喷涂喷漆工艺规程
涂装工艺规程
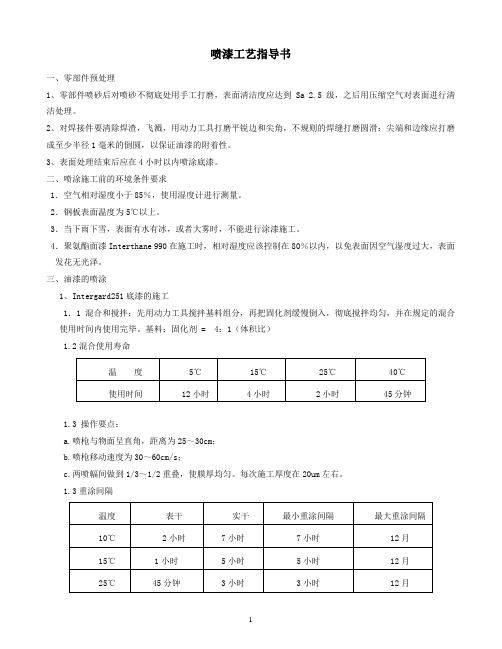
喷漆工艺指导书一、零部件预处理1、零部件喷砂后对喷砂不彻底处用手工打磨,表面清洁度应达到Sa 2.5级,之后用压缩空气对表面进行清洁处理。
2、对焊接件要清除焊渣,飞溅,用动力工具打磨平锐边和尖角,不规则的焊缝打磨圆滑:尖端和边缘应打磨成至少半径1毫米的倒圆,以保证油漆的附着性。
3、表面处理结束后应在4小时以内喷涂底漆。
二、喷涂施工前的环境条件要求1.空气相对湿度小于85%,使用湿度计进行测量。
2.钢板表面温度为5℃以上。
3.当下雨下雪,表面有水有冰,或者大雾时,不能进行涂漆施工。
4.聚氨酯面漆Interthane 990在施工时,相对湿度应该控制在80%以内,以免表面因空气湿度过大,表面发花无光泽。
三、油漆的喷涂1、Intergard251底漆的施工1.1混合和搅拌:先用动力工具搅拌基料组分,再把固化剂缓慢倒入,彻底搅拌均匀,并在规定的混合使用时间内使用完毕。
基料:固化剂 = 4:1(体积比)1.2混合使用寿命1.3 操作要点:a.喷枪与物面呈直角,距离为25~30cm;b.喷枪移动速度为30~60cm/s;c.两喷幅间做到1/3~1/2重叠,使膜厚均匀。
每次施工厚度在20um左右。
1.3重涂间隔2、 Intergard400施工说明2.1.混合和搅拌:具体操作与底漆相同基料:固化剂=5.67:1(体积比)2.2混合使用寿命3.3 重涂间隔3、Interthane 990施工说明3.1混合和搅拌:具体操作同底漆基料:固化剂=6:1(体积比)3.2混合使用寿命3.3.重涂间隔4、弛张筛结构件外表面用油漆系统三、注意事项1 在涂装中层漆和面漆之前应先检查前一道涂层表面是否有损坏、漏涂、流挂等现象,并进行处理,以达到规定的质量要求2 除了不易喷涂到的地方作刷涂之外,所有表面都要喷涂或滚涂施工。
四、完工检查1、漆膜:色泽均匀,无流挂、无漆雾、无污染。
2、缺陷:无针孔、无气泡、无漏喷等。
3、湿膜厚度与干膜厚度:根据规定的最低/最高厚度。
喷漆工操作规程

喷漆工操作规程一、引言喷漆工是指负责进行喷涂工作的专业技术人员。
为了确保喷漆工作的安全、高效和质量,制定本操作规程,规范喷漆工的操作流程和注意事项。
二、操作流程1. 准备工作(1)检查喷漆设备和工具的完好性,如喷枪、喷嘴、压缩空气供应等。
(2)检查喷漆材料的质量和储存条件,确保无异常。
(3)准备好个人防护装备,包括防护眼镜、防护口罩、手套等。
2. 表面处理(1)清洁工作面,确保无尘、无油污和杂质。
(2)修复任何表面缺陷,如刮痕、凹陷等。
(3)进行打磨,使表面光滑。
3. 涂料准备(1)根据工作要求选择适当的喷漆材料。
(2)按照涂料供应商的要求进行稀释或者搅拌。
(3)过滤涂料,确保涂料中无颗粒和杂质。
4. 喷涂操作(1)调整喷枪的喷嘴和压力,以适应不同的涂料和工作要求。
(2)保持喷枪与工作面的垂直距离恒定,通常为20-30厘米。
(3)均匀喷涂,避免浮现浓淡不均和滴漏现象。
(4)根据需要进行多遍喷涂,确保涂层均匀且厚度适当。
5. 喷涂后处理(1)等待涂料干燥,根据涂料供应商的要求进行时间控制。
(2)检查涂层的质量,如有需要,可以进行研磨和修复。
