干式壳管式蒸发器的设计过程
蒸发器壳程和管程

蒸发器壳程和管程下载温馨提示:该文档是我店铺精心编制而成,希望大家下载以后,能够帮助大家解决实际的问题。
文档下载后可定制随意修改,请根据实际需要进行相应的调整和使用,谢谢!并且,本店铺为大家提供各种各样类型的实用资料,如教育随笔、日记赏析、句子摘抄、古诗大全、经典美文、话题作文、工作总结、词语解析、文案摘录、其他资料等等,如想了解不同资料格式和写法,敬请关注!Download tips: This document is carefully compiled by the editor. I hope that after you download them, they can help yousolve practical problems. The document can be customized and modified after downloading, please adjust and use it according to actual needs, thank you!In addition, our shop provides you with various types of practical materials, such as educational essays, diary appreciation, sentence excerpts, ancient poems, classic articles, topic composition, work summary, word parsing, copy excerpts,other materials and so on, want to know different data formats and writing methods, please pay attention!蒸发器在化工装置中有着广泛的应用,其中蒸发器壳程和管程作为蒸发器的重要组成部分,在蒸发过程中起着至关重要的作用。
蒸发的方式及流程

第五章 蒸发
*
蒸发是分离液相均一系(溶液)的单元操作之一。这种操作是将溶液加热,使其中部分(或全部)溶剂气化并不断除去,以提高溶液中的溶质浓度。被蒸发的溶液由挥发性的溶剂和不挥发的溶质所组成,因此蒸发也是挥发性溶剂和不挥发溶质的分离过程。用来实现蒸发操作的设备称为蒸发器。
*
图5-11 单中,从溶液中蒸发出来的溶剂量可通过物料衡算来确定。 现对图5-11所示的单效蒸发器作溶质的物料衡算。进入和离开蒸发器的溶质量不变,
即: 由此可求得溶剂的蒸发量为: 完成液的浓度为: 式中:F—溶液的进料量(kg/h); W—溶剂的蒸发量(kg/h); xw0—原料液中溶质的质量分率; 的概念 将几个蒸发器顺次连接起来协同操作以实现二次蒸汽的再利用,从而提高加热蒸汽利用率的操作,称为多效蒸发。每一个蒸发器称为一效。通入加热蒸汽(生蒸汽)的蒸发器称为第一效。用第一效的二次蒸汽作为加热蒸汽的蒸发器称为第二效,用第二效的二次蒸汽作为加热蒸汽的蒸发器称为第三效,依此类推。 多效蒸发的流程 顺流加料 逆流加料 平流加料
*
图5-4 在垂直加热管内汽、液两相的流动状态
料液在加热管内沸腾和流动情况对长管蒸发器的蒸发效果有很大时进入加热管,料液被加热,温度上升,料液因在管壁与中心受热程度不同而产生自然对流,此时尚未沸腾,溶液为如图5-4(a)所示的单相流动;当温度升高至沸点时,溶液沸腾而产生大量气泡,如图5-4(b)所示,气泡分散于连续的液相中,此时管内开始两相流动;随着气泡生成数量的增多,由于许多气泡汇合而增大形成如图5-4(c)所示的片状流;气泡进一步增大形成如图5-4(d)所示的柱状流动或称气栓;继而柱栓破裂,而形成如图5-4(e)所示的环状流动体系;此后在管子中央形成蒸汽柱,上升的蒸汽柱将料液拉曳成如图5-4(f)所示的一层液膜沿管壁迅速上升;随着上升气速进一步增大,则由于雾沫夹带,在蒸汽柱内形成如图5-4(g)、(h)所示的带有液体雾沫的喷雾流。在上述现象中,以柱状流动的传热系数最大,因此操作时希望使柱状流占整个管长的比例尽量增大。
