德国原装URACA乌拉卡高压柱塞泵型号
ISCO高精度柱塞泵

!"#$%&'() *+,-
!"#
!"#$%&'()*+$, OMIMMMéëá !"#$%&' !"#$ !"#$%&'( L "#+ !" QMMãiL !"# fëÅç !"#$%&'()*
!"#$
fëÅç !"#$ !"#$%&'()*+ káíêçåáÅ=RM !"#$%& !"#$%&'()*+,# !" -./0 !"#$%&'()*+,-./01%23456 !"#$%&'( !"#$%&' !"#$%&'()*+,!"#$%&'()*+,-./ !"#$%& !
!"#$%&'()*+,-./0-1 !"#$%&
!"
a ri !"#$%&'()*%+,-./0 !"#$ `b !" ri ! riPNMN bkSNMNMJN
!"#$%&
!"#$% !"#$ !"#$%&'()* +,-./0 OMM !" JOM !"#$%&'( %&'()* !"#$%&'()*+,-./0 !"#$%&'()*+,-./
耐腐蚀柱塞泵型号参数
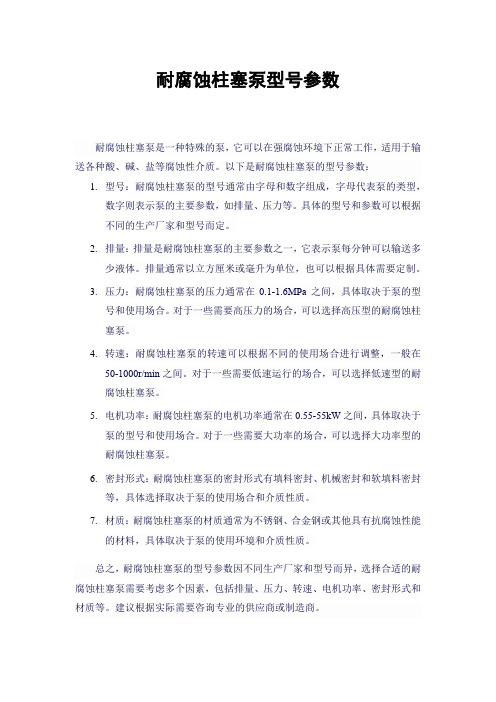
耐腐蚀柱塞泵型号参数
耐腐蚀柱塞泵是一种特殊的泵,它可以在强腐蚀环境下正常工作,适用于输送各种酸、碱、盐等腐蚀性介质。
以下是耐腐蚀柱塞泵的型号参数:
1.型号:耐腐蚀柱塞泵的型号通常由字母和数字组成,字母代表泵的类型,
数字则表示泵的主要参数,如排量、压力等。
具体的型号和参数可以根据不同的生产厂家和型号而定。
2.排量:排量是耐腐蚀柱塞泵的主要参数之一,它表示泵每分钟可以输送多
少液体。
排量通常以立方厘米或毫升为单位,也可以根据具体需要定制。
3.压力:耐腐蚀柱塞泵的压力通常在0.1-1.6MPa之间,具体取决于泵的型
号和使用场合。
对于一些需要高压力的场合,可以选择高压型的耐腐蚀柱塞泵。
4.转速:耐腐蚀柱塞泵的转速可以根据不同的使用场合进行调整,一般在
50-1000r/min之间。
对于一些需要低速运行的场合,可以选择低速型的耐腐蚀柱塞泵。
5.电机功率:耐腐蚀柱塞泵的电机功率通常在0.55-55kW之间,具体取决于
泵的型号和使用场合。
对于一些需要大功率的场合,可以选择大功率型的耐腐蚀柱塞泵。
6.密封形式:耐腐蚀柱塞泵的密封形式有填料密封、机械密封和软填料密封
等,具体选择取决于泵的使用场合和介质性质。
7.材质:耐腐蚀柱塞泵的材质通常为不锈钢、合金钢或其他具有抗腐蚀性能
的材料,具体取决于泵的使用环境和介质性质。
总之,耐腐蚀柱塞泵的型号参数因不同生产厂家和型号而异,选择合适的耐腐蚀柱塞泵需要考虑多个因素,包括排量、压力、转速、电机功率、密封形式和材质等。
建议根据实际需要咨询专业的供应商或制造商。
径向泵(高压大排量)

一、TRP-500、750、1000高压大排量径向柱塞泵
高压大排量径向柱塞泵主要应用于大型锻压设备,也可服务于装备制造、航空航天、数控机床、船舶等四大领域,高压大排量径向柱塞泵是国内多家科研院所著名专家与协作企业历时近20年共同开发的产品,2000年研制成功了TRP-750径向柱塞泵,2005年研制成功了TRP-500径向柱塞泵;2007年以后为了满足市场和广大用户的需求,组建成立了兰州泰瑞液压设备有限公司,已形成了批量生产径向柱塞泵、轴向柱塞泵和超高压径向柱塞泵的系列产品。
多年来为首钢、包钢、齐钢、包头二机厂等单位解决了进口泵价格高、周期长的难题,并节省了大量外汇。
是首钢、包钢、齐钢、包头二机厂径向柱塞泵专供厂家。
2011年泰瑞液压承担了国家重大专项《高压大排量径向柱塞泵系列化研制》课题,课题主要针对TRP-1000径向柱塞泵研发,与浙江大学、西安交大、贵州力源、北方重工等八家单位协作研发,历时3年目前已形成了批量生产。
二、德国威普克径向柱塞泵维修及国产化改造
1、RKP系列制造维修规格为:排量25ml/r、32ml/r、45ml/r、50ml/r、63ml/r、90ml/r、160ml/r、250ml/r 。
2、RX系列制造维修规格为:排量360ml/r、505ml/r、750ml/r、1000ml/r。
进口型号为:RX160、RX250、RX360、RX500。
3、RV、RF、RH系列径向柱塞泵维修
泰瑞液压是国内唯一一家有能力承担威普克-潘克泵维修的专业厂家,并且公司生产的TRP系列泵可以替代威普克-潘克进口泵,多年来承担了首钢、包钢、北满特钢、北方重工等厂家进口泵的维修,并实现了国产化改造。
Hartmann柱塞泵

Date
Model Assy. #
SO
☺
Maximum Pressure _3000_ psi
♦
Description of failure
Volumetrics
Flow at 500 psi ________ gpm Flow at 1500 psi ________ gpm Flow at 1000 psi _______ gpm Flow at 2000 psi _______ gpm
14
WS2是NASA研 發的用作太空探 測飛船用的潤滑 材料(在高真空和 高溫下,常用的 潤滑劑都會失效)
摩擦系數
不貼附 耐溫性 與液態氧的兼容 密度
PVX系列的柔性安裝
排氣系統
泄油口 一般安裝 側面安裝 向下安裝
建議使用雙泄油孔,加強排氣功能 !!!