(3)清洁喷枪和喷漆设备,防止涂料残留和阻塞。
三、注意事项1. 安全第一,确保操作过程中的个人安全。
佩戴适当的防护装备,避免吸入有害气体和接触有害物质。
2. 严格按照操作规程进行操作,不得随意更改操作步骤和参数。
3. 喷漆操作应在通风良好的环境下进行,以避免有害气体积聚和爆炸危(wei)险。
4. 喷漆过程中禁止吸烟,防止引起火灾。
5. 喷漆设备和工具应定期维护和保养,确保其正常工作状态。
6. 注意涂料的储存和使用期限,避免使用过期或者质量不佳的涂料。
7. 在喷涂过程中,要注意避免喷漆材料接触到皮肤和眼睛,如故意外接触,应即将用清水冲洗并寻求医疗救助。
四、总结喷漆工操作规程是确保喷漆工作安全、高效和质量的重要依据。
喷漆工应严格按照操作规程进行操作,保持良好的工作习惯和注意事项,以确保工作的顺利进行和涂层的质量。
喷涂喷漆工艺规程

7.3 预处理中除锈(酸洗)或抛丸处理
7.3.1 化学除锈
处理槽名称
主要成分
处理温度
液面控制风速
硫酸酸蚀处理槽
硫酸 15-25%
0.35m/s
若丁 15-25%
盐酸酸蚀处理槽
盐酸 10-2允许放于有色金属零件和含有有色金属零件的钢铁零件;
1)加工精度在 以上的零件不准酸洗;
喷涂喷漆工艺规程
———————————————————————————————— 作者:
———————————————————————————————— 日期:
ﻩ
喷涂喷漆工艺规程
1.本规程的全部内容为强制性
2.编制本规程的依据是:
GB 7692—1999 《涂装作业安全规程,涂装前处理工艺安全及其通风净化》
9.4 所使用的面漆必须要充分搅拌均匀,并用120目以上的铜(不锈钢)筛网过滤,工作完毕后用稀释剂清洗干净喷枪;
9.5 底漆的喷涂要特别注意边缘棱角,底漆一般喷两道,在前一道底漆未干燥之前,不能喷下一次漆,干燥要适度,干燥小容易被面漆咬起,干燥过大,与面漆结合不好,容易形成缩孔和发酵,喷完底漆的工件,小心再次被污染;
6. 操作现场场地要求
6.1 操作场地应通风良好,首先启动通风设备。通风设备未启动之前,喷涂喷漆设备不应工作,涂喷漆工作结束后,通风设备应继续运行5-10分钟;
6.2 操作场地外露电气应接地保护,防止静电及漏电,接地电阻值应小于100Ω;
6.3 被喷涂喷漆的零件,或喷涂材料,与电极,电器或带电导体之间应保持一定的安全距离,至少为该电极及带电导体电压下火花放电距离的两倍,并应有明显的警告标志。
GB 12367—2006 《涂装作业安全规程,静电喷漆工艺安全》
喷漆工艺操作规程

1、喷面漆与底漆间隔时间保持在30分 钟以上。 2、按需用量调配油漆并搅拌均匀。 3、喷漆前调好喷枪幅度,并注意保养 好喷枪。 4、下班前盖好油漆桶盖,远离电器开 关,注意安全。
25~30cm 喷枪口径 φ1.4~φ1.6mm 调漆比例 面漆:稀释剂 1:1~1.2 工件与枪咀距离 25~30cm
工件喷漆工艺操作规程
喷丙烯酸防锈底漆→喷丙烯酸面漆→30分钟后
工合格后→入库
操作规范说明及注意事项 1、喷底漆前须将工件处的锈、油污、 灰尘清理干净。 2、按需用量调配油漆并搅拌均匀。 3、喷漆时,喷枪与工件间距保持在 25-30mm左右,垂直均匀行走。
钢铁工件喷漆工艺操作规程
一、工艺流程 工件喷砂除锈→除油去尘→喷丙烯酸防锈底漆→喷丙烯酸面漆→30分钟后
