蒸发器原理结构简介
蒸发器:浅谈蒸发器的原理及分类
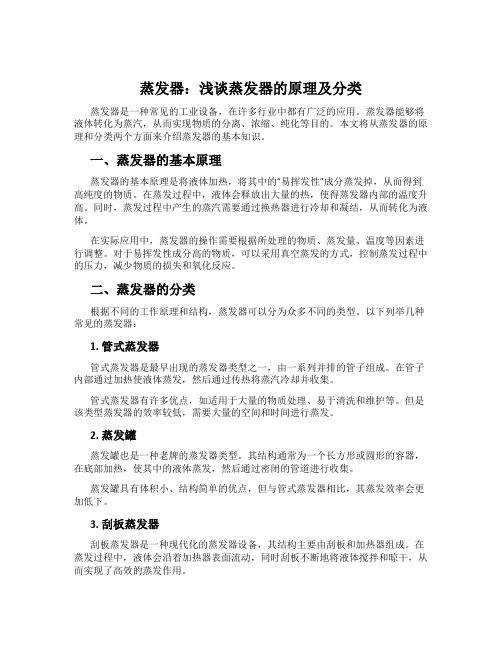
蒸发器:浅谈蒸发器的原理及分类蒸发器是一种常见的工业设备,在许多行业中都有广泛的应用。
蒸发器能够将液体转化为蒸汽,从而实现物质的分离、浓缩、纯化等目的。
本文将从蒸发器的原理和分类两个方面来介绍蒸发器的基本知识。
一、蒸发器的基本原理蒸发器的基本原理是将液体加热,将其中的“易挥发性”成分蒸发掉,从而得到高纯度的物质。
在蒸发过程中,液体会释放出大量的热,使得蒸发器内部的温度升高。
同时,蒸发过程中产生的蒸汽需要通过换热器进行冷却和凝结,从而转化为液体。
在实际应用中,蒸发器的操作需要根据所处理的物质、蒸发量、温度等因素进行调整。
对于易挥发性成分高的物质,可以采用真空蒸发的方式,控制蒸发过程中的压力,减少物质的损失和氧化反应。
二、蒸发器的分类根据不同的工作原理和结构,蒸发器可以分为众多不同的类型。
以下列举几种常见的蒸发器:1. 管式蒸发器管式蒸发器是最早出现的蒸发器类型之一,由一系列并排的管子组成。
在管子内部通过加热使液体蒸发,然后通过传热将蒸汽冷却并收集。
管式蒸发器有许多优点,如适用于大量的物质处理、易于清洗和维护等。
但是该类型蒸发器的效率较低,需要大量的空间和时间进行蒸发。
2. 蒸发罐蒸发罐也是一种老牌的蒸发器类型。
其结构通常为一个长方形或圆形的容器,在底部加热,使其中的液体蒸发,然后通过密闭的管道进行收集。
蒸发罐具有体积小、结构简单的优点,但与管式蒸发器相比,其蒸发效率会更加低下。
3. 刮板蒸发器刮板蒸发器是一种现代化的蒸发器设备,其结构主要由刮板和加热器组成。
在蒸发过程中,液体会沿着加热器表面流动,同时刮板不断地将液体搅拌和晾干,从而实现了高效的蒸发作用。
刮板蒸发器的优点在于处理效率高、能耗低,适用于对物质纯度和成分控制要求较高的场合。
但同时,刮板蒸发器的制造和维护成本较高。
4. 旋转蒸发器旋转蒸发器是一种将液体在旋转容器内进行蒸发的设备,其内壁通常有加热器以协助蒸发。
旋转蒸发器适用于小批量的物质处理,如制药、化妆品等领域。
双效蒸发器的构造与原理
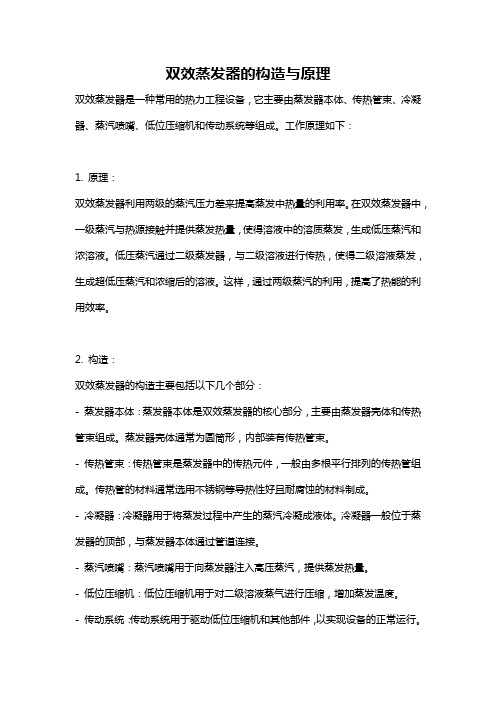
双效蒸发器的构造与原理
双效蒸发器是一种常用的热力工程设备,它主要由蒸发器本体、传热管束、冷凝器、蒸汽喷嘴、低位压缩机和传动系统等组成。
工作原理如下:
1. 原理:
双效蒸发器利用两级的蒸汽压力差来提高蒸发中热量的利用率。
在双效蒸发器中,一级蒸汽与热源接触并提供蒸发热量,使得溶液中的溶质蒸发,生成低压蒸汽和浓溶液。
低压蒸汽通过二级蒸发器,与二级溶液进行传热,使得二级溶液蒸发,生成超低压蒸汽和浓缩后的溶液。
这样,通过两级蒸汽的利用,提高了热能的利用效率。
2. 构造:
双效蒸发器的构造主要包括以下几个部分:
- 蒸发器本体:蒸发器本体是双效蒸发器的核心部分,主要由蒸发器壳体和传热管束组成。
蒸发器壳体通常为圆筒形,内部装有传热管束。
- 传热管束:传热管束是蒸发器中的传热元件,一般由多根平行排列的传热管组成。
传热管的材料通常选用不锈钢等导热性好且耐腐蚀的材料制成。
- 冷凝器:冷凝器用于将蒸发过程中产生的蒸汽冷凝成液体。