垂直安裝
内置泄油口
推薦選用排氣孔設計
15
PVX系列水基型號
75
100
60
80
45
60
30
40
15
20
0
0 500 1000 1500 2000 2500 3000
0 3500
பைடு நூலகம்Pump Pressure (psi)
Compensated Output of PVX XXXXX Pump ISO 32 Oil @ 120 °F
75 90
60
72
45
54
30
36
11
PVX系列工作介質
特殊調配油液 可採用多種特殊油液:
1)sub-sea preparations 2)耐燃性油 3)水乙二醇 4)轉化乳膠 5)高水基液壓油 (HWCF) 6)磷酸鹽酯 7)多元醇酯 8)合成油液
德国原装URACA乌拉卡高压柱塞泵型号

High pressure plunger pumpsHigh pressure plunger pumps for use in extreme conditionsReciprocating plunger pumps play a key role in almost all areas of process technology where fluids must be handled against high pressure.Possible fields of application and types of jobs are so varied that there is a con- stant need for new designs and materials in order to meet customer demands for new pump versions.Plunger pumps are used in indus- try where there are high or maxi- mum operating pressures. At a constant speed their capacity is virtually independent of operating pressure – an important feature in control operations. Capacity is proportional to speed. In all power ranges plunger pumps display high overall efficiency, which is as a rule above 90 %. This also applies to partial load operation. This is why plunger pumps are among the most economical machines – a major factor in view of rising energy costs.Uraca pumps are used worldwide.Test pumps are used for hydro- static pressure testing, including the testing of pipes, pipelines, vessels and containers, gas cylin- ders and many other high-pressure components. The units are also available for use in potentially explosive area zone 2 (equipment group II, equipment category 36 according to ATEX).Industrial pumps can be used in virtually all industrial areas, including heavy industry, energy technology, the oil industry as well as in the food and textile industry.The pumps are used mainly as drives for rolling mills, boiler feed pumps, pumps for hydrostatic bearing lubrication, for descaling as well as for cleaning with high- pressure w ater.Chemical and process pumps are used for hot, aggressive, abrasive, toxic agents as well as for liquid gases.The areas of application are mainly in the chemical and petro- chemical industry, but also in the manufacture of detergents, the recycling of plastics and oil residues as well as injection and the extraction of oil from coal.Pump units can be installed for the most varied of applications with diesel or electric motors.3Perfection in detailPower endsURAC A ’s power ends are usedworldwide. Every day they provethemselves in continuous operationto the satisfaction of our cus- tomers. The fields of application range from the polar circle tothe tropical climate zones. High operating safety and above-average service life are typicalURAC A features.Power ends for higher power requirements are equipped with oil cooling and forced oil lubrication. Power ends for lower powerrequirements have centrifugal lubrication. The various series cover a power range of up to approx. 2600 kW.The power ends for series KD 600 and KD 700 are compact and have a low weight coefficient. Power end and liquid end are separated by an intermediate chamber and special crosshead seals, preventing any liquid from entering the power end.The power ends of the big pumpseries KD 800 have an incline- divided power end for easier installation and for easier mainte- nance of the crank mechanism. The power ends are equipped with a bridge for centering of long stuffing boxes.The new generation of the P-series has a crankshaft with multiple slide bearings and features three power groups with 3, 5 and 7 plungers.4Stuffing boxesDue to the wide-range of appli-cations for our plunger pumps,stuffing boxes and seals aredesigned to meet the requisites ofthe respective liquid. Easy-to-handleliquids, such as water, emulsionsor similar, can be controlled withsimple seals.URACA will provide the bestpossible design to match the liquidyou handle.With fluids it is necessary, forexample, to take special measuresto reduce dead space or to installplunger guide bushes that are self-lubricating. The more demandingthe liquid is, the more extensivethe back up systems integrated inthe stuffing boxes. Consequently,heating, cooling, synchronousinjection, flushing or interlockingcomponents can be installed.Valve blocksThe design of the valve blocksdepends to a high degree on theproperties of the respective liquid.Cone, plate and ball valves areavailable. What they have incommon is high efficiency, lowwear and tear and outstandinglyeasy maintenance.5Leak-free handlingHeightened environmental awareness requires both the pump manufacturer and the operator to consider leak-free handling when designing and selecting the pumping equipment.URACA diaphragm pumps offer aunique solution in the handling ofdangerous fluids. They help in parti-cular to increase the operatingsafety of production plants and toimprove the working conditions ofthe operatives. Hermetically sealedplunger pumps are mainly used fortoxic, explosive, aggressive, foul-smelling, environmentally harmfulor abrasive fluids. URACA diaphragm pumps offer the advantages of a piston sealing that is virtually free of wear and tear as well as abso- lutely leak-free handling.URAC A diaphragm pump heads operate at a pressure range of up to 350 bar, while the temperatures of the fluid handled can be from -40 to +150° C . The PTFE-dia- phragm, which is resistant to virtu- ally all fluids, hermetically seals the fluid chamber. The