检验 { →合格→入库
→不合格→返工合格后→入库 二、喷漆工序和操作规范
工序 喷底漆
喷面漆
工艺技术参数 喷枪口径
φ1.6~φ1.8mm 喷漆气压4kg/cm2
调漆比例 底漆:稀释剂 1:1.2~1.5 工件与枪咀距离
喷漆工工艺守则

喷漆工艺守则一、喷漆前的表面处理:(1)铸件:对表面凸起不平处,应用工具进行磨凿平整,清除其表面污物。
(2)钢板件:一般应采取酸洗磷化处理,必须彻底清除残余酸液,以防漆层起泡。
(3)经机加工后的零部件,须用金属净洗剂或工业汽油等进行淋洗或刷洗,彻底清除表面的油污及其他赃物。
二、喷涂防锈底漆:底漆施工可用喷、刷、浸方法,漆膜要均匀,附着力要好。
三、填腻对于产品表面往往带有凹凸锈痕铸件砂孔等缺陷,必须采用填腻填平,每次填刮厚度应在0.5㎜以内,总厚度一般不超过1.5㎜为宜。
四砂磨:应用1#—2#金刚砂布或磨石在干燥的腻子表面进行砂磨,以达到表面平整去除粒屑,砂磨后需抹去表面的灰尘。
五水磨:将磨石或水砂纸全部浸湿,然后用少量水一起砂磨已干燥的涂层或腻子,以湿布擦净粉浆,最后的砂纹应不影响涂膜外观的性能。
六、喷涂面漆:应根据设计要求规定的漆类,调配置适当的粘度喷涂。
七、干燥:应放在通风、早晚干燥的地方,根据工艺规程严格控制,八、注意事项:1、涂装环境应清洁,无灰尘,施工时温度不得低于12℃,相对湿度不得低于80%。
2、喷漆时采用的压缩空气不允许含有油和水,并应经常检查油水分离器的可靠性。
3、钢板焊接件采用酸洗时,应特别注意把焊缝等地方的酸液及时清洗干净。
4、经清理或磷化处理过的表面不允许受到雨水、潮气、污物及腐蚀气体等的作用,并应在10小时内涂上底漆。
5、调配漆液时,应充分搅拌均匀,对底漆采用120目,而漆采用200目的钢丝网过滤。
6、漆种的稀释应使用规定的稀释剂,禁止不同漆种及稀释剂相互掺用,防止变质。
7、按工艺规程使喷枪和压缩机,每班后清洗喷枪,关闭电源。
8、在涂装施工过程中,操作人员必须穿戴防护用品,并要防止漆与皮肤直接接触。
威海市海翔试验机制造有限公司工艺科2003年12月。
喷涂喷漆工艺规程
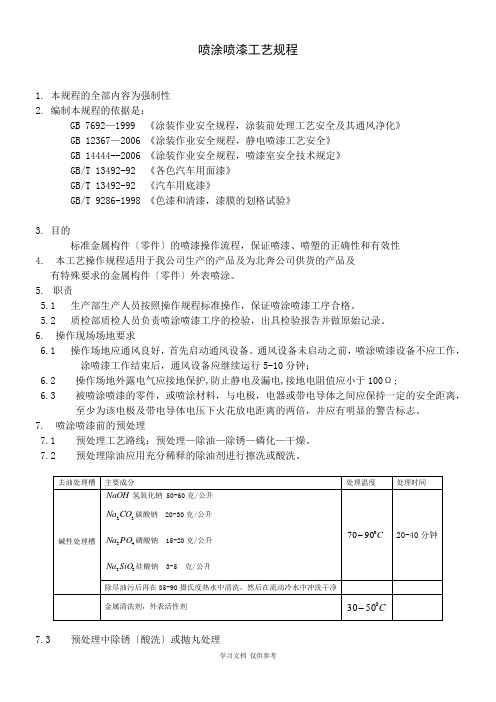
喷涂喷漆工艺规程1.本规程的全部内容为强制性2.编制本规程的依据是:GB 7692—1999 《涂装作业安全规程,涂装前处理工艺安全及其通风净化》GB 12367—2006 《涂装作业安全规程,静电喷漆工艺安全》GB 14444--2006 《涂装作业安全规程,喷漆室安全技术规定》GB/T 13492-92 《各色汽车用面漆》GB/T 13492-92 《汽车用底漆》GB/T 9286-1998 《色漆和清漆,漆膜的划格试验》3.目的标准金属构件〔零件〕的喷漆操作流程,保证喷漆、喷塑的正确性和有效性4.本工艺操作规程适用于我公司生产的产品及为北奔公司供货的产品及有特殊要求的金属构件〔零件〕外表喷涂。
5.职责5.1 生产部生产人员按照操作规程标准操作,保证喷涂喷漆工序合格。
5.2 质检部质检人员负责喷涂喷漆工序的检验,出具检验报告并做原始记录。
6. 操作现场场地要求6.1 操作场地应通风良好,首先启动通风设备。