详解干式、满液式、降膜式蒸发器

详解干式、满液式、降膜式蒸发器展开全文量的1/2~1/3左右。
满液式蒸发器降膜式蒸发器降膜式蒸发器,也称之为喷淋式蒸发器,这种换热器与满液式蒸发器相似,但是它又与满液式蒸发器有区别。
这种蒸发器的制冷剂是从换热器的上部喷淋到换热管上,制冷剂只是在换热管上形成一层薄薄的冷剂液膜,这样冷剂在沸腾蒸发时便减少了静液位压力,从而提高了换热效率,其换热效率较满液式机组提高了5左右。
降膜蒸发是流动沸腾,由于管外表面的液膜层厚度小,没有静压产生的沸点升高,传热系数高。
而满液式蒸发(也就是沉浸式蒸发)产生的气泡易于集聚在换热管的表面,导致换热效率下降,其换热效果不如降膜蒸发。
总的来说降膜蒸发属于小温差情况下,但要防止结垢,影响传热效率。
“冷水机组”,是对一种制冷机组的习惯命名法,这种“冷水机组”一般用于中央空调的冷源,或者空调工况的制冷,输出的是低温的冷水,通常叫做“冷冻水”,故而得名。
一般把只能制冷的叫做冷水机组,而能同时制热的,我们叫做“热泵”机组。
而“满液式”是指机组所用的“壳管式蒸发器”采用了“满液式蒸发器”的形式,这是区别于“干式”、“降膜式”的一种壳管式蒸发器。
它的“壳程”内走制冷剂循环,“管程”内走冷冻水循环,从剖面上看,就好像是筒体里有大半筒制冷剂,而走水的管束浸泡在制冷剂里。
它和“干式蒸发器”刚好相反,干式的是“管程”走制冷剂,“壳程”走水,好比制冷剂管束浸泡在水里。
满液式蒸发器,以及满液式机组,比起干式蒸发器/干式机组来说传热效率更高,出水温度与蒸发温度的趋近温差小,沿程阻力小,适合循环量大的机组(比如离心机),制冷效果好。
但是制冷剂充注量要求大,并且需要专用的回油系统,帮助压缩机回油。
如果在机组名字前再加上“水冷”,则是指机组的冷凝器形式,采用水冷却还是空气冷却,分为风冷、水冷。
如果再加上压缩机的形式“活塞式、螺杆式、离心式”,那么就是完整的机组命名了。
比如“水冷螺杆满液式冷水机组”。
在大部分场合,为了简略,会省却其中一两个部件的名称,只提和上下文相关的名称,比如“满优缺点与比较使水多次横掠管簇流动。
壳管式蒸发器工作原理

壳管式蒸发器工作原理壳管式蒸发器是一种常见的热交换器,广泛应用于化工、能源、制药等领域。
它以其高效的传热性能和稳定的工作特性备受青睐。
本文将深入探讨壳管式蒸发器的工作原理,帮助读者更好地理解和应用这一设备。
壳管式蒸发器由壳体和管束两部分组成。
壳体是一个密封的容器,内部有进出口管道用于介质的流动。
管束则是由许多平行排列的小管组成,通常是金属材料制成,用于传递热量。
壳管式蒸发器的工作原理可以简单概括为:通过壳体进出口管道引入待蒸发的液体(也称为进料液),并在管束内部通入蒸发介质(如蒸汽)。
当进料液经过管束内的小管时,与蒸汽进行热交换,液体被加热并蒸发。
蒸发后的蒸汽与管束外的冷却介质(如冷水)进行热交换,将热量传递给冷却介质,从而使蒸汽冷凝成液体。
最后,冷凝后的液体通过壳体的出口管道排出。
壳管式蒸发器的工作过程可以分为三个阶段:加热阶段、蒸发阶段和冷凝阶段。
首先,进料液从壳体的进口进入管束内,与蒸汽进行热交换,逐渐被加热。
在加热阶段,进料液的温度逐渐升高,直至达到蒸发温度。
接下来,进料液开始蒸发,液体逐渐转化为蒸汽。
在蒸发阶段,蒸汽与进料液之间进行传质传热,使得进料液中的挥发性组分逐渐蒸发出来。
最后,在冷凝阶段,蒸汽与冷却介质进行热交换,冷凝成液体,然后从壳体的出口排出。
壳管式蒸发器的工作原理可以通过热力学分析进一步理解。