selection ofmaterials for the parts touchedby the fluid as well as the designof the self-acting valves andthe stroke frequency of the pumpdepend on the respective fluid.Integrated monitoring systems pre-vent any overload of the unitand signal any diaphragmfailures immediately.URAC A diaphragm pumps are available in a power range of up to 250 kW. Operating pressure may be350 bar, capacity up to 850 l /min.URAC A diaphragm pumpsfeature the following specific advantages:■ Economy ■ High operatingsafety■ High service quality■ Space-saving design■ Flexibility of drive6▲▲Consistent URACA quality – the basis of a mutually beneficial relationshipProduct research and develop- ment at modern 3D-C AD-work- places to meet customer s’ needs and wants.Precision machining guarantees failure-free service lifeMeticulous assembly work by a highly trained and committed workforceA trial run lasting several hours on the test bed as well as comprehen- sive test programs are a demon- stration of guaranteed excellence.Many years of service life at the customer – the basis of a mutually beneficial relationship.7VP.e5.6L+S High Pressure –State of the Art Technology –WorldwideU RA CA Pumpenfabrik GmbH& Co. K GSirchinger Straße 15D-72574 B ad U rach, GermanyPhone +49 (71 25) 133 - 0Fax +49 (71 25) 133 - 202*************w ww.uraca.deCertified acc. to:■DI N EN IS O 9001:2000 by LRQ A■VGB KTA 1401■GostURACA is a leading manufacturer ofhigh pressure plunger pumps andhigh pressure water jettingtechnology equipment. Since 1893the company has been a globalleader in the development of thistechnology.URAC A‘s core competency lies inthe development, design,and manufacture of high pressureplunger pumps, pump units, andaccessories for almost all industrialfields.URACA offers leading technologicalknow-how in the field of fullyautomated and process-integratedsystem technology.The key focus is on two marketsegments:■High-performance pumpsolutions for the CPI sectorsand heavy industry.■ A universal and modularcomplete programme for high-pressure water jettingtechnology, especially for highlyautomated plants.The German domestic marketis covered by URAC A sales centersand a network of service centers.Internationally, URAC A hassubsidiaries and agencies.Additionally numerous representa-tives underline the company’spresence around the globe.A high standard of research anddevelopment, plus a modernmanufacturing facility stand forunsurpassed product quality.Ongoing market research and closeattention to current marketneeds safeguards the company’stechnological l eadership.Each URAC A cu stomer profits fromthis comprehensive experienceand technology and will find thatURACA is a highly competentpartner in the solution of theircleaning problems.。
Sigma Aldrich WP6111560 泵机用户指南说明书
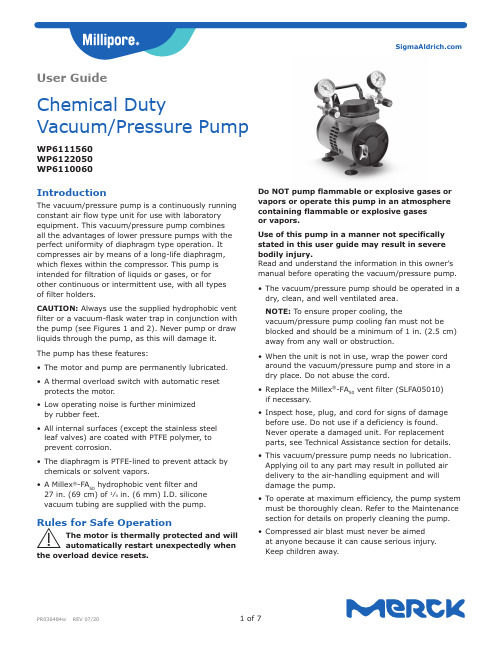
User GuideChemical DutyVacuum/Pressure PumpWP6111560 WP6122050 WP6110060IntroductionThe vacuum/pressure pump is a continuously running constant air flow type unit for use with laboratory equipment. This vacuum/pressure pump combines all the advantages of lower pressure pumps with the perfect uniformity of diaphragm type operation. It compresses air by means of a long-life diaphragm, which flexes within the compressor . This pump is intended for filtration of liquids or gases, or forother continuous or intermittent use, with all types of filter holders.CAUTION: Always use the supplied hydrophobic vent filter or a vacuum-flask water trap in conjunction with the pump (see Figures 1 and 2). Never pump or draw liquids through the pump, as this will damage it.The pump has these features:• The motor and pump are permanently lubricated.• A thermal overload switch with automatic reset protects the motor .• Low operating noise is further minimized by rubber feet.• All internal surfaces (except the stainless steel leaf valves) are coated with PTFE polymer , to prevent corrosion.• The diaphragm is PTFE-lined to prevent attack by chemicals or solvent vapors.• A Millex ®-FA 50 hydrophobic vent filter and 27 in. (69 cm) of 1⁄4 in. (6 mm) I.D. silicone vacuum tubing are supplied with the pump.Rules for Safe OperationYThe motor is thermally protected and will automatically restart unexpectedly whenthe overload device resets.Do NOT pump flammable or explosive gases or vapors or operate this pump in an atmosphere containing flammable or explosive gases or vapors.Use of this pump in a manner not specifically stated in this user guide may result in severe bodily injury.Read and understand the information in this owner’s manual before operating the vacuum/pressure pump.• The vacuum/pressure pump should be operated in a dry, clean, and well ventilated area.NOTE: To ensure proper cooling, thevacuum/pressure pump cooling fan must not be blocked and should be a minimum of 1 in. (2.5 cm) away from any wall or obstruction.• When the unit is not in use, wrap the power cord around the vacuum/pressure pump and store in a dry place. Do not abuse the cord.• Replace the Millex ®-FA 50 vent filter (SLFA05010) if necessary.• Inspect hose, plug, and cord for signs of damage before use. Do not use if a deficiency is found. Never operate a damaged unit. For replacement parts, see Technical Assistance section for details. • This vacuum/pressure pump needs no lubrication. Applying oil to any part may result in polluted air delivery to the air-handling equipment and will damage the pump.