冷凝器一般位于蒸发器的顶部,与蒸发器本体通过管道连接。
- 蒸汽喷嘴:蒸汽喷嘴用于向蒸发器注入高压蒸汽,提供蒸发热量。
- 低位压缩机:低位压缩机用于对二级溶液蒸气进行压缩,增加蒸发温度。
- 传动系统:传动系统用于驱动低位压缩机和其他部件,以实现设备的正常运行。
综上所述,双效蒸发器通过两级蒸汽的利用,提高了热能的利用效率。
其构造主要包括蒸发器本体、传热管束、冷凝器、蒸汽喷嘴、低位压缩机和传动系统等,通过蒸发热量的提供和蒸汽的传热,实现溶液的浓缩和蒸发。
蒸发结晶图文详解MVR蒸发器机构原理及特点

蒸发结晶图⽂详解MVR蒸发器机构原理及特点⼀、MVR⼯艺介绍1、MVR原理MVR是蒸汽机械再压缩技术,(mechanical vapor recompression )的简称。
MVR蒸发器是重新利⽤它⾃⾝产⽣的⼆次蒸汽的能量,从⽽减少对外界能源的需求的⼀项节能技术。
MVR其⼯作过程是将低温位的蒸汽经压缩机压缩,温度、压⼒提⾼,热焓增加,然后进⼊换热器冷凝,以充分利⽤蒸汽的潜热。
除开车启动外,整个蒸发过程中⽆需⽣蒸汽从蒸发器出来的⼆次蒸汽,经压缩机压缩,压⼒、温度升⾼,热焓增加,然后送到蒸发器的加热室当作加热蒸汽使⽤,使料液维持沸腾状态,⽽加热蒸汽本⾝则冷凝成⽔。
这样原来要废弃的蒸汽就得到充分的利⽤,回收潜热,提⾼热效率,⽣蒸汽的经济性相当于多效蒸发的30效。
为使蒸发装置的制造尽可能简单和操作⽅便,可使⽤离⼼式压缩机、罗茨式压缩机。
这些机器在1:1.2到1:2压缩⽐范围内其体积流量较⾼。
2、MVR⼯艺流程系统由单效或双效蒸发器、分离器、压缩机、真空泵、循环泵、操作平台、电器仪表控制柜及阀门、管路等系统组成,结构简单,操作维护⽅便。
⼆、蒸发器介绍1、MVR降膜蒸发器⼯作原理:物料原液从换热器上管箱加⼊,经过布液器把物料分配到每根换热管内,并且沿着换热管内壁形成均匀的液体膜,管内液体膜在向下流的过程中被壳程的加热蒸汽加热,边向下流动边沸腾并进⾏蒸发。
到换热管底端物料变成浓缩液和⼆次蒸汽。
浓缩液落⼊下管箱,⼆次蒸汽进⼊⽓液分离器。
在⽓液分离器中⼆次蒸汽夹带的液体飞沫被去除,纯净的⼆次蒸发从分离器中输送到压缩机。
压缩机把⼆次蒸汽压缩后作为加热蒸汽输送到换热器壳程⽤于蒸发器热源。
实现连续蒸发过程。
特点:1、换热效率⾼2、占地⾯积⼩3、物料停留的时间短,不易引起物料变质。
4、适⽤于较⾼粘度的物料。
应⽤范围:降膜蒸发器适⽤于MVR蒸发结晶过程预浓缩⼯序,可以蒸发粘度较⼤的物料,尤其适⽤于热敏性物料,但不适⽤处理有结晶的物料。
二十二种蒸发、结晶设备结构及工作原理图解

二十二种蒸发、结晶设备结构及工作原理图解一、中央循环管式蒸发器中央循环管式蒸发器的结构其加热室由一垂直的加热管束(沸腾管束)构成,在管束中央有一根直径较大的管子,称为中央循环管,其截面积一般为加热管束总截面积的40~100%。
当加热介质通入管间加热时,由于加热管内单位体积液体的受热面积大于中央循环管内液体的受热面积,因此加热管内液体的相对密度小,从而造成加热管与中央循环管内液体之间的密度差,这种密度差使得溶液自中央循环管下降,再由加热管上升的自然循环流动。
溶液的循环速度取决于溶液产生的密度差以及管的长度,其密度差越大,管子越长,溶液的循环速度越大。