通风设备未启动之前,喷涂喷漆设备不应工作,涂喷漆工作结束后,通风设备应继续运行5-10分钟;6.2 操作场地外露电气应接地保护,防止静电及漏电,接地电阻值应小于100Ω;6.3 被喷涂喷漆的零件,或喷涂材料,与电极,电器或带电导体之间应保持一定的安全距离,至少为该电极及带电导体电压下火花放电距离的两倍,并应有明显的警告标志。
7. 喷涂喷漆前的预处理7.1 预处理工艺路线:预处理—除油—除锈—磷化—干燥。
7.2 预处理除油应用充分稀释的除油剂进行擦洗或酸洗。
7.3 预处理中除锈〔酸洗〕或抛丸处理7.3.1 化学除锈操作要求酸洗槽内不允许放于有色金属零件和含有有色金属零件的钢铁零件;1)2)小型零件不能直接放入槽中,应放在框内或悬挂后放置槽内;3)酸洗后零件外表的黑膜冲洗不掉时,可以用毛刷刷掉之;4)每隔10-15分钟检查一次酸洗情况,一直到到达要求为止;5)防止温度过高和酸洗时间过长,造成零件过蚀;6)槽液铁盐含量到达200克/公升以上,或酸液浓度稀至5%以下时,更换新液;7)酸洗后再在流动冷水槽中仔细清洗零件;8)清洗后用压缩空气吹干,或自然干燥12-24h。
喷涂的工艺流程(3篇)

一、前言喷涂是一种将涂料均匀涂覆在物体表面的工艺,广泛应用于汽车、建筑、家具、金属制品等行业。
喷涂工艺具有施工简便、涂层均匀、附着力强等优点,能够提高产品的外观质量和使用寿命。
本文将详细介绍喷涂工艺的流程,以供相关从业人员参考。
二、喷涂工艺流程1. 准备工作(1)材料准备:根据产品要求,选择合适的涂料、固化剂、稀释剂等材料。
涂料应符合国家相关标准,确保产品质量。
(2)设备准备:检查喷涂设备是否正常,包括喷枪、喷壶、搅拌器、空气压缩机等。
(3)场地准备:确保喷涂场地通风良好,无灰尘、油污等杂质,地面平整。
2. 喷涂前的表面处理(1)清洗:使用溶剂或水将物体表面的油污、灰尘、锈蚀等杂质清洗干净。
(2)打磨:对物体表面的凹凸不平、焊缝、焊点等部位进行打磨,提高涂层的附着力。
(3)磷化:对金属表面进行磷化处理,提高涂层的耐腐蚀性。
3. 喷涂作业(1)涂装前的准备工作:将涂料、固化剂、稀释剂按比例搅拌均匀,确保涂料均匀。
(2)喷涂方法:根据产品形状、尺寸和涂料特性选择合适的喷涂方法,如空气喷涂、高压无气喷涂等。
(3)喷涂参数:根据涂料特性、物体表面及环境温度等因素调整喷涂压力、喷枪距离、喷涂速度等参数。
(4)喷涂操作:手持喷枪,均匀地喷涂涂料,避免漏喷、流淌、堆积等现象。
(1)自然固化:将喷涂后的物体放置在通风、干燥的环境中,待涂料自然固化。
(2)加热固化:对需要快速固化的物体进行加热处理,提高固化速度。
5. 检查与修整(1)外观检查:检查涂层颜色、光泽、厚度、平整度等是否符合要求。
(2)附着力检查:使用专用仪器检测涂层与物体表面的附着力。
(3)修整:对不符合要求的涂层进行修整,如打磨、补涂等。
6. 包装与储存(1)包装:将完成喷涂的物体进行包装,防止涂层受到污染。
(2)储存:将包装好的物体存放在干燥、通风、避光的场所,避免阳光直射和潮湿。
三、喷涂工艺注意事项1. 涂料选择:根据产品要求、施工环境等因素选择合适的涂料。
油漆、喷漆工安全技术操作规程模版

油漆、喷漆工安全技术操作规程模版一、介绍油漆、喷漆工作是建筑施工中常见的工艺之一,但由于其涉及到化学品、高温等安全隐患,必须严格按照操作规程进行操作,以确保工作的安全和质量。