• To operate at maximum efficiency, the pump system must be thoroughly clean. Refer to the Maintenance section for details on properly cleaning the pump.• Compressed air blast must never be aimed at anyone because it can cause serious injury. Keep children away.GA B D E• All vacuum/pressure pumps generate heat, even under normal operating conditions. To avoid serious burns, never touch the head parts or tubing during and immediately after operation.• If higher vacuum or pressure is required, use the High Output Vacuum/Pressure Pump (WP6211560, WP6222050, WP6210060).Usage Guidelines• Always use the Millex ®-FA 50 vent filter and1/4 inch silicone tubing included with the pump when applying vacuum. This will prevent liquids or vapors from entering the pump. A properly attached Millex ®-FA 50 vent filter is illustrated in Figure 1.• For maximum protection of the pump, use theMillex ®-FA 50 vent filter AND a vacuum trap to protect the pump from vapors and gases. The vacuum trap consists of a 1 liter filtering flask (Cat. No. XX1014705), No. 8 stopper (XX1014708) and silicone tubing. Additional tubing is available as Cat. No. XX7100004. This assembly is illustrated in Figure 2.• Never pump or draw liquids through the pump. This will damage the pump. The filter flask and vacuum trap should be emptied after each use.Filter flask Vacuum trap Vacuum pumpFilter flask Vacuum trap Vacuumpump Figure 1. Proper use of Millex ®-FA filterProduct Labeling SymbolsYWARNING Direction of Pressure Control(Valves)ON(Power)Hot SurfaceOFF(Power)Protective Conductor TerminalHow to Use the Chemical DutyVacuum/Pressure PumpThe Vacuum/Pressure Pump is shipped ready foruse. See the Specifications section for requiredoperating conditions.CAUTION: The pump is rated for indoor use only.CAUTION: Be sure available power matchesunit requirements. A grounded three-conductorAC electrical source is required. Units are available for115 V~ 60 Hz, 100 V~ 50/60 Hz, or 230 V~ 50 Hz.See the Specifications section for details of electricalsupply options available.1. Unpack the unit and retain all packing material untilyou verify proper product operation.2. The unit rests on four vibration isolator pads. Placethe unit on a suitable surface, such as a bench,desk, or table. Be sure not to block the ventilationholes located on the motor housing.3. Select appropriately-sized tubing, according to yourapplication. Use approximately 1⁄4 in. I.D. tubing towithstand the anticipated pressure or vacuum.CAUTION: During vacuum filtration, use thesupplied Millex®-FA50hydrophobic vent filter,to prevent excessive amounts of liquids or mistfrom entering the pump (Figure 1). For maximumprotection, use a vacuum-flask water trap(Figure 2).4. Prepare the necessary equipment or filter holder andconnect the tubing to the equipment. Do not connectthe tubing to the pump.5. Plug the power cord into an appropriateelectrical source.CAUTION: Do not turn the pump on withequipment or filter holder already attached.If the pump is inadvertently turned on with thetubing fully connected and it does not run, turnoff the pump and disconnect the tubing. Restartthe pump and then reconnect the tubing. If thepump’s thermal overload switch automaticallyshuts off the motor, disconnect the tubing andallow the pump to cool for at least 10 minutesbefore restarting. Reconnect the tubing only afterthe pump is operating.6. Turn on the pump, using the toggle switch locatedon the front of the pump.7. Connect the tubing from the filter holder or otherequipment to the pump and begin your procedure.8. If using the pump for vacuum: Adjust thevacuum by closing the pressure regulatorand opening the vacuum regulator fully(counterclockwise). Slowly tighten down (clockwise)the vacuum regulator until you obtain the desiredvacuum reading on the vacuum gauge.If using the pump for pressure: Adjust thepressure by turning the vacuum regulator downfully and opening the pressure fully (turn counterclockwise). Slowly tighten down (turn clockwise)the pressure regulator until you obtain the desiredpressure reading on the pressure gauge.9. Turn off the pump when you are finished.Disconnectthe tubing first from the pump and then from thefilter holder or other equipment.MaintenanceUnder normal operating conditions, and usingproper handling procedures, the chemical dutyvacuum/pressure pump should provide many hoursof trouble-free operation.Dry vacuum/pressure pumps are 100% oil-free.Thepump employs a non-lube piston and cylinder. Nomaintenance is necessary for the bearings.All bearings are sealed and permanently lubricated.Lubrication should not be attempted. The units arebuilt for continuous duty operation with quietnessand durability.CAUTION: Do not lubricate any of the parts with oil,grease or petroleum products. Do not clean with acids,caustics, or chlorinated solvents. Do not replace theconnecting rod or motor bearings.Disconnect the pump from power beforeperforming any maintenance.Replacing the O-ring1. Unscrew the four socket-cap screws from the pump head and unscrew the two screws from the pump handle. Remove the pump head assembly from the top of the pump.2. Remove the five Phillips-head screws that hold the valve plate assembly to the underside of the pump head assembly.3. Remove the O-ring and replace it by pressing the new O-ring into the groove.4. Replace the valve plate assembly with the recessed screw holes facing out and tighten the five Phillips-head screws.5. Replace the