但这类蒸发器由于受总高度限制,加热管长度较短,一般为1~2m,直径为25~75mm,长径比为20~40。
性能特点:中央循环管蒸发器具有结构紧凑、制造方便、操作可靠等优点,故在工业上的应用十分广泛,有所谓“标准蒸发器”之称。
但实际上,由于结构上的限制,其循环速度较低(一般在0.5m/s以下);而且由于溶液在加热管内不断循环,使其浓度始终接近完成液的浓度,因而溶液的沸点高、有效温度差减小。
此外,设备的清洗和检修也不够方便。
二、外热式蒸发器外热式蒸发器的结构特点是加热室与分离室分开,这样不仅便于清洗与更换,而且可以降低蒸发器的总高度。
因其加热管较长(管长与管径之比为50~100),同时由于循环管内的溶液不被加热,故溶液的循环速度大,可达1.5m/s。
三、升膜蒸发器升膜式蒸发器的加热室由一根或数根垂直长管组成,通常加热管直径为25~50mm,管长与管径之比为100~150。
原料液经预热后由蒸发器的底部进入,加热蒸汽在管外冷凝。
当溶液受热沸腾后迅速汽化,所生成的二次蒸汽在管内高速上升,带动液体沿管内壁成膜状向上流动,上升的液膜因受热而继续蒸发。
故溶液自蒸发器底部上升至顶部的过程中逐渐被蒸浓,浓溶液进入分离室与二次蒸汽分离后由分离器底部排出。
常压下加热管出口处的二次蒸汽速度不应小于10m/s,一般为20~50m/s,减压操作时,有时可达100~160m/s或更高。
蒸发器概述
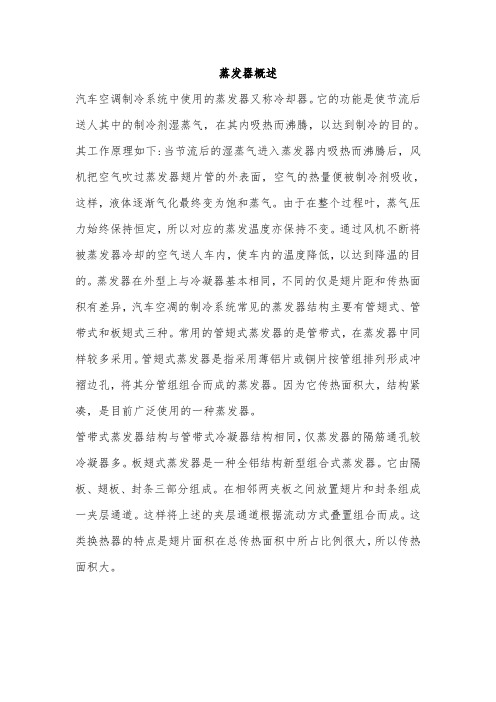
蒸发器概述
汽车空调制冷系统中使用的蒸发器又称冷却器。
它的功能是使节流后送人其中的制冷剂湿蒸气,在其内吸热而沸腾,以达到制冷的目的。
其工作原理如下:当节流后的湿蒸气进入蒸发器内吸热而沸腾后,风机把空气吹过蒸发器翅片管的外表面,空气的热量便被制冷剂吸收,这样,液体逐渐气化最终变为饱和蒸气。
由于在整个过程叶,蒸气压力始终保持恒定,所以对应的蒸发温度亦保持不变。
通过风机不断将被蒸发器冷却的空气送人车内,使车内的温度降低,以达到降温的目的。
蒸发器在外型上与冷凝器基本相同,不同的仅是翅片距和传热面积有差异,汽车空凋的制冷系统常见的蒸发器结构主要有管翅式、管带式和板翅式三种。
常用的管翅式蒸发器的是管带式,在蒸发器中同样较多采用。
管翅式蒸发器是指采用薄铝片或铜片按管组排列形成冲褶边孔,将其分管组组合而成的蒸发器。
因为它传热面积大,结构紧凑,是目前广泛使用的一种蒸发器。
管带式蒸发器结构与管带式冷凝器结构相同,仅蒸发器的隔筋通孔较冷凝器多。
板翅式蒸发器是一种全铝结构新型组合式蒸发器。
它由隔板、翅板、封条三部分组成。
在相邻两夹板之间放置翅片和封条组成一夹层通道。
这样将上述的夹层通道根据流动方式叠置组合而成。
这类换热器的特点是翅片面积在总传热面积中所占比例很大,所以传热面积大。
蒸发器的原理

蒸发器的原理蒸发器是一种常见的热交换装置,广泛应用于化工、制冷、空调等领域。
它的主要原理是利用液体在加热过程中产生的蒸汽与冷却介质接触,将热量传递给冷却介质,实现液体的蒸发。
以下将详细介绍蒸发器的原理及其工作过程。
一、蒸发器的原理蒸发器的原理主要基于液体的蒸发换热原理。
当液体受热后,其中的分子会获得足够的能量而从液态转变为气态,形成蒸汽。
蒸汽具有较高的温度和热量,可以通过与冷却介质接触而传递热量。