在加热阶段,进料液的温度升高,蒸发后的蒸汽温度也随之升高,熵增加。
在蒸发阶段,蒸汽与进料液之间的温差驱动传热,使得进料液中的挥发性组分蒸发出来。
在冷凝阶段,冷却介质的温度低于蒸汽的温度,使得蒸汽的熵减小,最终冷凝成液体。
壳管式蒸发器的性能受多种因素影响。
首先,进料液和蒸汽之间的温差会影响传热效果,温差越大,传热效果越好。
其次,管束的设计也会影响传热效果,例如管束的长度、直径和布置方式等。
此外,进料液的流速和管束内的流动方式也会对传热性能产生影响。
总结起来,壳管式蒸发器通过热交换的方式实现了液体的蒸发和冷凝过程。
干式壳管蒸发器
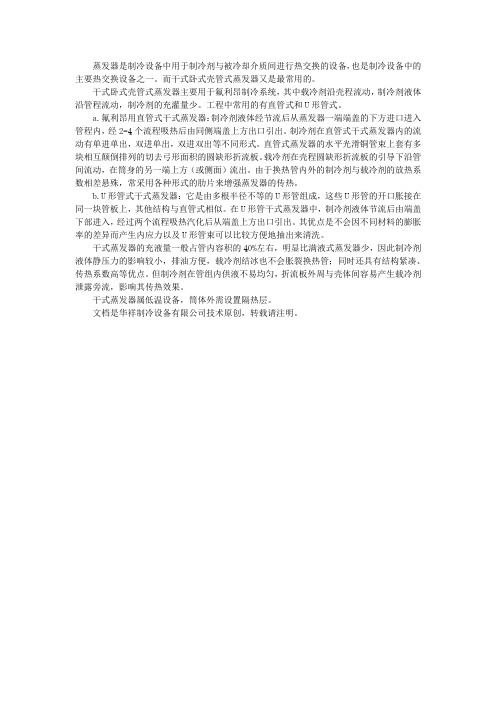
蒸发器是制冷设备中用于制冷剂与被冷却介质间进行热交换的设备,也是制冷设备中的主要热交换设备之一。
而干式卧式壳管式蒸发器又是最常用的。
干式卧式壳管式蒸发器主要用于氟利昂制冷系统,其中载冷剂沿壳程流动,制冷剂液体沿管程流动,制冷剂的充灌量少。
工程中常用的有直管式和U形管式。
a.氟利昂用直管式干式蒸发器:制冷剂液体经节流后从蒸发器一端端盖的下方进口进入管程内,经2-4个流程吸热后由同侧端盖上方出口引出。
制冷剂在直管式干式蒸发器内的流动有单进单出,双进单出,双进双出等不同形式。
直管式蒸发器的水平光滑铜管束上套有多块相互颠倒排列的切去弓形面积的圆缺形折流板。
载冷剂在壳程圆缺形折流板的引导下沿管间流动,在筒身的另一端上方(或侧面)流出。
由于换热管内外的制冷剂与载冷剂的放热系数相差悬殊,常采用各种形式的肋片来增强蒸发器的传热。
b.U形管式干式蒸发器:它是由多根半径不等的U形管组成,这些U形管的开口胀接在同一块管板上,其他结构与直管式相似。
在U形管干式蒸发器中,制冷剂液体节流后由端盖下部进入,经过两个流程吸热汽化后从端盖上方出口引出。
其优点是不会因不同材料的膨胀率的差异而产生内应力以及U形管束可以比较方便地抽出来清洗。
干式蒸发器的充液量一般占管内容积的40%左右,明显比满液式蒸发器少,因此制冷剂液体静压力的影响较小,排油方便,载冷剂结冰也不会胀裂换热管;同时还具有结构紧凑、传热系数高等优点。
但制冷剂在管组内供液不易均匀,折流板外周与壳体间容易产生载冷剂泄露旁流,影响其传热效果。
干式蒸发器属低温设备,筒体外需设置隔热层。
文档是华祥制冷设备有限公司技术原创,转载请注明。
壳管式干式蒸发器设计说明书

毕业设计(论文)题目名称:50kW壳管式干式蒸发器设计学院名称:能源与环境学院班级:学号:学生姓名:指导教师:2014年5月论文编号:20100112413050kW壳管式干式蒸发器设计50kW tubular DX evaporator design学院名称:能源与环境学院班级:学号:学生姓名:指导教师:2014年5月摘要换热器是化工生产中重要的设备之一,它是一种冷热流体间传递热量的设备,其中壳管式换热器应用最为广泛。
本设计为壳管式干式蒸发器的设计,换热器类型选择为U型管式换热器。
U型管式换热器仅有一个管板,两端均固定于同一管板上,管子可以自由伸缩,无热应力,热补偿性能好;管程采用双管程,流程较长,流速较高,传热性能较好,承压能力强,结构比较简单、价格便宜,适用于管、壳壁温差较大或者壳程介质易结垢需要清洗又不适宜采用浮头式和固定管板式的场合,特别适用于管内走清洁而不易结垢的高温、高压、腐蚀性强的物料。
U型管式换热器的主要结构包括管箱、筒体、封头、换热管、接管、折流板、防冲板和导流筒、防短路结构、支座及管壳程的其他附件等。
随着国家对节能产品的提倡,满液式机组也越来越受到欢迎。
满液式机组与普通冷水机组的区别就在于蒸发器采用了满液式蒸发器,而普通冷水机组采用干式蒸发器。
满液式蒸发器与干式蒸发器二者的明显区别在于制冷剂流程的不同,满液式蒸发器制冷剂走壳程,制冷剂从壳体下部进入,在传热管外流动并受热沸腾,蒸汽从壳体上部排出。
