继续向前推移。
位错的能量是正比于其长度的,因此位错遇到颗粒,滑移受到阻碍面发生弯曲时,必须增高外加切应力以克服位错弯曲而引起的位错线张力的加大。
作用于位错线的切应力增值△τbs与位错线张力增量2Tsinθ的平衡表明,附加切应力τ是以补偿位错线弯成曲线长度,和绕过角θ所引起的能量增大,于是可有,当θ很小时sin/θ/2≈θ/2,s≈λp=rθ,λp为有效的颗粒间距,r为位错弯曲线的曲率半径,又T=1/2·Gb2得到△T=Gb/rθ,b为柏氏矢量.当位错弯曲得使r1=λp/2时,τ将为最大,或者说要使位错围绕颗粒所需要的最大附加切应力,即临界切应力为这就是不可变形颗粒对屈服强度的贡献。
这个位错围绕颗粒的强化机制是由奥罗万(Orowan,E)提出的,是一个比较成功的理论,也得到实验上的证实。
可见位错绕过粒子所需的切应力反比于颗粒间距.故当沉淀相颗粒的半径为r,体积分数为f,且在基体上是弥散分布时,那么可导出沉淀相颗粒强化对合金屈服强度的贡献,即f很小时可简化为综上所述,不可变形颗粒的强化作用反比于颗粒尺寸,而正比于其数目。
(3)粗大的沉淀相群体的强化作用在钢中粗大的沉淀相颗粒成群分布,如奥氏体不锈钢的δ相和碳钢或低合金钢中的珠光体会产生显著的强化作用。
当两个相所组成的组织是一种不同晶粒尺寸的多晶体时,一个相晶粒的预先形成可以明显地影响另一个相晶粒的成长,可以规定另一个相的生长范围,并有可能引起另一个相晶粒细化,沉淀相的作用大小与沉淀相的形态、分布和数量,以及每一沉淀物承受外力的能力有关。
由两个相混合组成的组织的强化主要是由于:①纤维强化;②—个相对另一个相起阻碍塑性变形的作用,从而导致另一个相更大的塑性形变和加工硬化,直到末形变的相开始形变为止;③在沉淀相之间颗粒可由不同的位错增殖机制效应引入新的位错。
5.强化作用的更加如上所述,各个强化机制的作用对强度贡献虽有不同,但所起作用是一致的,而对其他性能,特别是塑性则有差异。
从此也可以看出,霍尔—佩奇(Hall,E,O-Petch,N.J.)公式中的σ1内容是很复杂的,它包含着除开细晶强化作用以外的其他的所有强化因子,可写为式中;σ1取决于温度和形变速率,是与P—N力密切相关的.σ2是为组织因素决定的,可有式中:△σsh、△σph和△σdh相应的为固溶强化、沉淀强化和位错强化所引起的强度增量。
影响△σsh、△σph和△σdh的因素是多方面的,在当前要准确计算尚有不少困难。
但对于具体钢种可以通过实验予以测定。
图l0—6为铁素体+珠光体型C—Mn钢于不同C量时各个强化因子对强度的贡献。
二、高聚物的强化原理高分子材料的强化主要有以下几个方面:(1)引入极性基链间作用力对高聚物的机械强度有着很大的影响,对不同的高聚物,为了比较它们分子链间的作用力的大小,一般取长度为0.5nm,配位数为4时计算出来的作用能数值。
链上极性部分越多,极性越强,链间作用力就越大;(2)链段交联在环境温度高于玻璃温度Tg时,随着交联程度的增加,交联键的平均距离缩短,高分子材料的断裂强度将会进一步增大,屈服强度和弹性模量也会大幅度提高;(3)结晶度和取向结晶性高分子材料的结晶度和大分子取向对其强度有着明显的影响.实际的结晶性尚聚物中存在着晶区和非晶区,一个大分子链可以贯穿好几个晶区和非晶区。
在非晶区分子链是卷曲和互相缠结的,因而当结晶性高聚物受力时,可使应力分散并导致分子微晶取向化,使强度得到提高。
结晶度的增大使高分子的密度增大,而且微晶还会起到物理交联的作用,使应力均匀分布,断裂强度上升;(4)定向聚合定向聚合是提高高分子材料结构上均一性的有效方法,能使高聚物的密度、拉伸弹性模量和物理性能、机械性能都有了提高。
第二节材料的韧化基本机理一、金属材料的韧化原理韧性是断裂过程的能量参量,是材料强度与塑性的作用综合表现,当不考虑外因时,断裂过程实际上包括裂纹形核所要求的塑性形变,以及裂纹的形核和扩展。
通常是以裂纹形核和扩展的能量消耗或裂纹扩展抗力来标志材料韧性的。
裂纹形核前的塑性形变、裂纹的扩展是与金属组织结构密切相关的,从而反映出不同的断裂方式,以及不同的断裂机制;它涉及到位错的运动,位错间弹性交互作用,位错与溶质原子和沉淀相弹性交互作用,以及组织形态,其中包括基体、沉淀相和晶界的作用。