蒸发器利用这一原理,通过设计合理的结构和流动方式,使液体能够充分蒸发并将热量传递给冷却介质。
二、蒸发器的工作过程蒸发器的工作过程可以分为两个阶段:蒸发阶段和冷却阶段。
1. 蒸发阶段在蒸发阶段,液体通过进入蒸发器的进口进入蒸发器内部。
在蒸发器内部,液体会被均匀分布到蒸发器的内部表面上,形成一层薄膜。
当蒸发器内部的加热元件加热时,液体的温度逐渐升高,其中的一部分液体会蒸发成为蒸汽。
蒸汽会沿着蒸发器内部的流动通道向上流动,并与液体接触。
在接触的过程中,蒸汽会将热量传递给液体,使其蒸发。
蒸汽在与液体接触的同时,温度逐渐降低,逐渐凝结成液态。
2. 冷却阶段在蒸发阶段后,凝结的液态物质会沿着蒸发器内部的下降通道流动,最终流入蒸发器的出口。
在这个过程中,冷却介质会与液态物质接触,将其余的热量吸收并带走。
冷却介质可以是空气、水或其他冷却介质。
通过与冷却介质的接触,液态物质的温度会逐渐降低,最终达到冷却介质的温度。
三、蒸发器的特点蒸发器具有以下几个特点:1. 高效传热:蒸发器通过设计合理的结构和流动方式,使液体能够充分蒸发并将热量传递给冷却介质,实现高效的传热效果。
2. 热量利用率高:蒸发器能够将液体中的热量充分利用,使其在蒸发过程中达到最大化。
3. 结构简单:蒸发器的结构相对简单,易于制造和安装。
4. 体积小巧:蒸发器的体积相对较小,可以满足不同场合的空间要求。
5. 适用范围广:蒸发器广泛应用于化工、制冷、空调等领域,可以满足不同行业的需求。
几种蒸发器的结构及工作原理
几种蒸发器的结构及工作原理蒸发器是一种用于将液态物质转化为蒸气态的装置,工作原理是利用热量使液体蒸发,分离出其中的溶质,从而实现液体的浓缩、纯化或提取。
根据结构和工作原理的不同,可以将蒸发器分为多种类型。
1.多效蒸发器:多效蒸发器是利用连续的蒸发、再冷凝来回顺序进行的节能蒸发方式。
其主要由多个效应器组成,每个效应器都是一个独立的蒸发器,通过串联在一起,从而实现了能量的逐级利用。
在多效蒸发器中,高压蒸汽由最后一效应器开始,逐级减压,逐效进行蒸发、冷凝,从而实现了蒸发过程中能量的多次回收利用,大大提高了能量利用率。
2.换热管蒸发器:换热管蒸发器是一种高效率的传热器,其主要由一组呈U型排列的换热管组成。
其中一端接受加热介质,另一端连接需要蒸发的液体。
加热介质在管内蒸发,释放的热量通过换热管传递给液体,使其蒸发。
换热管的U型设计可以大大增加了管内的传热面积,提高传热效率。
3.扇式蒸发器:扇式蒸发器是一种利用气体流动进行蒸发的装置。
其基本结构是一个笔直的管道,其内壁覆盖有形成扇状的薄片或网格状物体。
当高速气体通过管道时,在薄片或网格的作用下,气体的流动转化为薄膜流动,从而实现了大面积的液体暴露在气体中,促使液体发生蒸发的效果。
4.闪蒸器:闪蒸器是一种常用于液体分离和浓缩的蒸发器。
其主要工作原理是,在蒸发室中,液体通过闪蒸器进入低压蒸发环境,瞬间减压,液体中的易挥发物质瞬间蒸发为气体,与空气在闪蒸室中进行混合,之后通过冷凝器进行冷凝,最后获得目标物质的纯化。
5.露点蒸发器:露点蒸发器是一种利用物料与加热介质间的露点温差进行蒸发的装置。
一般由加热介质侧对流通道、物料侧对流通道组成。
加热介质在内侧对流通道中加热并蒸发满足露点条件的物料,物料中的挥发物质逸出,而由于外侧对流通道温度低于露点,液态物料不会发生蒸发。