pump head assembly and tighten the socket head screws.head Replacing the Diaphragm1. Unscrew the four socket-cap screws from the pump head and unscrew the two screws from the pump handle. Remove the pump head assembly from the top of the pump.2. Unscrew the four Phillips-head screws, thenremove the retainer plate, the diaphragm liner , and the diaphragm.3. Replace the diaphragm (the number printed on it should be facing up), aligning the holes in the diaphragm with the screw holes in the top of the pump.4. Replace the diaphragm liner , lining up holes in the liner with the screw holes in the top of the pump.5. Replace the retainer plate, aligning the four small holes with the screw holes and orienting the large hole to the left as shown. Replace and tighten the Phillips-head screws.CAUTION: Take care not to nick the heads of the screws; burrs can damage the inlet valve.6. Replace the pump head assembly and tighten the six screws to hold it in place.TroubleshootingVacuum ProblemsLeakage, contamination, and unusual out-gassing are the general causes of problems associated with poor vacuum. To operate at maximum efficiency, a system must be thoroughly clean. If the system is completely clean and free from leaks, and unwarranted vacuum problems still exist, the pump should be checked. A simple criterion for the condition of the pump is the determination of its maximum vacuum capability. This can be accomplished by blocking the intake and reading the vacuum level on the gauge.Pressure ProblemsLeakage and contamination are the general causes of problems associated with poor pressure. To operate at maximum efficiency, a system must be thoroughly clean. If the system is completely clean and free from leaks, and unwarranted pressure problems still exist, the pump/compressor should be checked bya service technician.RepairTwo replacement part kits are available for the chemical duty vacuum/pressure pump.The accompanying drawing outlines the contents of each of the kits. We recommend trained service technicians perform repairs. For further information and help ordering the correct kit, please contact Technical Service.Disconnect the pump from power before performing any maintenance.The life science business of Merck operates as MilliporeSigma in the U.S. and Canada.Merck, Millipore, Millex, and Sigma-Aldrich are trademarks of Merck KGaA, Darmstadt, Germany or its affiliates. All other trademarks are the property of their respective owners. Detailed information on trademarks is available via publicly accessible resources.© 2021 Merck KGaA, Darmstadt, Germany and/or its affiliates. All Rights Reserved.SpecificationsPerformance Vacuum24.0 inches of Hg (inHg)Maximum Free Air Displacement 37 L/minPressure20 psi continuous, 35 psi intermittent(230 V~ pump duty cycle: 15 minutes on, 15 minutes off)Sound Level Less than 60 dB(A)Dimensions WP6111560, WP6110060WP6122050Length 7.5 in. (19.1 cm)10.5 in. (26.7 cm)Width 7 in. (17.8 cm)9.4 in. (23.9 cm)Height8 in. (20.3 cm)9.7 in. (24.6 cm)Weight (approximate)9 lbs (4.1 kg)12 lbs (5.4 kg)Tubing connectorsStepped 1⁄4 in. hose barbMaterials of Construction Body and pump head Die cast aluminum Diaphragm Buna-N with PTFE lining Head gasket Buna-NLeaf valves High grade stainless steel Internal pump surfacesPTFE-coatedElectrical Specifications115 V~, 60 Hz, 3.5 A or 100 V~, 50/60 Hz, 4.0 A Shaded-pole, single phase,1⁄15 HP motor 3-pronged, grounded cord and plug 230 V~, 50 Hz, 1.7/1.1 AHAR cordage, CEE 7/7 (Schuko) plugLine voltage limits±10% of supply voltageEnvironmental Conditions Temperature 5 °C (41 °F) to 40 °C (104 °F)Relative Humidity, Max.80% for temperatures up to 31 °C, decreasing to 50% at 40 °C Altitude, Max.2,000 metersPollution Degree 2, per IEC 664(indoor usage: lab, office, etc.)Installation CategoryII, per IEC 624(local level: appliances, portable equipment, etc.)Product Ordering InformationPurchase products online at .Catalogue NumberChemical DutyVacuum/Pressure Pump 115 V~, 60 Hz WP6111560230 V~, 50 Hz WP6122050100 V~, 50/60 Hz WP6110060Replacement Parts Pump Maintenance KitWP61MNT00Includes diaphragm, diaphragm liner , O-ring gasket, head screws, and handle screws Pump Rebuild KitWP61RBD00Includes hold-down plateassembly, valve plate assembly, pump head, vacuum gauge, pressure gauge, head screws, and handle screws Millex ®-FA 50 filter unit, 10/pk SLFA05010Pressure tubing, silicone, 25 ft XX8000025Vacuum tubing, silicone, 4 ftXX7100004NoticeWe provide information and advice to our customers on application technologies and regulatory matters to the best of our knowledge and ability, but without obligation or liability. Existing laws and regulations are to be observed in all cases by our customers. This also applies in respect to any rights of third parties. Our information and advice do not relieve our customers of their own responsibility for checking the suitability of our products for the envisaged purpose.The information in this document is subject to change without notice and should not be construed as acommitment by the manufacturing or selling entity, or an affiliate. We assume no responsibility for any errors that may appear in this document.Contact InformationFor the location of the office nearest you, go to /offices .Technical AssistanceVisit the tech service page on our web site at /techservice .Standard WarrantyThe applicable warranty for the products listed in this publication may be found at /terms .。