干式蒸发器中制冷剂走管程,即制冷剂从端盖下部进入传热管束,在管内流动受热蒸发,蒸汽从端盖上部排出。
换热器作为传热设备随处可见,在工业中应用非常普遍,特别是耗能用量十分大的领域,随着节能技术的飞速发展,换热器的种类开发越来越多。
关键词:干式蒸发器,U型管式换热器,结构,设计计算IAbstractHeat exchanger is one of the important equipment in chemical industry ,it transfer heat between cold and heat fluid. In this heat exchanger the tubular heat exchanger is most widely used.This design is a tubular DX evaporator. The type of the heat exchanger is the U type heat exchanger. U type heat exchanger with a tube plate, both ends of which are fixed on the same tube plates, tubes can be freely telescopic, thermal stress, thermal compensation performance is good; tube with double tube pass, longer process, the flow velocity is higher, the heat transfer performance is good, strong bearing ability, simple structure, cheap price, applied to the tube, the larger temperature difference between the shell wall or shell pass medium easy scaling needs cleaning and not suitable for floating head type and fixed tube plate occasions, especially suitable for the tube away clean and not easy to scale the high temperature, high pressure, strong corrosive materials. U type heat exchanger main structure consists of a tube box, cylinder, head, tube, pipe, baffle plate, front panel and draft tube, short circuit protection structure, support and other accessories such as pipe shell.Flooded chiller is being more and more popular with our government’s promotion of energy saving products.The major difference between flooded chiller and normal chiller is their evaporator installed inside,flooded evaporator was installed in flooded chiller while DX evaporator in normal chiller.The