本文将详细介绍油漆、喷漆工操作的安全技术规程,力求提高工作人员的安全意识和操作水平。
二、操作前的准备工作1. 安全培训所有从事油漆、喷漆工作的人员必须接受相关的安全培训,掌握操作规程、事故预防等知识,并熟悉相关的PPE(个人防护装备)的选择和使用。
2. 安全装备准备2.1 根据工作环境和需求,配备符合国家标准的个人防护装备,包括防护眼镜、防护面具、防护手套、防护服等。
2.2 检查使用的工具、设备的完好性和稳定性,确保其可以安全可靠地使用。
3. 作业现场准备3.1 清理作业现场,确保周围没有易燃、易爆物品,并保持通风良好。
3.2 确保喷漆设备和油漆材料的质量和准备充足。
三、涂料和喷漆工具的选择使用1. 根据工作需要选择合适的涂料,应遵循以下原则:- 耐化学性:根据所需的耐化学性选择相应的油漆材料;- 燃烧性:选择不易燃烧的油漆材料;- 空气污染物排放:选择环保无污染的涂料材料。
2. 使用喷漆工具时,应遵循以下原则:- 确保喷枪、喷嘴等喷漆工具的安全并正确使用;- 确保喷漆工具的操作实现涂层厚度的均匀性和一致性;- 配备有效的喷漆过滤器和废气处理设备。
四、操作规程1. 强化安全意识:- 油漆、喷漆工作时要始终保持警惕,注意材料和设备的安全性;- 严禁在工作中抽烟,避免引起火灾事故。
2. 个人防护:- 确保所有工作人员都佩戴合适的个人防护装备;- 对护目镜、防护面具、防护手套等个人防护装备进行定期检查和更换;- 当涉及到高温、腐蚀性材料时,需穿戴防火服和防腐蚀服。
3. 安全操作:- 操作人员应熟悉喷漆工具的使用方法,并遵循使用说明书;- 在操作过程中要保持工作区域的整洁,避免杂物干扰;- 对于高空作业,应使用安全带等安全设备,并确保工作平台的稳定。
- 1、下载文档前请自行甄别文档内容的完整性,平台不提供额外的编辑、内容补充、找答案等附加服务。
- 2、"仅部分预览"的文档,不可在线预览部分如存在完整性等问题,可反馈申请退款(可完整预览的文档不适用该条件!)。
- 3、如文档侵犯您的权益,请联系客服反馈,我们会尽快为您处理(人工客服工作时间:9:00-18:30)。
喷涂喷漆工艺规程
1.本规程的全部内容为强制性
2.编制本规程的依据是:
GB 7692—1999 《涂装作业安全规程,涂装前处理工艺安全及其通风净化》
GB 12367—2006 《涂装作业安全规程,静电喷漆工艺安全》
GB 14444--2006 《涂装作业安全规程,喷漆室安全技术规定》
GB/T 13492-92 《各色汽车用面漆》
GB/T 13492-92 《汽车用底漆》
GB/T 9286-1998 《色漆和清漆,漆膜的划格试验》
北奔公司Q/NB.J04002-2013、DBL 7390.00和DBL2391.00涂漆技术要求
3.目的
规范金属构件(零件)的喷漆操作流程,保证喷漆、喷塑的正确性和有效性
4.本工艺操作规程适用于我公司生产的产品及为北奔公司供货的产品及
有特殊要求的金属构件(零件)表面喷涂。
5.职责
5.1 生产部生产人员按照操作规程规范操作,保证喷涂喷漆工序合格。
5.2 质检部质检人员负责喷涂喷漆工序的检验,出具检验报告并做原始记录。
6. 操作现场场地要求
6.1 操作场地应通风良好,首先启动通风设备。
通风设备未启动之前,喷涂喷漆设备不应工作,