这样通过露点温差可以实现挥发物质的高效分离。
总之,不同类型的蒸发器在结构和工作原理上都有所区别,但其基本原理都是利用加热使液体蒸发,分离其中的溶质。
蒸发器的组成结构及原理
蒸发器的组成结构及原理
蒸发器是一种用于将液体转变为气体的设备,它通常由以下几部分组成:
1. 加热元件:用于将液体加热至其沸点以上的温度,使其蒸发。
常见的加热元件有电加热管、火炉等。
2. 蒸发室:液体通过管道进入蒸发室,在加热的作用下蒸发成气体。
蒸发室通常是一个密封的容器,确保液体不会外泄。
3. 冷凝器:将蒸发室内的气体冷却并转变为液体。
冷凝器通常是一个金属管,外部通以冷却介质(如水)来降低气体温度。
当气体冷却到其饱和温度以下时,发生冷凝。
4. 排气系统:用于将已冷凝的液体排出蒸发器,并保持室内压力平衡。
排气系统通常由排气管和阀门组成。
蒸发器的工作原理基于液体的蒸发和气体的冷凝。
液体经过加热后蒸发,产生的气体由蒸发室排出。
随后,气体进入冷凝器被冷却并转变为液体,最终由排气系统排出。
整个过程中,蒸发器需要提供足够的热量将液体加热至沸点以上,同时通过冷凝器将产生的气体重新转变为液体。
蒸发器结构及原理
蒸发器结构及原理蒸发器是一种用于将液体转化为蒸汽的设备,其结构和工作原理主要包括加热表面、液体进料和蒸汽出口三个方面。
蒸发器的基本结构包括蒸发室和加热表面。
蒸发室是一个封闭的容器,用于容纳液体和蒸汽。
加热表面则位于蒸发室底部,用于将液体加热并转化为蒸汽。
加热表面通常由一系列管道或板组成,其形状和材料可以根据具体的应用需求进行设计。
液体进料是将待蒸发的液体输入到蒸发室的过程。
在蒸发器中,液体通常通过进料管道进入蒸发室,并通过一个或多个喷嘴将液体均匀地分布在加热表面上。
这有助于提高蒸发效率,并避免局部过热或结垢的问题。
蒸汽出口是指蒸发室中蒸汽排出的通道。
通常,蒸汽会通过蒸汽出口进入蒸汽收集系统,然后被输送到其他设备进行进一步的处理或利用。
蒸汽出口通常位于蒸发室的顶部,以利于蒸汽的顺利排出。
蒸发器的工作原理是利用加热表面与液体接触时的热传导和质量传递来完成液体向蒸汽的转化。
当液体进入蒸发室后,接触到加热表面的部分液体会被加热并转化为蒸汽。
这是由于加热表面的高温使得液体分子获得足够的能量以克服液体表面张力,从而从液体相转变为气体相。
在蒸发的过程中,液体从进料喷嘴均匀喷洒到加热表面上,形成一层薄膜。
薄膜与加热表面接触后,液体会迅速吸收加热表面的热量,从而增加液体内部的温度。
当液体温度达到饱和温度时,薄膜上的部分液体会转化为蒸汽。
转化为蒸汽的液体会沿着加热表面向上升腾,并逐渐聚集在蒸汽腔室中。
然后,蒸汽通过蒸汽出口排出蒸发室。
同时,剩余的液体会继续下降至加热表面上,循环进行蒸发过程。
蒸发器的性能主要与结构及工作参数有关。
蒸发器的结构设计需要考虑加热表面的大小和形状,以及进料和出口的位置和尺寸。
蒸发器的工作参数包括进料速率、蒸发温度和压力,以及蒸汽出口流量等。
蒸发器在各行各业中广泛应用,如化工、食品、制药和能源等领域。
通过有效地利用加热表面的热传导和质量传递,蒸发器能够将液体快速转化为蒸汽,实现液体的浓缩和分离,从而满足不同工艺过程的需求。
蒸发器的结构和类型.