obvious difference of these two kinds of chillers is their refrigeration passes.In the flooded chiller,refrigerant runs into shell from the bottom,then flows outside of heat exchanging piping,being heated and boiled,turns into vapor and being discharged from the top of shel1.In DX evaporator,refrigerant runs inside tubes.It enters tube bundles from the bottom of end cover,flows inside the tubes,being heated and evaporates,then being discharged from top of end cover.Heat exchanger is wide used in industry,special in energy consumption field. As energy-saving technology moving,,more serious heart exchanger will appear. Keywords:DX evaporator,U type heat exchanger,structure,design and calculation目录1 绪论 (1)1.1 课题的提出和研究内容 (1)1.1.1 课题背景 (1)1.1.2 课题任务 (2)1.2 干式蒸发器 (2)1.2.1 干式蒸发器简介 (2)1.2.2 干式蒸发器与满液式蒸发器的区别 (2)1.3 壳管式换热器 (3)1.3.1 壳管式换热器简介 (3)1.3.2 壳管式换热器分类 (4)1.3.3 壳管式换热器的发展 (6)2 设计与计算的理论概述 (8)2.1 壳管式换热器的结构 (8)2.1.1 管程结构 (8)2.2.2 壳程结构 (8)2.2 管程和壳程数的确定 (9)2.3 流动空间的选择 (9)2.4 流体流速的选择 (11)2.4 流体流动方式的选择 (12)2.5 流体温度和流体终温的确定 (12)2.6 材质的选择 (12)3 结构初步设计计算 (13)3.1 设计方案确定/ (13)3.2 设计条件确定 (13)3.3 制冷剂质量流量计算 (13)3.4 冷冻水流量计算 (13)3.5 对数传热温差初步计算 (14)3.6 管长初步计算 (14)3.7 结构初步设计 (15)4 换热器计算 (17)4.1 壳程换热系数计算 (17)4.2 管内换热系数的计算 (18)4.3 制冷剂流动阻力及传热温差的计算 (19)4.3.1 制冷剂的流动阻力计算 (19)4.3.2 实际对数平均温差 (20)4.4 传热系数0K 及按内表面计算的热流密度i q (21)4.4.1 传热系数0K (21)4.4.2 按内表面计算的实际热流密度 (21)4.5 所需传热面积 (22)5 总体结构设计 (23)5.1 换热管设计 (23)5.2 壳体结构设计 (25)5.2.1 壳体壁厚的确定 (25)5.2.2 壳体直径的确定 (26)5.3 进出口设计 (27)5.3.1 壳程接管设计 (27)5.3.2 管程接管设计 (28)5.3 端盖设计 (28)5.4 管板设计 (28)5.5 折流板设计 (30)5.5.1 折流板型式 (30)5.5.2 折流板尺寸 (30)5.6 拉杆和定距管 (32)5.6.1 拉杆的直径和数量 (32)5.6.2 拉杆的位置 (33)5.6.3 定距管尺寸 (33)5.7 结构部件明细表 (34)6 U 型管换热器的制造、检验和验收 (35)6.1 换热器的制造 (35)6.1.1 换热器的主要受压部分的焊接接头 (35)6.1.2 管箱、壳体和头盖 (35)6.1.3 换热管 (35)6.1.4 管板 (36)6.1.5 换热管与管板的连接 (36)6.1.6 折流板、支撑板 (36)6.1.7 管束的组装 (37)6.1.8 换热器的密封面 (37)6.1.9 换热器的组装 (37)6.1.10 无损检测 (37)6.1.11 压力试验 (37)6.1.12 铭牌 (38)6.2 安装、试车和维护 (38)6.2.1 安装 (38)6.2.2 试车 (39)6.2.3 维护 (39)结论 (40)致谢 (41)附录 (42)附录1 换热器设计计算表 (42)附录2 换热器整体结构图 (45)参考文献 (46)1 绪论换热器是一种实现物料之间传递热量的节能设备,在石油,化工,动力,食品,轻工等行业应用普遍。
干式蒸发器的应用和优化设计
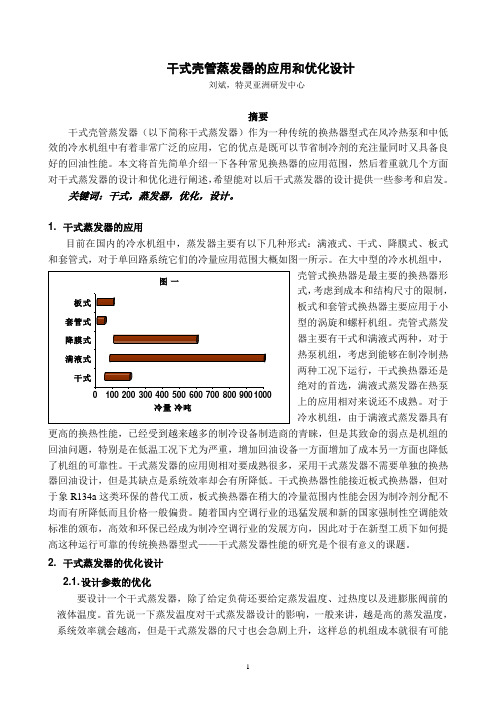
干式壳管蒸发器的应用和优化设计刘斌,特灵亚洲研发中心摘要干式壳管蒸发器(以下简称干式蒸发器)作为一种传统的换热器型式在风冷热泵和中低效的冷水机组中有着非常广泛的应用,它的优点是既可以节省制冷剂的充注量同时又具备良好的回油性能。
本文将首先简单介绍一下各种常见换热器的应用范围,然后着重就几个方面对干式蒸发器的设计和优化进行阐述,希望能对以后干式蒸发器的设计提供一些参考和启发。
关键词:干式,蒸发器,优化,设计。
1. 干式蒸发器的应用目前在国内的冷水机组中,蒸发器主要有以下几种形式:满液式、干式、降膜式、板式和套管式,对于单回路系统它们的冷量应用范围大概如图一所示。
在大中型的冷水机组中,壳管式换热器是最主要的换热器形式,考虑到成本和结构尺寸的限制,板式和套管式换热器主要应用于小型的涡旋和螺杆机组。
壳管式蒸发器主要有干式和满液式两种,对于热泵机组,考虑到能够在制冷制热两种工况下运行,干式换热器还是绝对的首选,满液式蒸发器在热泵上的应用相对来说还不成熟。
对于冷水机组,由于满液式蒸发器具有更高的换热性能,已经受到越来越多的制冷设备制造商的青睐,但是其致命的弱点是机组的回油问题,特别是在低温工况下尤为严重,增加回油设备一方面增加了成本另一方面也降低了机组的可靠性。
干式蒸发器的应用则相对要成熟很多,采用干式蒸发器不需要单独的换热器回油设计,但是其缺点是系统效率却会有所降低。
干式换热器性能接近板式换热器,但对于象R134a 这类环保的替代工质,板式换热器在稍大的冷量范围内性能会因为制冷剂分配不均而有所降低而且价格一般偏贵。
随着国内空调行业的迅猛发展和新的国家强制性空调能效标准的颁布,高效和环保已经成为制冷空调行业的发展方向,因此对于在新型工质下如何提高这种运行可靠的传统换热器型式——干式蒸发器性能的研究是个很有意义的课题。
2. 干式蒸发器的优化设计2.1. 设计参数的优化要设计一个干式蒸发器,除了给定负荷还要给定蒸发温度、过热度以及进膨胀阀前的液体温度。
第四章蒸发器

❖ 蒸发器的类型、基本构造及工作原理 ❖ 制冷剂在水平管内的沸腾换热 ❖ 冷却空气型蒸发器的设计与计算 ❖ 冷却液体型蒸发器的设计与计算
蒸发器的类型、基本构造及工作原理
❖ 蒸发器是一种吸热设备; ❖ 工作原理:制冷剂液体在较低的温度下沸腾,
转变为蒸气,并吸收被冷却物体或空间所散发 的热量,达到制冷的目的; ❖ 蒸发器是制冷系统中制造和输出冷量的设备; ❖ 按制冷剂的供液方式,蒸发器可分为满液式、 非满液式、循环式和淋激式。 ❖ 按照蒸发器中被冷却介质的种类分为冷却空气 型蒸发器和冷却液体型蒸发器
翅片管式排管
强制对流式空冷器
冷却液体型蒸发器
满液式蒸发器
干式壳管式蒸发器