A2VK计量泵
=N
=NTH_
12
28
55
Us
10.6
12.7
16
N
70
70
80
kg
19
36
64
107 13.4 120 117
油路图
闭环
)
9
;
<
<
; (
;
开环
)
9
;
<
<
<
<
:
<
;
< :
;
RC 94001/07.04 A2VK
尺寸,规格 12
9 )
<
;
3...4
– 高配流精度,可变抽吸体积具有可重复性
5
– 通过集成手轮进行可靠的手动调节 精度测量范围
6
– 工作压力最高达 250 bar
7
– 所抽吸介质的脉动低
8
– 由于特殊的材料配对和密封元件,泵配件与所抽吸介质
12
(多羟基化合物,异氰酸酯)相容
– 低噪音
– 对于高配流精度,容积效率极佳
– 带缓冲流体口的双重轴密封圈可保证安全运行 (以及保护环境)
首选安装位置: 传动轴水平
仅当调节心轴的安装角度与水平方向成 –30° 至 +30° 时, 才能保证 手轮中的调节显示工作。
闭环: 泄漏流体压力 p最大绝对___________________________ 10 bar 最大间歇性累积压力 A + B p最大__________________ 250 bar
A2VK RC 94001/07.04
术数据
值表
规格 排量 流量1) 速度为 n
德国乌拉卡(Uraca)TWK 三维清洗喷头
Cleaning of the highest quality2Perfect internal cleaningof vessels with the URACATWK system In industries such as the chemical,petrochemical, synthetics, paperand food industries, in short, when-ever or wherever deposits in vessels, reactors, autoclaves, tanks or similar equipment impair the product quality and production effi-ciency, the URACA TWK system comes into its own.Even boiler sediment, coke, poly-mers or tough residue such as natural, synthetic or PVC latex can easily be removed with the URACA TWK system.TWK - the new generation The tried and tested URACA tank cleaning heads have been comple-tely reworked and a new familyhas been created to cover comple-tely a huge spectrum of cleaning tasks.Three different model sizes are available in six different pressure levels (600 bar–1,200 bar), to handle various water flow rates.TWK – the advantages s More compact cleaning jet overa range of 3 metres.s Smaller displacement circle (in conjunction with extremely compact rotors).s Minimal pressure losses due to large internal cross-sections.sSimple assembly and disassem-bly.sPressure gaskets with a long service life are easy to replace.sSmooth casing surface means few catching areas. It is now impossible to get caught on the casing, so a protective cage is no longer necessary.sCleaning temperature up to 95 °C.sWear-free, adjustable, encapsu-lated solenoid brake. Easily regulated to ensure perfect adjustment of the rotor speed.sIs suitable for direct use with a hose, suspended from a cable via an eye-bolt or for horizontal application via positioning systems.sOutstanding running stability,even at the highest pressures.sSpecial rotor types and exten-sions adapted to the local con-ditions guarantee thorough cleaning.sCrNi steel. TWK – totally economical s Very effective reach to distantsurface areas reduces the "outof service" times and so impro-ves the utilisation of your pro-duction plant.s The comprehensive level ofcleaning improves the productquality and increases produc-tion efficiency.s Chemical cleaning additives canbe forgotten, because the TWKusually works with clear, coldwater. This results in simplewaste disposal and low costs.s Warm water, additives andother fluids are possible.s Partly or fully automatic opera-tion reduces personnel costs.s Gas- or pressure-tight installa-tion of the TWK system avoids the need to evacuate and flush the reactor, is environmentally friendly and helps to make the workplace more humane.s The URACA nozzle system with a convenient flow water supply saves time, water and energy costs.s Should a TWK become defec-tive, our replacement service will save you from sleepless nights. A replacement device will be sent to you within24 hours.Pressure level diagramP[bar]02004006008001000120014001600TWK 125-1600TWK 150-1400TWK 185-1200TWK 125-1000TWK 175-800TWK 200-600The TWK family at a glance3TWK-Type 125-1600150-1400185-1200125-1000175-800200-600DesignStandard Standard Standard Chemical Chemical Chemical Max. operating pressure bar1600140012001000800600Recommended flow rate l/min50-15050-250100-40050-20075-350100-600Transmittable power kW400600800350450600kv-rate ∆p =(Q kv)2Q = flow rate in l/min 3548784363130∆p = pressure loss in bar Min. displacement circle* Ømm125150185125175200Rotor speed min -15-204-203-205-204-203-20Compact jet length (400bar)m 333,533,54Connecting shaft screw threadM 24x1,5G1G1M 24x1,5G1M 38x1,5Overall lenght without adapter mm360405445360405435 Weight kg10,515,023,510,514,023,50061-521K W T 0001-521K W T 0041-051K W T 008-571K W T 0021-581K W T 006-002K W T Durchflussdiagramm P[bar]0510********Q [l/min]0100200300400500600700Conversion values: bar=14,5038 psi, 1l=0,26417 USGal., 1kW=1,3410 HP, 1mm=0,03937 inch.* The displacement circle describes the smal-lest possible space required for the rotatingTWK, including rotor.All URACA TWK cleaning heads have anextremely small displacement circle, meaningthat the required opening is minimal.The minimum displacement circle mentionedis achieved with the aid of a specific leverarm.125-1600125-1000150-1400175-800185-1200200-600TWKTWK TWK TWK TWK TWK 125-125-150-175-185-200-1600100014008001200600Stand.Chem.Stand.Chem.Stand.Chem.TWK A system made to measure You yourself determine the techni-cal design of your TWK system through your specific requirements in terms of automation level and luxury.Given your information about the work cycle and the local spatial dimensions, we are able to design "your system".TWK – integration into a wide range of products The URACA TWKs are the very core of the vessel cleaning system.Beyond them, URACA can complete the cleaning system you require by providing all the other necessary and sensible elements:s High-pressure pump units in all performance classes, mobile orstationary.s Semi- or fully automatic tank cleaning systems with manual,electric, hydraulic or pneumatic drives.s Positioning devices and other accessories.Please ask for our special brochures.T WK.d5.3dBURACA Pumpenfabrik GmbH&Co.KG Sirchinger Straße 15D-72574 Bad Urach, GermanyPhone +49 (7125) 133-0Fax +49 (7125) 133-202info@uraca.dewww.uraca.deCertified acc. to:■DINENISO9001:2000 by LRQA ■VGB KTA 1401■Gost。