涂喷漆工作结束后,通风设备应继续运行5-10分钟;
6.2 操作场地外露电气应接地保护,防止静电及漏电,接地电阻值应小于100Ω;
6.3 被喷涂喷漆的零件,或喷涂材料,与电极,电器或带电导体之间应保持一定的安全距离,
至少为该电极及带电导体电压下火花放电距离的两倍,并应有明显的警告标志。
7. 喷涂喷漆前的预处理
7.1 预处理工艺路线:预处理—除油—除锈—磷化—干燥。
7.2 预处理除油应用充分稀释的除油剂进行擦洗或酸洗。
7.3 预处理中除锈(酸洗)或抛丸处理
7.3.1 化学除锈
操作要求
酸洗槽内不允许放于有色金属零件和含有有色金属零件的钢铁零件;
1)
2)小型零件不能直接放入槽中,应放在框内或悬挂后放置槽内;
3)酸洗后零件表面的黑膜冲洗不掉时,可以用毛刷刷掉之;
4)每隔10-15分钟检查一次酸洗情况,一直到达到要求为止;
5)防止温度过高和酸洗时间过长,造成零件过蚀;
6)槽液铁盐含量达到200克/公升以上,或酸液浓度稀至5%以下时,更换新液;
7)酸洗后再在流动冷水槽中仔细清洗零件;
8)清洗后用压缩空气吹干,或自然干燥12-24h。
7.3.2 机械除锈(手工除锈或抛丸处理)
7.3.2.1 手工除锈:砂布,水砂纸,抛光或抛光机抛光
7.3.2.2 抛丸处理:
7.3.2.2.1 抛丸粒径Φ0.5-Φ1.8 每工作40小时,补加钢丸500kg;
7.3.2.2.2 将零件用行车和吊钩悬挂在环轨吊钩上,在设定的线速度下(14-20m/h),进入清
理室;
7.3.2.2.3 调节供料闸门,将抛丸器负载电流调节到20±2A后开机,当抛丸器负载电流小于
工作电流时,需补充新钢丸500kg;
7.3.2.2.4 依次开启Ⅰ--Ⅴ抛丸器,每个抛丸器开启时间间隔为5秒;
7.3.2.2.5 抛光处理后,零件表面应呈现均匀的金属色泽,达到表面清洁度Sa2.5级,粗糙
度达到Rz25-75um;
7.3.2.2.6 零件抛丸后,必须在4小时内做防护处理,当在湿度大于80%的气候条件下,必
须在2小时之内做防护处理,超过规定时间,重新进行抛丸处理;
7.3..2.2.7 零件抛丸后,用高压气体清理零件表面和螺纹孔中残余的弹丸和沙尘,并应戴好
无污物手套后搬运,防止新的污染;
7.3.2.2.8 实施抛丸操作时,应穿戴好防护用品。
8. 喷塑
8.1 喷塑过程中,注意优选工艺参数,目的是使粉末获得尽可能多的电荷,并在工件表面上达
到均匀的粉末涂层;
8.2 将工件挂靠在移动小车挂架上,移送至喷粉室,关闭折叠门;
8.3 打开高压静电发生器,通常调整高压在50-80V之间,电流值不大于300uA,喷粉枪柄必须
可靠接地,供粉量应根据喷涂状况随时调整,一般单位时间粉量在50-250g/min左右;
8.4 换粉和加粉过程中,不得混入杂质,保证输气、输粉畅通无阻,无漏气漏粉现象;
8.5 加热固化,将喷涂好的零件,轻轻地平稳地移出喷粉室,然后再平稳地送入低温辐射固化
加热炉,将温度调整在180度左右,20分钟即可,出炉后自然冷却,检查入库;
8.6 静电喷涂电压的高低是喷涂效果的关键,电压的选择一定要针对涂料品种及导电性能考
虑,适当进行调整;
8.7 产品色泽要符合要求,无起泡,露底现象。
9. 喷漆
9.1 零件表面应按预处理程序处理干净,现银灰色金属光泽,无油、无锈,无赘物等;