干式壳管式蒸发器:液态制冷剂在管内流动,沿程吸收管外载冷 剂的热量逐渐汽化,制冷剂处于液汽共存的状态,蒸发器部分 传热面与气态制冷剂接触,导致总传热系数较满液式低,但其制 冷剂充注量少,回油方便,适用于氟利昂作制冷剂。 优点:(1)充液量少,为管内容积的40%左右; (2)受制冷剂液体静压力的影响较少;(3)排油方便; (4)载冷剂结冰不会胀裂管子(5)制冷剂液面容易控制; (6)结构紧凑。 缺点:制冷剂在换热管束内供液不易均匀,弓形折流板制造与装 配比较麻烦,由于装配间隙的存在,载冷剂在折流板孔和换热 管间、折流板外周与筒体间容易产生泄漏旁流,从而降低传热 效果。
只有部分传热面积与液态制冷剂相接触,表面传热系数 相对较小; 充液量少,润滑油容易返回压缩机;
依靠泵强迫制冷剂在蒸发器中 循环,液体循环速度大小由泵 调节,制冷剂循环量是蒸发量 的几倍,沸腾换热强度较高, 润滑油不易在蒸发器内积存。
依靠泵把制冷剂喷淋在传热面 上,蒸发器中制冷剂充灌量很 少,液柱高度不会对蒸发温度 产生影响。
- 1、下载文档前请自行甄别文档内容的完整性,平台不提供额外的编辑、内容补充、找答案等附加服务。
- 2、"仅部分预览"的文档,不可在线预览部分如存在完整性等问题,可反馈申请退款(可完整预览的文档不适用该条件!)。
- 3、如文档侵犯您的权益,请联系客服反馈,我们会尽快为您处理(人工客服工作时间:9:00-18:30)。
干式壳管式蒸发器的设计过程
初步规划过程:已知制冷量O Q ,和制冷剂的质量流量mt q (如制冷剂质量流量未知可通过mt q =O Q /(1'3h h -)求出)。
过热度
过冷度
(1) 求出冷冻水的体积流量s qv =O Q /'"111()p c t t ρ-('1t 为冷冻水出水温度,"
1t 为冷
冻水进水温度)
(2) 估计换热器的传热系数K 估(采用一般的铜光管时,换热器的传热系数为
523~580w/(m 2
℃),如果采用小直径铜管密排时,传热系数可提高为1000~1160w/
(m 2
℃),采用强化管传热系数会有更大的提高,能提高多少,根据铜光管时的水速和制冷剂的质量流速而定,即为水侧的换热系数和制冷剂侧换热系数而定)
(3) 估算换热面积F 估=O Q /K 估m t ∆(初步规划的换热面积要考虑过热度对传热系数
的影响,因此规划的换热面积要比校核计算的换热面积提高15%~30%左右,根据过热度的大小,选择合适的范围,另外,管板及折流板占据了换热面积不参与换热,因此初步规划的换热面积要再提高5%左右)
(4) 单管程热交换器的管程流通截面积s A =mt q /m v (为了保证润滑油带回压缩机,
制冷剂在换热管的出口流速大于4m/s ,此时制冷剂的质量流速一般为m v =100 kg/(m.s)左右,质量流速越大,制冷剂侧和整体的换热系数越高)
(5) 单程的管数n=4s A /(πd i 2)(d i 为所选换热管的内径)
(6) 根据所估的换热面积,每根管子的长度L=F 估/πnd 0 (d 0为管子的计算直径) (7) 确定合适的管程数N 及换热管长度l ,N=L/l (换热管长度与壳体直径之比通常
为6~10),GB151-1999推荐的换热管长度采用:1.0、1.5、2.0、2.5、3.0、4.5、6.0、7.5、9.0、12.0m 等)。
(8) 总的管子数Z m =nN
已知参数对应的字母表示
壳体内径D i ,流程数N ,每一流程的平均管子数Z m ,总管数Z t , 管板厚度δB ,折流板厚度δb ,折流板数N b ,折流板间距s 1,s 2,上缺口高度H 1,上缺口内管子数n b1,下缺口高H 2,下缺口内管数n b2。
管子直径为d o ,按三角形排列,有一定的管间距,壳体直径附近的管子数n c ,管长l 。
制冷剂从下端进入管子,在管中蒸发,从上端出蒸发器。