萨澳90系列柱塞泵马达型号代码
P= 外接压力过滤器—卡口式过滤器(短的)○○○○○○○○L = 外接压力过滤器—卡口式过滤器(长的)-○○○○○○○
F
●= 标准Array○= 选用
- = 无货
* = 19-95年供货
250的泵
型号--90R250MA2CD80T3C05NNN262624
1—R-右旋
2—250-排量
3—MA-手控变量
4—2-只有高压溢流阀
5—CD-SAE C 14齿,带密封盖
6—T-远程液控,无滤清器
7—3-无排量限制器
8—C-14毫升补油泵
9—05-1.37毫米的节流孔
10—NNN-无特殊要求
11—26-26-“A”“B”腔的压力设定
12—24-补油压力
100的泵
型号-90R100MA1AC60L3S1E03GBA323224
90R-右旋
100—排量
MA—手控变量
13—带压力限制器
AC—SAE A 9齿 辅助安装
60—两侧油口
L—自带长压力滤清器
3—无排量限制器
S—14齿主轴
E—20毫升补油泵
03—0。
81毫米节流孔
GBA—低噪音配油盘
32—32—“A”“B”口压力设定
24—补油压力
100的马达
90M100NC0N8N0CTW00N0N000024
90M—定量马达
N(7)--轴向油口
C6—主轴21齿,C8—27齿W—带回路清洗
24—补油压力
定量马达型号名称与订贷代码
○ = 可供选用
- = 不供应 ** = 不应用
● = 标准的
○ = 可供选用 - = 不供应 ** = 不应用。
进口柱塞泵马达液压原理图集锦之1萨澳SAUER
进口柱塞泵马达液压原理图集锦第一部:萨澳-丹佛斯-大金液压柱塞泵马达萨澳-丹佛斯,20系列变量柱塞泵说明:1=变量柱塞泵 2=补油泵 3=控制阀 4=单向阀 5=补油溢流阀 6=滤清器 7=散热器油口:A,B=系统压力 S =吸油真空度 L 1,L 2=壳体回油 M =测压口萨澳-丹佛斯,20系列定量柱塞马达定量马达(无阀)说明:1=定量马达油口:L 1,L 2---壳体回油口 A,B---系统压力口定量马达(带冲洗阀)说明:1=定量马达 2=低压溢流阀 3=梭形阀 4=高压溢流阀油口:L 1,L 2---壳体回油口 M A ---A 口测压口 M B ---B 口测压口 M=低压腔测压口定量马达(带冲洗阀和旁通阀)说明:1=定量马达 2=低压溢流阀 3=梭形阀 4=高压溢流阀 5=手控旁通阀 油口:L 1,L 2=壳体回油口 M A =A 口测压口 M B =B 口测压口 M=低压腔测压口萨澳-丹佛斯,20系列变量柱塞马达油口:L1,L2=壳体回油压力M A=A口测压口M B=B口测压口M=低压腔测压口萨澳-丹佛斯,40系列泵马达MPV046手动控制泵液压原理图注释:MDC---手动控制阀单元 M 1---系统压力A 口测压口M 2---系统压力B 口测压口 M 3---补油压力测压口M 4,M 5---控制压力测压口 L 1,L 2---壳体回油口 A ,B---系统压力口 S---补油泵吸油口MPV035变量柱塞泵MPV046变量柱塞泵MPV046液动控制泵液压原理图HDC---液压控制阀单元 M 4,M 5---控制压测压口 X 1,X 2---壳体回油口 A ,B---系统压力口 S---补油泵吸油口MPV046 电磁阀控制泵液压原理图FNR---通断电控阀单元 M 4,M 5---控制压测压口 A ,B---系统压力口 S---补油泵吸油口MPV046 电比例控制泵液压原理图EDC---电比例控制阀单元M4,M5---控制压测压口A,B---系统压力口S---补油泵吸油口MPV035串泵,外补油选择MPV035串泵,内补油选择M25系列定量柱塞马达液压原理图(无冲洗阀) M25定量柱塞马达M25/35/44/46系列定量柱塞马达液压原理图(有冲洗阀)M35定量柱塞马达M25/35/44系列变量柱塞马达液压原理图(有冲洗阀)M46 变量马达液压回路图注释:M1---系统压力A口测压口M2---系统压力B口测压口X1,X2---控制压力口L1,L2---壳体回油口A,B---系统压力口40系列泵马达液压系统原理图萨澳-丹佛斯,90系列变量柱塞泵注释:M 1---A 口测压口 M 2---B 口测压口M 3---补油压力测压口M 4,M 5---控制测压口L 1,L 2---壳体回油口 A ,B---系统压力口 S---补油泵吸油口FNR控制方式EDC控制方式HDC控制方式MDC控制方式萨澳-丹佛斯,90系列变量柱塞马达油口解释:A,B =高压油口,称A,B口,或A,B腔S =补油口L1,L2=壳体回油口M1,M2 =A,B腔测压口M3=补油压力测压口M4,M5 =控制压力测压口萨澳-丹佛斯,90系列定量柱塞马达解释:A,B = A,B口,系统油口L1,L2=壳体回油口M1,M2=A,B口的测压口M3 = 低压测压口萨澳-丹佛斯,90系列无反馈变量柱塞泵90系列泵马达液压系统回路图萨澳-丹佛斯,51系列马达HZ控制方式马达回路图油口解释:A,B---系统压力口L1,L2---壳体回油口M1,M2---系统压力测压口M3,M4---伺服压力测压口M5---伺服压力供油测压口M7---控制压力测压口X1---控制压力口插装式两位控制E1,E2两位控制F1,F2液压比例控制HZ, HS, K1, K2制动压力失效回路图无制动压力失效 K1,K2控制阀液压比例控制HP制动压力失效回路图无制动压力失效电/液压比例控制EP,EQ,ER,ES制动压力失效回路图无制动压力失效压力补偿控制TA,TH,T1,T2制动压力失效回路图无制动压力失效90系列泵和51系列马达液压系统回路图萨澳-丹佛斯,H1系列泵萨澳-丹佛斯,42系列泵MDC带中位启动和过载保护MDC带过载保护MDC手动变量控制阀FNR开关式电控阀—原理图外形图EDC比例电控阀—原理图剖面图NFPE液控阀液压原理图 NFPE液控阀剖面图无反馈比例液控阀剖面图无反馈比例液控阀剖面图萨澳-丹佛斯,搅拌车用变量柱塞泵带高压溢流阀无高压溢流阀萨澳-丹佛斯,搅拌车用定量柱塞马达。
- 1、下载文档前请自行甄别文档内容的完整性,平台不提供额外的编辑、内容补充、找答案等附加服务。
- 2、"仅部分预览"的文档,不可在线预览部分如存在完整性等问题,可反馈申请退款(可完整预览的文档不适用该条件!)。
- 3、如文档侵犯您的权益,请联系客服反馈,我们会尽快为您处理(人工客服工作时间:9:00-18:30)。
High pressure plunger pumpsHigh pressure plunger pumps for use in extreme conditionsReciprocating plunger pumps play a key role in almost all areas of process technology where fluids must be handled against high pressure.Possible fields of application and types of jobs are so varied that there is a con- stant need for new designs and materials in order to meet customer demands for new pump versions.Plunger pumps are used in indus- try where there are high or maxi- mum operating pressures. At a constant speed their capacity is virtually independent of operating pressure – an important feature in control operations. Capacity is proportional to speed. In all power ranges plunger pumps display high overall efficiency, which is as a rule above 90 %. This also applies to partial load operation. This is why plunger pumps are among the most economical machines – a major factor in view of rising energy costs.Uraca pumps are usedworldwide.Test pumps are used for hydro-static pressure testing, includingthe testing of pipes, pipelines,vessels a nd c ontainers, g as c ylin-ders and many other high-pressurecomponents. The units are alsoavailable for use in potentiallyexplosive area zone 2 (equipmentgroup II, equipment category 36according to ATEX).Industrial pumps can be usedin virtually all industrial areas,including heavy industry, energytechnology, the oil industry as wellas in the food and textile industry.The pumps are used mainly asdrives for rolling mills, boiler feedpumps, pumps for hydrostaticbearing lubrication, for descalingas well as for cleaning with high-pressure w ater.Chemical and process pumpsare used for hot, aggressive,abrasive, toxic agents as well asfor liquid gases.The areas of application aremainly in the chemical and petro-chemical industry, but also inthe manufacture of detergents,the recycling of plastics and oilresidues as well as injection andthe extraction of oil from coal.Pump units can be installedfor the most varied of applicationswith diesel or electric motors.3Perfection in detailPower endsURACA’s power ends are usedworldwide. Every day they provethemselves in continuous operationto the satisfaction of our cus-tomers. The fields of applicationrange from the polar circle tothe tropical climate zones. Highoperating safety and above-average service life are typicalURACA features.Power ends for higher powerrequirements are equipped with oilcooling and forced oil lubrication.Power ends for lower powerrequirements have centrifugallubrication. T he v arious s eriescover a power range of up toapprox. 