职业教育环境监测与治理技术专业教学资源库《化工单元操作》课程
项目九
蒸发及设备操作
任务一、蒸发流程的确定和主体设备的选择 ---蒸发器结构和类型
大庆职业学院
蒸发设备
根据蒸发器中溶液的流动情况,把蒸发器分为循环型与非循环型(单 程型)两类。
(一)循环型蒸发器
特点:溶液在蒸发器中循环流动,溶液在蒸发器内停留时间长,溶液 浓度接近于完成液浓度。 由于引起循环运动的原因不同,分为自然循环型和强制循环型两类。
2 . 降膜蒸发器 原理:溶液预热后由加热室顶 部加入,经管端的液体分布器 均匀分配在各加热管内,在重 力作用下沿管内壁呈膜状向下 流动并进行蒸发,汽液混合物 从管下端流出,进入分离室, 汽、液分离后,完成液由分离 室底部排出。 适用:浓度高、粘度较大的溶
液。
不适用:易结晶、结垢的溶液。
这类蒸发器操作良好的关键是使溶液呈均匀的膜状沿各管内壁 向下流动,为此在每根加热管的顶部设置液体分布器。
4. 列文蒸发器 特点:在加热室上部设置沸腾室,加 热室的溶液由于受到上方沸腾室液柱 产生的压力作用,沸点升高使溶液不 在加热管中沸腾,上升到沸腾室时才
开始沸腾汽化。
优点:流动阻力小;循环速度高;传 热效果好;加热管内不易堵塞。
缺点:设备费高;厂房高,耗用金属
多。 适于处理有晶体析出或易结垢的溶液。
4.刮板薄膜蒸发器 原理:它的壳体外部装有加热蒸汽 夹套,壳体内装有旋转刮片。料液 由蒸发器上部沿切线方向加入后, 在重力和旋转刮片刮带下,溶液在 壳体内壁上形成旋转下降的液膜, 并在下降过程中不断被蒸发浓缩, 在底部得到完成液。 适用:易结晶、易结垢、高粘度的 溶液。 缺点:结构复杂,动力消耗大,传 热面积小,处理能力低。
- 1、下载文档前请自行甄别文档内容的完整性,平台不提供额外的编辑、内容补充、找答案等附加服务。
- 2、"仅部分预览"的文档,不可在线预览部分如存在完整性等问题,可反馈申请退款(可完整预览的文档不适用该条件!)。
- 3、如文档侵犯您的权益,请联系客服反馈,我们会尽快为您处理(人工客服工作时间:9:00-18:30)。
蒸发器主要由加热室及分离室组成。
按加热室的结构和操作时溶液的流动情况,可将工业中常用的间接加热蒸发器分为循环型(非膜式)和单程型(膜式)两大类。
一、循环型(非膜式)蒸发器
这类蒸发器的特点是溶液在蒸发器内作连续的循环运动,以提高传热效果、缓和溶液结垢情况。
由于引起循环运动的原因不同,可分为自然循环和强制循环两种类型。
前者是由于溶液在加热室不同位置上的受热程度不同,产生了密度差而引起的循环运动;后者是依靠外加动力迫使溶液沿一个方向作循环流动。
(一)中央循环管式(或标准式)蒸发器
中央循环管式蒸发器,加热室由垂直管束组成,管束中央有一根直径较粗的管子。
细管内单位体积溶液受热面大于粗管的,即前者受热好,溶液汽化得多,因此细管内汽液混合物的密度比粗管内的小,这种密度差促使溶液作沿粗管下降而沿细管上升的连续规则的自然循环运动。
粗管称为降液管或中央循环管,细管称为沸腾管或加热管。
为了促使溶液有良好的循环,中央循环管截面积一般为加热管总截面积的40%一100%。
管束高度为1—2m;加热管直径在25~75mm之间、长径之比为20~40。
中央循环管蒸发器是从水平加热室、蛇管加热室等蒸发器发展而来的,相对于这些老式蒸发器而言,中央循环管蒸发器具有溶液循环好、传热效率高等优点;同时由于结构紧凑、制造方便、操作可靠,故应用十分广泛,有“标准蒸发器”之称。