从上往下,各流程管数要确定。
1. 有效传热面积
'0F =0(2)t B b b d Z l N πδδ--
2. 管外换热系数的计算
(1) 折流板的平均间距 s =
12
2(1)1
b b s N s N +-+
(2) 横向流通截面积 c A =()i c o D n d s -
(3) 横向流速 c u =
s
c
qv A (4)
折流板上、下缺口面积 按公式(9-77)计算这两个面积。
计算时b K 值取自下表中。
2
2
11114
b b i b o A K D n d π=- 2
222214
b b i b o A K D n d π=-
b K 的数值 H/D i 0.15 0.20 0.25 0.30 0.35 0.40 0.45 K b
0.0739
0.112
0.154
0.198
0.245
0.293
0.343
(5)上、下缺口面积的平均值 b A =
121
()2
b b A A +
(6) 纵向流速 b u =s
b
qv A (7) c u 与b u 的几何平均值
u =
(8) 管外换热系数o α
冷媒水平均温度s t =
111()2t t '''+=1
(712)9.52
C +=︒。
据此温度查得水的物性数据为: Pr f =9.73,运动粘性系数61.28210/m s υ-=⨯,导热率0.575/()W m C λ=⋅︒,则
Re o
f ud υ
=
管外换热系数 o α=0.220.60.33Re Pr f f o
d λ
3. 管内换热系数的计算
假定蒸发器按内表面计算的热流密度i q >40002
W m /(此假定将在后面检验),则管 内换热系数
i α=0.60.2
0.257.8i m i
q
c d
υ
式中i d 为管子内径,c 值查下表可得。
每根管内R22的质量流量 mt
m m
q q Z =
质量流速
m v =
2
4
m
i q d π
将以上参数代入公式i α=0.60.20.257.8i m i
q c d υ
可得管内换热系数
4. 制冷剂流动阻力及传热温差的计算 (1) 制冷剂的流动阻力计算
① 制冷剂饱和蒸气的流速 2
4mt
m i q u Z d ρπ''
''=
②蒸发器出口处的蒸发温度2o t =2℃,据此从物性表中查得制冷剂的的以下参数:密度、普朗特数、运动粘滞系数,将以上数据代入下式中,得 Re i
u d υ''
''=
''
③沿程阻力系数 ε=
0.25
0.3164
(Re )
'' ④饱和蒸气的沿程阻力 2611
()102
i l p N
u d ερ''
''-∆=''⨯ ⑤两相流动时制冷剂的沿程阻力 1p ∆=1R P ψ''
∆
⑥总阻力 p ∆=51p ∆ (2) 对数平均温差
在2o t =2℃附近,压力每变化0.1MPa,饱和温度约变化5.5℃,因此蒸发器进口处制
冷剂的温度为 12 5.5
0.1
o o p t t ∆=+ 对数平均温差 1011021
01102()()
()ln ()
m t t t t t t t t t ''''
''---∆=-- 5. 传热系数0K 及按内表面计算的热流密度i q (1) 传热系数0K
管内侧污垢系数取为i γ=0,管外侧的污垢系数均取为o γ=8×10-5
2
m ⋅℃/W,则
0K =
1
1
1
()()()o o i o i i m o d d d d δγγαλα++++
(2) 按内表面计算的热流密度
0()o
i m i
d q K t d =
∆ 迭代求得 i q (i q 需大于40002
W m /)
(3) 传热系数0K 的数值
0K =(
)i
i o
m
d q d t ∆
6. 所需之传热面积
O
O O m
Q F K t =
∆
此值需比初步规划的有效传热面积小,以保证初步规划中所定的尺寸有足够的余量。