2600 kW.The power ends for series KD 600and KD 700 are compact and havea low weight coefficient. Powerend and liquid end are separatedby an intermediate chamber andspecial crosshead seals, preventingany liquid from entering the powerend.The power ends of the big pumpseries KD 800 have an incline-divided power end for easierinstallation and for easier mainte-nance of the crank mechanism.The power ends are equipped witha bridge for centering of longstuffing boxes.The new generation of the P-serieshas a crankshaft with multipleslide bearings and features threepower groups with 3, 5 and 7plungers.4Stuffing boxesDue to the wide-range of appli-cations for our plunger pumps,stuffing boxes and seals aredesigned to meet the requisites ofthe r espective l iquid. E asy-to-handleliquids, such as water, emulsionsor similar, can be controlled withsimple seals.URACA w ill provide t he b estpossible design to match the liquidyou handle.With fluids it is necessary, forexample, to take special measuresto reduce dead space or to installplunger guide bushes that are self-lubricating. The more demandingthe liquid is, the more extensivethe back up systems integrated inthe stuffing boxes. Consequently,heating, cooling, synchronousinjection, flushing or interlockingcomponents can be installed.Valve blocksThe design of the valve blocksdepends to a high degree on theproperties of the respective liquid.Cone, plate and ball valves areavailable. What they have incommon is high efficiency, lowwear and tear and outstandinglyeasy maintenance.5Leak-free handlingHeightened environmental awareness requires both the pump manufacturer and the operator to consider leak-free handling when designing and selecting the pumping equipment.URACA d iaphragm pumps o ffer aunique solution in the handling ofdangerous fluids. They help in parti-cular to increase the operatingsafety of production plants and toimprove the working conditions ofthe operatives. Hermetically sealedplunger pumps are mainly used fortoxic, explosive, aggressive, foul-smelling, environmentally harmfulor a brasive f luids. U RACA d iaphragm pumps offer the advantages of a piston sealing that is virtually free of wear and tear as well as abso- lutely leak-free handling.URACA diaphragm pump heads operate at a pressure range of up to 350 bar, while the temperatures of the fluid handled can be from -40 to +150° C . The PTFE-dia- phragm, which is resistant to virtu- ally all fluids, hermetically seals the fluid chamber. The selection ofmaterials for the parts touchedby the fluid as well as the designof the self-acting valves andthe stroke frequency of the pumpdepend on the respective fluid.Integrated monitoring systems pre-vent any overload of the unitand signal any diaphragmfailures immediately.URACA diaphragm pumps are available in a power range of up to 250 kW. Operating pressure may be350 bar, capacity up to 850 l /min.URACA diaphragm pumpsfeature the following specific advantages:■ Economy ■ High operatingsafety■ High service quality■ Space-saving design■ Flexibility of drive6▲▲Consistent URACA quality – the basis of a mutually beneficial relationshipProduct research and develop- ment at modern 3D-CAD-work- places to meet customer s’ needs and wants.Precision machining guarantees failure-free service lifeMeticulous assembly work by a highly trained and committed workforceA trial run lasting several hours on the test bed as well as comprehen- sive test programs are a demon- stration of guaranteed excellence.Many years of service life at the customer – t he basis of a mutually beneficial relationship.7VP.e5.6L+S High Pressure –State of the Art Technology –WorldwideURACA Pumpenfabrik GmbH & Co. KGSirchinger Straße 15D-72574 Bad Urach, GermanyPhone +49 (71 25) 133 - 0Fax +49 (71 25) 133 - 202info@uraca.dewww.uraca.deCertified acc. to:■DIN EN ISO 9001: 2000 by LRQA■VGB KTA 1401■GostURACA i s a l eading m anufacturer ofhigh pressure plunger pumps andhigh pressure water jettingtechnology equipment. Since 1893the company has been a globalleader in the development of thistechnology.URAC A‘s core competency lies inthe development, design,and manufacture of high pressureplunger pumps, pump units, andaccessories for almost all industrialfields.URACA offers leading technologicalknow-how in the field of fullyautomated and process-integratedsystem t echnology.The key focus is on two marketsegments:■High-performance pumpsolutions for the CPI sectorsand heavy industry.■A universal and modularcomplete programme for high-pressure water jettingtechnology, especially for highlyautomated plants.The German domestic marketis covered by URACA sales centersand a network of service centers.Internationally, URACA hassubsidiaries and agencies.Additionally n umerous r epresenta-tives underline the company’spresence around the globe.A high standard of research anddevelopment, plus a modernmanufacturing facility stand forunsurpassed p roduct q uality.Ongoing market r esearch and closeattention to current marketneeds safeguards the company’stechnological l eadership.Each URACA customer profits fromthis comprehensive experienceand technology and will find thatURACA is a h ighly c ompetentpartner in the solution of theircleaning p roblems.。