9.2 使用底漆稀释剂,面漆应符合工艺文件要求,喷涂应均匀,无流痕、刷痕、起泡、皱纹、
露底等缺陷,安装面或搭接面不得沾漆;
9.3 温度对漆液、漆膜粘度影响非常大,调配漆料和清漆时尽量保持存储场所及调配场所、操
作现场的温度相当;
9.4 所使用的面漆必须要充分搅拌均匀,并用120目以上的铜(不锈钢)筛网过滤,工作完毕
后用稀释剂清洗干净喷枪;
9.5 底漆的喷涂要特别注意边缘棱角,底漆一般喷两道,在前一道底漆未干燥之前,不能喷下
一次漆,干燥要适度,干燥小容易被面漆咬起,干燥过大,与面漆结合不好,容易形成缩
孔和发酵,喷完底漆的工件,小心再次被污染;
9.6 面漆在底漆干燥后进行,面漆喷涂应均匀、致密、光亮,并完全覆盖前一道漆层,面漆一
般喷2-3层,每喷一层漆,干燥后才能喷下一层漆,底漆漆膜厚度一般为30-40um,面漆
漆膜厚度为30-45um,底漆加面漆漆膜总厚度为60—150um;
10.电泳+面漆
10.1 前处理
10.2 电泳+面漆
11. 质量检查
11.1 预处理的检验:经预处理的零件表面必须干燥,清洁,无油污,无锈迹,否则必须重新
处理,再次检验合格后才能进入下一道工序;
11.2 底漆一般喷2遍,面漆一般喷2-3遍,每喷一道漆必须经干燥后才能喷下一道漆,室温
在15度以上时底漆一般干燥40-90分钟,面漆一般干燥30—40分仲,整体漆喷完干燥24小时后方可交货; 11.3 零件表面喷漆层应光滑平整,色泽一致,无气泡、漆瘤、流挂、皱纹等明显颗粒杂质存
在;
11.4 漆膜厚度均匀,无露底,并达到图纸工艺要求厚度;
11.5 漆膜对底材上脱离的抗性(附着力)检验,采用划格方法检验(车间现场); 11.5.1 交检零件在规定条件下至少放16小时以上;
11.5.2 切割数:切割图形,每个方向(090)的切割数应是6;
11.5.3 切割间距:每个方向的切割间距应相等,且切割间距取决于涂层的厚度和底材的类型:
0-60um 硬底材切割间距1mm (一般用于底漆) 0-60um 软底材 切割间距2mm (一般用于面漆) 60-120um 硬或软底材 切割间距2mm 121-150um 硬或软底材切割间距3mm
11.5.4 手工法切割涂层 11.5.4.1 单刀切割刀具
11.5.4.2 试验结果,共分六级
注:通常评定通过/不通过采用前三级
11.5.4.3 操作方法:
11.5.4.3.1 手握切割刀具,垂直于切割表面均匀拖动,按照间距,用均匀的速度在底材上形成
规定的切割数,重复动作,再作相同数量且与上次切割线90度面相交的平行切割线,
形成网格图形;
11.5.4.3.2 用透明的压敏胶粘带宽25mm 粘着力10±1N/25mm的胶带粘在网格上,胶粘的长度
至少超过网格20mm(手握部分)。
并用手指用力蹭胶粘带,透过胶带看到涂层颜色
全面接触显示接触良好。
在粘上胶粘带5分钟内,拿住胶带悬空一端,在接近60
度面0.5-1.0s内平稳地撕离胶带,用放大镜观察计算。
11.5.4.4 检验报告
检验报告应括下下列内容
a)识别产品所需的所有的必要细节;
b)注明参照GB/T 9286-1998;
c)涂层使于底材上的方法,干燥时间,切割刀具类型;
d)评定的检验结果;
e)与规定试验方法的任何不同之处;
f)检验日期
大成机电设备公司技术部
2013.10.24。