但实际上由于结构的限制,循环速度一般在~/s以下;且由于溶液的不断循环,使加·热管内的溶液始终接近完成液的浓度,故有溶液粘度大、沸点高等缺点;此外,这种蒸发器的加热室不易清洗。
中央循环管式蒸发器适用于处理结垢不严重、腐蚀性较小的溶液。
(二)悬筐式蒸发器
悬筐式蒸发器是中央循环管蒸发器的改进。
加热蒸汽由中央蒸汽管进入加热室,加热室悬挂在器内,可由顶部取出,便于清洗与更换。
包围管束的外壳外壁面与蒸发器外壳内壁面间留有环隙通道,其作用与中央循环管类似,操作时溶液形成沿环隙通道下降而沿加热管上升的不断循环运动。
一般环隙截面与加热管总截面积之比大于中央循环管式的,环隙截面积约为沸腾管总截面积的100%一150%,因此溶液循环速度较高,约在1~/s之间,改善了加热管内结垢情况,并提高了传热速率。
悬筐蒸发器适用于蒸发有晶体析出的溶液。
缺点是设备耗材量大、占地面积大、加热管内的溶液滞留量大。
(三)外热式蒸发器
外热式蒸发器,这种蒸发器的加热管较长,其长径之比为50—100。
由于循环管内的溶液未受蒸汽加热,其密度较加热管内的大,因此形成溶液沿循环管下降而沿加热管上升的循环运动,循环速度可达/s。
1一加热室 2一分离室 3一除沫器 4—环形循环通道 1一加热室 2一分离室 3一循环管
(四)强制循环蒸发器
前述各种蒸发器都是由于加热室与循环管内溶液间的密度差而产生溶液的自然循环运动,故均属于自然循环型蒸发器,它们的共同不足之处是溶液的循环速度较低,传热效果欠佳。
在处理粘度大、易结垢或易结晶的溶液时,可采用强制循环蒸发器。
这种蒸发器内的溶液是利用外加动力进行循环的,因此使用这种蒸发器时加热面积受到一定限制。
二、膜式(单程型)蒸发器
上述各种蒸发器的主要缺点是加热室内滞料量大,致使物料在高温下停留时间长,特别不适于处理热敏性物料。
在膜式蒸发器内,溶液只通过加热室一次即可浓缩到需要的浓度,停留时间仅为数秒或十余秒钟。
操作过程中溶液沿加热管壁呈传热效果最佳的膜状流动。
(一)升膜蒸发器
升膜蒸发器的加热室由单根或多根垂直管组成,加热管长径之比为100~150,管径在25~50mm之间。
原料液经预热达到沸点或接近沸点后,由加热室底部引入管内,为高速上升的二次蒸汽带动,沿壁面边呈膜状流动、边进行蒸发,在加热室顶部可达到所需的浓度,完成液由分离器底部排出。
二次蒸汽在加热管内的速度不应小于l0m/s,一般为20~50m/s,减压下可高达100~160m/s或更高。
·若将常温下的液体直接引入加热室,则在加热室底部必有一部分受热面用来加热溶液使其达到沸点后才能汽化,溶液在这部分壁面上不能呈膜状流动,而在各种流动状态中,又以膜状流动效果最好,故溶液应预热到沸点或接近沸点后再引入蒸发器。
这种蒸发器适用于处理蒸发量较大的稀溶液以及热敏性或易生泡的溶液;不适用于处理高粘度、有晶体析出或易结垢的溶液。
(二)降膜蒸发器
若蒸发浓度或粘度较大的溶液,可采用如图5-6所示的降膜蒸发器,它的加热室与升膜蒸发器类似。
原料液由加热室顶部加入,经管端的液体分布器均匀地流人加热管内,在溶液本身的重力作用下,溶液沿管内壁呈膜状下流,并进行蒸发。
为了使溶液能在壁上均匀布膜,且防止二次蒸汽由加热管顶端直接窜出,加热管顶部必须设置加工良好的液体分布器。
降膜蒸发器也适用于处理热敏性物料,但不适用于处理易结晶、易结垢或粘度特大的溶液。
液体分布器
(三)升一降膜蒸发器
升一降膜蒸发器的结构如图5—5所示,由升膜管束和降膜管束组合而成。
蒸发器的底部封头内有一隔板,将加热管束均分为二。
原料液在预热器1中加热达到或接近沸点后,引入升膜加热管束2的底部,汽、液混合物经管束由顶部流人降膜加热管束3,然后转入分离器4,完成液由分离器底部取出。
溶液在升膜和降膜管束内的布膜及操作情况分别与前述的升膜及降膜蒸发器内的情况完全相同。
升一降膜蒸发器一般用于浓缩过程中粘度变化大的溶液;或厂房高度有一定限制的场合。
若蒸发过程溶液的粘度变化大,推荐采用常压操作。
(四)刮板搅拌薄膜蒸发器
刮板搅拌薄膜蒸发器的加热管是一根垂直的空心圆管,圆管外有夹套,内通加热蒸汽。
圆管内装有可以旋转的搅拌叶片,叶片边缘与管内壁的间隙为—。
原料液沿切线方向进入管内,由于受离心力、重力以及叶片的刮带作用,在管壁上形成旋转下降的薄膜,并不断地被蒸发,完成液由底部排出。
刮板薄膜蒸发器是利用外加动力成膜的单程蒸发器,故适用于高粘度、易结晶、易结垢或热敏性溶液的蒸发。
缺点是结构复杂、动力耗费大(约为3kW/m2传热面)、传热面积较小(一般为3—4m2/台),处理能力不大。
三、直接加热蒸发器
前述的各种蒸发器都是间接加热的,工业上有时还采用直接加热蒸发器,图5—7所示的浸没燃烧蒸发器就是直接加热的蒸发器。
将一定比例的燃烧气与空气直接喷人溶液中,燃烧气的温度可高达1200~1800℃,由于气、液间的温度差大,且气体对溶液产生强烈的鼓泡作用,使水分迅速蒸发,蒸出的二次蒸汽与烟道气一同由顶部排出。
浸没燃烧蒸发器的结构简单,不需要固定的传热面,热利用率高,适用于易结垢、易结晶或有腐蚀性溶液的蒸发,但不适于处理不能被燃烧气污染及热敏性物料的蒸发。
目前广泛应用于废酸处理工业。
蒸发操作广泛用于各种工业中,对这类应用量大且面广的设备,如能作某些改进以提高蒸发强度,则对社会的经济影响是很显著的。
不论是间接加热的非膜式还是膜式蒸发器,其主要元件都是加热管束。
所以对蒸发器的加热管束加以改造,是提高蒸发器传热强度的可行途径。
由蒸发器的发展历程也可以看出,最初采用的是蛇管和横管蒸发器,后来发展为垂直管蒸发器,再进展为膜式蒸发器。
要提高蒸发器的传热强度往往用减薄管子两侧液膜或增加膜内湍动程度的方法来实现。
近年来,国内外差不多都是从改造管束着手以减薄液膜厚度从而提高蒸发强度。
例如,我国某研究所对多种不同形式的管子进行冷凝实验,最后选出一种较好的管外侧开纵槽的管子,即在φ22X2mm的铝管外侧开出48条纵槽,如图所示。
异丁烷蒸气在管外冷凝,管内通冷水,总传热系数较同条件下的光滑管提高2倍以上。
开槽用于蒸发一侧时,总传热系数可以提高3~4倍。
国外曾有人在内径为、长度为的内、外开纵槽的铜管内,在常压下对清水进行蒸发实验,获得的总传热系数较同条件下的光滑管高3~4倍。
蒸汽在管外侧槽峰上冷凝而产生冷凝液,由于表面张力的作用立即流至凹槽内,然后靠重力作用沿凹槽向下流动而排走,使槽峰及其附近始终保持极薄的液膜,而且管的上、下端基本一致,使管子热阻很小,克服了前章介绍的在垂直光滑管上凝液膜上薄下厚使冷凝传热系数降低的缺陷。
当纵槽开在沸腾液侧时,例如在升膜蒸发器中,溶液由下而上流过槽底,然后分布到槽峰,因此传热面始终保持薄膜蒸发状态,再加上蒸汽高速拉膜上升,使溶液侧的沸腾传热系数提高。
此外,在溶液中加入表面活性剂,可以降低溶液的表面张力,加大传热面的润湿性,避免产生干点,使整个壁面能有效地传热,表面活性剂在汽、液两相间起到润滑作用,减少流动阻力;由于管壁上覆盖了表面活性剂,阻止了污垢附在壁面上,故可使溶液侧壁面上不生成垢层,减小传热阻力。
表面活性剂可以回收循环使用,回收方法是于完成液中鼓人空气,活性剂即成泡沫浮在溶液表面上,可以回收95%~97%的活性剂。